Algunos líderes en el sector están migrando de la calefacción simétrica al método termodinámico
Tendencias en la tecnología de canales calientes
Por otro lado, los transformadores exigen componentes para las máquinas con un mantenimiento más sencillo, que sean más flexibles y que utilicen boquillas adaptables a nuevos diseños, materiales y aplicaciones. Todos estos avances están contribuyendo a reducir el uso de la resina, con lo que bajan los costes y disminuye el impacto medioambiental. Si observamos los últimos desarrollos en canales calientes, se hace evidente que están surgiendo varias tendencias.
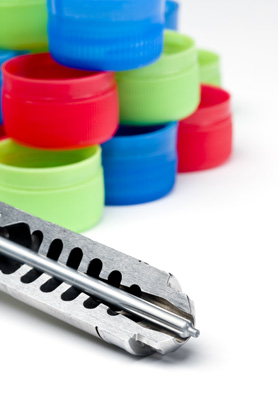
Mayor uniformidad térmica
El distribuidor es un componente primordial en el suministro a la cavidad de un material fundido consistente y homogéneo. Los modelos estándar actuales del sector incorporan canales de material fundido equilibrados de forma natural (con o sin cambios de nivel), así como calefacción perfilada que sigue la forma tanto de los canales de material fundido como del distribuidor.
Intentar demostrar lo que es un distribuidor con equilibrado térmico mediante una foto externa a las placas no constituye una representación precisa, ya que los disipadores de calor (puntos de contacto del distribuidor de calor en el interior de las placas) están separados. Es fácil conseguir una uniformidad térmica perfecta en el distribuidor cuando se le retira de las placas, sin embargo, lograr esta uniformidad dentro de las placas constituye todo un reto.
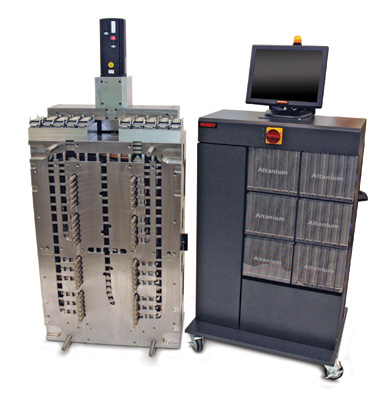
Por ello, algunos líderes en el sector están migrando de la calefacción simétrica al método termodinámico. Este método de calefacción utiliza software de análisis térmico, que evalúa a la vez la pérdida de calor y la entrada de calor. El software puede predecir de forma precisa la temperatura real del canal del distribuidor mientras se encuentra en las placas de mitades calientes durante el proceso de moldeo por inyección. Gracias a este método, analizando el distribuidor se pueden eliminar problemas habituales, como los puntos calientes y fríos. Así disminuye la posibilidad de degradar el plástico, se aceleran los cambios de color y se logra un impacto positivo en el equilibro entre cavidades.
Otros dos importantes factores son las resistencias de las boquillas y el control de temperatura. Las boquillas controladas por termopar se han convertido en lo habitual en el sector. De hecho, muy pocos segmentos del mercado siguen utilizando el control porcentual para las boquillas. Las boquillas controladas por termopar se han convertido en el estándar porque proporcionan a los transformadores un mayor control del proceso. El controlador y la información proporcionada por el termopar también se pueden utilizar para solucionar problemas al ofrecer una 'vista interior' del canal caliente y del molde, que de otro modo sólo sería posible desmontando e inspeccionando los sistemas. Por ejemplo, si la zona de una boquilla no alcanza la velocidad apropiada dentro del intervalo de tiempo adecuado o se queda atrás con respecto a las demás zonas, existe la posibilidad de que la boquilla esté en contacto con las placas o el casquillo de inyección de forma indebida y de que esté utilizando demasiada potencia o no esté alcanzando el valor de ajuste. El controlador puede detectar esto si existen termopares asociados a la boquilla y al distribuidor.
Los fabricantes de canales calientes más importantes buscan sin cesar mejores soluciones para conseguir un control preciso de la temperatura. Husky Injection Molding Systems ofrece un controlador de temperatura que no sólo regula la temperatura, sino que en función de las condiciones del proceso y termodinámicas específicas, adapta el propio algoritmo al entorno en el que la boquilla está funcionando. Por ejemplo, se necesita un algoritmo diferente dependiendo de si la boquilla está bien refrigerada en el punto de inyección o si solo cuenta con refrigeración limitada en el punto de inyección. En las pruebas, esto ha dado como resultado temperaturas mucho más próximas al valor de ajuste en la punta de la boquilla. Al comparar un controlador no adaptable con uno adaptable, la variación en el valor de ajuste pasó de +/-2,5 °C a tan solo +/-1 °C.
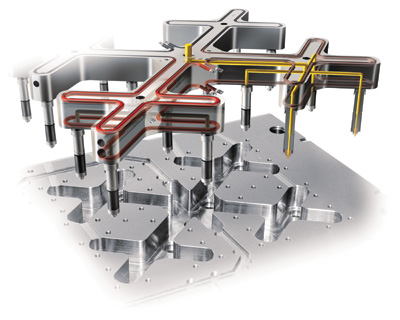
Homogeneidad avanzada del material fundido
Cuando se trata específicamente de aplicaciones de tapones y de consumo, la calidad de las piezas y de la producción, además del rendimiento en el cambio de color, son factores principales que hay que tener en cuenta. Para lograrlo, es fundamental mantener una homogeneidad óptima del material fundido.
Los canales de material fundido del distribuidor están diseñados para mantener un cizallamiento y perfil térmico uniformes y eliminar los puntos muertos. Algunas de las boquillas mejoradas del mercado mezclan el material fundido justo antes de que entre en la cavidad del molde. Al redistribuir el material fundido, el diseño interior crea flujos de material fundido que se superponen y fluyen uno por encima del otro para comenzar la mezcla.
El objetivo de los fabricantes líderes en canales calientes es aumentar la productividad al mismo tiempo que producen piezas más homogéneas estructuralmente. Como resultado, se pueden obtener mejoras en varias áreas: reducción en los tiempos de cambio de color, eliminación de las líneas de flujo y mayor estabilidad dimensional de las piezas gracias a una mayor uniformidad de la temperatura de distribución de la resina. Esto, a su vez, minimiza la contracción y el alabeo, logrando tolerancias más estrictas en las piezas.
Paredes más delgadas y mayor producción
En el envasado de alimentos, la tendencia ha sido conseguir paredes cada vez más delgadas y una mayor producción. Para adaptarse a esta tendencia, las boquillas deben ser capaces de soportar presiones cada vez mayores. Según ha aumentado la demanda de piezas más finas para las aplicaciones técnicas y de envasado, ha sido necesario aplicar presiones mucho más altas a las máquinas y a los sistemas de canales calientes. La media actual del sector para la presión de inyección es de aproximadamente 25.000 psi, pero hay disponibles boquillas con presiones de inyección más altas.
Si embargo, una presión más alta se traduce en una mayor necesidad de aumentar la resistencia al desgaste. Para conseguir esto, se puede modificar el diseño, la fabricación, las dimensiones o los materiales. Por ejemplo, Husky fabrica un cierre por válvula con tres aleaciones independientes: un material resistente al desgaste para evitar la abrasión interna, un material termoconductor en el exterior y otro material más resistente en el exterior para evitar dañar la junta.
Cierre por válvula eléctrica
Los sistemas de canales calientes han utilizado tradicionalmente actuación neumática o hidráulica para abrir y cerrar los cierres por válvulas. Aunque las dos tecnologías son muy útiles para aplicaciones específicas, las nuevas agujas de obturación accionadas eléctricamente garantizan mayor control, actuación más limpia, menor distancia entre boquillas, puntos de inyección de mayor calidad y menor mantenimiento.
En los últimos años, la tecnología de servomotor eléctrico se ha hecho más asequible. El sistema de cierres por válvula accionados eléctricamente de Husky combina la resistencia de las tecnologías de canales calientes neumática e hidráulica, utilizando un servomotor para abrir y cerrar las agujas del obturador de forma precisa. El sistema de actuación mediante agujas de obturación accionadas eléctricamente y sincronizadas satisface la creciente demanda de electrificar toda la célula del molde y ofrece soluciones únicas para el moldeo del sector médico y otras aplicaciones de gran producción.
Un sistema accionado eléctricamente ofrece a los transformadores varias ventajas. El servomotor eléctrico proporciona mayor consistencia y precisión al abrir y cerrar las agujas de obturación exactamente al mismo tiempo. Junto con la actuación de la placa, los sistemas eléctricos proporcionan funciones de inyección directa de menor distancia entre boquillas (18 mm/0,7 pulg.). Además, el controlador de temperatura integrado hace que el rendimiento sea fácil de documentar. Al dirigirse tanto el servomotor eléctrico como las resistencias de los canales calientes desde una única interfaz, la configuración se realiza fácilmente.
Conclusiones
Los requisitos de rendimiento de los canales calientes son cada vez más exigentes, por lo que una calidad superior, un mejor rendimiento, un mantenimiento sencillo y una mayor flexibilidad son factores primordiales que impulsan la tecnología de los canales calientes de hoy en día. Como las aplicaciones, los materiales y los diseños son cada vez más complejos y variados, es imprescindible que los fabricantes de canales calientes tengan estos factores en cuenta para seguir siendo competitivos en el mercado actual y futuro.