Hipermoulding, reducción de los tiempos de ciclo en el proceso de inyección
23 de marzo de 2009.
En el análisis de la termodinámica implicada en el proceso de inyección se ha realizado la definición de algoritmos para calcular el tiempo de ciclo y el análisis de costes, que se han llevado a cabo mediante una hoja de cálculo de fácil uso para comparar la solución convencional con respecto a la solución Hipermoulding que ayuda al moldeo por inyección de plásticos europeo a decidir cuando se ha de aplicar un canal de refrigeración conformado, dependiendo de los costes de producción.
El objetivo principal del proyecto Hipermoulding era la reducción de los tiempos de ciclo en el proceso de inyección, más específicamente mediante la optimización del posicionado de los canales de refrigeración (refrigeración con geometría libre). Para conseguirlo, se ha estudiado cada una de las diferentes etapas de diseño, fabricación y uso de los moldes de inyección, buscando determinar las tecnologías y procedimientos exigidos. Además de estas actividades basadas en la tecnología, una parte importante del proyecto se centró en probar la economía de este nuevo enfoque Hipermoulding, así como la integración y difusión dentro de la comunidad industrial.
La reducción de los tiempos de ciclo es esencial para el sector industrial debido a que tiene un efecto directo en el coste de las piezas inyectadas. Este objetivo se ha conseguido mediante la investigación y desarrollo de un útil juego de herramientas que pueden usarse con facilidad por diseñadores de piezas y de molde. Dependiendo de los requisitos específicos del caso y de la producción, los ahorros de tiempo son superiores al 30%. Por otra parte, las estrategias para conseguir la mejor calidad superficial posible de los Hipermoldes también ha sido objeto de investigación dentro del proyecto.
Las recientes y continuas mejoras en las tecnologías aditivas de fabricación y en los materiales de herramientas no han constituido el núcleo de este proyecto, admitiendo que a corto plazo existirán más y mejores combinaciones de máquinas y materiales. Sin embargo, la herramienta desarrollada podrá aplicarse a todas y cada una de ellas porque se ha concebido para que así sea.
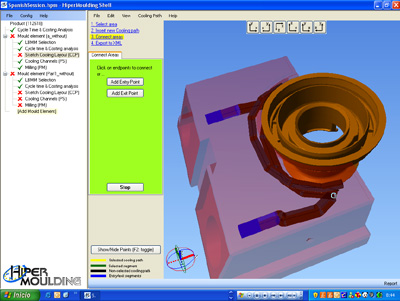
Desarrollando, combinando e integrando
Varios desarrollos previos en diferentes ramas de la tecnología y del conocimiento tienen soluciones existentes que se han reunido e integrado en este proyecto. Por una parte, las bases de la termodinámica y métodos numéricos ofrecen buenas soluciones para simular el comportamiento del polímero fundido durante el proceso de inyección. Por otra parte, los modelos de coste y la economía de las empresas inyectadoras ayudan a determinar el coste de la pieza de plástico producida. Y en medio de la cadena, las técnicas de fabricación aditivas han abierto un nuevo paradigma en la ingeniería de fabricación de moldes.
La unión de todas estas herramientas disponibles no ha sido fácil y la integración de todas ellas ha requerido el desarrollo de software, bases de datos, plugins e ingeniería basada en el conocimiento, no existentes previamente. Como resultado de todo ello, el software Hipermoulding necesita las siguientes entradas:
a) 3D de la pieza
b) 3D del molde
c) Material de la pieza
d) Requisitos de la pieza
e) Información sobre la máquina de inyección
Y genera las siguientes salidas:
f) Diseño de refrigeración con geometría libre
g) Tecnología de fabricación y sus procedimientos de acabado más adecuados
h) Parámetros de inyección
i) Tiempo de ciclo y análisis de costes
La figura 1 ilustra una de las pantallas del módulo Hipermoulding, que se ha efectuado de acuerdo con los requisitos de los usuarios finales desde el principio.
Ingeniería asistida por ordenador
Una vez está lista la información de inicio, el módulo Hipermoulding es capaz de dibujar los canales de refrigeración óptimos de acuerdo con la termodinámica y también con las restricciones de la tecnología de fabricación elegida. En cualquier caso, el usuario puede cambiar los parámetros y el módulo propondrá otro posicionado.
Es importante tener en cuenta que los dibujos de los canales de refrigeración pueden editarse ya que se exportan en un archivo CAD al software comercial. Como resultado, el tiempo requerido para diseñar los canales de refrigeración óptimos es realmente corto (algunos minutos en casos estándar).
El software valora también la estimación del tiempo de ciclo. Teniendo en cuenta que el algoritmo para situar los canales de refrigeración sigue las leyes ideales del intercambio de calor, puede afirmarse que la estimación del tiempo de ciclo será con toda seguridad la estimación ideal. Y como se ha demostrado en el marco del proyecto, esto es cierto en la mayoría de los casos reales.
Fabricación basada en capas
En la actualidad, los canales de refrigeración de libre geometría pueden realizarse por medio de técnicas de fabricación basadas en capas (conocidas también como fabricación aditiva). Se ha creado una base de datos exhaustiva para caracterizar las técnicas y los materiales disponibles. Se han llevado a cabo pruebas de fabricación y ensayos mecánicos para tener la misma información para cada técnica en un formato estándar de valores. Sabiendo que estas técnicas todavía se están desarrollando y mejorando, la base de datos puede ser actualizada en cualquier momento por el usuario.
Se han realizado también pruebas para determinar la vida media de los insertos fabricados con estas tecnologías. Se ha efectuado también un profundo estudio para fijar las mejores estrategias de acabado para cada tecnología y material.
Según los requisitos de la producción, el módulo Hipermoulding enumera las técnicas potenciales que pueden usarse de acuerdo con los criterios seleccionados por el usuario (costes, dureza, conductibilidad térmica y grado de acabado superficial).
Análisis de costes
El software Hipermoulding ofrece un módulo de análisis de costes muy útil. Conociendo los detalles de la producción prevista, el coste de los recursos necesarios y otros datos relacionados, se ha introducido un método numérico que proporciona una comparación entre coste de usar un molde estándar o un Hipermolde.
Todo lo relacionado con la reducción del tiempo de ciclo se traduce en el coste por pieza producida. El módulo incorporado tiene también un algoritmo interno de razonamiento basado en casos que ayuda a afinar el número estimado con respecto a los valores reales a partir de experiencias previas.
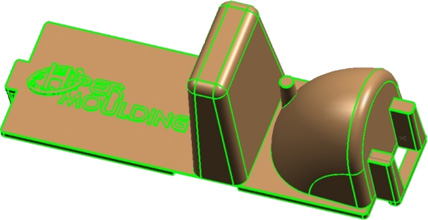
Casos experimentales de validación
Con el fin de comprobar y validar la funcionalidad de los Hipermoldes se han llevado a cabo cuatro experiencias industriales y una geometría patrón de prueba. Las figuras 2, 3, 4, 5 y 6 muestran cada una de las piezas plásticas utilizadas en esta etapa de validación. Cada ilustración muestra también la refrigeración conformable diseñada con el software Hipermoulding.
El método seguido para la comprobación del correcto funcionamiento del software ha sido el mismo en todos los casos:
- Recopilación de la información necesaria de partida: archivos 3D, requisitos de producción, material de la pieza, índices de costes, ...
- Diseño automático de los canales de refrigeración.
- Selección de la tecnología de fabricación basada en capas para los insertos.
- Estimación del tiempo de ciclo.
- Estimación de costes.
- Comparativa con otras distribuciones de la refrigeración y métodos de fabricación para analizar la variación de costes. Selección de la solución.
- Exportación de los dibujos de los canales de refrigeración al modelo CAD estándar con objeto de editar si es necesario y generar los insertos 3D finales.
- Fabricación de los insertos con la tecnología seleccionada.
- Acabado de los insertos siguiendo las estrategias propuestas.
- Montaje y ajuste de los insertos en los molde industriales.
- Fijación de los parámetros de producción.
- Producción industrial de piezas, con recogida de parámetros reales.
- Comprobación de la calidad de las piezas obtenidas, incluyendo la precisión en las dimensiones y la caracterización de materiales.
- Análisis de los resultados obtenidos y comparación con los valores proporcionados por el módulo Hipermoulding.
Se ha de tener en cuenta que todo este proceso ha sido realizado por técnicos industriales para validar la funcionalidad en condiciones de producción real. Los resultados de cada experiencia se exponen a continuación.

Contenedor para lentes ópticas
En este caso, el interés de disponer de un canal de refrigeración conformable es el de tener una refrigeración homogénea de la zona de nervaduras interiores de la pieza. El material plástico es PP. El molde industrial se obtuvo con un tiempo de ciclo de 27,2 segundos. El módulo Hipermoulding simuló un nuevo canal de refrigeración con un tiempo de ciclo de 17,67 segundos, mientras que en el obtenido realmente ha sido 17,9 segundos. Por lo tanto, la reducción del tiempo de ciclo ha sido de aproximadamente de un 34%. Sólo se refrigeró el punzón.
La caracterización de la pieza obtenida ha mostrado una mejor estructura de las cadenas de polímeros debido a que la velocidad de refrigeración ha sido más alta. Por otra parte, han desaparecido las deformaciones en las nervaduras internas sin cambio en las dimensiones.
La estimación de los costes indica que puede obtenerse un beneficio total de 8.500 debido a la importante reducción del tiempo de ciclo.
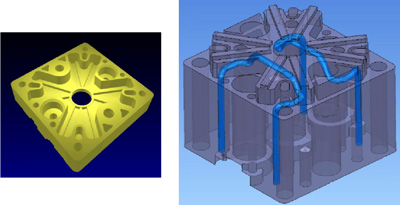
Cubierta de interruptor para zócalos eléctricos
La reducción del tiempo de ciclo para esta pieza de PA6 reforzado con fibra de vidrio ha sido de aproximadamente 31% utilizando canales de refrigeración de geometría libre tanto para el núcleo como para la cavidad. Para este caso, el tiempo de ciclo simulado era de 17,92 segundos y el real era de 22,4, lo que muestra una desviación importante. No se observó un mal resultado en la caracterización ni en el control dimensional de los moldeos.
Soporte TS para automoción
Esta es una pieza técnica realizada con PA6 que tiene profundidades internas difíciles de refrigerar debido a que la refrigeración debe estar en el lado inyección. La reducción del tiempo de ciclo ha sido del 15%. Pero en este caso, el resultado importante es que la diferencia entre el tiempo simulado y el tiempo real obtenido es sólo de unas décimas de segundo.
En este caso, la realización del inserto y su acabado es, de nuevo, más caro que el convencional. Sin embargo, los ahorros en tiempo y el aumento de la calidad de la pieza son suficientemente importantes para que finalmente se utilice el Hipermolde en lugar del molde convencional.
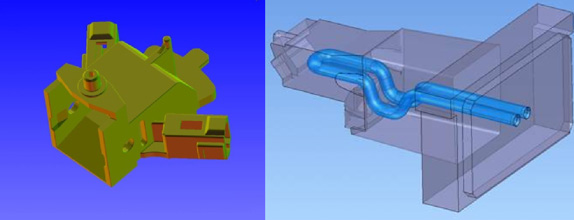
Tapón para envase de bebidas
El packaging es uno de los mercados más importantes de inyección de plástico. Por consiguiente, en este caso el objetivo era mostrar cómo una reducción del tiempo de ciclo se traduce en un ahorro de coste en la producción. Esta pieza en HDPE se inyecta normalmente en un molde de 8 cavidades, pero para la validación se ha utilizado un molde de una única cavidad, pero también con condiciones y ciclos industriales. El tiempo de ciclo convencional es de 38 segundos y el tiempo de ciclo de Hipermolde ha sido de 32 segundos. El tiempo de ciclo simulado ha sido de 18,97 segundos. La gran diferencia entre el tiempo simulado y el tiempo de ciclo real es debida a que la limitación del tiempo de ciclo viene determinada por la cara interna de la pieza, que no se ha refrigerado ni en el útil convencional ni en el Hipermolde.
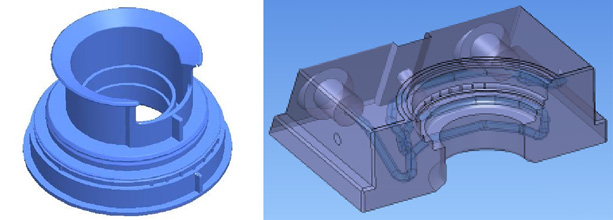
Conclusiones
Después de un proyecto de investigación de 3 años, se ha desarrollado y validado un software para ayudar a los moldistas de inyección de plástico a decidir en que casos de producción la solución de un canal de refrigeración con geometría libre es mejor que los métodos convencionales. El software Hipermoulding proporciona en un corto tiempo la comparación media de tiempos de ciclo y análisis de coste. Además, si se elige el Hipermolde, el módulo diseña automáticamente el canal de refrigeración conformable que puede exportarse en un archivo CAD editable para ayudar al diseñador y al fabricante del molde a su realización. Finalmente, el módulo proporciona instrucciones para el acabado de los insertos realizados mediante el proceso basado en capas con el objeto de aumentar la calidad de la superficie del inserto, lo que significa un aumento de la vida del útil.
Con respecto a la estimación del tiempo de ciclo:
- Los valores previstos son precisos en comparación con los valores reales obtenidos. Esto certifica la suposición de utilizar las condiciones ideales de intercambio térmico, es decir, los canales de refrigeración con geometría libre son realmente útiles.
- Si la refrigeración conformada es baja, la reducción de tiempo puede variar considerablemente.
- Con respecto a la estimación de coste:
- El coste de los insertos fabricados por capas ha de actualizarse a medida que estas técnicas sean más utilizadas en el mercado.
- El software proporciona información correcta y rápida para decidir el uso o
- no de circuitos de refrigeración con geometría variable.
- El usuario siempre puede introducir otro valor según su propia experiencia, que es especialmente buena para la estimación del tiempo de ciclo.
Con respecto al diseño:
- Los canales de refrigeración propuestos han mostrado un comportamiento muy bueno en lo que respecta a la velocidad de refrigeración de los moldes.
- La integración con otro software utilizado habitualmente, por ejemplo CAD/FEM, es buena.
- Con respecto a la inyección:
- La calidad de las piezas inyectadas es la misma para ambos tipos de refrigeración.
- El desgaste de los insertos es totalmente similar en los materiales usados.
- La reducción del tiempo de ciclo es en la mayoría de casos superior al 35%. Cuando la refrigeración está en las correderas, este porcentaje se reduce ya que la zona refrigerada no es la dominante del ciclo.
- Los costes de fabricación de los insertos por capas se han de reducir para extender el uso de los canales de refrigeración con geometría libre a otras aplicaciones.