(parte 3) - Resultados y evaluación
INYECCIÓN
Resultados
Cabe señalar que la obtención de la magnitud de esas fuerzas no es caso de estudio en este trabajo, ya que conocidas las condiciones de frontera de las fuerzas en la pieza, sabemos que los esfuerzos siempre estarán localizados en las mismas regiones, en mayor o en menor magnitud, pero su localización no cambiará de posición, y será precisamente en esas regiones donde se debe procurar no tener líneas de soldadura. La resina que se elija debe cumplir con las propiedades mecánicas, eléctricas, ambientales y térmicas para que la pieza no sufra alteraciones a corto o a largo plazo. La selección adecuada de la resina es el primer requisito para que la pieza sea segura y duradera. En el caso de la pieza en estudio se requiere que cumpla con dos características importantes: un material resistente a la tensión y un valor adecuado de elongación antes de la ruptura de acuerdo a los cálculos realizados. La resina seleccionada para la pieza en cuestión fue LATAMID 66 H2 G/25-V0KB1 cuya resistencia a la tensión es de 21800 psi, con 3% de elongación antes de la ruptura y densidad de 1.36 g/cm3. Éste es un material compuesto por PA 66 (Nylon 66), para procesos con velocidad media de inyección, 25% de fibra de vidrio, que cumple con la norma de UL94 V-0 para retardar la flama, y tiene excelentes propiedades eléctricas.
Análisis de esfuerzos y de flujo
Evaluación
Paso 2. Simetría en el punto de inyección (empaquetamiento). Al realizar las primeras simulaciones de flujo colocando el punto de inyección dentro de las zonas recomendadas por el software, no se cumplía con la condición de llenar todas las zonas más alejadas al punto en al menos un 95%, debido a la ranura en el centro de la pieza donde se estaba colocando el punto de inyección. Utilizando dos puntos de inyección se logró satisfacer el criterio del 97% de uniformidad.
Paso 3. Presión en la cavidad. Al utilizar dos puntos de inyección también se logró disminuir la presión y cumplir con el criterio de ser menor a 5, 000 psi. La figura 3 muestra la ubicación de los puntos de inyección que cumple con los primeros tres criterios de la metodología: estética de la pieza, simetría en el punto de inyección (empaquetamiento), y presión en la cavidad.
Paso 4. Comparación de regiones comunes entre líneas de soldadura y áreas de concentración de esfuerzos. Se realizaron una serie de simulaciones de flujo para poder obtener las mejores condiciones de proceso. Por las características de la pieza es normal que se presenten líneas de soldadura durante el proceso de inyección. Sin embargo se puede cambiar su posición en la pieza variando los parámetros del proceso, y así provocar que el menor número de líneas de soldadura se localice en las regiones críticas de concentración de esfuerzos. Las condiciones que se variaron para las simulaciones de flujo en el proceso de inyección fueron: temperatura del molde (Tmol), temperatura de fundición del material (Tfun), y la presión de inyección (Piny). En las simulaciones, siempre se mantuvieron constantes el material (el índice de flujo del material no cambia), la localización de los puntos de inyección, las dimensiones y la geometría de la pieza. El tiempo de llenado de la cavidad y el tiempo de ciclo de inyección fueron directamente calculados por el software. El fabricante del material recomienda rangos entre los cuales se debe realizar los procesos de inyección y en base a éstos se llevaron a cabo un total de 27 simulaciones, de acuerdo con los siguientes parámetros:
Tmolde (ºF) 158 176 194
T fund (ºF) 500 518 536
Presión (psi) 7.252 14.504 21.756
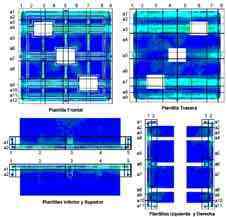

La primer simulación de flujo se realizó con los valores normales (ddd). Los resultados de esta simulación se muestran en la figura 3. El resultado del índice Fcels fue 27.1, que al concluir las 27 simulaciones resulto el segundo valor más alto. Esto indica que no siempre los valores normales recomendados por el fabricante y el software para el proceso de inyección resultan los más apropiados al considerar la concentración de esfuerzos y las líneas de soldadura. La figura 4 también muestra los resultados con el menor factor Fcels (combinación 1dd). La figura 4 muestra el resultado de todas las simulaciones que se realizaron para obtener los valores de Fcels con diferentes condiciones de proceso. El valor más alto fue 27.4 bajo las condiciones de proceso dd1, mientras el valor más bajo registrado para Fcels fue de 18.9 y se presenta en cuatro condiciones de proceso: 1d1, 1dd, 1d5 y d15.
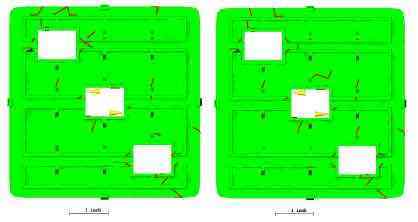
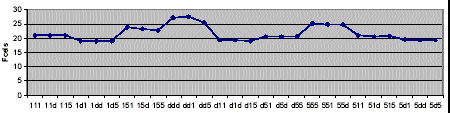
La figura 5 muestra los resultados de las variables de proceso para las diferentes combinaciones de condiciones de proceso. Se incluye también el análisis del factor de concentración de esfuerzos vs. líneas de soldadura (Fcels) e índice normalizado (definido como el valor Fcels de cada combinación / el valor máximo de Fcels obtenido de todas las combinaciones) para las 27 simulaciones de flujo. De acuerdo a la figura 7 existen cuatro condiciones de proceso 1d1, 1dd, 1d5 y d15 en las que el valor de Fcels fue igual a 18.9, que resulta ser el mínimo de todas las simulaciones. Como se establece en la metodología, en
caso de existir varios procesos con el mismo valor de Fcels, se debe considerar el proceso con el menor tiempo de ciclo, con lo que la combinación d15 queda automáticamente descartado por tener un mayor tiempo de ciclo (15.75 s). Las otras tres simulaciones (1d1, 1d5, 1dd), tienen el mismo tiempo de ciclo (15.69 s) y cualquiera de ellas puede ser elegida como la condición de proceso que más beneficia al moldeo de la pieza tomando en cuenta su funcionalidad para evitar el mayor número de líneas de soldadura en regiones críticas de concentración de esfuerzos. La alternativa 1d1 implica el uso de menor presión y por lo tanto menos energía y menor costo. Sin embargo, la condición 1dd sería la más recomendable ya que mantiene dos de sus variables de proceso en el rango normal determinado por el fabricante del material para obtener un proceso estable, la temperatura de fundición del material (Tfun) = 518 ºF y la Presión de inyección (Piny) = 14503.8 psi. Solamente para la temperatura del molde (Tmol) se utilizó el valor mínimo del rango de temperatura recomendada de 158 ºF con lo que el proceso de inyección sería más estable al compararlo con los procesos 1d1 y 1d5 que varían en su presión de inyección. Para obtener mayor calidad en las piezas, las condiciones de proceso deben mantenerse lo más cercano posible a las recomendadas por el fabricante del material elegido.
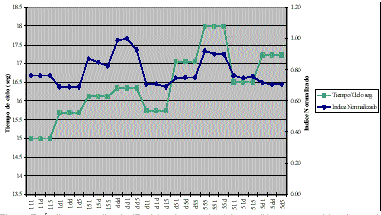
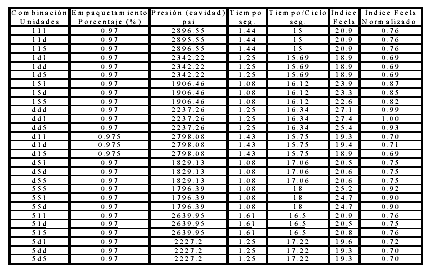