Estudio de Compensación de presión de inyección
José Ramón Lerma, dpto. técnico de Biesterfeld Ibérica
13/03/2019Este estudio nos informa de la capacidad de la inyectora de mantener el tiempo de llenado, es decir la velocidad de inyección con diferentes niveles de esfuerzo o carga o lo que es lo mismo con diferentes niveles de viscosidad del material debidos por ejemplo a diferentes lotes de material prima, a diferentes porcentajes de material recuperado, cambios de color o de masterbach, cambios de temperatura de masa, diferentes temperaturas de molde, etc.
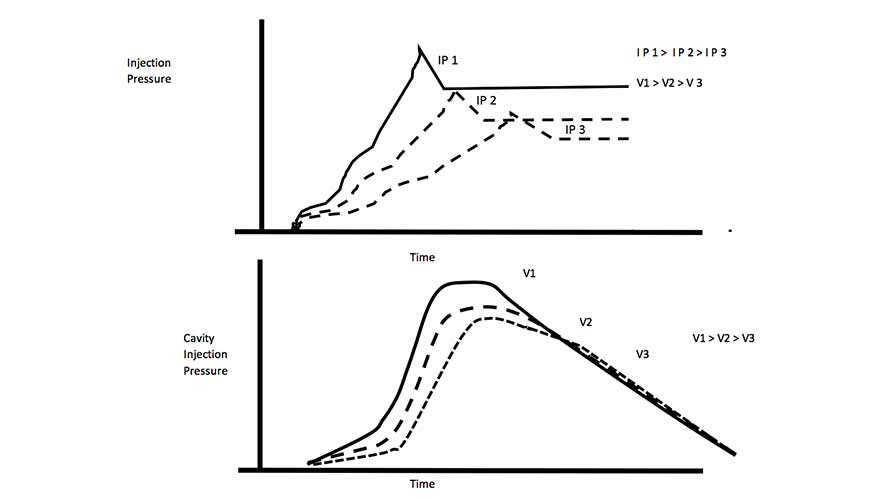
Este estudio nos ayuda a valorar el estado de la máquina inyectora desde el punto de vista de cómo realiza la maquina la compensación de la presión de inyección en función de la resistencia que ofrece el material a fluir. Comparamos con este estudio los valores de presión de inyección necesaria para llenar hasta el punto de conmutación y el tiempo de inyección hasta el punto de conmutación, es decir lo que se denomina la carrera dinámica de llenado, en dos condiciones:
- Condición de llenado del molde
- Condición de llenado en vacío
Con estos valores calculamos el porcentaje de compensación que realiza la inyectora por cada 100 bares necesarios.
Configuración de la máquina de inyectar para realizar el Estudio de Compensación de Presión
- Programar la inyectora para inyectar conmutando por carrera.
- Programar la velocidad de inyección obtenida en el ensayo de viscosidad relativa o 'in mold rheology'.
- Punto de conmutación habitual durante la fabricación.
- Asegurar suficiente presión de inyección y delta P, no limitar el proceso de inyección.
- Bajar la postpresión para asegurar que fabricamos piezas rechupadas o incluso ligeramente cortas.
- Programar el tiempo de postpresión mínimo o dejarlo a cero. En este ensayo no estamos interesados en la fase de compactación, tan solo la fase de llenado es la que vamos a analizar.
- Arrancar la inyectora y retocar punto de conmutación para obtener piezas al 90-98 % del llenado.
- Registrar el tiempo de llenado y la presión de llenado en este punto. Aquí tendremos los valores de 'Presión de Inyección PK1' y 'Tiempo de inyección FT 1'.
Para cumplir con la velocidad de inyección programada y repetir el tiempo de inyección (tiempo más crítico del proceso), la inyectora debe utilizar la presión de inyección necesaria en cada ciclo de inyección. Dependiendo por ejemplo de la viscosidad del material utilizado, temperaturas de molde y de masa, etc. esta presión puede variar debido a que la inyectora realiza esta llamada "compensación de la presión de inyección" automáticamente.
La capacidad de auto-compensar estas diferencias de presión es una característica importante de la inyectora y debe ser controlada ya que nos diferenciará qué inyectoras son precisas de las que no lo son.
En el ensayo se buscan dos condiciones en dos extremos, una con el polímero fundido en condiciones de trabajo habituales ya comentada y la otra inyectando en vacío sin material. Se puede realizar también el test con material fundido en dos o tres diferentes velocidades y también con el material a diferentes temperaturas de masa.
Esta condición de inyección en vacío es a menudo complicada de efectuar a través de una eyección o purga de material ya que actualmente las máquinas trabajan en modo seguro con baja presión y baja velocidad cuando están en modo manual y no es posible reproducir las condiciones de inyección de modo automático cuando estamos en modo manual.
Por ello, para esta inyección en vacío, sin material, podemos utilizar la succión antes de la dosificación de la unidad de inyección equivalente a la dosis requerida para conseguir que el husillo llegue a la posición de “dosis alcanzada” y poder realizar un ciclo de inyección sin material en la zona delantera del husillo, es decir, “en vacío”, ya que la inyectora desplazará el husillo hacia atrás sin hacerlo girar hasta la cota o posición deseada y por tanto no se producirá una dosificación de material.
Realizaremos un ciclo automático o semiautomático registrando los valores de presión de inyección alcanzada y tiempo de inyección para esta condición. Aquí tendremos los valores de 'Presión de Inyección PK 2' y 'Tiempo de inyección FT2 2'. El tiempo de inyección debería ser el mismo que en el ensayo con material dosificado, es decir 'FT2=F T1', lo que debe haber cambiado es la presión necesaria para realizar la inyectada que en el caso de PK2 debería ser mucho menor.
Para conocer esta función de compensación en nuestra inyectora tenemos que realizar este cálculo en el 'Estudio de Compensación'. En estos cálculos se tienen en cuenta los valores comentados de presión y tiempo de inyección en condiciones de carga normales (PK1 y FT1) y los valores de presión y tiempo sin carga (PK2 y FT2).
Obteniendo con este cálculo un porcentaje que nos indica la capacidad de la inyectora de compensar la presión de inyección con diferentes niveles de carga con el objetivo de cumplir siempre con el tiempo de inyección establecido por el inyectador.
Valores en los resultados de más de 5% no son aceptables, debe revisarse la calibración de la inyectora. Valores cercanos a cero o ligeramente negativos son aceptables.
Realizar este ensayo con tres diferentes velocidades de inyección, lenta, media y rápida.
Si una máquina pasa el test con las tres velocidades quiere decir que es fiable.
Hoja de Estudio de Compensación de la Presión de Inyección en la inyectora
En esta hoja de cálculo, entrando los datos de las celdas en verde podemos calcular el porcentaje de compensación de la presión de inyección por cada 100 bares.
Los valores de presión y de tiempo tanto en vacío como con carga a introducir en la hoja de cálculo pueden ser el resultado de una media de al menos 10 inyectadas, esto hará más fiable el estudio.
Los valores resultantes del ratio de compensación se interpretan como sigue:
Valores
- Hasta 5%: correcto, máquina con buena precisión, auto compensación correcta
- Entre 5 y 10%: correcto para inyección sin exigencias de estrechas tolerancias, necesario revisar
- Mas del 10%: no hay precisión ni repetibilidad, revisar unidad de inyección, alta variabilidad.
Otros ensayos o test para la compensación de la inyectora
Se puede forzar el cambio de viscosidad y por tanto de carga en la inyectora de modo intencionado para conocer la reacción y la fiabilidad de la máquina.
Por ejemplo, para modificar la viscosidad del material fundido podemos realizar un paro prolongado de la inyectora y arrancar. Podemos determinar en cuántas inyectadas la inyectora vuelve a los valores normales de presión y tiempo de llenado y podremos observar cómo la inyectora se autorregula y se auto compensa al disminuir la viscosidad del material por efecto del tiempo de permanencia.
Observaremos en este caso cómo la presión de inyección en los primeros ciclos después del arranque es menor que la habitual y que poco a poco la inyectora recupera los valores de presión de inyección habituales.
Podemos del mismo modo realizar un cambio de temperaturas importante, por ejemplo, reducir la temperatura de la masa para incrementar la viscosidad del plástico fundido y observar la reacción de la máquina de inyección y ver cómo se auto compensa la presión para mantener el tiempo de inyección. Esto nos asegurará la reacción de la máquina ante cambios de lote, de porcentaje de recuperado, de tipo de masterbach de color, etc.
En resumen, no demos por hecho que nuestra inyectora es fiable sin realizar las comprobaciones necesarias de modo frecuencial. Si nuestra inyectora no se auto compensa correctamente no podrá cumplir siempre con el tiempo de llenado o velocidades de inyección, obteniendo en cada caso piezas diferentes y teniendo un proceso con alta variabilidad, que es justo lo contrario de lo que el Scientific Injection Molding persigue.
Dedicar un poco de tiempo a hacer algunas comprobaciones básicas nos ahorrará mucho tiempo en retoques de parámetros, rechazos, selecciones, etc.
“La inyección en vacío es a menudo complicada de efectuar a través de una eyección o purga de material ya que actualmente las máquinas trabajan en modo seguro con baja presión y baja velocidad cuando están en modo manual”
José Ramón Lerma es autor del Libro Manual Avanzado de Inyección de Termoplástico, que tiene como objetivo ser, por un lado, una herramienta para la formación y, por otro, un manual de ayuda para todo el personal de una empresa de inyección de plásticos. El libro, comercializado por Plásticos Universales / Interempresas (libros@interempresas.net), consta de detallados casos prácticos, amplia información de moldeo científico y un ‘pendrive’ con 20 hojas de cálculo y herramientas de SC Molding o Scientific Injection Molding, además de optimización y definición de proceso, lo que lo hacen único en el mercado. Página web sobre Scientific Injection Molding: www.asimm.es
Más información sobre los cursos Scientific Molding online impartidos en Inefco, en los que José Ramón Lerma es tutor https://tienda.novaagoraformacion.com/home/62-procesos-avanzados-de-inyeccion-de-termoplasticos.html