Materiales para motores diésel ecológicos
Dr. Wolfgang Sauerer, responsable de Markéting Tecnológico de Ultraform en Basf AG, Alemania
Dr. Tilman Reiner, Director de Control de Calidad y Asistencia de Producto en la Unidad de Negocios de adhesivos y resinas de impregnación de Basf AG, Alemania
17/04/2008Los motores de combustión interna se ven obligados a trabajar en condiciones normativas cada vez más estrictas, trátese ya de los estándares LEV II del Estado de California o las regulaciones Euro 5 sobre gases de escape, aun pendientes de aprobación; ello supone un reto que obliga a la industria a continuar innovando. En pocas palabras: la labor del ingeniero, en estas circunstancias, consiste en reducir el consumo de carburante de los motores de gasolina hasta el nivel característico de los diésel, haciendo a estos al mismo tiempo tan limpios como sus homólogos de gasolina.
Límites y estándares de emisión de gases
Los motores diésel se hallan en el epicentro de un vasto movimiento de actividades de desarrollo industrial, debido a que sus emisiones características de partículas de carbón (polvo fino) y óxidos de nitrógeno (Nox) han intensificado el debate público forzando al legislador a establecer requerimientos más estrictos. Por ejemplo, los límites máximos permitidos de emisión para vehículos diésel de menos de 3 toneladas y media, bajo la actual normativa Euro 4 sobre gases de escape, son de 0,025 g/km para las partículas de polvo y 0,25 g/km para los óxidos de nitrógeno. El standard Euro 5, que habrá de entrar en vigor en septiembre de 2009, establecerá límites aun más bajos para los vehículos de la clase mencionada. Respecto a las emisiones de óxidos de nitrógeno se ha acordado una reducción por encima de un 20 por ciento hasta 0,18 g/km. Las emisiones de partículas caerán hasta solo 0,005 g/km, según lo propuesto también por el borrador americano LEV II. Esto representa una reducción del 80 por ciento en comparación con los estándares Euro 4. En relación con los vehículos de transporte pesados, en los cuales la emisión se mide en la unidad g/kWh, el standard Euro 4 especifica un límite de 3,5 g/kWh para la emisión de óxidos de nitrógeno. Bajo la normativa del Euro 5, el límite habrá de descender hasta los 2,0 g/kWh. La tecnología actual no permite alcanzar unos límites tan ambiciosos. Para tal fin será necesaria una combinación de innovaciones en diferentes campos como la gestión del calor, las tecnologías de combustión, los turbocompresores, recirculación de gases de escape y tratamiento catalítico de emisiones.
Cómo reducir los óxidos de nitrógeno en el escape
Las emisiones de partículas sólidas de los motores diésel se reducen mediante filtros; por otro lado, los fabricantes del automóvil recurren al nuevo proceso SCR (reducción catalítica selectiva) basado en AdBlue para hacer frente al problema de los óxidos de nitrógeno. AdBlue es una solución de urea ultrapura en medio acuoso, incluida en un depósito aparte, que actúa como agente reductor. AdBlue se inyecta a alta presión a través de una válvula dosimétrica en el flujo de gases de escape previamente limpiado. El calor del escape lo descompone en amoníaco y a continuación pasa a un convertidor catalítico que transforma los nocivos Nox en nitrógeno y vapor de agua inofensivos. Como líder en producción de urea industrial, AdBlue no podía faltar en la gama de oferta de BASF AG.
Daimler Chrysler fue el primer fabricante del automóvil en ofrecer un sistema de purificación de escapes SCR, al introducir Bluetec a comienzos de 2005 para todos los vehículos industriales con un peso total superior a las 6 toneladas. Según informa la propia empresa, ya hay más de 20.000 vehículos equipados con esta tecnología y cumpliendo los estándares Euro 5. Scania, Man, Daf, Iveco, Renault y otros constructores de camiones utilizan asimismo la tecnología SRC basada en AdBlue. El empleo de la tecnología de urea en los automóviles es inminente. De acuerdo con un anuncio del grupo Mercedes Benz, el E 320 será el primer turismo fabricado en serie que vaya provisto de Bluetec. Inicialmente disponible en América del Norte, el automóvil Bluetec también llegará al mercado europeo en 2008. Hasta ese momento los únicos vehículos que cargan AdBlue lo hacen en los talleres de mantenimiento de autobuses y camiones. Para los requisitos del futuro tendrá que desplegarse una red de estaciones de llenado.
Materiales y aplicaciones
Los materiales plásticos demuestran su superioridad también en los sistemas SCR basados en AdBlue: moldeabilidad sin límite de forma, ligereza y bajo coste específico para grandes series. La utilización de metales y cristal típicos resulta contraindicada debido a su escasa resistencia al AdBlue o bien al riesgo de contaminación de AdBlue en contacto directo con la solución de urea. Estos metales incluyen el cobre y las aleaciones a base del mismo, asi como el cinc, el hierro, aceros sin alear y galvanizados, y también aluminio y aleaciones.
Muchos de los numerosos dispositivos y depósitos a bordo de un vehículo que entran en contacto directo con AdBlue pueden fabricarse en plástico:
■ tanques de almacenamiento junto con sus tapones,
■ artefactos para ventilación,
■ dispositivos de medición de nivel,
■ aparatos de alimentación, bombas para AdBlue o aire comprimido,
■ tuberías y manguitos,
■ conectores eléctricos y de manguitos, uniones para carcasas,
■ filtros,
■ válvulas
■ elementos de sujeción.
También hay aplicaciones similares destinadas a la infraestructura de suministros, por ejemplo, las estaciones para repostar y los surtidores de carburante. Mientras las poleolefinas resultan de gran utilidad para depósitos y tanques, los plásticos de ingeniería como los copolímeros de polioximetileno (POM), la poliamida (especialmente PA 66) y los poliésteres como tereftalato de polietileno (PBT) se utilizan preferentemente para las aplicaciones más extremas, debido a su capacidad de satisfacer los requisitos sobre resistencia química.
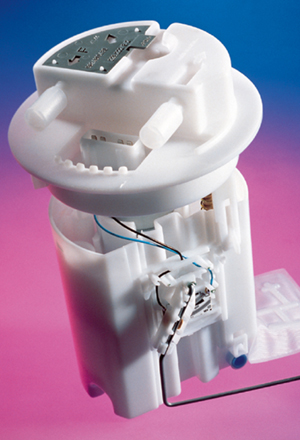
Plástico en contacto con la urea
¿Cuánto resiste el plástico en el contacto permanente con AdBlue? La urea es un compuesto orgánico polar, cuyas soluciones acuosas resultan ligeramente alcalinas. Una solución recientemente constituída presenta un pH entre 9,0 y 9,5, que puede incrementarse hasta 10 después de un período de almacenamiento. Los posibles efectos de esta propiedad sobre el comportamiento de los materiales plásticos deben ser objeto de estudio y de la debida consideración. Los mencionados estudios deberán de tener en cuenta la interacción de la urea tanto con la matriz del polímero como con los aditivos del mismo, así como cargas y materiales de refuerzo que pudieran hallarse presentes. Por otro lado también es importante asegurar que el rendimiento del sistema SCR no se vea afectado por la utilización del plástico. Ninguno de los componentes críticos debe pasar del material al AdBlue por arrastre. Lo propio se aplica a los productos resultantes de la reacción a largo plazo entre el plástico y sus partes constitutivas y AdBlue. Los requerimientos son altos: AdBlue admite contenidos máximos de 0,5 ppm en hierro, calcio, magnesio, sodio y potasio, y los límites permitidos para inhibidores de catálisis como cobre, cinc, cromo y níquel, particularmente aborrecidos por el ingeniero, se encuentran en torno a 0,2 ppm (a modo ilustrativo, 0,1 ppm supone 0,1 gramos en una tonelada).
Un estudio del comportamiento a largo plazo
Puesto que AdBlue es todavía un sistema reciente no se dispone aun de experiencia amplia en relación con el comportamiento a largo plazo de los materiales en contacto con la solución de urea. Por experiencia a largo plazo entiéndase en este caso la vida útil de un vehículo, de unos diez años (o 1 millón de kilómetros) para camiones y 15 años (o alrededor de 300.000 kilómetros) en un utilitario. Existe la necesidad de un modelo adecuado de ensayo comprimido de tiempo que pudiera aportar de manera rápida informaciones útiles sobre el comportamiento del plástico en el contacto permanente con AdBlue. Como posibles métodos para lograr esta aceleración se ha propuesto elevar la concentración de AdBlue, aumentar la superficie del material en contacto con AdBlue o inmersión a alta temperatura. Los tests acelerados actualmente disponibles en el mercado se basan en una combinación de los dos últimos procedimientos. Debido a su alto interés práctico, el proceso descrito a continuación es digno de ser detallado de manera especial. Se sumergen en AdBlue a +60 °C en botellas selladas de cuello ancho barras de tracción de 4 mm de espesor del tipo 1-A conforme a ISO 527, elaboradas con polipropileno o polietileno transparente. Lo habitual es, por ejemplo, sumergir cinco barras para ensayos de tracción en 1 kg de AdBlue durante un período de cuatro semanas. Es muy importante asegurar que la serie de ensayo utilice únicamente botellas procedentes del mismo lote de fabricación. Antes del ensayo hay que lavar las botellas una vez con agua destilada y dos veces con AdBlue. El almacenamiento paralelo de AdBlue sin añadir especímenes de ensayo resulta obligado al efecto de determinar valores en vacío, es decir, los cambios endógenos en la propia solución de urea, para tener este dato en su debida consideración a la hora de realizar el informe de ensayo. Los ensayos a temperaturas superiores a +60 °C proporcionan resultados poco fiables, ya que por encima de ese límite la urea comienza a descomponerse con rapidez en amoníaco y dióxido de carbono. Además por encima de +70 °C se forma biuret –un dímero de la urea-. Como resultado de los mencionados análisis se analiza la composición de AdBlue según DIN 70070 y DIN 70071. Los especímenes de los diferentes materiales deberán ser sometidos a los oportunos ensayos de propiedades mecánicas, por ejemplo test de tracción conforme a ISO 527. La experiencia obtenida hasta la fecha muestra que el resultado de dicho ensayo reproduce los efectos de un contacto entre plástico y solución AdBlue a lo largo de un año. Se trata de una aproximación equivalente al llenado del tanque AdBlue en un turismo diésel. Para simular períodos de mayor duración sería preciso incrementar los tiempos de ensayo o desarrollar otros tests acelerados.
El resultado: prácticamente ningún cambio
En el vigente borrador ISO 22241-3 se recomiendan algunos tipos de polímero como particularmente idoneos para el contacto con AdBlue. De acuerdo con esta norma, y al no incluir aditivos de ningún tipo, dichos plásticos no dan lugar a una contaminación apreciable del AdBlue. Los plásticos recomendados son: polietileno, polipropileno, poliisobutileno, perfluoroalcoxi (PFA), polifluoroetileno, fluoruro de polivinilideno, politetrafluoroetileno, los copolímeros de fluoruro de vinilideno y hexafluoropropileno. Esta lista no es exhaustiva, y tampoco se pueden excluir cambios en las propiedades de los materiales recomendados; por consiguiente los productos comerciales concretos deberán ser asimismo sometidos a ensayo por separado.
La idoneidad de algunos materiales de ingeniería aun no incluidos en el actual borrador de la ISO 22241-3 es objeto de descripción en lo que sigue. Los materiales seleccionados pertenecen a la gama comercial de BASF en las clases que se mencionan:
■ POM sin reforzar: Ultraform N2320 003 y Ultraform N2320 003 LEV, un material de emisiones optimizadas (LEV = Low Emission Version).
■ PA sin reforzar: Ultramid A4K AB, un PA 66 optimizado para AdBlue.
■ PBT reforzado con fibra de vidrio: Ultradur B4300 G4 con un 20% de fibra de vidrio.
Las barras del tipo 1-A para ensayos de tracción conforme a ISO 527 elaboradas a partir de los materiales anteriormente mencionados fueron sumergidas en solución AdBlue a +60 °C durante un total de tres períodos de tiempo de cuatro semanas de duración cada uno. A causa del significativo efecto del agua en las características mecánicas de las poliamidas, las referencias Ultramid fueron sumergidas en agua caliente (+60 °C) para un ensayo de control.
Como muestran las figuras 2-4, las propiedades mecánicas de Ultraform y Ultradur no experimentaron apenas variación durante el período de tiempo considerado. En el caso de Ultramid A4K AB, los cambios producidos son los típicamente esperados tras una inmersión del mismo tiempo en agua pura. A temperatura ambiente la PA 66 absorbe hasta un 9% de agua, mientras que esta cantidad no llega al 1% para el POM y el PBT. En virtud de esa absorción de agua la PA 66 experimenta una disminución significativa de rigidez y resistencia, acompañadas de un incremento de alargamiento a la ruptura.
Los análisis de las soluciones AdBlue utilizadas evidencian asimismo que las especificaciones para el cobre, cinc, cromo, níquel, calcio, hierro, aluminio, magnesio, sodio, potasio y fosfatos, son cumplidas con fiabilidad por todos los materiales verificados después de los tres períodos de almacenamiento.
Conclusiones
Los resultados de la inmersión a largo plazo de plásticos de ingeniería POM, PA y PBT en soluciones AdBlue refuerzan que dichos materiales sean utilizados en aplicaciones AdBlue. Este juicio se aplica de manera particular a los termoplásticos de la gama BASF que aquí se estudian. Deberán llevarse a cabo nuevos ensayos con componentes finales para comprobar hasta qué punto los resultados de los tests de aceleración diseñados pueden aplicarse a la práctica industrial en condiciones reales.