La refrigeración en el proceso de moldeo de plásticos por inyección
Objetivo de la torre de refrigeración
Como en todos los casos en los que es necesario disipar el calor producido por las centrales hidráulicas, también aquí se utiliza la torre de refrigeración para el mismo efecto.
En algunos casos, cuando la torre de refrigeración tiene grandes dimensiones y se instala un depósito tampón suficientemente grande, según el tipo de material plástico moldeado y el tamaño de la pieza, es posible utilizarla también para enfriar el molde, lo que conlleva grandes ventajas en forma de ahorro energético.
En cualquier caso, haciendo un cálculo preciso aguas arriba, el uso de la enfriadora puede limitarse a los meses más calurosos o puede ser utilizada como soporte de la torre de evaporación, sólo cuando sea necesario. Ver esquema del sistema:
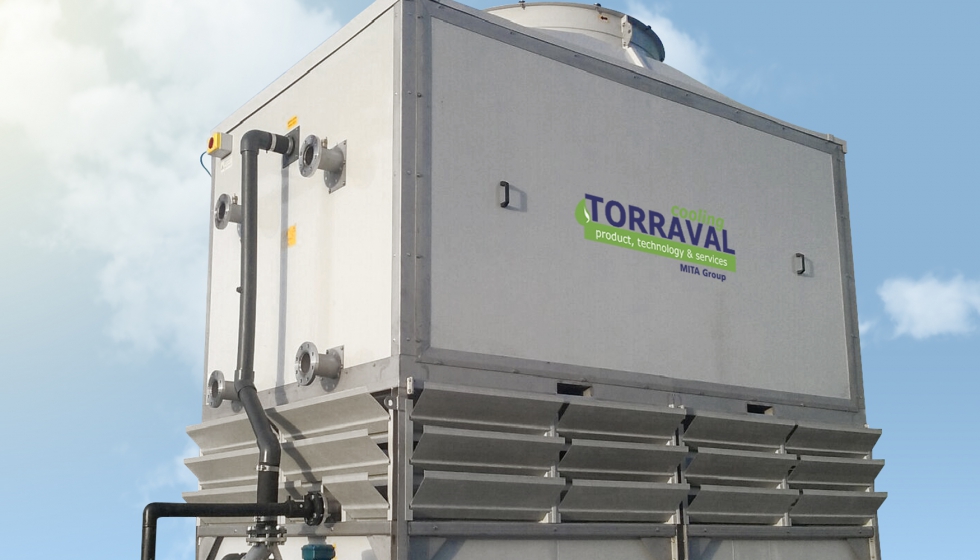
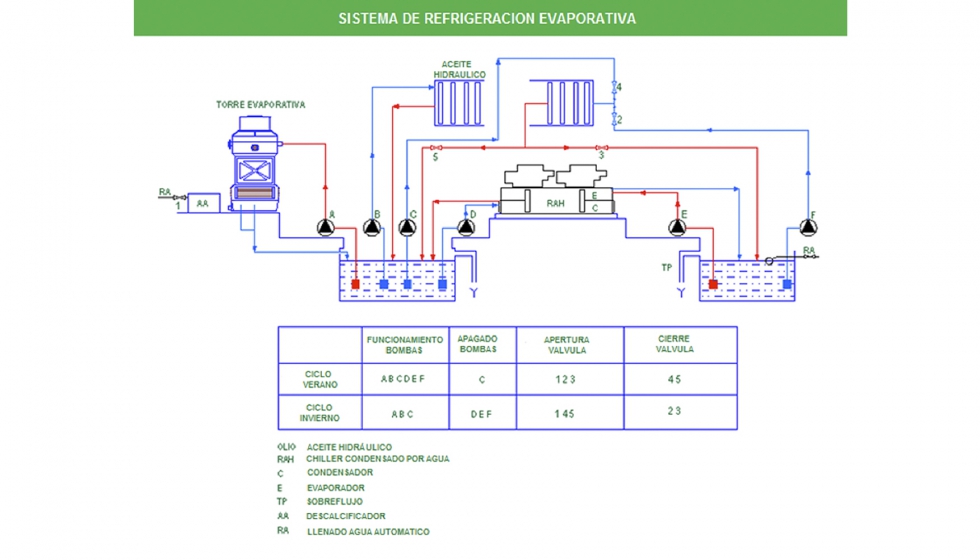
El dimensionamiento de la torre se realiza teniendo en cuenta la potencia instalada en las máquinas de moldeo (bomba de aceite), indicada normalmente en kW.
El circuito hidráulico recomendado es con dos tanques (agua caliente y agua fría), porque los usuarios, generalmente, más de uno, no necesitan operar simultáneamente, y también porque de esta manera es posible dimensionar una torre de refrigeración con mayor capacidad en relación con el circuito de los usuarios en beneficio de la temperatura final del agua fría.
En caso de que sólo sea necesario enfriar las centrales hidráulicas, el salto térmico a considerar en la torre es desde+ 40 oc a + 30 oc, mientras que si también se requiere enfriar los moldes, haría falta considerar la temperatura mínima posible para la zona de instalación y salto térmico adicional de 5 oc.
Ejemplo:
A continuación mostramos una comparativa técnica y económica entre un sistema gestionado con un chiller y el mismo sistema en el cual se instala una torre de refrigeración. Utilizamos de forma gráfica un caso real que se nos ha presentado:
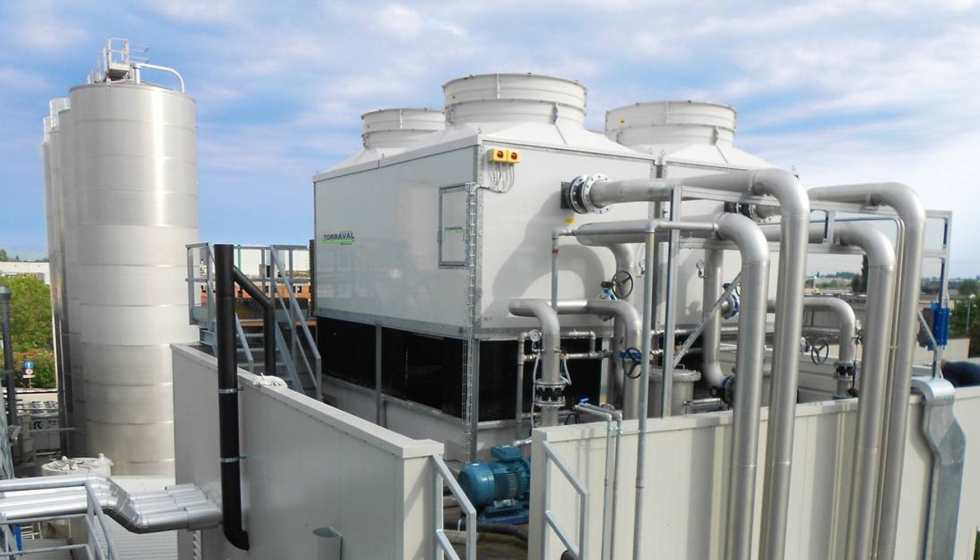
Chiller
Para un total de 223,000 fr/h, consistente en:
- 2 chillers de 44,500 fr/h cada uno, requiriendo 11,9 kW (compresor) + 1,1 kW (bomba) + 2,2 kW (ventiladores para el condensador de aire) por cada chiller.
- 2 chillers 67,500 fr/h cada uno, requiriendo 18 kW (compresor) + 1,5 kW (bomba) + 3,3 kW (ventiladores para el condensador de aire) por cada chiller.
Asumiendo una temperatura media externa de 25 °C, para conseguir agua a 15 °C la energía eléctrica absorbida por los dos chillers es equivalente a 74,6 kW/h.
Torre de refrigeración
Para el mismo caso, con un potencial igual a 225,000 kCal/h, con un motor eléctrico para el ventilador de 4 kW, 2,2 kW de la bomba centrifuga y 5.5 kW de la bomba centrifuga para los usuarios de suministro.
En total la potencia eléctrica utilizada equivale a 11,7 kW/h.
Comparando los dos sistemas, la energía eléctrica consumida por la torre de refrigeración es mucho menor. La diferencia es 74,6- 11,7 = 62,9 kW/h a favor de la torre de refrigeración.
Asumiendo un ciclo de trabajo de 8 horas/día, durante sólo 22 días/mes, 11 meses/año y considerando un coste medio de 0,11 euro por kW/hora, el ahorro anual asciende a nada menos que 13,884€.
Incluso asumiendo los necesarios costes de tratamiento de agua, la diferencia de costes generales de la instalación es aún sumamente favorable a la torre de refrigeración.
Torraval Cooling diseña, fabrica y comercializa torres de refrigeración de alta fiabilidad y rendimiento. Es una empresa orientada al ahorro energético, al respeto por el medio ambiente y en permanente proceso de innovación tecnológica. Así lo constatan los numerosos clientes en los cinco continentes.
Torraval Cooling, fundada en 1967, forma parte del Grupo MITA y en su dilatada y sólida trayectoria ha diseñado y fabricado más de 12.000 torres e intercambiadores de calor en todo el mundo, en diferentes tipos de industrias y aplicaciones, siendo el del plástico uno de los sectores con más presencia en el mercado de la compañía.
Más información: www.torraval.com
info@torraval.com