Factores de influencia importantes durante el proceso de reciclado de plásticos
Gneuss Kunststofftechnik GmbH15/04/2007
Cada uno de estos procesos tiene exigencias particulares acerca de las propiedades del poliéster reciclado, que son próximas a las del material virgen. Aparte del peso molecular (a menudo referido como viscosidad intrínseca - VI), de la viscosidad específica y del color/ transparencia del material, partículas extrañas de contaminación en el fundido (por ejemplo: papel, arena, adhesivo, otros plásticos, entre ellos PP, PVC y otros) tendrán un efecto sobre la calidad del producto.
Las exigencias de más alta calidad de todos, se encuentran en los denominados procesos de reciclado “botella a botella”. En este caso, los procesos solamente son realistas y económicamente viables cuando las botellas usadas se toman de una fuente definida y controlada (por ejemplo, depósito de botellas retornadas).
Si las botellas usadas se recogen de la basura domiciliaria, hay un peligro de contaminación desconocida. Además, se requerirán una clasificación y plantas de lavado sofisticadas que se agregan al costo de la escama de botellas. La calidad de la escama de botellas requerida para diferentes procesos puede definirse como sigue:
- Nivel de calidad I: Botellas para bebidas/alimentos
- Nivel de calidad II: Filamentos técnicos
- Cintas (para packaging)
- POY (Hilado parcialmente orientado)
- Fibra para Spun Bond leviano
- Revestimiento de acero
- Nivel de calidad III: Film plano
- BCF (filamento para alfombra a granel)
- Botellas para productos no comestibles
- BOPET (Film de PET biorientado)
- Nivel de calidad IV: Fibra para Spun Bond pesado
- Fibra corta
- Grupo de calidad V: Plástico de Ingeniería
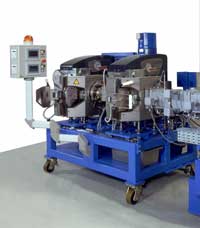
Procesar escamas de botellas de PET directamente en algunos de los productos del listado precedente hace que el proceso de producción sea susceptible de tener dificultades. En este contexto, el filtrado es de especial importancia. El sistema de filtrado debe poder manejar una carga de contaminación cambiante, tiene que funcionar automáticamente, hacer uso eficiente del medio filtrante (un costo variable según producción) y naturalmente debe trabajar con un alto nivel de estabilidad de proceso.
A continuación, serán presentados los más importantes problemas y factores perturbadores relativos al procesamiento de escamas de botellas de PET; junto con posibles soluciones y recomendaciones de cómo encarar el problema respectivo; en este contexto, el enfoque está centrado en el aspecto del filtrado del fundido.
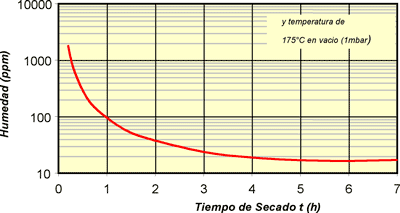
Principales factores de perturbaciones en el procesamento de escamas de botellas de PET
Factor perturbador: Humedad
Respecto al proceso de secado de las escamas, se puede distinguir entre humedad superfical y humedad del núcleo de éstas. La humedad superficial puede ser reducida en forma relativamente rápida, mientras que el caudal de aire, velocidad del aire, humedad del aire seco y temperatura son de particular importancia. En la mayoría de los casos, esto ocurre cuando el material está cristalizando a 170°C aproximadamente.
En contraste con esto, requiere mucho más tiempo reducir la humedad del núcleo, dado que la velocidad de transporte de la humedad del PET no puede ser acelerada para ningún porcentaje de la misma. El proceso de secado también se vuelve complicado ya que la velocidad de secado disminuye con el aumento del espesor de las escamas y con un creciente nivel de cristalización. (Figura 1).
La inversión en tiempo y costos aumenta considerablemente mediante la reducción de la humedad remanente en el núcleo y, por consiguiente, es recomendable analizar detenidamente cuánto se necesita ganar realmente en el producto final.
Otro método para reducir la humedad es la aplicación de vacío en el PET fundido. Si se usan extrusoras monotornillo, este efecto es bastante pequeño, sin embargo, si se utilizan extrusoras de dos tornillos este método es muy bueno y efectivo. Esta diferencia es el resultado de tener una superficie mucho mayor en el área de vacío provista por las extrusoras de dos tornillos, con todo esta diferencia también varía de acuerdo con la marca de la máquina así como con las especificaciones. Por supuesto, la altura del vacío es también un importante factor adicional. Una conclusión básica: Cuanto mayor sea el vacío, mejor reducción de humedad se consigue y el proceso se vuelve de costo más competitivo.
Por ejemplo, para obtener una reducción de humedad de 0,005 por ciento se requiere un vacío de aprox. 2 mbar. Los costos que surgen de esto son elevados.
Sin embargo, para una reducción de la humedad del 0,03 por ciento, es suficiente un vacío de 20-50 mbar. Los costos y gastos operativos son considerablemente más bajos. Por lo tanto, la pregunta es ¿Qué humedad puede quedar para que el producto pueda ser procesado exitosamente?
Para esto véanse los siguientes detalles:
• Refiriéndonos a las fibras textiles, una humedad remanente de alrededor del 0,03 por ciento es suficiente, dado que, para fabricar hilados un valor de la VI de 0,6 - 0,63 es absolutamente suficiente. En este caso, la degradación hidrolítica de la viscosidad del fundido provocada por la humedad remanente de aprox. 300 ppm, es aún deseada y razonable. Por supuesto que esto se aplica también para los materiales no-tejidos.
• Sin embargo, considerando el procesamiento de pellets para la producción de botellas, una degradación hidrolítica del fundido no es deseable, dado que el producto final requiere una viscosidad lo más alta posible. Sin embargo, aquí se puede evitar un secado costoso o un vacío adecuado mediante el recurso de limitar el tiempo de residencia del fundido a < 30 segundos y minimizando de esta manera la degradación hidrolítica. En lo referente al pelletizado, éste es básicamente posible, dado que el proceso es corto y claro. Si el proceso de manufactura está planificado minuciosamente, este objetivo puede alcanzarse. Pero un corto tiempo de permanencia en condición plastificada es un prerrequisito.
• Esto también se aplica para la fabricación de filmes, aunque en este caso una reducción del tiempo de residencia a < 30 segundos no puede ser alcanzada. Sin embargo, es posible que con una consistente reducción del tiempo de residencia del fundido y los compromisos correspondientes, el secado de las escamas puede cumplirse exitosamente. Por ejemplo, con una buena reducción de la humedad superficial y procesándolo mediante tornillo con paso de doble altura, y después con un vacío de aprox. 20 mbar, pueden producirse filmes brillantes que aseguren resistencia a la tracción. Hay muy buenos y promisorios métodos de resolución.
Factor de perturbación: Partículas duras
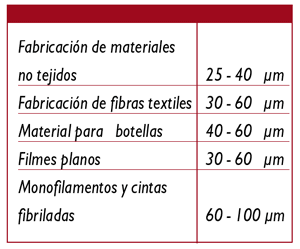
Factor de perturbación: Partículas blandas
Factor de perturbación: Plásticos extraños
Sin embargo, si estos plásticos están imperfectamente dispersos o mal homogeneizados en el fundido, lo que ocurre a menudo cuando se trabaja con extrusoras monotornillo, pueden entonces aparecer franjas en el producto final o roturas en el hilado con respecto a las fibras.
Factor de perturbación: PVC
Factor de perturbación: Adhesivos
Factor de perturbación: Madera
Factor de perturbación: Caucho
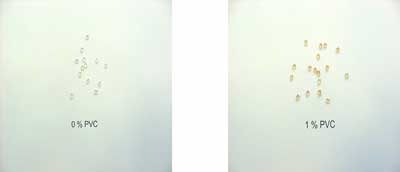
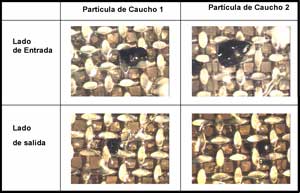
Factor de perturbación: Variaciones en el proceso de extrusión
• En cuanto a las variaciones de la extrusora monotornillo en la humedad del material, también provocarán cambios en la viscosidad del fundido y, por consiguiente, todas las características negativas que resultan de aquéllos.
• Variaciones y alteraciones en la estación de vacío de los tornillos dobles provocarán cambios en la viscosidad del fundido y también en el brillo del producto final.
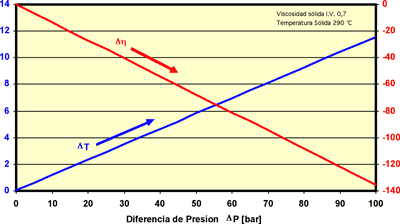
• Bombas de fundido, puntos muertos e inadecuada lubricación de los rodamientos pueden producir ojos de pescado, productos degradados y otros defectos.
Altos tiempos de residencia del fundido debidos a bolsas de material demasiado grandes también tienen un efecto negativo sobre la calidad del fundido.
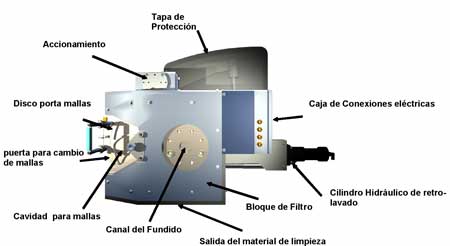
El RSFgenius como el perfecto sistema de filtrado para el procesamiento de escamas de botellas de PET
El control está determinado mediante la presión previa (aguas arriba) o mediante la presión diferencial. Las variaciones máximas de presión son de ±2 bar. El área de la superficie limpia de la malla, así como el nivel de contaminación son siempre constantes.
La operación del filtro es de proceso constante, porque la carga sobre las mallas no provoca ninguna variación con respecto a la temperatura y viscosidad, a lo que se agrega una producción absolutamente estable y porque el esfuerzo de cizallamiento del fundido siempre es el mismo. Además, la Tecnología Rotativa evita que las partículas degradadas entren al caudal del fundido cuando se cambian los filtros. (Figura 6).
El filtro trabaja en forma totalmente automática debido a la limpieza integrada de las mallas. Cuando se usan cambios de filtro convencionales, el operador tiene que retirar las mallas contaminadas fuera del fundido y reemplazarlas por otras nuevas. El disco filtrante con sus cavidades ubicadas en un área con forma de anillo está completamente encerrado por los dos bloques del filtro. Las cavidades están equipadas con una tapa que puede abrirse en caso necesario. El proceso no será alterado por el cambio de malla.
Comparado con otros cambios de filtro autolimpiantes, este procedimiento de limpieza se caracteriza por su eficiencia sumamente alta. Por una parte, esto lleva a una muy pequeña pérdida de fundido y, por otra, las mallas pueden usarse durante un tiempo mayor, el cual sólo está limitado por los tiempos de vida mecánicos de los elementos filtrantes.
El hecho de que el filtro RSFgenius sea universalmente aplicable constituye una característica adicional.
Puede usárselo en aplicaciones completamente diferentes, por ejemplo: en el filtrado de monómeros, en el reciclado o cuando se procesan las fibras finas de menor espesor. No existen limitaciones en lo referente a la viscosidad o a la presión del medio a ser filtrado, ni respecto a la fineza del filtrado. (Figura 7).
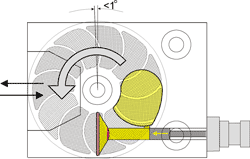
Un corto tiempo antes de que las mallas sean vueltas a introducir en el canal del fundido, las mismas son limpiadas mediante un sistema de pistón para purga integrado patentado. El fundido filtrado es removido del bloque de salida en un pistón de purga. Después de cada movimiento de indexación, este fundido es lanzado por el pistón por medio de impulsos de alta presión a través de un pequeño huelgo a través de la malla contaminada hacia el exterior. La cantidad necesaria para esto puede ser regulada individualmente y corresponde en la práctica al 0,02 por ciento, (ó 0,5 por ciento máximo con alta contaminación) de la producción.
La velocidad del lanzamiento también puede seleccionarse individualmente y se regulará de manera que el proceso de limpieza controlado de la malla sea mayor que el consumo de presión a través de la malla. Esto garantiza una óptima limpieza de las mallas. Esta limpieza tiene lugar sin afectar el proceso de producción.
El control del RSFgenius se realiza en forma totalmente automática mediante el control Genius, el cual como opción puede también estar integrado en el control existente de la línea. Hasta el último reuso de las mallas, el sistema de filtrado RSFgenius trabaja sin necesidad de atención de parte de ningún operador del sistema de filtrado. Sensores integrados permiten el monitoreo de los parámetros operativos (temperaturas, presión diferencial, presión de purga, cantidad corriente de usos de las mallas, etc.) mediante el sistema de control del proceso. (Figura 8).Temperatura a la salida del filtro. Cuando se procesa material sensible, debe evitarse la intrusión de aire o de fundido ya degradado por oxidación o térmicamente. El RSFgenius responde las demandas debido a su diseño completamente encapsulado. El disco filtrante con las mallas insertadas gira entre dos superficies metálicas y por eso evita el contacto del fundido y las mallas con aire o la humedad del aire. Cuando se cambian las mallas, se abre una tapa que posibilita trabajar al disco filtrante. Las mallas recién insertadas solamente entran en el circuito del fundido después de haber pasado el área de purga. El sistema de purga hace salir completamente el aire fuera de las mallas y llena las cavidades con fundido fresco y filtrado, precisamente antes de que éstas sean giradas hacia el canal del fundido.
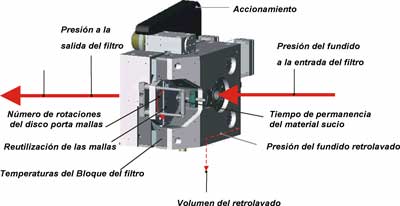
Ejemplos de reciclado directo de escamas de botellas de PET
Resina para botellas de PET
El sistema de filtrado es de vital importancia, dado que el tiempo durante el cual el PET es fundido debe mantenerse en un mínimo absoluto. Para eliminar la contaminación que es visible a ojo desnudo, la fineza de filtración debe estar entre 25 y 50 µm. Las partículas quemadas deben mantenerse fuera del producto final en todo momento, incluso durante los cambios de elementos filtrantes y en el curso de la autolimpieza de éstos. Por supuesto que el sistema de filtrado también debe poder regularse a sí mismo automáticamente para manejar las cambiantes cargas de contaminación - los factores claves del Sistema de Filtrado del Fundido Totalmente Automático, RSFgenius.
Lámina de A-PET
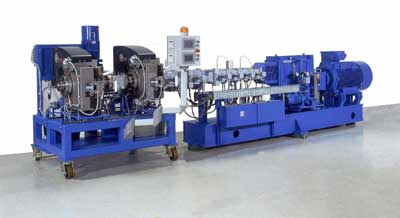
Hilado parcialmente orientado (POY)
Los procesos de hilado de alta velocidad para la fabricación de POY requieren normalmente una V.I. de hilado de 0,62 a 0,64 dl/g. Usando escamas de botellas, la V.I. puede controlarse mediante el presecado y/o la adición controlada de aditivos modificadores de V.I. También es necesaria la adición de TiO2 para un acabado totalmente mate o semimate.
A los efectos de proteger las lanzaderas de un bloqueo prematuro, el eficiente filtrado del fundido es un prerrequisito. La fineza de filtrado necesaria es típicamente de 20 µm o más fina.
La fibra textil se hila con un rango de V.I. entre 0,58 y 0,62 dl/g. En este caso también la V.I. está determinada por el nivel del presecado y/o la adición de un modificador de V.I. Nuevamente un eficiente filtrado es crucial para la eficiencia económica de la operación para evitar el bloqueo prematuro de los filtros del pack de hilado. La fineza de filtrado típica es de 36 µm.
El hilado engomado tanto para aplicaciones textiles en calibres finos como tipos más pesados para recubrimientos de pisos y de terraplenes, puede ser fabricado también con escamas de botellas. La V.I. para hilado debe regularse, en este caso, en 0,64 dl/g aprox. Debido al tamaño de las lanzaderas, el sistema de filtrado es de gran importancia. La fineza de filtrado depende de la característica del hilado.
En cualquier aplicación de hilado de fibra, la estabilidad del proceso del sistema de filtrado es crucial, pues cambios de presión y tiempos de residencia producirán roturas en el hilado. (Figura 10).
Cintas para packaging, monofilamentos de alta resistencia a la tracción
Usar escamas de botellas de PET es de gran interés para los fabricantes de cintas para empaque y monofilamentos a prueba de roturas, a los efectos de mantener los costos de materia prima lo más bajos posibles, especialmente porque el material reciclado puede usarse sin problemas cuando la línea ha sido diseñada con esta finalidad. Por esto, el material de PET virgen con una V.I. de aprox. 0,9 a 1,3 será mezclado. La relación de mezcla depende de la resistencia requerida por las cintas, así como de la calidad y humedad de las escamas. Además, el diseño de la línea juega un importante rol. Las posibilidades de aplicación de escamas de botellas de PET están determinadas especialmente por la consistencia del sistema de filtrado utilizado así como por la fineza del filtrado. Es también posible aumentar la V.I. de la escama en una SSP a 1,0 y más y entonces se puede usar 100 por cien de material reciclado.
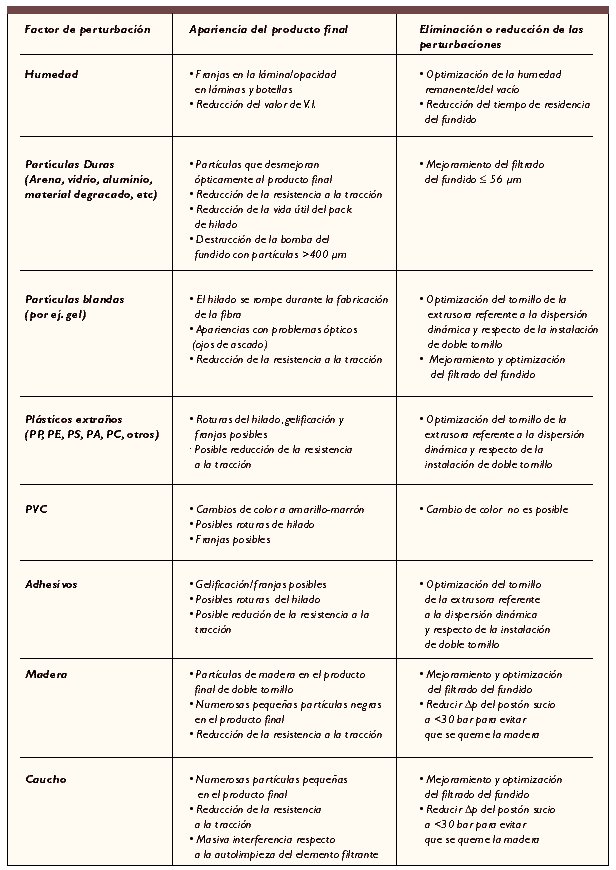
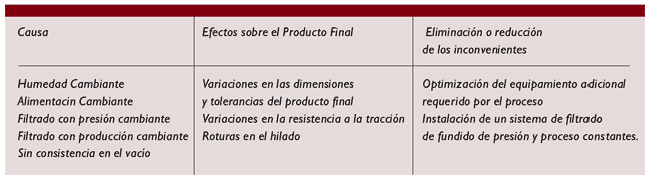
Conclusión
El filtrado del fundido es de gran importancia cuando se procesan escamas de botellas de PET. Muchos problemas específicos del material o del proceso de producción pueden ser resueltos solamente mediante un adecuado filtrado del fundido. A este respecto, el Sistema de Filtrado Rotativo Gneuss RSFgenius se caracteriza por varias perfectas características. Trabaja automáticamente con un proceso constante y de alta eficiencia. En consecuencia, cumple perfectamente todas las exigencias del reciclado directo de escamas de botellas de PET, lo cual está comprobado por su extraordinaria popularidad a nivel internacional.
Las características del RSFgenius, que son de específico interés para el reciclado de escamas de botellas de PET se pueden resumir como sigue:
- Adaptación automática a cargas de contaminación variables.
- Operación de proceso constante.
- Operación a presión constante.
- Operación totalmente automática.
- Tiempo de residencia del moldeado en el sistema lo más corto posible (<2 min)
- Tiempo de permanencia del pastón sucio en el fundido lo más corto posible
- Posibilidad de regulación precisa del sistema de contracorriente para usar el materia eficientemente.
- Alta cantidad de usos de las mallas (más de 200 usos posibles)
- Filtrado fino posible (hasta 10 µm) con el uso de escamas de botellas de PET
- El cambio de elemento filtrante se realiza sin interrupciones ni perturbaciones en el proceso.
El RSFgenius está trabajando exitosamente con escamas de botellas de PET en una variedad de procesos para reciclado directo, a saber :
- Regranulado de escamas de botellas para virutas de PET calidad alimentaria (Aprox. 20 unidades con producciones entre 800 y 1.500 kg/h)
- Hilado de fibra textil (Aprox 40 unidades, 300 - 1300 kg/h)
- Hilado de fibra engomada (Aprox 20 unidades, 400 -1000 kg/h)
- Lámina para termoformado en A- PET (aprox 110 unidades, 500 - 1500 kg/h).