La falta de un análisis metódico, genera costes insospechados en la producción
La falta de un análisis metódico, sobre el posible origen real del problema que nos presenta una pieza inyectada, puede generarnos unos costes añadidos, que después tendremos que soportar durante toda la vida de fabricación del producto.
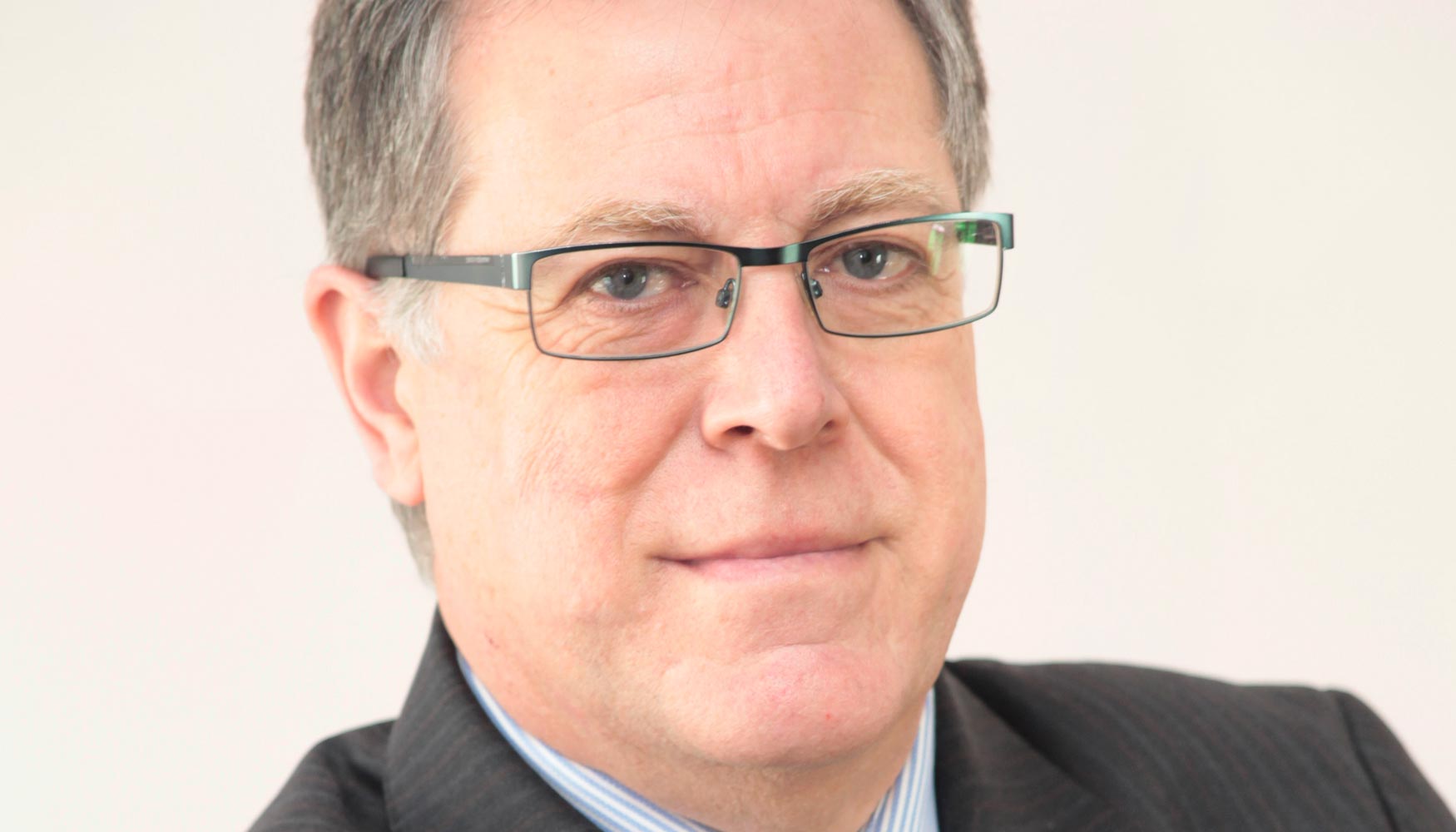
Cuántas veces, durante el proceso de homologación de una pieza, tomamos la decisión, más o menos alegremente, de modificar uno o varios parámetros muy relevantes, dentro del propio proceso de inyección.
Con estas “pequeñas modificaciones de parámetros”, pretendemos solucionar definitivamente el problema de estas piezas, en los que respecta a deficiencias de aspecto, variaciones irregulares de sus dimensiones, deformaciones en uno o varios puntos de las mismas, rechupes en las zonas nerviadas o zonas lejanas al punto de inyección, rebabas en las zonas próximas al punto de inyección o en puntos lejanos en una o varias de sus cavidades, etc.
Una vez ya ha sido homologada la pieza, muy probablemente, estas modificaciones se quedarán grabadas como parte del proceso de inyección ideal, dado que serán, aparentemente, imprescindibles para obtener la calidad deseada y homologada finalmente por nuestro cliente.
Debemos tener muy en cuenta que, en muchas ocasiones, el resultado de esta modificación de parámetros aparentemente “tan lógica”, puede ser una carga económica para el coste de la pieza que fabricamos; ya que, muy probablemente, se habrá incrementado del tiempo de ciclo, quizás también, la temperatura de la masa o el molde, y si existían rechupes, muy probablemente también incrementaremos la presión de inyección, con el consiguiente incremento del peso de la pieza inyectada, cosa que, casi siempre, hará que el peso final obtenido sea superior al teórico empleado para realizar la oferta.
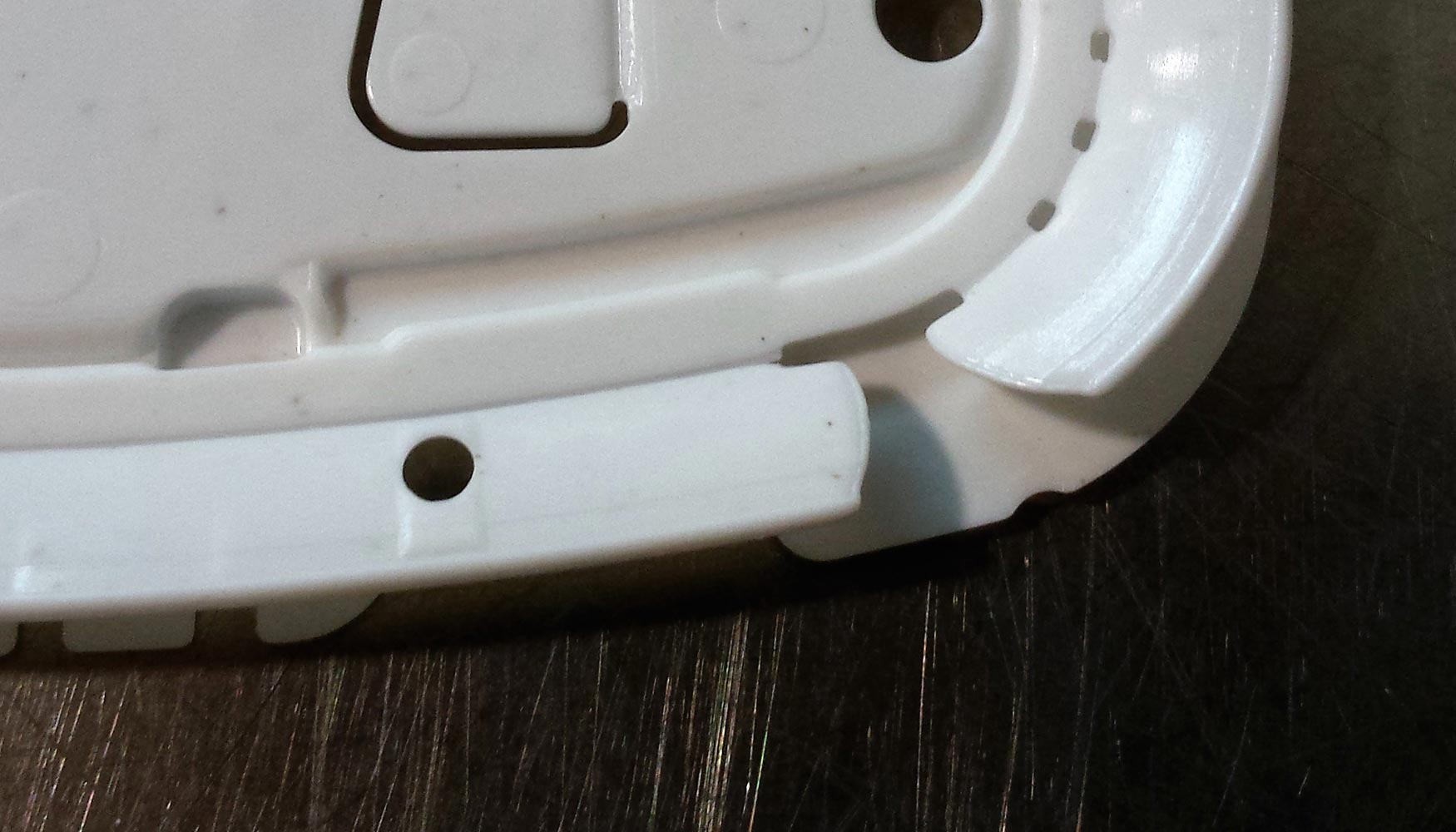
No debemos caer en la obviedad de pensar que la toma de este tipo decisiones, es o debe ser responsabilidad única del técnico que está manipulando la máquina de inyección, pues todas las personas que están involucradas desde el principio, directa o indirectamente, en el diseño del producto, en el diseño y fabricación del molde, en la elección de la materia prima, los aditivos que esta debe contener, los colorantes, el tipo de acabado que tendrá la pieza, etc., deberían tener un criterio de análisis y conocimiento muchos más amplios, que les permitan conocer la gran influencia en los costes finales de la pieza, que tienen los diferentes parámetros que determinan un proceso de inyección.
Sirva como muestra este ejemplo: en la inyección de una pieza, se observa que cuesta conseguir un llenado regular y estable de las cavidades; se decide que, puesto que la temperatura de la masa ya se había incrementado previamente, la mejor solución era incrementar la temperatura del molde, siendo únicamente necesario el incremento del 10%; aparentemente esta era la “decisión más lógica”. Dado que así se facilitaba el flujo del material, se reducirían tensiones de la pieza y el llenado de la pieza sería más estable. Efectivamente esto es lo que ocurrió, y se dio por validada tanto la calidad de la pieza como los parámetros de proceso utilizados para su inyección; entre ellos el ciclo total que se dio por óptimo.
El resultado real de esta “decisión lógica”, fue que al incrementar las temperaturas de la masa y del molde, también se incrementó el consumo energético unitario por ciclo, y aunque quizás parezca que no es lo más importante, también debemos tener muy en cuenta que al incrementar la temperatura del molde, aunque solo sea en un 10%, también se incrementó al mismo tiempo el tiempo ciclo total en un 2%, o lo que es lo mismo: la pieza se estaba fabricando con un ciclo y un coste superior al que estaba previsto inicialmente, gracias a esta “decisión muy lógica”, pero aparentemente inevitable, el margen de producción había bajado.
Pasado un tiempo, este mismo molde fue enviado a otra empresa transformadora, la cual cuando analizó detalladamente los parámetros de proceso que empleaba el anterior transformador, pensó que quizás el ciclo para esta pieza era un poco elevado, teniendo en cuenta el tipo de material empleado. Así empezó a plantearse la idoneidad de aquellos valores.
Por esta razón, el nuevo transformador, después de analizar el molde y la pieza detalladamente, determinó que para el tamaño y volumen de la pieza, el punto de inyección era excesivamente pequeño. Así que se procedió a modificar su tamaño, incrementando la sección de paso de material.
Con este sencillo análisis y esta sencilla modificación obtuvo una mejor y fácil fluencia del material, pudiendo reducir la temperatura de masa, y la del propio molde. Con ello redujo el consumo de la energía necesaria para transformar la pieza y por si fuera poco adicionalmente, también se redujo el tiempo de ciclo, puesto que la temperatura de la masa y el molde eran sensiblemente inferiores, y a la vez, se podía desmoldear la pieza en menos tiempo sin sufrir variaciones dimensionales.
Esto nos lleva a confirmar que el análisis profundo y metódico, que nos permita encontrar la raíz del problema, nos dará un nuevo punto de vista para la aplicación de posibles soluciones, y que con toda seguridad nos harán más competitivos y permitirán la generación de unos mayores beneficios.
Desde el Centro Español de Plásticos somos conscientes de la necesidad que existe en formar sobre este tema tan específico, no solo a los integrantes de los departamentos de producción, también a los gerentes y directivos, ingenieros de diseño y proceso, responsables de calidad, así como al personal del área comercial y de compras, puesto que el conocimiento de los motivos que pueden causar estas faltas de calidad, y su más que probable incremento de los costes del producto final es básico para poder afrontarlos.
Por todo ello, hemos organizado un taller interactivo sobre el análisis de defectos en la inyección de plásticos (Troubleshooting), en el que durante dos días, nuestros expertos, analizaran detalladamente y en profundidad, todos los problemas de calidad que pueden presentan las piezas de plástico y sus posibles soluciones a cada uno de los mismo, siempre teniendo en cuenta la solución más práctica e idónea y sobre todo pensando en cuál de ellas es la más económica, que permita rentabilizar al máximo producto que estamos fabricando.
Durante el segundo día de este Taller interactivo, todos los asistentes que lo deseen, tendrán la oportunidad de mostrar sus propias piezas, con el fin de analizar las posibles soluciones a sus problemáticas particulares.