El uso de estos materiales en la industria aeroespacial y de la automoción es ya un hecho innegable
Comportamiento a fatiga de uniones soldadas de termoplásticos reforzados
El uso de materiales compuestos de matriz polimérica en la industria aeroespacial y de la automoción es ya un hecho innegable, llegando incluso a ser el material predominante en los últimos desarrollos aeronáuticos. Atendiendo al tipo de resina distinguimos dos grandes grupos, los materiales de matriz termoplástica y los de matriz termoestable. Las resinas termoplásticas, en comparación con las termoestables presentan una serie de ventajas tales como que no tienen fecha de caducidad, presentan alta reciclabilidad, tienen una excelente resistencia a la fractura y una alta tolerancia al daño. Sin embargo, una de sus principales características es que pueden ser reutilizadas muchas veces tras su fabricación introduciendo calor y/o presión [1]. Debido a esta característica, los termoplásticos pueden ser soldados evitando así la necesidad de recurrir a uniones mecánicas. Esta operación de soldeo se realiza en un corto espacio de tiempo, y a priori presenta claras ventajas frente a otros procedimientos de unión como la unión mecánica o mediante adhesivos empleadas en los materiales de matriz termoestable [2].
1. Introducción
Para conseguir una soldadura de calidad en materiales termoplásticos este debe ser calentado por encima de la Temperatura de Transición Vítrea (Tg) o la Temperatura de Fusión (Tm) dependiendo de la estructura del polímero (amorfo o semicristalino). Una vez que la temperatura es alcanzada, se aplica presión, creando un contacto íntimo entre las superficies. Posteriormente, las asperezas superficiales son deformadas y el gas atrapado entre las piezas es eliminado debido a que la capa fundida fluye hacia afuera. El proceso concluye con la difusión molecular y la unión de las cadenas poliméricas.
Finalizada la unión, la intercara entre las piezas soldadas queda indiscernible, como se puede ver en la figura. 1a, mientras que en las uniones adhesivas, la unión entre las dos piezas es claramente visible (figura 1b). Por último, el proceso de enfriamiento permite la recristalización (en caso de semicristalinas) de las matrices.
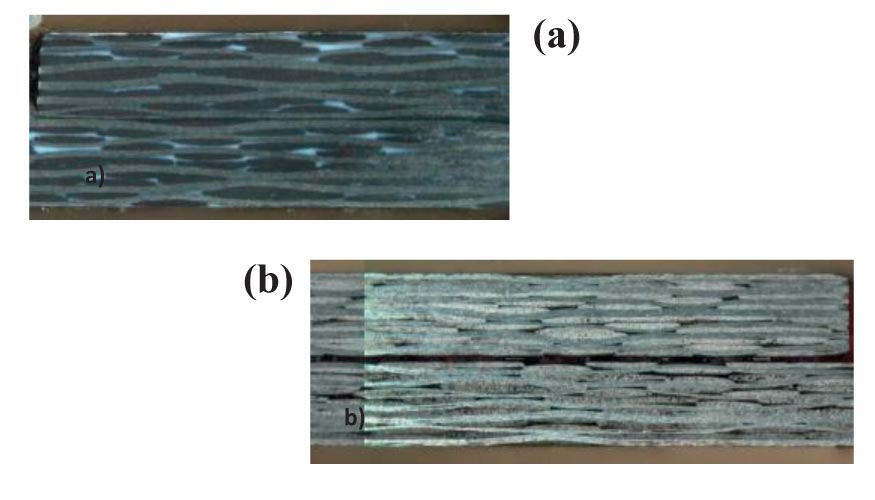
Fig. 1 Micrografía de unión soldada por ultrasonidos (a) y por unión adhesiva (b).
En termoplásticos, se usan diferentes técnicas para soldar, clasificándose éstas según el procedimiento que se emplee para aplicar calor. Dentro de estas técnicas la empleada en este trabajo ha sido la de ultrasonidos. En soldadura por ultrasonidos, altas frecuencias y bajas amplitudes son necesarias. Las vibraciones inducen movimiento molecular y la fricción genera calor. El principal inconveniente asociado a esta técnica y al equipo empleado (ACU Dynamic 3000) es el tamaño de la pieza a soldar y la configuración de las piezas a unir, solo solape. El proceso de soldeo es muy similar al de soldadura por resistencia de metales, distinguiéndose prácticamente las mismas fases. Los parámetros que controlan la soldadura son la amplitud y frecuencia de la vibración, el tiempo de soldeo y fuerza aplicada durante este tiempo, y el tiempo de solidificación y fuerza durante este tiempo [3]. Estudios realizados por Villegas [4] describen con profundidad las etapas del proceso y establecen las condiciones óptimas de los parámetros para conseguir una soldadura con una adecuada resistencia a cortadura.
Al igual que en los procesos de soldeo de metales esta operación provoca una distribución de temperaturas no uniformes que lleva aparejada un estado de deformaciones no compatible que provoca la aparición de tensiones internas. En metales, debido fundamentalmente al comportamiento plástico a cualquier temperatura, estas tensiones no desaparecen una vez finalizado el proceso y quedan almacenadas como tensiones residuales. Los materiales termoplásticos, usados en este trabajo, no presentan comportamiento plástico a temperatura ambiente ni a temperaturas ligeramente por debajo de la Tg, sin embargo, la no linealidad asociada a la dependencia de propiedades con la temperatura provocan la aparición, desde el punto de vista macroscópico, de tensiones, que en principio no desaparecen finalizado el proceso. Dichas tensiones podrían tener influencia en el comportamiento en servicio de piezas realizadas con materiales termoplásticos soldados.
El objetivo principal de este trabajo es por un lado evaluar experimentalmente las tensiones residuales asociadas al proceso de soldeo por ultrasonidos. Se han empleado materiales reforzados con fibra de carbono con dos tipos de matrices termoplásticas una semicristalina Polyphenylene sulphide (PPS) y otro amorfa Polyetherimide (PEI). Para el material PPS se han considerado dos condiciones de soldeo diferentes en la que una de otra se diferencia en la fuerza que se aplicaba durante la fase de vibración. Por otro lado, se han llevado a cabo ensayos de fatiga con el objetivo de obtener la curva SN de comportamiento.
2. Preparación de muestras
Como se ha comentado con anterioridad, los materiales usados en este trabajo fueron dos tipos de matrices termoplásticas ambas reforzadas con fibra de carbono. Las matrices eran la amorfa (PEI) y la semicristalina (PPS). La configuración de refuerzo elegida fue un tejido 5HS con refuerzos a 0º y 90º. La información técnica de los materiales puede ser consultada en el “datasheet” suministrado por el fabricante (Tencate, 2014, http://www.tencate.com). No obstante, para disponer de las propiedades de rigidez concretas de los materiales fabricados se llevaron a cabo ensayos de tracción según la norma UNE-EN ISO 527-4. Los resultados medios obtenidos se muestran en la tabla 1, estando los mismos en concordancia con los suministrados por el fabricante.
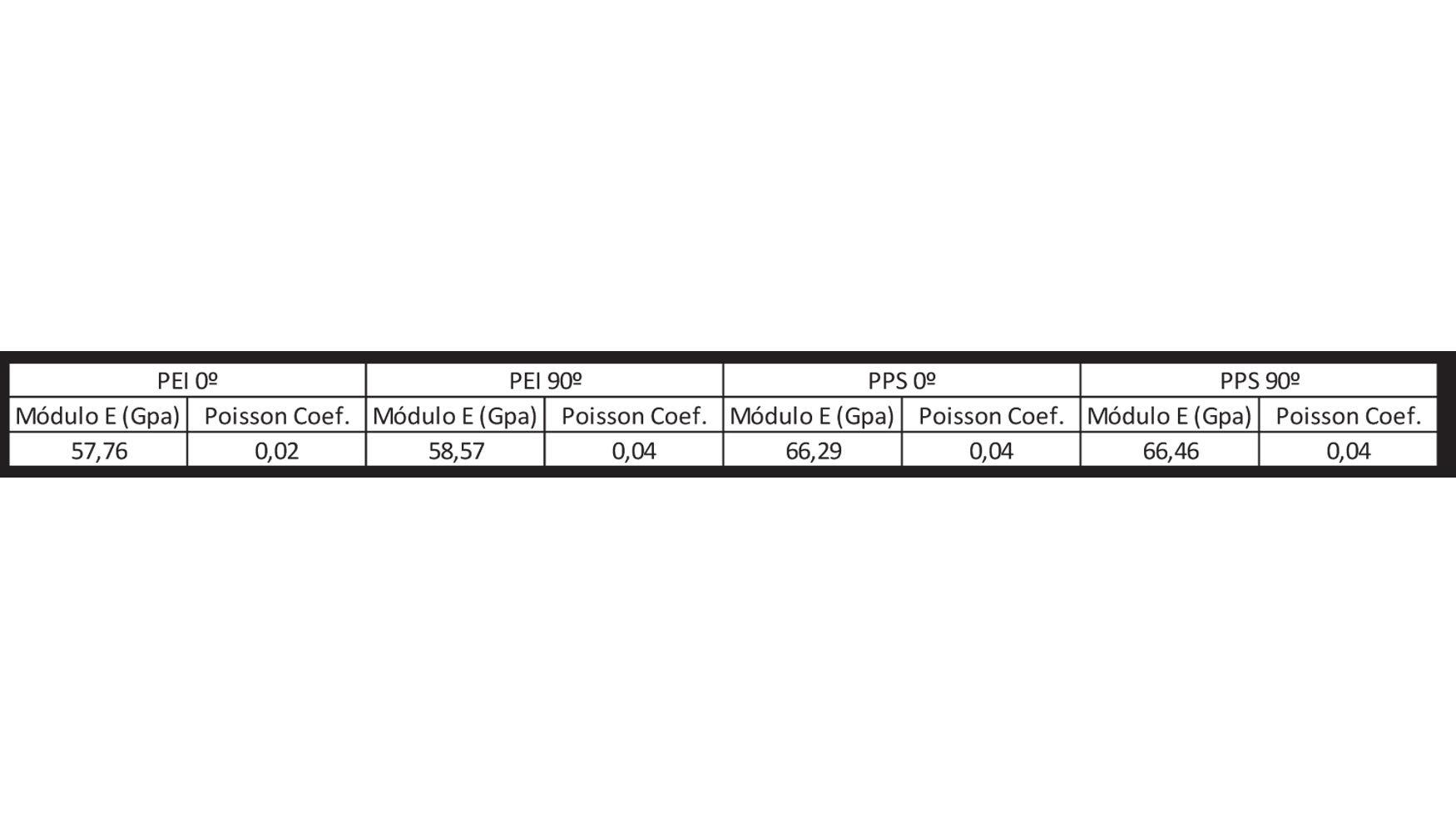
Una vez fabricados y caracterizados los laminados se cortaron los paneles para conformar mediante soldadura probetas de lap shear que serían ensayadas posteriormente a fatiga. La configuración adoptada fue la de simple solape. Toda la preparación del material se llevó a cabo en la Universidad Técnica de Delft (TU Delft).
Para soldar las piezas, se empleó una máquina de soldadura por ultrasonidos ACU Dynamic 3000 (Rinco Ultrasonic AG Company). Entre todos los parámetros involucrados en la calidad de la soldadura, sólo se cambió la fuerza 'Trigger' que es la fuerza a la cual el proceso de soldadura comienza. En la tabla 2 se muestran los parámetros de soldeo empleados, un conjunto para PEI y dos para PPS.
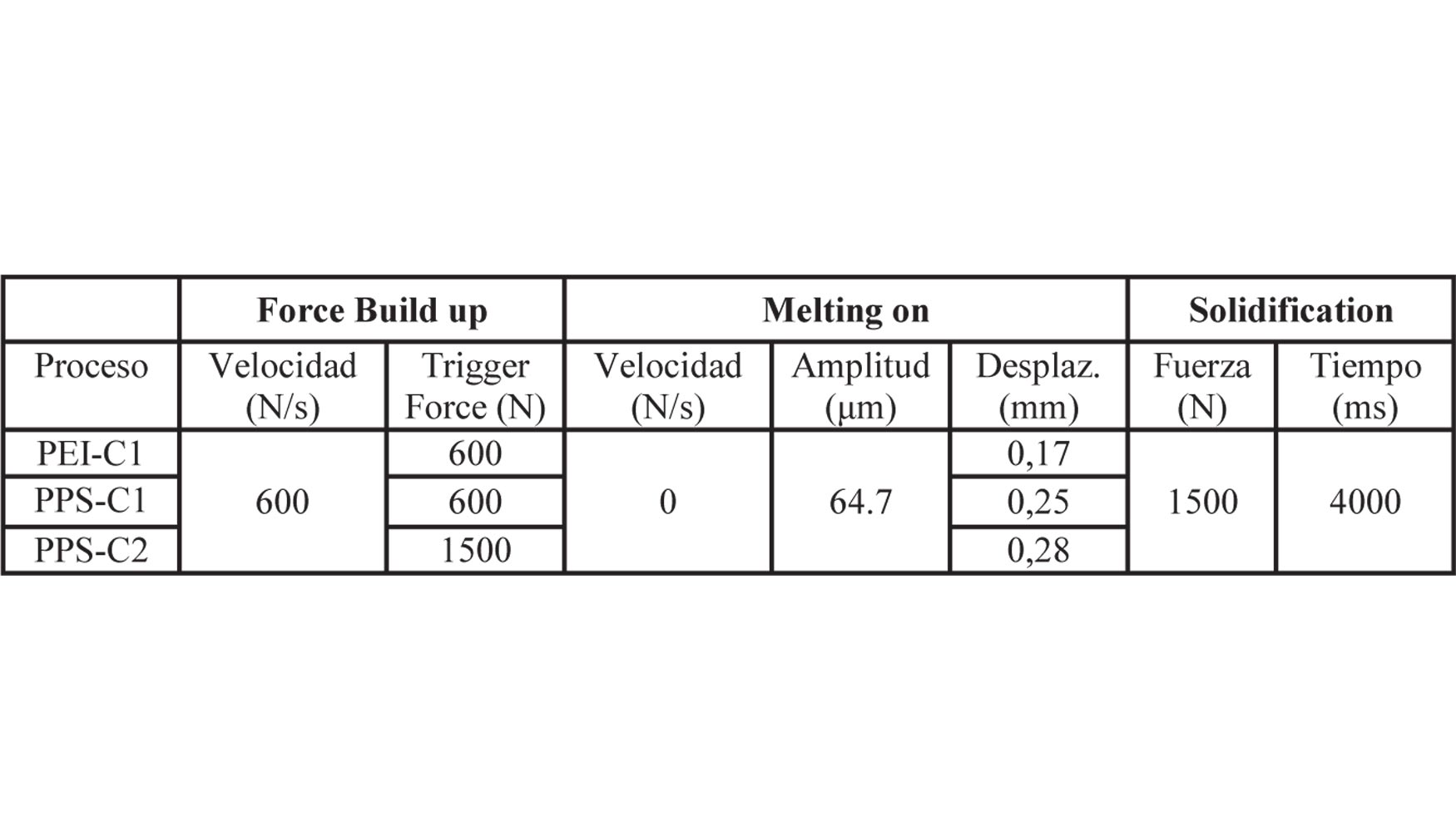
Como ejemplo de la evolución de las variables durante el proceso de soldeo se muestra en la figura 2 la evolución en el tiempo de la potencia y del desplazamiento del 'sonotrodo' para una probeta PPS.
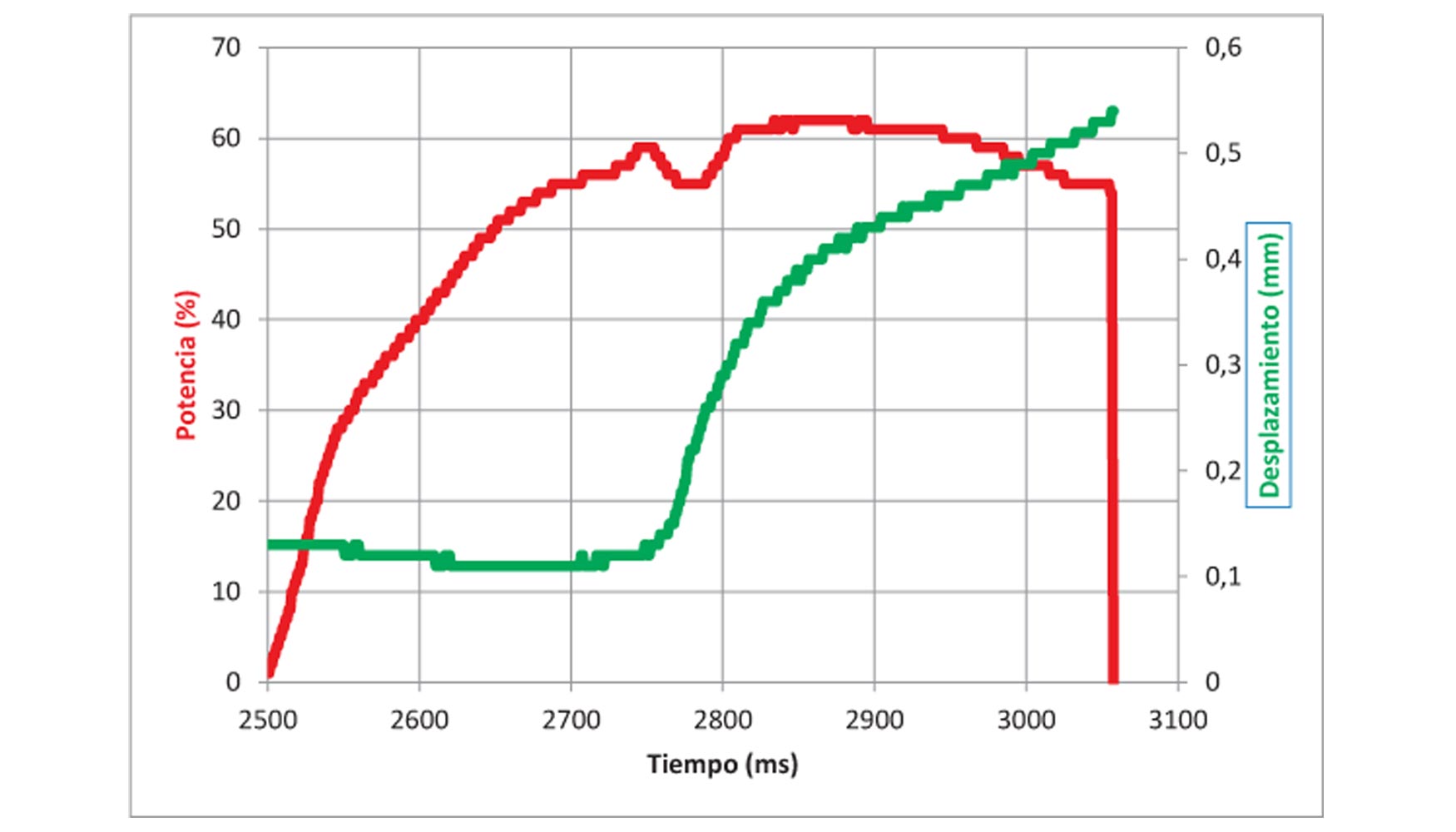
Una vez soldadas las probetas se procedió a su inspección mediante pulso eco manual. Al analizar las probetas, no se apreciaron atenuaciones y movimientos del eco de fondo significativos como para ser reportados.
3. Determinación de las tensiones residuales
Para la evaluación de tensiones residuales, dada la geometría de las probetas, se contemplaron 3 procedimientos, todos basados en la relajación del estado tensional por alteración de la geometría. El procedimiento I consistió en pegar una roseta biaxial en la zona solapada y someter a la probeta a un ensayo de “lap shear”, al producirse la separación de las dos semiprobetas, la lectura de las bandas junto con las propiedades de rigidez permitiría conocer el estado tensional residual. Este procedimiento no resultó satisfactorio dado que al producirse la separación de las dos semiprobetas, esta se produce de forma abrupta originándose el despegue de las bandas. Como alternativa,
procedimiento II, se usó esta misma idea pero en probetas sometidas a fatiga y niveles bajos de carga. Dado que el material presentaba un comportamiento elástico lineal, no cabría pensar en posibles relajaciones del estado tensional originado por la fatiga. El procedimiento III, también de relajación, consistió en aislar la zona solapada de una de las semiprobetas. Ello se llevó a cabo mediante operación de corte y mecanizado tal como se esquematiza en la figura 3. En la tabla 3 se muestran los valores medios de los resultados obtenidos con los dos procedimientos.
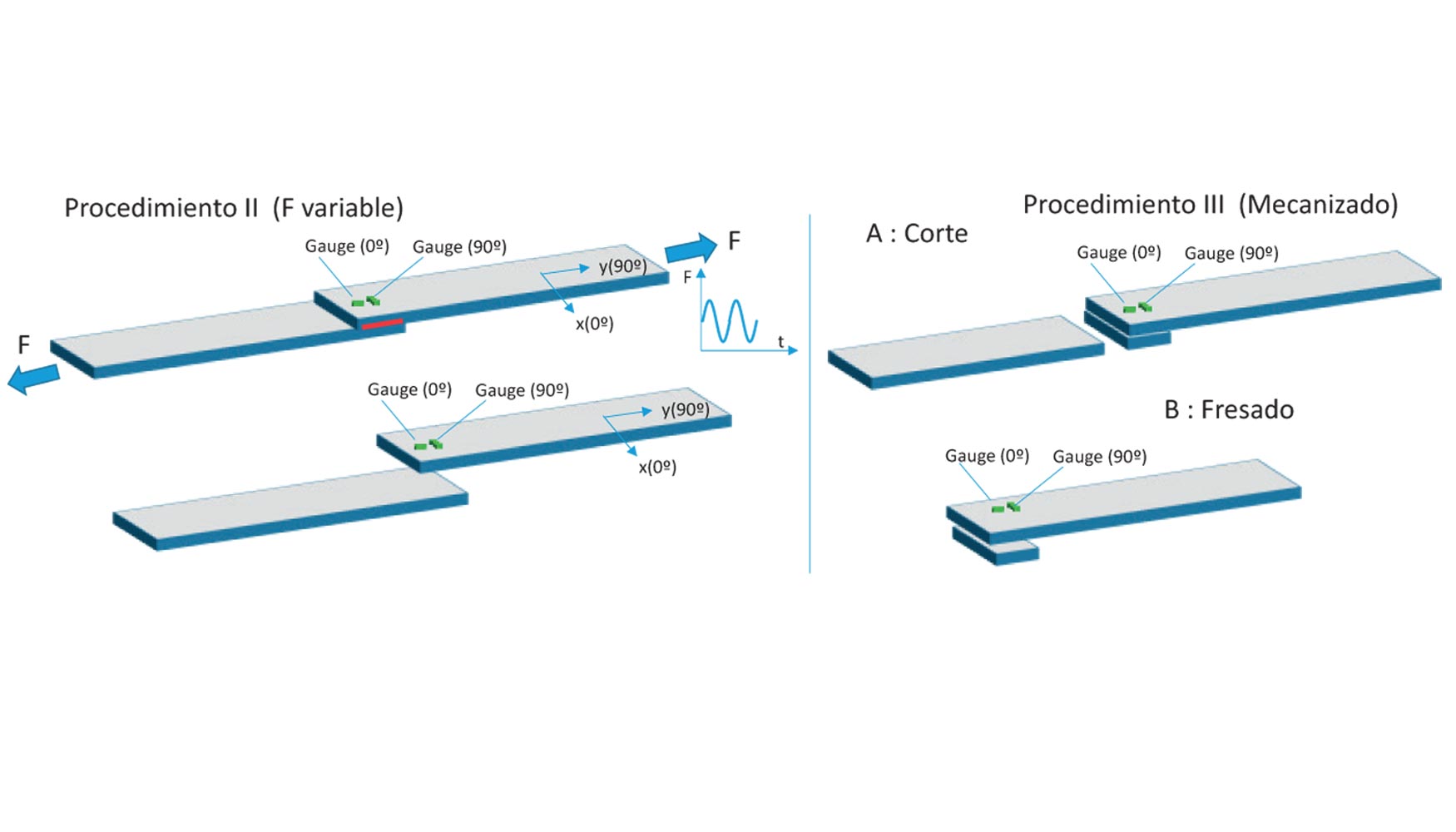
En general los valores encontrados son bajos (<5% de la resistencia a tracción). En cuanto a las diferencias encontradas en los materiales, se podría decir que la razón debe estar relacionada con la estructura interna del material. PEI al ser amorfo, podría presentar un nivel más bajo de tensiones residuales que el semicristalino PPS. El nivel de tensiones encontrado es similar al que otros autores han encontrado en uniones termoplásticas a tope [5].
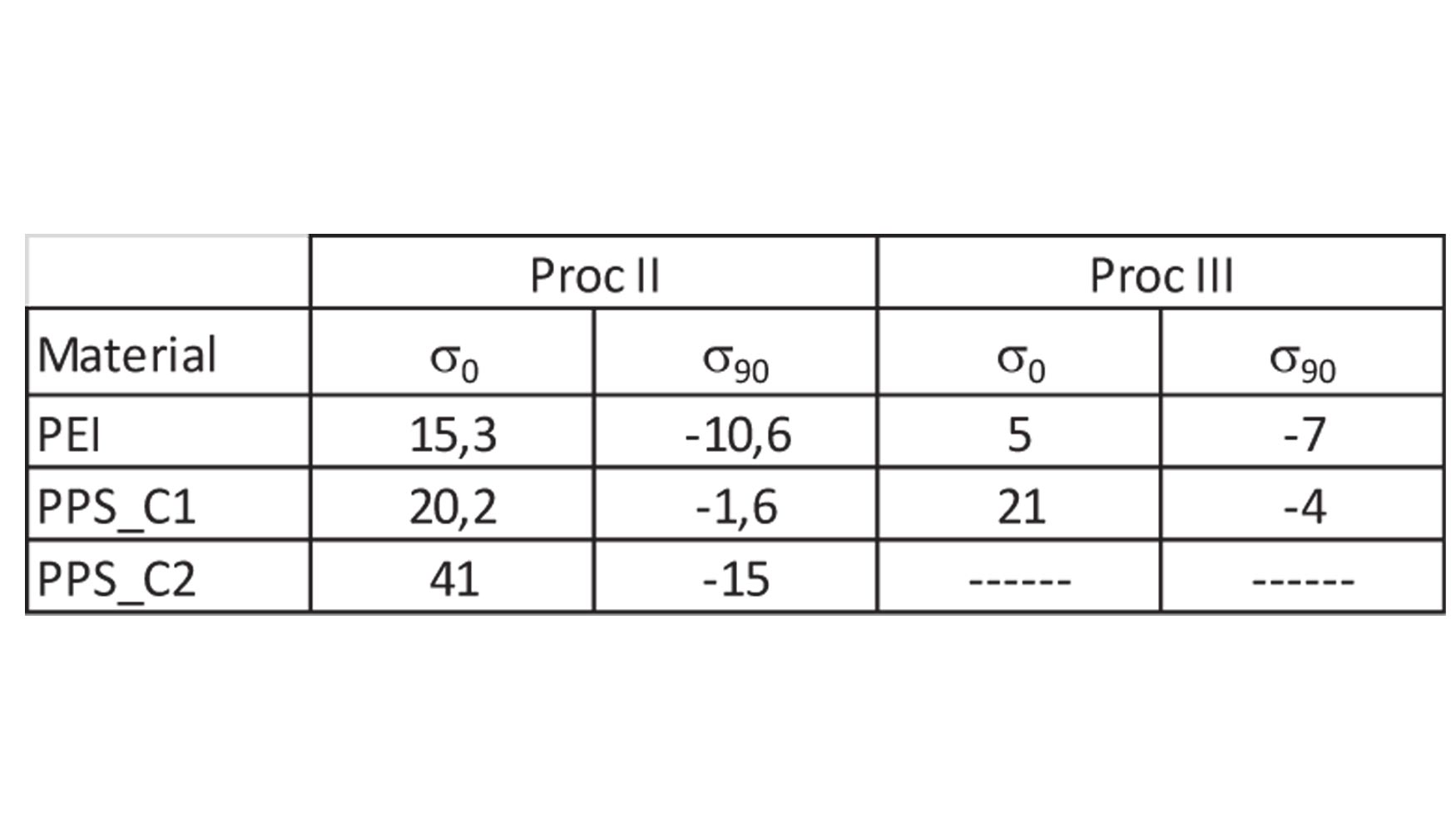
4. Comportamiento a fatiga
Por último se procedió a ensayar estáticamente y a fatiga, llevándose a cabo ambos ensayos sobre probetas de 'single lap shear', empleándose una geometría sin tacones como la definida por la Norma EN pr2667. Estudios realizados previamente por Cañas,
M. [6] muestran que el empleo de geometrías alternativas (probetas de doble muesca o el empleo de tacones de alineamiento) no conduce a mejoras significativas en el comportamiento estático.
Los resultados estáticos fueron similares en todos los casos analizados. Así, los valores medios de tensión última a cortadura obtenidos fueron para PEI de 33,2 MPa y para el PPS condición 1 y 2 de 36,4 y 34,6 MPa respectivamente.
Los ensayos de fatiga se llevaron a cabo en una máquina universal Instron 8801, los valores de carga máxima oscilaron entre el 80% y el 30% de las cargas estáticas, el valor R fue 0,1 y la frecuencia empleada de 10Hz. Se llevaron también a cabo ensayos en probetas a un valor de 50% de la carga estática, a frecuencias de 5 y 18 Hz para comparar el posible efecto sobre el número de ciclos, no apreciándose cambios significativos. Los ensayos se interrumpían si se superaban los 3,7 millones de ciclos sin romper. En la figura 4 se muestran las curvas SN obtenidas, así como el ajuste por mínimos cuadrados, para los casos analizados.
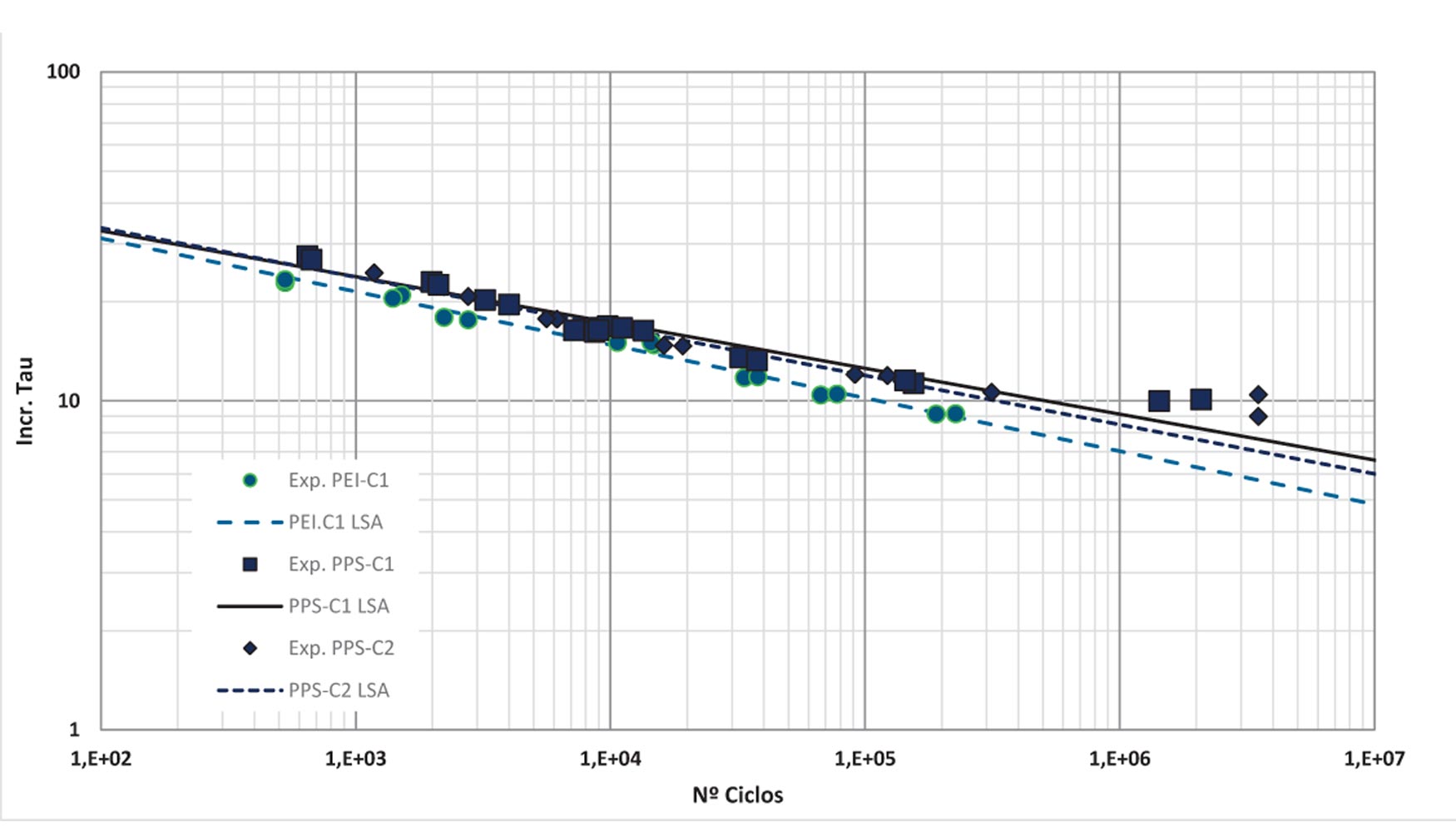
Fig. 4 Curvas SN.
Como puede apreciarse, el comportamiento a fatiga es muy similar en todos los casos siendo ligeramente más favorable en las probetas de PPS que en las de PEI. Analizando el mecanismo de fallo (Figs. 5 y 6) se vio que en todos los casos el mecanismo de rotura es interlaminar o delaminación, lo que indica, en cierta medida, que la soldadura fue satisfactoria. Otros investigadores [7, 8] han realizado también estudios a fatiga sobre configuraciones similares con otros materiales y otros procedimientos de soldeo y las conclusiones relevantes son similares a las obtenidas
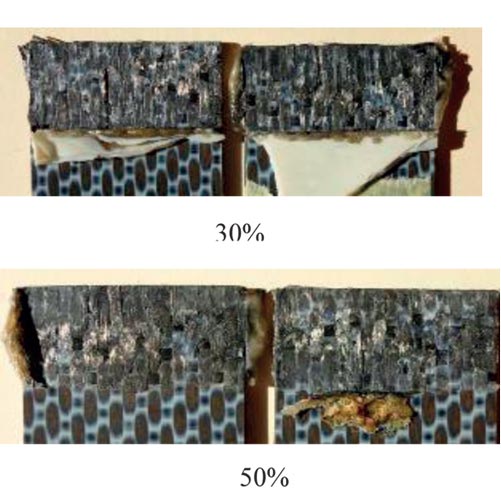
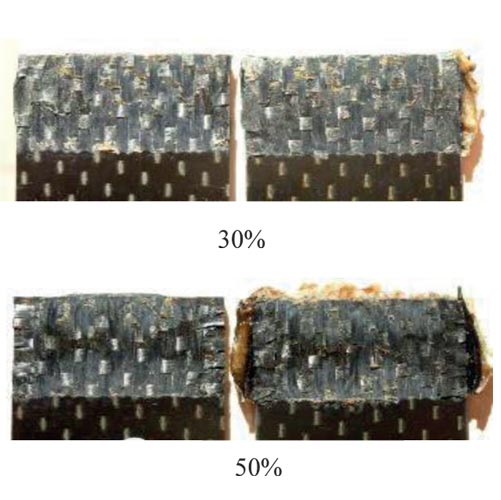
5. Conclusiones
Como conclusiones más relevantes de trabajo realizado citaremos:
- El nivel de tensiones residuales asociado al proceso de soldeo es muy similar para los dos materiales y los dos casos de soldeo contemplados. El nivel globalmente es bajo por lo que no hace pensar que sea muy influyente el comportamiento tanto estático como a fatiga.
- El comportamiento a fatiga es también muy similar aunque las probetas de matriz PPS presentan un comportamiento más favorable que las PEI.
- Para las probetas PPS y para ambas condiciones de soldeo se observó que para un nivel de carga del orden del 35% de la carga de rotura estática a cortadura la probeta no rompía por debajo de 3,7 millones de ciclos.
Referencias
- Baker, A., et al (2004). “Composite Materials Aircrafts Structures”. AIAA. REF
- Shi, H., et al (2103).”Strength and failure modes in resistance welded thermoplastic composite joints: Effect of fibre-matrix adhesion and fibre orientation”, Composites Part A 55, pp 1-10.
- Yousefpour A., et al. (2004). “Fusion Bonding/Welding of Thermoplastic Composites”. Journal of Thermoplastic Composite Material. Vo. 17. pp 303-341.
- Villegas, I.F. (2013). “In Situ Monitoring of Ultrasonic Welding of Thermoplastic Composites Through Power and Displacement Data”. Journal of Thermoplastic Composite Materials. 14. pp 1-20.
- Leggatt, R.H., TAVAKOLI, S.M. (1997). “Measurement of Residual Stresses in Welded Thermoplastics”. Plastic Rubber and Composites Proccesingand Applications. Vo. 26 Nº 5, pp 222-229.
- Cañas, M. (2015).”Ultrasonic Welded Thermoplastic Composites. An Experimental Study on the Static and Fatigue Behaviour”. Proyecto Fin de Carrera, Escuela Superior de Ingenieros de Sevilla.
- Dube, M., et al. (2013). “Characterization of Resistance-Welded Thermoplastic Composite Double Lap Joints Under Static and Fatigue Loading”. Journal of Thermoplastic Composite Material. pp 1-15.
- Villegas, I.F. et al. (2012). “Process and Performance Evaluation of Ultrasonic, Induction and Resistance Welding of Advanced Thermoplastic Composites”. Journal of Thermoplastic Composite Material. 26 (8). pp 1007-1024. 30% 50%