Desarrollo de nuevos SMC de altas prestaciones mecánicas basados en resinas epoxi y viniléster
Responsable de la Línea de Materiales Termoestables de Gaiker Centro Tecnológico01/11/2005
- Piezas destinadas al sector naval: Deben presentar unas adecuadas prestaciones mecánicas, apoyadas por la ligereza en su composición y buen acabado superficial, etc.
- Los destinados al sector de revestimientos: Deben presentar unas excelentes propiedades de aspecto superficial, así como unas propiedades a abrasión adecuadas.
- Los destinados a sectores de altas prestaciones mecánicas (eólico, vestuario de seguridad, construcción): Deben presentar unas excelentes propiedades mecánicas, generalmente a impacto, flexión y compresión.
- Las destinadas al sector de abrasivos: Deben presentar una resistencia a la abrasión adecuada y una rigidez o resistencia interlaminar en condiciones de funcionamiento (giro a alta velocidad).
- Las destinadas al sector eléctrico. Las propiedades de los plásticos composites como aislantes eléctricos, su resistencia mecánica, su alta resistencia al calor, a la humedad y su durabilidad hacen de ellos el material adecuado para este tipo de aplicaciones.
Los materiales utilizados para la fabricación de los preimpregnados han sido de diversos tipos de matrices; epoxi, viniléster-epoxi (resinas de última generación) y vinilésteres comunes, aditivos de formulación (agentes reforzantes, ayudantes de proceso, etc) y refuerzos varios (tejidos bidireccionales, mats y tejidos híbridos), pero manteniendo las características comunes en los SMC procesados ( gramaje, porcentaje de fibra de vidrio, % agentes comunes,…..) con el fin de realizar una correcta comparación entre ellos en sus prestaciones finales.
Por su parte, el método de transformación elegido ha sido el de compresión en caliente ya que permite una cadencia de producción muy grande debido a que se obtienen tiempos de ciclo bajos, con inversiones relativamente bajas.
El preimpregnado fabricado presenta unas condiciones de procesabilidad, manipulabilidad y reactividad adecuada (temperatura y pico de exotermia de curado) y la caracterización de la pieza fabricada se orienta a la condición final de uso a la cual va destinada y que ha quedado definida en párrafos anteriores.
Como conclusiones más destacadas se pueden apuntar que los preimpregnados diseñados en el proyecto permiten competir con los habitualmente utilizados en los sectores tradicionales. Así se puede apuntar de los preimpregnados desarrollados:
- Los preimpregnados de base viniléster cargados con nanopartículas para el sector de recubrimientos presentan unas propiedades de acabado superficial y resistencia a abrasión adecuadas, sin embargo no proporcionan el aporte en las prestaciones mecánicas esperadas, no sobrepasando a la lana de roca o microesferas.
- Estos mismos preimpregnados, cargados con lana de roca, permiten alcanzar unas prestaciones mecánicas comparables a los de naturaleza epoxídica, matriz destacada por su aporte mecánico.
- El uso de lana de roca con microesferas, proporciona una interesante combinación en cuanto al aporte de prestaciones mecánicas, pero dificulta el procesado por el incremento en su viscosidad.
- Los de naturaleza viniléster-epoxi, resinas de última generación, presentan unas propiedades mecánicas al impacto y flexión adecuadas para la sustitución de los preimpregnados de base exclusivamente epoxídica de difícil manipulación y conservación.
- Los preimpregnados en base a resina epoxi presentan la limitación de su conservación, quedando reservada a – 20 º C para la correcta manipulación.
- Una disposición sandwich en compresión de los prepreg desarrollados, (tejidos bidireccionales en las caras exteriores y el interior de fibra corta) permite definir la disposición óptima para alcanzar las mayores prestaciones.
- La optimización de los porcentajes del desmoldeante interno y del aditivo termoplástico en el seno de la pasta resínica resulta determinante para alcanzar las máximas prestaciones.
Los materiales termoestables y especialmente las estructuras tipo sandwich basadas en estos materiales han ido adquiriendo una importancia creciente en sectores claves como el aeronáutico y la construcción, sustituyendo a los materiales metálicos debido principalmente a sus buenas relaciones prestaciones/peso y la enorme resistencia que implica la utilización de estos materiales.
Los principales motivos para que el uso de estos preimpregnados se haya visto aumentado son entre otros su costo competitivo, su aislamiento eléctrico, buen comportamiento a altas temperaturas y alta resistencia a medios abrasivos y ambientes corrosivos.
La siguiente tabla muestra los consumos en toneladas de preimpregnados de los principales mercados:
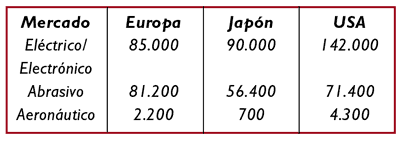
La novedad tecnológica que aporta dicho estudio es la aplicación de la técnica de compresión para la fabricación de piezas que actualmente presentaban un alto componente manual y requerirán de altos tiempos de ciclo debido a las técnicas aplicadas (autoclaves, laminados manuales fundamentalmente).
Hasta ahora en muchos sectores de aplicación de los composites se ha primado por encima de todo la seguridad y la relación prestaciones/peso, quedando el coste en un segundo plano. Hoy en día, y debido a la creciente competencia, el coste ha ido ganando progresivamente importancia y de ahí, el pensar en procesos más competitivos. Por ello el objetivo fundamental es aumentar la productividad y disminuir así el coste de mano de obra sin obviar las prestaciones mecánicas requeridas.
Existen otros sectores de aplicación para este tipo de materiales, generalmente relativos a altas prestaciones mecánicas:
- Sector eólico. Actualmente se utilizan preimpregnados de naturaleza epoxi en las aspas de los molinos de viento, debido a las altas prestaciones mecánicas que deben presentar estas piezas.
- Sector ocio-deporte. Son muchas las aplicaciones en este sector que utilizan este tipo de materiales: quillas, cascos de protección, etc.
- Sector calzado. Las punteras de los zapatos de seguridad deben de superar altos requisitos en propiedades de impacto por lo que es necesario la utilización de preimpregnados de naturaleza epoxi o viniléster-poliéster.
- Sector transporte. En aplicaciones estructurales se están utilizando preimpregnados de tipo epoxi, mientras que en aquellos destinados a revestimientos se utilizan de tipo poliéster y fenólico dependiendo de las exigencias de comportamiento al fuego exigidas.
- Sector abrasivos. Los discos abrasivos utilizan generalmente preimpregnados de naturaleza fenólica aditivados con cargas resistentes a la abrasión como puede ser carburo de silicio, etc.
Desarrollo experimental
- Definición de las especificaciones a cumplir por parte de los preimpregnados fabricados y de las piezas transformadas.
- Búsqueda y desarrollo de materiales adecuados para la fabricación de preimpregnados procesables por compresión en caliente.
- Desarrollo de formulaciones y fabricación de preimpregnados a escala de laboratorio.
- Caracterización de los preimpregnados.
- Transformación de los preimpregnados desarrollados en el molde a escala de laboratorio.
- Caracterización de las piezas transformadas.
Medios Técnicos
Los principales materiales utilizados se pueden resumir en los siguientes:
a) Sistemas resinosos de distinta naturaleza.
- Resina poliéster
- Conjunto resina viniléster y aditivo termoplástico en base a poliéster, con capacidad de madurar con óxido de magnesio. Las prestaciones óptimas de dicho sistema viene definida por un porcentaje adecuado de resina- aditivo incorporada y de las partes de desmoldeante interno.
- Resinas viniléster de última generación con altas prestaciones al impacto. Resinas vinylester-epoxi (1 y 2).
- Resina epoxi común.
b) Cargas reforzantes
- Gel de Sílice.
- Microesferas.
- Lana de roca.
- Polvo de fibra de vidrio.
- Nanopartículas.
c) Aditivos específicos de fabricación
- Agentes maduradores adecuados para los distintos sistemas resinosos: óxido de magnesio para madurar las formulaciones de base poliéster – viniléster, y vinilésteres de altas prestaciones.
- Desmoldeante interno líquido, 1810-HT.
- Agente humectante.
- Agentes catalizadores y aceleradores de polimerización. La catálisis de los sistemas viniléster, poliéster se realizan mediante la aplicación conjunta de calor y catalizadores tipo peróxidos y los sistemas epoxi mediante calor y la combinación del agente endurecedor con los catalizadores amínicos
d) Refuerzos de vidrio de diversos gramajes y naturaleza
- Tejidos de fibra de vidrio bidireccionales de gramaje 800 g/m2 y fibra corta de 25 a 35 mm, para preimpregnados con altas prestaciones mecánicas.
Método experimental
Esta técnica se denomina compound, comúnmente se llama SMC (Sheet Moulding Compound).
La fabricación se realiza en la máquina de fabricación de preimpregnados de SMC. La máquina consta de dos cubetas de dosificación de los sistemas resinosos (como se observa en el esquema siguiente). La capa fina de resina, aditivada según convenga, se dosifica y se deposita sobre un film protector de PA, Polietileno, etc., uno en la cara superior y otro en la inferior. Estas capas de resina empapan el tejido o la fibra cortada y pasan por una etapa posterior de compactación en rodillos de compactación.
La particularidad de este producto es la función jugada por uno de los componentes: el agente de maduración. Este espesante, siendo el más habitual el óxido o hidróxido de magnesio, posee la propiedad de hacer cambiar la viscosidad de la pasta de impregnación en los primeros momentos del proceso. La viscosidad de la pasta, lo suficientemente fluida para conseguir una buena impregnación, aumenta hasta un valor de varios cientos de miles de Poises. El producto se presenta no pegajoso, para lo cual la manipulación es sencilla.
El moldeo de compounds tipo SMC se realiza por compresión entre el molde y contramolde en caliente.
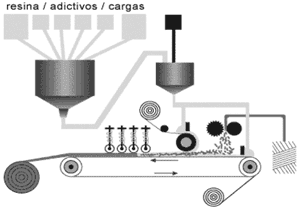
Formulaciones y resultados obtenidos
Seguidamente se modificó la naturaleza de las resinas utilizando siempre el agente reforzante seleccionado como óptimo. Finalmente, se analiza la disposición de las diferentes capas del SMC (alternancia de capas de tejido con fibras cortas).
Así las formulaciones procesadas para un SMC de 2.000 g/m2 de gramaje y constituido por un refuerzo combinado por tejido bidireccional de 800 g/m2 y 110 gr/m2 de fibra corta procedente de robing presentan la siguiente composición:
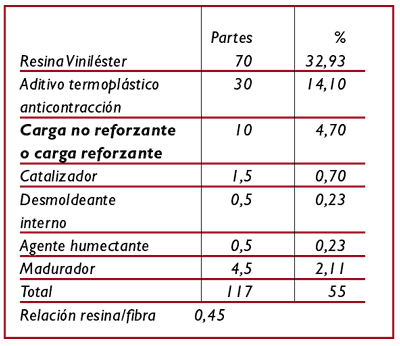
Los agentes reforzantes utilizados han sido gel de sílice, microesferas, lapinus, polvo de fibra de vidrio, nanopartículas y microesferas junto con lapinus.
Los resultados de la caracterización mecánica tras la compresión en caliente a 150º-160ºC en ciclos de 180 s. y una disposición sandwich (tejido en las caras vistas y mat en su interior) de las 2 capas de SMC empleadas para el llenado del molde se pueden observar en las gráficas siguientes (ensayo de impacto Charpy y ensayo de flexión):
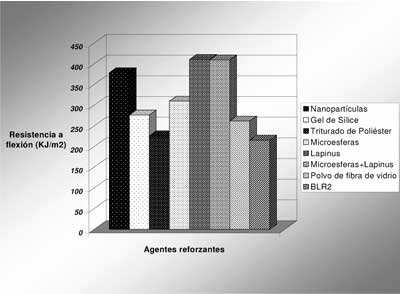
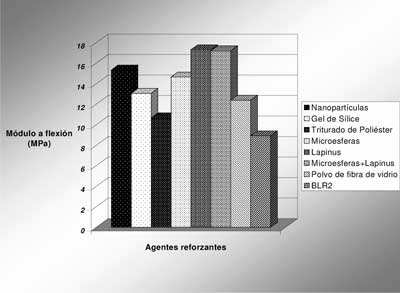
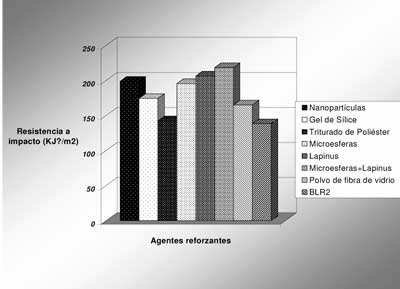
A continuación, se realizaron formulaciones para analizar la influencia del aditivo anticontracción en las prestaciones del prepreg.
Para ello, en las formulaciones desarrolladas se modificó la relación resina viniléster aditivo termoplástico anticontracción estudiando las siguientes proporciones: 70/30, 80/20, 90/10 y 100/0.
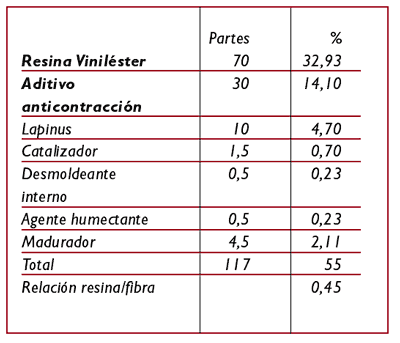