LPMC: un sistema económico de prensado de composites
Los pre-impregnados de baja presión LPMC
Los pre-impregnados con poliéster cristalino Crystic Impreg son materiales cuyo producto final es comparable en características a las que se obtienen mediante el prensado de los SMC tradicionales, pero que requieren entre un tercio y una quinta parte de la presión necesaria para su transformación. Consecuentemente, el coste del equipo y los moldes necesarios se reducen drásticamente.
La menor presión que se necesita para transformar los LPMC y su mayor tiempo de almacenamiento (hasta un año) se deben al distinto proceso que se utiliza para obtener la manejabilidad característica de los SMC. En los SMC, su consistencia se obtiene por la maduración generada por la adición al complejo de óxidos alcalino-térreos, que incrementan progresivamente la viscosidad de su componente poliéster y limitan su vida útil. En los LPMC ( Low Pressure Moulding Compound ), esta viscosidad se obtiene mediante la adición al poliéster amorfo de base -que puede ser ortoftálico, isoftálico, viniléster o retardante a la llama- de un nuevo tipo de poliéster cristalino, que es sólido a temperatura ambiente.
Este poliéster cristalino, desarrollado por Scott Bader y denominado Crystic Impreg, es sólido a temperatura ambiente y funde a 55º C. Sustituyendo parte de la resina de poliéster insaturado de base por el cristalino durante la preparación del compuesto a transformar, que se efectúa en caliente (93º C), actúa como espesante físico al enfriarse el compuesto, por lo que no se precisa un período posterior de maduración (incremento químico de la viscosidad) del material.
Esta característica no sólo le confiere una larga vida de almacenaje sino que permite obtener formulaciones con una viscosidad en caliente bajísima comparada con la del SMC. En el ensayo de flujo en espiral, un LPMC supera a un SMC con la misma formulación en cuanto a contenido de cargas en un 50%. Pero con una diferencia: la presión de pistón para el SMC es 2,5 veces mayor que la del LPMC y al ensayarlo a igual presión de pistón se llega a un recorrido dos veces mayor.
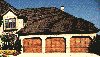
Posibilidades y limitaciones del sistema
En consecuencia, estos materiales permiten reducir de manera considerable la presión necesaria para producir una pieza dada o, alternativamente, hacen posible la fabricación de piezas de un tamaño y complejidad mucho mayores que las realizables con SMC. Se mejora el llenado correcto de costillas y otras formas complejas y es posible utilizar moldes mucho más económicos.
En algunas de las formulaciones, especialmente en las de low profilepara superficies de clase A, se produce una dilatación final (hasta el 0,042%) al fraguado, en lugar de contracción, por lo que pueden presentarse problemas de desmoldeo o de calidad de superficie en moldes con superficies graneteadas o en piezas con costillas estrechas. Sin embargo, este tipo de materiales se suele utilizar en piezas de superficie lisa y brillante, por lo que no es probable que este factor genere problemas. Las demás formulaciones tienen contracciones de polimerización pequeñas.
Las presiones de moldeo pueden llegar a poco más de 1 MPa en piezas de superficie simple, habiéndose producido incluso piezas por saco de vacío. Sin embargo, es imprescindible operar a temperaturas desde 110ºC (hasta 150ºC para ciclos rápidos), lo que dificultaría adoptar este proceso. Las presiones habituales, en función de la complejidad de la pieza, son del orden de 10 a 15 MPa. Como referencia, las necesarias para moldear SMC oscilan entre 75 y 100 Mpa.
La baja viscosidad del fundido y su mínima retracción facilitan la fijación segura de insertos en el moldeo y, más importante, permite impregnar refuerzos adicionales tales como mechas de rovingo tejidos unidireccionales o cruzados en seco, que resultan correctamente impregnados y se eleva así económicamente el nivel de resistencia mecánica del producto final en comparación con los de SMC.
Como los recortes son totalmente recuperables aunque hayan estado fuera de un circuito de refrigeración y puede obtenerse una resistencia mecánica elevada, el proceso disfruta de muchas de las ventajas del moldeo de termoplásticos y de las características mecánicas de los composites semi-estructurales.
Para casos en que se exige la resistencia al fuego que proporcionan las resinas fenólicas, se han desarrollado también formulaciones de LPMC con estas resinas como base.
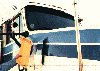
Moldes y máquinas
Con las características expuestas, los LPMC se convierten en una de las alternativas que tiene el moldeador por contacto para efectuar un salto importante en tecnología de proceso sin una inversión de capital excesiva. Para series parecidas, pueden emplearse moldes de la misma construcción que para RTM.
Pero, además, el moldeador de SMC puede aumentar la capacidad de sus prensas sin gasto alguno en equipamiento. Especialmente, le abre el acceso a piezas de una superficie sustancialmente mayor de la que podría realizar con el equipo disponible.
El coste de los moldes es función de las series a realizar y de la calidad superficial de la pieza. En todo caso, al reducirse la presión, las grandes series no precisan de moldes con calidades de acero de alto coste. Pero en las series piloto o pequeñas pueden utilizarse moldes de mortero epoxi resistente al calor, moldes electroformados con superficie de níquel y respaldo de mortero epoxi o moldes realizados por proyección de metal fundido. Los moldes de aluminio precisarán, como en todos los casos en que se presenta la calidad abrasiva de la fibra de refuerzo, un recubrimiento duro con parecida dilatación en el rango de temperaturas indicado.
En Estados Unidos, donde se inició el desarrollo del proceso, se han diseñado prensas específicas. La empresa Hepburn Paradine Plusha elaborado una versión especial para moldear LPMC que tiene un coste 40-50% menor que las equivalentes para SMC. Jesse Engineeringofrece una prensa de 350 T con platos de 1200 \’d7 1500 mm que tiene un precio del orden de 18 MPtas. Stauch, Merva System dispone de prensas que funcionan por un proceso especial que, con parecidas dimensiones, tienen un precio cercano a los 7,5 MPtas y un coste muy bajo de instalación y mantenimiento.
Estado actual de la técnica
En 1980 se calculaba que hacia 1990, el mercado europeo de SMC consumiría 250.000 T/año. Sin embargo, incluyendo SMC y BMC, el consumo de 1992 fue de menos de 230.000 T/año. Scott Bader, conocido suministrador de resinas para fabricantes de SMC consideró que la principal razón para esta deficiencia es que el SMC se basa en un proceso químico de espesado que no es totalmente controlable y que lo sitúa en desventaja frente a materiales alternativos, debido a inconsistencias en la calidad del producto final.
Para superar este problema, la firma británica se embarcó en un programa de desarrollo cuyo resultado son las resinas Crystic Impreg, que permiten el sistema de espesado físico expuesto. En 1989 licenció a la firma norteamericana National Composites( NCI) para el uso de la tecnología Crystic Impreg y NCI diseñó e inició la comercialización del procedimiento LPMC. Al mismo tiempo, inició un programa de desarrollo de mercado, del que vale citar dos ejemplos concretos, cuyas características muy diferenciadas darán idea de las posibilidades del procedimiento.
El primero es la fabricación de tapas para bocas de hombre de alcantarillado. En nuestro país se fabrican en fundición de hierro y son pesadas y con problemas de corrosión. En Estados Unidos, se ensayó el uso de fundición de aluminio, más ligeras y sin corrosión, pero el alto valor de la chatarra de aluminio produjo problemas de hurto. Además, el fallo de ambos materiales es catastrófico cuando se aplican cargas excesivas. La tapa de 500 mm de diámetro en LPMC de 28% de fibra, prensada conjuntamente con mat de fibra contínua en seco, resiste la carga central de prueba de 9.100 kg con una deflexión menor de media pulgada (12,5 mm) admisible, el fallo no es catastrófico sino de fractura gradual y tiene un coste competitivo, moldeada en color.
El segundo ejemplo son puertas para garaje con anchos de 2,4, 2,7, 4,9 y 5,5 m. Para producir los elementos, la firma CDIdesarrolló un juego de moldes de aluminio montados sobre una prensa con placas de 6 \’d7 1,4 m. Cada elemento tiene una altura de 550 mm, por lo que la superficie de los mayores es de más de 3 m\’b2. Estas dimensiones dan idea de las posibilidades de moldeo con estos materiales.
Actualmente, los programas de desarrollo incluyen un LPMC fenólico para los casos en que se exige la resistencia al fuego que proporcionan estas resinas, así como materiales con densidades más bajas y otros que podrán moldearse a temperaturas del orden de 85º C. Estos avances permitirán el moldeo de piezas semi-estructurales con superficies mayores de 10 m\’b2.
El producto final es comparable al que se obtienen mediante los SMC tradicionales, pero requieren entre un tercio y una quinta parte de la presión necesaria para su moldeo. | Las piezas fabricadas con pre-impregnados LPMC, al reducirse la presión de moldeo, pueden ser de un tamaño y un nivel de complejidad mucho mayores que las realizables con SMC. |