Policarbonato para el acristalamiento en el automóvil
Bayer MaterialScience27/11/2007
Una solución para el perfeccionamiento del acristalamiento del automóvil es el empleo de nuevos materiales. En la actualidad, el policarbonato es el único material alternativo aceptado en el mercado y ya utilizado en aplicaciones prácticas.
En este campo, el policarbonato compite tanto con el vidrio templado como con el vidrio laminado. Para utilizar policarbonato en estas aplicaciones es necesario tratar la superficie del material con revestimientos adecuadamente seleccionados destinados a mejorar la resistencia al rayado y a la intemperie.
Esta gráfica comparativa entre el policarbonato y el vidrio templado muestra claramente las diferencias entre ambos materiales: a las ventajas del vidrio –en particular en cuanto a resistencia a la intemperie y al rayado– se oponen el menor peso, la tenacidad claramente mayor y la libertad de diseño del policarbonato.
Por ejemplo, utilizando policarbonato en vez de vidrio en módulos de techo transparentes pueden lograrse ahorros de peso de hasta un 40 por ciento. Las posibilidades de procesado del policarbonato permiten una diversidad de formas y una capacidad de integración, lo que proporciona una gran libertad para aplicar ideas de diseño muy variadas.
El policarbonato se caracteriza por una excelente tenacidad, por lo que su uso en los acristalamientos mejora notablemente la protección de los ocupantes en caso de accidente.
Los mencionados inconvenientes del policarbonato en cuanto a resistencia a la intemperie y al rayado, pueden reducirse mediante los revestimientos a los que se ha hecho referencia, con lo que pueden obtenerse superficies similares al vidrio.
Al seleccionar el tipo de policarbonato a utilizar, es esencial que este presente un perfil de características equilibrado.
Además de la alta tenacidad deseada, debe lograrse una fluidez suficiente, a fin de que las tensiones en el componente sean mínimas.
Esto se consigue utilizando tipos de policarbonato de viscosidad media. Dado que los fabricantes de automóvil demandan características de color específicas para los acristalamientos, las condiciones de pureza exigidas hacen que no se utilicen mezclas de plásticos estándar, sino tipos ajustados especialmente para este tipo de aplicación.
Además de las numerosas ventajas del policarbonato mencionadas, deben citarse retos como:
• El coste
• La resistencia a la abrasión y el rayado
• La resistencia a la intemperie a largo plazo
• La fabricación sin tensiones
• La protección frente a radiación infrarroja
• La rigidez (módulo de elasticidad)
• La dilatación térmica lineal
Estos retos pueden resolverse mediante las correspondientes medidas de diseño técnicas de procesado, o mediante las modificaciones y perfeccionamientos del policarbonato. Estos incluyen p.ej. nuevas formulaciones con una mayor absorción de radiación infrarroja.
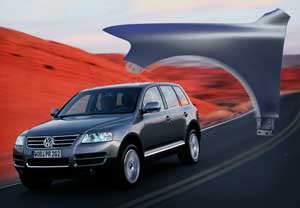
Aplicaciones
Nuevos desarrollos en elementos de carrocería transparentes pasaron a la siguiente etapa en el Smart For-Four, equipado con un módulo de techo fijo transparente.
El avance más reciente en policarbonato lo constituye el techo de laminas del Mercedes Clase A de Daimler-Chrysler.
En la actualidad están en fase de proyecto otras aplicaciones de acristalamiento con policarbonato, que pasarán a la producción en serie en los próximos años. Los principales factores que impulsan estos avances son el ahorro de peso, con la consiguiente reducción del consumo de combustible y el ventajoso descenso del centro de gravedad.
Con ello no se agotan ni mucho menos las posibilidades de aplicación del policarbonato. La siguiente etapa en el desarrollo serán las lunetas traseras de policarbonato, que permiten su integración en un módulo trasero completo de plástico. El aumento de las exigencias en cuanto a la resistencia de la superficie al rayado,
p.ej. en caso de utilizar un limpiaparabrisas, hace necesario emplear nuevas tecnologías de superficie. Un recubrimiento adicional de PECVD (técnica de plasma) sobre el revestimiento duro de silicona, proporciona a la superficie de policarbonato propiedades semejantes a las del vidrio. Un conocido líder tecnológico, ofrece en este campo soluciones integrales que han demostrado su viabilidad en numerosos ensayos y prototipos.
Las aplicaciones de policarbonato pueden compararse en cuanto a costes con las soluciones de vidrio, siempre que se agoten las posibilidades de integración y se comparen los respectivos costes del sistema.
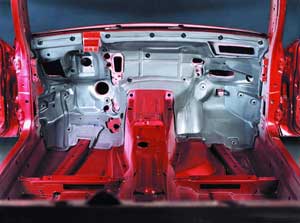
Cadena de proceso
Ya en el desarrollo previo deben tenerse en cuenta todos los procesos parciales: por ejemplo, la calidad del revestimiento del policarbonato depende mucho de la forma de la pieza. Si no se tiene suficientemente en cuenta la dirección del recubrimiento y los bordes de entrada y salida, no es posible lograr una calidad aceptable, en particular en cuanto a las características visuales de la pieza. En ese sentido es altamente recomendable recurrir al asesoramiento de empresas que cuenten con experiencia previa en la producción de piezas de policarbonato, p.ej. fabricantes de materias primas, empresas de moldeo por inyección y recubrimiento, fabricantes de maquinaria y proveedores de tecnología.
Diseño de componentes / criterios aplicados
• Integración de funciones, salientes, piezas de unión, nervios,
dispositivos de encaje, etc.
• Radios
• Transiciones de los componentes anexos
• Variaciones del espesor de pared
• Proporción entre el espesor de pared
y el espesor de los nervios
• Contracción
• Líneas de unión y de flujo
• Inyección de los componentes
• Diseño de la pieza para el recubrimiento
Los principios de integración mencionados pueden llevarse muy bien a la práctica con el proceso de inyección.
El ejemplo de una ventanilla trasera fija, con carril guía y junta integrada, permite ilustrar bien las posibilidades de integración. Ésta incluye
• Perfiles guía moldeados en el mismo componente
• Elementos de fijación
• Guía para la junta
• Elementos de recubrimiento /
protección
Utilizando diversas herramientas CAE es posible elaborar y calcular los diseños correspondientes. Sin embargo, para la aplicación en el sector del acristalamiento del automóvil es imprescindible una amplia experiencia en relación con las exigencias específicas.
Como ejemplos para el uso de CAE en planteamientos específicos para las lunas de policarbonato en automoción, citaríamos los siguientes:
• Cálculo de la fuerza del viento
• Comportamiento acústico
• Dilatación longitudinal
• Simulación de colisiones
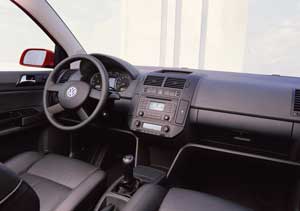
Producción mediante moldeo por inyección
• Llenado suave de la masa fundida
• Moldeo por compresión con llenado de los moldes a presión reducida
• Capacidad de inyectar múltiples
materiales y/ó colores
• grado de libertad para todo tipo
de geometría y tamaño de pieza
• Combinación de la tecnología de máquinas y de moldes, los fabricantes de maquinaria han desarrollado conceptos especiales. Entre ellos figuran, por ejemplo, moldeadoras por inyección equipadas con unidades inyectoras enfrentadas y con una mesa pivotable en torno a un eje horizontal para alojar el molde.
El reto de fabricar componentes que presenten tensiones mínimas con las dimensiones habituales de las lunas se soluciona hoy día mediante el empleo del moldeo por compresión. Otra ventaja de esta técnica es que la presión de cierre necesaria es relativamente baja.
Fundamentalmente se emplean tres técnicas diferentes de moldeo por compresión.
Moldeo por compresión paralelo:
A continuación, la unidad de cierre de la máquina cierra la cavidad ampliada, y la masa fundida es transportada ulteriormente por el movimiento de moldeo.
Moldeo por expansión:
Moldeo en cuña:
Revestimiento
Una típica estructura de capas sobre policarbonato comienza por una fina capa de imprimación, que facilita una buena adherencia entre el policarbonato y la capa antirayado. En segundo lugar se aplica la capa antirayado, significativamente más gruesa. Tanto la capa de imprimación como la laca de cobertura resistente al rayado contienen absorbentes de radiación ultravioleta y estabilizadores UV que proporcionan al sistema resistencia a la intemperie.
Si las exigencias de resistencia al rayado son muy elevadas, es posible lograr una dureza de la superficie similar a la del vidrio, utilizando tecnologías especiales y aplicando una capa adicional de PECVD sobre la laca final.
Tanto la aplicación de la capa de
imprimación como de la laca protectora se realizan preferentemente por “inundación”. Los procedimientos de “spray”, utilizados p.ej. en recubrimientos de policarbonato para faros, no pueden emplearse en las lunas debido a las elevadas exigencias visuales.
Es imprescindible que el revestimiento con los sistemas de pintura, generalmente de fraguado térmico, se realice en condiciones de sala blanca.
En la actualidad el policarbonato se utiliza ya para la producción de lunas en serie y constituye el único material alternativo al vidrio.
Con el policarbonato se abren nuevas y numerosas posibilidades de diseño para el acristalamiento del automóvil. Hoy en día, los principales campos de aplicación son las ventanillas laterales fijas, las lunetas traseras o módulos traseros completos y los techos panorámicos o solares.
Se han desarrollado nuevas técnicas de moldeo por inyección.
El uso de revestimientos superficiales adecuados permite responder a las necesidades de los fabricantes de automóviles.
Para llevar a cabo con éxito un proyecto de lunas para automóvil es imprescindible desarrollar y controlar la cadena de proceso en su integridad.