Carbono y Aramida, del concepto a la producción
La principal dificultad de los PMC es que su temperatura de trabajo está limitada, en la mejor de las situaciones, a unos 350ºC. A temperaturas mayores es necesario emplear composites con matriz metálica (MMC, “Metal-matrix composites”) o composites con matriz cerámica (CMC, “Ceramic-matrix composites”). Adicionalmente, los MMC se adaptan mejor a ciertos requerimientos relacionados con las conductividades térmica o eléctrica, la estabilidad frente a radiaciones... Las fibras de carbono, por sus peculiares cualidades, se pueden usar como refuerzo tanto de matrices metálicas como de matrices cerámicas.
Se atribuye a Edison el uso de las primeras fibras de carbono comerciales, logradas por la carbonización de fibras de algodón y bambú, para producir filamentos de lámparas de incandescencia. Sin embargo, el empleo como refuerzo de estas fibras se sitúa a finales de los años 50. Actualmente, las materias primas (o precursores) para la fabricación de fibras de carbono son, ordendas por volumen de utilización, el poliacrilonitrilo (PAN), determinadas derivadas del carbón y petróleo (breas, alquitranes), y el rayón [2].
Los materiales compuestos reforzados con fibras de carbono son más ligeros y resistentes que determinados aceros al carbono. Su comportamiento frente a la fatiga es superior al de los metales y, cuando se combinan con los polímeros adecuados, constituyen uno de los tipos de materiales más resistentes al deterioro ambiental. Ciertas fibras obtenidas de breas y alquitranes de carbón o petróleo (fibras “pitch”) poseen conductividades térmicas tres veces superiores a la del cobre. Gracias a su conductividad eléctrica, los materiales que contienen estas fibras eliminan con facilidad la electricidad estática (por ejemplo, en componentes de ordenadores). Estas fibras tienen alta temperatura de fusión y no reblandecen con el calor, permitiendo su aplicación a altas temperaturas. Es más, su resistencia mecánica se incrementa con la temperatura en atmósferas no oxidantes [3].
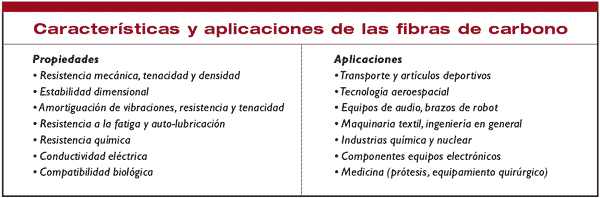
La estructura de las fibras de carbono
Este tipo de estructura implica que la fibra va a presentar una anisotropía en sus propiedades, cuyos valores vienen determinados, entre otros, por los siguientes factores:
- La existencia de fuertes enlaces covalentes carbono-carbono en las capas, en contraste con las débiles fuerzas de van der Waals que actúan entre capas.
- La perfección de la orientación tanto en sentido longitudinal como transversal.
- Presencia de picaduras, poros y grietas.
- El tipo de precursor usado.
- Proceso de fabricación empleado y condiciones en las que se realiza.
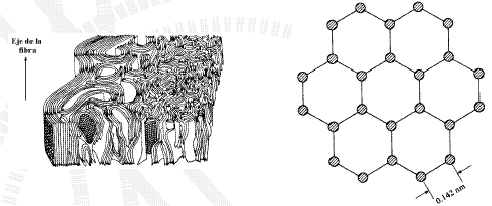
Tipos y propiedades de las fibras de carbono
Las tablas 2 y 3 recogen diversas propiedades para fibras obtenidas de diferentes precursores y con distintos grados de calidad [3]. La anisotropía del refuerzo queda reflejada en la tabla 4, que muestra los valores del módulo de Young en direcciones axial y transversal para cinco fibras seleccionadas [3,5].
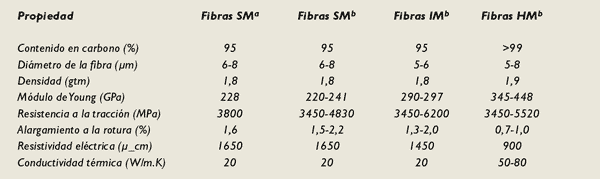
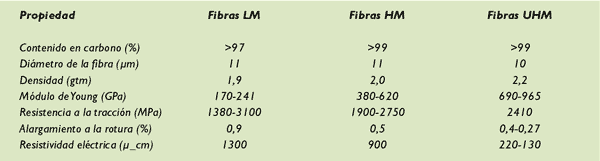

Las fibras de aramida
Las características de ligereza, alta resistencia mecánica y elevada tenacidad han permitido su utilización en numerosos sectores (materiales compuestos, sustitución del asbesto, fabricación de cables y tirantes para sujeción de diversos tipos de estructuras, protección antibalística, tejidos y ropas de protección personal...). Posteriormente, se han desarrollado otras fibras de aramida, entre las que destacan las resultantes de la mejora del primitivo Kevlar y las conocidas con las denominaciones comerciales de Twaron [7] y Technora [8].
Una clasificación útil de las fibras de aramida es la que se realiza atendiendo a los valores de módulos de elasticidad que presentan. De acuerdo con este criterio, resultan tres grupos de fibras:
- De bajo módulo (“low modulus”, LM).
- Con módulo intermedio (“intermediate modulus”, IM).
- De alto módulo (“high modulus”, HM).
La tabla 5 recoge distintas propiedades para fibras típicas de bajo y de alto módulo [3]. El módulo de Young específico es una propiedad clave para el empleo de materiales compuestos en la industria aeroespacial. Los valoes de esta propiedad para las fibras de aramida son más elevados que los correspondientes a las fibras de vidrio, pero inferiores a los que se encuentran con las fibras de de carbono. La temperatura máxima recomendada para el uso continuado de estas fibras es de 160 ºC [9].
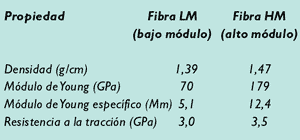
Las fibras de Kevlar
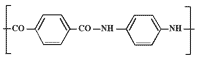
Los procesos utilizados para fabricar estas fibras originan una orientación de las macromoléculas paralelamente al eje de la fibra, con la consiguiente mejora de las propiedades mecánicas en esa dirección. También, la estructura de las fibras es la responsable de la escasa resistencia a la compresión que exhiben estos materiales.
Las características destacadas, y comunes, a las diferentes fibras de Kevlar se pueden resumir en:
- Alta relación resistencia mecánica/peso.
- Rigidez estructural (elevado módulo de Young y bajo alargamiento a la rotura).
- Elevada tenacidad. Resistencia a la fatiga.
- Rotura dúctil, no frágil como las fibras de vidrio y de carbono.
- Son aislantes eléctricos.
- Alta resistencia química. Tolerancia general al deterioro ambiental, aunque la radiación ultravioleta puede degradar el material.
- Pequeña contracción térmica.
- Excelente estabilidad dimensional.
- Alta resistencia al corte.
- Elevado grado de estabilidad térmica (temperatura de descomposición, en aire: 425 ºC).
- Baja conductividad térmica.
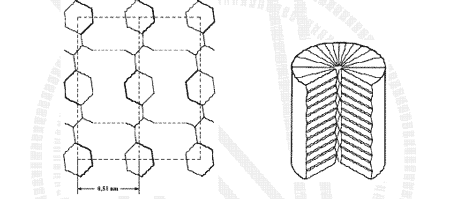
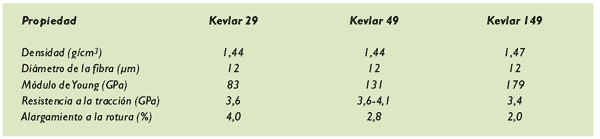
Las fibras de Twaron
Entre las características de estas fibras destacan [7]:
- Baja densidad
- Alta resistencia a la tracción y módulo de Young (rigidez).
- Pequeño alargamiento a la rotura. Rotura dúctil.
- Tenacidad extremadamente alta.
- Elevada resistencia al impacto.
- Escasa fluencia.
- Alta flexibilidad
- Estabilidad y resistencia químicas.
- Bajo (negativo) coeficiente de expansión térmica.
- Temperatura de descomposición térmica de 450 ºC. Altas resistencias al calor y a la llama.
- Estabilidad dimensional.
- Buen comportamiento dieléctrico.
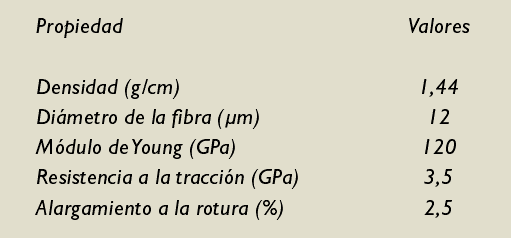
Las fibras de Technora

- Elevada resistencia a tracción.
- Buen comportamiento a fatiga cuando se compara con otras fibras de alta tenacidad.
- Estabilidad dimensional (bajas fluencia y contracción térmica).
- Son aislantes eléctricos.
- Resistencia al calor. Su temperatura de descomposición es de 500ºC. Se puede emplear a 200 ºC durante largos períodos de tiempo. A 250ºC, mantiene más de la mitad de resistencia a la tracción que posee a temperatura ambiente.
- Resistencia química. Exhibe un excelente comportamiento frente a ácidos, álcalis y disolventes orgánicos. Es también resistente al agua al mar y al vapor de agua.
Las fibras de Technora se emplean con diversas finalidades entre las que destacan:
- Materiales para la sujeción de componentes y estructuras (cables, tirantes...)
- Refuerzo de materiales de construcción
- Materiales para la protección y seguridad personal (ropas, guantes...)
- Refuerzo de cauchos y elastómeros (automóviles, maquinaria...)
- Fabricación de composites.
Comparativa de fibras. composites con fibras de carbono o de aramida
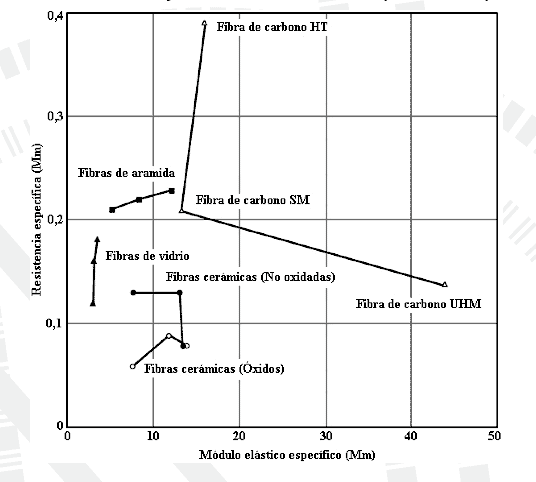
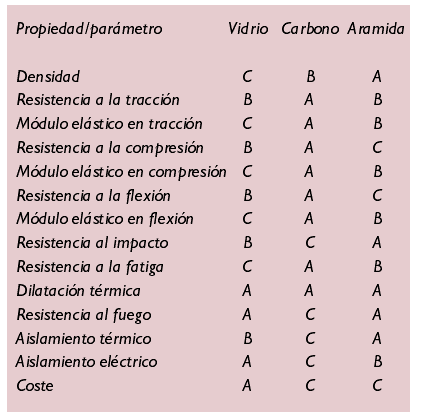
Conclusiones
Las fibras de carbono sobresalen por poseer un excelente conjunto de propiedades mecánicas que superan, en general, a las presentadas por las fibras de aramida. Estas últimas destacan por su baja densidad, su resistencia al impacto y su comportamiento como aislantes térmicos.
Los materiales compuestos con fibras de carbono y de aramida incluyen una amplia gama de fabricados. La mayoría de los métodos de fabricación de composites con matrices poliméricas que contienen estas fibras son similares a los usados para fibras de vidrio.
Bibliografía
- Wallenberger, F.T.: Advanced Inorganic Fibers—Processes, Structures, Properties, Applications.Kluwer Academic Publishers, Dordrecht, Países Bajos, 1999.
- Donnet, J.B. y Bansal, R.C.: Carbon Fibers. Dekker, Nueva York, 1990.
- ASM: ASM Handbook, Vol. 21. Ohio, 2003.
- Johnson, D.J.: Recent advances in studies of carbon fibre structure. Phil. Trans. R. Soc. Lond.A, 294, 443-449, 1980.
- Hull, D.: Materiales Compuestos. Reverté, Barcelona, 1987.
- Dupont.
- Teijin Twaron BV: .
- Teijin.
- Bunsell, A.R.: Fibre Reinforcements for Composite Materials. Elsevier, Oxford, 1988.
- Dobb, M.G.; Johnson, D.J.; y Saville, B.P: Structural aspects of high modulus aromatic polyamide fibres. Phil. Trans. R. Soc. Lond. A, 294, 483-485, 1980.
- SP Systems: .
- Net Composites.
- US Department of Defense : Department of Defense Handbook - Composite MaterialsHandbook - Vol. 2. Polymer Matrix Composites Materials Properties. .
- Bunsell, A.R. y M. H. Berger: Ceramic fibers