Estudio de materiales termoestables reforzados para uso en aisladores eléctricos
Catedrático de ingeniería química, director de postgrado de Ingeniería Técnica Industrial de Bilbao - E.H.U.15/04/2005
A pesar de ello las cadenas aislantes de porcelana y de vidrio tienen algunas limitaciones intrínsecas, como son:
- Limitada resistencia al choque térmico, lo que los hace sensibles a variaciones bruscas de temperatura, a efectos térmicos del arco eléctrico,etc.
- Muy elevada fragilidad, con lo que ello comporta en cuanto la dificultad de almacenaje y transporte, delicada manipulación, sensibilidad crítica a los actos vandálicos (causa frecuente de fallo en líneas eléctricas aéreas de A.T.).
- Elevada densidad, lo que da lugar a un peso excesivo, que en líneas de A.T. (situadas en lugares alejados y de difícil acceso) dificultan notablemente la manipulación y montaje de las cadenas dada la altura de los soportes.
- Alta respuesta a procesos contaminantes, que hacen variar sensiblemente su comportamiento aislante, además de que esta respuesta es dependiente del tipo de contaminación depositada y de las condiciones atmosféricas predominantes en la zona.
Entre los materiales que se han utilizado para aislamiento eléctrico en media y alta tensión cabe destacar:
- los fenol-asbesto,
- las resinas melamina-fenol con carga mixta,
- las melaminas mineralizadas y
- las epoxídicas reforzadas principalmente con fibra de vidrio;
A lo largo de la presente investigación se han ensayado resinas poliéster de altas características y diferentes resinas epoxídicas utilizando distintos sistemas catalíticos (endurecedores) de tipo amínico y de tipo anhídrido tal como había sido planificado, ya que como se verá en el apartado de resultados, las propiedades fisicoquímicas son dependientes del sistema catalítico utilizado. Precisamente las exigencias mecánicas (particularmente las propiedades en tracción han sido las que en principio han dirigido el presente estudio).
Las características de flujo no son relevantes en el diseño de estas piezas ya que pueden diseñarse con geometrías relativamente sencillas. Sólo en los extremos de amarre de los bastones será necesario buscar una solución idónea a las exigencias mecánicas a las que se verá sometida la pieza.
En la selección del tipo de refuerzo será necesario tomar en consideración las elevadas solicitaciones mecánicas a que se va a ver sometido en servicio el bastón aislante. Este mismo tipo y disposición del refuerzo vendrá condicionado por la técnica de transformación que en la hipótesis de trabajo presentada nos inclinábamos entre las opciones de pultrusión y arrollamiento filamentario, técnicas que conducen a materiales composites de las más altas características mecánicas, con la particularidad de ser técnicas de proceso en continuo, lo que reduce costos de fabricación además de permitir incorporar muy elevados contenidos en fibra de vidrio.
En nuestro caso nos hemos decantado por la técnica de pultrusión para lo cual ha sido necesario diseñar y construir la máquina de pultrusión correspondiente.
En fases posteriores del proyecto se deben incorporar, las aletas para aumentar la línea de fuga y el recubrimiento hidrofóbico, lo cual se puede realizar por extrusión o inyección del material hidrofóbico a alta presión. Finalmente será necesario diseñar las uniones a los casquillos finales metálicos.
De acuerdo con estos factores, se estudiarán familias de materiales y formulación de sistemas que se investigarán sistemáticamente pretendiendo finalmente la construcción de prototipos que serán ensayados posteriormente para proponer los resultados que se persiguen en el proyecto que deberán ser industrializables.
2. Metodología experimental
2.1 Reactivos
- Poliéster insaturado (PE420 y PE154)
- Viniléster (VE430 y VE580)
- Epoxídicas ( E-4650, E-4660, E-95 y E-720)
Como catalizadores para las resinas poliéster y vinilésteres se ha utilizado peróxido de metiletilcetona (PMEK); hidroperóxido de butilo terciario (TBHP); perbenzoato de butilo terciario (TBPB); peróxido de benzoilo (PBO) y perisononanoato de butilo terciario.
Para las resinas epoxídicas se han utilizado catalizadores de tipo anhídrido metiltetrahidroftálico (K-4660) y del tipo amínico cicloalifático, concretamente 3-aminometil-3,5,5-trimetilciclohexilamina (K-4650), del tipo amidoamínico, específicamente 3,6-diazaoctano-1,8-diamina (K-490G) y del tipo mezcla de aminas cicloalifáticas con alquilfenoles y alcohol bencílico (K-368V). También se ha utilizado catalizador m-fenilendiamina (m-PDA) específicamente para la resina epoxídica E-720.
Como (co-)catalizadores se han seleccionado dos poliaminas KC-54A y KC- 230J.
Como aceleradores, en formulación conjunta con el catalizador, se han utilizado para los poliésteres insaturados y para las resinas de viniléster octoato de cobalto (al 6%). En el caso de las resinas epoxídicas E-4660 se ha utilizado un acelerador de tipo fenólico, concretamente el 2,4,6-tris (dimetilaminometil) fenol (KC- 4660).
Con el fin de estudiar la influencia que puede causar la incorporación de una carga se ha incluido en la investigación una carga de fácil incorporación y procesado como es el CaCO3 2,5 mm que suma la ventaja adicional de ser la más económica.
Como refuerzo, una vez previamente seleccionada la tecnología de fabricación (pultrusión), se ha seleccionado la fibra de vidrio en forma de roving de hilo plano con designación normalizada EC16-4896(408)706 y un tejido biaxial XET300 y XET305.
* Todos los materiales han sido previamente caracterizados con el fin de que los resultados sean reproducibles.
2.2 Diseño y construcción de la máquina de pultrusión
La máquina de pultrusión consta básicamente de un cantre metálico que soporta las bobinas de roving. La fibra de refuerzo se hace pasar a través de un sistema de guiado por una bandeja que contiene la resina, catalizada (y acelerada) y sale de la misma a través de un sistema de guiado y escurrido del exceso de resina, entrando seguidamente en el molde.
El molde construido en acero inoxidable y pulido ha sido diseñado con una geometría muy estricta para producir barra de 25 mm de diámetro, debe ir sólidamente guiado (en sus dos partes) ya que deberá soportar esfuerzos de tracción complejos (tendentes a desalinear el sistema) y ha sido adecuadamente sobredimensionado a su fijación. El molde debe ir calefactado ya que se ha previsto la operación de pultrusion para que se lleve a cabo a 170ºC para lo que se han calculado 6 resistencias eléctricas exteriores que se fijan sobre el molde.
Igualmente para controlar la temperatura se han previsto 4 taladros para alojar termopares digitales que permitan el control de temperatura del molde. Tres termopares son del tipo K y el cuarto es PT100, mandan una señal a los lectores digitales de temperatura que se han alojado en una caja de maniobra.
Para tracción del pultruido se ha previsto un cilindro oleohidráulico de 4 Tm de fuerza con un recorrido útil de 1.100 mm. Para el pisado del pultruido se ha previsto un cilindro secundario oleohidráulico de 3,0 Tm de fuerza que se monta sobre una cruceta deslizable sobre unos vástagos con rodamientos.
3. Comportamiento de los materiales termoestables durante el curado
Con objeto de obtener una mejor comprensión del fenómeno de curado se ha desarrollado el concepto de diagrama Tiempo-Temperatura-Transformación (1,2) o diagrama TTT (Figura 1). Este diagrama es una representación del tiempo requerido para alcanzar la gelificación y la vitrificación, respectivamente, durante un curado isotermo como función de la temperatura de curado.
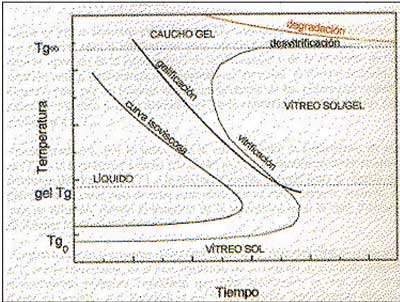
La vitrificación ocurre cuando la temperatura de transición vítrea de la macromolécula, en proceso de crecimiento, es superior a la temperatura de curado y marca la transición desde el estado caucho a un vidrio gelificado (si ocurre la gelificación) o a un vidrio sin gelificar (si la gelificación no ocurre). Por debajo de la temperatura de transición vítrea de la resina sin reticular, Tgo, no sucede prácticamente ningún tipo de reacción dado que las posibles especies reactivas se encuentran inmovilizadas en estado vítreo.
También pueden tener lugar otras reacciones competitivas como la degradación. Si la temperatura de degradación solapa con Tg∞, nos encontraremos en una situación en la cual la resina nunca podría alcanzar conversiones del 100% puesto que entraría en competencia con su propia degradación (5).
Sobre nuestro objetivo de aportar una herramienta utilizable en la industria de transformación con este tipo de materiales, procederemos a la utilización de un modelo basado en los conceptos de Ferry y col. (6) y en la ecuación de Di Benedetto, posteriormente mejorado por Pascault y Williams (7) por su buen ajuste y por la sencillez que implica.
3.1- Cinética de reticulación
Para acercarnos a la situación real del moldeo de resinas de poliéster es necesario que los modelos tengan en cuenta el efecto de la inhibición y las limitaciones de la difusión sobre la velocidad de reacción y la conversión final. Los datos experimentales muestran que la concentración de radicales libres disminuye durante la reacción, con lo que no podremos aplicar el clásico modelo del estado estacionario. Tanto la velocidad de propagación como la de terminación se ven influenciadas por la resistencia difusional.
En ausencia de control por difusión la ecuación general cinética se puede expresar como:
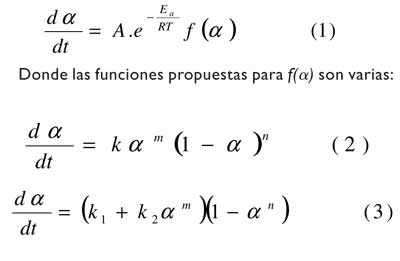
La velocidad de curado es un parámetro proporcional a la velocidad de emisión de calor a temperatura constante:
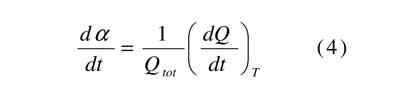
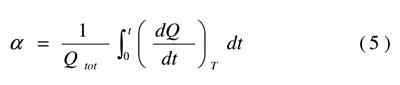
Por tanto, la velocidad de emisión de calor durante el proceso isotermo, (dQ/dt) T, el valor (Qtotal – Qiso)= Qult, la velocidad de curado (da/dt), y el grado de curado, a, pueden deducirse directamente a partir de los datos generados por el DSC. Estos valores pueden ser utilizados para la determinación de expresiones analíticas que representen la dependencia entre a y (da/dt).
Para determinar las constantes cinéticas y los órdenes de reacción hemos procedido a ajustar los datos experimentales, mediante regresión múltiple no lineal utilizando el algoritmo de Levenberg-Marquard. De los cuales se muestra un ejemplo en la figura 2, conduce a la obtención de los parámetros de la ecuación, k, m y n que se reflejan en la tabla 1
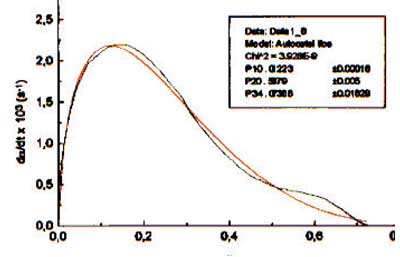
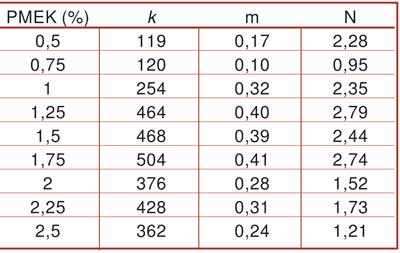
k = A · e –Ea/RT
ln k = ln A – Ea/RT
En la Tabla 2 se encuentran los diferentes valores obtenidos para A y Ea para los diferentes % w de PMEK observándose la dependencia (el aumento) de Ea con la concentración del PMEK lo que confirma la complejidad del proceso cinético.
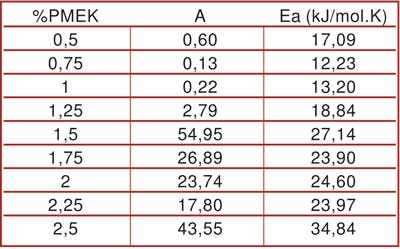
3.2 .- Medida de la reactividad de las resinas
Se han modificado las temperaturas del procedimiento SPI para adaptarlas al sistema catalítico de alta temperatura que se empleará en pultrusión y se ha utilizado un indentador, tal como preconiza el modo de funcionamiento propuesto por SPI (geltimer DIN 55990).
3.2.1- Conclusiones del estudio de reactividad
- En el caso de las resinas de poliéster insaturado parece que la incorporación de carga en la formulación no hace variar el “tiempo de gel” sensiblemente.
Los tiempos de gel más cortos (a la temperatura del ensayo 145ºC) son de 5 minutos y aunque se pueden lograr con cualquiera de los catalizadores ensayados parece que sería el TBHP-70 el más recomendable, ya que, su comportamiento permanece prácticamente constante con la concentración, lo que no sucede con otros catalizadores y/o concentraciones.
Conviene destacar que concentraciones elevadas de catalizador TBHP-70 (≥3,0%) provoca un aumento en el tiempo de gel, por lo que la formulación deberá mantener su concentración por debajo de este límite. - Con referencia a la resina epoxídica E-4660 catalizada con (tipo anhídrido) y acelerada con K-4660, parece que la incorporación de carga disminuye los tiempos de gel para una formulación dada de catalizador y acelerador.
En las formulaciones sin carga los menores tiempos de gel se producen para las concentraciones más altas de catalizador y de acelerador, como cabe esperar. Sin embargo, los elevados tiempos de gel recomiendan operar en fabricación a temperaturas más elevadas con el fin de lograr un curado satisfactorio durante el tiempo de paso por la boquilla de pultrusión. - Con referencia a la resina epoxídica E-4650 catalizada con endurecedor K-4650 y con acelerador KC-230J nuevamente parece evidenciarse que disminuyen ligeramente los tiempos de gel cuando la formulación incorpora carga de carbonato de calcio, no obstante casi es irrelevante su efecto práctico.
Igualmente cabe destacar que los tiempos de gel son ligeramente menores para este sistema resina E-4650-endurecedor K-4650 que los correspondientes a los sistemas anteriores. - Con respecto a la resina epoxídica E-95 catalizada con dos catalizadores diferentes K-368V y K-490G se observa una diferencia sustancial con respecto al resto de formulaciones ya que presenta menores “tiempos de gel” que el resto de las formulaciones ensayadas. Además el efecto de la presencia de carga carbonato de calcio (30%w) no parece influir de forma determinante sobre el tiempo de gel.
En cualquier caso debería notarse que tiempos de gel tan cortos son inútiles para la mayoría de las aplicaciones. Por esta razón se decidió trabajar con la formulación del 45% de endurecedor K-490G, porque su reactividad era suficientemente elevada y además, como se verá más adelante, la dureza Shore D (entre 75-79) es igualmente adecuada (aunque no es tan alta como la dureza 95D que puede alcanzarse con esta resina).
4. Ensayos
Por tanto, se ha utilizado la medida de la dureza Shore D siguiendo las directrices de la norma UNE 53-130-91, utilizando un durómetro fijado sobre un soporte Bareiss para aumentar la precisión y sobre todo la reproducibilidad.
La conclusión general que puede extraerse es que para cualquier porcentaje de catalizador la dureza se encuentra comprendida entre 68 y 80,8 Shore D.
Los valores de dureza obtenidos para este sistema son prácticamente independientes de la presencia de carga y de magnitud similar a los mayores obtenidos con sistemas formulados con E-4660.
La dureza Shore D para la resina epoxídica E-95, en función del porcentaje de endurecedor (K-368V y K-490G respectivamente) tanto para las formulaciones con carga (carbonato de calcio al 30%w) como sin carga parecen evidenciar que la presencia o no de carga no parece influir sobre la dureza alcanzada por la resina cuando se emplea el endurecedor K-368V.
Cuando se utiliza una mezcla de endurecedores se alcanza el valor mínimo de dureza (80 Shore D) cuando la proporción de ambos es igual (20%w), obteniéndose en general mejores resultados de dureza cuando predomina un endurecedor.
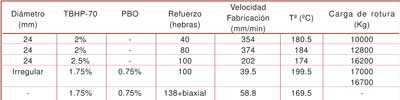
4.2.- Resultados de los ensayos en tracción de los bastones
Los ensayos de tracción se han realizado en una máquina universal de 500KN tipo T/C Denison T.42.B4 con mordazas de apriete progresivo, la inferior móvil y la superior fija. Los ensayos de tracción se han realizado hasta la rotura.
- En poliéster Insaturado Ortoftálico
En la Tabla 3 se recogen los resultados obtenidos para los bastones fabricados por pultrusión sobre la resina de poliéster ortoftálico insaturado utilizando diferentes proporciones del catalizador TBHP-70 y sus mezclas con PBO, empleando diferentes porcentajes de refuerzo (hebras) y diferentes velocidades de fabricación (mm/min), encontrándose el molde a temperaturas de 185±15ºC.
Destaca el resultado evidente del aumento en la resistencia mecánica con el porcentaje de refuerzo.
En cualquier caso los valores que pueden obtenerse de carga de rotura se encuentran dentro de los exigibles para los bastones utilizados en líneas de baja y media tensión. - En resina epoxídica E-4650
Se han estudiado los resultados obtenidos para los bastones fabricados por pultrusión sobre resina epoxídica E-4650 utilizando como catalizador K-4650 al 22%w, manteniéndose constante el tipo y porcentaje de refuerzo (136 hebras + biaxial), encontrándose la temperatura del molde a 165±15ºC y variando la velocidad de fabricación, que se estableció en 3 rangos con objeto de sistematizar su influencia:- velocidad baja (alrededor de 30 mm/min)
- velocidad media (aprox 50 mm/min)
- velocidad alta (más de 70 mm/min)
* En este estudio se introdujo una variable adicional sobre la probeta formulada con 24%w de catalizador K-4650, la cual es someterla a un prolongado proceso de postcurado a 170ºC. El objetivo es constatar la magnitud de ganancia de propiedades que se consiguen mediante esta operación, habitual entre los fabricados con resinas epoxídicas.
El resultado obtenido es que la ganancia de propiedades que se consigue es muy pequeña (1%) sobre unos valores de carga de rotura superiores a los exigibles.
En consecuencia, no parece procedente recomendar ciclos de postcurado posteriores a la fabricación que alargan notablemente el proceso a la vez que lo encarecen innecesariamente. - En resina epoxídica E-4660
Se han estudiado los resultados obtenidos para los bastones fabricados por pultrusión sobre resina epoxídica E-4660 utilizando como catalizador K-4660 (a dos niveles, 75% y 85%) y acelerador KC-4660 (al 2,6%). En todos los casos el refuerzo se mantuvo constante (136 hebras + biaxial) excepto en las probetas nº 5, que se prescindió del biaxial con el fin de comprobar el efecto de su inclusión sobre las propiedades en tracción. Las variables de proceso fueron la temperatura y la velocidad de fabricación.
Parece obtenerse mejores resultados a temperaturas bajas (140ºC) y concentraciones bajas de acelerador (KC), posiblemente como consecuencia del sistema catalítico utilizado. Nuevamente puede notarse (sobre las probetas nº1) que la influencia del proceso de postcurado sobre el material es irrelevante, tal como se había obtenido para los bastones fabricados con la resina epoxídica E-4650.
La resina E-4660 conduce a resultados en tracción iguales (o mejores) que la resina E-4650 teniendo sobre ésta la ventaja de una mayor viscosidad, lo que conduce a una mejor impregnación de las fibras, un mejor llenado de molde y un buen aspecto superficial. - En resina epoxídica E-95
Se han estudiado los resultados obtenidos para los bastones fabricados por pultrusión sobre resina epoxídica E-95 utilizando como catalizador K-490G (45%w). El refuerzo utilizado ha sido el mismo que el empleado en los estudios anteriores con el fin de comparar los resultados. La temperatura de molde ha sido 168ºC.
Con esta resina se logran excelentes resultados de carga de rotura incluso a velocidades altas de fabricación, con un excelente acabado superficial. En sentido contrario debe indicarse que la escasa viscosidad de la resina hace dificultoso el llenado del molde (salvo que se incremente el porcentaje de refuerzo).
4.3.- Resultados de los ensayos en torsión de los bastones
El equipo utilizado ha sido una máquina de ensayos de torsión RIEHLE Mod. PT-10 nº R-91776 debidamente calibrada. Incertidumbre ± 2%. El ensayo se ha realizado a 25ºC con una H.R =62,8% y con una velocidad de ensayo de 0,07 r.p.m.
Los resultados obtenidos han demostrado las mayores cargas de rotura para el sistema basado en la resina E-4660 y la sensibilidad del adhesivo utilizado para la unión de los casquillos metálicos, confirmando por tanto nuestras previsiones.
5. La fractura frágil en barras de aisladores de composite
A estos patrones de rotura se les denomina genéricamente “rotura frágil (brittle fracture)”.
5.1.- Mecanismo de la fractura frágil
Se han encontrado roturas frágiles, tanto en las proximidades o en el herraje terminal, como en la longitud libre de la barra FRP, donde lógicamente la tensión en tracción es menor que en el herraje terminal. Esto nos ha inducido a suponer un mecanismo de la fractura frágil aceptable.
En líneas eléctricas de alta tensión, especialmente 345-500kV o superiores, se producen descargas corona, que generan concentraciones notables de ozono y en presencia de nitrógeno del aire (más si existe contaminación ambiental presente) puede dar lugar a óxidos de nitrógeno que en presencia de humedad atmosférica da lugar a ácido. Si esta disolución penetra en los herrajes puede producirse la rotura frágil.
Aunque es necesario confirmar experimentalmente este extremo, creemos que el aire húmedo puede ser suficiente para producir la rotura frágil. Si hay pequeñas gotas de agua en el aire o si la humedad está sometida a efecto corona, se formará ácido nítrico rápidamente (13).
Bajo el punto de vista químico, incluso pensamos que el NO2, que se forma durante esta reacción, podría reaccionar rápidamente con los polímeros, los aditivos, los agentes de tratamiento interfacial, etc., por ser una especie muy reactiva. Esto podría crear problemas adicionales ya que el agua podría formarse incluso por la propia reacción de la matriz polimérica (no siendo necesario que sea de procedencia exógena). Esto justificaría la rotura frágil incluso en lugares extremadamente secos, aunque es mucho más probable (si es cierta esta hipótesis para el mecanismo de fractura frágil) que se produzca por la entrada externa de humedad. Como consecuencia, se hace necesaria una extremada precaución para evitar la entrada de agua o vapor de agua al interior de la barra, siendo éste uno de los objetivos de una etapa posterior de este proyecto.
Es decir, si hay descargas en corona (14), la barrera polimérica podría descomponerse y uno de los productos de la reacción podría ser el agua. Así tenemos NO2 (procedente del N2 del aire y O3 producido en la descarga) y agua procedente de la reacción de los componentes de la resina; es posible la formación de ácido nítrico sin suministro externo de agua, lo que podría justificar la rotura frágil incluso en lugares extremadamente secos. Esta es una hipótesis de trabajo sobre la que estamos trabajando para determinar las condiciones bajo las cuales se puede producir rotura frágil en los bastones aislantes de composite (6,7, 15).
Existe la posibilidad de diseñar los aisladores de forma que el recubrimiento de goma se extienda incluso dentro del herraje; otro diseño de fabricación es realizar la operación de recubrimiento extendiendo la goma por encima de los herrajes terminales, con lo que se tiene una interfase y una protección frente a la penetración de humedad; finalmente se podría pensar en no tomar precauciones en la interfase de recubrimiento, en cuyo caso el elemento en las condiciones de servicio, se formará un gap entre el end-fitting y el housing que posibilitará la entrada de agua, incluso por lluvia.
La causa de que el ácido nítrico influya tanto es debido a que resulta extremadamente agresivo para la fibra de vidrio utilizada en la barra (fibra de vidrio tipo E, eléctrico). Esta fibra de vidrio tiene tres componentes básicos: sílice, alúmina y calcio. Cuando el ácido ataca a la fibra se produce un intercambio iónico de los cationes por H+ procedentes del ácido. Esto debilita las fibras y así, bajo tensión mecánica, se romperán. Esto conduce a una tensión en la superficie de la fibra de vidrio capaz de producir fisuras en espiral (spiral cracks) sobre la superficie de la fibra.
Sin embargo, también es posible la formación de ácido oxálico como consecuencia de las descargas eléctricas, especialmente si existen enlaces hidrocarbonados (4,5) y en el caso más frecuente de resinas epoxídicas reforzadas con fibra de vidrio (17). También podremos demostrar que la agresión por ácido oxálico es, incluso, más perjudicial que la producida por ácido nítrico. Finalmente es esperable que los bastones construidos con fibra de vidrio E/ poliéster insaturado fallen antes que los fabricados en resina epoxi/ fibra de vidrio, ya que los lugares más vulnerables para el ataque químico son los enlaces éster. La práctica ausencia de enlaces éster en la cadena epoxídica de un viniléster le hace menos susceptible que al poliéster frente al ataque por ácidos fuertes. También se encuentran resultados de investigación en sentido diametralmente opuesto.
Un área especialmente sensible es la unión de los herrajes finales y el recubrimiento. En esta área los tres materiales en contacto tienen diferentes coeficientes de expansión térmica y deben estar permanentemente unidos para evitar la entrada de humedad.
Hay varios tipos de fibras de vidrio que muestran mayor resistencia a la corrosión bajo tensión. Se sugiere que el refuerzo de fibra de vidrio debe considerarse como el factor más importante en la resistencia a la rotura frágil.
Puesto que, razonablemente, el contenido en B y Al en el vidrio podría ser una potencial causa de formación de grietas y cracks y, en definitiva, de la corrosión bajo tensión que conduciría a la rotura frágil, nos propusimos analizar el comportamiento de una nueva fibra de vidrio (fibra Z experimental) baja en B y Al.
Con ánimo de probar la hipótesis de trabajo se ha establecido el objetivo de analizar:
- La posible existencia de grietas o cracks en el interior de las barras pultruídas que permitirían la difusión de agua por su interior.
- Los resultados de los ensayos de corrosión de las fibras de vidrio de refuerzo bajo diferentes agresivos y concentraciones.
5.2.- Ensayo de corrosion de las fibras bajo diferentes agresivos
Después de la agresión, se ha cuantificado la pérdida de peso sufrida (siguiendo el procedimiento gravimétrico estándar) como consecuencia del ataque y eventual disolución de los componentes de las fibras, lo que nos permitirá proponer un mecanismo de actuación del agresivo.
5.3.- Ensayo de penetración de colorante
6. Resultados y discusión
6.1.- Efecto producido por los agresivos químicos
- La F.V. normal (tipo E) si es atacada con ácido oxálico, aparentemente, presenta algunas anomalías, aunque la pequeña magnitud de las variaciones no permite extraer conclusiones. Será necesario recurrir a un ataque más prolongado por parte de los agresivos si se quieren extraer conclusiones. En cualquier caso, incluso a bajas concentraciones y durante corto espacio de tiempo, parece que la agresión por parte del ácido oxálico es más importante de lo que cabe esperar solamente considerando su constante de ionización.
- La F.V. normal (tipo E) pierde más de un 1 % en peso con el ataque de ácido nítrico. Este es un aspecto a tener en cuenta, ya que, debido a la lluvia ácida en presencia de contaminación urbana e industrial se puede formar fácilmente este tipo de ataques a las barras aislantes.
- También será necesario considerar el ataque por ácido sulfúrico, presente también en la lluvia ácida, especialmente de origen industrial, ya que parece tener una importancia notable.
Con el fin de confirmar la agresión sobre la fibra de vidrio E y Z se ha realizado un segundo ensayo de agresión utilizando concentraciones superiores de los agresivos (1 M) y durante un tiempo más prolongado, ya que, se han mantenido sumergidas las fibras de vidrio E y Z durante 52 días (1250 horas) al cabo de los cuales se han lavado las fibras, se han secado en estufa, y acondicionado higrotérmicamente según indica UNE.
Las conclusiones que pueden extraerse de los resultados del 2º ensayo son:
- Destaca la elevada resistencia, en general, que presentan las fibras del tipo bajo contenido en B y Al frente a las fibras de vidrio convencional tipo eléctrico (E), aunque éstas superan a las primeras en resistencia a los álcalis.
- A largo plazo, la pérdida de peso es notable para ambos tipos de fibras de refuerzo, siendo particularmente destacable la pérdida producida por la agresión por el ácido oxálico (lo que sin duda justifica la pérdida de propiedades mecánicas y la fractura frágil e incluso que ésta se produzca cerca del extremo energetizado del aislador).
- La agresión producida por los ácidos nítrico y sulfúrico, presentes en las atmósferas contaminadas de tipo industrial y urbano, es también destacable, por lo que será necesario diseñar revestimientos y uniones lo más estancas posibles.
Basándonos en estos datos, parece sencillo recomendar composiciones de fibra de vidrio libre de boro, para las barras. Sin embargo, al tratarse de un aislador, deben tomarse en consideración las propiedades eléctricas
6.2.- Ensayo de penetración de colorante
6.3.- Ensayo de penetracion de agua o de humedad
7. Fabricación de bastones aislantes de composite utilizando como refuerzo fibra de vidrio “Z” (Baja en B)
Se partirá de la formulación optimizada de la resina (E-4660) en la etapa anterior (referida al estudio de resinas), y se incorporará el mismo número de hebras de roving, sólo que, en vez de ser FV-tipo E, será FV-tipo Z (baja en B/Al). Puesto que los efectos de corrosión se manifestarán a largo plazo, el ensayo que se utilizará es la medida de propiedades mecánicas y la pérdida de las mismas después de someter las barras de composite a una intemperización acelerada en un ensayo de larga duración.
Esta puede ser una buena medida del comportamiento de estos elementos cuando se encuentren en servicio (ya que hay que garantizarlos durante períodos > 20 años).
7.1.- Metodologia experimental
La fibra de vidrio que forma el roving es del tipo Z (bajo contenido en B/Al) de 2400 tex y está distribuida por 136 bobinas.
Procediendo en las condiciones de anteriores procesos de pultrusión se fabrica la barra a una temperatura de molde de 140ºC y con una velocidad de fabricación de 177,8 mm/min. A la salida se deja enfriar la barra y se corta a longitudes adecuadas para la ejecución de los ensayos.
A partir de estas barras se hace una subdivisión, sometiendo parte de los
especímenes a postcurado (150ºC/ 4 días) y dejando otras sin este post-proceso para investigar si esta operación tiene efecto sobre las propiedades mecánicas.
7.2.- Ensayos de intemperizacion acelerada
- Después del ensayo de intemperización acelerada se medirán las propiedades mecánicas en tracción sobre una máquina d ensayos Denison T/C T.42.B4 para obtener una gráfica de carga de rotura (daN) y desplazamiento máximo (mm).
- También se miden probetas sin intemperizar del mismo lote como contraste y para comparación con vidrio E.
- Se reservan una serie de bastones para recubrirlos con silicona en la siguiente etapa del proyecto.
7.3.- Resultados de los ensayos realizados sobre los bastones aislantes de composite que emplean fibra vidrio z (baja en b/al).
7.3.1.- Ensayos mecanicos
- Nuevamente se constata el escaso efecto que produce la operación de postcurado sobre las propiedades mecánicas, por lo que puede prescindirse de esta operación en el proceso productivo industrial, lo que facilita notablemente la organización.
- La intemperización acelerada produce un aumento en la resistencia máxima y en el módulo del material, aspecto que hemos descrito en trabajos anteriores y por parte de otros autores.
- La carga de rotura en tracción para bastones aislantes de composite fabricados con fibra tipo Z (baja en B/Al) es menor que la obtenida con refuerzos del tipo E, aunque cubre sobradamente las especificaciones técnicas requeridas para MT y HT. Además, la manipulabilidad de las fibras y el propio proceso de fabricación es más complejo que con fibras del tipo E. Se aprecia que existe una mayor contracción y tendencia a pegarse al molde de la máquina de pultrusión, lo que es razonable dado que el B es un componente anticontracción de probada eficacia en vidrios. Probablemente este es un objetivo que debería estudiarse en el futuro.
7.3.2.- Ensayos de resistencia dieléctrica
En la tabla 4 se muestran las composiciones químicas de dos suministradores de FV baja B/Al que se han utilizado para preparar especímenes de ensayo, al objeto de hacer una autocontrastación de materiales. Si bien, los ensayos de difusión de agua y penetración de colorante fueron satisfactorios en ambos casos y los valores de carga de rotura fueron comparables en ambos tipos de FV baja B/Al, no sucedió lo mismo en 3 ensayos realizados (cf. ASTM D-149) para medir resistencia dieléctrica.
Este ensayo utiliza una muestra grande (30 mm) y el ensayo implica introducirla en agua desionizada conteniendo 0,1% w. NaCl durante 100 h, inmediatamente antes de someterla a la medida de la corriente de fuga (mA). La especificación establece que cuando la muestra se expone a 12 kV durante 1 min, no debe producirse perforación, ni flashover superficial y la corriente de fugas durante este ensayo no debe superar 1 mA.
Los resultados muestran que el material hecho con FV libre de B procedente del suministrador 1 presenta mucha mayor dispersión entre sí y la corriente de fugas es 10-43 veces mayor que los procedentes del suministrador 2, y las muestras estaban calientes al finalizar el ensayo. Este comportamiento probablemente está asociado con la no adecuación del método de fabricación ya que la FV tipo Z, merecería dedicarle
un esfuerzo de investigación futura (probablemente mediante análisis SEM y métodos térmicos).
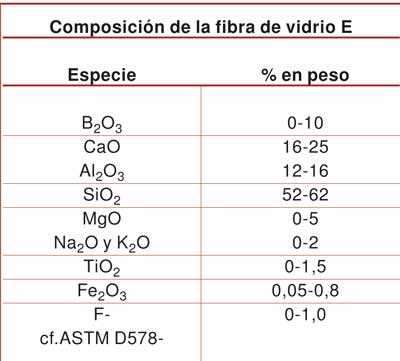
Bibliografía
- Kumosa, M.S.; Final report, July, 1992 through June 30, 1994, Dpt. Materials Engineering, Oregon Graduate Institute of Science and Technology, Portland, Oregon 97291-1000.
- Kuhl,M.; “FRP Rods for Brittle Fracture Resistant Composite Insulators” IEEE Trans. On Dielectric and Electrical Insulators, Literature Digest, October (1999)
- Chughtai, A.R.; Smith, D.M.; Kumosa, M.; Journal of Composites Science & Technology (1997).
- McMahon,E.J.; IEEE Trans. E 1-3, 3 (1968)
- Mayoux, C.J.; J. Phys.D. : APL Phys. Vol. 20, pp 69-74 (1987)
- Valea, A.; et al. “Estudio del comportamiento de una resina epoxídica curada......” Memoria Proyecto Investigación UPV-EHU /99. (2001)
- Valea Pérez, A.; Mondragón Egaña, I.; Vilas Vilela, J.L.; González Arce, M.L.; “Identificación de la fractura frágil de los bastones aislantes de composite”. Anales de Mecánica de la Fractura vol. 19, pp.275-281 (2002).
- Smith, T.H., Chu, W.L., J. Polym. Sci: Part A: Polym. Chem. Ed., 10, 133 (1972)
- Lohse, F., Schmid, R., Batzer, H., Fisch, W., Br. Polym. J., 1, 110 (1969)
- Imaz, J.J., Jurado, M.J., Corcuera, M.A., Mondragon, I., Journal Applied Polymer Science, 46, 147 (1992)
- Fernández – Nograro, F., Llano – Ponte, R., Mondragon, I., Polymer, 37, 1589 (1996)
- Mondragon, I., Quintard, I., Bucknall, C.B., Plastic Rubber Proc. Appl., 23, 331 (1995)
- Chughtai, A.R.; Smith, D.M.; Kumosa, M.; Journal of Composites Science & Technology (1997).
- Electric Power Research Institute; “Initial Laboratory and Field Evaluation of Daytime Corona Viewing Technology” Final report TR-113-459 (1999)
- Valea, A.; et al. “Estudio y diseño del revestimiento y separadores de la linea de descarga (fuga)” Memoria Proyecto Investigación UE9/99 (2001)
- Mayoux, C.J.; J. Phys. D. : APL Phys. Vol. 20, pp 69-74 (1987)
- Chandler, H.D.; Jones, R.L.; Reynders, J.F.; Proceedings of 4th International Symposium on High Voltage Engineering, Athens (National Technical University of Athens) Paper 23-09. September (1983).
Trabajo presentado en las 17 Jornadas de Materiales Compuestos organizadas por el Centro Español de Plástico.