Soluciones Haas para el sector de los implantes ortopédicos de precisión
28 de noviembre de 2011
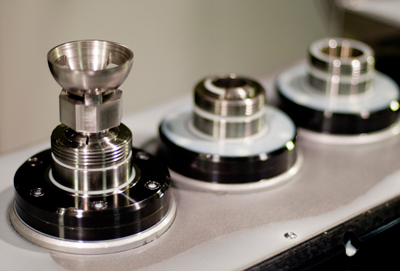
La población mundial está envejeciendo muy rápido. La ONU prevé que en el año 2050 una de cada tres personas del primer mundo tendrá más de sesenta años y una de cada diez habrá superado los ochenta años. Por supuesto, es positivo que la gente tenga una vida más larga y sana, pero un número cada vez mayor de personas padecerá dolencias relacionadas con el envejecimiento de los huesos y las articulaciones. Por suerte, los avances en la tecnología médica permiten que los cirujanos puedan sustituir los huesos y las articulaciones dañadas por piezas fabricadas por empresas como Rochester Medical Implants (RMI). “La gente anhela tener nuestros productos, pero, el día que los necesite, se alegrará de que los fabriquemos”, dice James Evans, presidente y director general de la empresa.
James Evans entró en RMI en 2007 después de una larga carrera en el sector, incluido el puesto de vicepresidente de una de las divisiones de la empresa Corning, encargado del marketing y del desarrollo de productos. “RMI inició su andadura en 1996”, dice, “pero mis socios Marv Selge y Michael Method no entraron en la empresa hasta 2005. Enseguida se dieron cuenta de que su participación no podía limitarse a la de unos inversores pasivos, así que me pidieron que los ayudara. La empresa era proveedora de implantes e instrumental quirúrgico para un gran fabricante de equipos originales. Pero, aunque el listón de calidad de los productos era alto, los procesos internos no funcionaban bien. Era una empresa pequeña, pero faltaba disciplina y la tasa de desperdicio era enorme”. Evans sólo tardó cinco días en darse cuenta de que tendría que cortar por lo sano.
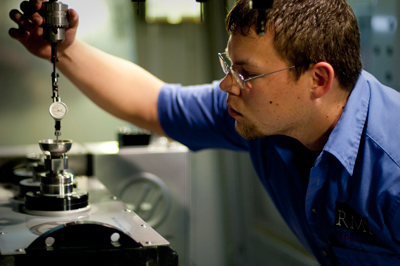
“No fue agradable — admite— pero hubo que actuar rápido para salvar la empresa. Había veinticuatro empleados y sólo queríamos quedarnos con dieciséis. Así que, en mi quinto día, liquidamos a todo el mundo y pedimos a quince de ellos que volvieran el lunes siguiente para que los volviéramos a contratar. Así fue como refundamos la empresa. Por suerte, ya teníamos algunos equipos buenos, como varias máquinas y tornos Haas, pero nadie les estaba sacando verdadero partido. Entonces, Tim Taylor, director comercial de la tienda de la fábrica Haas HFO Midwest, nos visitó un día. No sólo nos dio consejos sobre cómo aprovechar todo el potencial de las máquinas Haas, sino que nos ayudó a encontrar a nuevos empleados, colaboradores y buenos proveedores de herramientas”.
En 2007, RMI empezó a fabricar piezas de Peek-Optima, un material termoplástico ligero pero muy fuerte que se emplea para implantes de larga duración, pero la empresa se topó con un inconveniente: “Los empleados más veteranos no acababan de conseguir buenos resultados, teníamos muchos problemas con las rebabas.” Evans, licenciado en física nuclear y en bioingeniería, nos cuenta que hizo a continuación: “Yo estoy acostumbrado a trabajar con una metodología rigurosa y veía que ése era nuestro punto débil. Así que le pregunté a Tim qué era lo que necesitábamos para mecanizar Peek correctamente. Me puso en contacto con proveedores de herramientas que nos enseñaron a hacerlo bien, lo que me llevó a realizar mi primera gran compra: una fresadora Haas a 30.000 rpm. Fue la única máquina que compramos en 2007, pero, con la precisión de las herramientas y la gran velocidad del husillo, mejoramos mucho y comenzamos a obtener acabados excelente con Peek”.
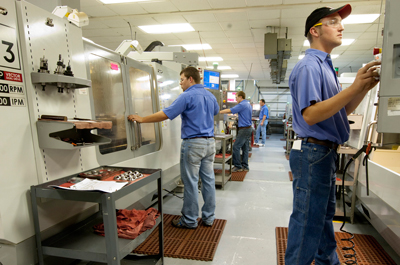
Invertir en personas con talento era otro de los pasos fundamentales para conseguir reflotar a RMI. “Para sacar el máximo provecho de las máquinas CNC, necesitábamos a los mejores especialistas en diseño y fabricación asistidas por ordenador (CAD/CAM) que pudiéramos encontrar, y en esos primeros seis meses tuve la suerte de contratar a dos ingenieros estupendos. Uno de ellos era un programador de Mastercam y al otro lo encontré a través de la tienda de la fábrica Haas. Tim [Taylor] me dijo que la University of Vincennes tenía un centro de formación técnica Haas en el que daban un curso de tecnología de fabricación para estudiantes de tercer año de ingeniería. Sólo en el tercer año hacen ochocientas horas de mecanizado con Mastercam, creación de modelos y fresado vertical con máquinas Haas. Es un vivero de futuros ingenieros, y pude contratar al mejor estudiante de ese año”.
Ahora todos los productos de RMI empiezan con un modelo tridimensional en su sistema CAD/CAM. David Langenkamp, director de producción de RMI, nos lo explica: “Contamos con muy buenos especialistas en CAD/CAM y tenemos tres licencias completas de Mastercam. Así que si el cliente no nos da un modelo en 3D, lo producimos nosotros”. RMI usa luego los modelos para generar programas para las máquinas CNC: “No hacemos programación manual; pasamos los datos directamente de Mastercam a las fresadoras mediante los puertos USB. Así tardamos sólo unos minutos en volver a programar los cambios menores que necesitemos hacer”.
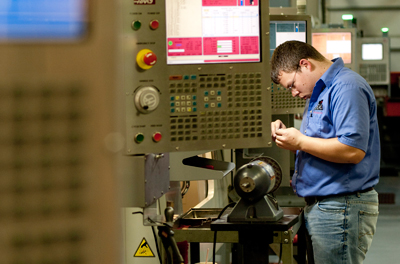
La empresa trabaja con varios tipos de material, como titanio, acero inoxidable, cobalto-cromo, tantalio y, como se ha mencionado, Peek-Optima. “El 75% de los implantes los fabricamos con metal, pero tenemos un departamento sólo para el Peek —dice Langenkamp— porque hay que manejarlo en un entorno muy limpio”. La empresa también registra todos los pasos de fabricación y medición que se siguen de acuerdo con un nuevo sistema de control de calidad, adoptado para conseguir la certificación ISO1345. “Estamos en mitad del proceso de conseguir la certificación AS9100”, continúa Langenkamp, “con lo que mejoraremos aún más el control de calidad, aunque la ISO1345 ya nos da mucha tranquilidad. Lo bueno es que no tenemos que cambiar las máquinas”.
James Evans nos explica por qué: “En 2008, hicimos una puesta al día completa comprando ocho máquinas Haas nuevas: otras dos fresadoras a 30.000 rpm para el departamento de Peek y seis fresadoras a 15.000 rpm para el taller de mecanizado de metal. Hemos seguido invirtiendo en trabajadores y máquinas desde entonces y ahora tenemos un buen equipo: treinta y dos empleados y quince fresadoras verticales Haas (casi todas de cinco ejes). Las máquinas están en marcha cinco días a la semana —en dos turnos—, pero podemos trabajar los sábados si hace falta. Las máquinas muy importantes para que podamos responder de forma positiva y flexible a las necesidades de los clientes, algo esencial para ofrecer un servicio de calidad”.
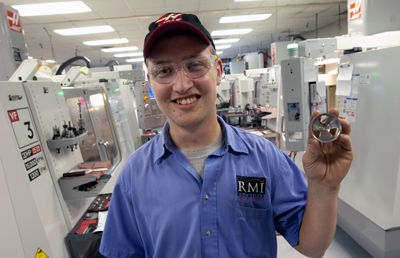
Un buen servicio se consigue con trabajo en equipo, plazos de entrega cortos, ingeniería avanzada, control de calidad, creatividad, eficiencia y buenas máquinas. “Lo peor que podría pasar es que una de nuestras piezas fallara después de la cirugía y causara más dolor al paciente, lo que obligaría a volver a intervenir. Hasta ahora nunca nos ha ocurrido algo así, pero de todos modos, para motivar al equipo, siempre les decimos: Recordad que esto va dentro de un cuerpo humano. ¡No podemos equivocarnos!”.
Alrededor del 80% del trabajo de RMI consiste en fabricar implantes ortopédicos de gran precisión, principalmente para cirugía de columna, y el 20% restante se dedica a la producción de los instrumentos que se utilizan en las propias intervenciones. “También hacemos productos para la cirugía de cadera y rodilla, pero estamos especializados en la columna vertebral —dice James Evans— porque es un mercado que requiere soluciones creativas y ofrece un crecimiento muy estable. “El año pasado crecimos casi un 25%. No sé si alguno de nuestros competidores puede decir lo mismo. Y este año debería ser aún mejor”.
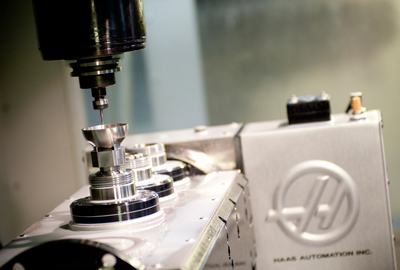
Los cirujanos son quienes tienen las ideas. Por ejemplo, se dan cuenta de que una determinada pieza ayudaría a que un paciente se recuperase. Luego los fabricantes de equipos originales desarrollan esas ideas y contratan a RMI para que las fabrique. “No tenemos la propiedad intelectual de los implantes e instrumentos, pero sí la propiedad industrial de los procesos de fabricación”, apunta David Langenkamp. “Llevamos a cabo muchas innovaciones en materia de diseño. También producimos prototipos rápidos en la Haas Mini Mill, para que el cliente pueda probar el producto antes de mandarlo a la FDA (Food and Drug Administration) para que lo apruebe”.
Otro de los puntos fuertes de la empresa es que es capaz de llevar el producto al mercado en muy poco tiempo. “Un jueves por la tarde nos vino un cliente que necesitaba piezas para una operación que tendría lugar la semana siguiente”, cuenta James Evans. “Pero ni siquiera tenían un modelo en 3D. Organizamos un turno de noche con un par de empleados, trabajamos el fin de semana y al paciente se le implantaron las piezas ¡el martes! No todo el mundo ofrece ese servicio; por eso las empresas confían en nosotros”, concluye.
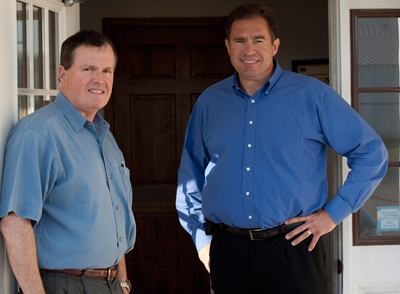