Optimización de costes mediante un mejor empleo del aire comprimido
26 de septiembre de 2011
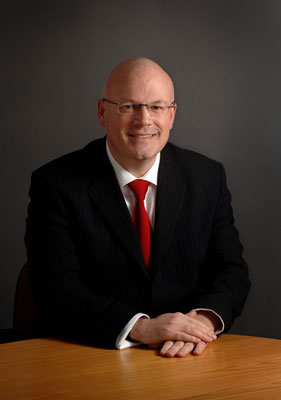
Más del 10% de la electricidad que emplea el sector industrial se destina al uso y empleo de aire comprimido, ya sea para enfriar, secar, limpiar, descontaminar o aspirar. En algunos casos, el consumo de electricidad que se deriva de su uso alcanza el 30% del consumo total de electricidad. A pesar de que sólo el 8-10% de la energía total que consume un compresor acaba convirtiéndose en la energía final necesaria para hacer que el equipo funcione. Lo que representa, evidentemente, un importante derroche energético así como económico.
El aire comprimido se suele derrochar a través de escapes y fugas de aire, la falta de mantenimiento, el uso incorrecto y la falta de control. A lo largo del tiempo son muchas las empresas que no han logrado corregir estos fallos ni tomar la decisión adecuada para optimizar la producción y empleo de aire comprimido, incurriendo, así, en una elevada facturación eléctrica. De hecho, alguna de las razones por las que el uso, y especialmente el abuso, de aire comprimido está tan extendido, es porque es cómodo y fácil de usar. Además, también se percibe como una herramienta gratuita.
Sin embargo, para entender hasta qué punto un mantenimiento regular y concienzudo supone un ahorro de costes, es importante tener en cuenta que el coste del mantenimiento equivale tan sólo al 7% del coste total de funcionamiento de un compresor a lo largo de 10 años.
La reducción de fugas de aire, supone, en este sentido, la mayor vía de ahorro de energía para muchas plantas de producción. De hecho, el ahorro que se logra evitando estas fugas compensa prácticamente por sí sólo el desembolso que se realiza en equipos de detección y piezas de repuesto.
Las fugas de aire son, además, un problema de seguridad por la potencia del soplido del aire y el elevado nivel de ruido que generan. Pueden llegar a causar fallos en los equipos que obliguen a parar la producción, provocando costes derivados del sistema de presión variable, de la reducción de la vida útil y el incremento en el mantenimiento de los equipos, además de tener que aumentar la capacidad del compresor en exceso.
Los puntos en los que se presentan fugas más a menudo son los manguitos, las juntas, las tuberías, las pestañas y juntas de tubería, los reguladores de presión, las válvulas manuales de condensación y llaves de paso que se dejan abiertas, sin olvidar, tampoco, los equipos que consumen aire y se dejan en modo operativo, incluso cuando no se usan.
Por ello, es interesante realizar una auditoría del uso y empleo del aire comprimido en la planta. Este tipo de evaluaciones ayuda a los fabricantes a mejorar su eficiencia energética porque gracias a ella se eliminan las fugas de aire, se emplea menos energía para producir el mismo volumen de aire, facilita consejos prácticos de uso del aire comprimido y asegura, así, que los equipos se usan eficientemente. Algunos de nuestros técnicos han llevado a cabo con éxito auditorías e informes para una gran variedad de industrias, trabajos que han permitido ahorrar energía por valor de miles de euros cada año.
Una detección compleja
Las fugas en un sistema de aire comprimido acostumbran a emitir un pitido difícil de identificar por el oído con el ruido ambiental de una factoría. No obstante, sí se pueden detectar con equipos de detección y lectura de ultrasonidos de última generación capaces de etiquetar y numerar las fugas.
Si tenemos en cuenta las condiciones de funcionamiento de los compresores (tiempo operativo semanal), su coste eléctrico, la presión del sistema de aire comprimido y la eficiencia productiva de cada compresor, podemos cuantificar con exactitud el coste de las fugas de aire para cada máquina, departamento y planta de producción. Por lo tanto, podemos calcular también el ahorro de costes que se obtendría tras una adecuada reparación o mantenimiento.
Estos datos se pueden presentar en un documento dinámico que se actualiza a medida que se reparan las fugas. La monitorización en tiempo real también es posible si se instala un medidor de flujo de aire en el sistema en un punto anterior al equipo de preparación del aire comprimido. Una solución proactiva y duradera que identifica cualquier incremento de uso de aire para así poder investigar y subsanar su origen con rapidez.
Se puede ahorrar más evaluando el empleo de los equipos, determinando si el uso de aire comprimido está justificado. Por ejemplo, su uso para secar tiene un coste más elevado que hacerlo con calefactores, o, incluso, que hacerlo mediante el calor residual del compresor de la planta. Otro ejemplo: las fresadoras eléctricas de ángulo inclinable suelen ser mucho más eficaces que las de aire comprimido automatizadas. Limpiar el serrín, polvo o virutas de la maquinaria con aire comprimido es rápido y práctico, pero también caro.
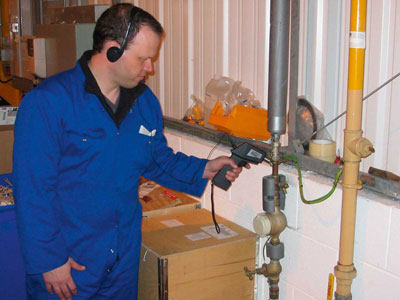
La vía para reducir de forma considerable el uso de aire comprimido, ahorrar costes y mejorar así los resultados pasa por desarrollar una política razonable de uso del aire junto un experto proveedor de equipos así como planificar y realizar un mantenimiento periódico basado en auditorías. En el contexto actual, mediante este tipo de rutinas y procesos de trabajo, pero especialmente a través de la concienciación de la importancia que tiene el funcionamiento correcto del detalle más nimio, podremos ser capaces de mantener la misma capacidad productiva a un menor coste energético.