Hacia el electroconformado de alta velocidad
22 de julio de 2010
Las tecnologías de Rapid Manufacturing se definen como el conjunto de tecnologías de fabricación utilizadas en cualquier etapa de desarrollo o fabricación de un producto, que se genera capa a capa a partir de información digital. El proyecto dispone de tres grandes elementos a desarrollar: la tecnología (al que pertenece el presente trabajo), los materiales y las tecnologías de información y comunicación.
El grupo de investigación ‘Procesos de Fabricación (Centro de Fabricación integrada)’ de la Universidad de Las Palmas de Gran Canaria (ULPGC) participa en varios subproyectos del IB-RM. Dentro del subproyecto dedicado a nueva tecnologías RM la desarrollada por la ULPGC es la denominada ‘High Speed Electroforming (HSE)’ que pretende ir mas allá de los convencionales procedimientos de electroconformado (electroforming), en los que dicho grupo de investigación lleva trabajando durante casi ocho años.
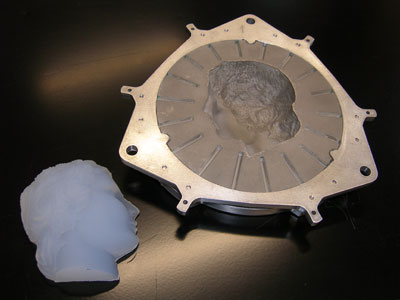
El electroforming es una tecnología que permite crear cáscaras metálicas de cierto espesor, con reproducibilidad de un orden incluso inferior a micras, a partir de un proceso de deposición electrolítica sobre un modelo que previamente se ha hecho eléctricamente conductor. Si se parte de un modelo de material plástico realizado mediante tecnologías de Rapid Prototyping se dispone de un sustrato, en poco tiempo, que permite obtener geometrías complejas incluso con texturas. Una vez se dispone este modelo o patrón se procede al electroconformado que, en realidad, es un procedimiento de deposición aditiva de material metálico pero que, a diferencia de otros existentes en las tecnologías RM, se realiza a nivel iónico, lo que le imprime un plus de enorme precisión y reproducibilidad del modelo de partida. Una vez depositado el material metálico (habitualmente níquel o cobre) la cáscara se separa del modelo y puede utilizarse para diferentes aplicaciones tales como piezas decorativas, elementos mecánicos de precisión, insertos para moldes de inyección, electrodos para electroerosión, etc. Sin embargo el electroforming convencional tiene una serie de limitaciones, que el proyecto pretende superar, y de las que destacan: 1. Velocidad de deposición lenta 2. Falta de uniformidad de espesores que, además de ser un problema para ciertas aplicaciones, tiene un efecto indirecto en el tiempo de fabricación de la cáscara si se tiene que conseguir un espesor mínimo.
El proyecto tiene como objetivo último el fabricar un equipo prototipo denominado EF2-Compact y que incluirá todas las innovaciones que se comentarán posteriormente. El trabajo tiene varios hitos algunos de los cuales ya han sido concluidos y que se basan en las siguientes fases:
- Diseño, fabricación y mejora de un dispositivo de orientación catódica asistido por ordenador.
- Modelización teórico-experimental del proceso de deposición electrolítica para su implementación en el software de simulación y control (ELECFORM3DTM).
- Selección y formulación de baños electrolíticos de alta velocidad.
- Diseño y fabricación de un equipo compacto y modular que, además de incluir las innovaciones indicadas en 1 y 2 permita acercar la tecnología a usuarios que no necesariamente tienen que disponer de formación en procesos químicos o electroquímica.
EF2-Compact pretende ser un equipo HSE de bajo coste para producir cáscaras metálicas de alta calidad fabricadas mediante deposición aditiva iónica. A continuación se describen los trabajos realizados en relación a los puntos 1 y 2 y los objetivos que todavía están en marcha en los puntos 3 y 4.
Descripción del dispositivo de orientación
El dispositivo automático de orientación (DAOC) es capaz de modificar la posición relativa entre ánodo y cátodo (modelo), y en consecuencia la distribución de densidad de corriente sobre este último a lo largo del proceso de electrodeposición. El objetivo es mejorar la uniformidad de espesor de las cáscaras metálicas, y por ende una reducción del tiempo del proceso, favoreciendo el depósito en áreas deprimidas o de sombra de la pieza y en aquellas que se encuentren a mayor distancia del ánodo.
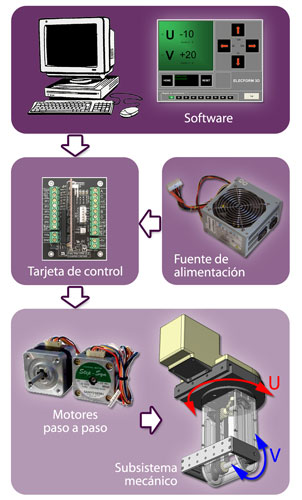
El DAOC es un sistema modular constituido básicamente por un subsistema mecánico de dos grados de libertad y un subsistema de control de posición del elemento terminal del aparato. El control se ejecuta por medio de un software desarrollado específicamente para esta aplicación que dispone de varios modos de funcionamiento que permiten tanto introducir las órdenes de movimiento simples como establecer una secuencia de posiciones óptimas en función de la geometría del modelo, calculadas previamente en el software de simulación. Se ha utilizado un circuito controlador para cada movimiento, que recibe las instrucciones de la interfaz a través del puerto serie RS232 y genera una señal que envía a la etapa de potencia. La tarjeta de control integra tanto la parte de potencia como la parte de control y generación de secuencias de impulsos que se envían a los actuadores.
En cuanto al subsistema mecánico, está provisto de dos movimientos de rotación (U, V) accionados por motores paso a paso unipolares con caja reductora. Se trata de una máquina construida íntegramente en materiales plásticos, lo que garantiza un buen comportamiento ante el ambiente agresivo generado por la composición química del baño electrolítico. Además, es un equipo totalmente hermético, por lo que no hay riesgo de penetración del electrolito al interior de la parte sumergida en el baño, y fácilmente desmontable puesto que se han empleado uniones atornilladas. La sujeción de la pieza modelo se realiza mediante un sistema de sujeción estandarizado, versátil y sencillo, que se adapta fácilmente a una gran variedad de formas y dimensiones de las piezas modelos. El prototipo fabricado, mostrado en la Figura 3, soporta una carga máxima de 1 kilo incluida la cáscara metálica y tiene una precisión de +/-1º medida en el elemento terminal de la cadena cinemática.
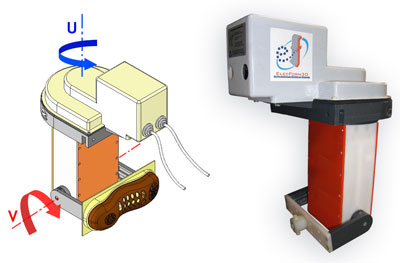
Modelización teórico-experimental
La modelización del proceso de electroconformado ha sido implementada en una aplicación denominada ELECFORM3DTM. Se trata de un software orientado hacia el análisis, simulación y monitorización, que facilita las tareas de diseño y fabricación de las cáscaras obtenidas por este proceso. La versión inicial consta de una rutina de cálculo básica que toma como espesor de partida el espesor teórico ideal proporcionado por la Ley de Faraday, corregido por medio de coeficientes determinados de forma experimental. Esta aplicación proporciona al usuario un primer criterio basado en un análisis estadístico de consideraciones puramente geométricas, para la elección de la secuencia óptima de posiciones de deposición. Además consta de un conjunto de herramientas básicas como son la definición y configuración del equipo, tanto para el electroconformado en posiciones estáticas como para una secuencia de movimientos, así como el conjunto de herramientas necesarias para la definición de esta secuencia en función de los parámetros de configuración del sistema.
En la actualidad se trabaja en una evolución de la aplicación cuyo modelo de análisis consiste en una rutina básica que proporciona el cálculo de la distribución de espesores para una determinada configuración de la célula electrolítica (posición relativa entre ánodo y cátodo) empleando para ello el modelo de la teoría de la teoría de potenciales (Ecuación de Laplace), sujeto a las condiciones de contorno de flujo nulo en las paredes de la cubeta o tanque de electrodeposición, y determinado por las denominadas leyes de polarización en las superficies de los electrodos anódico y catódico. El conjunto es resuelto haciendo uso del método de los elementos de contorno (BEM) combinado con Newton Raphson para tratar la no linealidad impuesta por las condiciones de contorno en las superficies de los electrodos. Se ha considerado el uso del método de elementos de contorno, ya que no es necesario discretizar todo el dominio del problema. Basta con dividir las fronteras o contornos del mismo, por lo que se emplean elementos de superficie y no de volumen. Con esta discretización se logra reducir de forma significativa el número de nodos procesados, lo que los convierte en el método más atractivo para la resolución de aquellos problemas en los que el dominio es grande y sólo nos interesa obtener la solución del problema en la superficie o contornos del mismo.
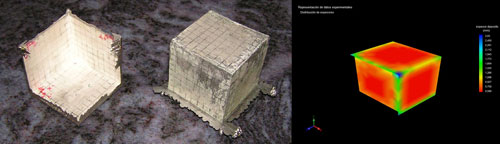
Los primeros ensayos realizados sobre modelos de geometría sencilla (Figura 4), han demostrado que se consigue una mejora significativa de la uniformidad del espesor, sobre todo en aquellas zonas menos expuestas y por tanto más críticas de la geometría del modelo. Además se controla el crecimiento de aquellas zonas más expuestas que introducen una distorsión cada vez más importante a medida que avanza el proceso.
Desarrollos en proceso
Para que la tecnología HSE sea competitiva y eficiente es necesario proponer un nuevo concepto de equipo que vaya más allá de la idea convencional de electroconformado. Las ventajas que se pretenden conseguir con este nuevo concepto son las siguientes:
- Que exista una combinación óptima entre los baños electrolíticos empleados (en función de las aplicaciones) y los medios electro-mecánicos del equipo, de tal manera que la velocidad de fabricación de piezas se encuentre dentro de unos parámetros más competitivos con el resto de las tecnologías RM.
- Equipo compacto, fácilmente manejable y con una imagen de limpieza y seguridad necesaria debido principalmente a la presencia de productos químicos.
- Concepción modular que facilite el grado de automatización y control.
- Coste bajo en relación a otras tecnologías RM.
- Monitorización en tiempo real e interconectividad con software de aplicación diseñado al efecto para optimizar el proceso de deposición electrolítica.
- Abierto a la integración de dispositivos adicionales DAOC, como el comentado en los párrafos anteriores.
- Estabilidad del baño electrolítico, esto es, que no requiera de controles periódicos con excesiva frecuencia.
Con todo esto la solución del diseño conceptual es la mostrada en la Figura 5, donde además de una idea visual completamente renovadora, se pretende romper con la idea de electroconformado como sistemas formados por cubetas, bombas y filtros. El equipo integra sistemas de llenado y vaciado automático de producto electrolítico, que permita una más cómoda manipulación de la pieza, sistemas automatizados de posicionamiento y desplazamiento de la pieza en la cubeta, absoluta hermeticidad desde un punto de vista de derrames accidentales de producto así como sistemas de evacuación de gases, apertura y cierres automáticos. Desde un punto de vista del control se plantea un módulo básico y otro acoplable según los niveles de automatización y control deseados. Existe una interfaz con el software de simulación actualmente en desarrollo para envío de programas de posicionamiento de la pieza.
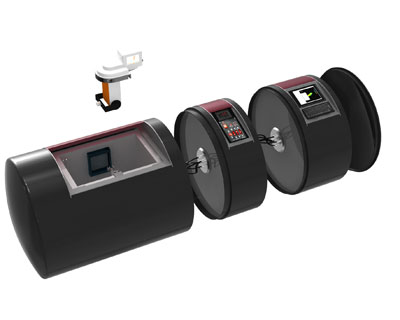
Por otro lado el proyecto IB-RM ha contemplado la valoración de las diferentes opciones de baños electrolíticos existentes y el empleo de aditivos propuestos por el propio grupo de investigación con vistas a mejorar los tiempos de fabricación de la cáscara metálica y su calidad. La idea es establecer una serie de escalas de productos propuestos de tal manera que vayan clasificados en relación a su velocidad pero también en relación al control de otros parámetros que pueden ser importantes en determinados casos, tales como: dureza, resistencia, nivel de tensiones internas, estabilidad del baño. Aunque el grupo de investigación ha trabajado con deposición de níquel y cobre, dentro del proyecto IB-RM los estudios se han centrado tan solo en el níquel.
Conclusiones
Aunque el proyecto IB-RM todavía se encuentra en su ecuador, en relación a la aportación desarrollada por la universidad de Las Palmas de Gran Canaria, ya se han obtenido interesantes avances hacia el objetivo de alcanzar el 'High Speed Electroforming', entre ellos el desarrollo y mejora de un dispositivo de orientación catódico controlado por ordenador, el desarrollo de un software de simulación y análisis basado en elementos de contorno que permite optimizar los desplazamientos del dispositivo (ELECFORM3DTM), los ensayos de dicho dispositivo y los estudios de diferentes posibilidades de baños electrolíticos con el objetivo de mejorar la velocidad del proceso. Por último ya se ha definido la idea conceptual del equipo innovador que recoja todos los avances anteriores y que permita al electroconformado abandonar la vieja idea de que se trata de un proceso lento y que requiere conocimientos químicos profundos al operario que utilice estas tecnologías.
Agradecimientos

Datos de contacto
Edificio de Fabricación Integrada. Campus Universitario de Tafira. Las Palmas de Gran Canaria – 35017.