Tecnología para recubrimientos superficiales
19 de febrero de 2010
Los recubrimientos se especializan en cierta propiedad superficial crítica característica de cada aplicación o tipo de demanda, con la finalidad de mejorarla. Algunas de esas demandas son la resistencia al desgaste y oxidación, el coeficiente de fricción y la dureza, las cuales se combinan para lograr el recubrimiento idóneo para sus condiciones últimas de servicio.
Un factor fundamental es la temperatura de proceso; es conocida la relación directa entre la adherencia de la capa dura y la temperatura de deformación de la misma. Los fenómenos de difusión entre el sustrato y los componentes duros que se forman en su superficie provocan una adherencia superior a la obtenida en los procesos a baja temperatura. La utilización de nuevos materiales base con prestaciones superiores a los convencionales se ha complementado con la mejora de las propiedades superficiales.
Una de las características principales que debe presentar el material a recubrir es la dureza o posibilidad de ser endurecido. Toda capa dura debe poder transmitir los esfuerzos que recibe al material base sin que en él se produzcan deformaciones. Si la dureza del sustrato es insuficiente, esta capa dura y frágil y, por lo tanto, poco deformable, rompe hasta desprenderse como consecuencia del hundimiento del núcleo.
La aplicación de recubrimientos sobre un sustrato permite jugar, como en un material compuesto, con las propiedades de la capa y del material base. Generalmente, las propiedades relacionadas con el desgaste se atribuyen al recubrimiento y las propiedades mecánicas las aporta el sustrato.
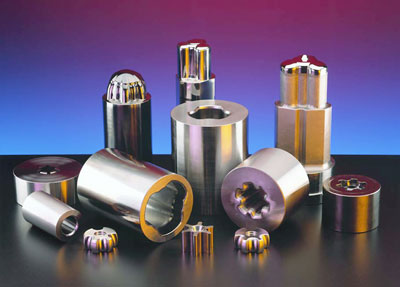
Los recubrimientos de superficies realizados son numerosos y aún así, cada día se descubren nuevas aplicaciones que aportan algunas mejoras en el proceso industrial desde distintos puntos de vista:
- En la producción en lotes de piezas, donde se aplica un recubrimiento que confiere las características superficiales deseadas sobre un sustrato más económico o con mayor resistencia mecánica.
- En la reparación de grandes elementos de máquinas cuya fabricación sea costosa, por haberse desgastado excesivamente o estar mal mecanizadas.
- En aplicaciones especiales y decorativas.
Proyección térmica
La proyección térmica engloba un grupo de procesos donde un material alimentado es calentado y proyectado como partícula individual en forma de gotas sobre una superficie. El equipo de proyección térmica genera el calor necesario mediante gases combustibles o arco eléctrico. Los materiales son calentados cambiando a plástico o fundido y son comprimidos y acelerados hacia el sustrato usando gas comprimido. Las partículas proyectadas impactan en el sustrato de superficie fría, aplastándose y formando placas delgadas, que aumentan superponiéndose partículas, adhiriéndose a las irregularidades de la superficie preparada y entre ellas mismas, produciéndose el recubrimiento de estructura laminar, que no es homogéneo y típicamente contiene cierto grado de porosidad y óxidos en el caso de proyección de metales.
Los materiales de alimentación pueden ser metálicos, cerámicos, polímeros o una combinación de ellos en forma de polvos, alambres o barras; pueden aplicarse bajo condiciones atmosféricas normales o especiales. Los sistemas de proyecciones térmicas son tecnologías respetuosas con el medio ambiente, rápidas de aplicar, flexibles a nivel tecnológico y ventajoso en el tema de recubrimientos de espesores mayores de 100 µm.
La unión entre el sustrato y el recubrimiento puede ser mecánica, química o metalúrgica o una combinación de ambas. El proceso para elevar la temperatura y fundir el material se alcanza químicamente (combustión) o eléctricamente (arco); con ello se consiguen mejoras sustanciales en la resistencia a la corrosión, la resistencia al desgaste y a las elevadas temperaturas. Las propiedades aplicadas al recubrimiento o capa dependen del material de alimentación, del proceso de proyección térmica, de los parámetros aplicados y del postratamiento.
Sistemas de proyección térmica
- Proyección por Llama (Flame Spray o FS)
Este proceso es la forma más antigua de proyección térmica denominado ‘proceso frío’, concerniente al material del sustrato que está revestido y es donde se encuentra el punto más bajo de temperatura el cual permanece sin modificaciones, cambios metalúrgicos y distorsiones. El material es alimentado continuamente hacia el soplete o pistola donde es fundido en una llama de combustión realizada en el aire de una mezcla gas comburente (oxígeno O2) y gas combustible (acetileno C2H2, hidrógeno H2 y propano C3H8), para producir una fuente de calor o llama, utilizándose el aire comprimido para proyectar y acelerar las partículas en forma de gotas fundidas sobre el sustrato, donde fluyen juntas y solidifican proporcionando una capa. La proyección por llama se encuentra limitada para los materiales que se funden a temperaturas más altas que la proporcionada por la llama o para materiales que se descomponen durante el calentamiento. Debido a la temperatura relativamente baja de la llama y la velocidad de la partícula, las capas son generalmente de menor calidad, tienen alta porosidad y bajas fuerzas cohesivas y adhesivas, baja resistencia y espesor limitado.
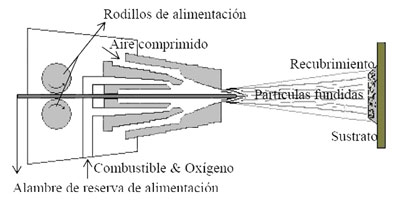
La proyección por llama a alta velocidad (High Velocity Oxy-Fuel Spray o HVOF Spray), se desarrolló a principios de los años 80. Desde entonces, se ha convertido en una de las técnicas más utilizadas y en esta última década ha surgido un notable interés en esta técnica de proyección como herramienta de conformado de piezas. Este proceso, se basa en la generación de un flujo gaseoso de gran velocidad (> 1.400 m/s) originado en la combustión a alta presión y detonación en el interior de la cámara de combustión de una mezcla oxígeno O2 y combustible de un gas C3H8, metano CH4, propileno 2HC = CH – CH3, etileno C2H4, hidrógeno H2, nitrógeno N2, acetileno C2H2) o un líquido (querosén), la mezcla de gases es acelerada a velocidades supersónicas y el material de alimentación en forma de polvo es inyectado dentro de la llama donde cambia a estado fundido o semifundido de tal forma que las partículas proyectadas alcanzan la máxima energía cinética impactando contra el sustrato, formando las capas o recubrimientos de alta calidad con propiedades específicas, extrema densidad (densos), cohesión interna y adherencia (alta fuerza de enlace) al sustrato y con baja porosidad.Los espesores de capa se extienden a partir de 0,000013 – 3 milímetros. Puede ocurrir una cierta oxidación o reducción de óxidos bajos, debido a que en la fuente de calor se obtiene menos temperatura de llama, 3.000 °C, y las partículas por su velocidad pasan menos tiempo dentro.
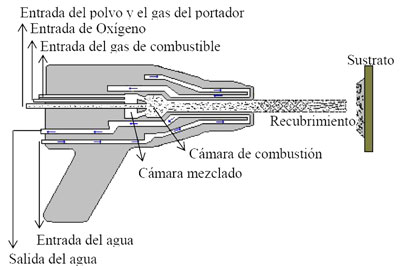
En la proyección por detonación se usa la combustión continua con una serie de explosiones o detonaciones intermitentes controladas, que funden el material de capa transformándolo en partículas y lo proyectan por impacto con alta energía cinética hacia el sustrato, para obtener por acumulación de capas, un determinado espesor. Estas capas son el resultado de la mezcla de gas de oxígeno (O2) y de combustible, comúnmente acetileno (C2H2), junto con el material de capa en forma de polvo, se introduce o alimenta en el cañón, que consiste en un tubo de salida, en cuyo extremo cerrado o final se encuentra la cámara de combustión, y el otro está abierto, refrigerado por agua y limpiado con nitrógeno (N2) después de cada detonación. Dependiendo del equipo usado, hay 1 – 15 detonaciones por segundo. La mezcla de gas es encendida por una bujía en el interior de la cámara, una chispa inicia la detonación, resultando la expansión del gas caliente, que funde y acelera las partículas de los materiales del polvo en un rango de temperaturas que se extienden a partir de 1.100 – 19.000 °C.
Debido a la alta velocidad de impacto, 600 m/s, en que se depositan los materiales comúnmente óxidos y carburos, los sopletes de combustión y los cañones de detonación se pueden usar solamente en los sustratos de metal. El procedimiento alcanza niveles de ruido mayores de 140 decibelios y, por lo tanto, debe realizarse en habitaciones a prueba de sonido y de explosiones. Los espesores de capa típicos se extienden de 0,05 – 0,5 milímetros, aunque pueden obtenerse capas más finas y gruesas. El cañón de detonación se considera el primer proceso de proyección térmica a alta velocidad, donde las características de las capas son menos sensibles al ángulo de deposición que otros tipos de proyecciones. Los recubrimientos producidos con este método son de excelente calidad, con alta resistencia a la abrasión y elevadas temperaturas, pero con un costo muy alto.
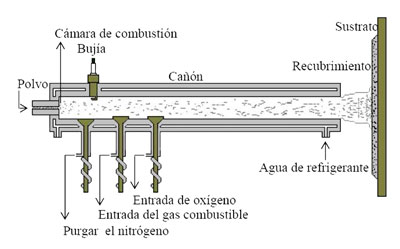
Aimme y la UPV, dentro del expediente Imoca/2006/51 del programa de I+D, en cooperación de Impiva (Instituto de la Pequeña y mediana Industria Valenciana), llevaron a cabo una investigación en la que se aplicó la proyección térmica por llama con uso de polvo mediante HVOF, a fin de encontrar alternativas en el campo de la reparación de las matrices de embutición que se complementen con las tecnologías actuales, garantizándose la función para las que fueron destinadas, antes de ser consumidas, durante las operaciones severas de trabajo contra el deslizamiento interno, rozamiento, deformación e impacto principalmente en sus bordes o aristas.
Durante la investigación llevada a cabo se consideraron distintos factores de los cuales tres variables fueron fundamentales: la composición de los recubrimientos de polvos micropulverizado; las distintas morfologías de roscas de paso; y la temperatura.
El trabajo presentado reportó importantes aportaciones originales, entre las que se destacan:
- La demostración de la aplicabilidad práctica de la técnica de proyección térmica por llama en la resolución del problema basado en recubrimientos para matrices de embuticiones.
- El desarrollo de una metodología para realizar a través de la técnicas de proyección térmica por llama recubrimientos a lo largo de una zona periférica completa o parcial y, además de altura acotada.
- Cómo se puede emplear la técnica de emisión acústica para la resolución del problema de fallos en los recubrimientos realizados a través de la proyección térmica por llama sometidos a cizalladura en las aplicaciones de procesos industriales de matricería.
- La utilidad de la estadística en la solución de todo tipo de problema, en este caso aplicada a la investigación de las características de adherencia en la interfase del sustrato con el recubrimiento.
Bibliografía
- Programa de cooperación Tecnológica entre centros de investigación y tecnología Impiva Imoca/2006/51. Desarrollo de recubrimientos cerámicos nanométricos por proyección térmica para incrementar la resistencia a la corrosión y desgaste en matrices.
- Vilana A., José R., Recubrimiento de Superficies por Proyección Térmica, Revista Habitat, 2002.
- Pawlowski, Lech, The Science and Engineering of Thermal Spray Coatings, 1995.
- Herman, H. y Sampath, S., Thermal Spray Coating, 1996.
- Guilemany C., José M. y Miguel, J. R., La Proyección Térmica en la Ingeniería de Superficies: Posibilidades y Aplicaciones, Jornada Sobre Recubrimientos y Tratamientos Superficiales de Aplicación en Moldes y Matrices, CPT-UB, 26 de Junio de 1997.
- Hermanek, Frank J., Thermal Spraying, 2004.
- Abello Linde, S. A., Proyección Térmica, 2004, pp. 1 - 20.