Cortar formas imposibles, un reto superado
22 de enero de 2010
Teniendo en cuenta que valores como la precisión, velocidad de corte, máxima calidad y facilidad de uso son algunas de las prestaciones más apreciadas, tanto el láser como el chorro de agua han puesto en el mercado diversas soluciones que han ampliado, y mucho, el horizonte de sus posibilidades.
Con el poder del láser
Los sistemas láser, utilizados desde los años 70 en aplicaciones industriales —y en guerras interespaciales, claro, pero ese es otro campo en el que no entraremos— han permitido sustituir a las máquinas tradicionales especialmente en aquellos casos en que la flexibilidad y la programabilidad son de vital importancia en cuanto a la calidad del producto acabado y la eficiencia de los procesos productivos.
El corte por láser es un proceso en el cual se usa la radiación para calentar la pieza, hasta alcanzar la temperatura de fusión, mientras una corriente de gas a presión arrastra dicho material fundido. Y, de hecho, el uso del láser para cortar materiales ofrece muchos aspectos positivos. Por ejemplo, el haz de láser enfocado sobre las piezas actúa como una herramienta puntual a la vez que la zona afectada térmicamente es muy limitada, evitando así que se produzcan distorsiones en el material. Además, el contorno de la pieza que se corta puede ser tener cualquier forma y ser compleja. Se trata de un proceso que puede realizarse a altas velocidades que permite aprovechar el material puesto que la anchura del surco generado es mínima. Asimismo, las paredes de corte son perpendiculares a la pieza, paralelas entre sí y no redondeadas, como sí ocurre con otros procesos térmicos de corte. Finalmente, la pieza cortada no necesita ningún tratamiento posterior ni limpieza y se pueden realizar cortes en cualquier dirección.
Por otra parte, según la experiencia de las empresas, elaborar bajas producciones puede ser rentable y al no realizar prototipos y pruebas reduce tanto el tiempo como el coste de producción. Tampoco existen consumibles que haya que sustituir y puede trabajar sobre una amplia variedad de materiales. Además, al no existir contacto con la pieza no hay desgaste por fricción.
Cabe destacar también que con el láser se pueden realizar cortes y grabados complejos, de calidad, precisión y permanentes. Finalmente, desde el punto de vista empresarial, el corte por láser permite trabajar en múltiples sectores y cuenta, todavía, con poca competencia, lo que sumado aumenta las posibilidades de negocio para las empresas.
Dentro del panorama de máquinas de corte por láser podemos encontrar modelos como la CCL, de Adira —que comercializa Lorenzo Muñoz—, con control numérico de cuatro ejes y destinada especialmente al corte de chapas planas de grandes dimensiones, con gran velocidad y elevada precisión. El concepto de movimiento de esta máquina se basa en el llamado principio de ‘óptica móvil’ (el haz se mueve sobre la chapa), con una cabeza de corte accionada verticalmente (eje Z) y desplazándose a lo largo de un pórtico (eje Y). Este pórtico, a su vez, se desplaza a lo largo de una estructura accionado por motores lineales en 2 ejes perfectamente sincronizados (2 ejes X). Con ello, la chapa a procesar no se mueve durante el corte, lo que permite una elevada velocidad de posicionamiento, independientemente del espesor de la chapa.
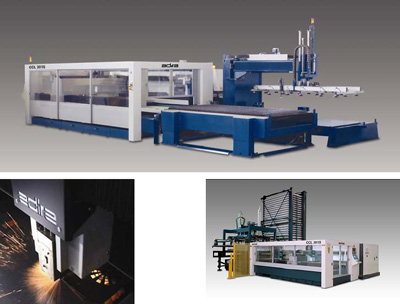
Trabajar en 3D
Entre sus principales aplicaciones encontramos el mecanizado de materiales, en particular chapas metálicas planas (2D) o plegadas y estampadas (3D).
En este caso, el láser proporciona una flexibilidad máxima de trabajo —puede mecanizar desde acero de todo tipo hasta aluminio y aleaciones, titanio, etc., y la mayoría de materiales plásticos— además de las anteriores ventajas como la múltiples formas que se pueden lograr, la elevada precisión y la inalterabilidad de la herramienta.
Pero es precisamente en las piezas tridimensionales (ya sean estampadas, plegadas o preensambladas), el corte láser ha supuesto posibilidades de aplicación hasta ahora impensables. Es decir, permite modificar los perfiles de corte de forma fácil y rápida, no requiere de soportes y los materiales endurecidos, o aquellos que desgastarían una herramienta convencional, se procesan correctamente. Además, el corte por láser permite perforar y contornear con alta precisión (hasta pocas centésimas de milímetro) incluso en piezas tridimensionales no precisas o inconstantes.
En este segmento encontramos soluciones como Rapido y Optimo, dos propuestas de Prima Industrie que utilizan láseres de CO2 y controles Prima Electronics. Desde su presentación, Rapido siempre ha estado en la vanguardia de la mecanización láser tridimensional y, con los años, Prima Industrie ha introducido nuevas versiones para responder e incluso anticiparse a las necesidades del sector. Así nació Rapido Evoluzione, con nuevas metas como carreras más largas (4.080 x 1.530 x 765 mm), lo que le permite procesar piezas de mayor tamaño y variedad. Algunas de sus características principales son las óptimas móviles, el eje C adaptativo con sensor capacitivo y una estructura monolítica compacta (ocupa poco suelo), además de una accesibilidad total por tres lados y una instalación fácil y rápida sin necesidad de cimentación. Este modelo cuenta con un kit de corte a alta presión, sistema de calibración automática del cabezal automática y sin errores, entre otras.
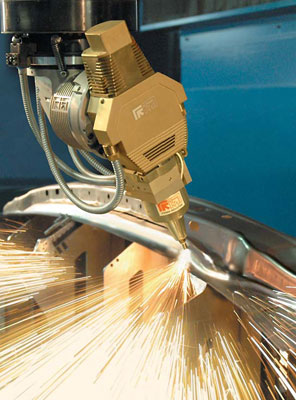
En cuanto a Optimo —la mayor de sus máquinas 3D— es una máquina tridimensional para corte y soldadura de grandes piezas, utilizada principalmente en la fabricación de carrocerías de vehículos automotores y en la industria aeroespacial. Ampliamente utilizada también en la manufactura de prototipos, repuestos y pequeñas o medianas series reciente, ofrece un amplio volumen de trabajo (más de 11 metros cúbicos). Es accesible, con ópticas móviles, estructura cartesiana monolítica y en pórtico, de elevada precisión y fácil de programar.
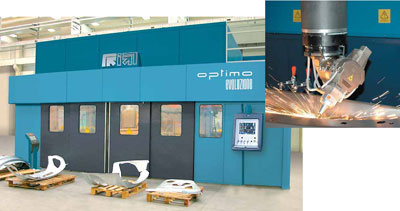
Más allá de la gota malaya
Es de sobra conocida la implacable eficacia de la gota malaya a la hora de romper cráneos; una tras otra logra el mismo efecto que un martillazo pero a cámara lenta. Sin embargo, es lógico pensar que, desde la óptica empresarial es, por lo menos, un sistema poco rentable, más que nada por su lentitud.
Así que, a la hora cortar metal, el chorro de agua se antoja más eficiente. Y es que precisamente una de sus principales ventajas es su implementación ultra rápida.
Pero, más allá de la velocidad, destaca que se trata de un proceso en frío, un detalle importante para aquellos trabajos donde cortar, mecanizar con levantamiento de virutas o con procesos térmicos aportan resultados de corte de calidad insuficiente. Porque los materiales cortados con chorro de agua no sufren ninguna tensión térmica, ni se produce endurecimiento, torsión de la superficie, fusión goteante o emisiones de gas. Además, para cortar metales con recubrimiento de plástico, el corte por chorro de agua es, generalmente, el proceso más conveniente al no producirse ningún cambio superficial negativo. Asimismo, aporta también ventajas a la hora cortar titanio, acero inoxidable, cobre o aluminio, o determinados minerales o materiales reforzados con fibra de vidrio.
Otras ventajas a destacar son su gran precisión junto a una elevada velocidad de corte y la seguridad que supone para los operarios y el medio ambiente (no crea vapores ni polvo de material). Tampoco crea zonas calientes en el material. Además, no requiere del reafilado de herramientas y ofrece un producto final limpio, eliminando la necesidad de procesos de retoque. Del mismo modo, permite obtener cantos de corte sin rebabas (sin necesidad de mecanizar los cantos de corte). Es, en definitiva, ideal para la elaboración rápida de prototipos y la producción flexible.
Dynamic Waterjet, diseñado para superar todas las limitaciones
Dynamic Waterjet —de Flow— incorpora Active Tolerance Control (control activo de tolerancias), que mejora la precisión de las piezas e incrementa la velocidad de corte, comparativamente con las máquinas convencionales de corte con agua. Este proceso utiliza un sistema de movimiento que incorpora modelos matemáticos de corte únicos, desarrollados por el equipo de científico liderado por Glenn Erichsen. Estos modelos controlan un sistema articulado fijado al cabezal de corte. Este sistema permite al cabezal de corte inclinarse en cualquier dirección, compensando la conicidad y retraso del haz que actualmente se produce en las máquinas convencionales. Cabe recordar que el retraso del haz y la conicidad, a pesar de ser naturales, son las limitaciones de cortar con una tecnología como el chorro de agua. Cuanto mayor es la velocidad, mayor es el retraso del haz y este retraso causa errores en la geometría de las piezas. Además, el incremento de la velocidad supone también un incremento de la conicidad. Las máquinas de corte con chorro de agua convencionales deben disminuir la velocidad, para reducir o eliminar los errores de tolerancia que se producen por el retraso del haz y la conicidad. Y el sistema Dynamic Waterjet supera estas limitaciones.
Dynamic Waterjet permite cortar piezas entre un 25-400% más rápido que en otras máquinas convencionales, mejora además la geometría y la tolerancia de las piezas, incluso cortadas a alta velocidad, y elimina virtualmente la conicidad. Con este sistema, el corte por pieza se reduce y no requiere operaciones posteriores. Además, corta materiales a partir de cualquier archivo CAD, o escaneando un dibujo en FlowMaster. De hecho, es un modelo ideal para actuales usuarios de tecnologías de corte plano o aplicaciones donde anteriormente fuera muy impreciso, lento o caro usar la tecnología de corte con agua y abrasivo convencional.
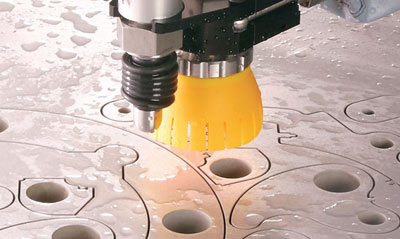