La integración más estrecha del desarrollo produce grandes beneficios en Ducati
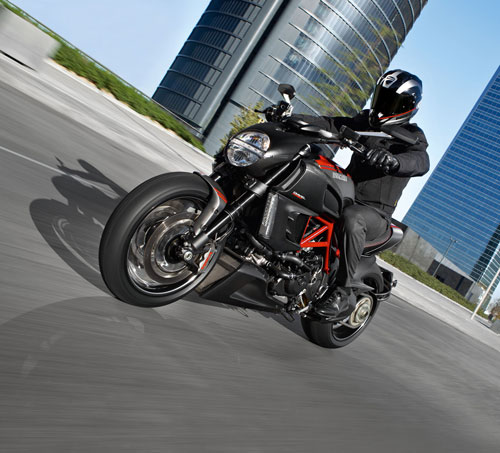
23 de abril de 2012
Caso de éxito
- Industria: automoción y transporte
- Retos empresariales: un amplio sistema de socios y proveedores; aumento del uso de la electrónica y el software en las motos
- Las claves del éxito: NX se utiliza para el desarrollo de productos desde el concepto inicial hasta su lanzamiento. Teamcenter se utiliza para integrar todas las operaciones de desarrollo de productos La funcionalidad de NX para el diseño integrado del cableado.
- Resultados: el ciclo del desarrollo de una moto nueva pasa de 36-40 meses a 24. Los modelos existentes se actualizan anualmente. Desarrollo paralelo del cableado, electrónica, software y accesorios. Se eliminan los documentos en papel en la fabricación y el almacenaje
De los 1.000 empleados que trabajan en Ducati, cerca de 200 están involucrados en la investigación y desarrollo (I+D), un área que la compañía mantiene con grandes inversiones cada año. El personal de ingeniería incluye, aproximadamente, a 90 personas, 60 de las cuales se dedican al diseño. Asimismo, Ducati tiene operaciones globales y una amplia red de socios y proveedores que gestionan el 92% de la producción. Debido a que cualquier retraso o error al transferir la información puede traducirse en tiempos de ciclo más largos y un aumento de costes, Ducati ha estado persiguiendo activamente conseguir una mayor integración entre todos los miembros de sus equipos de desarrollo de productos.
Entre las tecnologías que la compañía ha puesto en marcha para lograrlo existen dos soluciones de Siemens Industry Software: el software NX y el software Teamcenter. NX, el programa de diseño asistido por ordenador (CAD) de la compañía, se utiliza para modelar digitalmente y gestionar el montaje completo del vehículo. Por su parte, la solución Teamcenter para la gestión del ciclo de vida del producto (PLM) permite el intercambio seguro de los datos y su distribución, tanto en la empresa como con los proveedores.
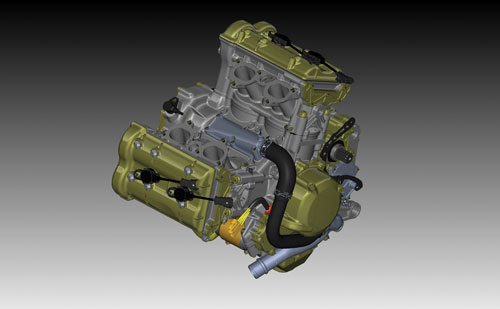
Moldes, carrocería y cableado; todo con NX
“NX es la herramienta que se utiliza desde el momento en que se empieza a pensar en un nuevo proyecto hasta su finalización”, explica Piero Giusti, gerente de Tecnología de la Información de I+D de Ducati Motor Holding. “NX es utilizado para el diseño de muchos componentes de la moto, incluyendo las ruedas, el chasis y la carrocería, así como para las piezas de encargo —prácticamente todo menos el motor—”.
Actualmente, existen más de 50 estaciones de trabajo NX en Ducati. “Los principales beneficios de NX son la flexibilidad y la facilidad de uso”, afirma Giusti. “Por flexibilidad quiero decir que te permite generar modelos en 3D con diferentes métodos, sin limitarse a un enfoque fijo. NX con Synchronous Technology es una aproximación híbrida que evita tener que parametrizar todo, por lo que el usuario es libre de elegir la forma de lograr el resultado final”.
Los ingenieros de Ducati usan las funcionalidades de cableado NX 3D de forma amplia. Eso les permite verificar el enrutamiento de cables dentro del ensamblaje virtual, minimizando los posibles problemas. “El próximo paso será la integración del diagrama de cableado para eliminar el uso del software por separado, lo que, inevitablemente, causa problemas con la actualización y la referencia”, añade Giusti. “Hemos esquematizado el flujo de tal manera que podamos crear diagramas de cableado mediante la funcionalidad de esquema NX. Después de esto, el diagrama se pasa a la aplicación de cableado NX para incorporar toda la información eléctrica en el diseño. Y, por último, utilizando la solución NX de enrutamiento eléctrico, preparamos la documentación para el cableado de la instalación. NX nos permite cubrir todo el proceso con un enfoque integrado”.
Seguridad de datos compartidos con Teamcenter
NX soporta una colaboración más estrecha tanto en el equipo de desarrollo interno como con los proveedores externos, que incluyen a las empresas que fabrican moldes y componentes clave como los menos importantes. Ducati espera lograr una colaboración aún más estrecha a través del uso de Teamcenter. “Cada vez nos resulta más necesario el intercambio de los datos del modelo con los proveedores”, apunta Giusti. “Con algunos de nuestros socios más antiguos estamos investigando la posibilidad de proporcionar un acceso directo a la información en nuestro sistema para que se pueda reducir aún más el tiempo de desarrollo al tener que trabajar de forma paralela a nuestros diseñadores. Dentro de pocos años, integraremos a todos nuestros proveedores estratégicos que producen la tecnología a nuestro favor”. Ducati ha iniciado este proceso con varios de sus proveedores.
Dentro de Ducati, el uso de Teamcenter está muy extendido. La compañía cuenta con 250 puestos de trabajo que utilizan Teamcenter para acceder a la información generada por el departamento de ingeniería. La empresa también ha desplegado Teamcenter en su almacén de Saima, en Módena. Todas las motos pasan por este lugar para algunas operaciones de montaje, verificación de piezas de repuesto u otras modificaciones debido a errores de montaje.
El personal tiene acceso a la información almacenada en Teamcenter a través de una línea dedicada. Se pueden ver dibujos, diagramas y tablas de montaje para todos los productos terminados. Los usuarios de este sitio pueden ejecutar las operaciones de montaje de menor importancia, por lo general, la instalación de las partes del cuerpo y los elementos personalizados pero, de vez en cuando, llevan a cabo modificaciones más significativas. Los usuarios necesitan tener acceso a la documentación del producto.
“Vale la pena señalar que fue fácil para el personal de Saima aprender a utilizar Teamcenter”, apunta Giusti. “El hecho de que no tuvieran ninguna formación específica es testigo de la intuición y de la facilidad de uso de Teamcenter”. “No nos podemos imaginar trabajando sin Teamcenter. De nuestro proceso previo que requería toneladas de papel hemos eliminado el papel y los gabinetes de presentación. Usando Teamcenter hemos implementado un sistema de gestión de la información digital con trazabilidad, un acceso basado en roles y un alto grado de seguridad intrínseca”.
Motos más complejas, evolución más rápida
La solución PLM de Ducati ha acelerado considerablemente el ritmo de desarrollo de los productos, permitiendo a la compañía desarrollar un nuevo modelo mucho más rápido a pesar de que el uso de la electrónica y el software relacionado ha crecido sustancialmente. De hecho, las motos de hoy en día pueden tener hasta seis o siete unidades de control electrónico (ECU) para la suspensión, transmisión, frenado y estabilidad. “Todos estos sistemas están interactuando y deben ser manejados de una manera eficiente y confiable”, apunta Giusti. “Ahora contamos con los requisitos de manejo de configuración de productos muy similares a los de las empresas de automoción o el sector aeroespacial”.
A pesar de la complejidad mayor del producto, Ducati ha reducido un año el ciclo de desarrollo de las motos nuevas. “Nuestro ciclo de diseño y desarrollo se ha reducido de un promedio de 36 a 40 meses a tan sólo 24 meses, gracias a las herramientas proporcionadas por Siemens Industry Software”, afirma Giusti. “También estamos actualizando todos los modelos existentes a intervalos anuales. Sería impensable pensar en lograr tales resultados con los métodos convencionales de diseño”.
La suite PLM de Siemens Industry Software ha permitido a Ducati integrar todos los departamentos y las operaciones: prototipos, almacén, piezas de repuesto y accesorios. “Mediante la integración de todos estos procesos ahora podemos desarrollar accesorios al mismo tiempo que la moto”, señala Giusti. “Antes, esto solía llevarnos de 6 a 12 meses antes de que los accesorios fueran comercializados. Ahora ya están listos, junto con la moto, generando sinergias de ventas significativas”.
