Incremento de la productividad y eficiencia en operaciones de rectificado
La creciente preocupación por el medio ambiente y la sostenibilidad están presionando a las operaciones de mecanizado hacia la reducción o incluso la eliminación completa de los fluidos de corte. El proceso de rectificado tampoco se ha librado de esta presión pero debido a las particularidades de este proceso todavía no ha sido posible conseguir una solución industrial de aplicación de mínima cantidad de lubricante (MQL).
Ante la evidencia de que en los procesos de rectificado el campo de mejora en la eficiencia de la aplicación de condiciones de refrigeración tradicionales es sustancial, en el presente trabajo se ha llevado a cabo un análisis experimental sobre la influencia de las condiciones de refrigeración (caudal, coherencia, orientación y velocidad del chorro) en el acabado superficial (rugosidad), integridad superficial (dañado térmico), tolerancias geométricas y estabilidad dimensional de las piezas. Los resultados reflejan la importancia y ventajas del empleo de chorros coherentes a elevada velocidad dirigidos al punto de corte sobre la precisión, estabilidad y productividad de los procesos. Con la finalidad de conseguir este tipo de chorros y, al mismo tiempo incrementar la eficiencia de los sistemas de refrigeración, se ha realizado un análisis de la influencia del diseño de las boquillas en la obtención de campos de velocidad mediante el empleo de herramientas de simulación CFD. Como resultado se han obtenido nuevos diseños de boquillas que optimizan las características del chorro empleado con un máximo aprovechamiento de la presión del sistema. Finalmente, el empleo de boquillas correctamente dimensionadas y de geometría optimizada se ha validado sobre aplicaciones industriales, donde se han obtenido elevados incrementos de productividad e importantes mejoras en la eficiencia energética de los sistemas de refrigeración.
1. Introducción
Los procesos de rectificado están comúnmente relacionados con el mecanizado de materiales de alta dureza con tolerancias y acabados superficiales muy ajustados. Sin embargo, tal como describen Oliveira et al. [1] en su revisión de los retos industriales en el rectificado, surgen nuevas oportunidades de desarrollo debido a la necesidad de productos de alta tecnología. Sectores como el aeronáutico, la generación de energía, ferrocarriles de alta velocidad o microtecnologías, caracterizados por producir componentes de alto valor añadido, generan nuevos necesidades sobre los procesos abrasivos convencionales, conduciendo al desarrollo de soluciones innovadoras.
Los nuevos avances en los procesos de rectificado están también relacionados con la producción sostenible. El aumento de la preocupación en temas medioambientales y de sostenibilidad está conduciendo a la industria hacia un nuevo paradigma. Los fabricantes de máquina-herramienta y los usuarios finales tienen que soportar las presiones impuestas por las regulaciones a escala global. La atención no solo está centrada en el consumo de energía y la eliminación de residuos (ver la norma ISO 14000), sino también en los costes generados por las prácticas industriales no sostenibles, que incluyen criterios sociales, medioambientales y de eficiencia económica [2]. Está científicamente aceptado que la producción debe contribuir al desarrollo sostenible ya que es el principal facilitador para llevarlo a cabo [2,3].
Los refrigerantes y lubricantes son utilizados normalmente en las operaciones convencionales de mecanizado y en los procesos abrasivos. En este sentido, ha aparecido un nuevo punto de vista basado en la consideración de los costes medioambientales y los riesgos asociados a su uso. Sin lugar a dudas, los refrigerantes y lubricantes mejoran en gran medida el funcionamiento de los procesos. La selección y aplicación óptima de estos fluidos en rectificado es un aspecto de gran importancia. El fluido debe reunir unas características para alcanzar una refrigeración y lubricación favorables a la vez que se genera una eliminación de material eficiente y una protección efectiva contra la corrosión [4]. Por lo tanto, los costes y riesgos relacionados con el uso de refrigerantes en rectificado deben de tenerse en cuenta en la definición de la operación. Además del coste del propio fluido, existen otros aspectos que se deben tener en cuenta: la eliminación del fluido, el reciclado, las medidas de seguridad, etc.
Aparte de estos aspectos, el refrigerante debe estar limpio y en buenas condiciones, por lo que hoy en día es obligatorio el uso de equipos de filtrado. Estos sistemas son caros y ocupan un considerable espacio en planta, hasta un 120% del espacio de máquina. Actualmente existen tecnologías para reducir el consumo de refrigeración y lubricación en los procesos de mecanizado convencionales. Se pueden encontrar en la bibliografía numerosos trabajos de investigación en este campo [5]. Algunas de estas técnicas, como el MQL (Minimum Quantity Lubrication) o el mecanizado en seco, se pueden encontrar en aplicaciones industriales, especialmente en procesos como el torneado, el taladrado o incluso el fresado. Como ejemplo, en una reciente publicación Sharma et al. [6] enseñan técnicas de refrigeración avanzadas para mejorar la productividad en el torneado de materiales difíciles de mecanizar. Sin embargo, aunque las últimas publicaciones [7] y trabajos hacia sistemas que conducen a la reducción o incluso eliminación del refrigerante en rectificado son prometedores, aún no ha sido posible conseguir una solución industrial de aplicación de mínima cantidad de lubricante (MQL). En estos procesos, se alcanzan elevadas temperaturas y la fricción gobierna el mecanismo de eliminación de material. Como consecuencia de esto, se tiene que evacuar una gran cantidad de calor generado, ya que en caso de no hacerlo se puede producir dañado térmico de la pieza, un desgaste de muela elevado o deformaciones térmicas que resultan en una baja calidad de los componentes rectificados [8].
Además de las tecnologías que conducen hacia la reducción o eliminación del refrigerante, existe una segunda línea de trabajo en torno a la optimización de aplicación de condiciones de refrigeración tradicionales. Esta línea aborda aspectos que se consideran críticos para maximizar el caudal de refrigerante útil (caudal que penetra en la zona de contacto muela rectificadora-pieza y que es realmente efectivo en las funciones de lubricación y extracción de calor de esta zona). Entre estos factores se encuentran el tipo geometría y posicionamiento de las toberas, la velocidad y coherencia de los chorros, el empleo de rascadores y el tipo de lubricante utilizado [9].
Trabajos previos en la década de los 80 [10] estimaban valores de caudal útil de entre 20 y 40 del caudal total empleado; sin embargo, estos valores parecen estar sobrestimados según el trabajo posterior de Engineer et al. [11], que fija los valores en un rango de 5-20 % del caudal total.
La influencia del posicionamiento de la tobera y el efecto de la capa de aire que rodea a la muela han sido entre otros estudiados en [12]. Webster [13] afirma que para garantizar que el refrigerante llegue a la muela, la velocidad del flujo debe ser la misma que la de la muela, dando así importancia a la velocidad y coherencia del chorro empleado. Realiza una definición y presenta una expresión para el cálculo de lo que denomina longitud coherente y diseña una forma de tobera optimizada, basada en los diseños de Rouse de toberas para bomberos realizadas en los años 40.
En un trabajo más reciente, Morgan et al. [14] utilizan la mecánica de fluidos computacional y técnicas experimentales para mostrar que el máximo caudal útil alcanzable depende de las características de la muela rectificadora y los parámetros de proceso (porosidad, velocidad de muela) y que el alcance real del mismo depende de la posición de la tobera, su diseño, caudal y velocidad del chorro. Entre los diferentes diseños analizados, la mejor coherencia se puede encontrar con la tobera de Rouse/Webster [13]. En cuanto a las necesidades de velocidad del chorro para penetración en la capa de aire afirman que la velocidad debe ser entre el 80 y el 100% de la velocidad tangencial de la muela.
Se puede afirmar que se ha generado gran conocimiento en este entorno y que en bibliografía están documentadas ciertas bases sobre la definición de condiciones de refrigeración [8]. Sin embargo, se aprecia también que en la práctica aún existe una gran incertidumbre y disparidad de opiniones a la hora de establecer las necesidades del caudal, velocidad y orientación del chorro de refrigerante para una determinada aplicación, o sobre los efectos reales de utilización de rascadores y toberas de zapata. En el entorno industrial cada vez se aprecia una mayor concienciación sobre la importancia del empleo de unas condiciones de refrigeración idóneas, pero las condiciones de refrigeración y limpieza de muela habitualmente utilizadas distan de ser óptimas o eficientes. El presente trabajo se centra en este entorno, donde a través de un trabajo teórico y experimental se aclaran algunas de estas incertidumbres existentes y se establecen pautas para incrementar la productividad y eficiencia en operaciones de rectificado mediante la aplicación de condiciones óptimas de refrigeración y el empleo de boquillas eficientes.
2. Condiciones óptimas de refrigeración. Estudio experimental
Con el objetivo de contrastar las directrices del estado del arte actual y adquirir un mayor conocimiento en torno a la influencia de las condiciones de refrigeración en los resultados de pieza, estabilidad del proceso, y desgaste de muela se han realizado una serie de ensayos que se describen a continuación. Se han analizado fundamentalmente la influencia del caudal, velocidad, coherencia y orientación del chorro de refrigerante en diferentes condiciones de trabajo.
2.1 Descripción de ensayos
Los ensayos se han realizado en rectificado en penetración llevándose a cabo en una rectificadora sin centros Estarta 301 MV. Las características de la pieza empleada han sido:
- Material F522 Templado, 50HRc
- Diámetro: 30 mm; 25 mm de ancho
Se han empleado dos muelas de características similares pero diferentes porosidades:
- Muela de porosidad estándar: MA 100J8V489
- Muela porosa: MA 100K15V489P36P
Se han empleado dos velocidades de muela: 63m/s y 45m/s; se han empleado igualmente dos tipos lubricante en base agua:
- Rhenus TR 34
- Castrol Syntilo 2000
Se han empleado 4 ciclos de plongée diferentes, con diferentes agresividades.
Los ensayos han consistido en la realización de una serie de 50 piezas rectificando en plongée para diferentes combinaciones de tipo de muela, velocidad de muela, refrigerante y ciclos de plongée. En cada una de las combinaciones se han probado y analizado varias condiciones de trabajo en cuanto a caudal, velocidad, coherencia y orientación del chorro de refrigerante.
Las variables controladas y medidas en cada ensayo han sido (Ver figuras 1,2 y 3):
- Caudal del refrigerante. (fig.1,2 y 3).
- Presión a la salida de la bomba y antes de la salida de la tobera.
- Velocidad del chorro (fig. 1,2 y 3).
- Potencia y evolución de la potencia durante la secuencia de rectificado. (fig. 1,2 y 3).
- Rugosidad y evolución de la rugosidad durante la secuencia de rectificado.
- Temperatura final de la pieza y su evolución durante la secuencia de rectificado. (Medida en el diámetro exterior inmediatamente después de realizar el plongée empleando un termómetro digital de contacto pt-100), (fig. 1,2 y 3).
- Dureza de la pieza, aspecto visual frente a quemados.
- Desgaste de muela (por diferencia de diámetros en piezas).
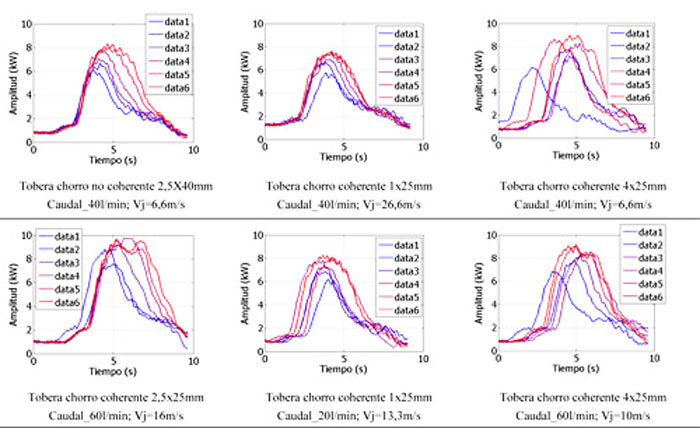
En la Figura 1 cada curva corresponde con: data1: pieza 1; data2: pieza 10; data3: pieza 20; data4: pieza 30; data5: pieza 40; data6: pieza 50 de una serie de plongées.
2.2 Resumen de resultados y conclusiones
A continuación se resumen los resultados y las principales conclusiones extraídas.
2.2.1 Influencia de la coherencia y velocidad del chorro (Vj)
Todos los ensayos realizados reflejan que a mayor velocidad y coherencia del chorro se consigue mayor estabilidad de proceso, apreciable en una mayor estabilidad de la potencia (lo cual redunda en una disminución de la posibilidad de dañado térmico), mayor estabilidad de la rugosidad y mayor estabilidad de temperatura en pieza (lo cual redunda en una mayor estabilidad dimensional de la pieza).
En la Fig. 2 se muestra un ejemplo de resultados obtenidos en una de las series de condiciones de trabajo ensayadas (misma serie que la de la Fig. 1). En el gráfico de la izquierda se muestra la influencia del caudal efectivo por mm de rectificado en la estabilidad del proceso como incremento de potencia y en el de la derecha la influencia de la velocidad del chorro (Vj). En el gráfico de la derecha se aprecia una clara tendencia a la estabilidad (menor incremento de potencia) a mayor velocidad de chorro. Además se aprecian dos pares de puntos con mismo caudal efectivo en los cuales la estabilidad es mayor para la aplicación a mayor velocidad.
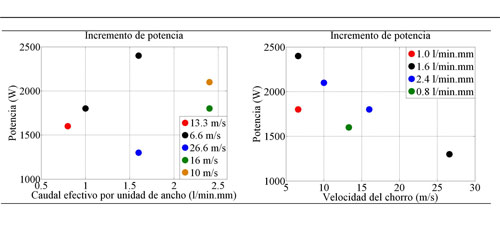
Una conclusión relevante de estos ensayos es que el efecto del incremento de velocidad del chorro (con el empleo de chorros coherentes) sobre la estabilidad del proceso se aprecia desde velocidades relativas del chorro muy bajas. Esto es, no se ha apreciado un umbral mínimo necesario de velocidad de chorro para apreciar su efecto en la estabilidad del proceso, y se aprecia una clara tendencia a la estabilidad (mejora) a mayor velocidad de chorro.
El efecto beneficioso del incremento de velocidad en la estabilidad de la temperatura se evidencia más aún cuando el empleo de caudal es bajo.
En cuanto a la rugosidad, la tendencia en los ensayos ha sido a obtener una mejor rugosidad inicial al emplear chorros coherentes a mayor velocidad.
2.2.2 Influencia del caudal
El incremento de caudal no ha aportado beneficios a la estabilidad de potencia del proceso pero cuanto más caudal se emplea la variación de temperatura inicial (Tª de la primera pieza antes y después de ser rectificada) es menor (para la misma o incluso mayor cantidad de calor/potencia generada) como puede apreciarse en la Fig. 3. La estabilidad de la variación de temperatura también es mayor. Los resultados reflejan que un incremento de caudal es útil para lograr estabilidad dimensional de la pieza, pero al no reflejarse un efecto beneficios sobre la estabilidad de potencia se puede asegurar que tampoco lo tiene sobre el dañado térmico.
El factor de estabilidad de temperatura es clave para lograr una estabilidad dimensional en las piezas. A menores variaciones de temperatura en las piezas la estabilidad dimensional es mayor. En este sentido, los caudales de refrigerante necesarios para garantizar un enfriamiento del bruto de la pieza (un incremento de Tª por inferior a un valor dado) han sido en todos los casos superiores a las que determinan la siguiente expresión teórica (1) empleada en bibliografía [8], incluso suponiendo que todo el calor generado penetra en la pieza rectificada.
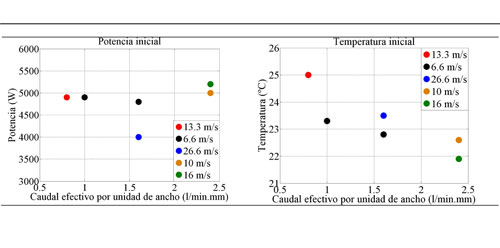
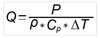
Donde
- ∆T: Variación de temperatura aceptada en la pieza
- Q: Caudal de fluido refrigerante
- P: Parte del calor generado (parte de la potencia de rectificado) que penetra en la pieza
- ρ: densidad del fluido
- Cp: capacidad de calor especifico
Una apreciación importante al respecto es que si empleamos medidor inprocess (como el 90% de las aplicaciones hoy en día) el factor de estabilidad de temperatura es aún más crítico ya que el medidor no compensa la dilatación que haya podido haber en pieza por un incremento de temperatura. Sin embargo si no empleamos medidor el desgaste de la muela tiende a compensar el efecto de la dilatación de la pieza y realmente la variación dimensional de la pieza se compensa en cierta medida aunque sin ningún tipo de control.
2.2.3 Influencia de la orientación
En las series realizadas con el objeto de analizar este punto la estabilidad en potencia es mayor cuando orientamos el chorro al punto de corte frente a orientarlo a la muela y a la pieza. El ratio G y la estabilidad de la rugosidad también han sido mayores en esta condición.
3. Diseño óptimo de toberas mediante CFD y análisis de comportamiento real en banco de ensayos
En este apartado presenta el trabajo y resultados obtenidos en desarrollo de toberas eficientes con el apoyo de cálculos de mecánica de fluidos computacional (CFD).
3.1 Diseño óptimo de Toberas mediante CFD
Como se ha visto en el apartado anterior, se ha llevado a cabo una gran cantidad de trabajo de investigación en relación a la optimización del caudal necesario en los procesos de rectificado. Sin embargo, se observa una falta de investigación relacionada con el análisis de la geometría de la tobera y su influencia en la distribución de presión del chorro. La mecánica de fluidos computacional (CFD en sus siglas en inglés) es una herramienta de gran ayuda para la optimización del diseño de las toberas. En este apartado se muestra el ejemplo de un procedimiento de optimización de las características geométricas de la tobera. El objetivo es obtener la máxima velocidad a la salida de la tobera con un caudal de 0,5 kg/s a la salida de la bomba, asegurando a su vez la coherencia del chorro. Se ha utilizado el software comercial CD Adapco para el análisis. La tobera para aplicaciones rectas de Webster en base a la geometría de tobera circular de Rouse ha llegado a ser considerablemente popular en los últimos años, debido principalmente a su excelente funcionamiento en una gran variedad de situaciones [8]. Partiendo de este diseño ampliamente aceptado, se pueden sacar unas primeras conclusiones al observar el comportamiento en el interior de la tobera. Las características geométricas de la tobera se pueden ver en la Fig. 4 (a). El diámetro a la entrada es de 9,53 mm mientras que la sección a la salida tiene un espesor de 0,5 mm y una anchura de 50 mm.
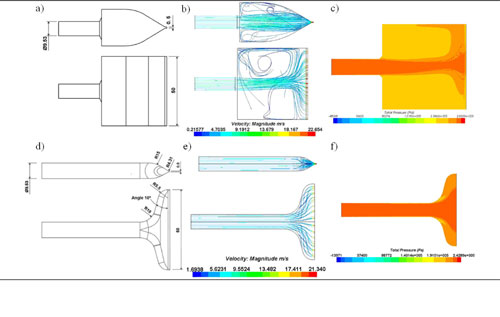
La simulación multifase 3D (Fig. 4 (b)) realizada a través del software ANSYS CFX muestra las líneas de velocidad en el interior de la tobera. Se puede observar la generación de las zonas de estancamiento y recirculación (como se comenta en [14]). Estas zonas son las responsables de las pérdidas de carga que reducen el funcionamiento de la tobera. Se pueden observar también variaciones en la velocidad a la salida de la tobera desde 18.0 a 22.6 m/s, que conducen a un caudal no uniforme hacia la muela.
La presión generada en el interior de la tobera se muestra en la Fig.c4 (c). Se puede deducir a partir de los resultados que la presión más alta tiende a concentrarse en el centro de la salida de la tobera, con pérdidas significativas en sus bordes. Como se ha comentado previamente, la tobera de Webster es una de las mejores soluciones existentes para la conducción del refrigerante en las operaciones de rectificado. Sin embargo, en vista de los resultados anteriores, se puede pensar en mejoras teóricas en el chorro mediante el uso de una nueva geometría de la tobera. Por lo tanto, mediante la información obtenida de las simulaciones CFD se propone un nuevo diseño de tobera. Este diseño es tal que adapta las líneas de caudal en el interior de la tobera de tal forma que las pérdidas de energía son minimizadas, generando un funcionamiento óptimo del chorro. La Fig. 4 (d) muestra dos vistas del nuevo diseño. El caudal, la sección de entrada y la de salida se mantienen respecto a la geometría de partida de la tobera de Webster.
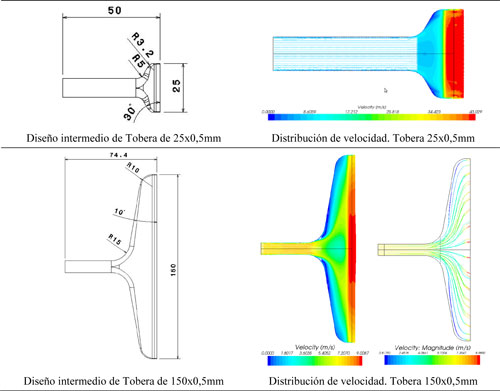
La evolución de las líneas de velocidad de la Fig. 4 (e) dentro de la nueva tobera muestran la eliminación virtual de las zonas de recirculación. Una observación cercana a la salida revela una mayor uniformidad en la velocidad hacia la muela. De hecho, las variaciones de velocidad a la salida de la tobera se encuentran entre 20,4 y 21,2 m/s. Esto indica una reducción de la variación de velocidad del 82,6% respecto a la tobera de Webster. La distribución de la presión en el interior de la tobera también se ha mejorado notablemente, como se observa en la mayor uniformidad de presión a la salida de la tobera (Fig. 4 (f)). Una vez validado los resultados de este diseño, se ha procedido a analizar la forma óptima de escalar esta tobera para obtener diferentes anchos de muela y secciones de salida. Para ello se ha recurrido de nuevo a la simulación por ordenador (CFD), (Fig. 5).
3.2 Validación de las toberas diseñadas mediante CFD. Análisis experimental de la influencia de la geometría y diseño de las toberas en las características del chorro obtenido y eficiencia energética (pérdida de presión)
Posteriormente a la realización de estos diseños se han fabricado varios prototipos de toberas correspondientes a diseños optimizados, escalados y comunes. En un banco de ensayos se ha analizado la influencia de la geometría y diseño de las toberas en las características del chorro obtenido y pérdida de carga. La actividad se ha llevado a cabo sobre un banco de ensayos, el cual cuenta con una bomba que proporciona un caudal de 150 l/min con una presión máxima de 20 bares. El banco permite la instalación de muelas abrasivas y ponerlas girando hasta una velocidad de giro de 4.500 rev/min. El rango de posicionamiento y orientación de la tobera es completo a través de dos movimientos de traslación y uno de giro. El banco está modificado con una ventana de vidrio transparente al infrarrojo para la toma de termografías y que permite una visión extremadamente cercana del contacto chorro-muela. Dispone de un caudalímetro y de dos manómetros colocados a la salida de la bomba y justo antes de la entrada a la tobera para medir las presiones de trabajo, (Fig. 6).
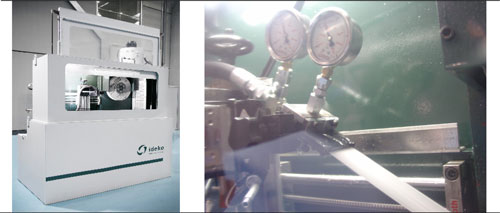
La sistemática de ensayos para analizar la influencia de la geometría y diseño de las toberas en las características del chorro obtenido y pérdida de carga han consistido por un lado en observar el chorro de salida y su coherencia en un amplio rango de condiciones (ver ejemplo en Fig. 7). Para estimar la pérdida de carga real en las toberas (Pmedida/ Pteórica) se ha calculado la velocidad de salida del chorro con los datos de presión, caudal y sección de salida de la tobera (ver ejemplo en Tabla 1). Paralelamente a la contrastación experimental de los resultados teóricos predichos por los cálculos CFD con respecto a la influencia de la propia geometría interior de la tobera, se han analizado la influencia de otros factores como la relación entre diámetro de entrada Vs área de salida o la longitud de la punta. Se han medido las pérdidas de presión en un amplio rango de condiciones, apreciándose que en toberas con geometría interior no optimizada para las condiciones en las que va a trabajar, las pérdidas de presión y en consecuencia las pérdidas de eficiencia energética pueden llegar a ser del orden de 2,5-3 veces superiores a las estrictamente necesarias y alcanzadas con toberas de geometría optimizada. En la tabla 1 podemos encontrar valores para diferentes tipos de diseños con o sin utilización de CFD. Una de las principales conclusiones extraídas es que para conseguir un chorro coherente y una máxima eficiencia en la aplicación del refrigerante, es necesario dimensionar la tobera en base a las características de la bomba disponible (o mejor aún, definiendo las condiciones en las que va a trabajar y la bomba necesaria para ello) y optimizar la geometría interior con la utilización de cálculos CFD para las condiciones de velocidad y caudal a las que va a trabajar.
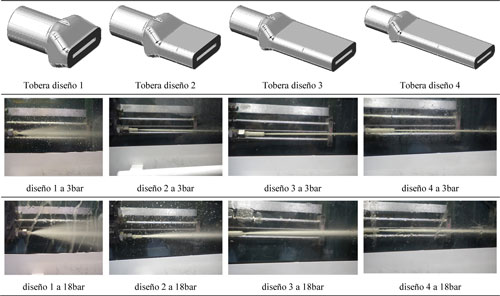
Teniendo en cuenta las conclusiones obtenidas en el apartado 2 en cuanto al efecto beneficioso en la estabilidad de los procesos del empleo de chorros coherentes a elevada velocidad, la importancia de un diseño óptimo de tobera cobra mayor importancia, no solo desde el punto de vista de eficiencia energética. También porqué la velocidad de chorro alcanzable es proporcional a la eficiencia o aprovechamiento de la presión para acelerar el fluido dentro de la tobera.
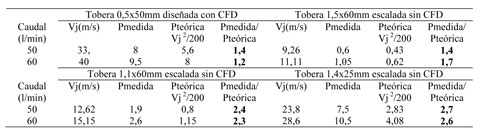
4. Estudio de penetración de la capa de aire en banco de ensayos
También en el banco de ensayos se ha procedido al estudio de la penetración de la capa de aire en diferentes condiciones de aplicación del chorro de refrigerante. Más allá de las consideraciones que se puedan hacer acerca del concepto de flujo útil y tal como lo han demostrado los resultados experimentales, este análisis se considera crítico a la hora de indicar la velocidad, caudal y orientación necesarios para una aplicación determinada.
Según la bibliografía el espesor de la capa de aire que hay que vencer depende de los siguientes factores: velocidad tangencial de la muela, porosidad, tamaño de grano, radio de la muela y condiciones de diamantado.
La metodología de ensayos ha consistido por un lado en realizar el mismo experimento que se describe en [9] donde se sumerge parte de la muela en un depósito con un fluido estanco y se pone la muela a girar. El agua del depósito no llega a tocar la muela porque la capa de aire que se genera lo impide. El espacio que aparece entre la muela y el fluido es proporcional a la capa de aire. Mediante un sistema de medida por visión se mide este espacio con una cámara situada en el exterior y se realiza un estudio comparativo de los diferentes parámetros que influyen en el espesor de la capa de aire (Fig. 8). Se han realizado estudios con muelas con diferentes porosidades y tamaños de grano, cambiando la velocidad tangencial de las muelas, así como empleando rascadores justo antes del contacto entre el chorro y la muela.
Por otro lado, utilizando el mismo sistema de medida se han realizado ensayos aplicando chorros de refrigerante en diferentes condiciones de velocidad, caudal y orientación de los chorros, (Fig. 9).
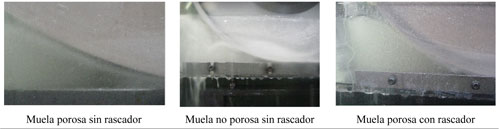
En cuanto a las necesidades de velocidad del chorro para penetración en la capa de aire los resultados de los ensayos reflejan que las velocidades necesarias para la penetración de la capa de aire son inferiores a las citadas en bibliografía, y que además de la velocidad y coherencia de los chorros, el ángulo de ataque con respecto a la tangente es un parámetro más a tener en cuenta la hora de considerar cómo entra en contacto el fluido con la muela. Se ha confirmado que si la velocidad de salida es menor que la de la muela el ángulo de ataque óptimo es distinto a la tangente, por lo que en muchas ocasiones la refrigeración más efectiva no será la que se produce con un ataque tangencial. En las fotografías de la Fig. 9 se puede apreciar como en el caso de una muela no porosa con una velocidad de chorro Vj>70%Vs y sin empleo de rascadores se alcanza a tocar la muela en un ataque no tangencial y como con una velocidad el chorro Vj< 30%Vs flecta y no toca la muela.
Con muelas no porosas la velocidad de chorro necesaria para penetrar la capa de aire ha sido inferior a los datos que se proporcionan en bibliografía y muy inferior en el caso de muelas porosas. El empleo de rascadores refleja un efecto muy positivo a la hora de disminuir la velocidad del chorro necesaria para la penetración de la capa de aire.
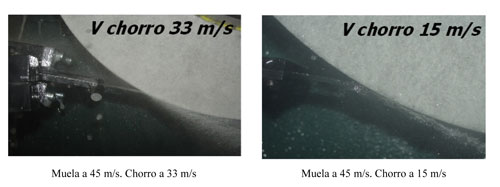
5. Resultados sobre aplicaciones industriales
El empleo de boquillas correctamente dimensionadas y de geometría optimizada se ha validado sobre aplicaciones industriales. A continuación se muestran algunos de los resultados obtenidos.
5.1 Aplicación de una tobera de dimensión y geometría optimizada sobre una aplicación industrial de rectificado de barras calibradas de 150 mm de diámetro en Rectificado Sin Centros
Teniendo en cuenta los resultados experimentales sobre la influencia de las condiciones de refrigeración y las pautas de dimensionamiento óptimo de toberas, se ha procedido a realizar una definición de tobera para un máximo aprovechamiento de la bomba disponible logrando un chorro de tobera coherente con la mayor velocidad de chorro posible. En la tabla 2 y Fig. 10 se pueden apreciar las diferencias entre las condiciones de refrigeración conseguidas y los resultados de ratio G correspondientes.
- Rectificado de barras de 150 mm de diámetro en pasante
- Producción: 0,1 mm de pasada en diámetro a 2 mm/min
- Bomba disponible: 400 l/min, 3 bar
- Velocidad de corte: Vs: 50 m/s
|
Tobera Inicial |
Tobera final |
Caudal (l/min) |
360 |
240 |
Velocidad chorro: Vj (m/s) |
2 |
16 (32% Vs) |
Presión antes de la tobera (bar) |
--- |
2 |
Ratio G |
13,6 |
24,7 (+81%) |
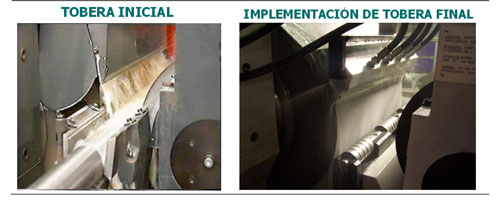
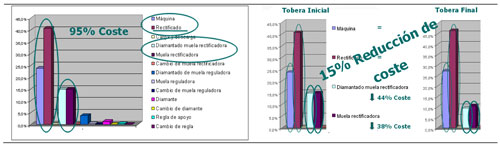
Al mismo tiempo se ha realizado de un análisis de coste pieza para la aplicación, la cual refleja que el 95% de coste de pieza asociado a esta operación lo suponen el coste de adquisición y amortización de máquina, coste de operación (rectificado), coste de diamantado y coste de muela rectificadora, (Fig. 11). Los aumentos de ratio G obtenidos con la utilización de la nueva tobera suponen una reducción de coste en consumo de muelas de un 38% lo que unido a una reducción de un 44% de coste relativo a las operaciones de diamantado asociadas, supone para esta aplicación una reducción de coste total de pieza en torno a un 15%, (Fig. 11). Hay que tener en cuenta que estos resultados se han obtenido sin la necesidad de ir a bombas de elevada presión.
5.2 Aplicación de una tobera de diseño optimizado en rectificado cilíndrico de exteriores de brocas de metal duro
En este caso la aplicación consiste en un rectificado cilíndrico de exteriores de brocas de metal duro con muela de diamante. Se ha pasado de utilizar unas toberas estándares a una tobera de diseño optimizado cuyo chorro se puede apreciar en la Fig. 12. La presión del sistema es de 3 bares. La taladrina utilizada es Delta Polar 44 con una concentración entre 4 y 6%. La velocidad del chorro obtenido es de 22 m/s con un caudal de 120 l/min.
Resultados:
A) Producción con toberas estándares (Loc-Line): 8 piezas entre diamantados. 2 horas de trabajo y 1 hora de regeneración (debido a la necesidad de regeneración de muela fuera de máquina).
B) Producción con toberas optimizadas: 17piezas entre diamantados. 4 horas de trabajo y 1 hora de regeneración.
Estos resultados suponen un incremento de vida de muela del 100% y un incremento de productividad para esta operación del 20%.
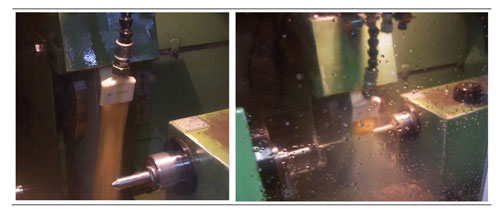
5.3 Aplicación de toberas de diseño optimizado y diferentes condiciones de refrigeración en rectificado plano de piezas de grandes dimensiones
Una de las principales problemáticas en las operaciones de rectificado de piezas de grandes dimensiones y elevado valor añadido es la de pérdida de precisión dimensional de las piezas por problemas de generación de gradientes de temperatura en las propias piezas durante las operaciones de rectificado. Una de las claves en este tipo de proceso es minimizar la generación de estos gradientes de temperatura y en este caso, utilizando las toberas diseñadas específicamente se ha analizado la importancia de unas condiciones de refrigeración idóneas, orientación del refrigerante y caudal en las tres condiciones siguientes.
_ Condición 1: Aprox. 5 bar, 150 l/min; Vj=25 m/s y orientada al punto de corte
_ Condición 2: Aprox. 5 bar, 150 l/min; Vj=25 m/s y orientada a la muela
_ Condición 3: Aprox. 1 bar, 50 l/min; Vj=8 m/s y orientado a la pieza
Los ensayos realizados han sido los siguientes:
- 1º Rectificado de guía plana (1.500 x 54 mm)
- Condiciones de rectificado:
- 20 pasadas de 0,015 mm a 25m/min. 0,3 mm en total
- 2º Rectificado de pared lateral (1.500 x 15mm)
- Condiciones de rectificado:
- 40 pasadas de 0,015 mm a 25 m/min. 0,6 mm en total
Resultados y conclusiones:
En la página siguiente se muestra por un lado el estado inicial y final de los gradientes de temperatura obtenidos en varias condiciones de ambas operaciones medidos con cámaras termográficas y por otro los ratios G obtenidos en las mismas, (Fig. 12). La influencia de las condiciones de refrigeración se aprecia claramente en una reducción del gradiente térmico generado hasta el 60% así como en unos menores desgaste de muela (mayores ratios G), (Fig. 12).
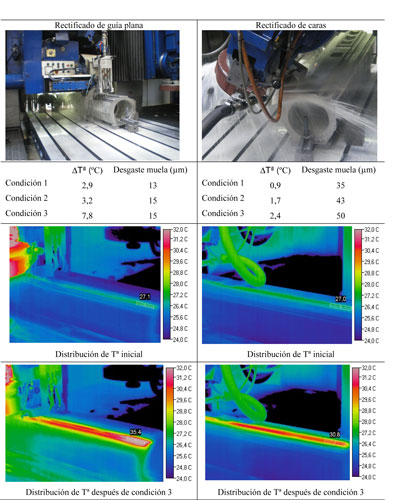
6. Conclusiones
Los ensayos de conocimiento realizados en torno a la aplicación de condiciones de refrigeración han reflejado la importancia del empleo de chorros coherentes a elevada velocidad en la estabilidad de los procesos de rectificado. Una conclusión relevante de estos ensayos ha sido que el efecto del incremento de velocidad del chorro (con el empleo de chorros coherentes) sobre la estabilidad del proceso se aprecia desde velocidades relativamente bajas con respecto a la velocidad de la muela, produciéndose una clara tendencia a la estabilidad a mayor velocidad de chorro. Un aumento de estabilidad de proceso conlleva una mayor duración de muela, un incremento de los intervalos de diamantado y menor riesgo de dañado térmico de pieza entre otros, afectando a un incremento de productividad de los procesos. Los resultados muestran también que en algunos casos sería posible reducir las dimensiones de los equipos de refrigeración a más de la mitad de sus dimensiones a través de un aumento de velocidad del refrigerante y una reducción del caudal. El impacto económico y ecológico que ello conlleva es palpable. Los resultados permiten establecer unas pautas para la definición de condiciones óptimas de refrigeración, siendo el factor más importante el empleo de chorros coherentes orientados al punto de corte a la mayor velocidad posible (con el empleo de la bomba disponible) pero estableciendo un compromiso con el caudal a emplear. Si la operación es exigente y existen riesgos de quemado debe darse aún mayor importancia a la velocidad y coherencia del chorro a emplear, mientras que si el factor crítico es la estabilidad dimensional de la pieza habrá que adoptar un compromiso con la cantidad de caudal a emplear, ya que los caudales de refrigerante necesarios para garantizar un enfriamiento del bruto de la pieza (para no superar un determinado incremento de temperatura en la pieza) son superiores a los teóricos y que se recomiendan en bibliografía.
Los resultados del estudio de la capa de aire también han reflejado que los umbrales de velocidad necesarios para penetrar la capa son inferiores a los que se indican en la bibliografía. La orientación del chorro y el empleo de rascadores son factores importantes a la hora de facilitar la penetración de la capa de aire.
Por otro lado se ha procedido a analizar la influencia del diseño interior de las toberas de refrigeración en la eficiencia la aplicación del refrigerante y pérdida energética del sistema. Se han empleado herramientas de cálculo CFD para optimizar los diseños interiores de las toberas. Posteriormente al diseño, se han fabricado y validado en un banco de ensayos varios de los diseños realizados, midiéndose las pérdidas de presión en un amplio rango de condiciones de trabajo. Se ha apreciado que en toberas con geometría interior no optimizada para las condiciones en las que va a trabajar, las pérdidas de presión y en consecuencia las pérdidas de eficiencia energética pueden llegar a ser del orden de 2,5-3 veces superiores a las estrictamente necesarias y alcanzadas con toberas de geometría optimizada.
Una de las principales conclusiones extraídas ha sido que para conseguir un chorro coherente y una máxima eficiencia en la aplicación del refrigerante, es necesario dimensionar las toberas en base a las características de la bomba disponible (o mejor aún, definiendo las condiciones en las que va a trabajar y la bomba necesaria para ello) y optimizar la geometría interior con la utilización de cálculos CFD para las condiciones de velocidad y caudal a las que va a trabajar.
Teniendo en cuenta las conclusiones obtenidas en cuanto al efecto beneficioso en la estabilidad de los procesos del empleo de chorros coherentes a elevada velocidad, la importancia de un diseño óptimo de tobera cobra mayor importancia, no solo desde el punto de vista de eficiencia energética, sino también porqué la velocidad de chorro alcanzable es proporcional a la eficiencia o aprovechamiento de la presión para acelerar el fluido dentro de la tobera.
Finalmente el empleo de dichas toberas se ha validado sobre aplicaciones industriales donde se han logrado aumentos de vida de muela del orden del 40-100%, reducciones de coste en tiempo de diamantado del orden del 45%, reducciones de coste de pieza hasta un 15% y un aumento de productividad hasta un 20% con el simple cambio de la tobera.
Agradecimientos
En primer lugar, los autores quieren expresar su reconocimiento a Latz S.Coop, Goimek S. Coop, Estarta Rectificadora S.Coop y Danobat S.Coop, sin cuya ayuda y colaboración este trabajo no habría sido posible. Este trabajo se ha realizado con el soporte económico del Gobierno Vasco en las convocatorias Gaitek (Proyecto Coolgrind anualidades 2010,2011) y Etorgai (Proyecto Ecofab anualidades 2012, 2013,2014).
Referencias
[1] J.F.G. Oliveira, E.J. Silva, C. Guo, F. Hashimoto, Industrial challenges in grinding, Annals of the CIRP 58 (2009) 663–680.
[2] F. Pusavec, P. Krajnik, J. Kopac, Transitioning to sustainable production—Part I: application on machining technologies, Journal of Cleaner Production 18 (2010) 174– 184.
[3] F. Jovane, H. Yoshikawa, L. Alting, C.R. Boer, E. Westkamper, D. Williams, The incoming global technological and industrial revolution towards competitive sustainable manufacturing, Annals of the CIRP 57 (2008) 641–659.
[4] I.D. Marinescu, M. Hitchiner, E. Uhlmann, W.B. Rowe, I. Inasaki, Handbook of Machining with Grinding Wheels, CRC Press, 2007.
[5] K. Weinert, I. Inasaki, J.W. Sutherland, T. Wakabayashi, Dry machining and minimum quantity lubrication, Annals of the CIRP 53 (2) (2004) 511–537.
[6] V.S. Sharma, M. Dogra, N.M. Suri, Cooling techniques for improved productivity in turning, International Journal of Machine Tools and Manufacture 49 (6) (2009) 435– 453.
[7] R. Alberdi, J.A. Sanchez, I. Pombo, N. Ortega, B. Izquierdo, S. Plaza, D. Barrenetxea. Strategies for optimal use of fluids in grinding. Int. J. Mach. Tools Manuf., (2011) 51(6), 491-499. Elsevier.
[8] W.B. Rowe, Principles of Modern Grinding Technology, William Andrew Applied Science Publishers, 2009.
[9] E. Brinksmeir, C. Heinzel, M. Wittmann, Friction, Cooling and Lubrication in grinding, Annals of the CIRP, 1999, p. 581.
[10] T. Akiyama, J. Shibata, S. Yonetsu, Behaviour of grinding fluid in the gap of the contact area between a grinding wheel and workpiece, in: Proceedings of the Fifth International Conference on Production Engineering, Tokyo, 1984.
[11] F. Engineer, C. Guo, S. Malkin, Experimental measurement of fluid flow through the grinding zone, ASME Journal of Engineering for Industry 114 (1992) 61–66.
[12] S. Ebbrell, N.H. Wooley, Y.D. Tridimas, D.R. Allanson, W.B. Rowe, Effects of cutting fluid application methods on the grinding process, International Journal of Machine Tools and Manufacture 40 (2) (2000) 209–223.
[13] Webster, Jhon A. Manufacturing engineering, march 2008
[14] M.N. Morgan, A.R. Jackson, H. Wu, V. Baines-Jones, A. Batako, W.B. Rowe, Optimisation of fluid application in grinding, Annals of the CIRP 57 (2009) 363–366.