Conformado superplástico: Aproximación a tecnologías emergentes
22 de julio de 2010
Muchos procesos industriales de conformado, como la laminación o la extrusión producen grandes deformaciones plásticas y, en ocasiones, pueden formar granos submicrométricos (100 nm a 1 µm). Sin embargo, mediante estas técnicas de deformación o conformado, una o más dimensiones del material se reducen de tal forma que, si se requieren acumular grandes deformaciones, lo que se obtiene son láminas muy delgadas (laminación) o filamentos (extrusión) que tienen poca utilidad práctica, si se piensa en aplicaciones de tipo estructural.
Sin embargo, existen métodos de deformación intensa en que el material sufre cambios mínimos en sus dimensiones, por lo que no hay un límite geométrico definido a la deformación que se puede alcanzar, suponiendo que el material tenga la suficiente ductilidad.
El término superplasticidad introducido en metalurgia por Bochvar y Sviderskaya, en 1945, es la propiedad que posee un material policristalino de experimentar (sin elevados esfuerzos aplicados) grandes alargamientos, de manera isotrópica, sin fractura, cuando está sometido a esfuerzos de tracción mecánica (Ver figura 1).
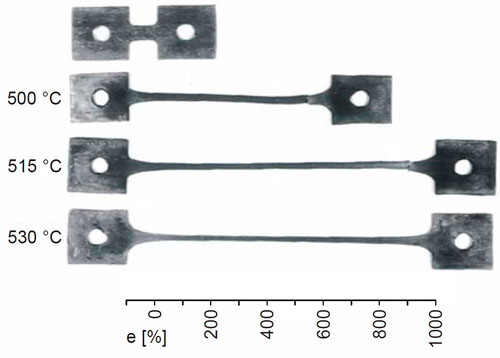
Aunque no existe un límite de alargamiento que delimite el comportamiento superplástico del que no lo es, los alargamientos máximos a fractura que se obtienen con materiales superplásticos varían desde varios cientos a varios miles por ciento. En aleaciones metálicas superplásticas se han reportado deformaciones de hasta un 8.000% en aleaciones de bronce, aluminio y otros materiales.
En la literatura se reconocen tres tipos de superplasticidad: la superplasticidad de transformaciones, que se exhibe en materiales policristalinos que experimentan cambios dimensionales anisotrópicos frente a la aplicación de cambios físicos determinados. En segundo lugar, la superplasticidad microestructural o de grano fino, que es aquella que se exhibe en materiales policristalinos metálicos, intermetálicos o cerámicos, cuyo tamaño de grano no supera los 10 µm, cuando son sometidos a bajas velocidades de deformación y temperaturas absolutas del orden de, o mayor, que la mitad de la temperatura de fusión, sin llegar a ésta. En tercer lugar la superplasticidad por esfuerzos internos.
Lo que interesó a muchos investigadores fue la gran ductilidad, definida como el beneficio potencial de la superplasticidad en el área del conformado de metales, la cual condujo al desarrollo de esta técnica (Superplastic Forming, SPF) como medio para conformar materiales superplásticos de clase única. La técnica de SPF se considera como un proceso de conformado de formas casi acabadas (near-net shape) que requiere de una sola matriz superficial, en lugar de los pares de matrices que se utilizan normalmente en las operaciones de conformado de chapa metálica. Una lámina de material se conforma en un paso dentro de la cavidad de la matriz (la cual se calienta previamente a la temperatura deseada) que suele tener la forma final a las dimensiones de la parte deseada, usando gas a presión, el proceso se ilustra esquemáticamente en la figura 2.
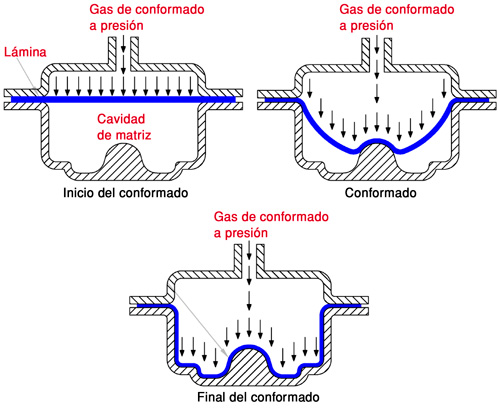
La superplasticidad microestructural o de grano fino es la que se utiliza para la obtención de piezas por conformado de chapas y los requisitos básicos para conseguir deformación superplástica son, fundamentalmente, tres:
- Microestructura con grano fino, uniforme y equiaxial menor a 10 µm
- Velocidad de deformación controlada, normalmente en el rango 1x10-5 – 1x10-1 s-1
- Temperatura experimental de trabajo mayor o igual de 0,5 Tm (donde Tm es la temperatura absoluta de fusión del material)
Este último requisito (que aparece por el hecho de que la superplasticidad es un proceso controlado por difusión), suele ser incompatible con la retención de un grano pequeño, ya que las altas temperaturas favorecen el crecimiento de grano (por lo que en algunas aleaciones metálicas se necesita la presencia de ‘dispersoides’ distribuidos uniformemente para impedir el crecimiento de grano y que favorezcan el comportamiento superplástico).
Además del conformado convencional, por la técnica de SPF se puede obtener beneficios adicionales mediante la mejora de la técnica, impulsada principalmente por la gran flexibilidad del proceso. El SPF puede combinarse con otros procesos de fabricación para un mejor y más eficiente proceso de conformado; por ejemplo con procesos de unión convencional, unión por difusión (Difussion Bonding, DB) y embutición profunda (Deep Drawing, DD).
El SPF se combina con la unión por difusión (Diffusion Bonding, DB) para fabricar formas más complejas (tipo panal de abeja). La DB es la unión dos componentes mediante la aplicación de carga a temperaturas elevadas donde la unión molecular resultante es completamente homogénea. Con la técnica SPF/DB las partes se fabrican mediante la unión por difusión de varias chapas o láminas con un patrón específico y, a continuación, se expanden superplásticamente las chapas para producir una estructura integral rígida (Figura 3).
Se pueden incorporar modificaciones, alteraciones o incluso características adicionales con el fin de producir los conceptos avanzados que enriquecen la capacidad de la técnica convencional SPF, en diversos medios y aspectos. Hay varios ejemplos de tales conceptos que incluyen el SPF de doble cara, SPF de varias partes y el SPF con presión posterior. El último concepto se ilustra esquemáticamente en la figura 4, donde se representa la presencia de presión sobre la parte posterior de la chapa conformado. No se incrementan aspectos como el costo o la eficiencia, lo que se quiere es evitar o minimizar la cavitación en la pieza conformada y mejorar así sus propiedades mecánicas, que se cree están asociadas con la presencia de presión posterior.
La combinación SPF/DD, por ejemplo, es un nuevo concepto en el que una parte se conforma parcialmente mediante una embutición profunda rápida, seguida por una etapa de SPF, que se encarga de los detalles complejos de la forma que se creó. De esta manera, el tiempo de conformación se reduce aún más, manteniendo la importancia del SPF. Un esquema del proceso se muestra en la figura 5.
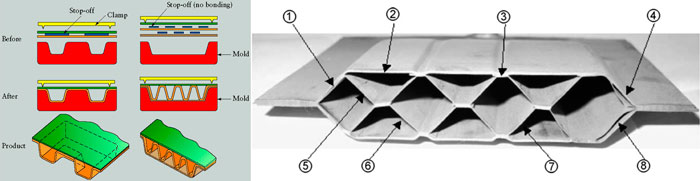
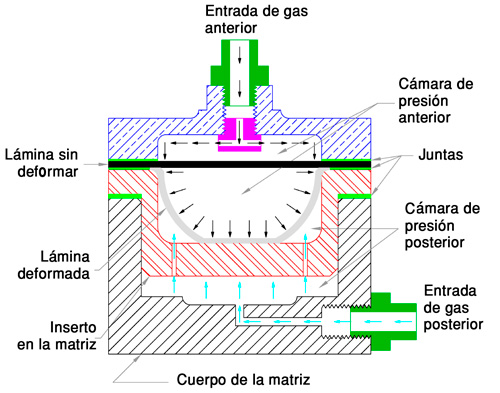
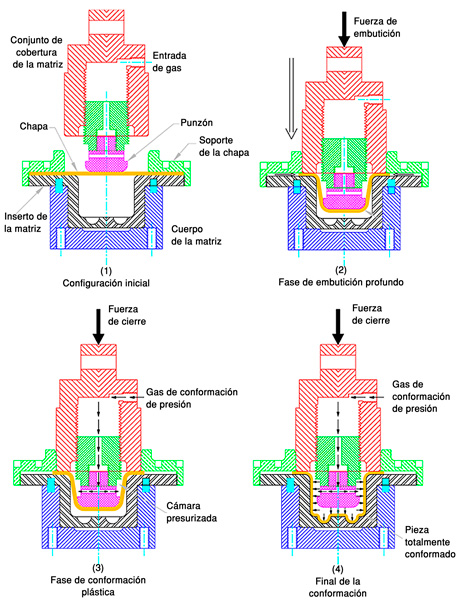
Aplicaciones
El conformado superplástico comercial incluye preferencialmente aleaciones de aluminio, níquel, zinc y titanio para la producción de componentes en las industrias automotriz, aeroespacial, médica. Varias aleaciones ligeras de gran importancia industrial y comercial exhiben superplasticidad, como la aleación de titanio Ti6Al4V, la aleación de aluminio 5083 y la aleación de magnesio AZ31. De hecho, por estas y muchas otras aleaciones ligeras, el conformando mediante cualquier otra técnica sería poco práctico, debido a su limitada formabilidad en las condiciones de recibido. En la figura 6 se muestran algunas piezas fabricadas por este método.
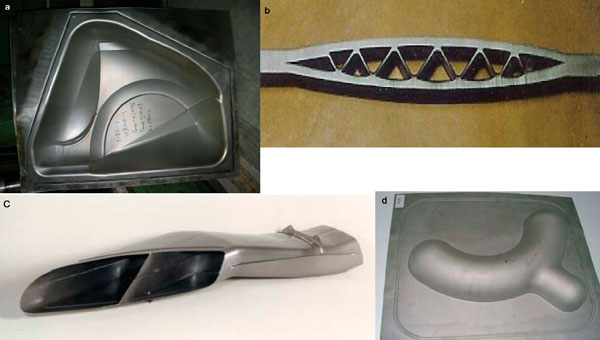
Las propiedades termomecánicas de los materiales obtenidos con esta tecnología, hacen que su aplicación industrial sea insustituible para la obtención de piezas de formas complicadas que requieran altas exigencias en el conformado o en el servicio, como las partes estructurales de aviones supersónicos. Actualmente, esta propiedad está presente en cerámicos con tamaño de grano <1 µm y ha situado el estudio de cerámicos superplásticos como un campo de investigación de gran interés. En estos últimos se han encontrado deformaciones de hasta un 1.040% en un policristal de circonio tetragonal estabilizado con itria (YTZP).
Ventajas frente a las alternativas tradicionales
El conformado superplástico (SPF) ofrece muchas ventajas con respecto a las operaciones de conformado convencionales:
- La capacidad para conformar componentes con formas muy complejas, que no pueden ser fabricadas por técnicas convencionales, o sólo se pueden obtener por múltiples conformados sucesivos seguidos por unión o soldadura de varias partes
- La capacidad para dar forma, a materiales muy difíciles de conformar, con relativa facilidad como son las aleaciones de titanio y magnesio, que se sabe que tienen menor ductilidad en la condición de llegada debido a sus estructuras cristalinas HCP
- Bajo costo en matrices, ya que se necesita una matriz con una sola cavidad para conformar el componente, independientemente de la complejidad de la forma y de la relación de aspecto dimensional
- El proceso se realiza en un solo paso, produciendo un bien terminado o un componente casi acabado
- Reducción del número total de partes y, en consecuencia, el número de fijaciones y/o uniones, lo que conlleva a la mejora de la seguridad en determinadas aplicaciones (por ejemplo, el sector aeroespacial)
- Mayor flexibilidad de diseño y control dimensional
La técnica de SPF se ha enfrentado a una serie de retos y problemas que impiden su uso generalizado a mayor escala. Las costosas operaciones de preconformado, como la preparación de los materiales con estructura de grano fino y el calentamiento a la temperatura de conformado deseada, representan una de estas cuestiones. Además, debido a que la velocidad está controlada y limitada, a velocidades bajas, hace el proceso relativamente lento y desfavorable para aplicarlo en la producción de un alto volumen de componentes de automoción. Sin embargo, la técnica proporciona una herramienta única para conformado de aleaciones ligeras, y, a pesar de los obstáculos y desafíos en el camino, todavía ofrece notables ventajas y méritos sobre las técnicas de conformado convencionales.
Referencias
- J. R. Marty Delgado, J. E. Alonso Pérez, M. López Escobar. Caracterización del comportamiento superplástico de materiales: revisión del estado del arte. V Conferencia Internacional de Ingeniería Mecánica, Universidad Central Marta Abreu de Las Villas, Cuba. 2008.
- Caballé Rodríguez, Iván. Diseño y puesta a punto de un sistema de conformación por extrusión en canal angular para obtención de materiales metálicos con grano ultrafino. Tesis de Máster, Departamento de Ciencia de los Materiales e Ingeniería Metalúrgica, Universidad Politécnica de Cataluña, 2005.
- A. Smolej, E. Slacek, R. Turk. State and development of some wrought aluminum alloys for special and general applications. Metalurgija, Vol. 41, Nº 3, 2002, 149 – 155.
- Fadi K. Abu-Farha, Marwan K. Khraisheh. An integrated approach to the Superplastic Forming of lightweight alloys: towards sustainable manufacturing. International Journal Sustainable Manufacturing, Vol. 1, Nos. 1/2, 2008, 18 – 40.
- Wang Gang, Zhang Kair-Feng, Chen Jun, Ruan Xue-Yu. Superplastic forming gas pressure of titanium alloys bellows. Trans. Nonferrous Met. Soc. China, Vol. 14, Nº 5, 2004, 896 – 900.
- Zhipeng Zeng, Yanshu Zhang, Yi Zhouc, Quanlin Jin. Superplastic Forming of Aluminum Alloy Car Body Panels. Materials Science Forum Vols. 475 – 479, 2005, 3025 – 3028.
- Han Wenbo, Zhang Kaifeng, Wang Guofeng. Superplastic forming and diffusion bonding for honeycomb structure of Ti–6Al–4V alloy. Journal of Materials Processing Technology, Vol. 183, 2007, 450 – 454.
- Conformado de Chapa. Departamento de Ingeniería Mecánica y Fabricación. Tecnología Mecánica, ETSII, UPM, WIKIFAB.
- Peter Anderton. Superplastic Forming/ Diffusion Bonding (SPF/DB) of Titanium and Aluminium Alloys, ENIMEP Novotel São Paulo Center, São Paulo, Brasil, 26th & 27th November 2007
- http://www.formtech.de/en/en-spfdb.htm