Verificación volumétrica, una solución real en la verificación de máquina-herramienta de grandes dimensiones
1. Introducción
La alta competitividad existente en un sector como el de la máquina-herramienta (MH) la precisión y la posibilidad de compensación de los errores es una diferencia competitiva entre fabricantes y usuarios de las mismas, adquiriendo especial relevancia en el mecanizado de precisión.
De las distintas fuentes de error que afectan a la precisión de una máquina-herramienta [1,2], son los errores geométricos los que mayor contribución realizan al error total de la máquina con un 60-70% del error total [3]. Estos pueden dividirse en errores cuasi-estáticos, causados por la estructura de la máquina, y dinámicos, causados por el movimiento de los husillos o vibraciones de la estructura. Su caracterización y posterior compensación vendrá determinada por la configuración estructural, volumen de trabajo y software de control de cada MH.
Tradicionalmente, la verificación geométrica ha sido ampliamente utilizada en la verificación de MH y máquinas de medir por coordenadas (MMC). Esta se basa en la caracterización de los errores de cada eje por separado mediante la medición directa de los errores a compensar en unos posiciones determinadas de la máquina, independientemente del modelo cinemático de la máquina y de su secuencia de movimientos [4]. La extrapolación de las funciones de caracterización obtenidas mediante este método al resto del volumen de trabajo es un proceso complejo. La necesidad de utilizar sistemas de dimensiones conocidas de alto rango junto con el considerable tiempo de preparación necesario, hace que esta complejidad sea especialmente relevante en máquinas de largo recorrido capaces de mecanizar piezas de grandes dimensiones; haciendo de la verificación geométrica un proceso lento y costoso. Es en este tipo máquina, ampliamente utilizada en sectores como el eólico, ferroviario o naval, donde la verificación volumétrica mediante laser tracker proporciona grandes ventajas frente a la verificación geométrica.
La verificación volumétrica trabaja a partir de la medición del efecto conjunto de los errores geométricos en cada punto a partir del modelo cinemático de la máquina y el movimiento multi-eje de la misma [5-7]. Lo que se traduce una reducción significativa del tiempo necesario en la captura de información frente a la verificación geométrica. Al mismo tiempo, el fuerte desarrollo experimentado por los controles de CN de arquitectura abierta proporciona un marco propicio para la corrección homogénea de los errores geométricos en todo el volumen de trabajo de la MH, a partir de las funciones paramétricas de compensación obtenidas mediante el proceso de identificación base de la verificación volumétrica.
La fuerte demanda de mecanizado de piezas de grandes dimensiones con gran valor añadido, experimentado por el auge de sectores como el eólico, ferroviario o naval, hacen de la verificación volumétrica mediante laser tracker la técnica idónea de verificación y mejora de precisión en MH de largo recorrido. Esta presenta una reducción de tiempo y costes frente a otros métodos de verificación.
2. Verificación Volumétrica
La verificación volumétrica es un proceso de identificación intensiva de parámetros a partir de un modelo de optimización no lineal mediante la medición indirecta de los errores de la máquina en su volumen de trabajo. Esta consiste en la minimización, mediante el software desarrollado, de la diferencia entre pares de puntos teóricos introducidos mediante control numérico (CN) y reales capturados por el sistema de medida, en función de las posibilidades y necesidad de la técnica a emplear.
En máquinas de largo recorrido el volumen de trabajo de las mismas será un factor limitante de la utilización de artefactos de medida tradicionales, reduciendo las posibilidades de técnicas a emplear con las que realizar la captura de puntos. Los sistemas de medida que mejor se adecuan al recorrido de los ejes de este tipo de máquina son los sistemas de largo rango como laser tracker y laser tracers. La verificación volumétrica mediante LT se basa en la caracterización de los errores geométricos de cada máquina a través del modelo matemático de su cadena cinemática (figura 1).
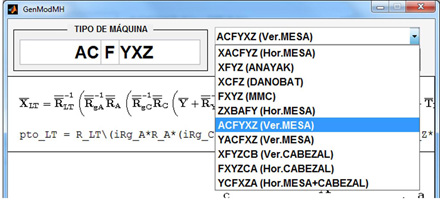
A partir de la configuración de la MH y su secuencia de movimientos se genera la ecuación de movimiento que permite obtener la posición de la punta de la herramienta con respecto a la posición nominal programada.
La diferencia entre coordenadas teóricas de la máquina y las coordenadas obtenidas por el laser tracker muestra la influencia conjunto de los errores geométricos de la máquina en su volumen de trabajo, error volumétrico (ev). La minimización de este mediante diferentes estrategias de identificación, funciones de regresión y criterios de convergencia empleados el software proporciona las funciones de caracterización de cada uno de los errores geométricos (figura 2).
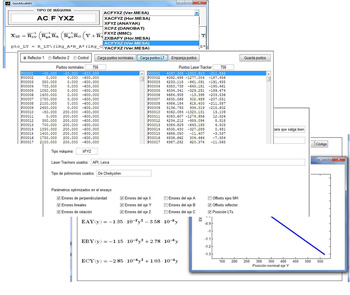
Notar que se trata de una compensación matemática no física de los errores, la cual compensa el efecto conjunto de los errores geométricos en todo el volumen de trabajo y no cada uno de ellos de manera independiente.
La caracterización de los errores a partir de la medición indirecta de los mismos disminuye el tiempo necesario frente a la medición directa de los errores (figura 3). Para ello, el posicionamiento de la máquina se realiza mediante un programa CN configurando adecuadamente el tiempo de parada en cada posición, y mediante la detección de esta por parte de los laser tracker se toma un número de mediciones predefinidas proporcionando el LT el valor medio de todas ellas.
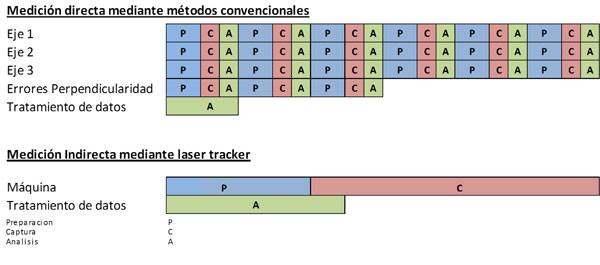
3. Captura de datos in-situ
La disposición espacial del laser tracker respecto al volumen de trabajo a verificar viene determinada por la configuración estructural de la máquina a verificar. El laser tracker ocupa el lugar correspondiente a la pieza dentro de la secuencia de movimientos de la máquina mientras el retro-reflector ocupa la posición de la herramienta durante el mecanizado.
La distribución espacial de los puntos a medir se determina en función de los rangos de trabajo más utilizados por cada máquina durante el mecanizado. Si el mecanizado se realiza en todo el volumen de trabajo de la máquina, se realiza una distribución homogénea de puntos a partir de los cuales se proporciona una corrección global dando la misma importancia a toda la zona de trabajo. Sin embargo, si el mecanizado se realiza fundamentalmente en una zona determinada, la distribución espacial de los puntos a medir se centra en esta zona lo cual se traduce en una mejor compensación de los errores en esta zona respecto al resto (figura 4)
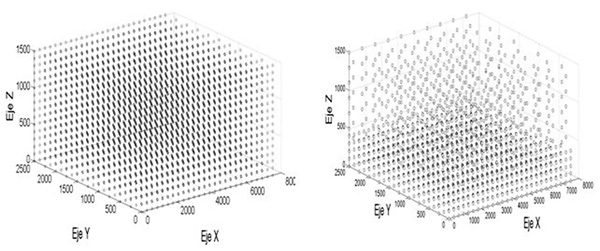
En cualquier caso, la medición de los puntos debe realizarse sin que se rompa el rayo entre LT y reflector siendo necesario alejar los laser tracker del volumen de trabajo a verificar evitando los giros no permitidos por el cabezal del LT, bien simplemente alejando el trípode sobre el que se coloca o bien mediante un perfil en voladizo asociados al movimiento de la pieza. Una vez comprobado que el LT es capaz de direccionar el rayo a cualquier punto del volumen de trabajo, es necesario comprobar que no se produce perdida del haz por parte del reflector en este. Para ello se dispone de reflectores con diferentes diámetros y diferentes ángulos de entrada del haz del laser (figura 5). Un retro-reflector convencional SMR de 2,5 pulgadas tiene un ángulo de incidencia de ±30º, mientras que un reflector cateye presenta ángulos de incidencia próximos a las ±90º. Mención especial merece el active target de Api, retro-reflector motorizado el cual orienta el reflector automáticamente de manera que el haz del rayo incida en el centro del mismo permitiendo la captura de puntos en volúmenes de trabajo mayores.
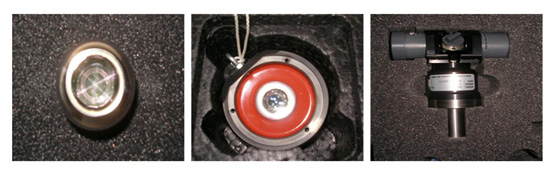
Durante la fase de adquisición de datos, las condiciones ambientales deben ser lo más estables posibles evitando variaciones térmicas durante la medición. Estas se pueden producir como consecuencia de gradientes de temperatura debido a corrientes de aire, instalaciones como calefacción o sistemas de iluminación. Es necesario procurar tener una temperatura homogénea a lo largo de la medición tanto en los componentes estructurales que definen la cadena cinemática de la máquina como en el volumen de trabajo de la misma. En el caso de producirse variaciones significativas de temperatura los elementos estructurales modifican sus dimensiones haciendo que la máquina no se posicione en el mismo punto al principio y al final de la toma de datos frente a una misma coordinada nominal. De la misma manera, si se produce una variación significativa a lo largo del camino que recorre el haz laser del LT esta influye en su longitud de onda y por lo tanto en las coordenadas del punto capturado. La monitorización de la temperatura durante la toma de datos en diferentes puntos de la máquina mediante sensores de temperatura permite conocer los cambios de esta con el objetivo de determinar su influencia en las coordenadas de los puntos medidos, pero no nos permite compensar su efecto (figura 6).
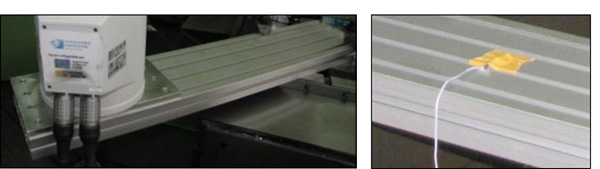
Uno de los factores más influyentes en la captura de datos es la incertidumbre de medición asociada al sistema de medida empleado.
Punto Medido = Punto Real ± Incertidumbre medición
La incertidumbre de medición está formada por la influencia conjunta de errores sistemáticos de carácter constructivo o ambiental, fácilmente compensables, y errores aleatorios como el ruido de medida del LT. Consecuencia de los errores introducidos por los dos encoders angulares y el interferómetro que proporcionan la posición del punto medido en coordenadas esféricas. La influencia del ruido de medición con las coordenadas obtenidas está directamente relacionada con la distancia entre reflector y laser tracker. Ante un mismo error del encoder angular la diferencia entre las coordenadas de un punto con y sin ruido angular aumenta al aumentar la distancia de medición. Una contribución menor realiza la incertidumbre radial determinada por una relación lineal entre la distancia reflector-laser tracker mas un término independiente aleatorio (figura 7).
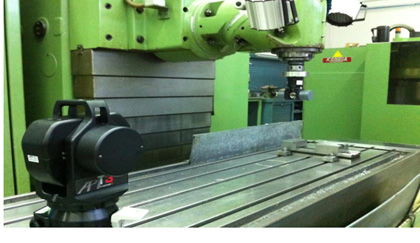
La influencia del ruido de medida en las coordenadas de los puntos capturados, así como el proceso de auto-calibración del LT hacen que el error volumétrico de la máquina no esté formado únicamente por la influencia conjunta de los errores geométricos de la máquina, dificultando la caracterización de estos al incluir en ella un comportamiento no achacable a los errores geométricos. La verificación volumétrica resulta espacialmente útil en máquinas de largo recorrido, donde la contribución de los errores geométricos al error volumétrico es mucho mayor que la contribución de incertidumbre de medición. Mediante un correcto posicionamiento del laser tracker respecto a los puntos a medir se reduce la influencia de la incertidumbre de medición, siendo posible aplicar esta técnica en máquinas de menor tamaño al eliminar la contribución del ruido de medida angular mediante técnicas como la multilateración. A partir de la información proveniente de tres o más laser trackers (figura 8).
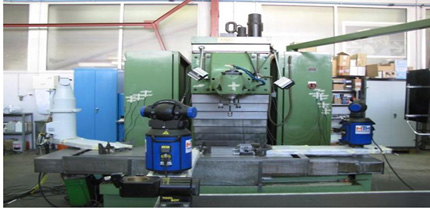
4. Resultados
En este punto se presentan los resultados obtenidos en la verificación volumétrica de dos centros de mecanizados con características dimensionales completamente diferentes. Ambas se realizaron mediante la utilización de un sólo laser tracker en una única posición partiendo de la misma estrategia de optimización.
En primer lugar se presentan los resultados de una fresadora de control numérica estándar, a la cual se realizó una compensación homogénea de sus errores geométricos en todo su volumen de trabajo. Para ello se realizo un mallado homogéneo de su volumen de trabajo con 0 mm ≤ X ≤ 500 mm, 0 mm ≤ Y ≤ 400 mm 0 mm ≤ Z ≤ 200 mm.
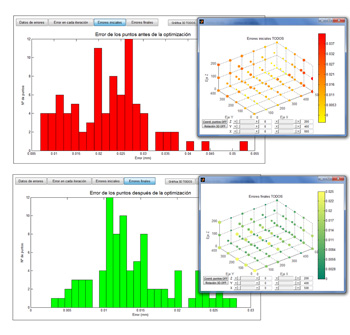
Los resultados de la figura 9 muestran como se ha producido una compensación homogénea del efecto conjunto de los errores geométricos a lo largo de todo el volumen de trabajo. Se ha reducido el error volumétrico medio de 63.9µm a 14,9µm, lo que equivale a una reducción del error del 76.7%. Del mismo modo, el error máximo se ha reducido de 101.9 µm a 32.3 µm, lo que equivale a una reducción de 68.3%.
En esta MH el error volumétrico final es del mismo orden que el error de medición consiguiéndose reducir el error volumétrico inicial en un 76.7%. Ante este tipo de MH, en el que el error volumétrico final es del mismo orden que el error de medición pueden surgir problemas de overfitting. La aplicación de técnicas de multilateración en condiciones adecuadas puede reducir el límite de optimización mejorando la caracterización de los errores [8, 9].
En la figura 10 se observan los resultados de la verificación volumétrica de una máquina con un recorrido de movimiento mayor que en el ensayo anterior. El volumen de trabajo de esta máquina-herramienta 0 mm ≤ X ≤ 1500 mm, 0 mm ≤ Y ≤ 1500 mm -1490 mm ≤ Z ≤ 0 mm se discretizó formando un mallado uniforme con once puntos de medición en cada uno de su ejes.
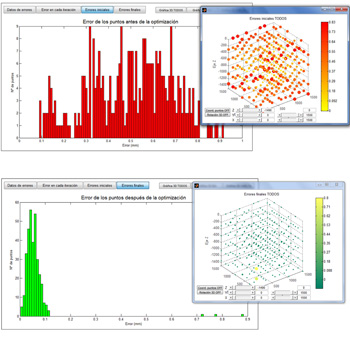
Mediante la práctica de un proceso de verificación volumétrica se reduce el error volumétrico de la máquina de un valor inicial en el proceso de identificación de 503.4 µm a 54.2, lo que equivale a una reducción del 89.3%. El error volumétrico de la optimización no está formado solamente por el efecto de los errores geométricos sino también por otros errores aleatorios, como el ruido de medición, o influencias de las variaciones térmicas en los elementos estructurales de la máquina a verificar. Motivo por el cual el error tras la compensación no es igual al error volumétrico obtenido en el proceso de identificación.
Para poder compensar la influencia de los errores geométricos, una vez obtenidas las funciones de aproximación de los diferentes errores geométricos, y dependiendo del software de control que disponga la máquina es necesario realizar un tratamiento de las mismas con objeto de compensar los errores en el CN de la máquina. Si el software de la máquina es capaz de trabajar con funciones paramétricas de compensación de cada uno de los errores de la máquina este tratamiento no será necesario. Si esto no ocurre, es necesario aplicar un proceso de postprocesado de los CN a utilizar en la máquina; mediante la utilizar de un software y a partir del modelo cinemático de la máquina se compensa el efecto de los errores geométricos generando un nuevo CNC (figura 11). El postprocesado se puede realizar tanto desde un PC como desde el software de la máquina a través de una rutina dedicada.
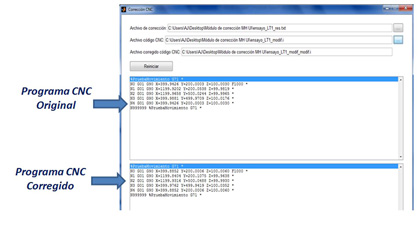
Conclusiones
La verificación volumétrica mediante laser tracker disminuye el tiempo empleado en la adquisición de datos al realizar una medición indirecta de los errores geométricos de la MH, siendo estos tratados posteriormente en modo off-line permitiendo mientras tanto el uso de la máquina a verificar. Del mismo modo, resulta el procedimiento más adecuado en la verificación de máquinas de largo recorrido, permitiendo una caracterización en función de las zonas de interés de la máquina y eliminando las zonas de concentración de errores.
Mediante la datos capturados en tres o más posiciones distintas mediante 1, 3 o más laser tracker, en función de las condiciones ambientales en la que se realice la toma de datos, y aplicando técnicas de multilateración, se reduce el efecto del ruido de medida de los laser tracker mejorando la caracterización de los errores pudiendo emplearse esta técnica de verificación en MH con menor rango de trabajo.
Bibliografía
[1] R.Ramesh, M.A. Mannan, A.N. Poo (2000). Error compensation in machine tools Part I: geometric, cutting-force induced and fixture- dependent errors. Machine Tools & Manufacture 4. Páginas1235-1256.
[2] R.Ramesh, M.A. Mannan, A.N. Poo (2000). Error compensation in machine tools Part II: thermal errors. Machine Tools & Manufacture 40. Páginas 1257-1284.
[3] N.A.Barakat, M.A. Elbestawi, A.D. Spence (2000). Kinematic and geometric error compensation of a coordinate measuring machine. Machine Tool Manufacture International Jurnal of Machine Tools and Manufacture 40. Páginas 833-850.
[4] Jenq shyong Chen, Tzy Wei Kou, Shen Hwa Chiou (1999). Geometric error calibration of multi-axis machines using an auto-alignment laser interferometer. Precision Engineering 23. Páginas 243-252.
[5] S.Aguado, D.Samper, J. Santolaria, J.J. Aguilar (2011). Identification strategy of error parameter in volumetric error compensation of machine tool based on laser tracker measurements. International Journal of Machine tool & Manufacture. Volume 53. Páginas 160-169
[6] H.Schwenke, W.Knapp, H. Haitjema, A. Weckenmann, R.Schmitt, F.Delbressine (2008). Geometric error measurement and compensation of machines-An update. CIRP Annals-Manufacturing Technology. Pages 660-675.
[7] S.Aguado, D.Samper, J. Santolaria, J.J. Aguilar (2012). Towards an effective identification strategy in volumetric error compensation of machine tools. Measurement Science and Technology, 23,12pp.
[8] S.Aguado, D.Samper, J. Santolaria, J.J. Aguilar (2013). Influence of measurement noise and laser arrangement on measurement uncertainty of laser tracker multilateration in machine tool volumetric verification. Precision Engineering. 37, 929-943.
[9] S.Aguado, D.Samper, J. Santolaria, J.J. Aguilar (2013). Study of self-calibration and multilateration in machine tool volumetric verification for laser tracker error reductions.PartB: Journal of Engineering Manufacture. DOI: 10.1177/0954405413511074.