Estudio de la viabilidad de FSW para la unión del AA1100 B4C
Soldadura FSW de material compuesto de matriz de aluminio reforzado con partículas de B4C
El objetivo de este trabajo es analizar si la técnica permite la obtención de una unión soldada de elevada calidad, libre de defectos; y al mismo tiempo, evaluar los efectos que produce la agitación del material durante el proceso de soldeo en la microestructura del material compuesto.
Los resultados mostraron que la soldadura FSW no tiene influencia significativa en la distribución de las partículas de B4C, que se mantiene homogénea tras el proceso, si bien produce un efecto de rotura que disminuye su tamaño. En cuanto a la forma de las partículas, se ha observado que la soldadura FSW produce un efecto de redondeo, probablemente causado por el impacto y la abrasión producida entre ellas durante el proceso. Por otro lado, se ha determinado mediante la técnica de EBSD, que el tamaño de grano en el cordón de soldadura es inferior al de la matriz del material compuesto, lo que demuestra que ha tenido lugar un proceso de recristalización dinámica como consecuencia del batido del material.
Estas modificaciones en la microestructura del cordón justifican el aumento de dureza obtenido, que es un 25% superior al material base, y la mejora de las propiedades tribológicas, cuya tasa de desgaste es un 9% inferior al material base. Además, los ensayos de tracción han demostrado que la unión soldada mediante FSW es más resistente que el material compuesto.
1. Introducción
El soldeo de distintos materiales compuestos de matriz de aluminio (AMMCs) se ha convertido, en estos últimos años, en una necesidad para un gran número de aplicaciones, con el inconveniente de la complejidad de la unión de los compuestos de matriz metálica (MMCs). Algunas técnicas de soldadura por fusión que han permitido soldar MMCs pueden, aun así, llegar a presentar problemas como oclusión de óxidos en el cordón, porosidad, fisuración en caliente y reacciones químicas en las interfases refuerzo/matriz. La soldadura FSW se presenta, por tanto, como una opción alternativa [1, 2], ya que se trata de una soldadura en estado sólido, que en principio elimina los principales defectos provocados por la soldadura por fusión.
Uno de los principales usos del material compuesto AMMCs B4C es el almacenamiento y transporte de combustible nuclear gastado ya que este material responde a los requerimientos térmicos, de resistencia estructural y asimismo a los de protección radiológica, por ser el boro uno de los elementos que presenta mayor sección de captura neutrónica [3].
El presente trabajo pretende evaluar la viabilidad de FSW para la unión del AA1100 B4C. Para ello, se ha caracterizado la microestructura del material compuesto o material base (MB) y de la zona soldada por FSW, utilizando diversas técnicas como microscopía óptica (MO) y microscopía electrónica de barrido (SEM), y análisis de difracción de electrones retrodispersados (EBSD) [4]. El objetivo de esta caracterización es determinar la posible presencia de defectos en el interior de la soldadura, así como los efectos que produce la agitación del material durante el proceso en la microestructura del AMMC. Además, este estudio se ha complementado con la caracterización mecánica y tribológica, mediante ensayos de dureza, tracción y desgaste, tanto del MB como de la zona soldada.
2. Procedimiento experimental
El material compuesto utilizado es obtenido por vía pulvimetalúrgica (PM). Se trata de placas laminadas de 8 mm de espesor de una aleación de aluminio puro, cuya composición se muestra en la tabla 1, y que según la designación de la Asociación Internacional del Aluminio se corresponde con la aleación (AA1087), reforzado con un 8% en peso de B4C.
Elemento |
Fe |
Si |
Cu, Mn, Pb, Zn, Zr, Cr |
Mg |
Ni |
Ti |
Ga |
O |
Al |
% en Peso |
0,07 |
0,07 |
0,001 |
<0,001 |
0,005 |
0,006 |
0,005 |
0,126 |
99,87 |
Las soldaduras FSW han sido realizadas en el Centro Tecnológico Aimen, empleando el equipo de FSW ISTIR PDS-4 de la compañía MTS (figura 1). Partiendo de un total de cuatro chapas, el proceso se llevó a cabo realizando los cordones de soldadura a tope en la dirección de laminación, siendo la posición de las chapas en ‘L’, como se muestra en la figura 2, hasta formar un prisma rectangular hueco (figura 3), cuyas dimensiones finales son 150 x 150 x 500 mm. La herramienta utilizada para la realización de las soldaduras FSW está elaborada en carburo de tungsteno con cobalto (WC/Co), material apropiado para resistir el desgaste provocado por las partículas de B4C. El pin de la herramienta tiene forma troncocónica y su superficie es lisa, siendo su diámetro mínimo de 5 mm y máximo 7,28 mm, con una longitud de pin 6,8 mm; por su parte, el hombro de la herramienta tiene una superficie cóncava y lisa. Los parámetros de soldadura utilizados fueron: velocidad de rotación de 1.300 rpm, velocidad de avance de 100 mm/min, ángulo de inclinación de 3º, sentido de giro de la herramienta antihorario y modo de control de posición.
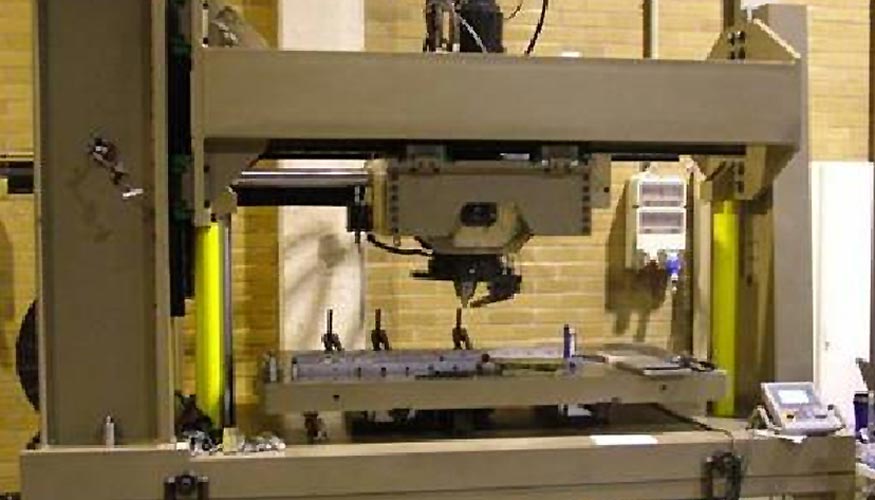
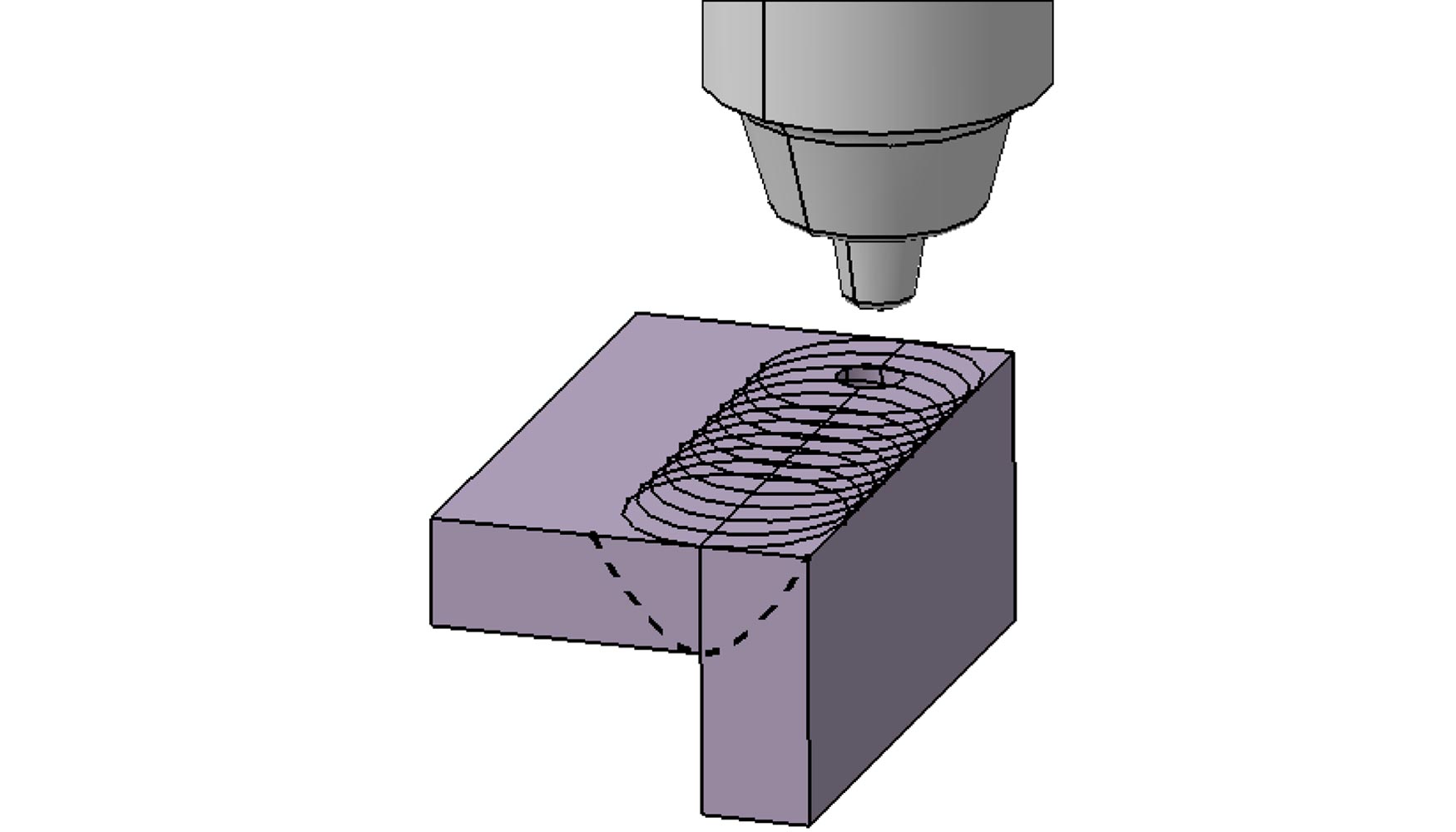
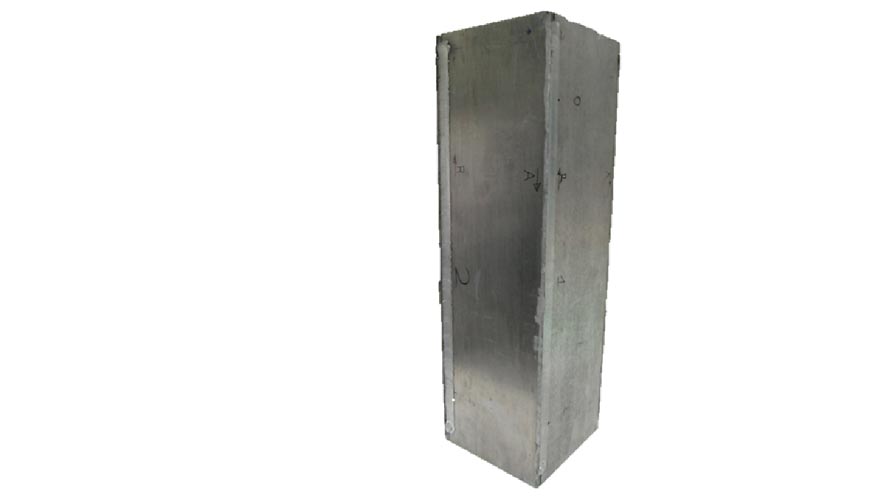
Las muestras para la caracterización microestructural se prepararon mediante desbaste y pulido mecánico, siendo la etapa final de pulido, realizada en un disco de lana con abrasivo de sílice coloidal de 0,04 μm, de gran importancia para el análisis mediante EBSD, ya que esta técnica requiere un alto grado de preparación superficial [4, 6, 7].
El análisis microestructural se ha realizado mediante un microscopio óptico, modelo Olympus GX51, dotado de software de análisis de imagen Five-Analisis Auto; un microscopio electrónico de barrido (SEM), modelo JSM 6510 de Jeol, equipado con un sistema de microanálisis por espectroscopía de dispersión de energía de rayos-X (EDS), Oxford Link, y un FIB (Focused Ion Beam), marca FEI Helios Nanolab 400, equipado con detector de difracción de electrones retrodispersados (EBSD), marca Oxford KHL. Las medidas de dureza (escala Vickers) se llevaron a cabo con un Microdurómetro, modelo EMCOTEST DuraScan 5, bajo la norma UNE-EN ISO 6507, utilizando una carga de 1 kgf con una separación entre huellas de 1 mm.
Las probetas de tracción, de forma prismática, se mecanizaron transversalmente a la unión soldada de forma que, después del mecanizado, el eje de la soldadura permanece en el centro de la longitud calibrada de la probeta (UNE-EN ISO 4136:13). Las probetas presentan una anchura máxima de soldadura (Ls) igual a 17 mm y una longitud de la zona calibrada (Lc=Ls + 60 mm) igual a 77 mm. Los ensayos de tracción se llevaron a cabo en una máquina Universal MTS 250 kN.
Por último, para la determinación de las propiedades tribológicas se utilizó un tribómetro con configuración ‘pin-on-disk’, de Microtest, modelo MT/60/NI/CORR, bajo las normas ASTM G99-05a (2000) y ASTM G115 04. Para la realización de los ensayos de desgaste se utilizó como contraparte o ‘pin’ una bola de alúmina de 4 mm de diámetro, una carga de 5 N, un radio de huella de 3 mm y una velocidad angular de 200 rpm. La distancia de deslizamiento ensayada fue de 500 metros. Para la medición de los perfiles de las huellas generadas en los ensayos de desgaste se usó un perfilómetro mecánico Wyko-Dektak 150; a partir de estas medidas se determinó el volumen de material perdido y la tasa específica de desgaste.
3. Resultados y discusión
3.1. Caracterización microestructural del material compuesto (AA1087- B4C)
La caracterización microestructural del MB muestra la presencia de gran cantidad de partículas de B4C, de distintos tamaños y forma irregular, distribuidas de forma diferente en función de la sección analizada. Las figuras 4 y 5 muestran micrografías ópticas y electrónicas del MB donde se observa que, la distribución de las partículas en la superficie de las chapas es menos homogénea que en la sección transversal, lo que puede achacarse al proceso de laminación. En las muestras obtenidas de la superficie, el porcentaje medio de superficie ocupada por el B4C es del 11,6%, el área media de la partícula es de 24,4 µm2 y el diámetro medio (dm) es de 6,3 µm; mientras que en la sección trasversal, el porcentaje medio de superficie ocupada por el B4C es del 13,0%, el área media de partícula es de 20,2 µm2 y el dm es de 6 µm. También se aprecia la presencia de numerosos poros, típicos de los materiales PM, y la ausencia de interacción química en la interfase Al-B4Ccomo consecuencia del proceso de sinterización, como se puede observar en la figura 6.
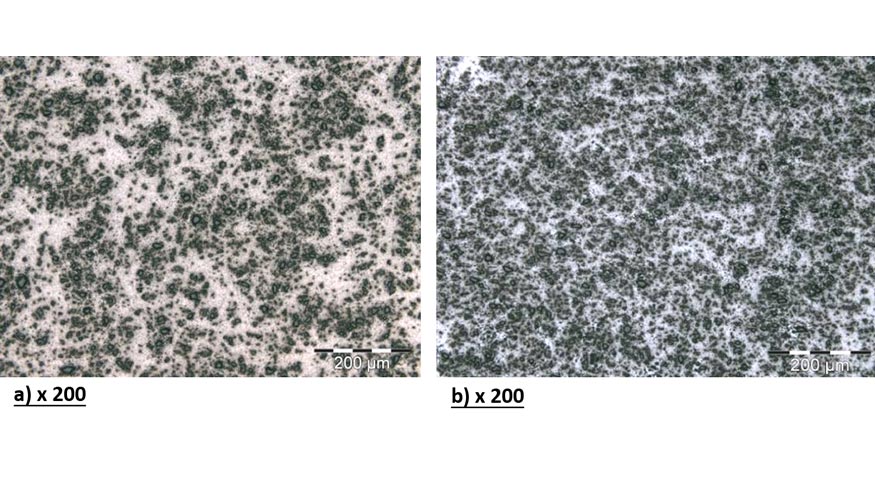
Fig. 4. Micrografías ópticas del MB: a) superficie y b) sección transversal.
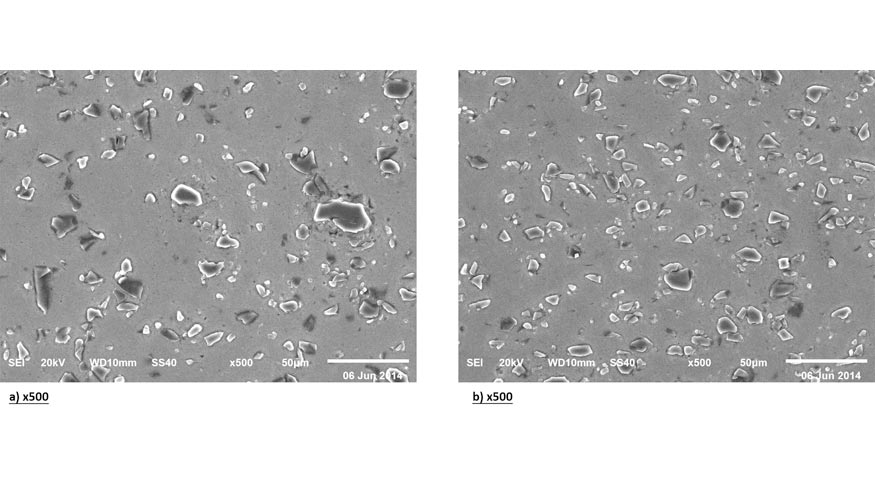
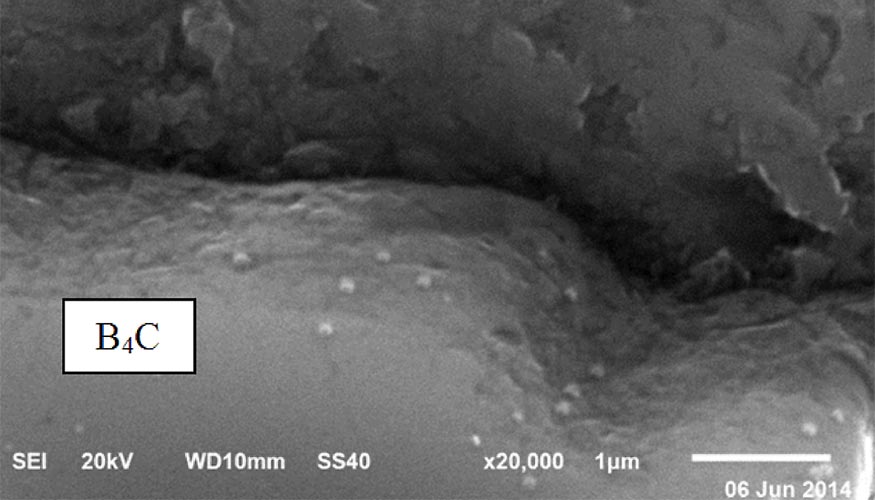
Fig. 6. Micrografía SEM de una interfase refuerzo/matriz en el AA1087- B4C.
3.2. Caracterización del cordón de soldadura
Tras la inspección visual todos los cordones de soldadura fueron radiografiados con el fin de asegurar la ausencia de defectos internos. Un ejemplo puede observarse en la figura 7, que muestra la macrografía superficial de uno de los cordones, junto con su correspondiente radiografía.
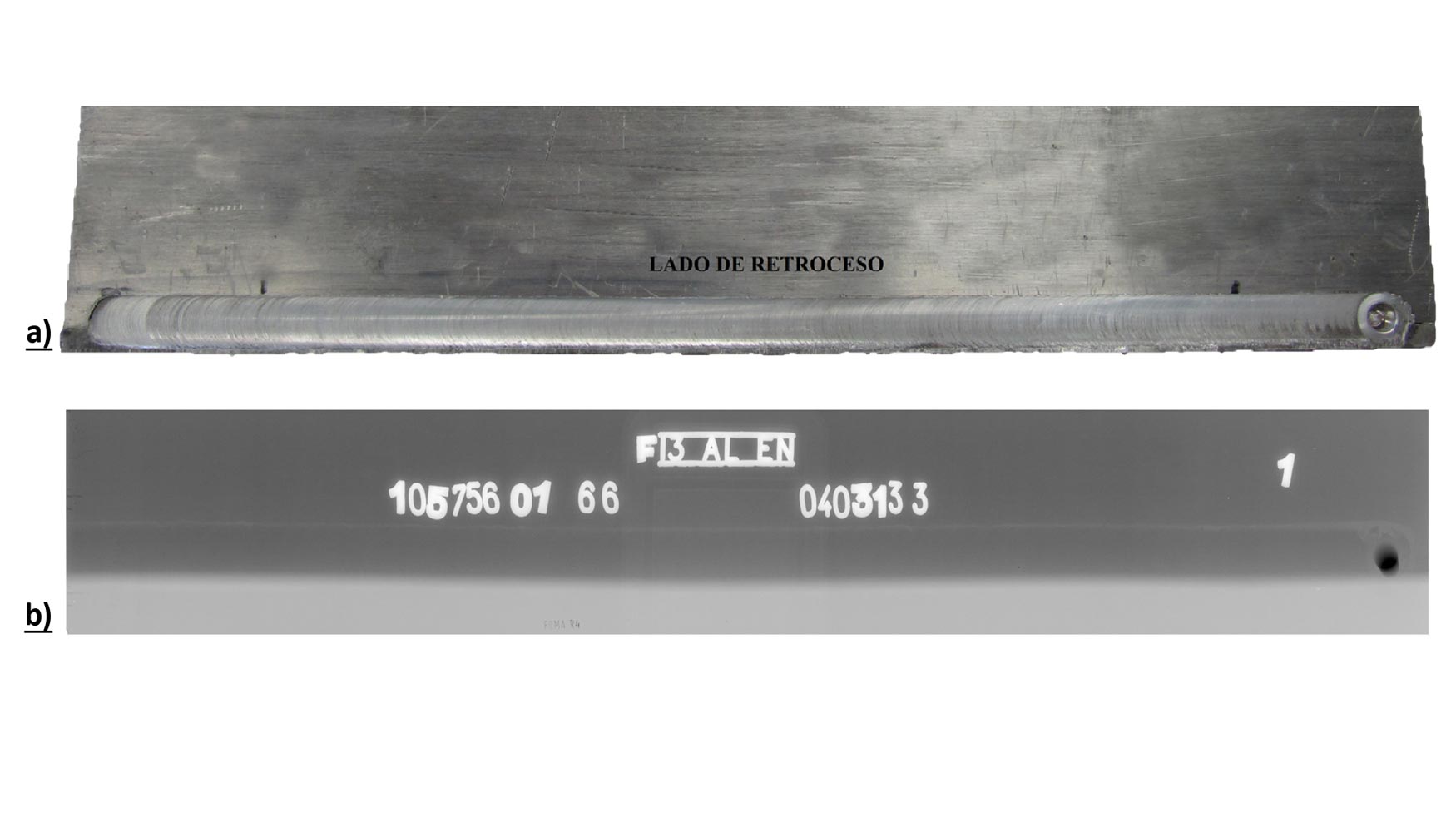
Para la identificación de las diferentes zonas características del cordón de soldadura se llevó a cabo el ataque de las muestras con NaOH al 20% [3]. En la figura 8 se muestra una macrografía de la sección transversal del cordón, mostrando la diferenciación aproximada de las zonas habituales de un cordón realizado mediante FSW: zona batida (nugget), la zona afectada termo-mecánicamente (ZATM) y la zona afectada térmicamente (ZAT). Se confirma la obtención de una unión consolidada y sin defectos. Un examen detallado a más aumentos demuestra que la distribución de las partículas es sustancialmente la misma en todas las zonas. Al realizar la cuantificación de las partículas en la zona batida se obtienen que el porcentaje medio de superficie ocupada por el B4C es del 15%; el área media de la partícula es de 23,0 µm2; y el dm es 5,3 µm, valores próximos a los obtenidos en la sección transversal del MB. Como indican estos datos, el proceso de FSW no afecta a la distribución de las partículas, pero revelan un mayor número de partículas de menor tamaño, justificable por la rotura de las partículas mayores a consecuencia del batido de la herramienta.
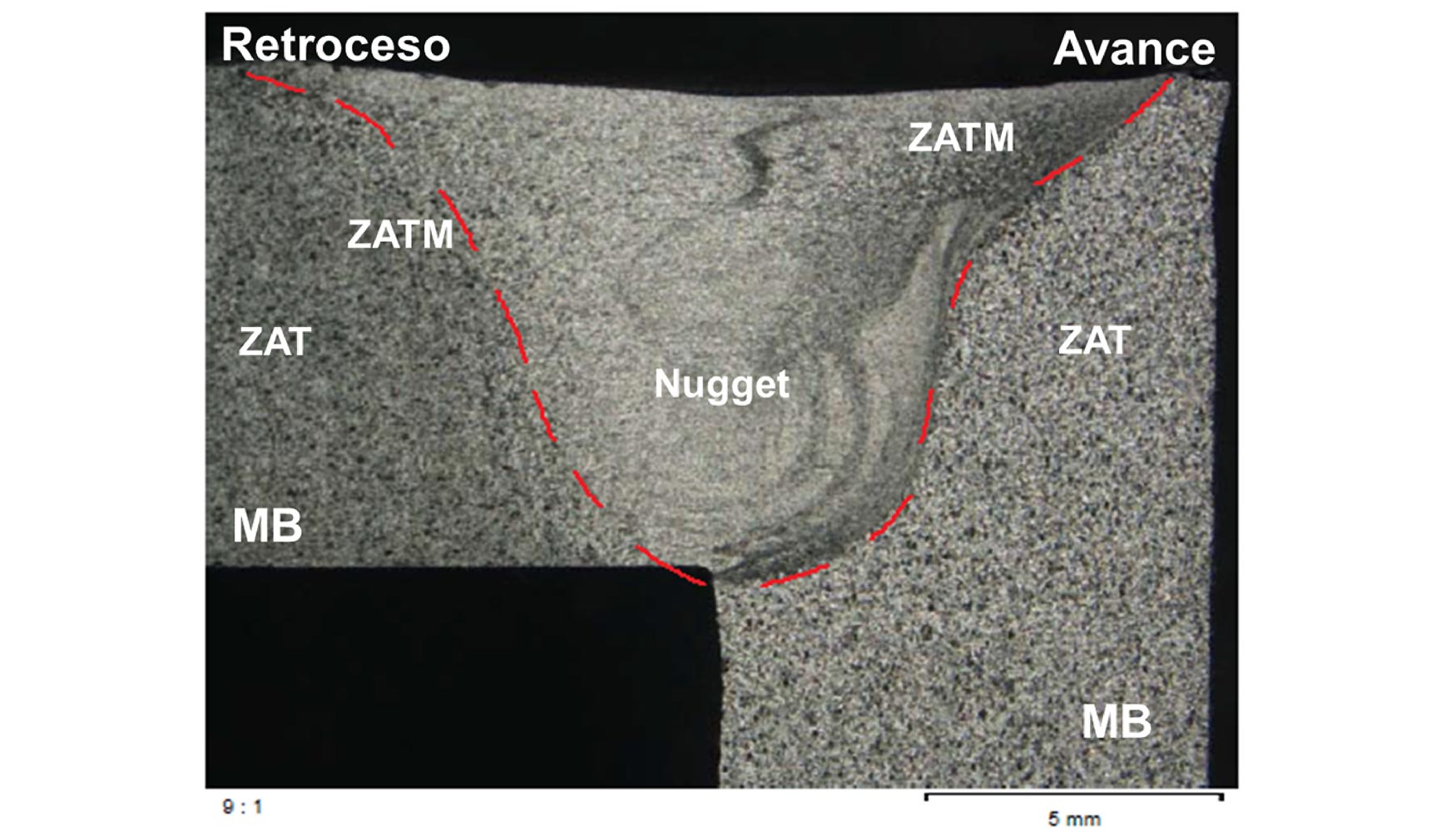
3.3. Determinación del tamaño de grano mediante EBSD
El análisis de la muestra por EBSD se realizó usando un FIB equipado con pantalla de fósforo y cámara CCD. Los mapas obtenidos se construyen a partir de los patrones de Kikuchi. Para el estudio de las muestras, se empleó un tamaño de paso en el MB de 0,2 µm y 0,05 µm en la zona batida. Para la indexación solo se ha seleccionado la matriz de Al, ya que la estructura cristalina del B4C es compleja y dificulta la obtención de resultados [4, 6, 7].
En el MB la tasa de éxito fue del 85%, consecuencia de la exclusión de las partículas cerámicas en el análisis, como se puede observar en la figura 9.a donde aparecen de color verde. Para evitar este efecto, en la zona batida se seleccionó una zona con menor número de partículas de B4C, obteniéndose una tasa de éxito próxima al 95%, como se puede apreciar en la figura 9.b.
Para la determinación del tamaño de grano, se consideró como límite de grano un ángulo de desorientación mayor a 10º y como subgrano un ángulo comprendido entre 5º y 10º.
En la figura 9 se representa dos mapas solapados: el mapa de contraste de banda (líneas grises), que ofrece información de la localización de los límites de grano/subgrano atendiendo al nivel de desorientación entre granos contiguos, y el mapa de límite de grano (marcado con una línea gruesa negra), que permite diferenciar entre granos y subgranos, en base al ángulo de desorientación establecido.
La figura 10 muestra solapados el mapa de límite de grano (líneas gruesas) y el mapa de figuras de polos inversa (IPF). Los mapas de figuras de polo inversas nos dan información de la orientación cristalina o textura de cada uno de los granos analizados, cuya orientación viene dada por distintos colores. Los mapas de IPF que se muestran están tomados en la dirección Z, normal a la superficie de la muestra, que se corresponde con la dirección de laminación y de soldadura. Los granos con el eje <111> normal a la superficie de la muestra aparecen en azul. El color verde indica una orientación preferencial en el eje <101>, y el color rojo en el eje <001>. En el MB se observa una cierta textura ya que en la dirección analizada (dirección Z), no existen prácticamente granos orientados en el eje <101>. Sin embargo, en el mapa de IPF correspondiente a la zona batida no se aprecia este efecto.
El análisis de las imágenes muestra un refinamiento del tamaño de grano en la zona batida en comparación con el del material compuesto o MB. El tamaño medio de grano en el MB es de 1,0 μm con una desviación estándar de 1,82, mientras que en la zona batida es de 0,7 μm con una desviación estándar de 1,42. Además, en el MB se observa la existencia de dos tamaños de grano bastante diferenciados; el 64% de los granos presenta un valor de diámetro medio (Dm) inferior a 1 µm, y un 36% un valor de Dm > 1 µm. Sin embargo, en la zona batida el 82% de los granos presentan un Dm < 1 µm, y sólo un 18% superan este valor (Dm >1µm). Este refinamiento de la estructura del grano se debe a la gran deformación plástica que, junto con el aumento de temperatura producido por el proceso de fricción/agitación, causan una recristalización dinámica de la matriz del material compuesto. Este efecto es típico de la soldadura FSW, y ha sido observado en distintos tipos de aleaciones férreas y no férreas [8,9].
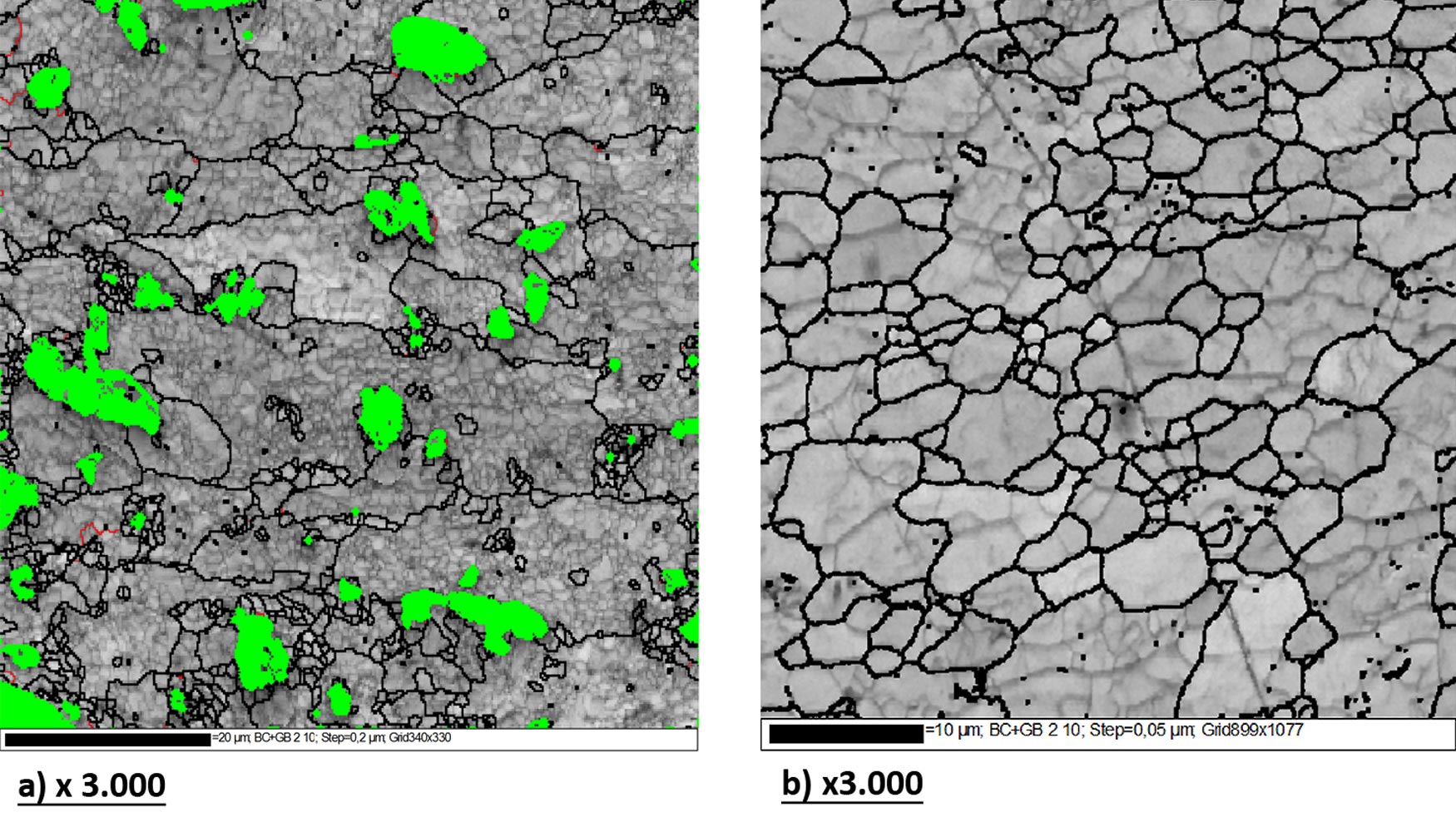
Fig. 9. Mapas solapados (contraste de banda + límite de grano): a) MB y b) Zona batida. Las partículas de B4C se muestran en verde y no son considerados en el estudio.
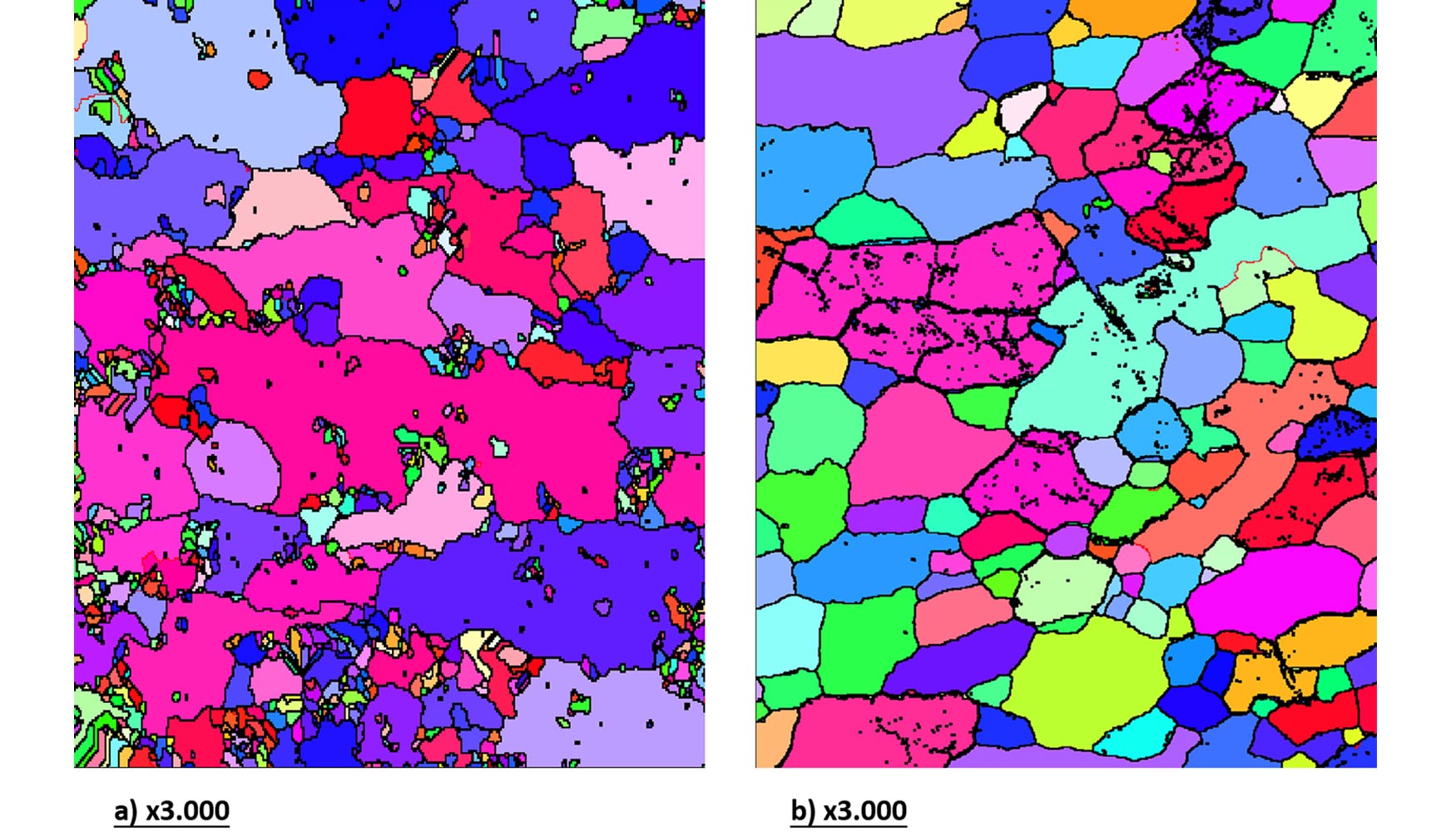
Así mismo también se construyó un perfil que muestra la distribución de la desorientación angular tanto para el MB como para la zona batida (figura 11), dando como resultado una predominancia de los límites de grano de alto ángulo.
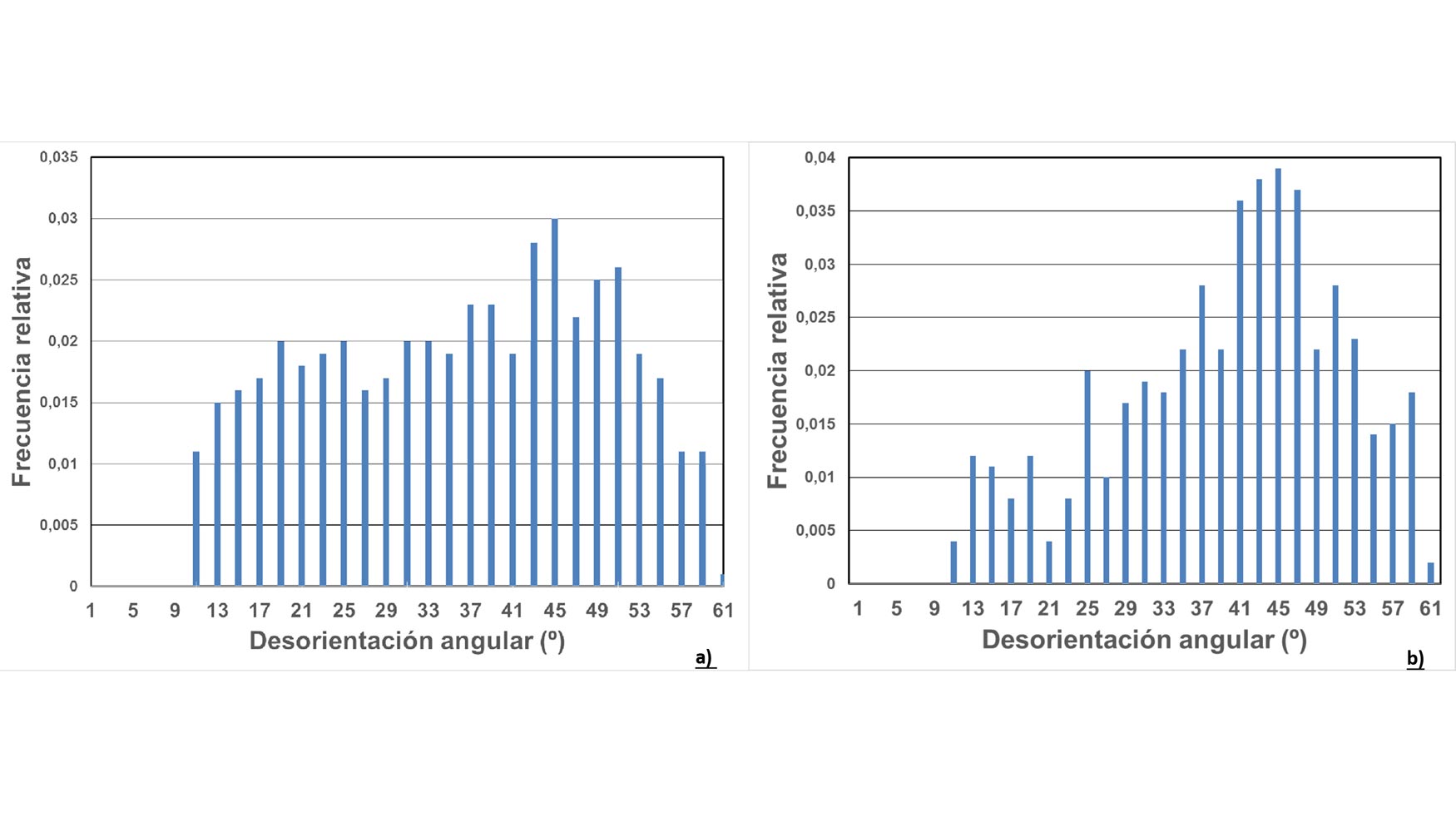
3.4. Caracterización de las propiedades mecánicas
3.4.1. Determinación de los perfiles de dureza
Se ha determinado la dureza tanto en superficie como en la sección transversal del cordón de soldadura. La figura 12 muestra los resultados obtenidos de los perfiles de dureza realizados a lo largo de la sección transversal de la unión soldada, donde la línea azul corresponde a los valores obtenidos en la zona superior, y la línea rosa a la zona inferior. Además se ha realizado un tercer barrido de durezas en la dirección perpendicular a los anteriores, en el centro del cordón. En resumen, las durezas medias obtenidas en el MB son: 44 HV en la zona superficial y 45 HV en la sección transversal. En relación al cordón, como ya se ha apuntado anteriormente, no se llega a distinguir con claridad las diferentes zonas características de esta soldadura (ZAT, ZATM y Zona batida), por lo que se ha calculado un valor medio de toda la zona soldada que es de 55 HV. Por otro lado, se ha obtenido un valor de 49 HV en la zona central del cordón (nugget), y un valor de 46 HV en la superficie del cordón. El aumento de la dureza en la zona soldada, puede atribuirse a la disminución del tamaño de grano, y a la mayor cantidad de partículas de menor tamaño consecuencia de la fractura de los B4C durante el proceso de FSW.
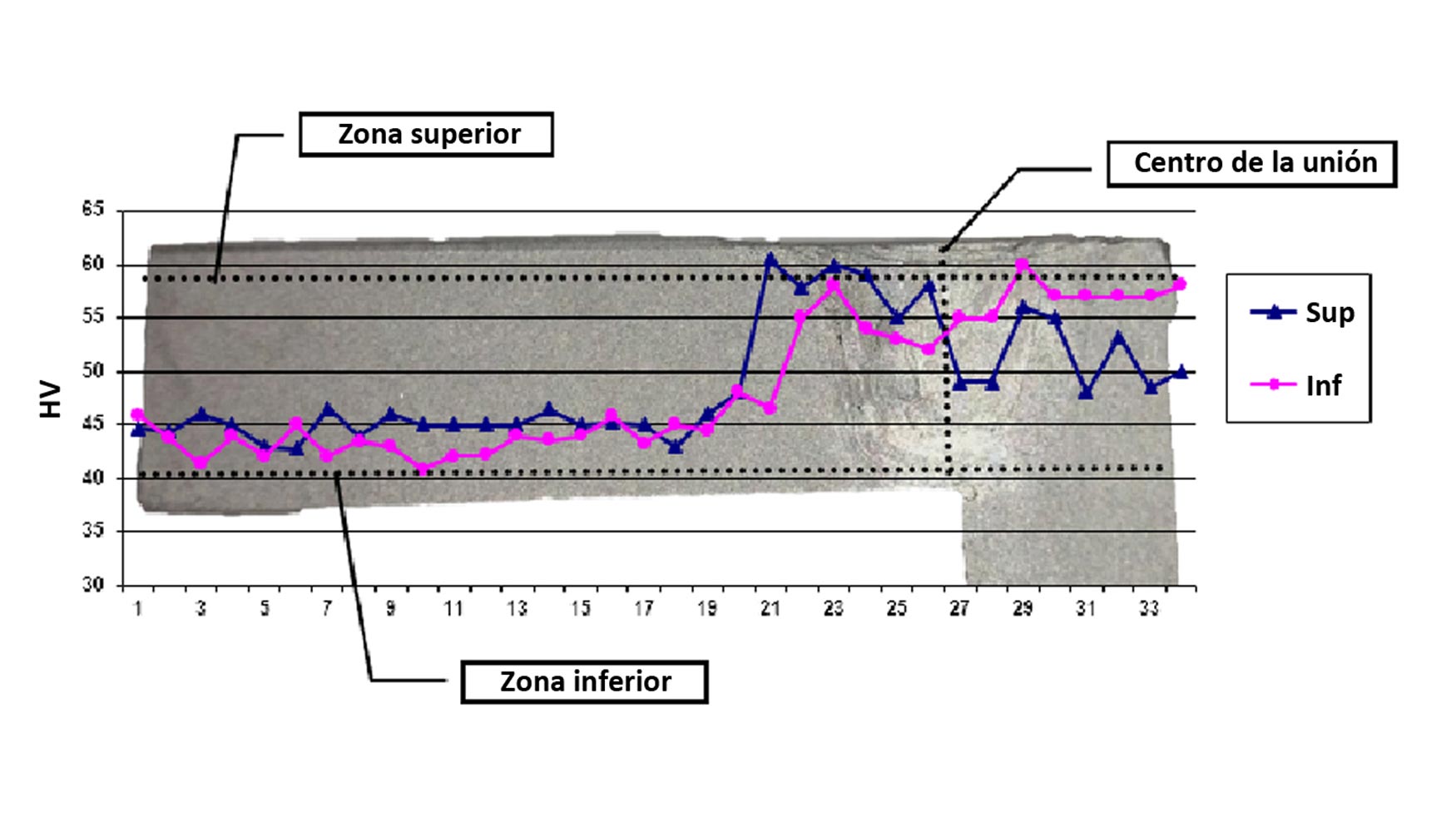
3.4.2. Ensayo de tracción
Para evaluar la resistencia mecánica de la unión FSW sobre el material Al-B4C se realizaron ensayos de tracción. Para ello se soldaron en configuración a tope dos chapas planas de este material y se realizaron ensayos de tracción transversales a la unión soldada. Los resultados se recogen en la tabla 2 y en la figura 13.
Probeta |
Resistencia a la tracción |
Zona de rotura |
|
Nº |
Sección [mm2] |
Rm [MPa] |
|
1 |
25,05 x 8,14 = 203,9 |
117,8 |
Material base |
2 |
25,04 x 8,13 = 203,6 |
117,8 |
Material base |
3 |
25,10 x 8,13 = 204,1 |
117,8 |
Material base |
En los tres casos, la rotura se produce por el metal base (lo que se observa claramente en la fotografía de la fig. 13), lo que evidencia el excelente comportamiento mecánico de la soldadura FSW.
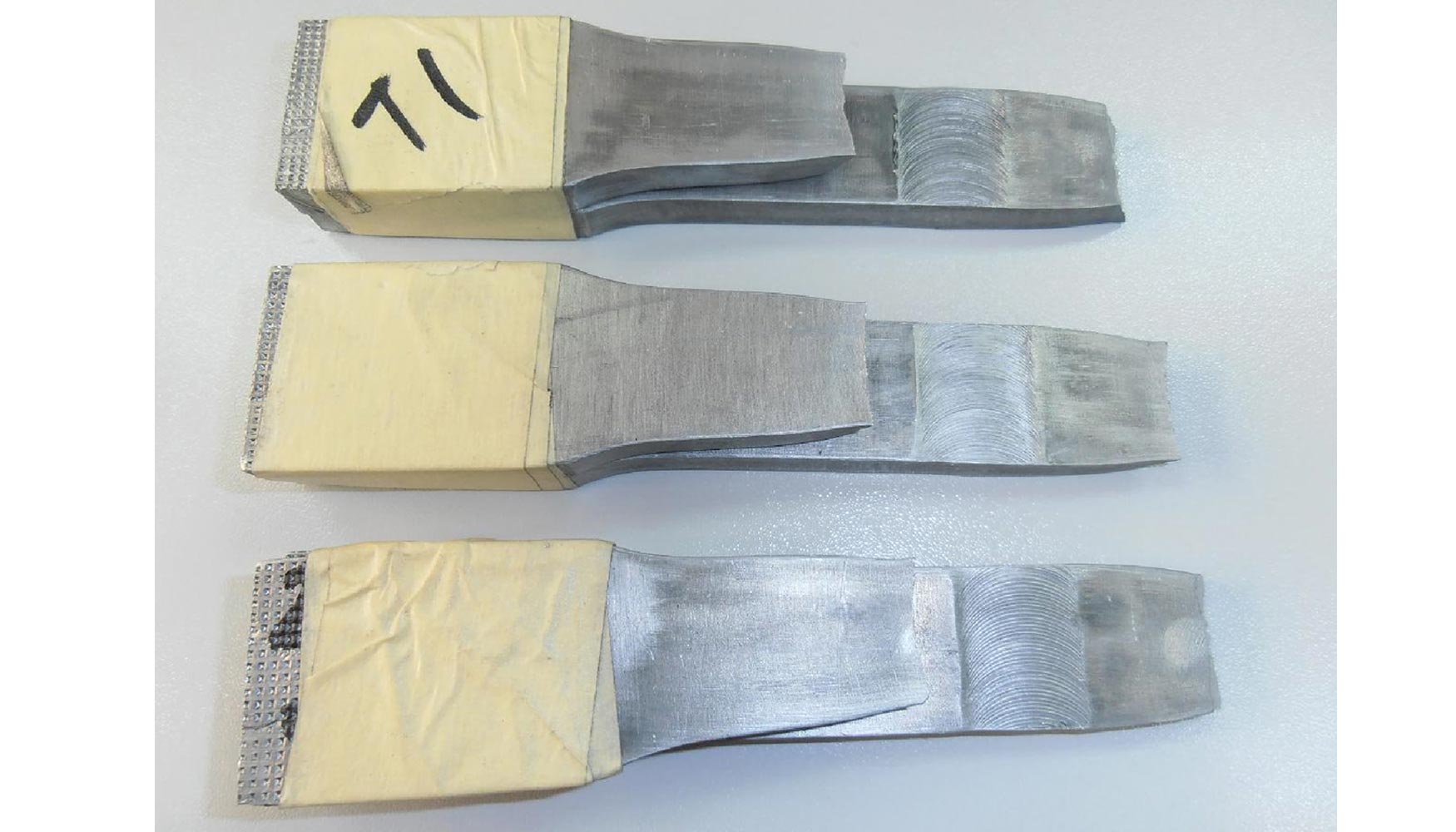
3.5. Determinación de las propiedades tribológicas
3.5.1. Determinación del coeficiente de desgaste
En la figura 14 se muestra una gráfica comparativa del coeficiente de fricción entre el MB y el cordón, donde el eje de ordenadas de la izquierda corresponde al MB y el de la derecha al cordón. Estos resultados muestran un ligero aumento del coeficiente de fricción en el cordón (0,62) con respecto al MB (0,58). En ambos casos la evolución del coeficiente de fricción es la misma. Se observa una primera etapa (200 m en el MB y 250 m en el cordón), donde aparecen fluctuaciones significativas del coeficiente de fricción que se producen conjuntamente al desprendimiento de gran cantidad de partículas de material de color oscuro, siendo la mayor parte de ellas de B4C. Este arranque de las partículas es indicativo de un mecanismo de desgaste fundamentalmente abrasivo. También se observa que el valor de esta fluctuaciones es algo menor en el cordón que en el MB, lo que puede achacarse a una mayor dureza en esta zona. En una segunda etapa, caracterizada por la estabilización del coeficiente de fricción, el desprendimiento de partículas es menor. Por otro lado, la observación de las huellas de desgaste al final del ensayo (figura 15), muestran que la superficie del surco está cubierta en gran medida por partículas de desgaste (debris) que son aplastadas durante el paso del pin, formando una nueva superficie de desgaste. Ambos efectos indican que en esta etapa final el mecanismo de desgaste predominante ha sido el adhesivo [7].
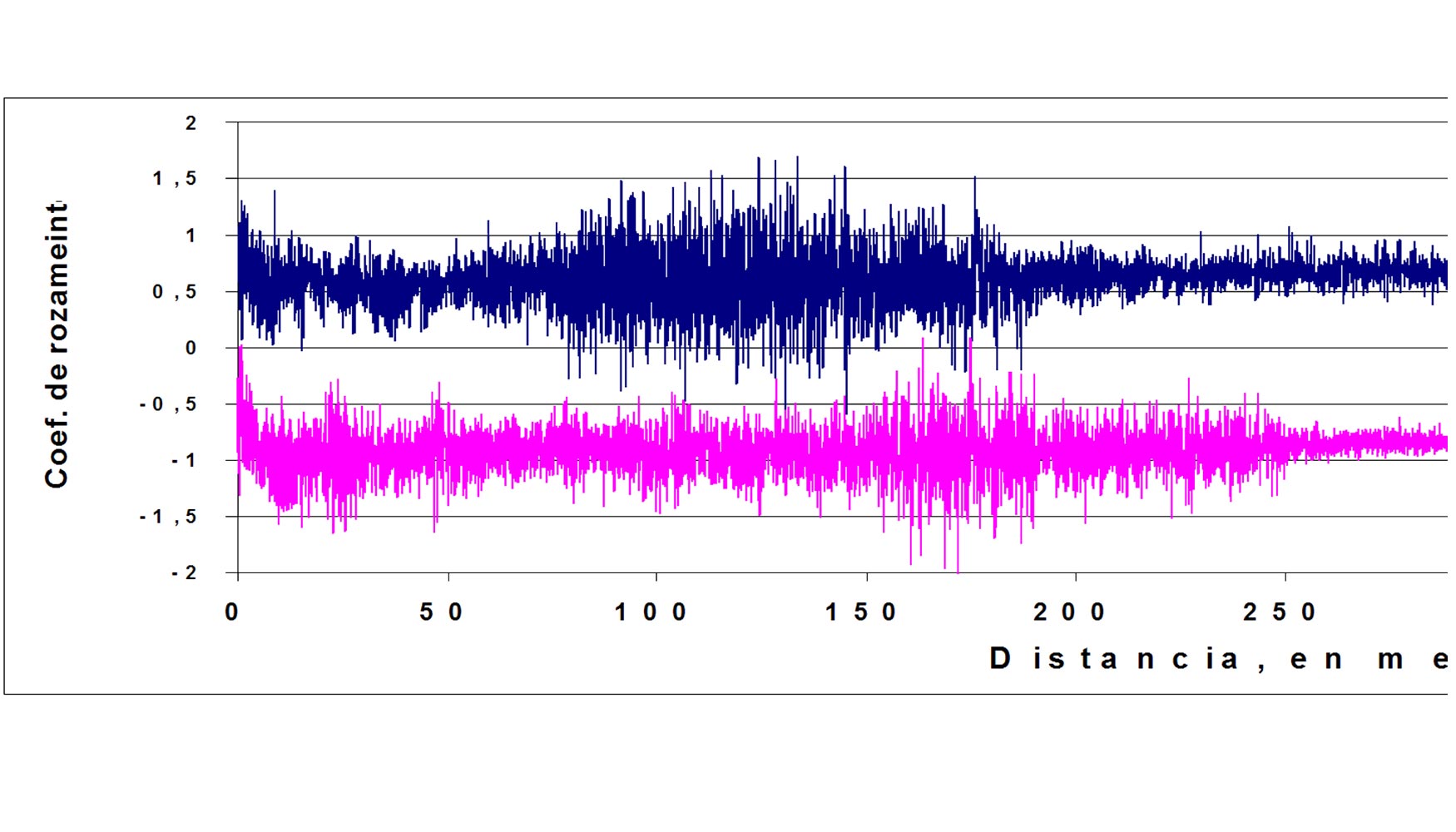
3.5.2. Tasa de desgaste
La tasa de desgaste en la superficie del cordón (1,15x10-3 mm3/N·m) es ligeramente inferior a la obtenida en la superficie del material compuesto (1,27x10-3 mm3/N·m); sin embargo, sí existen diferencias reseñables en la morfología de las huellas de desgaste. En el cordón la huella presenta una profundidad de 154,4 μm y un ancho de 1.578,7 μm, mientras que en el MB la profundidad de 166,5 μm y el ancho de 1.579,4 μm. Por consiguiente, debido a la mayor dureza en el cordón se produce una huella menos profunda y ligeramente menos ancha que en el MB el cual experimenta una mayor deformación plástica.
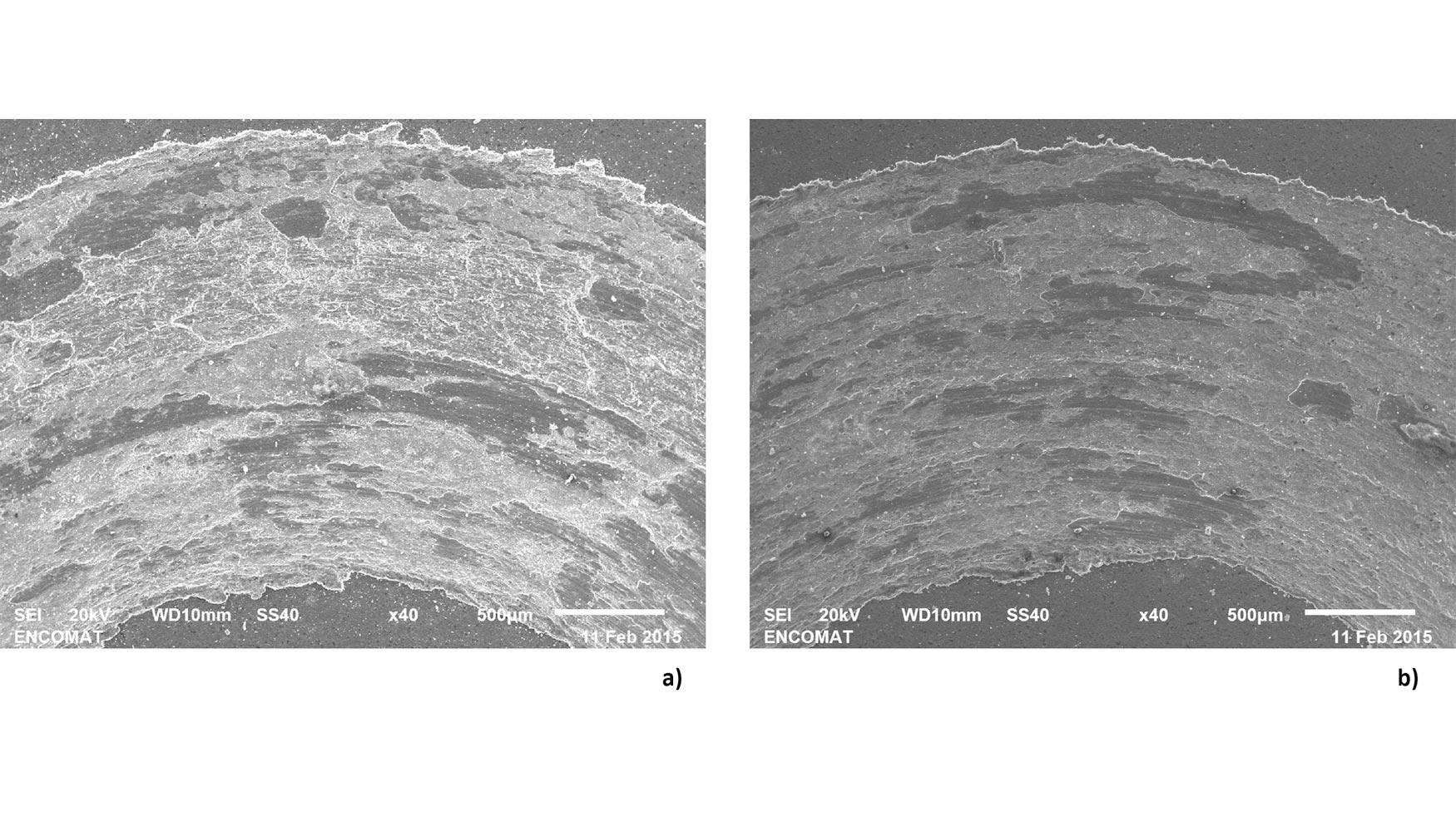
4. Conclusiones
- FSW ha demostrado ser una técnica adecuada para la unión de chapas de aluminio puro (AA1087) reforzadas con partículas cerámicas de B4C, incluso en configuración de junta en esquina.
- El proceso de FSW no afecta de manera significativa a la distribución de las partículas de refuerzo, pero produce un ligero efecto de rotura de las partículas de B4C que reduce su tamaño.
- Los ensayos de tracción muestran que la unión soldada mediante FSW, es más resistente que el propio material base (Al-B4C).
- La disminución del tamaño de grano en la zona batida consecuencia de la recristalización dinámica de la matriz contribuye, junto con la rotura de partículas, al aumento de dureza obtenido en el cordón, que es un 25% superior al MB, y a la mejora de las propiedades tribológicas, como indica la tasa de desgaste obtenida en el cordón cuyo valor es un 9% inferior al material base.
[1]. R.S. Mishra. Z.Y. MA, Friction stir welding and processing. Mater. Sci. Eng., 50 (2005) pp. 1-78.
[2]. J.A. Lee, R.W. Carter and J. Ding. Friction stir welding for aluminium metal matrix composites (MMCs). MSFC Center Director's Discretionary Fund Final Report, Project No. 98-09, Marshall Space Flight Center, (1999) pp. 1-21.
[3]. X. G. Chen, Application of Al–B4C metal matrix composites in the nuclear industry for neutron absorber materials. Proceedings of solidification processing of metal matrix composites, TMS, USA, (2006). p. 343–50.
[4]. D. H. Mesa (2010). Principios y aplicaciones de la técnica de difracción de electrones retroproyectados (EBSD, Electron Back-Scattering Diffraction), nº 74.
[5]. Guo, J. Amira, S. Gougeon, P. Chen, X. G. Effect of the surface preparation techniques on the EBSD analysis of a friction stir welded AA1100-B4C metal matrix composite. Materials Characterization 62 (2011) pp. 865-877.
[6]. J Guo, P. Gougeon, F. Nadeau y X. G. Chen Joining of AA1100–16 vol.-% B4C metal matrix composite using laser welding and friction stir welding. Canadian Metallurgical Quarterly: The Canadian Journal of Metallurgy and Materials Science Vol. 51 (2012) pp.
[7]. X. G. Chen, M. da Silva, P. Gougeon, L. St-Georges. Microstructure and mechanical properties of friction stir welded AA6063–B4C metal matrix composites. Materials Science and Engineering A 518 (2009) pp. 174–184.
[8]. D. Gesto, D. Verdara, P. Rey, P. Minino, G. Pena, Obtaining Sub-Micron Grain Size in AM60 Magnesium Alloy Using Friction Stir Processing. Friction Stir Welding and Processing VI. (Ed. By: Rajiv Mishra, Murray W. Mahoney, Yutaka Sato, Yuri Hovanski and Ravi Verma). TMS, (2011) pp. 299-306.
[9]. T Saeid, A Abdollah-Zadeh, T Shibayanagi, K Ikeuchi, H Assadi, On the formation of grain structure during friction stir welding of duplex stainless steel, Materials Science and Engineering: A, Vol. 527 (2010) pp 6484-6488.