El decapado con la tecnología de granallar para la industria aeronáutica
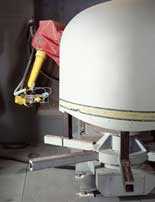
Este proceso ya no se utiliza, en parte por el coste y en parte por motivos medioambientales.
Hoy día, dependiendo del tamaño, una hélice puede decaparse en un sistema especial de granallado en 40 minutos. Este sistema ha sido desarrollado por Vapor Blas una conocida y respetada empresa francesa fabricante de sistemas de granallado que recientemente forma parte del grupo Rösler. Vapor Blas desarrolló el sistema de granallado automático en 1995. Este sistema completamente automatizado, ha sido utilizado por muchos fabricantes de helicópteros, y puede decapar 12 metros cuadrados de superficie de hélice por hora, dando como resultado una superficie igualada, con protección total de la hélice.
La velocidad se alcanza mediante dos sistemas de chorreado, que durante el proceso de granallado tratan simultáneamente todos los lados de la pala, asegurando así un resultado uniforme.
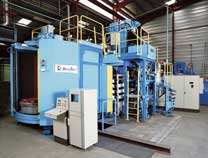
Decapado de geometrías complejas
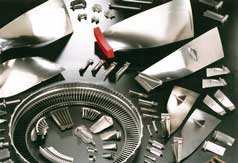
Decapado de geometrías complejas
Los “radomos” están fabricados en material CFC, protegidos con una capa especial contra la corrosión y condiciones medioambientales extremas.
En un mantenimiento rutinario se tiene que decapar el “radomo” para examinar su estado. Este decapado mediante proceso químico, no se lleva a cabo debido a razones medioambientales; el completo tratamiento mediante arenado, puede llevarse a cabo en 3 días lo que significa un gasto de tiempo innecesario. Con la solución automatizada desarrollada por Vapor Blas, el tiempo de tratamiento para un radomo puede reducirse a una hora. Es posible quitar la capa protectora con mucha precisión y cuidado en un área de 5 m2 por hora utilizando el granallado controlado por robot.
Para seguir los contornos con precisión, Vapor Blas ha desarrollado un software especial. Un sensor láser en el “brazo” del robot informa de la estructura de la pieza al sistema. La curva a trabajar, se calcula automáticamente, y la distancia requerida, el ángulo y la velocidad se envían al robot. Todos los parámetros quedan grabados en una hoja de datos.
La granalla que se utiliza es de almidón de trigo. Este sistema se utiliza para cualquier tipo de radomo, ya sea de aviación civil o militar.
Para decapar radomos de grandes dimensiones (como los que utilizan los Boeing 747), cubiertas de maquinaria, así como pequeñas palas de rotor, se ha desarrollado un sistema similar, completamente automatizado. Para estos casos el robot se monta en la parte superior de la cabina en un eje móvil para poder cubrir una zona más amplia de granallado.
Shot peening de piezas de motor
El Sto. ping requiere exactitud y reproducción, ambos son rasgos decisivos para poder cumplir las regulaciones exigidas por los fabricantes aeroespaciales y así alcanzar el más alto nivel de seguridad y efectividad. El endurecedor universal desarrollado por Vapor Blas (sistema de granallado mediante robot) para EADS, Snecma y otras compañías fabricantes y de mantenimiento de la industria aérea, asegura la absoluta precisión y productividad conseguido a través de un control del proceso completamente automatizado. El peso de la granalla utilizada se controla continuamente, y unos sensores controlan su flujo. 20 lecturas de sensor por segundo hacen posible que el flujo de granalla sea igual y esté garantizado a un +- 2%. Esto de todas maneras no era suficiente para Vapor Blast y Snecma. Para ellos había que asegurar los resultados con mayor precisión y constancia.
Esta instalación tiene un sistema de lectura electrónica Almen que monitoriza constantemente la intensidad del chorro de granalla. Esto se consigue únicamente utilizando tiras Almen. El gasto adicional de las tiras puede ahorrarse utilizando un sistema electrónico. El sistema se puede utilizar para procesar una amplia gama de piezas, mejorando y /o restableciendo sus limites de endurecimiento. El sistema puede programarse por completo, funciona automáticamente y cumple con las especificaciones de la industria aeroespacial. Parte del sistema es un robot de 6 ejes para la manipulación del chorro y de la mesa rotativa. Durante el proceso, la granalla se somete a un sistema integrado de clasificación y es elegido de acuerdo con el tamaño y la forma, procesada continuamente y devuelta al ciclo, esto asegurará la integración del proceso de Sto. ping en todas las operaciones del proceso.
Granallado en húmedo de alta presión a 4000 bar
Existen muchas ventajas para usar el granallado en húmedo :
- El tiempo de proceso para quitar las capas se reduce. En algunos casos hasta 20 veces en comparación con los sistemas convencionales.
- En muchos casos las piezas no han de enmascararse.
- El proceso no es agresivo medioambientalmente.
- El único residuo resultante son los restos de pintura que se desprenden y el filtro de papel. El agua del proceso puede reutilizarse tras el filtrado.
- Sin deformaciones, desgaste mínimo, de 0,008 mm en comparación con el 0,018 mm utilizando procesos convencionales.
- Alta precisión en el proceso, sin desgaste de granalla, sin aditivos químicos.
Gracias a las ventajas descritas, este proceso experimenta un incremento de demanda entre los fabricantes de sistemas de mantenimiento para tecnologías de aviación militar o civil.
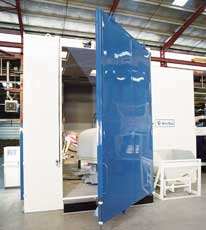
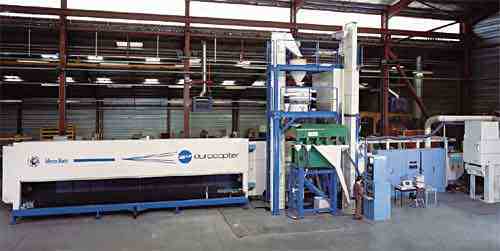