Utilidad de los adhesivos para fabricar piezas complejas de ABS obtenidas por prototipado rápido
16 de febrero de 2012
La solución de estas deficiencias requiere una revisión integral del diseño tridimensional de la pieza en el sistema de CAD 3D para que en el prototipo fabricado se potencien las prestaciones y ventajas de la fabricación por FDM (escaso impacto ambiental, economía, etc.) y se reduzcan sus limitaciones (geométricas, superficiales, etc.). Como elemento clave de este rediseño se propone una novedosa metodología de construcción por unión de partes mediante juntas adhesivas estructurales diseñadas específicamente para adecuarse al material plástico del sustrato (ABS) y a la tecnología de fabricación FDM (construcción mediante capas, cualidades mecánicas dependientes de la dirección constructiva, etc.). En el presente trabajo se seleccionan los adhesivos estructurales más adecuados para unir piezas de ABS fabricadas mediante FDM.
1. Introducción
Los avances tecnológicos que se han producido en los últimos años han facilitado el desarrollo de sistemas avanzados para la fabricación rápida de prototipos. Estas técnicas proporcionan modelos físicos en un periodo relativamente corto (menos de 24 horas) de diseños tridimensionales elaborados en un sistema de CAD. Actualmente estas técnicas se aplican en tres campos industriales (Rapid Prototyping, Rapid Tooling y Rapid Manufacturing) con sistemas muy diversos, tanto en prestaciones como costes, destacando la estereolitografía (SLT), fotopolimerización por luz ultravioleta (SGC), deposición de hilo fundido (FDM), sinterización selectiva láser (SLS), fabricación por corte y laminado (LOM) e impresora 3D (3DP). Debido a las grandes diferencias que existen entre los sistemas de RP descritos, tanto en lo relativo a materiales empleados, precisión, complejidad, costes, etc. como en cuanto al ámbito de su aplicación práctica (modelos, maquetas y/o prototipos) [1], se han realizado numerosas investigaciones para describir las características de cada uno de los métodos y establecer criterios de selección y mejora en función de la precisión, funcionalidad o coste, entre otros aspectos [2-3].
Uno de los sistemas más utilizados es el FDM ya que proporciona piezas con una razonable resistencia (polímero ABS) y un impacto ambiental muy reducido. Las máquinas de FDM son limpias, requieren muy poco mantenimiento y utiliza materiales relativamente baratos, inodoros y no tóxicos [4]. Sin embargo, el sistema FDM presenta deficiencias en el acabado superficial (condicionado a la orientación que tenga la superficie respecto al plano XY), dificultad para la obtención de geometrías complejas y/o pequeñas, escasa consistencia en elementos ‘esbeltos’ de la pieza y necesidad de grandes estructuras de material soporte para sustentar partes ‘voladas’ de las piezas. Estas restricciones ocasionan, además de una importante pérdida de calidad, un notable incremento de tiempos y costes de fabricación y posprocesado lo que restringe tanto la gama de piezas obtenibles (sencillas, sin huecos complejos interiores, etc.) como su ámbito de aplicación técnica (modelos y/o maquetas).
Por ello, en los últimos años se han realizado diversos trabajos de investigación [5-8] que permiten mejorar atributos específicos de las piezas obtenidas por FDM (como el acabado superficial, la precisión dimensional, etc.) variando los parámetros característicos del proceso, tales como el espesor de cada capa, la orientación de la pieza, estructura del material de relleno, etc. Sin embargo, los resultados obtenidos solo han permitido mejoras de índole parcial y no han considerado la conveniencia de un rediseño general de la pieza prototipo para adaptarla al proceso de fabricación.
La solución de estas deficiencias requiere una revisión integral del diseño tridimensional de la pieza en el sistema de CAD 3D para que en el prototipo fabricado se potencien las prestaciones y ventajas de la fabricación por FDM (escaso impacto ambiental, economía, etc.) y se reduzcan sus limitaciones (geométricas, superficiales, etc.). De esta forma, las piezas fabricadas por FDM conjugarán de manera adecuada precisión, prestaciones mecánicas y costes reducidos, constituyendo una alternativa óptima frente a otro tipo de procesos de prototipado rápido.
Como elemento clave de este rediseño se propone una novedosa metodología de construcción por unión de partes mediante juntas adhesivas estructurales diseñadas específicamente para adecuarse al material plástico del sustrato (ABS) y a la tecnología de fabricación FDM (construcción mediante capas, cualidades mecánicas dependientes de la dirección constructiva, etc.). El uso de juntas adhesivas facilitará el rediseño de las partes componentes para lograr la calidad superficial y geométrica deseada sin disminución de sus prestaciones mecánicas y con tiempos y costes de fabricación reducidos.
Las uniones adhesivas se utilizan cada vez con más frecuencia en numerosos sectores industriales sustituyendo o complementando sistemas tradicionales de unión como la soldadura o el remachado. Entre las ventajas de los adhesivos estructurales cabe señalar su elevada resistencia (incluso en condiciones ambientales desfavorables), un menor peso, estanqueidad y eliminación de la corrosión galvánica [9].
El presente trabajo muestra el proceso para el análisis y selección del adhesivo más adecuado para unir piezas de ABS obtenidas mediante FDM.
2. Metodología
La selección de los adhesivos que se han utilizado en los ensayos ha tenido en cuenta, por un lado, que sus características fueran adecuadas para unir sustratos de ABS (acrilo nitrilo butadieno estireno) y, por otro lado, que sean representativos de cada una de las principales familias de adhesivos estructurales. De esta forma, se han elegido los siguientes adhesivos:
- Acrílicos: Adhesivo SikaFast 5211 de Sika
- Poliuretano: Adhesivo bicomponente SikaForce 7710 L100 y SikaForce 7010 de Sika.
- Cianocrilato: Loctite 420 de Henkel
- Epoxi: Adhesivo bicomponente Loctite 9489 de Henkel.
- Silicona: Loctite 5910 de Henkel.
Los sustratos son piezas prismáticas de ABS (acrilonitrilo butadieno estireno) de dimensiones 50x7x7 (en milímetros) obtenidas mediante prototipado rápido por deposición de hilo fundido (FDM). La máquina FDM es un modelo Dimensión 768 BST con software Catalist y área de trabajo 203x203x305 (en milímetros). Los sustratos se han construido mediante adición de capas de ABS de 0,2 milímetros de espesor (paralelas al plano XY) y forma rectangular de 50x7 (en milímetros) hasta alcanzar una altura de 7 milímetros. En estas condiciones, las características técnicas de los sustratos son las siguientes: resistencia a tracción 20.3 MPa (en dirección coaxial al eje de construcción X), módulo de elasticidad 1.4 MPa, rugosidad superficial 2,7 µm. La figura 1 muestra algunas piezas de ABS obtenidas con la máquina FDM.
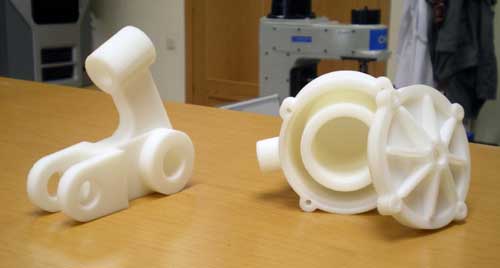
Dada la anisotropía del sustrato (que presenta un mejor comportamiento técnico para resistir esfuerzos en direcciones paralelas al plano de construcción XY) se ha elegido el modelo de junta a tope para efectuar ensayos de tracción con los diferentes adhesivos. La Figura 2 muestra las dimensiones de la junta a tope.
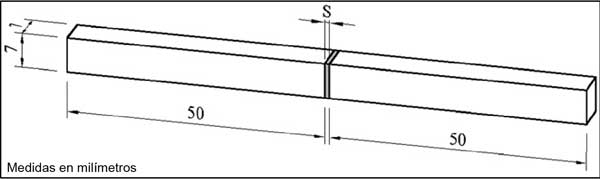
Después del tiempo de curado, se realiza una comprobación dimensional con un calibre digital y se efectúa el ensayo de tracción. Para el ensayo de tracción se ha utilizado una máquina modelo TN-MD (Hoytom, S.L., Bilbao, Spain) motorizada con control automático por ordenador (Figura 3). Su capacidad es de 200 kN, la carrera del pistón es de 125 mm y la velocidad de desplazamiento se ha fijado en 2 mm/s. Se han ensayado a tracción 10 juntas por cada adhesivo representativo de las familias consideradas (acrílicos, cianocrilatos, poliuretanos, epoxis y siliconas) siguiendo un procedimiento semejante al indicado en la norma UNE-EN 15870 sobre determinación de resistencia a la tracción de uniones a tope [10].
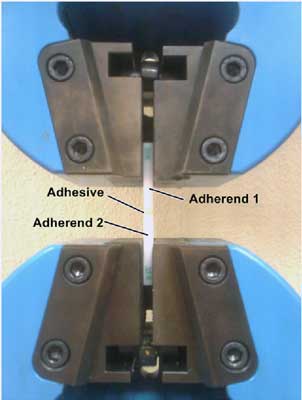
3. Resultados
La tabla 1 muestra los valores obtenidos para la tensión de rotura (τ: carga de fallo/ superficie de la unión) y el modo de fallo para cada adhesivo utilizado. El análisis de la Tabla 1 permite deducir las siguientes conclusiones:
El cianocrilato Loctite 420 presenta el valor medio de la tensión de rotura más elevado (12.67 MPa) con un amplio porcentaje de fallo cohesivo (el más apropiado). Este adhesivo tiene el rango de variación entre el valor máximo y mínimo más alto (5,23 Mpa).
Los adhesivos acrílicos (Sikafast 3201) y poliuretanos (SikaForce 7710 L100 + 7010) tienen valores medios de la tensión de rotura semejantes (8,92 y 8,12 MPa, respectivamente) pero inferiores al cianocrilato. El acrílico presenta un rango de variación entre valor máximo y mínimo más reducido que el poliuretano (1,59 MPa frente a 2,87 MPa) y, sobre todo, que el cianocrilato (1,59 MPa frente 5,23 MPa). Sin embargo, el poliuretano tiene un porcentaje de fallo cohesivo muy superior al acrílico (60% frente 20%)
Los adhesivos epoxi (Loctite 9489) y silicona (Loctite 5910) presentan valores bajos de la tensión media de rotura (5,45 y 1,37 MPa, respectivamente) y rangos de variación entre valor máximo y mínimo relativamente reducidos (2,27 y 0,79 MPa, respectivamente). Estos resultados junto a los amplios porcentajes de fallo adhesivo obtenidos con epoxi y silicona (80%) aconsejan descartar su utilización en unión de piezas de ABS.
Por otra parte, el control dimensional efectuado después del tiempo de curado de la uniones adhesivas ha puesto de manifiesto una adecuada precisión dimensional en todas las juntas elaboradas excepto en las que se empleó cianocrilato. En este caso, el adhesivo atacó químicamente el sustrato ocasionando una ligera disolución irregular de la capa más externa del mismo (disminución comprendida entre -0,1 y -0,2 milímetros) que alteró la geometría de la junta. Por todo ello, se considera que el adhesivo de poliuretano es el adhesivo estructural más adecuado para unir piezas de ABS obtenidas por DFM ya que proporciona altos valores de resistencia (8,12 MPa) y una buena adherencia a los sustratos (60% de fallo cohesivo).
|
Tensión de rotura (MPa) |
Modo de Fallo (%) |
||||||
Adhesivo Utilizado |
Espesor Adhesivo (mm) |
Medio |
Max. |
Min. |
Desv. típica |
Cohesivo |
Adhesivo |
Mixto |
Acrílico SikaFast 5211 |
1 |
8,92 |
9,63 |
8,04 |
0,56 |
20 |
10 |
70 |
Poliuretano SikaForce 7710 L100 + 7010 |
0,5 |
8,12 |
9,65 |
6,78 |
0,83 |
60 |
10 |
30 |
Cianocrilato Loctite 420 |
0,1 |
12,67 |
15,41 |
10,18 |
1,85 |
60 |
0 |
40 |
Epoxy Loctite 9489 |
0,2 |
5,45 |
6,43 |
4,16 |
0,79 |
0 |
60 |
40 |
Silicona Loctite 5910 |
1 |
1,37 |
1,69 |
0,90 |
0,23 |
0 |
80 |
20 |
4. Conclusiones
Los avances tecnológicos que se han producido en los últimos años han facilitado el desarrollo de sistemas avanzados para la fabricación rápida de prototipos. Uno de los sistemas más utilizados es el FDM ya que proporciona piezas con una razonable resistencia (plástico ABS) y un impacto ambiental muy reducido.
Sin embargo, el sistema FDM presenta deficiencias en el acabado superficial, dificultad para la obtención de geometrías complejas y/o pequeñas, escasa consistencia en elementos ‘esbeltos’ de la pieza y necesidad de grandes estructuras de material soporte para sustentar partes ‘voladas’ de las piezas. Para resolver estos problemas se propone la construcción por unión de partes mediante juntas adhesivas estructurales diseñadas específicamente para adecuarse al material plástico del sustrato (ABS) y a la tecnología de fabricación FDM (construcción mediante capas, cualidades mecánicas dependientes de la dirección constructiva, etc.).
Los ensayos realizados con adhesivos representativos de cada una de las cinco familias de adhesivos estructurales han puesto de manifiesto que el poliuretano es el adhesivo más adecuado para unir piezas de ABS obtenidas por DFM ya que proporciona altos valores de resistencia (8,12 MPa) y una buena adherencia a los sustratos de ABS (60 % de fallo cohesivo).
Agradecimientos
Nuestro reconocimiento a Antonio Conesa de Henkel-Loctite y Alberto Sastre de Sika por la aportación de adhesivos y dosificadores necesarios para realizar los ensayos.
Bibliografía
- Capuz, S.: Introducción al proyecto de producción. Ingeniería concurrente. Universidad Politécnica de Valencia. Valencia, 1999; pp.103 – 136.
- D T Pham and S S Dimov.: Rapid prototyping and rapid tooling—the key enablers for rapid manufacturing. Proc. Instn Mech. Engrs Vol. 217 Part C: J. Mechanical Engineering Science. 2003; pp. 1-23.
- Matthew Frank, Sanjay B. Joshi and Richard A. Wysk.: Rapid prototyping as an integrated Product/process development tool: an overview of issues and economics. Journal of the Chinese Institute of Industrial Engineers, Vol. 20-3. 2003; pp. 240-246.
- L. Vargas and Cordoba, E.: Calidad superficial en el prototipado rápido, proceso FDM. Revista de Ingeniería e Investigación. Vol. 24 – 3. 2004; pp. 28-32.
- B.H. Lee, J. Abdullah, Z.A. Khan.: Optimization of rapid prototyping parameters for production of flexible ABS object. Journal of Materials Processing Technology Vol. 169, 2005; pp. 54–61.
- C W Ziemian; P M Crawn III.: Computer aided decision support for fused deposition modelling. Rapid Prototyping Journal; Vol. 7-3; 2001; pp. 138-147.
- P.M. Pandey, N.V. Reddy, S.G. Dhande: Real time adaptive slicing for fused deposition modeling, Int. J. Machine Tools Manuf; Vol. 43; 2003; pp. 61–71.
- R. Anitha, S. Arunachalam, P. Radhakrishnan: Critical parameter influencing the quality of prototype in fused deposition modelling. J. Mater. Proc. Technol. Vol. 118; 2001; pp. 385–388.
- Adams RD, Comyn J, Wake WC. Structural adhesive joints in engineering. London: Chapman & Hall; 1997.
- AENOR. UNE-EN 15870: Adhesivos: determinación de resistencia a la tracción de uniones a tope. Asociación española de normalización; 2009.