Brochado, lecciones aprendidas
En el mismo sentido, The Insight Partners [2], reportó que el mercado de herramientas de brochado experimentará oportunidades de crecimiento impulsadas por la industrialización en ascenso durante el período de 2021 a 2028. Según un estudio reciente, el mercado, valuado en 148,89 millones de dólares en 2020, se proyecta alcanzar los 216,90 millones de dólares en 2028, con una tasa compuesta anual del 5,3%. Se espera que el segmento automotriz sea el de mayor crecimiento durante este período. Geográficamente, el mercado está segmentado en América del Norte, Europa, Asia Pacífico, Medio Oriente y África, y América del Sur, siendo Norteamérica el líder de participación del negocio (figura 1). Sin embargo, Asia Pacífico ha comenzado a liderar el crecimiento del mercado.
![Figura 1. Mercado global de máquinas brochadoras y herramientas de brochado [2] Figura 1. Mercado global de máquinas brochadoras y herramientas de brochado [2]](https://img.interempresas.net/fotos/4641764.jpeg)
La importancia del proceso de brochado en la fabricación, mantenimiento y desarrollo de sistemas energéticos y de transporte resalta la relevancia de ciertos apartados clave (Lecciones aprendidas), que sirven como punto de partida y guían el camino hacia mejoras en este proceso. Este texto incluye un resumen de los factores más destacables del proceso y explora los cambios más relevantes que experimentará este ámbito de la industria.
1. El brochado es un proceso significativo y competitivo relevante y difícil competidor
El proceso de brochado permite realizar el proceso completo de fabricación desde el desbaste hasta acabado superficial. El proceso funciona gracias a una herramienta especial que lo caracteriza, la brocha. Una brocha es una herramienta de varios filos de corte que arrancan material de forma progresiva (figura 2). El número de dientes involucrados en el trabajo es grande, por lo que el ancho total de corte aumenta y los procesos de desbaste, semiacabado y acabado se pueden completar con un solo golpe de la brocha Esto conlleva una notable reducción, tanto en el tiempo del proceso principal, como en el tiempo auxiliar, dando como resultado, una operación de corte que supera a otras en términos de en velocidad. En aplicaciones de producción en masa, este enfoque conlleva una disminución significativa en el costo de procesamiento por unidad de producto.
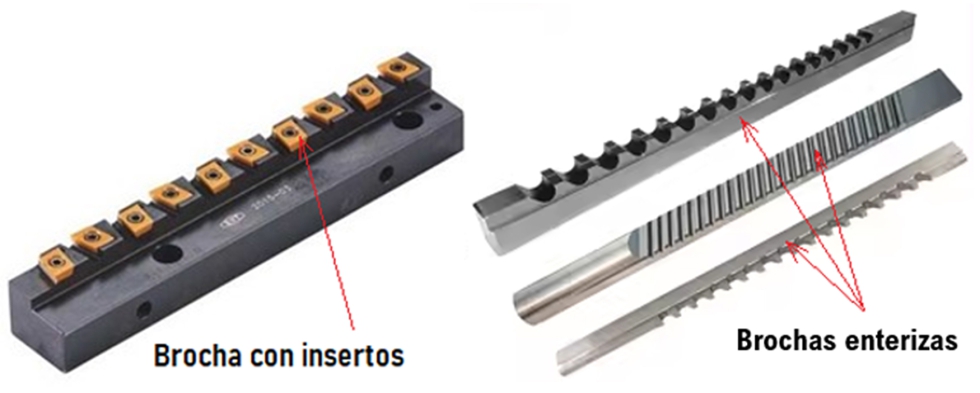
El brochado destaca como un proceso único homologado para la fabricación de componentes aeronáuticos, otorgándole una ventaja significativa sobre sus competidores, quienes enfrentan el desafío de demostrar igual o mejores condiciones y resultados en el proceso de corte. En industrias como la fabricación de componentes de motores para la aviación, la obtención de certificaciones internacionales reconocidas por entidades regulatorias regionales o internacionales es crucial, siendo en Europa donde las certificaciones ISO (EN9100:2018/AS9100D) y las certificaciones específicas para la fabricación aeronáutica (EASA) son fundamentales. [3], [4]. Sin embargo, el proceso de obtención y mantenimiento de estas certificaciones representa un obstáculo importante para los competidores del brochado, ya que implica costos considerables y procedimientos prolongados. Mientras tanto, normativas como EN9100:2018 y la labor de entidades como la Agencia de Seguridad Aérea de la Unión Europea (EASA) juegan un papel crucial en la garantía de la seguridad aérea y la protección del medio ambiente en Europa y a nivel global, al establecer estándares y supervisar la conformidad de las organizaciones en el sector aeronáutico.
Los principales competidores del proceso de brochado, ordenados por orden según su importancia: fresado, rectificado, electroerosión por hilo WEDM y Mecanizado electroquímico por hilo WECM (Figura 3). En el campo energético, los discos de las turbinas de gas son componentes críticos que giran a velocidades de hasta 60.000 revoluciones por minuto y deben resistir condiciones extremas de temperatura y presión. Para cumplir con estos requisitos, se utilizan materiales de alta calidad, como superaleaciones a base de níquel, y se emplean técnicas de mecanizado precisas, principalmente como el brochado, rectificado y fresado [6]. La electroerosión ha ganado relevancia en la fabricación de componentes aeronáuticos gracias al desarrollo de nuevos generadores. Estos generadores ofrecen mayor potencia, lo que aumenta la productividad, y permiten una mejor adaptación de la tecnología para reducir la zona afectada térmicamente y la capa blanca, aspectos cruciales en la industria aeronáutica (ONAC empresa fabricante de maquinaria EDM [7]).
![Figura 3. Distintos procesos de fabricación de ranuras con forma de firtrees [8] Figura 3. Distintos procesos de fabricación de ranuras con forma de firtrees [8]](https://img.interempresas.net/fotos/4641766.jpeg)
La tabla 1 presenta una comparación sobre el rendimiento de los principales competidores del proceso de brochado. La información está basada en la fabricación de una ranura firtree común [8]. Los valores pueden cambiar de acuerdo con las condiciones y características del material, sin embargo, ilustra cuantitativamente las mayores ventajas y desventajas de estos. Se evidencia notablemente que el proceso de brochado tiene una tasa de remoción volumétrica de material 4 veces superior a su inmediato competidor. Para el caso, del proceso de electroerosión y WECM la diferencia se agranda, siendo hasta 50 a 160 veces respectivamente más lento frente al proceso de brochado.
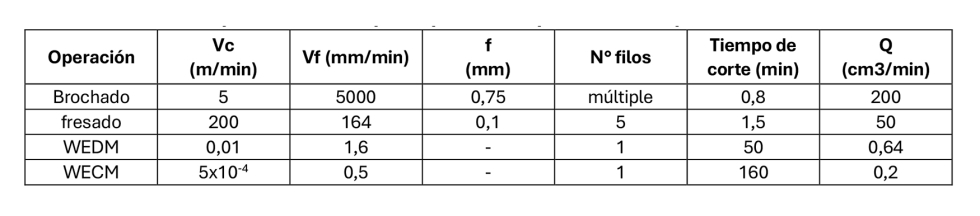
2. Ventajas y límites del proceso
El proceso brochado ofrece ventajas notables, respecto a sus competidores, como alta eficiencia y precisión. Sin embargo, también tiene limitaciones, particularmente en términos de coste y rango de flexibilidad en su aplicación. Este proceso es más adecuado para la producción a gran escala (grandes lotes), pero puede no ser rentable para la producción de una sola pieza o de lotes pequeños. La consideración de las necesidades de procesamiento es crucial al decidir si las brochadoras son adecuadas para los requisitos de producción. A continuación, se amplía un poco más cada una de las ventajas y limitaciones identificadas:
2.1. Ventajas del proceso de brochado
- Se obtiene una alta eficiencia de producción y bajo ciclo de procesamiento, reduciendo el costo por producto en la producción en masa, permitiendo amortizar inversión inicial en máquina y herramienta
- Ofrece una amplia gama de aplicaciones de mecanizado, capaz de realizar operaciones de corte tanto internas como externas. Todos los materiales de ingeniería pueden brocharse con relativa facilidad, que está relacionada con las propiedades intrínsecas de cada material. Un rango adecuado para el brochado está en materiales que poseen de 12 a 22 HRC. Por debajo de 12 HRC el material tiende a desgarrarse causando un pobre acabado superficial. Para el mecanizado de perfiles complejos como los ‘firtree’, se emplean brochas progresivas que están formadas por un conjunto de dientes de formas progresivas que construyen el perfil final de la ranura (Figura 4). Este es un ejemplo excepcional de la ventaja que ofrece el brochado.
- Logra un mayor acabado superficial, precisión dimensional y tolerancias más pequeñas en comparación con otras operaciones de corte de metales. el brochado puede lograr una alta precisión y una baja rugosidad superficial. Generalmente, el nivel de tolerancia de precisión dimensional del brochado es IT7~IT8, y la rugosidad de la superficie Ra es 0,4~0,8μ.
- La máquina posee una estructura y operación sencillas, lo que demanda niveles bajos de habilidad por parte de los operadores. Dado que su funcionamiento es mayormente ortogonal, la programación y manejo resultan más accesibles en comparación con procesos más complejos como el fresado en 6 ejes, por ejemplo.
- Las brochas tienen una vida útil prolongada debido a su desgaste lento (El corte es intermitente) y la posibilidad de ser afiladas varias veces. Por lo general, las brochas enterizas pueden ser afiladas hasta tres veces, o hasta que su geometría básica se vea comprometida. Esta práctica es común debido al alto costo de reemplazo de una herramienta de brochado, que puede ascender a varias decenas de miles de euros. Este aspecto se trató más ampliamente en el artículo “Reacondicionamiento de las herramientas de brochado” del Interempresas Metalmecánica número 490905 (25/septiembre/2023).
- Brinda estabilidad térmica. La temperatura de la pieza de trabajo relativamente constante, lo que evita errores causados por estrés térmico.
- La fuerza de corte actúa en la dirección de sujeción, ayudando a la estabilidad de la pieza de trabajo.
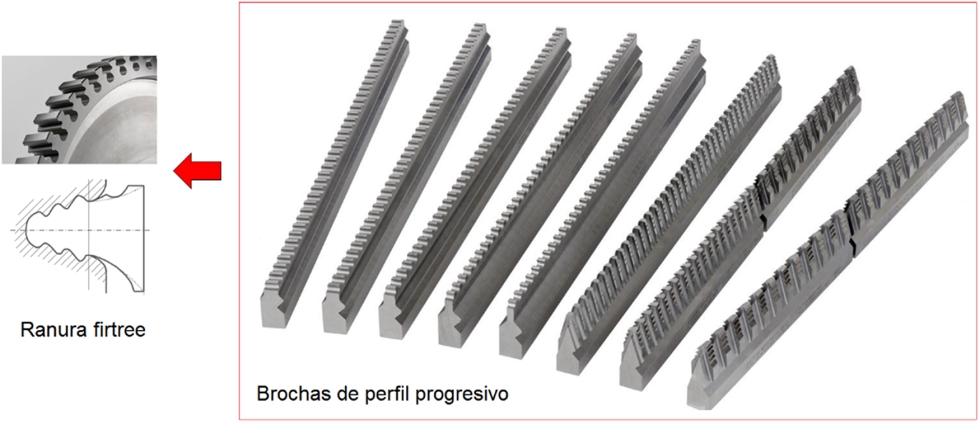
2.2. Limitaciones del proceso
- El diseño y fabricación de las herramientas es una inversión importante, llegando a valer decenas de miles el juego completo. Su elevado costo las hace poco rentables para piezas únicas, siendo más rentables en la producción en masa.
- La reparación y afilado de las brochas son costosas. Esto se debe a las grandes dimensiones de la herramienta que puede llegar a medir hasta 6 metros. En cambio, el reacondicionamiento de las brochas toma tiempos largos debido al trabajo especializado y al traslado de estas. Una práctica útil que brindan las empresas de reafilado de herramientas son la implementación de una estación de trabajo dentro de las plantas manufactureras.
- Rango de aplicación limitado, incapaz de manejar orificios ciegos, orificios profundos, orificios escalonados o superficies exteriores obstruidas.
- Cada perfil requiere una brocha específica, lo que implica la necesidad de una nueva brocha cada vez que cambia la geometría de la pieza de trabajo. (figura 5 y 6).
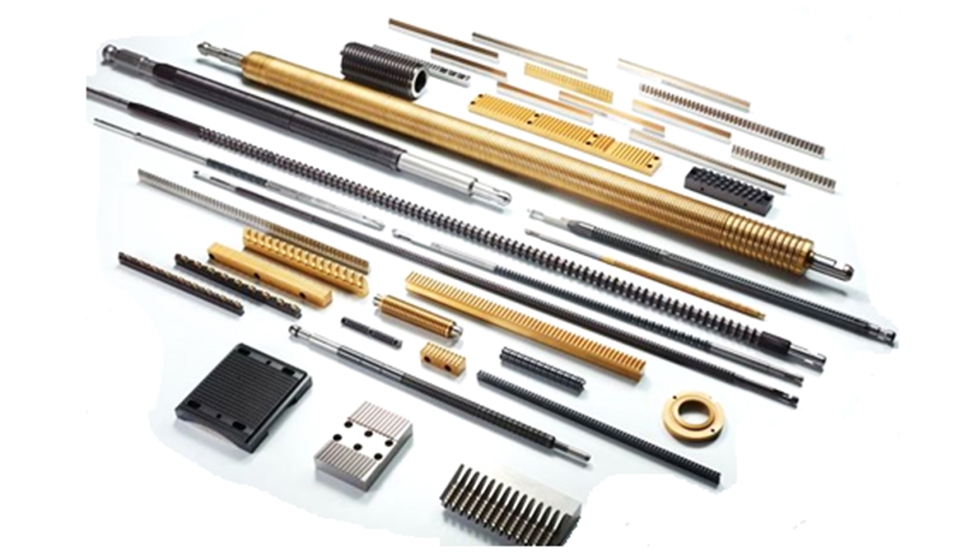
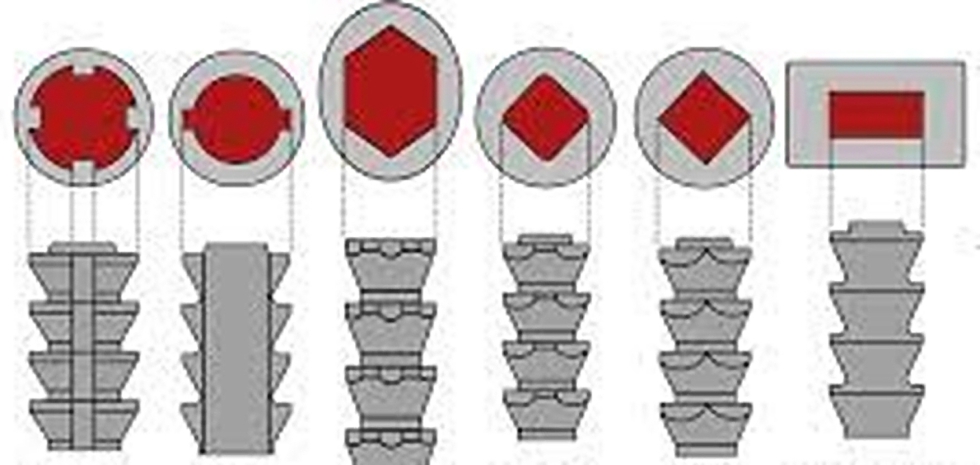
Todos los tipos de brochas ya sean de tracción o de empuje, siguen un movimiento de trabajo lineal similar, aunque enfrentan distintas condiciones de servicio según su geometría, dimensiones, material y si se utilizan para el brochado interno o externo. Durante la operación, las brochas de tracción soportan una fuerza de tensión que evita el pandeo, mientras que las de empuje, más cortas y fabricadas en segmentos, se emplean especialmente en el brochado externo para cortes ligeros y una profundidad de arranque de material reducida.
3. Sus parámetros de corte y su afectación en la calidad de los componentes
El proceso de brochado es uno de los procesos de mecanizado más reconocidos que puede producir alta productividad y calidad cuando se aplica correctamente. Una de sus desventajas del brochado es que todos los parámetros del proceso, excepto la velocidad de corte, están incorporados su herramienta de corte (Brocha). Por lo tanto, no es posible modificar las condiciones de corte durante el proceso una vez que se fabrica la herramienta. El diseño óptimo de las herramientas de brochado tiene un impacto significativo para aumentar la productividad y obtener productos de alta calidad.
La optimización del diseño de herramientas de brochado es un problema bastante complejo, debido a todas las variables interrelacionadas con el diseño. en consecuencia, investigadores y desarrolladores de herramientas de brochado han aplicado métodos de optimización de perfiles como algoritmos de optimización. Además, hay muchas soluciones factibles, y es difícil juzgar si la solución es realmente la óptima. El método ensayo error con herramientas reales tendría un altísimo costo. Un método paralelo y complementario es la optimización por medio de análisis numérico [9]. Esto permite un ahorro sustancial en el desarrollo de un nuevo perfil de corte (figura 7).
![Figura 7. Proceso sistemático de diseño para herramientas de brochado [10] Figura 7. Proceso sistemático de diseño para herramientas de brochado [10]](https://img.interempresas.net/fotos/4641779.jpeg)
La herramienta de brochado debe ser lo más corta posible para un diseño óptimo que minimice el tiempo de producción. Los valores de fuerza y tensión deben mantenerse por debajo de los límites y deben satisfacerse todas las restricciones dinámicas, prácticas y geométricas.
4. Importancia del radio de filo en el proceso
El filo de corte de una herramienta en el mecanizado es clave, ya que determina el área principal de contacto entre la herramienta y la pieza. La forma del filo puede influir significativamente en el proceso de corte, las cargas y tensiones residuales que se generan, así como en la calidad de la superficie resultante [11]. Se han realizado diversos estudios para entender cómo afecta la variable del radio de filo en las tensiones y cargas. Por ejemplo, experimentos aceros y aleaciones titanio y níquel han mostrado que aumentar el radio del filo puede incrementar las tensiones residuales de compresión y la deformación plástica [12]. Además, se ha demostrado que los filos de corte redondeados pueden inducir tensiones residuales más altas que los filos afilados, pudiendo varias según proceso y el material.
Durante el brochado, las fuerzas resultantes se definen como la suma de fuerza de corte y la fuerza de avance. Aunque se asume un filo de corte afilado en teoría, en la práctica suele ser redondeado, lo que causa deformación en el material alrededor del filo, conocido como efecto de arado [13]. Este efecto a menudo se ha subestimado años atrás. El radio del filo de corte afecta estas fuerzas, especialmente en el mecanizado de materiales difíciles como de aleaciones de titanio y níquel. Estudios han mostrado que un mayor radio de corte aumenta las fuerzas de corte y avance [14]. El desgaste de la herramienta cambia el radio del filo durante el proceso de brochado. Sin embargo, predecir este radio durante el trabajo insitu sigue siendo un desafío.
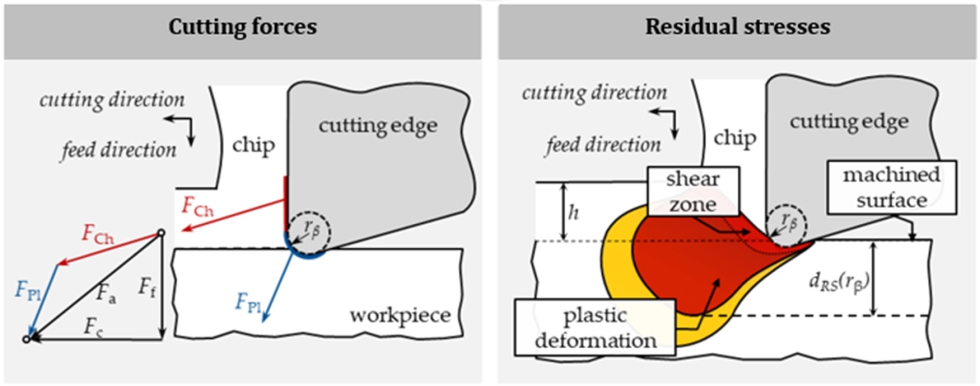
5. Los recientes avances y lo que se está investigando
5.1. Diseño de herramientas
La Industria 4.0 y el Internet industrial de las cosas (IIoT) están impulsando la fabricación inteligente de herramientas de corte, gracias a la combinación de las operaciones físicas con tecnología digital inteligente. Factores como la interconectividad, la automatización, el aprendizaje automático, la utilización de datos en tiempo real y la inteligencia artificial (IA), hace que la nueva Industria 4.0 están logre reducir tiempos y costos en el desarrollo de herramientas. Los investigadores y desarrolladores son capaces de exportar datos de herramientas de los productos directamente a las plataformas digitales CAD/CAM, ERP y otros entornos de taller de los clientes, acelerando el modelado y las simulaciones de la herramienta. En el desarrollo de herramientas de brochado no es la excepción. Recientemente se desarrolló un método inteligente de diseño de herramientas de brochado basado en CBR y máquina de vectores de soporte SVM. El esquema del método se muestra en la figura 9. Se reporta que este método aumentó aproximadamente un 98% la eficiencia del diseño en comparación con los tradicionales [16].
![Figura 9. Sistema de diseño inteligente para herramientas complejas [16] Figura 9. Sistema de diseño inteligente para herramientas complejas [16]](https://img.interempresas.net/fotos/4641781.jpeg)
5.2. Monitorización de la herramienta de corte
La vida de la herramienta es un factor trascendental en un sistema de fabricación, debido a que afecta coste del proceso y a la calidad del producto final. Por este motivo la monitorización de la condición de la herramienta es una línea de investigación importante en los actuales tiempos. En los últimos años se han trabajado métodos novedosos como el uso de la inteligencia artificial y recientemente también la integración flexible de las tecnologías 5G y IIoT en la Industria 4.0 (figura 10).
La monitorización del desgaste de herramientas es desafiante debido a la naturaleza no lineal y variable en el tiempo de muchos procesos de mecanizado. Establecer un modelo teórico preciso para un seguimiento exacto o medir directamente el desgaste durante el corte puede ser igual de difícil. El control del desgaste de herramientas se puede dividir en control directo e indirecto. El control directo implica el uso de cámaras CCD para capturar cambios geométricos causados por el desgaste. La visión artificial enfrenta varios desafíos debido al contacto continuo entre la herramienta y la pieza de trabajo, así como a la presencia de fluidos de corte y/o obstrucciones de viruta. Además, algunos métodos requieren separar la herramienta del soporte, lo que puede provocar desalineación. La mayoría de las técnicas de medición directa son limitadas a laboratorios y pocas son aplicables en la industria, razón por el cual los métodos de monitorización indirecta tienen una mayor aceptación y uso en la industria 4.0.
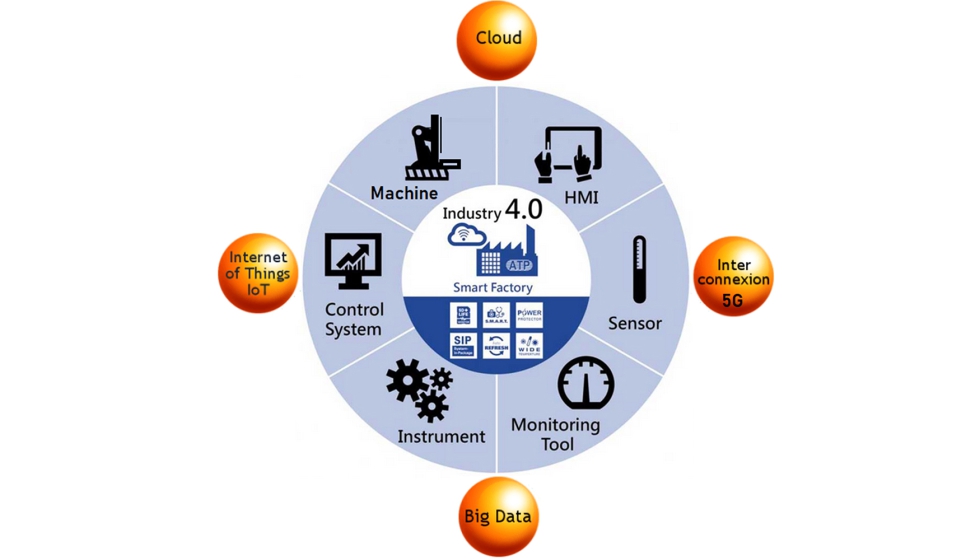
El Centro de Fabricación Avanzada Aeronáutica (CFAA) aloja uno de los nodos de la plataforma Smart Networks for Industry (SN4I) que hace posible el desarrollo de proyectos de integración en la industria 4.0 en procesos como el brochado. Donde se estudia cómo afrontar los desafíos en la monitorización eficiente del control de desgaste de brochas [17].
5.3. La inteligencia artificial en el brochado
La inteligencia artificial, en el contexto del mecanizado, se refiere a la capacidad de las máquinas para aprender de datos, reconocer patrones y tomar decisiones autónomas para optimizar los procesos de fabricación. Esta tecnología se está integrando a los diferentes procesos de arranque de viruta, sobre todo en procesos de alta demanda, calidad y precisión. Un ejemplo relevante son los avances significativos que se están obteniendo son la implementación de algoritmos de Machine Learning (ML) en los procesos de mecanizado. Algunos de los aspectos importantes a tener en cuenta son:
- El Machine Learning se ha utilizado para optimizar los parámetros de corte en el mecanizado.
- Los algoritmos de Machine Learning se aplican para detectar anomalías en el proceso de mecanizado, como desgaste de herramientas o defectos en las piezas fabricadas.
- Mediante el análisis de datos de sensores en las máquinas de mecanizado, el Machine Learning puede predecir cuándo es probable que ocurran fallos.
- Los algoritmos de Machine Learning pueden analizar datos de rendimiento de herramientas de corte y sugerir mejoras en el diseño o el material para optimizar su durabilidad y rendimiento.
- Utilizando técnicas de machine learning, se pueden prever las demandas futuras y optimizar la planificación de la producción en los procesos de mecanizado.
- El Machine Learning se utiliza para desarrollar sistemas de visión por ordenador y análisis de imágenes que pueden inspeccionar automáticamente las piezas mecanizadas para detectar defectos y garantizar la calidad.
- Automatización inteligente: Se están desarrollando sistemas de mecanizado automatizado que utilizan algoritmos de Machine Learning para tomar decisiones en tiempo real.
En el caso del brochado casi todos los aspectos nombrados se están abordando, investigando y/o implementando en los procesos de fabricación. Por mencionar dos ejemplos relevantes sobre el uso de la Inteligencia artificial en los últimos años se está abordando la predicción de la geometría del borde de corte en brochas. Un primer caso presenta un nuevo enfoque en inteligencia artificial, que utiliza las relaciones entre los parámetros del proceso, el radio de corte y las fuerzas de corte medidas para pronosticar cambios en la geometría de la herramienta. Los datos medidos y los parámetros del proceso se utilizaron como valores de entrada y salida para el método Machine Learning (ML). La estructura de este método se puede observar en la figura 11.
![Figura 11. Estructura del método de Machine Learning para la predicción de la geometría del borde de la herramienta [15]... Figura 11. Estructura del método de Machine Learning para la predicción de la geometría del borde de la herramienta [15]...](https://img.interempresas.net/fotos/4641783.jpeg)
Un segundo estudio se ha desarrollado un nuevo método en base a análisis de imágenes para describir la forma de herramientas de brochado de manera eficiente. Este método lee los puntos de corte de la herramienta de un modelo proporcionado en un formato pixelado, comúnmente utilizado en ingeniería. La geometría resultante puede ajustarse y utilizarse fácilmente en simulaciones, lo que garantiza su adaptabilidad a la realidad de los procesos de brochado [18].
También se ha desarrollado métodos inteligentes de detección de desgaste en herramientas de brochado. El algoritmo de aprendizaje supervisado es alimentado mediante imágenes de diferentes tipos y grados de desgaste de herramientas [19]. El algoritmo de Machine Learning es capaz de detectar el progreso de desgaste con errores mínimos.
5.4. Brochado duro y brochado de alta velocidad
Las demandas técnicas del proceso de brochado están en constante aumento. Las demandas de industrias automotriz y aeronáutica crecen constantemente lo que hacen pensar en el aumento de la producción en menor tiempo posible. Se está reduciendo la holgura en los conjuntos de piezas brochadas para mejorar su rendimiento, como reducir el ruido y hacer las cajas de cambios más eficientes. Por lo tanto, en muchos casos, las tolerancias dimensionales y geométricas, así como las especificaciones de rugosidad, requieren que el brochado se realice después del tratamiento térmico de la pieza. El re-brochado en piezas templadas se está volviendo más frecuente y las piezas resultantes tienen una calidad muy similar a las obtenidas mediante rectificado.
Para cumplir este propósito se trabaja en dos frentes interrelacionados: la lubricación y recubrimientos de herramientas. En primera instancia se está investigando el brochado en seco, donde este enfoque presenta dos ventajas fundamentales: Eliminación del uso de refrigerante y reduciendo así el consumo y desperdicio de agua y aceites de corte. Otra ventaja es que los componentes salen limpios de la máquina sin la necesidad de lavador posterior de las mismas [20]. Con las crecientes preocupaciones medioambientales, la sustitución del fluido de corte a base de aceite mineral también se convierte en un problema prioritario a vencer. Se ha estimado que más del 85% del fluido de corte utilizado en las industrias de mecanizado es de base mineral, lo que es potencialmente cancerígeno y que más del 70% de los residuos del fluido de corte se liberan a la naturaleza sin ningún proceso de purificación. Por lo tanto, la ‘Green-lubrication’ es otra línea de trabajo investigativo relevante para mejorar procesos de brochado amigables con el medio ambiente. Ejemplos recientes se están utilizando aceites vegetales como el aceite de soja como fluido base. A este aceite base se prepara el fluido de corte con nanofluidos (NFCF) añadiendo diferentes concentraciones en peso de partículas de nanografito (NGP). Los resultados reportados son que Cuando la concentración de NGP es del 0,4% en peso, la lubricación del proceso de brochado exhibe un estado de lubricante mixto ideal (figura 12), lo que da como resultado una resistencia a la fricción mínima [21].
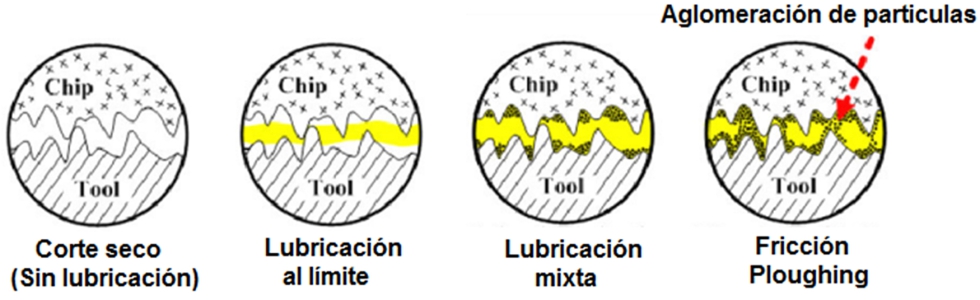
En la misma línea de una refrigeración más sostenible, se estudia la mitificación de los efectos negativos de los lubricantes irremplazables. Realizándose estudios sobre microorganismos que crecen en este entorno, como los Pseudomonas. Se han encontrado que el uso de nano partículas como el óxido de cobre (CuO) pueden combatir la formación de biopelículas de estos microrganismos ayudando a la conservación de aceites de corte [22].
Se está investigando la aplicación de recubrimientos anti-desgaste en herramientas de brochado para resistir condiciones de servicio difíciles. Sin embargo, el principal desafío radica en depositar estos recubrimientos en herramientas de gran tamaño debido a sus dimensiones. Se ha desarrollado recientemente una tecnología eficiente, el equipo de recubrimiento PVD HIPIMS/UBM, capaz de recubrir brochas de tamaño universal con éxito, demostrando resultados positivos en propiedades como dureza, adhesión y resistencia al desgaste [23]. El esquema de esta tecnología de recubrimiento industrial para herramientas de brochado se muestra en la figura 13.
![Figura 13. Esquema de tecnología de pulverización catódica por impulso de magnetrón de alta potencia (HIPIMS) para el recubrimiento de brochas [23]... Figura 13. Esquema de tecnología de pulverización catódica por impulso de magnetrón de alta potencia (HIPIMS) para el recubrimiento de brochas [23]...](https://img.interempresas.net/fotos/4641785.jpeg)
6. Objetivos y retos
Las tendencias emergentes en el mercado mundial de brochadoras incluyen la creciente adopción de tecnología avanzada, como los sistemas CNC (control numérico por computadora), que mejoran la eficiencia y la precisión en las operaciones de mecanizado. Además, existe una demanda creciente de brochadoras con capacidades multieje para atender tareas de mecanizado complejas (figura 14). El mercado también está siendo testigo de un cambio hacia el desarrollo de brochadoras ecológicas y sostenibles para alinearse con las normativas medioambientales. Además, se está explorando la integración de la automatización y la robótica en las brochadoras para mejorar la productividad y reducir los errores humanos. Estas tendencias reflejan el enfoque de la industria en mejorar el desempeño operativo y satisfacer los requisitos cambiantes de los clientes.
![Figura 13. Máquina brochadora horizontal para el mecanizado de firtrees [24] Figura 13. Máquina brochadora horizontal para el mecanizado de firtrees [24]](https://img.interempresas.net/fotos/4641786.jpeg)
La fabricación de máquinas brochadoras se refiere a la aplicación de tecnologías avanzadas y mejoras en las propias máquinas de brochado para aumentar eficiencia, precisión y producción. Algunos avances y objetivos en este campo incluyen:
- Automatización: la integración de sistemas automatizados en las máquinas brochadoras, como carga y descarga automáticas y controles CNC avanzados, promueve una operación más eficiente y reduce la necesidad de intervención humana.
- Mejoras en la precisión: la fabricación de las máquinas brochadoras se centra en mejorar la precisión dimensional y la calidad superficial de las piezas mediante sistemas de control de retroalimentación, herramientas de alta precisión y tecnologías de medición integradas.
- Mayor flexibilidad: las máquinas brochadoras modernas son más versátiles, capaces de manejar una variedad más amplia de piezas y procesos de brochado con sistemas de cambio rápido de herramientas, programación CNC avanzada y la capacidad de realizar múltiples operaciones en una sola máquina.
- Reducción de los tiempos de ciclo: la fabricación de las máquinas brochadoras busca reducir los tiempos de ciclo y aumentar la productividad mediante la optimización de procesos de corte, reducción de tiempos de cambio de herramientas y mejoras en velocidad y precisión.
- Integración de tecnologías digitales: la implementación de tecnologías digitales como IoT, análisis de datos e inteligencia artificial permite monitorear y optimizar el rendimiento de las máquinas brochadoras, predecir fallas y mejorar la planificación de la producción.
En resumen, los avances en la fabricación de máquinas brochadoras tienen como objetivo mejorar la eficiencia, la precisión y la flexibilidad de estas máquinas para satisfacer las demandas de la industria moderna y aumentar la competitividad de los fabricantes.
Bibliografía
[1] Verified Market Research, ‘Broaching Machine Market Size, Share, Trends, Opportunities & Forecast’, [línea]. Available: https://www.verifiedmarketresearch.com/product/broaching-machine-market/. Accessed: Mar. 14, 2024. [Online]. Available: https://www.verifiedmarketresearch.com/product/broaching-machine-market/
[2] The Insight Partners, ‘Broaching Tools Market to Grow at a CAGR of 5.3% to reach US$ 216.90 Million from 2020 to 2028’, [línea]. Available: https://www.theinsightpartners.com/reports/broaching-tools-market. Accessed: Mar. 14, 2024. [Online]. Available: https://www.theinsightpartners.com/reports/broaching-tools-market
[3] ITP Aero, ‘Certificaciones y Calidad - ITP Aero Fabricante de motores aeronáuticos y turbinas’, [línea]. Available: https://www.itpaero.com/es/sobre-itp-aero/certificaciones-y-calidad/. Accessed: Mar. 14, 2024. [Online]. Available: https://www.itpaero.com/es/sobre-itp-aero/certificaciones-y-calidad/
[4] Safran Group, ‘Safran Aircraft Engines’, [línea]. Available: https://www.safran-group.com/companies/safran-aircraft-engines. Accessed: Mar. 14, 2024. [Online]. Available: https://www.safran-group.com/companies/safran-aircraft-engines
[5] EASA, ‘Aircraft certification | EASA’, [línea]. Available: https://www.easa.europa.eu/en/domains/aircraft-products/aircraft-certification. Accessed: Mar. 14, 2024. [Online]. Available: https://www.easa.europa.eu/en/domains/aircraft-products/aircraft-certification
[6] P. J. Arrazola, J. Rech, R. M’Saoubi, and D. Axinte, ‘Broaching: Cutting tools and machine tools for manufacturing high quality features in components’, CIRP Annals, vol. 69, no. 2, pp. 554–577, Jan. 2020, doi: 10.1016/J.CIRP.2020.05.010.
[7] P. Gilormini, E. Felder, L. Tronchet, F. Leroy, and F. Le Maitre, ‘A Comparative Analysis of three Machining Processes: Broaching, Tapping and Slotting’, CIRP Ann Manuf Technol, vol. 33, no. 1, pp. 19–22, 1984, doi: 10.1016/S0007-8506(07)61371-7.
[8] F. Klocke, M. Seimann, M. Binder, and B. Doebbeler, ‘Milling of Fir-Tree Slots in Allvac 718 plus’, Procedia CIRP, vol. 77, pp. 409–412, 2018, doi: 10.1016/j.procir.2018.08.297.
[9] P. Vogtel, F. Klocke, D. Lung, and S. Terzi, ‘Automatic Broaching Tool Design by Technological and Geometrical Optimization’, Procedia CIRP, vol. 33, pp. 496–501, 2015, doi: 10.1016/j.procir.2015.06.061.
[10] P. Vogtel, F. Klocke, D. Lung, and S. Terzi, ‘Automatic Broaching Tool Design by Technological and Geometrical Optimization’, Procedia CIRP, vol. 33, pp. 496–501, 2015, doi: 10.1016/j.procir.2015.06.061.
[11] F. Zanger, N. Boev, and V. Schulze, ‘Surface Quality after Broaching with Variable Cutting Thickness’, Procedia CIRP, vol. 13, pp. 114–119, 2014, doi: 10.1016/j.procir.2014.04.020.
[12] D. Ulutan and T. Ozel, ‘Machining induced surface integrity in titanium and nickel alloys: A review’, Int J Mach Tools Manuf, vol. 51, no. 3, pp. 250–280, Mar. 2011, doi: 10.1016/j.ijmachtools.2010.11.003.
[13] P. Albrecht, ‘New Developments in the Theory of the Metal-Cutting Process: Part I. The Ploughing Process in Metal Cutting’, Journal of Engineering for Industry, vol. 82, no. 4, pp. 348–357, Nov. 1960, doi: 10.1115/1.3664242.
[14] C. Fabián Pérez-Salinas, P. Fernández-Lucio, A. del Olmo, I. Aldekoa-Gallarza, and L. Norberto López de Lacalle, ‘The influence of cutting edge microgeometry on the broaching of Inconel 718 slots’, Engineering Science and Technology, an International Journal, vol. 48, p. 101563, Dec. 2023, doi: 10.1016/j.jestch.2023.101563.
[15] M. Wimmer, R. Hartl, and M. F. Zaeh, ‘Determination of the Cutting-Edge Microgeometry Based on Process Forces during Peripheral Milling of Ti-6Al-4V Using Machine Learning’, Journal of Manufacturing and Materials Processing, vol. 7, no. 3, p. 100, May 2023, doi: 10.3390/jmmp7030100.
[16] C. Chen, J. Xu, J. Ni, G. Chen, and Z. Lyu, ‘An intelligent broaching tool design method based on CBR and support vector machine’, Advanced Engineering Informatics, vol. 60, p. 102447, Apr. 2024, doi: 10.1016/j.aei.2024.102447.
[17] J. Sasiain, A. Sanz, J. Astorga, and E. Jacob, ‘Towards Flexible Integration of 5G and IIoT Technologies in Industry 4.0: A Practical Use Case’, Applied Sciences, vol. 10, no. 21, p. 7670, Oct. 2020, doi: 10.3390/app10217670.
[18] Z. Gabos, D. Plakhotnik, and Z. Dombovari, ‘Digital geometry generation of high precision broaching tool cutting edges through image processing algorithm’, MM Science Journal, vol. 2023, no. 4, Nov. 2023, doi: 10.17973/MMSJ.2023_11_2023124.
[19] I. Holgado, C. Pérez-Salinas, N. Ortega, L. N. L. de Lacalle, and A. del Olmo, ‘An Intelligent Machine Learning Based Method for Tool Wear Estimation in the Vertical Broaching Process’, in Proceedings of the XV Ibero-American Congress of Mechanical Engineering, Cham: Springer International Publishing, 2023, pp. 306–312. doi: 10.1007/978-3-031-38563-6_45.
[20] F. Klocke, B. Döbbeler, and M. Seimann, ‘Dry Broaching Using Carbon Free Steel as Tool Material’, Procedia CIRP, vol. 46, pp. 496–499, 2016, doi: 10.1016/j.procir.2016.04.076.
[21] M. Xu, X. Yu, and J. Ni, ‘Penetration and lubrication evaluation of vegetable oil with nanographite particles for broaching process’, Friction, vol. 9, no. 6, pp. 1406–1419, Dec. 2021, doi: 10.1007/s40544-020-0421-0.
[22] S. H. Musavi and B. Davoodi, ‘A challenging study on compatibility or incompatibility of vegetable-based lubricant with human health’, The International Journal of Advanced Manufacturing Technology, Feb. 2024, doi: 10.1007/s00170-024-13083-z.
[23] W.-D. Münz, R. Klink, D. Aleksic, and M. Mazaheri, ‘HIPIMS/UBM PVD Coating Equipment Designed to Coat Universal Sized Broaches’, Coatings, vol. 12, no. 3, p. 300, Feb. 2022, doi: 10.3390/coatings12030300.
[24] Federal Broach, ‘Electromechanical Horizontal Surface Broach - Federal Broach & Machine Company’, [línea]. Available: https://www.federalbroach.com/products/broaching-machines/surface-broaching/. Accessed: Mar. 14, 2024. [Online]. Available: https://www.federalbroach.com/products/broaching-machines/surface-broaching/