Electroerosión de altos vuelos
Esta crisis ha tumbado las previsiones que tenían los diferentes fabricantes aeronáuticos respecto al crecimiento del mercado aéreo para los próximos años. A principios de año, los dos mayores fabricantes de aviones del mundo, Airbus y Boeing, coincidían en la previsión de crecimiento de 4-5% tanto en el transporte aéreo de pasajeros como en el transporte de cargas [1]. Sin embargo, recientemente Airbus ha anunciado que su producción bajará un 30% y Boeing tiene un escenario similar.
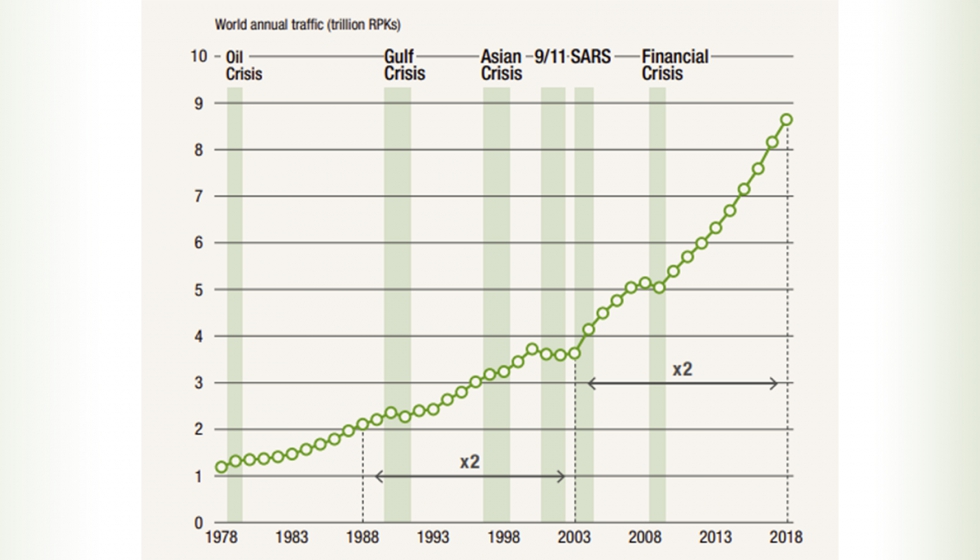
En este contexto, y teniendo en cuenta las características de esta crisis, el futuro es incierto y depende totalmente de cómo evolucione la pandemia. No se sabe cuánto durará la crisis, pero parece algo temporal, que se acabará cuando el mundo busque el modo de librarse de esta enfermedad. Por ese motivo, la industria aeronáutica esta ante un periodo de oportunidad para desarrollar nuevos productos, mejorar los diseños, ganar eficiencia, reducir consumos o pensar en soluciones para que cuando esto acabe, el producto sea mucho más competitivo. Es más, ya antes de la crisis de la COVID-19, la industria aeronáutica tenía dentro de sus prioridades la reducción de emisiones de gases y ruido. El ACARE (Advisory Council for Aviation Research and Innovation in the EU) había fijado para el 2050 una reducción de las emisiones de CO2 del 75%, un 90% para las emisiones de NOx y un 65% las emisiones de ruido tomando como base los valores del año 2000. Y es que el cambio climático ya es algo evidente y es tan o más peligroso que la pandemia actual.
Son motivos más que suficientes para aprovechar este valioso periodo en pensar, desarrollar, probar… y fabricar. El sector aeronáutico tiene detrás toda una industria para su fabricación y mantenimiento. En el coste global de fabricación de un avión, el motor es una de las partes que mayor coste genera, tanto en su propia fabricación como en el mantenimiento. Por eso, una de las tendencias actuales para mejorar la eficiencia económica y ecológica de un avión, consiste en optimizar su sistema de propulsión o su eficiencia térmica. Para ello, se opta por hacer cambios de diseño para mejorar la aerodinámica o bajar el peso. Además, la mejora de eficiencia térmica se logra incrementando la temperatura de combustión y para ello hay que utilizar materiales que soporten esas temperaturas o incorporar sistemas de refrigeración en las piezas (agujeros o canales de refrigeración).
Sin embargo, implementar estas optimizaciones de diseño o el uso de nuevos materiales en el motor aeronáutico conllevan un reto en la fabricación de las diferentes piezas. Para ello, muchas veces es necesario optimizar o incluso reformular los métodos de fabricación utilizados. Hay casos en los que los métodos de fabricación tradicionales tienen limitaciones a la hora de conseguir ciertas geometrías o trabajar con ciertos materiales, lo cual lleva a utilizar nuevos procesos de fabricación o procesos utilizados en otras aplicaciones pero que no se utilizaban en la fabricación de piezas del sector aeronáutico. Algunos de estos procesos de fabricación están muy de moda actualmente, por ejemplo, la fabricación aditiva, un método nuevo de fabricación que se está aplicando para diversas soluciones. Otros, como la electroerosión, no son tan conocidos ni atrayentes, incluso puede parecer que es un método de fabricación antiguo y que está en desuso, pero la realidad es otra. La electroerosión se utiliza para la fabricación de ciertas operaciones o piezas del motor aeronáutico y es un método con mucho potencial para ser aplicado en nuevos diseños y soluciones.
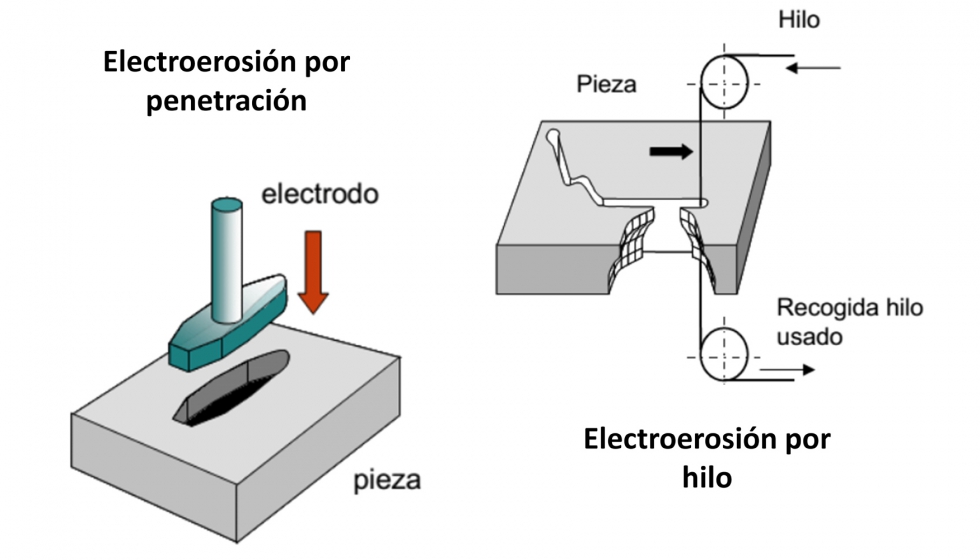
La electroerosión ¿Qué es?
Los inicios de esta técnica de fabricación datan de la segunda guerra mundial, aunque aún hoy en día no es un proceso tan conocido como los métodos de fabricación tradicionales. Está catalogado como un proceso de fabricación no-convencional, en el que el arranque de material se logra mediante descargas eléctricas controladas que se dan entre herramienta (más conocida como electrodo) y pieza. La cantidad de material eliminado en cada descarga es muy pequeña, pero como estas descargas son muy rápidas, de microsegundos, a medida que pasa el tiempo el arranque es perceptible y finalmente el negativo de la forma del electrodo queda reflejado en la pieza, hecho que permite generar piezas con geometrías complejas.
Hay dos tipos principales de electroerosión, la electroerosión por penetración y la electroerosión por hilo. En la electroerosión por penetración la pieza toma el negativo de la forma del electrodo (herramienta), el cual normalmente se fabrica con grafito o con cobre. En la electroerosión por hilo, la herramienta es un hilo fino, el que más comúnmente se utiliza suele ser de latón y un diámetro de 0.25mm. Según se desplaza el hilo por la trayectoria programada, corta el material que encuentra en su camino y así se obtiene la forma de pieza deseada. Además, cada vez más fabricantes están optando por generar una nueva línea de producto de hole drilling mediante electroerosión. Si bien es cierto que es una técnica que entraría dentro de la electroerosión por penetración, la técnica sufre unas variaciones que la hacen merecedora de una línea aparte.
La tasa de arranque no es muy alta comparándolas con otros procesos tradicionales de fabricación [2]. Sin embargo, las ventajas de esta técnica superan con creces sus limitaciones. En el proceso de electroerosión no existe contacto entre electrodo y pieza, se mantiene una distancia llamada ‘gap’. La ausencia de contacto es la razón de la principal ventaja de la electroerosión, no hay fuerzas entre electrodo y pieza y por ello se logra una precisión muy alta. Además, mientras el material de la pieza tenga la suficiente conductividad eléctrica, es capaz de dar forma a materiales de muy alta dureza o baja maquinabilidad, muchas veces imposibles de mecanizar con otros procesos. Por ello es una buena solución para los materiales utilizados en el motor aeronáutico, materiales que deben soportar altas temperatura como las superaleaciones de base níquel o cobalto o el titanio.
Las ventajas mencionadas hacen que este proceso sea merecedor de ser una opción a la hora de fabricar una pieza del motor de un avión y por ello su uso se está extendiendo en cada vez más aplicaciones de este tipo. Los fabricantes de máquinas de electroerosión, no se han quedado atrás y ya tienen líneas específicas para este tipo de desarrollos, además de servicios de llave en mano para la puesta a punto de aplicaciones de fabricación de piezas aeronáuticas.
¿Es fiable esta técnica de fabricación?
Históricamente, la industria aeronáutica ha sido reticente en incorporar piezas fabricadas mediante electroerosión en los motores de avión. Sobre todo, en las denominadas piezas ‘criticas’, es decir, piezas rotativas o que soportan cargas cíclicas y que pueden sufrir fallos a fatiga. La razón de esta reticencia es la integridad superficial de las piezas electroerosionadas. Debido al carácter térmico del proceso, las descargas generadas funden y/o evaporan material de la pieza, generando un cráter. La zona próxima al cráter sufre un aumento de la temperatura. Además, se genera una sobrepresión que hace que parte del material eliminado se vuelva a depositar en la superficie de la pieza. Estos dos fenómenos mencionados, generan en la superficie de la pieza una zona afectada térmicamente (ZAT) y una capa de material refundido, de alta dureza, pero gran fragilidad, conocida como ‘capa blanca’. Esta capa es fuente de grietas que, si se combinan con cargas cíclicas, se pueden propagar en la pieza generando un fallo fatal.
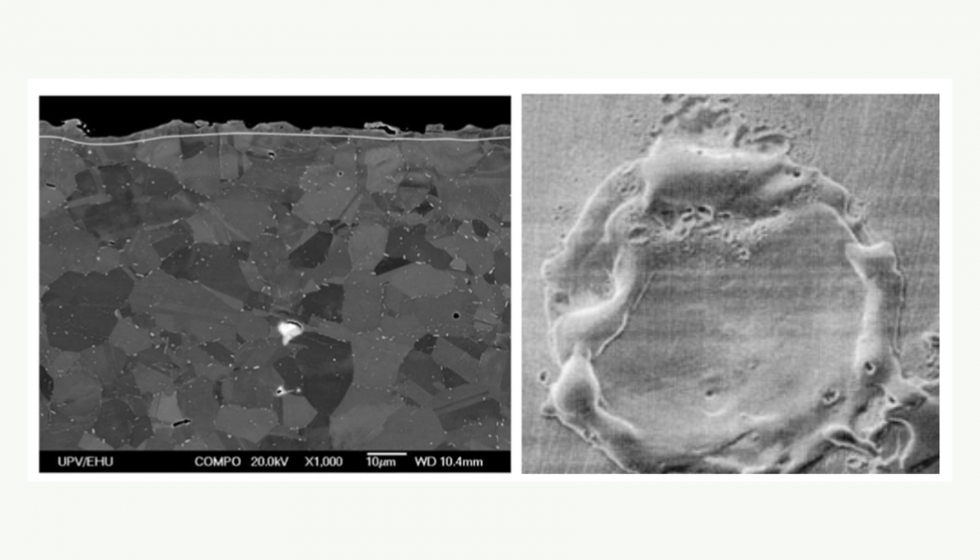
Durante muchos años, esta característica del proceso de electroerosión ha dificultado aplicar este proceso de fabricación a piezas críticas del motor aeronáutico y si no había otra opción ha sido necesaria la aplicación de tratamientos superficiales posteriores para eliminar esta capa, o incluso mecanizarlas, con el sobrecoste que eso conlleva.
Sin embargo, las máquinas de electroerosión modernas y sobre todo los nuevos generadores de máquina, han evolucionado significativamente con respecto a sus predecesoras. Hoy en día, las pruebas han demostrado que las máquinas de electroerosión no dejan ZAT medibles y producen capas de material refundido casi inexistentes. Estas máquinas pueden producir componentes con acabados de hasta que miden 0,15 Ra, y dejan las superficies de las piezas prácticamente sin daños. La razón de esta evolución está en la mejora de generadores, que son capaces de controlar el aporte de energía de cada descarga y así poder generar descargas de alto contenido energético y corta duración, que logran menor afección térmica en la pieza y dejan una superficie libre de capa blanca y con una zona afectada térmicamente nula [3].
Electroerosión para piezas aeronáuticas
Tal como se ha mencionado, en la actualizad, existen procesos y piezas del motor aeronáutico que se están produciendo mediante electroerosión. Para algunas de ellas, la electroerosión ya es un método de fabricación establecido. Hay otras operaciones, sin embargo, en las que la electroerosión es una alternativa viable al método de fabricación actualmente utilizado o incluso está buscando su nicho junto a este método de fabricación principal. En esta sección se mostrarán muchas de estas aplicaciones, aunque visto el potencial de este método de fabricación históricamente olvidado en este sector, confiamos que en el futuro sean más numerosas las piezas aeronáuticas donde se aplique.
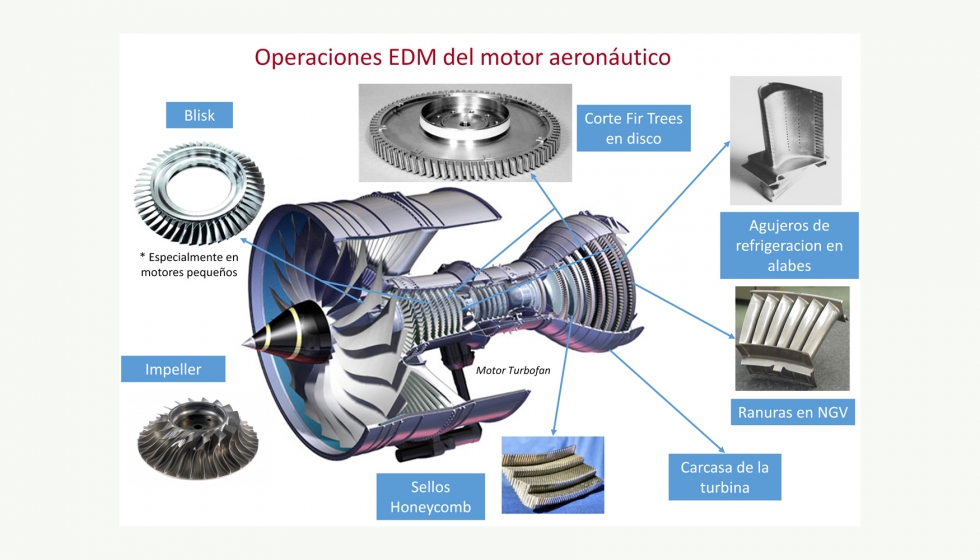
Una de las operaciones donde la electroerosión está más establecida son la fabricación de las ranuras de las caras laterales de NGV (Nozzle Guided Vanes). Estas son piezas del estator de la turbina aeronáutica y son grupos de alabes unidos por un segmento de anillo interior y exterior. Su función es dirigir el aire hacia la zona de alabes rotativos para que se aproveche la máxima energía. Estos grupos de alabes, se une entre sí por unas chapas que se introducen en una ranura que se erosionan en sus caras laterales y así se forma el anillo completo del estator. Estas piezas, debido a las altas temperaturas que tienen que soportar, se fabrican con superaleaciones base níquel y cobalto, aleaciones termorresistentes capaces de mantener sus propiedades a altas temperaturas. Si a esto le añadimos la geometría de las ranuras, son ranuras de alta relación de aspecto, estrechas y profundas (pueden tener entre 0,6 y 1mm de anchura y una profundidad de hasta 10 mm), el mecanizado se vuelve actualmente imposible y por ello se aplica la electroerosión.
En la industria, se utiliza la electroerosión por penetración para fabricar estas ranuras. Se mecanizan electrodos de grafito mediante fresado, dejando una espina de pequeño espesor (menor que la anchura de la ranura, para compensar el gap del proceso). Una vez posicionados pieza y electrodo, se procede a electroerosionar y chispa a chispa se consigue la geometría de la ranura deseada. Esto que se ha explicado de manera breve, suele ser más complicado. Los primeros milímetros de profundidad el proceso suele ser estable y rápido. Sin embargo, de una profundidad en adelante, la suciedad (las partículas que se eliminan en el proceso) se va acumulando en el espacio estrecho de la ranura y empiezan a generar cortos, ralentizando el proceso y aumentando los tiempos de erosión. Esta problemática ha generado muchos estudios en los últimos años, algunos para estudiar los flujos de suciedad dentro de la ranura y entender mejor lo que sucede, otros para buscar los mejores parámetros de erosión para que el proceso sea lo más rápido y productivo posible [4][5].
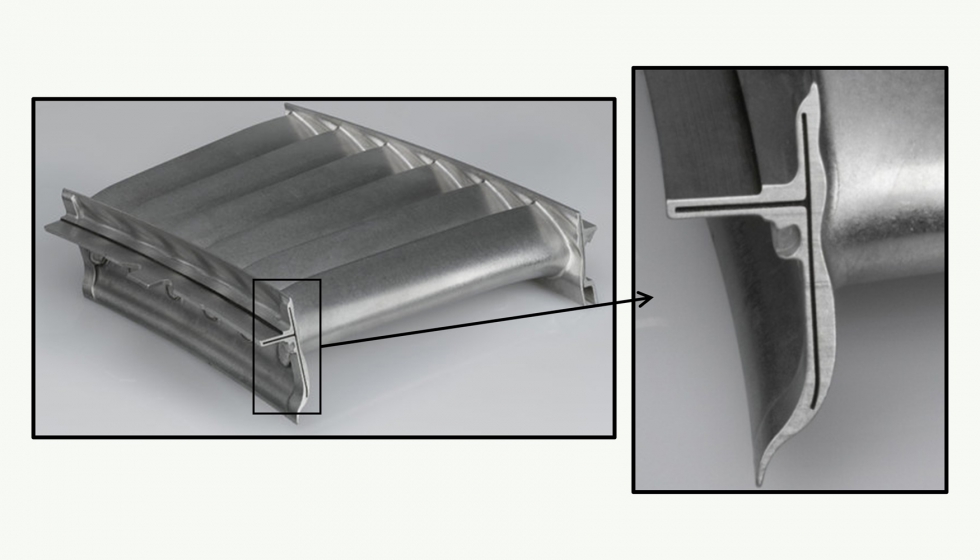
Algo similar sucede con los agujeros de refrigeración de los vanos y alabes. Tal como se ha comentado, la alta temperatura de combustión que hay dentro de los motores hace necesario emplear materiales de alta resistencia que mantengan sus propiedades a altas temperaturas. Sin embargo, incluso utilizando superaleaciones base níquel y cobalto, estas piezas pueden tener temperaturas de funcionamiento de hasta 800°C y para ello, además de emplear materiales adecuados es necesario un enfriamiento interno adicional para poder sobrevivir el tiempo suficiente en estas condiciones extremas.
La producción del gran número de agujeros de refrigeración es una tarea compleja. Al igual que ocurre con las ranuras, estos agujeros son de pequeño diámetro y alta profundidad. Además, llevar un ángulo de inclinación respecto a la superficie del alabe. En estos casos, aplicar métodos convencionales de fabricación como el taladrado o fresado, generan fuerzas laterales que llevan faltas de precisión y roturas de herramienta. En el caso del láser, la zona afectada térmicamente puede llegar a ser alta, además de perder precisión según se profundiza. Otra alternativa, el ECM, puede evitar el daño térmico, pero las tasas de arranque son bajas.
La electroerosión es una buena solución para la fabricación de agujeros de refrigeración en alabes y vanos. No obstante, la necesidad de lograr un proceso con una tasa de arranque alta, ha hecho que se desarrollen máquinas específicas de penetración para ello. Por ello, la mayoría de fabricantes tratan la fabricación y el desarrollo de este tipo de máquinas de forma independiente a la electroerosión por penetración. Las singularidades de este tipo de máquinas son varias. Normalmente se utiliza un electrodo rotativo cilíndrico con un agujero (o varios) interior, por el cual se inyecta liquido dieléctrico a muy alta presión. Esta limpieza interior ayuda a eliminar la suciedad, evitando cortos y ganando eficiencia. Además, el electrodo lleva una guía próxima a la zona de erosión, para evitar que flecte y mantener la precisión. En cuanto al liquido dieléctrico utilizado, el agua desionizada es lo más habitual, aunque también existen máquinas que trabajan con aceite, sobre todo en agujeros micro o cuando se necesita un muy buen acabado [6]. No obstante, toda tecnología tiene sus hándicaps, que en este caso son el elevado desgaste de electrodo, el control en agujeros ciegos o las erosiones en las superficies inclinadas, lo cual muestra una necesidad constante de desarrollo de tecnología para obtener los mejores resultados.
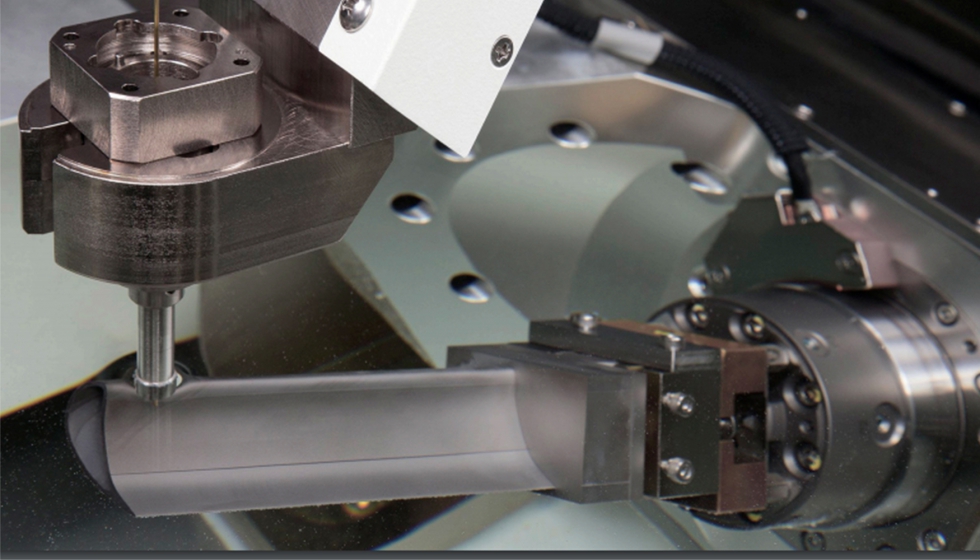
Otra tipología de piezas del motor aeronáutico donde se aplica la electroerosión son los sellos. La función de estas piezas es evitar las fugas de gas entre diferentes etapas de compresión y turbinado, para no reducir el rendimiento del motor. Los dos métodos más utilizados son el sellado por laberinto y el sellado por ‘honeycomb’. En este segundo caso, se utiliza una estructura en forma de panal de abeja, unido a un trozo de anillo, por ello, también se conocen como segmentos. Normalmente el honeycomb y el segmento de anillo se unen mediante soldadura brazing, y se utiliza la electroerosión para acabar la pieza. Se realizan dos operaciones para el acabado de precisión del componente, el corte lateral del anillo y el acabado de las celdas del honeycomb, necesario para que el componente tenga las medidas adecuadas después de la soldadura realizada. Esta última operación no es posible realizarla mediante métodos convencionales de mecanizado, ya que las paredes de la espuma metálica que conforma el honeycomb pueden llegar a tener 0,1 mm de espesor. Con las fuerzas que se generan en el proceso de mecanizado, estas paredes se deforman o se rompen. Gracias a la ausencia de contacto y de fuerzas del proceso de electroerosión por penetración, se pueden acabar las caras del honeycomb y obtener la precisión necesaria de los requerimientos de la pieza.
Para esta operación el objetivo principal es el aumento de la productividad, además de mantener las exigencias de precisión e integridad superficial de la pieza. Por ello, en los últimos años los fabricantes de este tipo de piezas se han centrado en la optimización del proceso de fabricación, así como en fabricación monolítica (sin uniones). Como ejemplo está el proyecto ROTOSEAL (Hazitek 2019) fruto de la colaboración entre la empresa vasca WEC Velatia y el CFAA, que busca desarrollar toda una ‘nueva generación’ de piezas para el sellado dinámico de turbinas de motores aeronáuticos, y para ello se trabaja en los últimos desarrollos tecnológicos basados tanto en soldadura avanzada como en electroerosión (por penetración y por hilo) [7].
Continuando en el área de la electroerosión por penetración, las piezas monolíticas con cavidades complejas es un reto que está teniendo respuesta. Este tipo de piezas, como por ejemplo los blisk e impellers, se fabrican en una sola pieza, evitando así la unión entre la parte central (el disco) y los alabes. La ausencia de uniones se traduce en ventajas. La principal de ellas es que una unión puede ser fuente de inicio de grietas, si se elimina, no existe ese peligro. Además, la fabricación integral de este tipo de piezas permite optimizar el diseño, mejorando la aerodinámica y/o ahorrando peso de componentes, lo cual lleva a un aumento de la eficiencia.
El método natural de fabricación de este tipo de componentes es el fresado, ya que es un método muy versátil, donde se pueden programar las trayectorias necesarias para cada tipo de pieza y tiene unas tasas de arranque de material altas. Sin embargo, el fresado tiene sus dificultades. Las tasas de rotura de herramientas son altas, debido a los materiales termorresistentes con los que se fabrican las piezas. Además, las geometrías cerradas (shrouded blisk y shrouded impellers) tienen canales en los que no es posible acceder con una herramienta de fresado a todas las zonas a mecanizar porque existirían colisiones con el material que no es necesario eliminar.
Entre los procesos alternativos al fresado para la fabricación de este tipo de piezas esta la electroerosión por penetración, que en los últimos años está tomando mucho peso. Las ventajas de esta tecnología (independencia de la dureza o la baja maquinabilidad del material), permiten que se use como una solución factible. Sin embargo, se ha tenido que invertir muchos recursos en el diseño de electrodos y generación de trayectorias para la fabricación de piezas. Numerosos grupos de investigación han estado trabajando en diferentes métodos, tanto para el diseño óptimo de electrodos, geometrías, numero de electrodos, estrategias, etc. como para hallar la trayectoria perfecta de erosión [8] [9]. La diversidad de geometrías y tamaños de piezas, muestra que no parece que exista un método global que se pueda aplicar a cualquier geometría y que proporcione una solución óptima de estrategia de erosión, sino que es necesario un estudio previo de la forma de la pieza para obtener la mejor solución de erosión. Cada una de este tipo de geometrías conlleva una serie de retos como el diseño de electrodos y sus trayectorias multiejes, disposición optima de la pieza, proceso de fabricación de electrodos, desgaste de los electrodos y su compensación, comportamiento del material, metrología…
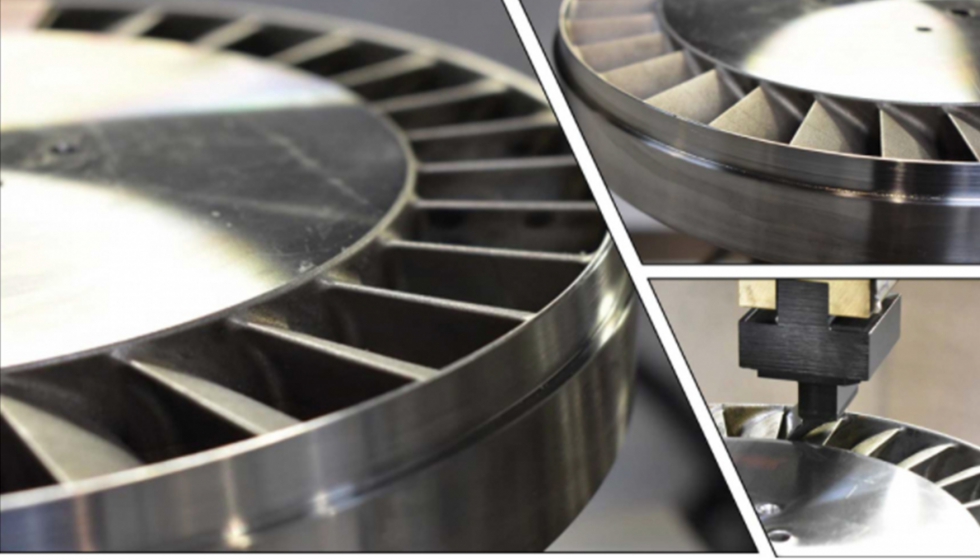
Ejemplo de ello, recientemente, ONA junto con el CFAA han participado en un estudio para probar la competitividad de la electroerosión por penetración para la fabricación de un blisk cerrado. Primero, se diseñaron los electrodos y sus trayectorias asociadas utilizando metodologías y algoritmos basados en métodos de optimización. Luego se diseñaron las estrategias de mecanizado y se definió la secuencia de operaciones. Finalmente, se fabricó el disco completo, que tomó 300 horas para producirse. Con este proyecto, además de consolidad la capacidad de fabricación de este tipo de piezas, se ha probado la viabilidad de esta tecnología de fabricación, además de verificar la necesidad de una fabricación unitaria como paso previo e indispensable para la producción en masa.
Por último, aunque en una operación que normalmente se realiza por fresado, el desbaste de las carcasas de las turbinas puede realizarse por electroerosión por penetración. ONA, en una colaboración con una empresa de fabricación aeronáutica China, han llegado a la conclusión de que realizar esta operación mediante electroerosión por penetración tiene sus ventajas. La inversión en equipamiento industria es menor, el gasto en consumibles también (los electrodos se re-mecanizan una vez desgastados) y a menor riesgo de rotura, menores costes derivados de la no calidad. Para competir en productividad en fresado, ONA tiene generadores que pueden llegar hasta los 400 amperios, cuando el estándar en electroerosión por penetración está en torno a 100 amperios. Esto, combinado con máquinas de doble cabezal, puede multiplicar las tasas de material arrancado para poder competir con el mecanizado convencional y convertirse en un método de fabricación para este tipo de operaciones
En cuanto a la electroerosión por hilo, el corte de las ranuras con forma de ‘Fir Tree’ del disco de las turbinas es una de las operaciones más populares para la fabricación de piezas aeronáuticas. En la industria esta operación se realiza por brochado, ya que se trata de un proceso critico de fabricación. El brochado es un proceso con elevadas tasas de arranque y que consigue una alta precisión e integridad superficial de la pieza. Sin embargo, el elevado coste de la maquinaria y herramientas necesarias unidos a la costosa puesta a punto y ajuste del proceso, solo lo hacen rentable en series altas de fabricación.
La electroerosión por hilo se ha convertido en una alternativa viable de fabricación de ‘Fir Trees’ debido a las mejoras de los generadores antes mencionadas. Además, el coste del hilo de electroerosión por hilo es bajo y la flexibilidad del proceso es tal que es especialmente adecuada para series cortas de fabricación, además de piezas en desarrollo que requieran cambios de geometrías hasta llevar al diseño final. Otro de los usos que se le puede dar es el predesbaste de los ‘Fir Tress’, para después acabarlos con brochado.
En cualquier caso, esta aplicación requiere unas tolerancias de fabricación muy altas, que puede llegar en casos hasta ±5 micras en el perfil, además de la integridad superficial adecuada mencionada. Lograr esto no es sencillo y por ello hay una diversidad de trabajos de investigación realizados para lograr las tolerancias marcadas y otros que estudian el efecto de la electroerosión por hilo en las superficies de materiales aeronáuticos además del efecto en la vida a fatiga. Todos estos concluyen en la viabilidad del proceso de electroerosión en la fabricación de esta operación [10].
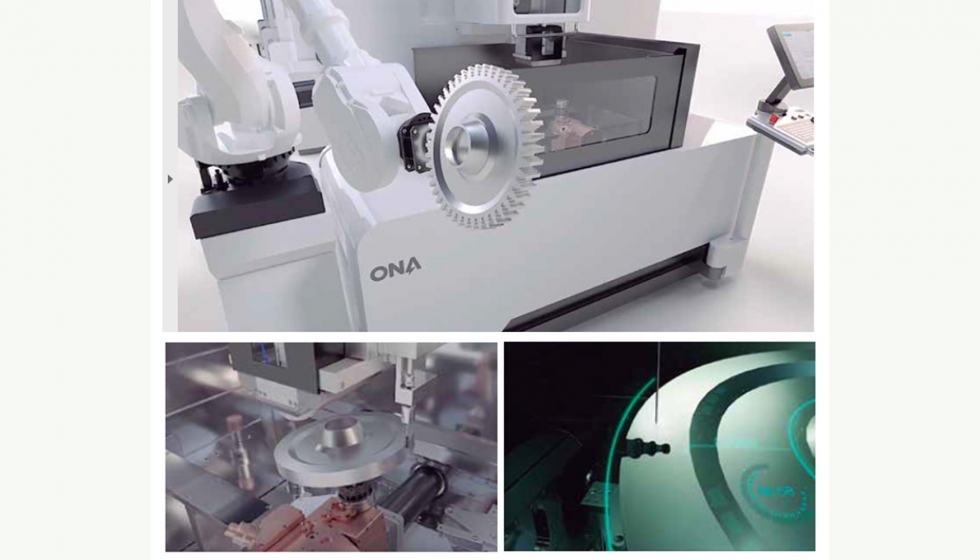
Los fabricantes de máquinas de electroerosión lo han visto claro y cada vez ponen más esfuerzo en dotar a sus máquinas con las características necesarias para la producción de discos de turbinas. Por ejemplo, GF Machining Solution tiene su máquina especifica llamada ‘Dedicated’ dotada de dos ejes adicionales para la rotación y balanceo de los discos de turbina [11]. Por otra parte, ONA Electroerosión en su último Magazine [12] muestra el resultado de un proyecto de fabricación de ‘Fir-tree’ para una prestigiosa compañía aeronáutica. Han empleado la máquina de hilo standard ONA AV35, la cual han tenido que adaptar (mesa rotativa de 2 ejes, robot para cargar piezas, palpador para posicionamiento, tecnología utilizada) para la fabricación de este tipo de componente. Dos planteamientos distintos para una misma aplicación, cada fabricante hace su apuesta.
Los datos, chivatos del control del proceso
El desarrollo de técnicas de Machine Learning en los últimos años ha abierto una nueva perspectiva sobre los problemas de seguimiento y trazabilidad del proceso mediante el uso de grandes cantidades de datos adquiridos. Es conocido que estas técnicas consisten en tomar datos del proceso para realizar algún tipo de predicción que pueda ayudar al usuario. La aplicación de estas técnicas en el mundo está muy extendida y es muy variada, pero en el campo de la fabricación, y más concretamente en el tema que estamos tratando en este artículo, la aplicación de la electroerosión en la fabricación de piezas aeronáuticas, apenas se aplican.
Sin embargo, en los últimos años, sobre todo en el plano de la investigación, están aflorando aplicaciones donde el Machine Learning puede dar soluciones. Una de las más notorias es el control de calidad de los Fir Trees cortados mediante electroerosión por hilo. Como ejemplo, Wang [12] ha desarrollado un sistema para monitorizar las tolerancias obtenidas en este proceso basada en métodos de aprendizaje automático no supervisados. Como variable de entrada utiliza datos del tiempo de ionización de las chispas. El sistema clusteriza las señales obtenidas, en diferentes grupos. Las mediciones realizadas en MMC muestran que la predicción de este sistema es realmente prometedora.
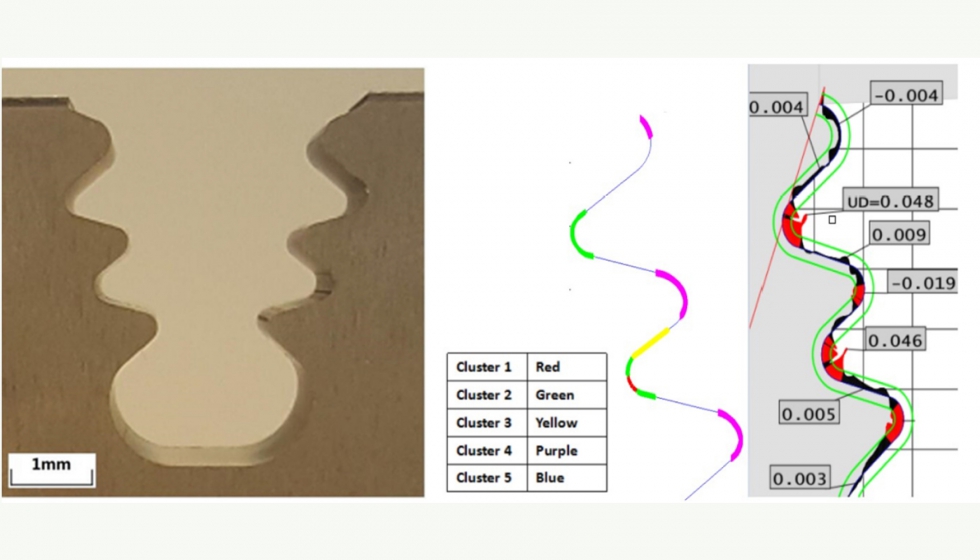
En el plano más industrial, fabricantes de máquina como ONA o GF+ tienen sus sistemas de control de proceso basados en datos de máquina. El sistema ONA Smart Connect promete la monitorización del proceso de electroerosión durante el corte, para poder obtener trazabilidad de pieza y análisis del proceso (prevenir errores, predecir mantenimientos, etc.). En el caso de GF su sistema Spark Track realiza un control de distribución de la chispa. Detectan el lugar donde se da cada chispa y lo procesan, para evitar las roturas de hilo y adaptar las condiciones de corte en cada instante. Ambos sistemas tienen un potencial enorme para controlar procesos productivos como los del sector aeronáutico, donde el control de la calidad es un aspecto esencial.
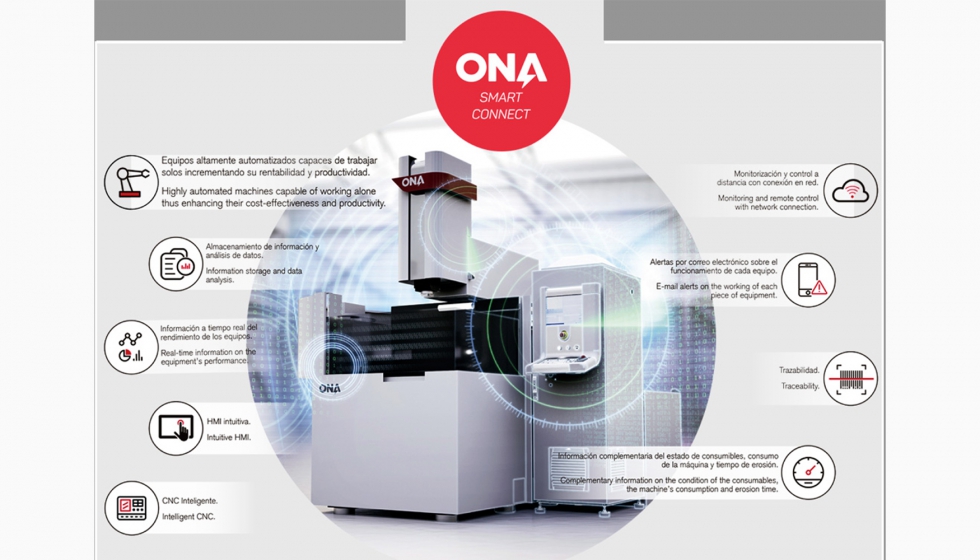
Un mundo por explorar
Como se muestra en este artículo, el hecho de utilizar la electroerosión como método de fabricación de piezas aeronáuticas está más vivo que nunca. El desarrollo que esta tecnología ha sufrido en los últimos años le ha abierto la puerta en este sector. Ahora es esencial aprovechar esta oportunidad en este periodo convulso para optimizar las aplicaciones actuales, desarrollar la tecnología, generar conocimiento y buscar nuevos nichos de mercado donde se pueda aplicar la electroerosión. Y es que cuando el mundo vuelta a rodar a ritmo frenético y las estelas de los aviones vuelvan a colmar el cielo, no queda otra que estar preparados con las mejores soluciones posibles.
Referencias:
[1] Airbus Global Market Forecast 2019-2038. https://www.airbus.com/aircraft/market/global-market-forecast.html
[2] F. Klocke, M. Zeis, A. Klink, D. Veselovac. Technological and Economical Comparison of Roughing Strategies via Milling, Sinking-EDM, Wire-EDM and ECM for Titanium- and Nickel-Based Blisks. CIRP Journal of Manufacturing Science and Technology, Vol. 6, pp. 198-203, 2013.
[3] I. Ayesta, B. Izquierdo, O. Flaño, JA Sanchez, J. Albizuri, R. Aviles. Influence of the WEDM process on the fatigue behavior of Inconel 718. International Journal of Fatigue, Vol 92, pp. 220-233,2016.
[4] I. Ayesta, B. Izquierdo, J.A. Sanchez, J.M. Ramos, S. Plaza, I. Pombo, N. Ortega, H. Bravo, R. Fradejas, I. Zamakona. Influence of EDM Parameters on Slot Machining in C1023 Aeronautical Alloy. Procedia Cirp, Vol 6, pp. 129-134, 2013.
[5] O. Flaño, I. Ayesta, B. Izquierdo, J.A. Sanchez, Y. Zhao, M. Kunieda. Improvement of EDM performance in high aspect ratio slot machining using multi-holed electrodes. Precision Engineering, Vol 51, pp. 223-231, 2018.
[6] B. Pfluger. Selecting the appropriate EDM technology for hole-drilling Applications. MAKINO 2014
[7] WEC y la UPV/EHU trabajan para incorporar la fabricación aditiva al sellado de turbinas de motor en el sector aeronáutico. SPRI, 2020.
[8] I. Ayesta, B. Izquierdo, J.A. Sanchez, J.M. Ramos, S. Plaza, I. Pombo, N. Ortega. Optimum electrode path generation for EDM manufacturing of aerospace components, Robotics and Computer-Integrated Manufacturing Vol. 37, pp. 273-281, 2016.
[9] O. Flaño, I. Ayesta, B. Izquierdo, J.A. Sanchez, J.M. Ramos. Expermental Study on the influence of electrode geometry and electrode path on wear pattern in EDM. Procedia CIRP, Vol 68, pp. 405-410, 2018.
[10] D. Welling. Results of Surface Integrity and Fatigue Study of Wire-EDM Compared to Broaching and Grinding for Demanding Jet Engine Components Made of Inconel 718. Procedia CIRP, Vol 13, pp. 339-344, 2014.
[11] https://www.gfms.com
[12] ONA EDM Magazine 2020. https://onaedm.es/
[13] J. Wang, J. A. Sanchez, I. Ayesta, J. A. Iturrioz. Unsupervised Machine Learning for Advanced Tolerance Monitoring ofWire Electrical Discharge Machining of Disc Turbine Fir-Tree Slots. Sensors Vol 18, pp. 3359-3369, 2018.