Optimización del proceso de taladrado dentro del contexto de la Industria 4.0
El sector aeronáutico siempre ha mostrado un gran interés por la investigación, desarrollo e innovación, convirtiéndose en un sector referente en este sentido. Este interés es impulsado por la intensa competitividad que existe dentro de este sector, generando la continua necesidad de mejorar el rendimiento de los procesos desde cualquiera de sus vertientes: funcional, medioambiental o energética, siempre garantizando la calidad y buscando el impacto directo sobre el rendimiento económico.
Uno de los primeros retos a los que se enfrenta el sector aeroespacial en esta cuarta revolución es la de lograr automatizar los procesos que, a día de hoy, contemplan el uso extensivo del trabajo manual, especialmente en operaciones tan relevantes para esta industria como son las operaciones de montaje.
Las piezas obtenidas a través de los diversos procesos de fabricación constituyen las diferentes secciones que se unen hasta conformar las estructuras aeronáuticas. Entre los diferentes métodos de unión utilizados se encuentran la unión mecánica, mediante aportación térmica (soldadura) y uniones adhesivas, así como diferentes combinaciones de las anteriores. Sin embargo, sigue siendo la unión mecánica por remachado el método mayoritariamente utilizado en dicho sector, independientemente de los materiales implicados en el ensamblaje. Es por esto que la operación de taladrado —previa al remachado— es considerada una fase crítica. Así, un avión de tamaño pequeño puede estar compuesto en torno a 85.000 remaches, todos sometidos a esfuerzos de cortadura y de tracción, lo que muestra el grado de importancia que presenta en la estructura final [2–5]. El número de veces que se repite la operación, junto con la consideración de que se realiza en las fases finales y que un fallo puede suponer el rechazo de un componente completo, permiten discernir la repercusión que cualquier mejora en el proceso puede tener sobre el producto final.
Es por esto que, para la industria aeronáutica, la optimización del proceso de taladrado y remachado es un objetivo prioritario, habiéndose propuesto diversas técnicas entre las que destaca el OWA (One Way Assembly) como método de ensamblaje ‘en un paso’ que garantice la calidad en todas las operaciones involucradas en el proceso ensamblaje, sin necesidad de realizar desemsamblajes que no aportan valor al producto final.
El grado de automatización del remachado en la industria aeronáutica varía desde la producción manual hasta la automatizada como se aprecia en la figura 1. Durante las diferentes etapas que se desarrollan en el proceso de remachado, los componentes a unir se mantienen fijos mediante utillajes específicos en su posición final. La unión de estos componentes de igual o diferente material constructivo se denominan ‘apilados’ o stacks que, cuando son de materiales disímiles también reciben el nombre de estructuras híbridas. En esa posición los apilados son taladrados, surgiendo una nueva problemática que se une a la dificultad ya existente para conseguir agujeros dentro de los estrictos rangos de tolerancia exigidos en los diferentes materiales por separado [6]. Entre la problemática mencionada destaca la dificultad de sujeción de los componentes, la aparición de vibraciones no deseadas trasmitidas a través de los utillajes y los defectos de fabricación inherentes a los procesos/materiales que aparecen en la intercara del apilado.
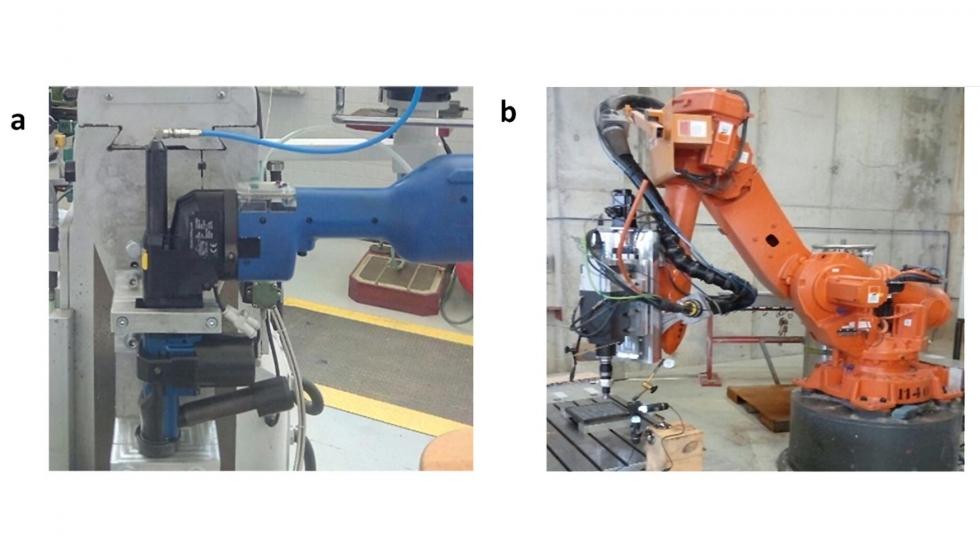
Con el fin de mejorar la productividad reduciendo los tiempos de mecanizado, se tratan de utilizar estrategias de taladrado en un solo paso (One Shot Drilling-OSD), evitando así el cambio de herramientas (brocas y escariadores) durante el taladrado de estructuras híbridas. Por el contrario, al estar mecanizando materiales disímiles, al tener propiedades diferentes como el coeficiente de dilatación, se obtienen resultados dispares entre los mismos, afectando principalmente a los diámetros. Es por esto, que surge la necesidad de optimizar las técnicas OSD.
Para su implementación, están siendo empleadas diferentes estrategias de taladrado con cambio de parámetros de corte en función del material a mecanizar, junto con el uso de avances interrumpidos o discontinuos, denominados comúnmente como ‘picoteos’ o ‘Peck-Drilling’, bien sea mediante programación CNC [7] o bien mediante el uso de portaherramientas específicos para el taladrado asistido por vibraciones [2]. Aunque el primer caso (CNC) es de inmediata aplicación, la dinámica de las máquinas imposibilita rápidas aceleraciones en desplazamientos tan cortos (< 1 mm), por lo que los sistemas tipo MITIS (gigura 2) ofrecen mejor resultado en términos de tiempos de ciclo, al ser el propio cono porta-herramientas el que incorpora las microvibraciones en un avance continuo guiado por CNC. En ambos casos, se consigue un mayor grado de fragmentabilidad de la viruta, minimizando los defectos producidos por virutas largas.
![Figura 2. Movimiento oscilatorio durante el taladrado asistido por vibraciones [2] Figura 2. Movimiento oscilatorio durante el taladrado asistido por vibraciones [2]](https://img.interempresas.net/fotos/1617089.jpeg)
Una vez finalizado el proceso de taladrado, habitualmente es necesaria la separación de los componentes, verificando la no existencia de virutas en la intercara y de defectos a la entrada o salida de los agujeros (rebabas, delaminaciones, astillamientos, etc). En caso de localizarse, ha de procederse a la ejecución de los retrabajos necesarios, así como operaciones de limpieza que garanticen la continuidad del material de forma previa a su re-ensamblaje definitivo, mediante la colocación de los elementos de unión definitiva de acuerdo a las normativas específicas de cada tipo de remache [8–11].
La problemática asociada a este tema ha generado gran interés industrial. La figura 3 muestra el número de publicaciones científicas que han abordado la temática del taladrado de apilados híbridos CFRP-Al y CFRP-Ti (CFRP, Carbon Fiber Reinforced Plastics), en la que se aprecia el interés que está resurgiendo en los últimos años.
![Figura 3. Número de publicaciones sobre taladrado de apilados híbridos según el portal Scopus [12] Figura 3. Número de publicaciones sobre taladrado de apilados híbridos según el portal Scopus [12]](https://img.interempresas.net/fotos/1617090.jpeg)
Figura 3. Número de publicaciones sobre taladrado de apilados híbridos según el portal Scopus [12].
Entre la problemática y defectología asociada al taladrado de los diferentes materiales, destaca especialmente el defecto de rebaba en las aleaciones metálicas y la delaminación en los materiales compuestos. Por un lado, la formación de rebabas es asociada a una serie de fracturas y deformaciones plásticas generadas en el material no mecanizado de la periferia del agujero tal como se muestra en la figura 4. Este defecto se produce tanto a la entrada como a la salida, siendo este último el que ocasiona mayores problemas. Esto es debido a que existe un frente de calor que se acumula delante de la broca, reblandeciendo localmente el material, lo que unido a los esfuerzos axiales producidos por la herramienta produce la deformación platica del material, formando una deformación de material no mecanizado o rebaba [2,13].
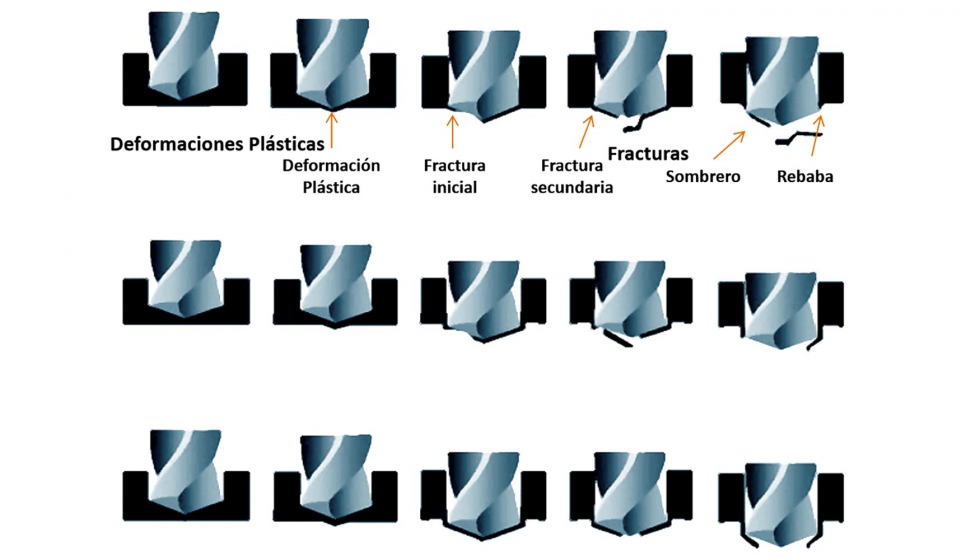
Por otro lado, la formación de la delaminación en CFRPs es debida a que las láminas del compuesto que conforman el material ofrecen una baja resistencia a la hora de retener la propagación de grietas (figura 5). La presencia de fuerzas axiales producidas durante el mecanizado provoca la separación de las capas del material. Como consecuencia, el daño originado en las capas del material provoca una reducción de la capacidad de carga soportada, traduciéndose en una disminución de las características y propiedades del material [2,14,15].
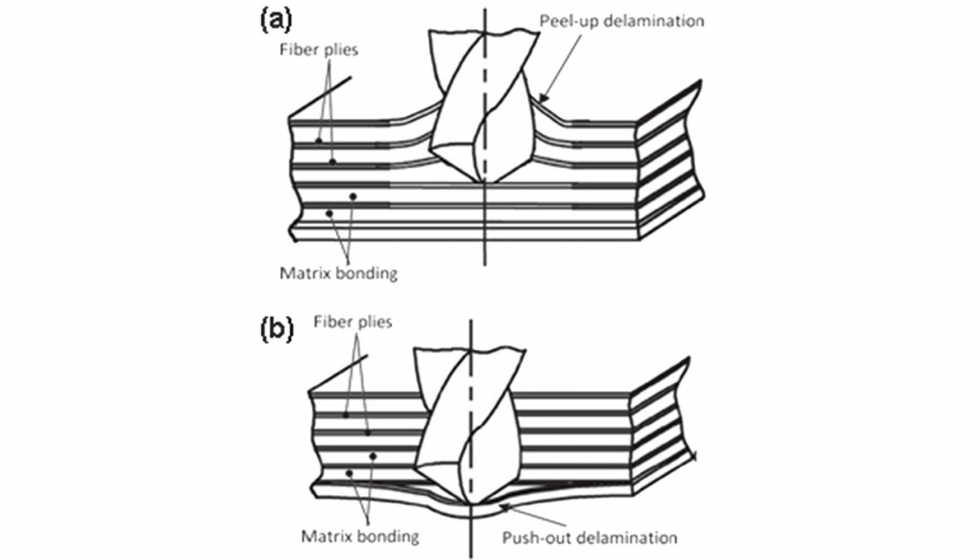
Figura 5. Generación de delaminaciones a la entrada (Break-In) y salida (Break-Out) del taladro.
Sin embargo, el principal reto consiste en el taladrado de estos materiales en forma de apilados. Al unir estos materiales —CFRP y aleaciones metálicas— en una estructura híbrida, la zona más crítica durante mecanizado se encuentra en la intercara de ambos. En este caso, aparecen nuevas problemáticas asociadas a la diferente conductividad térmica de los distintos materiales. En el caso de las aleaciones de Ti, puede producirse una concentración de calor en la intercara llegando a generar una degradación en la matriz del material compuesto, aumentando así el riesgo de delaminación (figura 6).
Con el fin de poder automatizar el remachado de materiales disimiles en forma de apilados y mejorar la productividad del proceso, es necesario minimizar la defectología comentada.
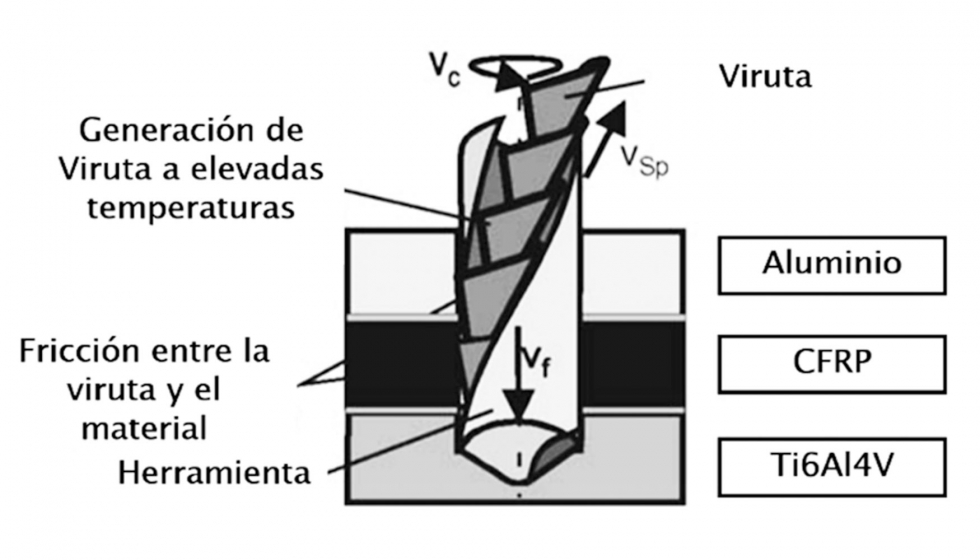
Surge así la combinación de estrategias OSD implementadas en técnicas OWA. Para ello se emplean equipos automáticos o semiautomáticas que combinan tecnologías como el MITIS para ser capaces de realizar el taladrado en un único paso, minimizando la viruta obtenida y reduciendo la rebaba generada. Como consecuencia, se puede conseguir evitar la posterior separación del apilado y, paralelamente, establecer un control sobre los diámetros generados en ambos materiales.
Por ello, las investigaciones actuales buscan el uso de estas técnicas juntos con la combinación de diferentes parámetros de corte que ofrezcan los mejores resultados por material.
Uso de Tecnologías Limpias en el proceso de mecanizado
Gran parte de las técnicas de taladrado empleadas en estructuras híbridas, precisan aún del uso de fluidos de corte para evitar y/o minimizar la generación de la defectología anteriormente comentada durante el proceso de taladrado. Sin embargo, el uso de fluidos de corte de base mineral, requieren de un tratamiento especial una vez han sido utilizados para eliminar los componentes tóxicos que alberga y cumplir con la legislación medio ambiental [16]. El uso de estos fluidos puede llegar unos sobrecostes del 16% al proceso de mecanizado [17], además de la necesidad del desmontaje del apilado para su limpieza, impidiendo así la automatización del proceso.
Desde el punto de vista energético, los fluidos de corte presentan beneficios como la lubricación y refrigeración del proceso de mecanizado, por un lado, reduciendo el coeficiente de fricción entre la herramienta y la pieza, y por otro, entre la herramienta y la viruta evacuada. Además, favorece la evacuación del calor que se produce en la zona de corte, contribuye a la retirada de la viruta generada y mejora la vida de la herramienta [16,18].
No obstante, existe una tendencia mundial a minimizar o eliminar el uso de los fluidos tradicionales en las operaciones de mecanizado, apostando por técnicas más comprometidas con el medioambiente y que permitan la automatización del proceso de taladrado y el uso de técnicas OWA. La tendencia es la utilización de técnicas NDM (Near to Dry Machining), o directamente el mecanizado en seco, también llamado mecanizado verde (Green Machining). Sin embargo, esta última técnica da lugar a condiciones de corte muy agresivas desde el punto de vista de esfuerzos mecánicos y térmicos, especialmente para las aleaciones metálicas exóticas ampliamente utilizadas en el sector aeroespacial. La aparición de programas de investigación como Horizonte 2020 y CLEAN SKY de la UE, entre cuyos objetivos figuran el desarrollo de tecnologías innovadoras para reducir el impacto medioambiental del transporte aéreo y mejorar la sostenibilidad de los actuales procesos de fabricación, han tenido un importante impacto en el avance de estas técnicas alternativas.
Debido a las altas temperaturas que se generan durante el proceso de taladrado, (especialmente en las aleaciones de titanio), se deriva el interés hacia procesos que sean respetuosos con el medio ambiente, mantengan las tolerancias mínimas de calidad y permitan la implementación de técnicas OWA. Es en este punto donde el estudio de nuevas técnicas alternativas se hace imprescindible [19,20].
Se enumeran a continuación las más relevantes dentro de la industria aeroespacial [20,21]:
- Lubricantes sólidos. Donde se usan herramientas con recubrimientos laminares como el Disulfuro de Molibdeno (MoS2) o grafito para disminuir el rozamiento entre la viruta y la herramienta. En este caso tanto la temperatura de corte como las fuerzas se ven reducidas, sin embargo, al suprimirse cualquier fuente de caudal líquido o gaseoso se pierde la función de refrigeración y evacuación de la viruta.
- Mecanizado MQL. Se proyectan sobre la herramienta micropartículas de aceite, generalmente biodegradable. Gracias a esta técnica se consigue reducir el uso de fluidos de corte de entre 10-100 ml/h. Se aumenta la higiene industrial y la viruta aparece prácticamente limpia. Sin embargo, el proceso se ve penalizado en cuanto a la refrigeración, por lo que en materiales de baja maquinabilidad esta técnica es ineficiente. Además, las partículas pueden llegar a volatilizarse antes de contactar con la zona de corte.
- Mecanizado con Cold-Gun. Esta técnica se basa en el uso de aire frío como fluido de corte. Mediante un tubo Vórtex de Ranque-Hilsch, por cuyo interior se centrifuga el aire comprimido, se logra la separación de la fracción fría del aire, proyectándose la misma hacia la zona de corte, llegando a disminuir la temperatura del aire de entrada en 50 °C.
- Mecanizado criogénico. Consiste en asistir al proceso de mecanizado con la proyección de gases licuados. El uso de esta tecnología disminuye drásticamente la temperatura de corte y se obtienen piezas totalmente limpias. Los resultados para materiales de baja maquinabilidad son similares o incluso superiores al mecanizado con taladrinas, ya que el desgaste producido por el efecto térmico se reduce drásticamente.
Entre las técnicas de refrigeración/lubricación comentadas, el estudio del mecanizado criogénico es una línea de investigación iniciada hace algunos años donde se emplean gases como el nitrógeno y dióxido de carbono, ver figura 7.
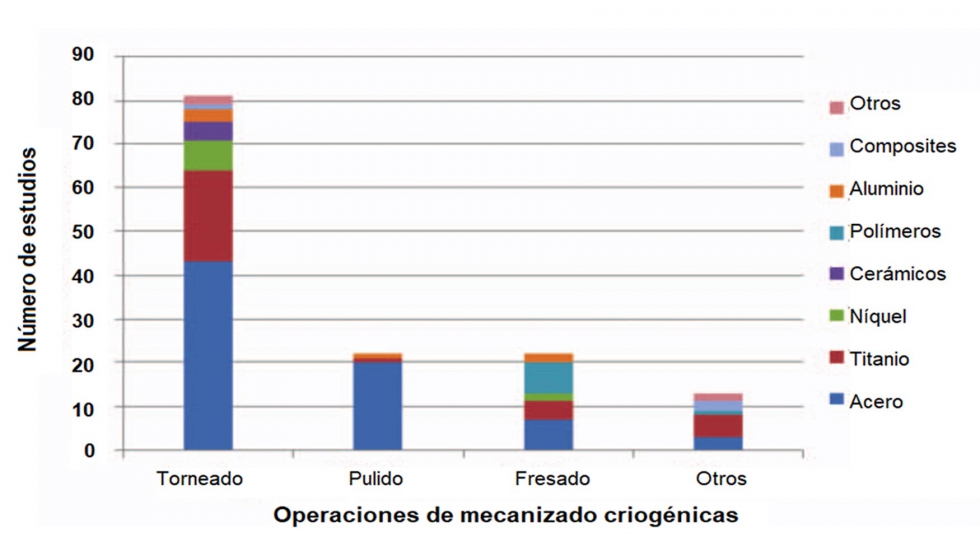
En el caso del nitrógeno, éste se proyecta en la zona de corte a una temperatura de -198 °C, el nitrógeno absorbe el calor generado durante el mecanizado y posteriormente se evapora, por lo que no existe un impacto ambiental adverso. Sin embargo, un sobre-enfriamiento de la pieza puede provocar un aumento de las fuerzas de corte junto con la fragilización de la pieza y de la herramienta. En la aplicación del dióxido de carbono líquido las temperaturas con las que se trabaja son siempre inferiores a -73 °C [22].
Las investigaciones llevadas a cabo en los últimos años se basan en las estrategias de mecanizado criogénico en su aplicación a las operaciones de corte. Estas estrategias se pueden dividir en una pre-refrigeración de la pieza de trabajo, refrigeración indirecta de la herramienta y la refrigeración directa de la herramienta mediante la inyección del fluido sobre cara de desprendimiento e incidencia. Los mejores resultados se han obtenido a bajas velocidades de corte, ya que la capacidad de refrigeración decrece con el incremento de la velocidad de corte. Esto es debido a que altas velocidades de corte, el contacto entre la herramienta y la viruta tiende a ser plástico, obstaculizando la penetración del fluido criogénico en la cara de desprendimiento de la herramienta [36,38].
Entre las ventajas del mecanizado criogénico se destacan la gran reducción de temperatura en la cara de desprendimiento (herramienta-viruta), la obtención de piezas sin contaminantes de fluidos de corte, la reducción del desgaste de herramienta, alta tasa de producción, calidad final del proceso, ahorro energético, viruta seca y limpia (reciclable), además del ahorro en cuanto a la gestión de taladrinas.
Por todo ello, la refrigeración criogénica es considerada limpia, segura y respetuosa con el medio ambiente, además de incrementar la productividad del proceso de taladrado al no tener que separar los materiales apilados al no generar residuos sobre la pieza. No obstante, la principal desventaja que presenta es el coste adicional del equipo y los costes de adquisición de los refrigerantes LCO2 y LN2.
Estudio comparativo entre el taladrado en seco y refrigerado mediante CO2 de materiales estratégicos para el sector aeronáutico
En este apartado se presentan resultados preliminares obtenidos en el marco del proyecto ‘Investigación en tecnologías de proyección acoplada de fluidos criogénicos para la mejora de maquinabilidad de materiales aeronáuticos’ (Criomec) con el código EXP 00082035/IDI-20151204, promovido por la empresa Hergome y financiado por el CDTI, y en el que han participado la Universidad de Cádiz y la Universidad de Vigo.
Como se ha expuesto anteriormente, la formación de rebabas en aleaciones metálicas, junto con la delaminación en materiales CFRP y la necesidad de eliminar los fluidos de cortes y suciedad atrapada en la intercara de la estructura híbrida, son los factores que determinan la necesidad de separar el apilado para verificar y corregir de los defectos, impidiendo la aplicación de técnicas OWA y por tanto la automatización del proceso de montaje.
En el presente estudio, se ha analizado la influencia de la refrigeración criogénica de CO2 sobre la altura de la rebaba en las aleaciones metálicas, delaminación para los materiales CFRP, y la desviación de diametral para ambos casos. Los ensayos se han llevado a cabo en un equipo CNC realizando tandas de 200 taladros (figura 8).
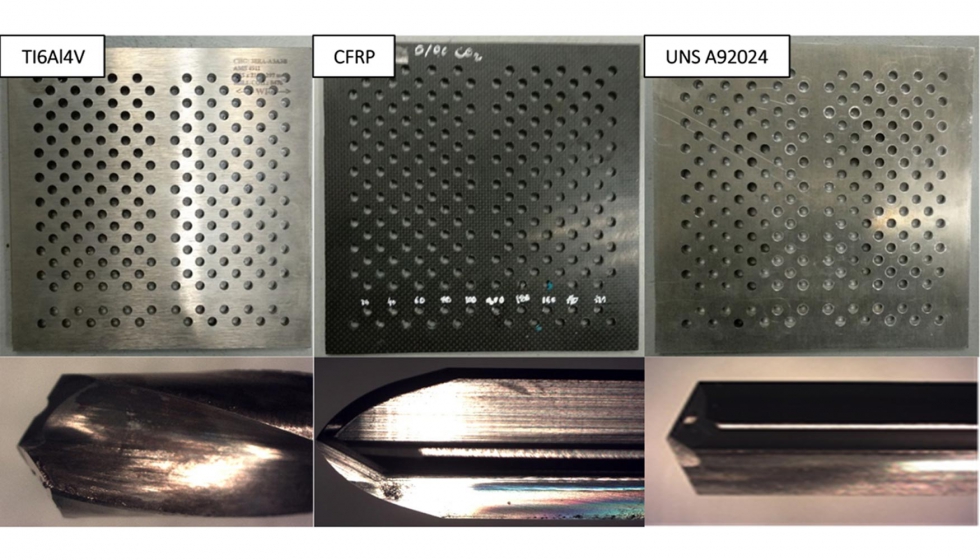
En el caso de utilización de fluido criogénico, éste es impulsado por el interior de la herramienta (figura 9). Las aleaciones metálicas empleadas han sido: aleación de aluminio UNS A97075 (Al-Zn), y aleación de titanio UNS R56400, mientras que el material compuesto es CFRP con una configuración 0-90-45. En ambos casos (con refrigeración y sin refrigeración) se emplearon los mismos parámetros de corte, siendo estos los que se muestran en la siguiente tabla:
|
Velocidad de avance (mm/min) |
Velocidad de corte (m/min) |
UNS A97075 |
960 |
122 |
UNS R56400 |
194 |
39 |
CFRP 0-90-45 |
64 |
33 |
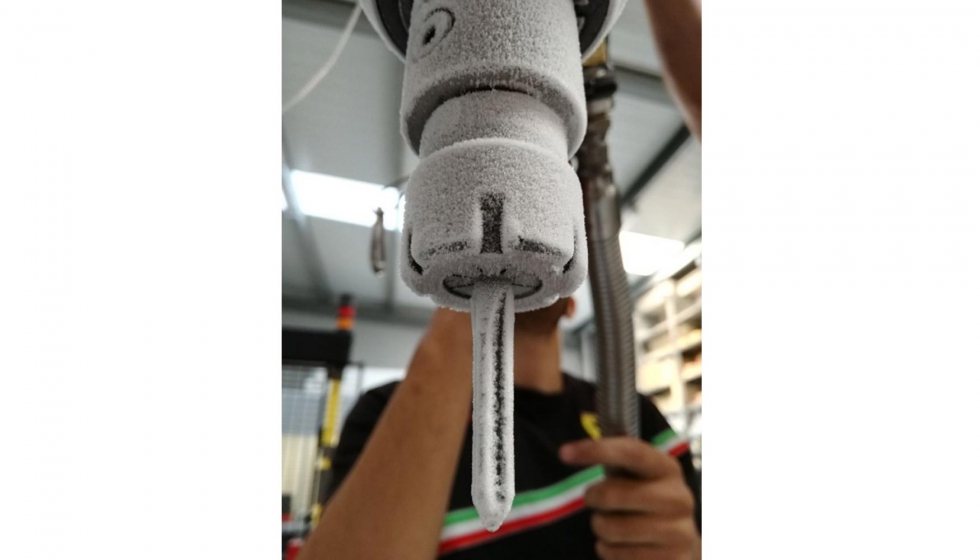
Figura 9. Apariencia exterior de la herramienta debido a la refrigeración interna mediante CO2.
Los resultados de los ensayos se han comparado con los obtenidos en condiciones de mecanizado en seco. En la figura 10 se muestran los valores de la altura de rebaba obtenidos para ambos casos.
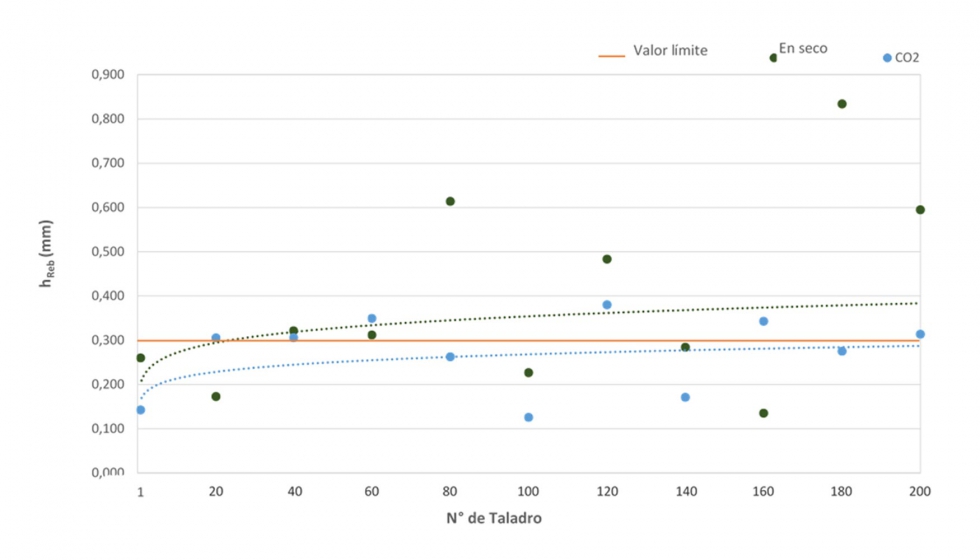
En los resultados obtenidos en el taladrado de la aleación de aluminio, a pesar de que son dispersos, se aprecia que con la refrigeración criogénica con CO2, estos valores de altura de rebaba son ligeramente inferiores y más estables que cuando se realiza el proceso en ausencia de refrigerante. Esto puede ser consecuencia de un valor de temperatura más estable durante el proceso de taladrado, por lo que no se favorece la plasticidad del material. Por lo tanto, puede verse que la aplicación de esta técnica de refrigeración tiene un efecto positivo en el taladrado de este tipo de materiales reduciendo y estabilizando la altura de la rebaba.
Con respecto a la evaluación de los diámetros, los resultados se exponen en la figura 11.
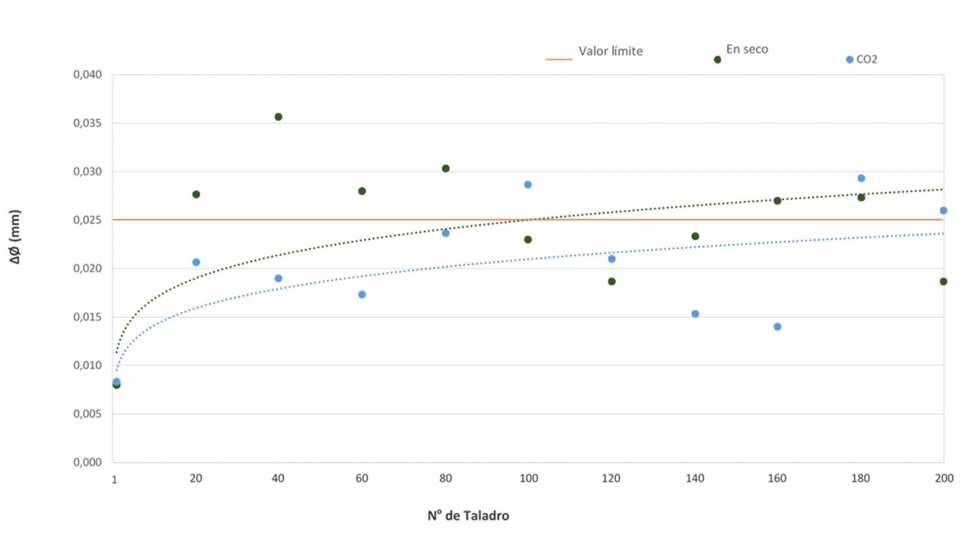
En ambos casos de estudio, los valores presentan tendencias similares con fluctuaciones que no llegan a estabilizarse con el número de taladros realizados. La incorporación de CO2 parece mantener las variaciones producidas en el diámetro de los agujeros (valores medios de 20-25 µm) y, al mismo tiempo, ofrece los valores más cercanos al diámetro nominal.
De igual manera, los resultados obtenidos mediante la refrigeración por CO2 se mantienen en casi su totalidad por debajo de la tolerancia establecida por el sector aeronáutico.
Por otro lado, debido a las características que posee el titanio, es muy inusual que se mecanice en ausencia de lubricación. Por ese motivo, en el taladrado de dicha aleación los ensayos se han realizado con lubricación por inmersión (taladrina), comparándolo con los resultados obtenidos utilizando lubricación con CO2. En ambos casos se utilizaron los mismos parámetros de corte, siendo estos siendo estos una velocidad de avance 194 mm/min y una velocidad de corte 39 m/min.
En la figura 12 se muestran los resultados obtenidos de altura de rebaba en ambos casos.
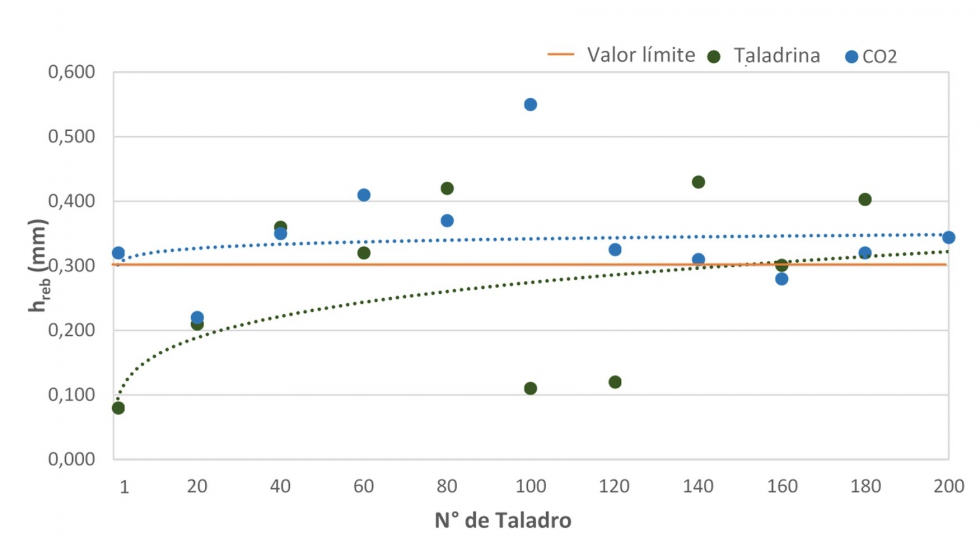
De igual manera, en el caso de la aleación de titanio, a pesar de la dispersión de datos la lubricación tradicional muestra una tendencia al crecimiento con el número de taladros, aunque con los resultados absolutos más bajos (0,1 mm). Esto puede manifestar la evolución geométrica de la herramienta durante el mecanizado.
En el caso de aplicación de CO2 como fluido refrigerante, se aprecia una estabilización del proceso de formación de rebaba (valores medios de 0,3 mm).
Por lo tanto, puede observarse cómo la utilización de CO2 como fluido de corte estabiliza el comportamiento térmico del proceso, aproximándose a los valores obtenidos con la utilización de taladrinas al aumentar el número de taladros. No obstante, la principal ventaja es que se elimina la utilización de lubricantes convencionales permitiendo el taladrado de este tipo de materiales con similares resultados.
Paralelamente, en la figura 13 se muestran los diámetros obtenidos en ambos casos de estudio para el taladrado de la aleación Ti6Al4V.
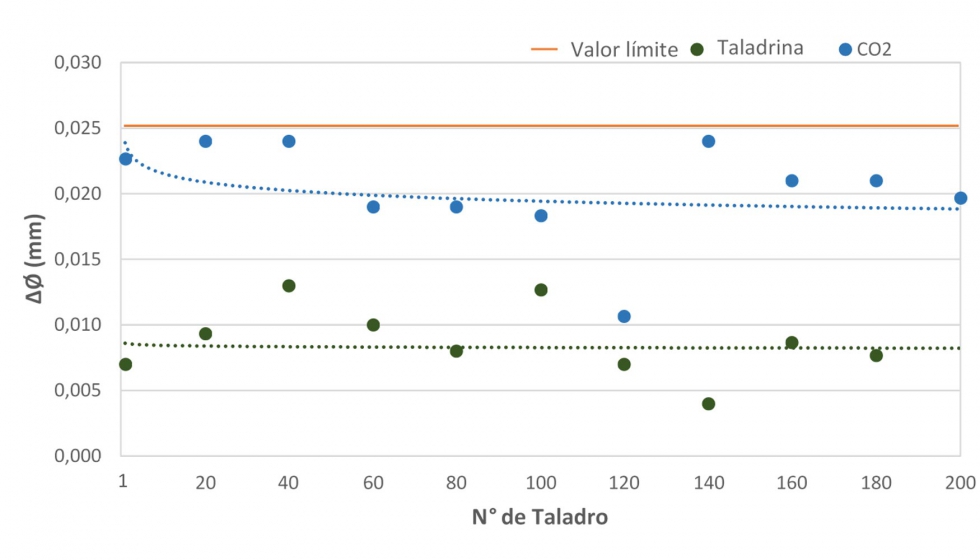
Los resultados parecen ser muy heterogéneos, aunque presentan tendencias similares en todos los casos a la estabilización.
Al contrario de lo que ocurre en el taladrado de la aleación de aluminio, se aprecia que el uso de refrigeración mediante CO2 empeora los resultados obtenidos en comparación con la lubricación tradicional. Sin embargo, en ambos casos de estudio, todos los valores están por debajo del límite impuesto, lo que indicaría que serían aptos una posterior etapa de remachado.
Por su parte, la lubricación tradicional parece mostrar los mejores valores en este sentido (valores medios por debajo de 10 µm).
En última instancia se ha evaluado la delaminación generada a la salida (Break Out) durante el taladrado de CFRP, así como los diámetros obtenidos.
Para determinar el daño causado por la delaminación, se está evaluando el área afectada por la misma en comparación con el área nominal del taladrado generado [23] tal como se muestra en la figura 14. De esta manera, se calcula un factor de delaminación tal como se muestra a continuación:

En la figura 15 se exponen los resultados obtenidos correspondientes a la delaminación generada en porcentaje para las condiciones de mecanizado en seco y refrigerado mediante CO2. En ambos casos se utilizaron los mismos parámetros de corte, siendo estos siendo estos una velocidad de avance 64 mm/min y una velocidad de corte 33 m/min.
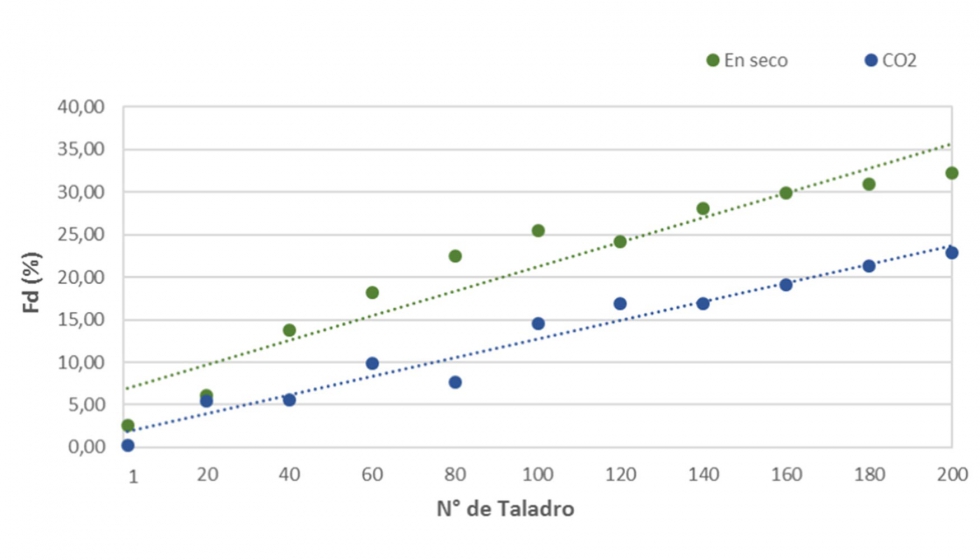
Se aprecia una tendencia lineal creciente en los dos casos estudiados. Esto es debido al continuo desgaste al que se ven sometidos los filos de corte de la herramienta, donde en los instantes iniciales la delaminación generada es muy próxima en ambos casos.
Si bien en ambas condiciones el área de la delaminación generada aumenta considerablemente, es notable la reducción existente al aplicar el CO2 como refrigerante del proceso, llegando a reducir la delaminación en casi un 10%. Esto puede ser debido a que, al refrigerar la herramienta, esta sufre un desgaste menor lo que reduciría los esfuerzos necesarios para mecanizar el material y, por tanto, reducir la delaminación generada a la salida de la herramienta.
De esta manera se observa la funcionalidad del uso de tecnologías limpias como la refrigeración criogénica mediante CO2 al evitar usar fluidos de corte durante el proceso y, además, reducir la delaminación generada pudiendo evitar o minimizar la separación del material al ser implementado en forma de apilado.
Finalmente, se exponen los resultados correspondientes al taladrado del material compuesto para ambos casos de estudio (figura 16).
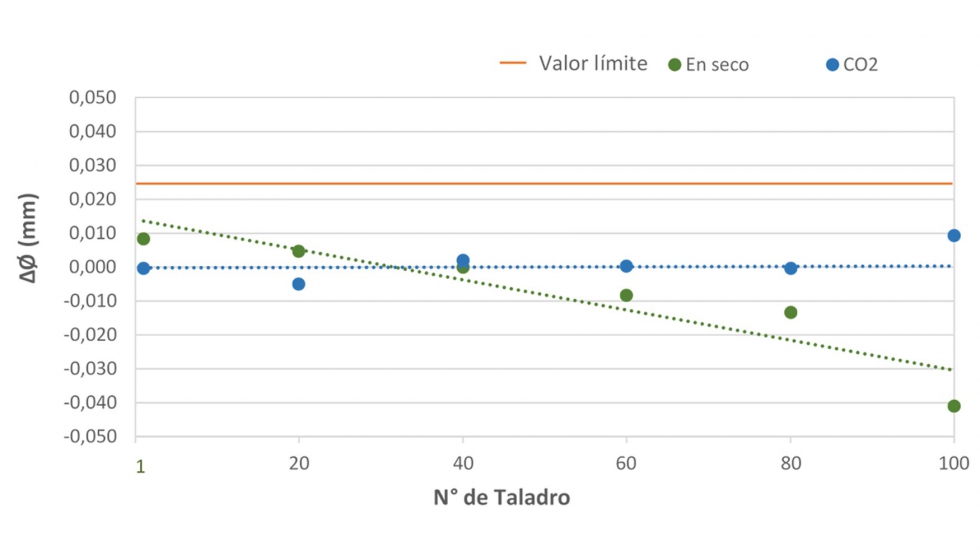
Los resultados obtenidos presentan unos valores muy cercanos entre ellos con tendencias casi estables.
Mientras que para el taladrado en seco la tendencia es ligeramente decreciente destaca especialmente que, la refrigeración por CO2 ofrece una tendencia constante casi lineal con unas desviaciones mínimas con respecto al valor nominal del taladro.
De esta forma se aprecia que, de los tres materiales mecanizados, el uso de refrigeración criogénica ofrece los mejores resultados en diámetros en el mecanizado de CFRP.
Conclusiones
La búsqueda de la automatización del proceso del remachado dentro del sector aeronáutico ha creado la necesidad de implementar técnicas OWA con el fin de garantizar la calidad final en el proceso de taladrado y evitar la separación del apilado.
De esta forma se ha buscado aumentar la productividad del proceso mediante diversas alternativas que eviten o disminuyan la defectología ocasionada durante el taladrado de materiales disímiles en forma de apilado.
Dentro de dichas alternativas destaca la implementación de tecnologías limpias que sustituyan a los fluidos de corte utilizados hasta el momento y que, junto con la defectología ocasionada, obligan a la separación y posterior limpieza de la intercara del apilado.
Se ha realizado un caso de estudio donde se han taladrado materiales estratégicos para el sector aeronáutico en dos condiciones: seco y refrigeradas mediante CO2.
Destaca como la implementación de la refrigeración criogénica parece que estabiliza la formación de rebabas en el taladrado de las aleaciones metálicas, llegando a reducirlas en comparación con el mecanizado en seco y, al mismo tiempo, disminuye considerablemente la delaminación generada a la salida del material compuesto. Esto podría indicar al mismo tiempo la reducción del desgaste ocasionado en la herramienta, dando lugar a una vida útil mayor al ser refrigerada mediante CO2.
Al mismo tiempo, si bien ofrece sus peores resultados en el taladrado de la aleación Ti6Al4V, en general, el uso de refrigeración mediante CO2 ofrece unos valores correspondientes a los diámetros con tendencias muy estables. Al mismo tiempo, dichos resultados están casi en su totalidad por debajo del límite establecido por el sector aeronáutico, favoreciendo de esta forma su aplicación para el OSD y conseguir, por tanto, el remachado automático mediante técnicas OWA.
Referencias
[1] H. Kagermann, W. Wahlster. J. Helbig, Recommendations for implementing the strategic initiative INDUSTRIE 4.0, Final Rep. Ind. 4.0 W.G., 2013.
[2] S.R. Fernández Vidal, Analysis of Vibration-Aided Dry Drilling of light alloys hybrid structures (in Spanish). PhD Thesis, University of Cadiz, Cadiz, Spain, 2016.
[3] C.-Y. Wang, Y.-H. Chen, Q.-L. An, X.-J. Cai, W.-W. Ming, M. Chen, Drilling temperature and hole quality in drilling of CFRP/aluminum stacks using diamond coated drill, Int. J. Precis. Eng. Manuf. 16 (2015) 1689–1697.
[4] K. Zhang, Z. Yang, Y. Li, A method for predicting the curing residual stress for CFRP/Al adhesive single-lap joints, Int. J. Adhes. Adhes. 46 (2013) 7–13.
[5] R. Zitoune, V. Krishnaraj, F. Collombet, Study of drilling of composite material and aluminium stack, Compos. Struct. 92 (2010) 1246–1255.
[6] Desarrollos en la automatización del taladrado de estructuras aeronáuticas, (n.d.). https://www.interempresas.net/Aeronautica/Articulos/143203-Desarrollos-en-la-automatizacion-del-taladrado-de-estructuras-aeronauticas.html (accessed January 2, 2018).
[7] Taladrado con interrupciones de avance: CoroDrill Delta-C® y Coromant Delta®, (n.d.). https://www.sandvik.coromant.com/es-es/knowledge/drilling/wear-and-troubleshooting/chip_evacuation/pages/peck-drilling-–-corodrill-delta-c®-and-coromant-delta®.aspx (accessed January 2, 2018).
[8] I.S. Shyha, S.L. Soo, D.K. Aspinwall, S. Bradley, R. Perry, P. Harden, S. Dawson, Hole quality assessment following drilling of metallic-composite stacks, Int. J. Mach. Tools Manuf. 51 (2011) 569–578.
[9] Y. Wei, Q. An, W. Ming, M. Chen, Effect of drilling parameters and tool geometry on drilling performance in drilling carbon fiber-reinforced plastic/titanium alloy stacks, Adv. Mech. Eng. 8 (2016) 1–16.
[10] J. Xu, M. El Mansori, Experimental study on drilling mechanisms and strategies of hybrid CFRP/Ti stacks, Compos. Struct. 157 (2016) 461–482.
[11] R. Zitoune, V. Krishnaraj, F. Collombet, S. Le Roux, Experimental and numerical analysis on drilling of carbon fibre reinforced plastic and aluminium stacks, Compos. Struct. 146 (2016) 148–158.
[12] Scopus, (n.d.). https://www.scopus.com/freelookup/form/author.uri (accessed January 2, 2018).
[13] D. a. Dornfeld, J.S. Kim, H. Dechow, J. Hewson, L.J. Chen, Drilling Burr Formation in Titanium Alloy, Ti-6AI-4V, CIRP Ann. - Manuf. Technol. 48 (1999) 73–76.
[14] H. Cheng, K. Zhang, N. Wang, B. Luo, Q. Meng, A novel six-state cutting force model for drilling-countersinking machining process of CFRP-Al stacks, Int. J. Adv. Manuf. Technol. 89 (2017) 2063–2076.
[15] D. Liu, Y. Tang, W.L. Cong, A review of mechanical drilling for composite laminates, Compos. Struct. 94 (2012) 1265–1279.
[16] S. Debnath, M.M. Reddy, Q.S. Yi, Environmental friendly cutting fluids and cooling techniques in machining: A review, J. Clean. Prod. 83 (2014) 33–47.
[17] S. Paul, A.B. Chattopadhyay, Environmentally conscious machining and grinding with cryogenic cooling, Mach. Sci. Technol. 10 (2006) 87–131.
[18] Refrigeración criogénica para operaciones de mecanizado de alto valor añadido, (n.d.). http://www.interempresas.net/MetalMecanica/Articulos/149215-Refrigeracion-criogenica-para-operaciones-de-mecanizado-de-alto-valor-anadido.html (accessed January 2, 2018).
[19] F. Pusavec, A. Deshpande, S. Yang, R. M’Saoubi, J. Kopac, O.W. Dillon, I.S. Jawahir, Sustainable machining of high temperature Nickel alloy - Inconel 718: Part 1 - Predictive performance models, J. Clean. Prod. 81 (2014) 255–269.
[20] O.M. Pereira, Reduction of the environmental impact of machining processes through the combination of MQL micropulverization and cryogenic refrigeration (in Spanish). PhD Thesis, University of Leon, Leon, Spain, 2017.
[21] J.P. Davim, ed., Green Manufacturing Processes and Systems, 2013.
[22] A. Shokrani, V. Dhokia, P. Muñoz-Escalona, S.T. Newman, State-of-the-art cryogenic machining and processing, Int. J. Comput. Integr. Manuf. 26 (2013) 616–648.
[23] P. Mayuet, A. Gallo, A. Portal, P. Arroyo, M. Álvarez, M. Marcos, Evaluación de Defectos B - IN / B - OUT en el Taladrado en Seco de CFRP a partir del Análisis de Imagen de Áreas Dañadas, (2013).
La criogenia en el taladrado de stacks Ti6Al4V-CFRP. Caso de éxito
Uno de los retos que se enfrentan en el sector aeronáutico es la reducción de peso de las estructuras de las aeronaves; disminuyendo de ese modo el consumo de combustible durante los vuelos. Para ello, se utilizan materiales compuestos —también conocidos como composites— que están formados por diversos materiales (matriz y refuerzo). De este modo, presentan propiedades mecánicas muy superiores a las que presentarían por separado. Esta solución cubre la necesidad de fabricar estructuras más ligeras, y reducir así el peso de las aeronaves. De hecho, actualmente los composites suponen entre un 45 y 55% del peso total de las aeronaves.
Uno de los composites más utilizados en la industria aeronáutica está formado por una matriz de Ti6Al4V reforzada con fibra de carbono (CFRP). Este material satisface los requisitos exigidos por los ingenieros debido a sus excelentes propiedades mecánicas. Sin embargo, a la hora de ser mecanizado - más concretamente taladrado - presenta una alta temperatura de corte, ya que la fibra de carbono debe ser mecanizada en seco, lo que dificulta su procesamiento. Además, como consecuencia de la ausencia de fluidos de corte, se producen adhesiones de titanio en el filo de la broca – reduciendo notablemente su vida útil - y se llega a poner en tela de juicio la integridad superficial de la pieza.
Por ello, en el taller mecánico de la UPV/EHU se han realizado ensayos de taladrado en stacks formados por Ti6Al4V-CFRP utilizando la refrigeración criogénica con CO2 por el interior de la broca, con el fin de aumentar la productividad en este proceso que actualmente debe ser realizado en seco. Concretamente se han utilizado brocas de metal duro recubiertas de diamante. En la figura adjunta se muestran los resultados obtenidos. Se puede apreciar como la utilización de la refrigeración criogénica implica una disminución de la adhesión del titanio en el filo de la herramienta y eliminación del daño térmico de la fibra carbono para un mismo número de agujeros. Alcanzando así lo que se conoce como ‘Fabricación ECO2’.
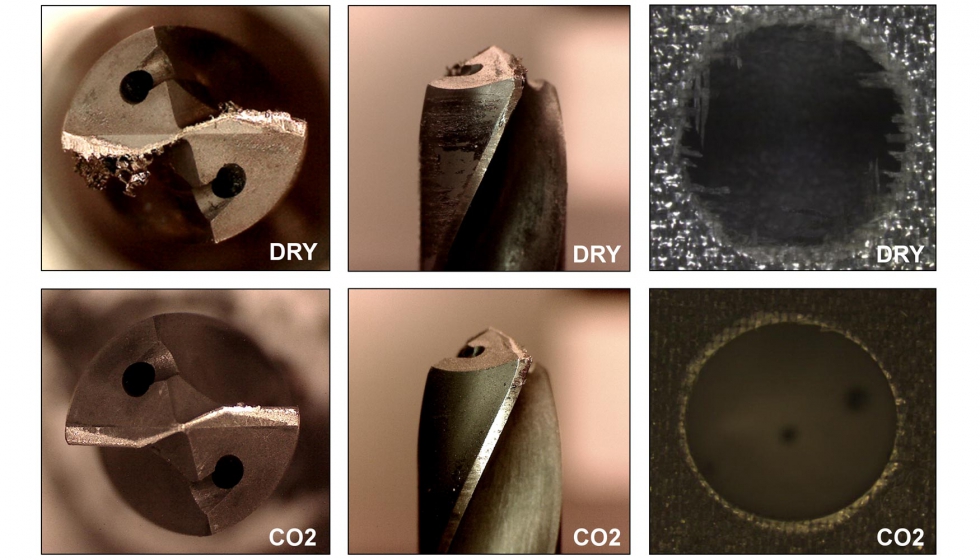