Aplicación de aleaciones de magnesio para fabricación de moldes
El magnesio es el más ligero entre los metales para usos estructurales. En el caso de la automoción permite una disminución del peso total del automóvil del 10 por ciento y un ahorro de combustible de entre el 20 y el 30 por ciento.
Entre otras ventajas destacan su excelente rigidez y resistencia específica, una alta conductividad eléctrica y térmica y unas inmejorables propiedades de protección frente a las interferencias electromagnéticas. También se caracteriza por una excelente tolerancia en las dimensiones finales de las piezas, permite obtener piezas de pequeño espesor (hasta Ø pared= 2 mm), un buen acabado de las piezas, es totalmente reciclable, los costes son más bajos en relación a los polímeros y es fácil de mecanizar.
Elementos de aleación
• Elementos que afectan activamente al caldo. Los elementos no requieren una gran solubilidad en el magnesio líquido Be (reduce la oxidación del caldo), Mn (ayuda a rebajar el contenido de Fe y así mejorar el comportamiento frente a ala corrosión de la aleación).
• Elementos que modifican la microestructura. Los elementos requieren una cierta solubilidad en el magnesio líquido. Algunos elementos pueden afectar a la colabilidad de la aleación. Interesantes para las aleaciones comerciales Al, Ce, Cu, La, Li, Mn, Nd, Ag, Th, Y, Zn, Zr.
Técnicas de moldeo
Las técnicas de procesado de material son diversas: moldeo en arena, moldeo a la cera perdida, moldeo en coquilla, moldeo por inyección (die casting) y moldeo tixotrópico (thixomolding).
Moldeo en arena
Se crea un molde compactando arena de moldeo en torno a una replica de la pieza a fabricar. Asimismo, requiere aditivos tanto para eliminar la humedad del molde de arena como para evitar reacciones entre la aleación y el molde de arena.
Entre las ventajas destaca que es una técnica relativamente económica, permite además producir piezas de gran tamaño y formas complejas y se puede aplicar a la inmensa mayoría de las aleaciones de magnesio.
Por otro lado, también tiene desventajas ya que, las tolerancias del producto final no son buenas, por lo que suelen requerir de un pulido o mecanizado de la superficie, ofrece una baja productividad en relación con otras técnicas de moldeo y el molde se destruye para recuperar la pieza.
Moldeo a la cera pérdida
Se trata de una técnica similar el moldeo en arena, si bien la fabricación del molde es mucho más compleja.
Esta técnica permite unas alta velocidades de producción, la fabricación de formas complejas, ofrece un excelente acabado superficial y se puede aplicar a la inmensa mayoría de las aleaciones del magnesio.
Contrariamente, se trata de procesos largos, que requieren un equipamiento caro y que generalmente requieren del uso posterior de técnicas de endurecimiento.
Moldeo en coquilla
En esta técnica, el caldo se vierte sobre un molde metálico, generalmente de acero o cobre.
Entre las ventajas de utilizar esta técnica destaca que permite altas velocidades de producción, y excelente acabado superficial, microestructuras más finas que la resultante del moldeo por arena o la cera pérdida y se puede aplicar a la inmensa mayoría de las aleaciones de magnesio excepto a ZK61A.
Sin embargo, las desventajas son claras: control de recubrimiento utilizado para alargar la vida de la coquilla y las limitaciones en la geometría de las piezas que pueden ser fabricados.
El proceso de fundición a presión es la inyección a alta presión en un molde (o herramienta) de acero, de una aleación de metal fundido que solidifica rápidamente (de milisegundos a unos pocos segundos) para fabricar un componente en su forma final, que es automáticamente extraído. Tiene numerosas ventajas. Y es que se trata de un proceso de producción rentable de grandes tiradas de componentes metálicos de tolerancias ajustadas y forma final. Ofrece la ventaja de una calidad y reproducibilidad mejoradas, a menudo a costos inferiores si se compara con otros procesos. Asimismo, el periodo de vida útil del molde es muy largo, se pueden obtener piezas con paredes de mejor espesor que las obtenidas por otros métodos de fundición y las propiedades mecánicas de las piezas son mejores a las obtenidas utilizando otros métodos de colada.
Moldeo por inyección en cámara caliente
El moldeo por inyección en cámara caliente se aplica a aquellas aleaciones que no atacan o erosionan al crisol donde se contiene el calor fundido.
Gracias a esta técnica se consigue un control preciso de la temperatura del metal, que mejora la fluidez, y permite que las presiones de inyecciones sean menores, lo que somete a los equipos a menores esfuerzos. Una mejor fluidez proporciona un mejor llenado de la cavidad, produce piezas más compactas y permite paredes de menor espesor.
El cilindro sumergido en la colada que se llena automáticamente, acorta el tiempo de ciclo y facilita el control de la temperatura del metal. Además, no se produce enfriamiento de la carga como puede ocurrir cuando se transfiere metal fundido al cilindro de la colada de una máquina de cámara fría. El metal fundido es sometido a una menor oxidación.
En cuanto a las desventajas, al emplearse presiones de inyección y velocidades más bajas, las piezas fundidas pueden ser menos compactas y los costos de mantenimiento son mayores.
Moldeo por inyección en cámara fría
La fundición a precisión en cámara fría difiere de la cámara caliente en cuanto a que el sistema de inyección de la primera no se sumerge en el material fundido. En su lugar, la carga de metal fundido (más material del que se necesita ara fundir la pieza) se transporta, mediante una cuchara de colada, del crisol a un contenedor donde un émbolo accionado hidráulicamente empuja al metal hacia el interior del molde. El material adicional se utilizar para introducir mayor cantidad de metal fundido en la cavidad del molde con el objetivo de compensar la contracción que se produce durante la solidificación.
Las ventajas del moldeo por inyección en cámara fría son varias, teniendo en cuenta que ciertas aleaciones de magnesio pueden ser procesadas solamente en cámara fría, que requiere mayores presiones y velocidades de inyección que permiten producir piezas más compactas y que los costes de mantenimiento son menores.
Por otro lado, los ciclos son más largos, hay un menor control sobre la temperatura del metal, menor fluidez y menos posibilidades de producir piezas con paredes de poco espesor. Asimismo la carga se enfría antes de la inyección y el metal fundido está expuesto a la oxidación.
Moldeo tixotrópico (Thixomolding)
Se basa en el principio de que las aleaciones de Mg, Al y Zn, se encuentran en estado semisólido entre las temperaturas de liquidus y solidus. El cizallado del metal semi sólido, mediante una fuerte agitación, genera una estructura tixotrópica que permite moldear el material utilizando un proceso similar al moldeo por inyección de plásticos.
Esta técnica aumenta la resistencia mecánica del material y de la ductibilidad; la presencia de una fracción del material en estado sólido disminuye la contracción que se experimenta durante la solidificación del líquido y una reducción de la porosidad hasta de un 50 por ciento. Las piezas quedan libres de inclusiones y óxidos.
Squeeze casting o forja en estado líquido
Es una combinación de procesos de colada y forja. El metal fundido es vertido sobre la mitad de una matriz precalentada. Cuando el caldo empieza a solidificar se cierra con la otra mitad de la matriz y se aplica una presión durante el proceso. La presión aplicada es mucho menor que en un proceso convencional de forja. La porosidad es baja y las propiedades mecánicas aumentan.
Otras técnicas de procesado
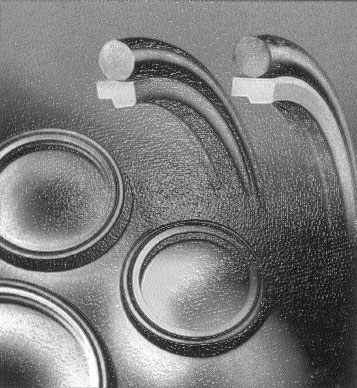
También existen otros tratamientos termomecánicos (forja, extrusión, laminación, etc.), conformado superplástico, mecanizado o pulvimetalurgia.
El magnesio en el Cenim
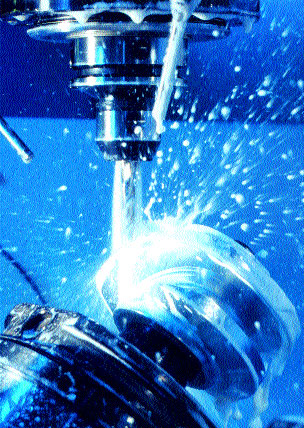
Se trata de uno de los escasos centros en España en los que se estudia el magnesio para aplicaciones estructurales.
El grupo Manoeq se encarga del desarrollo de nuevas aleaciones de magnesio estructurales y para almacenamiento de H2; mejora de las propiedades mecánicas a través del control de procesado, Pulvimetalurgia y materiales compuestos.
Mientras, el grupo Promeco se dedica a la deformación severa de aleaciones comercial y mecanismos de deformación.
Al:
Aumenta la resistencia mecánica
(Al) > 6% at Aleaciones envejecibles
Máxima ductibilidad y resistencia mecánica cuando (AL) = 6% at
Ca:
Se añade en bajas cantidades. Aumenta la resistencia mecánica
Cu:
Mejora la fluencia del magnesio. Disminuye la resistencia frente a la corrosión.
Fe:
Impureza que aumenta sensiblemente la velocidad de corrosión
Li:
Rebaja la densidad del magnesio. Aumenta la ductabilidad pero disminuye la resistencia. Aleaciones pueden ser envejecidas
Mn:
Se emplea para mejorar la resistencia a la corrosión
Ni:
Impureza que aumenta sensiblemente la velocidad de corrosión
Tierras raras:
Se añaden como mischmetal (mezcla de Ce, La y Nd) o didimio (85% Nd y 15% Pd). Mejora la resistencia a altas temperaturas.
Ag:
Aumenta la resistencia mecánica, ya que favorece la respuesta del material al envejecimiento.
Th:
Aumenta la resistencia del material hasta 370ºC. Suele añadirse a aleaciones Mg-Zn.
Sn.
Se adiciona en pequeñas cantidades a las aleaciones Mg-Al. Aumenta la ductabilidad. Aumenta la resistencia al agrietamiento en caliente (aleaciones buenas para forja).
Y.
Mejora las propiedades mecánicas hasta 250- 300º C. Suele adicionarse al Mg junto a otras tierras raras.
Zn.
Se suele emplear en combinación con el aluminio. Mejora la resistencia a bajas temperaturas. Frecuentemente se adiciona junto a otras tierras raras o Zr, ya que son aleaciones envejecibles con elevadas propiedades mecánicas.
Zr.
Se adiciona en pequeñas cantidades por su capacidad para refinar el grano.