Avances en el mecanizado de materiales combinados con magnesio
(Fundación Tekniker)01/06/2006
Se denomina material híbrido al resultado de la combinación de materiales de distinta naturaleza [2] con objeto de aunar las características técnicas ventajosas de cada material y reducir tanto peso como costes. Es por esta razón, que en los últimos años están proliferando las piezas fabricadas con materiales híbridos en construcciones ligeras, encontrándose componentes híbridos de magnesio-aluminio (Mg-Al) y magnesio-acero sinterizado (Mg-Sint). Un ejemplo lo constituye el bloque-motor desarrollado por BMW, en el que se emplea la combinación aluminio-magnesio para la parte del alojamiento de los cilindros y magnesio/acero sinterizado en la parte del soporte del cigüeñal (Foto 1). Este tipo de estructuras está atrayendo un gran interés ya que presenta la ventaja de su bajo peso combinado con su alta resistencia y buenas características de desgaste y fatiga. Sin embargo, afrontar el mecanizado de estos materiales híbridos supone un gran reto en términos de precisión, calidad y seguridad [3].
En general, el mecanizado de magnesio y sus aleaciones presenta riesgo de fuego y explosiones debido a su facilidad de ignición (combustión auto-sostenida), que depende fundamentalmente de su forma y tamaño. Las piezas grandes de magnesio se incendian con dificultad debido a su alta conductividad térmica. Sin embargo, las virutas y polvo resultantes del mecanizado de magnesio (con alta relación superficie/volumen) son sustancias altamente combustibles susceptibles a la oxidación, calor e ignición espontánea [4]. Estos finos pueden ser llevados a la temperatura de ignición con una pequeña fuente de calor y una vez que se ha encendido la viruta, el fuego puede extenderse a las virutas adyacentes.
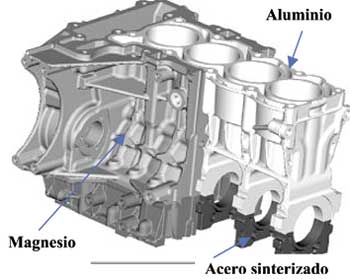
Además de estos problemas inherentes a cada uno de los materiales, el mecanizado de componentes híbridos basados en magnesio presenta dificultades adicionales. En la combinación magnesio/aluminio, ambos materiales ofrecen diferentes calidades de mecanizado y a fin de evitar la discontinuidad de calidad resulta necesario ajustar los parámetros de la máquina-herramienta cuando se produce el desplazamiento de un material al otro. Por otra parte, el peligro de incendio se presenta más acentuado en el mecanizado de magnesio/acero sinterizado debido a las altas temperaturas que alcanza la viruta del acero sinterizado y a la alta inflamabilidad de los finos de magnesio.
Para conseguir un mecanizado seguro de magnesio resulta indispensable emplear máquinas-herramienta que incorporen el concepto de seguridad, así como lubricantes y herramientas especiales. Con el fin de evitar los peligros derivados de la ignición, las actuales tecnologías para el mecanizado de materiales basados en magnesio emplean gran cantidad de fluido de corte -en forma de aceite o emulsión- para refrigerar la zona de corte y poder retirar la viruta del área de trabajo, reduciéndose de esta manera el riesgo de incendio y aumentándose la vida de la herramienta. Sin embargo, el empleo de fluido de corte no elimina el potencial peligro ya que existen una serie de riesgos adicionales tales como la posible ignición de la niebla de aceite (o aerosol provocado por el aceite mineral) o la liberación de hidrógeno libre (resultado de la reacción del Mg con el agua de la emulsión). En la actualidad se están llevando a cabo investigaciones en torno a conseguir estrategias de lubricación más seguras y medioambientalmente aceptables, empleando fluidos de corte adecuados que aseguren unos resultados óptimos y eviten situaciones de peligro. En este artículo se presentan los resultados obtenidos empleando una estrategia de mínima cantidad de lubricación (MQL) e incluso condiciones secas para conseguir un mecanizado eficiente y aceptable medioambientalmente de materiales híbridos basados en magnesio.
Medidas de seguridad adoptadas
El extractor de nieblas consta de tres etapas: prefiltro, aspirofiltro y postfiltro y cumple con el requisito de no ser electromagnético. El prefiltro ha sido especialmente introducido pensando en el mecanizado en condiciones secas y asistidas con MQL, casos en los que hay mayor probabilidad de generación de polvo y partículas metálicas en la zona de trabajo.
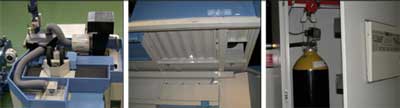
Además, resulta necesario evitar la acumulación de la viruta de magnesio así como extraerla de la zona de mecanizado, debido a la alta probabilidad de que se produzca su ignición como consecuencia de las chispas generadas en la zona de corte. Para poder desalojar adecuadamente esta viruta, el centro de mecanizado presenta los elementos necesarios no sólo para su extracción automática sino también para el filtrado y recirculación del fluido de corte. En este sentido, se han colocado rampas y chorros superiores de aceite a presión para la evacuación de la misma, así como canales inferiores localizados a ambos lados de la mesa, que contribuyen a acelerar la retirada de la viruta de la zona de corte y a su inmediata refrigeración.
De cara al mecanizado resulta necesaria la puesta a punto de todos estos sistemas, comprobando su correcto funcionamiento, lo que garantizará una total seguridad durante el mecanizado de materiales híbridos basados en magnesio. Además el operario de la máquina debe estar perfectamente informado de todos los aspectos de seguridad relacionados con el mecanizado de este material.
Fresado de materiales híbridos
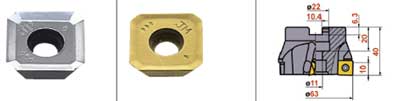
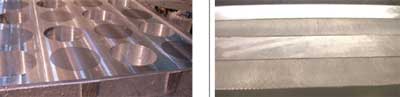
Los pruebas se han realizado de forma comparativa en condiciones secas y aplicando mínima cantidad de lubricante, empleando en este caso un aceite puro sintético de viscosidad media especialmente desarrollado para el mecanizado de este tipo de híbridos. El sistema MQL utilizado está basado en microbombas que dosifican el aceite y el aire mediante un conducto coaxial, produciéndose la mezcla de ambos (aceite/aire) a la salida de la boquilla. Se ha aplicado lubricación externa empleando dos boquillas con manguera flexible con un consumo total de lubricante de 22 ml/h.
Como principales parámetros de salida para controlar el proceso se han considerado la rugosidad superficial y el desgaste de la herramienta. La vida de la herramienta se ha valorado de acuerdo a la norma ISO 8688, midiéndose el desgaste de flanco hasta alcanzar un valor medio VB de 0,3mm. Las medidas de desgaste se han llevado a cabo “in situ” con un microscopio de contacto Keyence.
Combinación de magnesio/acero sinterizado
Bajo dichas condiciones se observa que el empleo de MQL mejora la calidad superficial del magnesio y metal sinterizado, alcanzándose valores de Ra inferiores a 1,46 y 1,83µm, respectivamente. En cuanto al desgaste de flanco, se detecta también cierta mejora con la aplicación de MQL, retrasándose la obtención de un desgaste de 0,2 mm en la herramienta en 0,7m2.
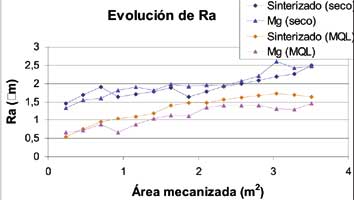
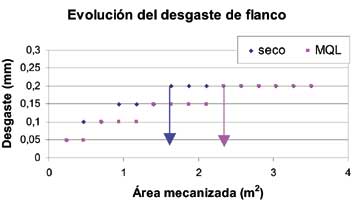
En la figura 2 se representa la evolución de la rugosidad superficial y del desgaste de flanco con el área mecanizada en las condiciones mencionadas.
El empleo de lubricación MQL mejora ligeramente la rugosidad superficial del metal sinterizado, pero no del magnesio, y disminuye el desgaste de la herramienta, alcanzándose un valor en el flanco de 0,2 mm para un área mecanizada de 4,42 m2 en lugar de 2,65 m2 en condiciones secas.
Como resultado de estas pruebas se puede concluir que el límite en la velocidad de corte para el fresado de la combinación Magnesio/acero sinterizado se encuentra en torno a 200m/min para profundidades de corte moderadas. Si este último parámetro debe incrementarse, la velocidad deberá disminuir si se quiere mantener un mecanizado seguro del componente.
Combinación de magnesio/aluminio
En esta combinación de materiales, la aplicación de MQL no produce mejora en la calidad superficial de ambos metales, afectando en mayor grado el propio material que las condiciones de lubricación. Esta diferencia de rugosidades tan significativa es un factor a tener en cuenta en la fabricación del componente final dado que la calidad superficial no es homogénea y va a estar condicionada por la calidad alcanzada en la parte de Aluminio. En cuanto al desgaste, el suministro externo de MQL supone una mejora en la vida de la herramienta en torno al 10%.
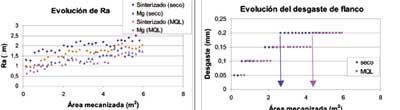
Conclusiones
• El empleo de sistemas de suministro externo de MQL ayuda positivamente.
• Aplicando MQL, en ambas combinaciones de materiales híbridos se observan mejoras en cuanto a rugosidad superficial de la pieza y desgaste de la herramienta.
• Esta mejora podría ser más significativa aplicando mínima lubricación internamente a través del cabezal y la herramienta, actividad a realizar en un futuro próximo.
Los autores agradecen a la Comisión Europea por la subvención recibida para el desarrollo del proyecto CRAFT “ECOHYB” dentro del 6º Programa Marco y al consorcio por apoyar este trabajo
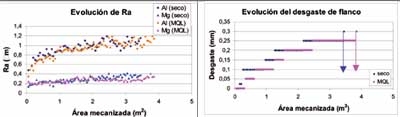