Erema y Dornier combinan componentes de una máquina para crear una solución de reciclaje innovadora
Cuando dos líderes tecnológicos en ingeniería mecánica trabajan conjuntamente para dar respuesta a los requisitos específicos de sus clientes, se obtiene como resultado una solución de reciclaje única. El reciclaje de residuos de producción de los fabricantes de films planos estirados biaxialmente es una práctica habitual, pero la producción de film se convierte en un reto específico de una aplicación si el reciclado de post-consumo también se añade a un film de BOPET. Erema, firma representada por Protecnic 1967, y Lindauer Dornier han sido capaces de dar respuesta a este requisito específico de cliente integrando componentes de ambas compañías por primera vez en una línea de reciclaje de un fabricante de film de Europa.
Han combinado una máquina de reciclaje Intarema 1512 TE con un filtro Dornier para obtener una filtración fina. El sistema de reciclaje compacto Intarema ha probado sobradamente sus méritos una y otra vez durante años para el reciclaje de residuos de BOPET y BOPP en la fabricación de film de envases y embalajes. La máquina de rema presenta un extrusor mono husillo corto y tiene doble desgasificación por pertenecer a la serie TE. El filtro Lindauer Dornier es un filtro eléctricamente calentado que los fabricantes de máquinas de tejer y máquinas especiales normalmente implementan en la fase de extrusión de sus líneas de film estirable. El filtro se diseña individualmente para la producción requerida por el cliente y es adecuada para un grado de filtración de 10 µm.
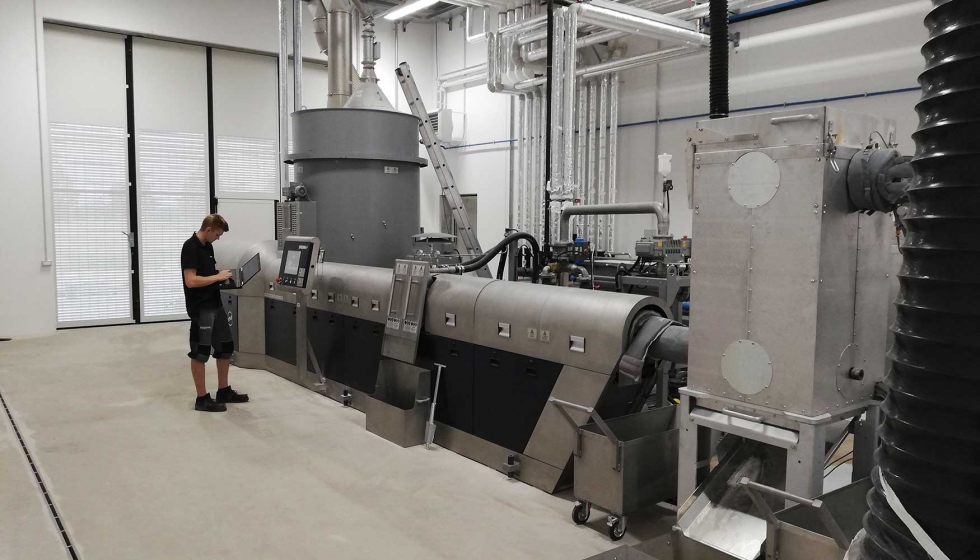
El sistema de reciclaje es una combinación específica de aplicación de una recicladora Intarema 1512 TE con un filtro Lindauer Dornier para filtración fina. Autor de la foto: Dornier.
El cliente que utiliza esta combinación de reciclaje lo usa para procesar escama de botella de PET lavada que compra. Las escamas tienen una densidad aparente de 370 kg/m³ y miden entre 0,6 y 8 mm. La granza reciclada de 3 x 3 x 2 mm con una densidad aparente de 700 a 800 kg/m³ son parte de la receta para conseguir film de poliéster estirable biaxialmente con un espesor de 23 a 30 µm para aplicaciones industriales. La capa de extrusión más importante de este film de BOPET se fabrica usando granza reciclada en un contenido del 30%. Como resultado, no se puede detectar una opacidad adicional del film.
Invirtiendo en esta máquina de reciclaje, nuestros clientes ahora son capaces de monitorizar de forma continua el proceso de la escama de botella de PET comprada por ellos mismos. Esto significa que tienen completo control sobre la calidad de la granza reciclada así como del valor añadido interno. “Los clientes de nuestros clientes piden cada vez más que el film de plástico lleve la máxima proporción de poliéster reciclado posible. Con esta maquinaria de reciclaje especialmente configurada por rema y Dornier para esta aplicación, la granza reciclada se optimiza para alcanzar el mayor rendimiento posible de la línea de film estirable", indica Michael Stötzel, responsable de servicio en Dornier“.
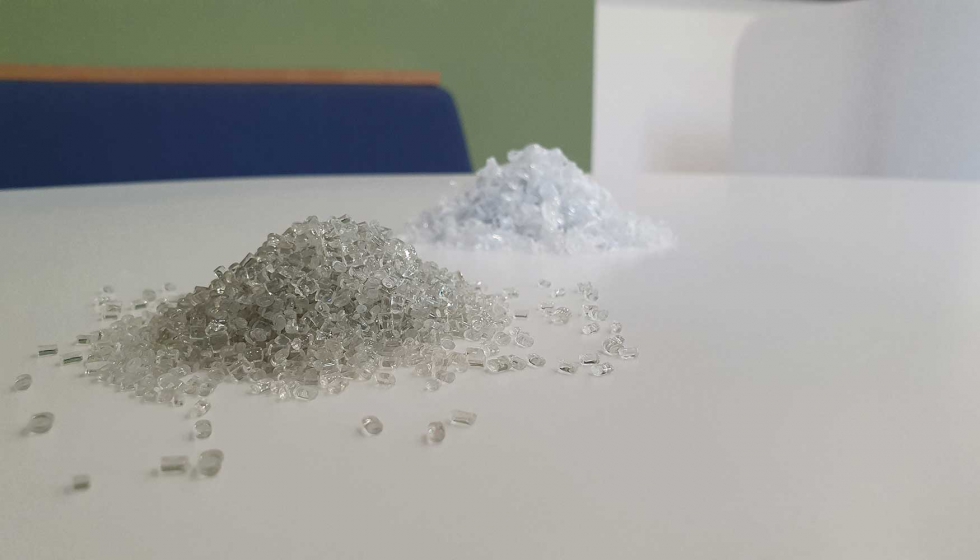
La granza reciclada está optimizada para el mayor rendimiento possible en una línea de film estirable. Autor de la foto: Dornier.
“En general, la demanda para proporciones superiores de rPET en productos de film está creciendo continuamente", confima Andeas Dirnberger, director de desarrollo de negocio de Aplicación Inhouse e Industrial en el Grupo rema: “Los fabricantes de film son llevados por el desarrollo de conceptos de producto sostenibles. La alta calidad de la granza de rPET que ahora produce este cliente, es el resultado del desarrollo tecnológico continuo de proceso de reciclaje de materiales de post-consumo. Esto es solo posible si los partners del proyecto trabajan conjuntamente de forma eficiente con un mismo objetivo”. Erema y Dornier han estado cooperando durante muchos años en las soluciones de reciclaje in-house para los productores de film BOPET. “El hecho de que los equipos involucrados en este proyecto ya conozcan el producto del otro de antemano, ciertamente ha sido un factor decisivo para esta aplicación de cliente, ” dice tanto Michael Stötzel como Andreas Dirnberger.