Intarema ZeroWastePro: el nuevo estándar para el reciclaje de residuos de producción de film
El nuevo sistema de reciclaje inhouse Intarema ZeroWastePro está especialmente diseñado para residuos de producción de film de PE y PP procesados en línea y fuera de línea. Cuenta con un potente empaquetado automatizado, soluciones de conectividad modernas y un corto plazo de entrega, gracias a un alto nivel de estandarización. Hasta el 100% del material reciclado puede ser alimentado otra vez en el proceso de producción principal. Como novedad también hay que destacar un cabezal granceador con refrigeración por aire, el cual consigue productividades superiores y menores costes de energía, así como de infraestructura.
La estabilidad del proceso, la consistente alta calidad, y el alto grado de automatismo son de vital importancia para el procesado de residuos de producción. La nueva ZeroWastePro ha sido diseñada precisamente para alcanzar estos requisitos. El fabricante austriaco de máquinas de reciclaje, representado en España por Protecnic 1967, implementa su tecnología patentada Counter Current y el probado concepto de funcionamiento Smart Start con el que están equipadas todas las máquinas Intarema. Adicionalmente, los componentes especialmente diseñados para aplicaciones de film (geometría de husillo optimizada y controles inhouse de calidad optimizada) que están incluidos en la ZeroWastePro estándar, aseguran un incremento decisivo en calidad. Por ejemplo, el novedoso ajuste automático de la velocidad de granceado utilizando combinaciones de parámetros adecuados, permite que la producción del granulado tenga una densidad aparente y de forma incluso más consistente que antes.
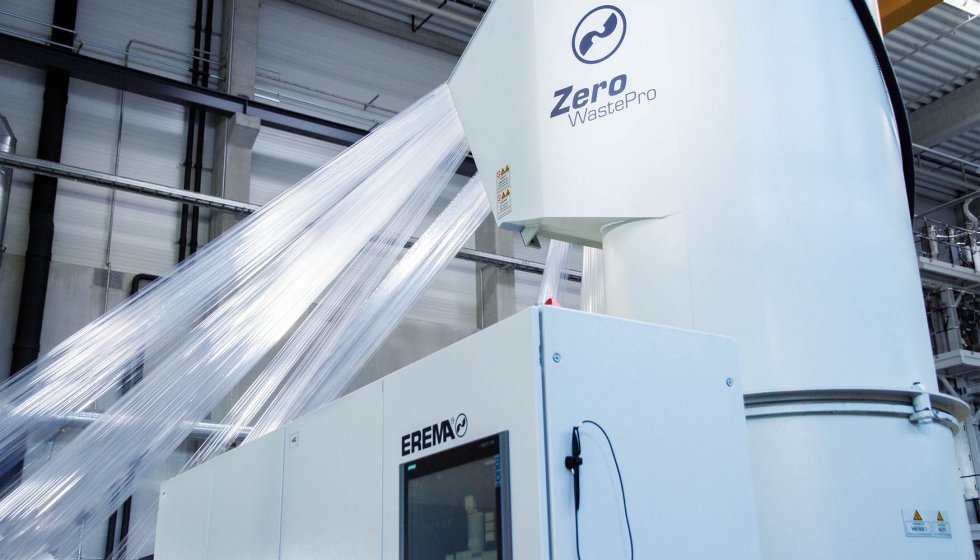
Funcionamiento sencillo y soluciones de conectividad modernas
“Uno de los requisitos esenciales en nuestra agenda de desarrollo fue simplificar aún más el manejo general de la nueva máquina de reciclaje", dice Andreas Dirnberger, responsable de Desarrollo de Negocios Inhouse e Industrial del Grupo Erema. Este concepto de simplicidad se ha implementado de forma consistente, empezando por la instalación e integración dentro de la producción de film existente a través de los sistemas de asistencia modernos para operaciones en curso. La nueva ZeroWastePro también ofrece soluciones de conectividad impresionantes, tales como el paquete Smart Service, que está incluido gratuitamente durante los primeros 12 meses y que proporciona un práctico acceso remoto a todos los servicios, así como a BluPort, la nueva plataforma digital de cliente. Desde un punto de vista rentabilidad, la máquina de reciclaje tiene un tiempo de entrega especialmente corto, el cual, dependiendo de la versión, va de un rango de tres a cuatro meses y medio una vez que el pedido ya se ha procesado. Esto ha sido posible gracias a la gran estandarización de los componentes del sistema y a la optimización de los procesos internos. Los usuarios de la máquina también se benefician de la reducción de materias primas utilizadas y menores costes de residuos, lo cual significa que los costes de inversión se pagan por sí mismos en un plazo de tiempo muy corto.
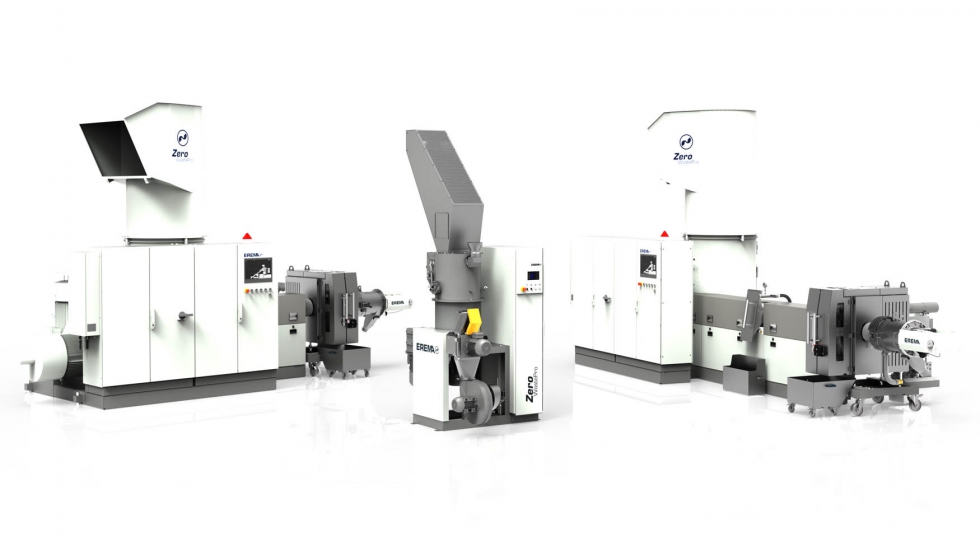
Cabezal granceador con refrigeración por aire
Erema ha desarrollado una innovación más para el segmento inhouse con un nuevo concepto que consiste en un cabezal granceador con refrigeración por aire y un sistema de transporte de granza mejorado. Adicionalmente a un diseño optimizado que simplifica el mantenimiento y funcionamiento, todo el sistema de flujos ha sido optimizado utilizando el análisis informático. Esto ha mejorado la eficiencia de la refrigeración de la granza y el transporte. El nuevo sistema granceador es particularmente aconsejable para máquinas de reciclaje tales como la serie Intarema K, que funcionan en combinación con líneas de film soplado. Dependiendo de la composición del film, se pueden alcanzar rendimientos superiores al procesar films de PE sin intercambio de aire adicional. Así mismo, los films multi-polímero con un contenido de PP de hasta un 10% pueden procesarse usando esta configuración. “Con la ayuda de este nuevo estadio de desarrollo, somos otra vez capaces de conseguir un ahorro de coste significativo para nuestros clientes. La infraestructura que se necesita para utilizar el agua como medio de refrigeración ya no se necesita más. Además, el cabezal granceador requiere menor energía y espacio”, explica Andreas Dirnberger.