Mecanizado por ultrasonidos rotatorio de cerámicas técnicas: estudio del proceso
Dadas las buenas características en servicio de las cerámicas técnicas debido a su alta dureza, gran resistencia al desgaste y a la abrasión incluso a altas temperaturas y a su baja densidad, se están introduciendo en el mercado con aplicaciones nuevas y más avanzadas, lo que hace más evidente la necesidad de optimizar sus costes de fabricación. Los costes actuales mediante procesos convencionales como el rectificado oscilan normalmente entre el 30-60%, llegando en algunos casos hasta el 90% del coste total de producción.
Entre los procesos de mecanizado no convencionales que están siendo desarrollados para el mecanizado de estas cerámicas destaca el Mecanizado por Ultrasonidos Rotatorio (RUM-Rotary Ultrasonic Machining) por ser un proceso eficiente y económicamente viable para el mecanizado de materiales duros y frágiles [2].
El RUM es un proceso que consiste en la eliminación de material utilizando una herramienta de superabrasivo mediante la combinación de tres movimientos: rotación, vibración axial ultrasónica (frecuencia del orden de 20 Khz.) y avance contra la pieza. Por otro lado, una corriente de taladrina es bombeada a través de la herramienta eliminando las virutas de la zona de corte, evitando el embotamiento y refrigerando el proceso.
En cuanto al mecanismo de arranque de material, el RUM es un proceso híbrido que combina los mecanismos de arranque del rectificado con diamante y del mecanizado por ultrasonidos tradicional (USM), mejorando ambos procesos [3]. A continuación se detallan las ventajas que aporta el RUM frente a ambas tecnologías:
Comparado con el mecanizado por ultrasonidos tradicional (USM), los beneficios que destacan se podrían resumir en los siguientes aspectos [2, 3, 4]:
- Es 10 veces más rápido.
- Resulta más fácil taladrar pequeños agujeros y su precisión mejora notablemente.
- Se produce menor presión en la herramienta y menor tasa de desgaste.
- No es necesario emplear fluido abrasivo.
Comparado con el rectificado, las ventajas son las siguientes [5, 6]:
- Produce menores fuerzas de corte (65%-70%) y desgaste de herramienta.
- Se mejora la rugosidad superficial (29%).
- No se produce zona afectada térmicamente, ni alteraciones químicas en la superficie de la pieza.
- Se crea una capa de tensiones residuales de compresión que podrían aumentar la vida a fatiga del componente mecanizado.
El rectificado produce mucho calor y no está indicado para el mecanizado de geometrías pequeñas ni para producir aristas vivas sin daños en la superficie. En este sentido, la tecnología RUM surge como una solución eficiente, capaz de producir diámetros de hasta 0.5mm sin apenas daños superficiales.
En este trabajo se presenta un estudio del comportamiento de la tecnología RUM en el mecanizado de una cerámica técnica: Óxido de Aluminio. Con este objetivo, se han analizado dos operaciones de mecanizado: fresado y taladrado, ambas en condiciones de acabado, empleándose el método de diseño de experimentos para evaluar los principios y ventajas reales que ofrece esta tecnología frente al rectificado.
Los ensayos se realizaron en una máquina de RUM de la marca Sauer Ultrasonic (DMG) modelo DMS 35, ver Figura 1, que incluye un generador de ultrasonidos y un cabezal ultrasónico. Así mismo, incorpora 2 algoritmos de control que regulan el avance de acuerdo con el valor del par (control ADR), y el valor de una señal acústica que tiene relación con el esfuerzo axial que se produce en el proceso (control ACC). Estos sistemas monitorizan el proceso protegiendo la integridad tanto de la herramienta como de la pieza.
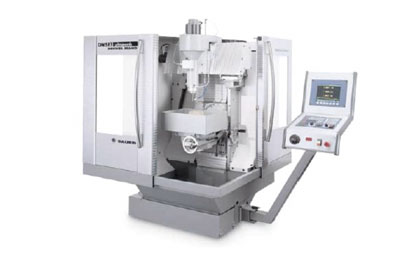
Los ensayos se llevaron a cabo modificando diversos parámetros de corte y midiendo las fuerzas de corte, rugosidad y redondez (en el caso del taladrado), y manteniendo las condiciones de vibración constantes durante los mismos.
La medición de los resultados se realizó utilizando los siguientes equipos:
- Las fuerzas de corte se capturaron mediante una plataforma dinamométrica de la marca Kistler modelo 9257-BA.
- La rugosidad superficial se midió con un rugosímetro de la marca Mitutoyo modelo SJ201P. Las mediciones se realizaron en la dirección de avance de la herramienta en cada operación de mecanizado.
- La redondez se midió empleando una máquina de medir por coordenadas de la marca Zeiss modelo UPMC 850 CARAT en 3 planos diferentes de cada agujero.
Las condiciones de corte utilizadas en los ensayos son las que se muestran en la Tabla 1y la Tabla 2. Se ha utilizado un método de diseño de experimentos y los resultados han sido analizados empleando el método de análisis de varianza, ANOVA.
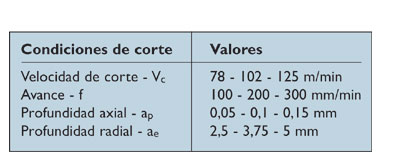
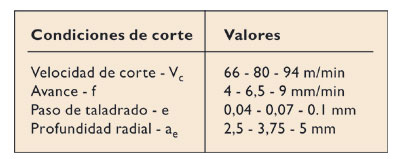
Las variables de salida eran las 3 componentes de las fuerzas de corte y la rugosidad en el caso del fresado, siendo para el taladrado la componente axial de la fuerza de corte, la rugosidad y la redondez.
Tanto los ensayos de taladrado como los de fresado se realizaron con y sin asistencia de los ultrasonidos, con el objeto de comparar el comportamiento del proceso de RUM frente a una operación similar al rectificado.
Ensayos de fresado
Los resultados de los ensayos indican una clara reducción tanto de las fuerzas de corte como de la rugosidad obtenida en el proceso con vibración frente al proceso sin vibración ultrasónica. Los intervalos de reducción obtenidos se muestran en la Tabla 3.
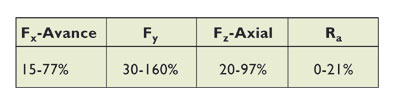
La reducción de las fuerzas de corte se produce debido a la acción de la vibración ultrasónica y está también asociado al hecho de que las virutas generadas son menores debido a una mejor fractura del material bajo el efecto de la vibración ultrasónica [7].
Las medidas de la rugosidad confirman lo apuntado en estudios previos [8], observándose con RUM una reducción de la misma, llegando en este caso hasta el 21%, como se indica en la Tabla 3.
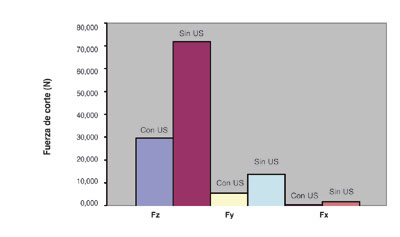
En lo referente a los ensayos de taladrado, los resultados indican una clara reducción tanto de la fuerza axial de corte como de la rugosidad obtenida en el proceso con vibración frente al proceso sin vibración ultrasónica. Los intervalos de reducción obtenidos se muestran en la Tabla 4.
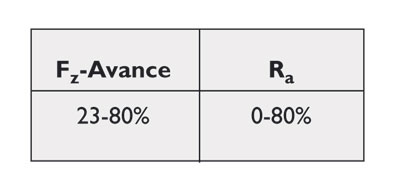
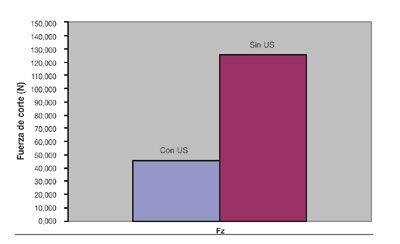
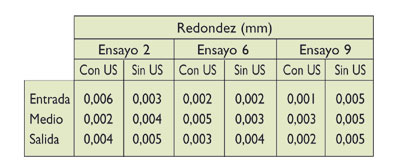
La calidad de los agujeros obtenidos con el mecanizado
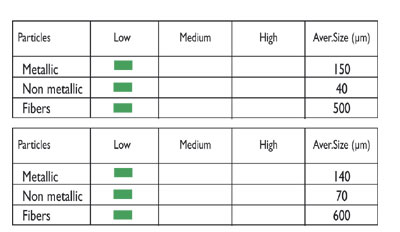
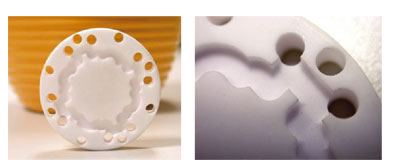
Como se puede comprobar, exceptuando algunas de las medidas como la entrada del ensayo 2 y el plano central del ensayo 6, todos los planos tienen una mejor redondez con ultrasonidos.
Tamaño de las virutas
Durante los ensayos experimentales se recogieron muestras del fluido de corte que posteriormente fueron analizadas por filtrografía para conocer el tamaño de las partículas presentes. Este ensayo proporciona información acerca de las partículas metálicas provenientes del desgaste de la herramienta, fibras de restos del filtro del fluido de corte, y partículas no metálicas que corresponden a las virutas cerámicas del material mecanizado. En la Figura 4 se puede observar que el valor correspondiente al tamaño de las partículas no metálicas en el caso de mecanizado con ultrasonidos es de 40 ºm frente a las 70 ºm del mecanizado sin ultrasonidos, que implica una reducción de tamaño del 57%.
Pieza test
Con objeto de verificar las ventajas y beneficios de la tecnología del Mecanizado por Ultrasonidos Rotatorio se mecanizó una pieza real, esta pieza de ensayo corresponde a un anillo de ajuste, ver Figura 5. El mecanizado de este componente incluye operaciones de taladrado y fresado, y el tiempo empleado para su fabricación partiendo de un disco de material fue de 1 hora y 10 minutos, siendo la rugosidad media menor de 1 µm Ra.
Conclusiones
Como conclusiones se pueden establecer las siguientes ventajas y beneficios de la tecnología del mecanizado por ultrasonidos rotatorio:
- Se produce una clara reducción de las fuerzas de corte debido a la vibración ultrasónica para las operaciones de fresado y las de taladrado. Esta reducción de esfuerzos de corte evita la creación de defectos en los bordes de los componentes durante el mecanizado.
- Se observa así mismo, una mejora de la rugosidad de hasta el 20% en operaciones de fresado y del 80% en las de taladrado. Estos resultados confirman los beneficios de esta tecnología y su aplicabilidad a mecanizados de acabado.
- Los resultados que arrojan las medidas de redondez son positivos respecto a que el proceso con ultrasonidos produce una mejor calidad en los taladros.
- Finalmente, se mecanizó una pieza test utilizando las dos operaciones estudiadas, fresado y taladrado, confirmando las posibilidades de este proceso como sustituto del rectificado para la realización de componentes complejos en materiales duros y frágiles.
Agradecimientos
Los autores quieren agradecer al Departamento de Industria del Gobierno Vasco-Eusko Jaurlaritza la ayuda recibida para la realización de este trabajo en el proyecto CIC MARGUNE del programa ETORTEK.
Referencias
[1] E.Uhlmann, G.Spur. “Surface Formation in creep feed grinding of advanced ceramics with and without Ultrasonic Assistance”. Annals of the CIRP, 1998.
[2] Z.J.Pei, D.Prabhakar, P.M.Ferreira. “Rotary Ultrasonic Drilling and Milling of ceramics”. The Design for Manufacturability and Manufacture of Ceramic Components Symposium.
[3] D. Prabhakar, Z.J. Pei, P.M. Ferreira, M. Haselkorn, “A theoretical model for predicting material removal rates in rotary ultrasonic machining of ceramics”, Transactions of the North American Manufacturing Research Institution of SME 21 (1993) 167-172.
[4] P.G.Petrukha et al., “Ultrasonic diamond drilling of deep holes in brittle materials”, Journal of Russian Engineering 50 (10) (1970) 70-74.
[5] D.V.Cleave. “Ultrasonics gets bigger jobs in machining and welding”. Iron Age 218 (11) (1976) 69-72.
[6] K.F.Graff, “Ultrasonic machining”, Ultrasonics 1975: 103-109.
[7] Vicario I, Gonzalo O, Abasolo U. “Rotary Ultrasonic Machining of Aluminum Oxide ceramics: designed experiments”. Fifth International Conference-High speed machining 2006, Metz (France).
[8] Y.B. Wu, M. Nomura, Z.J. Feng and M. Kato. “Modelling of Grinding Force in Constant-depth-of-cut Ultrasonically Assisted Grinding”. Material Science Forum Vols. 471-472 (2004) pp.101-106. n
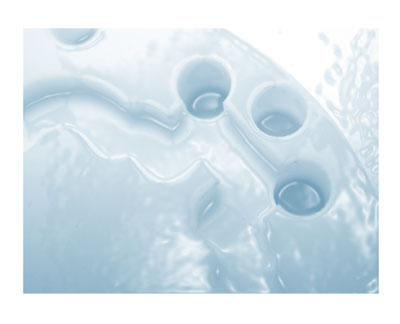