La evolución de la tecnología inkjet
23 de agosto 2010
En la actualidad la mayoría de centros de investigación y universidades sobre todo en Estados Unidos, Japón, Corea, Inglaterra y Alemania están apostando por la tecnología de impresión inkjet de última generación para la impresión de electrónica orgánica. Estas impresoras no imprimen sólo de manera convencional sobre papel, sino también sobre películas, textiles y mucho más; aplicando tintas con propiedades conductoras o polímeros orgánicos para producir circuitos electrónicos impresos flexibles, estructuras fotovoltaicas, RFIDs, etiquetas inteligentes, secuencias de material genético o sensores químicos y biológicos entre otras muchas aplicaciones. Básicamente se podría decir, que la tecnología de inyección de tinta se puede utilizar para realizar la gran mayoría de aplicaciones que involucra cualquier método usado para depositar una capa delgada de material sobre un sustrato.
La impresión de electrónica orgánica abre un nuevo mercado de aplicaciones alternativas a las actuales aplicaciones inorgánicas o de silicio, ya es posible de una producción más barata sobre soportes y dispositivos más delgados, más ligeros y más flexibles. La electrónica orgánica está basada en una combinación de técnicas que permite un recubrimiento o estructura multicapa, sobre la base de un soporte ligero y flexible y estratificado en función de su composición química, aislantes, semiconductores, etc.
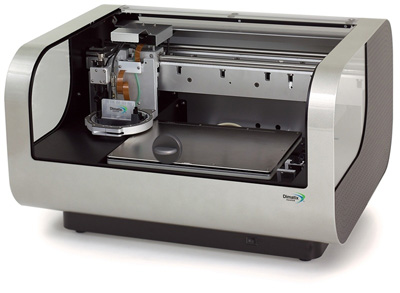
El plástico puede estar formado por grandes cadenas moleculares (polímeros) o moléculas individuales (monómeros). Se pueden fabricar componentes eléctricos a partir de ambos materiales. Sin embargo existen diferencias en la forma de aplicarlos, por lo general los monómeros se aplican en un proceso de depositado en vacio. En cambio los polímeros se pueden aplicar en procesos de impresión como por ejemplo inkjet porque se disuelven en líquidos y permiten una impresión capa por capa para construir un dispositivo eléctrico de forma muy económica.
El método de impresión inkjet resulta un método adecuado en el ámbito de impresión funcional, ya que se trata de un proceso sin contacto al soporte. De esta manera es posible imprimir sobre soportes muy sensibles como en el caso de la impresión de materiales fotovoltaicos para paneles solares. Aparte resulta más económico que otros procesos de deposición de materiales como por ejemplo tecnologías de evaporación en vacío y de spin coating ya que en su proceso a penas se generan desperdicios de materiales. Por otro lado, la tecnología inkjet permite imprimir una capa uniforme y realizar un control de espesor de capa adecuado.
Hay una amplia variedad de materiales funcionales imprimible por inkjet como conductores resistente a los rayos UV, polímeros, materiales orgánicos de película fina, dieléctricos, nano-tubos de carbono, nano-partículas. En función de los materiales utilizados podremos realizar aplicaciones diversas:
Impresión de antenas y etiquetas RFID
Una antena es un dispositivo diseñado con el objetivo de emitir o recibir ondas electromagnéticas desde y hacia el espacio. Para utilizar estas ondas, se debe adaptar la antena a una frecuencia determinada y debe ser conductora de electricidad. Con una tinta metalizada de plata se puede imprimir antenas sobre soportes flexibles por inkjet.
Se prevé un gran desarrollo de futuro para las antenas impresas ya que forman parte de los transponedores RFID (siglas de Radio Frequency IDentification, o Identificación por Radiofrecuencia) utilizadas en envases para su comercialización y otras muchas aplicaciones. Equipadas con un chip, las etiquetas RFID están sustituyendo los actuales códigos de barras, y permitirán en un futuro, entre otras cosas, identificar automáticamente el precio de compra para un carro lleno de productos. Las etiquetas RFID funcionan mediante ondas de radio, de manera que se eliminará la necesidad de escanear códigos de barras a la salida del centro comercial.
Los transponedores RFID son un desarrollo innovador frente a los transponedores convencionales basados en el silicio. Estos nuevos transponedores están desarrollados mediante polímeros semiconductores, imprimibles por el proceso de impresión inkjet sobre soportes plásticos y finos, por lo que también se llama respectivamente “transponedores RFID impresos” o “electrónica impresa”.
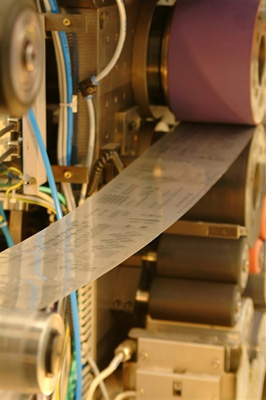
En comparación con los transponedores de silicio, los transponedores RFID impresos tienen la ventaja de que son más finos y más elásticos y, por tanto, son mucho más resistentes mecánicamente. Los de silicio, sin embargo, son un material rígido y, por tanto, susceptibles a la tensión mecánica, como fuerzas de choque o dobleces lo que los hace más frágiles. Debido al bajo coste en la producción de transponedores RFID impresos y a sus ventajosas propiedades, el campo de aplicación de la tecnología RFID se amplía ya que permiten aplicaciones impensables hasta ahora con los RFID convencionales por razones de coste o por la rigidez del material.
Incluso en la industria del automóvil las antenas están adquiriendo una importancia significativa. Y es que se utilizan para la radio y para los sistemas de navegación. Desarrolladores y diseñadores han encontrado la forma de integrar las antenas en el aspecto general del vehículo, de manera que no se ven a simple vista, ya que se pueden realizar mediante tintas metalizadas de plata conductivas, imprimiendo sobre soportes plásticos flexibles. Estos soportes se aplica en partes del cuerpo de plástico de los automóviles o en un espejo u ocultos en amortiguadores, sin que el diseño del vehículo se vea afectado y quedando totalmente invisibles para los usuarios del vehículo.
Energía solar fotovoltaica
Las células solares orgánicas (OPV) se plantean como una buena alternativa a medio plazo respecto a las células solares de silicio, tanto por su coste como por su flexibilidad y posibilidades de adaptación, permitiendo en un futuro no muy lejano la democratización de las energías renovables.
Las células solares orgánicas consisten en un soporte ligero y flexible y se puede imprimir mediante materiales poliméricos. Dado que los polímeros se disuelven en líquidos y en dependencia de su composición química, tienen condiciones aislantes, semiconductores o conductivas, es posible su impresión mediante tecnología inkjet al igual que los transistores y otras componentes electrónicas de manera económica.
“La energía fotovoltaica orgánica tiene un gran potencial, ya que dentro de pocos años será posible producir energía con un coste inferior a 50 céntimos de euro por pico vatio ”, dice Christoph Brabec, Gerente Técnico de la empresa Konarka Technologies Inc. de Estados Unidos. Un pico vatio se refiere a la cantidad de potencia producida por una célula o módulo bajo las condiciones nominales de irradiación (STC). “Esto significa que las células orgánicas fotovoltaicas serán mucho más baratas que otras tecnologías comparables”, dice Brabec. El proceso de fabricación de células solares fotovoltáicas impresas es similar a la impresión convencional roll to roll o en bobina.
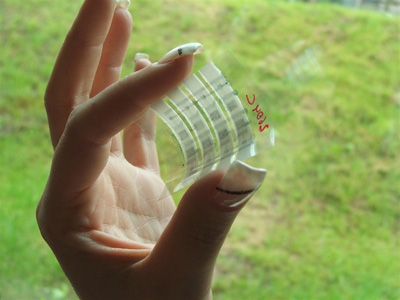
Para que los paneles solares fotovoltaicos que revisten fachadas de edificios y otras aplicaciones similares sean de interés para el consumidor, es necesario hacer frente a dos desafíos, el rendimiento y la durabilidad de los dispositivos, es decir, la vida útil del dispositivo y la eficiencia en la generación de electricidad. Ambos parámetros dependen principalmente del proceso y de la calidad y la interacción en el dispositivo multicapa de los componentes del sistema.
Hoy en día la eficiencia de los paneles solares orgánicos impresos en masa están en torno al 4%. Es decir: Para iluminar una lámpara de escritorio con 60 vatios, la luz del sol debe caer sobre un área relativamente grande de un panel solar de unos dos metros cuadrados. Los institutos de investigación y los fabricantes trabajan para doblar la eficiencia de las células solares orgánicas a medio plazo. Un ejemplo destacable es el anuncio realizado por el consorcio PIEM (Bélgica) y Plextronics Inc. (EE UU) ya que esperan desarrollar para 2012 células solares orgánicas con una eficiencia promedio de ocho por ciento y con una vida útil de cinco años El mayor desafío en el desarrollo de tan alto rendimiento es optimizar la absorción de los materiales eléctricamente conductores.
Diodo orgánico de emisión de luz OLED
Los OLED son dispositivos orgánicos electroluminiscentes que cuentan con dos principales aplicaciones, pantallas e iluminación, y entre sus principales características podemos hablar de mayor contraste, menor consumo de energía, y películas más delgadas y flexibles. En la actualidad, grandes fabricantes como Philips y Osram están buscando la manera para conseguir una producción a gran escala sobre soportes flexibles y a un bajo coste.
Los OLED, al igual que las células solares fotovoltáicas, se puede imprimir con polímeros sobre soportes plásticos flexibles y ligeros. En comparación con pantallas de cristal líquido o LCD (acrónimo del inglés Liquid Crystal Display), las pantallas OLED tienen sus ventajas, porque tienen un principio de funcionamiento distinto. Los cristales líquidos actúan como un obturador de persiana, la luz que se recibe desde el fondo se enciende o apaga. Por el contrario, las pantallas de OLED no requieren iluminación posterior, ya que el diodo de luz al mismo tiempo crea un voltaje eléctrico y emite luz.
- Muestra mayor eficiencia energética que una pantalla LCD, ya que un elemento OLED apagado realmente no produce luz y no consume energía, a diferencia de los LCDs que no pueden mostrar un verdadero “negro” y lo componen con luz consumiendo energía continuamente.
- Muestra más brillo y contraste que una pantalla LCD con iluminación posterior convencional. Los píxeles de OLED emiten luz directamente. Por eso, respecto a los LCDs posibilitan un rango más grande de colores, más brillo y contrastes, y más ángulo de visión. Los OLED muestran un ratio de contraste que alcanza valores de hasta 1.000.000 a1.
- Es más delgado, ya que se renuncia a la luz de fondo. Los fabricantes ya han mostrado pantallas de OLED muy delgados de un grosor de solo tres milímetros.
Sin embargo, los resultados y rendimientos actuales se han alcanzado utilizando el vidrio como sustrato. “Los fabricantes están trabajando sin descanso para que los dispositivos OLED se puedan imprimir sobre soportes flexibles, en el mejor caso en producción a gran escala en bobina”, dice el Dr. Udo Heider, Director del sector OLED en la empresa Merck AG de Darmstadt, Alemania. Los desafíos son, por ejemplo, en la elección de la tecnología de impresión adecuada, o la formulación de un sistema eficiente de la tinta. “Incluso en la resolución, brillo y durabilidad de los OLED impresos deben ser correspondiente a los altos estándares de las pantallas LCD”, dice Heider.
- Los OLED son fuentes de luz plana. En el futuro, se podrán producir pantallas de lámparas incandescentes o papel de paredes iluminados por OLED.
- Las fuentes de luz OLED no emiten calor porque transforman la energía eléctrica en energía lumínica de manera eficiente. De manera que es posible tocar esta fuente de luz sin quemarse. En una reciente aportación el Instituto Fraunhofer IPMS en Dresden ha mostrado una lámpara OLED con funcionalidad táctil que enciende y apaga con el movimiento de la mano.
Obtener luz blanca se ha convertido en uno de los principales retos en la investigación y desarrollo de dispositivos OLED para iluminación, debido al diferente rendimiento de los polímeros que emiten en el rojo, en el verde y en el azul, siendo éste último el más problemático, lo que dificulta el desarrollo de dispositivos que emitan luz blanca. En un trabajo de investigación a nivel europeo se han desarrollado OLED blancos con una eficiencia de más de 50 lúmenes por vatio (y una vida de más de 10.000 horas). Con estos valores un OLED de tamaño de 30 por 30 centímetros llega a unos los valores similares a un tubo fluorescente convencional.
Basados en estos resultados las empresas de Philips, Osram Opto Semiconductors, Siemens y Novaled siguen investigando. Empezaron en septiembre 2008, el proyecto OLED100.eu para el desarrollo de OLED más eficientes y económicos. Siendo los principales objetivos doblar la eficiencia de a 100 lúmenes por vatio y aumentar diez veces la vida útil del dispositivo hasta llegar a más de 100.000 horas. Finalmente, otro de los objetos del proyecto consiste en desarrollar un proceso de fabricación de OLED que permita la producción de un metro cuadrado de superficie iluminada a un costo inferior a 100 euros.