Los pulsos de la electroerosión y el fluido dieléctrico
- Pulsos en situación de circuito abierto
- Pulsos en situación de descarga efectiva o de chispa real
- Pulsos en situación de arco eléctrico
- Pulsos en situación de cortocircuito
Generalmente, los diferentes tipos de pulsos existentes se definen en base a la evolución de la diferencia de potencial y/o la intensidad de la corriente de descarga con respecto al tiempo (ver la figura 1).
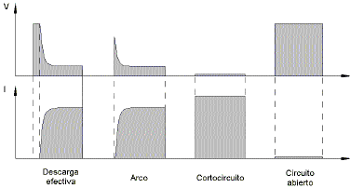
Cuando se produce el contacto entre el electrodo y la pieza, se da una situación de cortocircuito que tampoco contribuye a la eliminación de material. Se considera que los valores del gap usados en la práctica se encuentran en el intervalo de las distancias del electrodo a la pieza comprendidas entre las dos situaciones extremas anteriores, es decir, la situación de circuito abierto y la de cortocircuito. Es decir, un gap de trabajo adecuado debe producir descargas que den lugar a situaciones de chispa real o de arco eléctrico. Ambos tipos de pulsos muestran una caída característica de la diferencia de potencial en el gap durante la ocurrencia de un pulso eléctrico. Por otro lado, es bastante difícil de establecer la diferencia entre las situaciones de chispa y arco aunque se cree que las situaciones de arco ocurren en el mismo punto o sobre la superficie del electrodo y pueden producir, por lo tanto, roturas o daños importantes tanto en el electrodo como en la pieza. Además, se asume que las situaciones de arco se producen cuando el canal de plasma del pulso anterior no se encuentra totalmente desionizado y, por consiguiente, la corriente de descarga del pulso siguiente circulará, preferentemente, a lo largo del mismo camino anterior. En tal caso, no se requiere nada de tiempo para dar lugar a la formación de un nuevo camino para la corriente eléctrica, siendo considerada la formación del anterior canal de plasma gaseoso, a su vez, necesaria para iniciar una nueva interrupción o colapso de la chispa.
Por lo tanto, se piensa que son, de manera única, las situaciones de chispa real las que contribuyen a una eliminación del material de una forma adecuada. Por otro lado, queda todavía abierta la cuestión de cómo es la contribución de las situaciones de arco eléctrico en lo que respecta a la eliminación del material y al desgaste del electrodo.
La aparición en el mercado de la electroerosión del generador de pulsos con forma rectangular resultó en la mejora de tanto las tasas de eliminación de material como del desgaste de los electrodos, en comparación con los valores que se obtenían con el anteriormente utilizado generador de tipo relajación. Sin embargo, es un hecho real que el problema del desgaste del electrodo todavía persiste y que es de especial importancia durante las operaciones de acabado. En las operaciones de acabado, la precisión dimensional es uno de los factores más importante; por el contrario, el factor de la tasa de eliminación de material, aunque se preferiría que fuera más alto, no es tan importante como el anterior.
Como solución al problema del desgaste del electrodo, se ha aplicado de manera satisfactoria, además de una adecuada selección de los valores de los parámetros que más influyen en el proceso, la utilización de pulsos de corriente con formas no rectangulares, tales como los trapezoidales. En lo que respecta a la forma de los pulsos de corriente, los últimos modelos de generadores de pulsos tienen la opción de producir tanto formas rectangulares como otras que no lo sean (ver la figura 2).
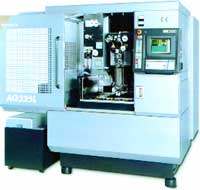
La eliminación de material en el mecanizado por electroerosión se basa fundamentalmente en la transformación de la energía eléctrica en energía de tipo térmica. Así, la distribución de dicha energía térmica sobre la superficie del electrodo es de especial importancia. Se cree que, aproximadamente, el canal de plasma se expande a lo largo de la duración del pulso según la relación que se cita en la ecuación 1:
0<=t<=ti
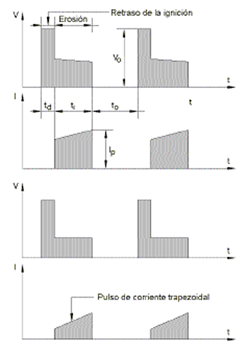
Otro parámetro que tiene influencia sobre el desgaste del electrodo es el tiempo de pausa, ya que se sabe que si se reduce dicho factor hasta el punto en que se da lugar a una situación de arco eléctrico, se favorece la deposición de una capa protectora de grafito, haciendo dicha película que se incremente la resistencia a la erosión eléctrica del electrodo de cobre. Por el contrario, un aumento en la duración del tiempo de pausa produce un aumento del desgaste del electrodo ya que, a su vez, se produce una disminución en la deposición de la capa de grafito. De este modo, unas condiciones de proceso que favorezcan la deposición de la anterior película de grafito, junto con una disminución de la intensidad de la corriente al comienzo del proceso de descarga, producen una disminución del desgaste del electrodo.
El fluido dieléctrico
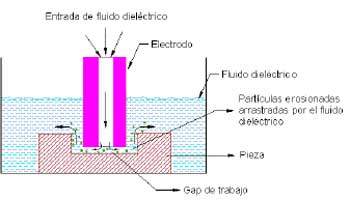
Las funciones más importantes que debe cumplir un fluido que se use como dieléctrico en el proceso de la electroerosión, según se cita en Crosby [1], son:
- limpiar o evacuar los restos de partículas erosionadas, es decir, la viruta del proceso de la electroerosión de la zona del gap, así como eliminar dichas partículas del dieléctrico mediante el hacer pasar al mismo a través de un sistema de filtrado adecuado;
- refrigerar el área que se calienta durante el proceso de mecanizado;
- proporcionar un medio aislante en el gap de trabajo, entre el electrodo y la pieza a electroerosionar.
Los dos tipos de fluidos más utilizados en estos procesos son los aceites minerales, compuestos de hidrocarburos derivados del petróleo, y agua que ha sido previamente desionizada (ésta última es utilizada generalmente para los procesos de corte por hilo). También se pueden utilizar como fluido dieléctrico en el caso de la electroerosión por penetración, determinadas soluciones acuosas de compuestos orgánicos, tales como ciertos glúcidos, alcoholes y polímeros, entre otros. Tales disoluciones sirven para solucionar el problema de la inflamabilidad del dieléctrico pero, por otro lado, dan lugar a unas menores tasas de eliminación de material con respecto a los hidrocarburos: Masuzawa [2] y König [3]. Finalmente, según se presenta en los trabajos de Kunieda [4], el proceso de la electroerosión puede también llevarse a cabo en un medio gaseoso, generalmente formado por aire u oxígeno. En este caso, el material fundido que procede de la pieza se extrae de la zona de trabajo gracias a la ayuda del anterior flujo de gas a una elevada presión. La mayor ventaja que presenta este método es la referente a la reducción del desgaste del electrodo hasta prácticamente cero, para cualquier valor del tiempo de impulso.
Los aceites dieléctricos usados deberían tener una densidad y viscosidad elevadas, ya que así se favorece el efecto de una concentración del canal de descarga y de la energía de descarga adecuadas. Por otro lado, podría darse, debido a sus propiedades características, alguna dificultad a la hora de evacuar o limpiar los restos que se originan en la zona de la descarga eléctrica.
En la mayor parte de las aplicaciones de la electroerosión, el dieléctrico más utilizado es el queroseno, al que se le suelen añadir determinados aditivos para evitar la formación de burbujas de gas y la emisión de malos olores. Para el caso de la electroerosión de aleaciones de titanio así como de ciertos aceros de herramienta, se han obtenido excelentes resultados del acabado superficial con la utilización de fluidos dieléctricos con suspensiones de polvos de materiales tales como silicio, grafito, aluminio, vidrio, carburo de silicio y disulfuro de molibdeno Mohri [5]. Tales resultados obtenidos se expresan también en términos de unos valores más elevados de las tasas de eliminación de material, una dispersión más uniforme de las descargas eléctricas y un mecanizado estable Wong [6]. Entre el resto de los fluidos dieléctricos utilizados con éxito en aplicaciones de mecanizado por electroerosión, pueden citarse, entre otros, los compuestos polares tales como las soluciones acuosas de etilenglicol (C2H6O2), las emulsiones acuosas y el agua destilada.
Según se establece en Herdman, [7], algunas de las propiedades más importantes que se deben tener en cuenta a la hora de realizar una adecuada selección del fluido dieléctrico a utilizar son:
- su punto de inflamación
- la rigidez del dieléctrico
- la viscosidad del fluido dieléctrico
- la densidad relativa
- el color
- el olor
El punto de inflamación representa la temperatura a la que el vapor del fluido dieléctrico se inflama. Generalmente, por el bien de la seguridad en el proceso, se prefiere que dicho valor sea lo más alto posible.
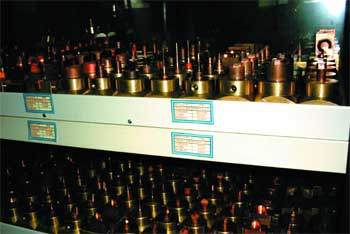
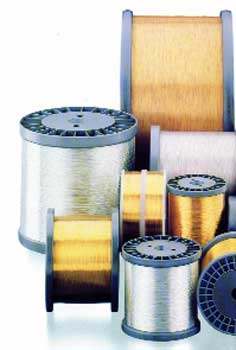
En lo que respecta a la viscosidad del dieléctrico, cuanto menor sea ésta mejor será el acabado superficial así como la precisión dimensional que puede obtenerse. En el caso de condiciones de acabado superficial de tipo espejo, las distancias del gap son tan pequeñas que se prefiere la utilización de aceites más ligeros y de menor densidad. Por otro lado, en el caso de las operaciones de mecanizado que requieren de un acabado superficial de tipo medio, tales como la fabricación de matrices para procesos de forja, pueden usarse aceites dieléctricos más densos. La viscosidad del fluido en tales casos puede ser alta, debido al mayor tamaño del gap, evitándose así una perdida excesiva de dieléctrico debido a la vaporización del mismo.
La densidad relativa, que a veces se confunde con la viscosidad, es el valor de la densidad de una substancia medida con un aparato denominado hidrómetro. Cuanto menor sea el valor de dicho parámetro, tanto más rápido se depositan en el fondo las partículas más pesadas, tales como la viruta procedente del proceso. La situación anterior, además, reduce la contaminación del gap y la posibilidad de formación de situaciones de arco eléctrico o de descargas secundarias.
Por lo que se refiere al color, generalmente, todos los fluidos dieléctricos se acaban ennegreciendo u obscureciendo conforme van siendo utilizados. Por este motivo, se prefiere que al principio el dieléctrico sea lo más claro posible, de forma que permita verse el fondo así como la pieza sumergida.
La variación del color del dieléctrico no es necesariamente una indicación de posible substitución del mismo, ya que, independientemente de la claridad de su color inicial, el aceite se va degradando con el uso y el paso del tiempo, debido a su exposición a la alta temperatura. La descomposición del aceite en sustancias diversas tales como alquitranes, resinas e hidrocarburos es lo que hace que el dieléctrico modifique su color, pero, por otro lado, no se debe confundir un aceite con cierto grado de coloración con un aceite que está realmente sucio.
Durante el proceso de la electroerosión, el fluido dieléctrico se ve sometido a condiciones de contaminación variables, siendo muy importante el control de la composición del mismo, ya que el hecho de trabajar con un nivel constante de contaminación da lugar a un mejor control de la distancia del gap y, por lo tanto, a una mejor precisión dimensional de las piezas y a unos valores más elevados de la tasa de eliminación de material, así como a un menor desgaste del electrodo. Por lo que respecta a los métodos de medición de dicha contaminación, merecen destacarse las investigaciones que se llevan a cabo en Frei [8].
En cuanto al olor del aceite dieléctrico, se deben utilizar siempre fluidos que no desprendan olores apreciables. Además de por evidentes razones de higiene, la utilización de aceites dieléctricos que desprenden olores es peligrosa, debido a que dicho olor puede ser una indicación de la presencia de compuestos de azufre, que son elementos no deseables dentro del proceso de la electroerosión.
Dependiendo del tipo de utilización así como del mantenimiento del aceite dieléctrico, éste puede llegar a durar varios años. La eliminación del agua que se encuentra contenida en el dieléctrico es uno de los factores más importantes a la hora de la alargar la vida útil del mismo. El agua no puede eliminarse de manera completa, ya que se produce la condensación de la misma sobre la superficie del electrodo cuando ésta se calienta. Los electrodos de grafito, frente a los que son metálicos, favorecen dicha condensación ya que tienen una estructura porosa que les permite absorber la humedad que se encuentra en el aire. Por consiguiente, los electrodos de grafito deberían almacenarse en sitios secos o, incluso, pueden introducirse en hornos de secado antes de su utilización.
Con respecto al mal estado de la limpieza del fluido dieléctrico, hay una serie de factores que pueden hacer sospechar acerca de cuándo llevar a cabo la misma, o de si ésta se está llevando a cabo de una manera incorrecta (debido al mal estado de los filtros, por ejemplo), entre los que pueden citarse:
- unas lecturas en los manómetros del circuito características y que suelen venir especificadas en los manuales de mantenimiento del equipo;
- un aumento de las situaciones de arco eléctrico o de picaduras localizadas en condiciones de mecanizado que antes eran satisfactorias;
- una duración superior de los ciclos de mecanizado;
- un empeoramiento de la calidad superficial del acabado de la pieza;
- una inspección visual de una muestra de dieléctrico en la que se compruebe su estado de coloración, turbiedad así como sus sedimentos
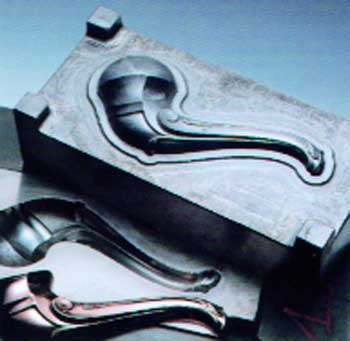
Referencias Bibliográficas
- Crosby, H. C., Fundamentals of EDM, Aerospace Engineering Conference (California), Enero 1984.
- Masuzawa, T.; Tanaka, K.; Nakamura Y.; Kinoshita N., Water-Based Dielectric Solution for EDM, Annals of the CIRP, 1983.
- König, W.; Jörres, L., Aqueous Solutions of Organic Compounds as Dielectrics for EDM Sinking, Annals of the CIRP, 1987.
- Kunieda, M.; Yoshida, M.; Taniguchi, N., Electrical Discharge Machining in Gas, Annals of the CIRP, 1997.
- Mohri, N.; Saito, N.; Higashi, M.; Kinoshita, N., A New Process of Finish Machining on Free Surface by EDM Methods, Annals of the CIRP, 1991.
- Wong, Y. S.; Lim, L. C.; Rahuman, I.; Tee, W. M., Near-Mirror-Finish Phenomenon in EDM using Powder-Mixed Dielectric, Journal of Materials Processing Technology, 1998.
- Herdman, F. H., Edm Dielectric Fluid "Buying Smart", Manufacturing Conference (Illinois), Septiembre 1992.
- Frei, C.; Hirt, C.; Girardin, R.; Dauw, D. F., A New Approach for Contamination Measurements for EDM Dielectrics, Annals of the CIRP, 1987.