Experiencias con resinas Epoxi Vinilester en sistemas de tuberías químicamente resistentes
Por: Michael Jaeger+, Rea Hentrich++, Ham Benson+++, Bernd Schwanewilms++++, Fernando Hurtado+++++01/12/2002
RESUMEN
+ DOW Deutschland GmbH & Co. OHG., Rheinmuenster Technical Center, Technical Service and Development
++ Buna SOW Leuna Olefinverbund GmbH, Schkopau, Maintenance Technical Service, FRP Specialist
+++ The Dow Chemical Company, Plaquemine, Design + Maintenance Engineering, FRP Specialist
++++ DOW Deutschland GmbH & Co. OHG, Stade, Design + Maintenance Engineering, FRP Specialist
+++++ Traducido y adaptado por F. Hurtado / QUIMIDROGA S.A
INTRODUCCIÓN
CAPÍTULO 1: EL PROCESO DE CALIDAD PARA UNA LARGA VIDA EN SERVICIO
• En algunos procesos, una larga vida puede ser tan corta como 2-4 años. Esto puede ser bastante razonable para algunos procesos en condiciones muy severas. Por ejemplo, The Dow Chemical Company (DOW) tiene una chimenea en FRP que trabaja en condiciones tan severas, que sólo dura 2-4 años. En estas condiciones, el FRP está considerado como un material de construcción efectivo, comparado con otras alternativas tales como el metal.
• En otros casos, la vida de un proceso (y por consiguiente la vida del equipo), puede ser de 10-20 años (procesos y/o cambios tecnológicos pueden hacer que el equipo FRP se quede obsoleto). Un equipo obsoleto puede ser reformado y vuelto a poner en servicio.
• En otros procesos una larga vida en servicio puede ser de 25 años y más. Así pues, el concepto de larga vida es relativo. Lo realmente importante es el coste efectivo de un material comparado con soluciones alternativas, teniendo en cuenta su ciclo de vida completo. Cuáles son los elementos del “proceso de calidad”
La vida de servicio puede estar influenciada por muchos
parámetros. Los principales son:
• Selección del material
• Diseño y especificación
• Fabricación
• Inspección / métodos de Ensayo No Destructivos
• Instalación
Y cuando el equipo está en operación:
• Control del proceso
• Supervisión / Determinación de la vida residual
• Mantenimiento
• Reparación
1.1 SELECCIÓN DEL MATERIAL
1.2 ESPECIFICACIÓN / FABRICACIÓN
construcción del equipo, y en el momento en que el diseño se ha completado de acuerdo con los estándares más relevantes, el comprador del equipo debe recopilar una detallada especificación para la fabricación, control e instalación. Junto con el diseño se debería incluir idealmente el tipo de resina, las características de la barrera química y la estructura, el sistema de curado, la técnica de fabricación permitida para todas las partes incluyendo accesorios como bridas, etc., condiciones de post-curado si se requiere, el diseño del ensamblaje, selección/posición/envergadura de los soportes, requisitos y garantías de calidad. Ver referencias 4 y 9 para más detalles. La inspección del FRP debe llevarse a cabo antes de aplicar cualquier topcoat de color.
1.3 INSTALACIÓN
Recientes estudios sobre fallos prematuros de las tuberías subrayan la necesidad de un trabajo de calidad para evitar costosas reparaciones o reposiciones12.
1.4 INSPECCIÓN
1.5 INSPECCIÓN VISUAL / DEFECTOS TÍPICOS 6
Los 5 defectos necesitan reparación. ASTM D 2563 puede ser consultado para la clasificación de defectos visuales.
a) Burbujas, vacíos (Aire atrapado dentro y entre los
pliegues; vacíos esféricos no interconectados)
Causas: Vaivén del agitador durante el mezclado.
Superficie pobre o sucia. Burbujas de aire no
eliminadas con el rodillo durante la fabricación.
b) Delaminación (Separación de capas, detectable
visualmente o golpeando con una moneda)
Causas: Baja saturación de la fibra de vidrio.
Superficie sucia. Excesivo contenido en fibra de vidrio.
No eliminar el inhibidor de aire antes de laminar una
nueva capa.
c) Blisters (Ampollas) (De forma redonda, a veces
elevaciones claramente definidas de la superficie de
laminado semejando ampollas)
Causas: Curado demasiado rápido. Humedad en la
resina, la carga o la fibra de vidrio.
d) Fracturas por impacto (Separación del material por
medio de grietas y visible en la superficie)
Causas: Impacto, refuerzo insuficiente o excesiva
concentración de resina en un área determinada.
e) Agrietamiento (Trama de finas grietas en o bajo la
superficie)
Causas: Área aislada rica en resina. Impacto mecánico.
Servicio intermitente causando diferencias de
temperatura, ciclos de seco/mojado y contracción de la resina.
Debajo se observan 2 ejemplos muy comunes de defectos de tuberías en FRP:
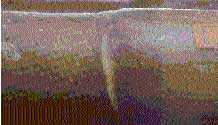
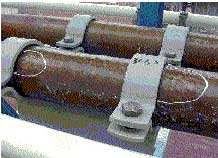
1.6 MÉTODOS DE ENSAYO NO DESTRUCTIVOS (NDT) PARA TUBERÍAS EN FRP
La Dureza Barcol se utiliza para evaluar el grado de curado de la resina. Se deben realizar 12 lecturas en el interior y el exterior del FRP, y mejor en un corte que no en la barrera química (CR) ya finalizada. Las lecturas mayor y menor se desprecian y las 10 restantes sirven para hacer una media aritmética. Los puntos críticos son las uniones secundarias, tales como bridas o conexiones internas. Es importante conocer la relación del desarrollo del curado de la resina tomando cualquier lectura obtenida dentro de la primera semana de fabricación: Una sola puede dar el 50% del mínimo de Dureza Barcol (especificada por el suministrador de la resina) después de 24 horas, y aún conseguir el 110% o más después de un período de 3 a 7 días. La experiencia muestra que en la mayoría de los casos, la mínima Dureza Barcol se alcanza después de 1-3 días de curado a temperatura ambiente. El equipo no debería ser puesto en servicio en tanto no se haya alcanzado la mínima Dureza Barcol.
El Test de Acetona debe ser utilizado de la siguiente forma: se coloca un algodón impregnado de acetona en el laminado durante 30 segundos y posteriormente se retira. La superficie se puede considerar que está satisfactoriamente curada si el laminado no resulta pegajoso al tacto. Este test sólo es significativo si está hecho en la barrera química. No es aplicable para una superficie externa, que no está protegida de la inhibición del aire.
El Ensayo de Ultrasonidos permite la detección de falta de adhesivo de unión, de delaminación o vacíos y de desviaciones en el espesor de la pared7.
Vacíos y zonas de falta de adherencia pueden ser detectados usando métodos estándares de US a resoluciones de 10mm y a profundidades de más de 10mm. En áreas de pobre adhesión, ej. uniones enfrentadas (“kissing bonds”) este método no es aplicable. Las delaminaciones se pueden detectar con una resolución similar a la de los vacíos.
Variaciones del espesor de la pared del orden del 5-10% pueden también ser determinadas. El personal que lleve a cabo la inspección debe estar certificado con el nivel 2 NDT (como mínimo) en los Estados Unidos, como se describe en la SNT-TC-1A por la Sociedad Americana para NDT. Se usan métodos manuales y automáticos. El método manual A-scan es usado en la planta de Stade (Alemania) desde 1988 para medir espesores de los equipos en FRP. El sistema automático P-scan8 se utiliza desde 1992 para detectar defectos de fabricación y si es necesario mantener los equipos bajo control durante su servicio7.
La Radiografía es de gran utilidad para detectar variaciones de espesor en las paredes, inclusión de agua, formación de incrustaciones y vacíos, ej. falta de adhesivo en uniones pegadas. Áreas de pobre adhesión, ej. uniones enfrentadas (“kissing bonds”) no serán detectadas por este método. Las limitaciones de esta técnica son el coste y la necesidad de fotografiar muchas secciones para conseguir una imagen amplia de los defectos en una zona determinada. Nuevos equipos en tiempo real basados en sistemas de video pueden convertirlo en un método más atractivo.
La planta de Stade (Alemania) aplica este método junto con los ensayos de US. El método radiográfico ha sido puesto a punto en la planta de BSL (Alemania) para realizar mediciones de espesor y detecciones de defectos de laminado como se detalla en el siguiente apartado:
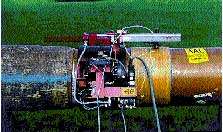
Defectoscopía Radiográfica de Uniones de Laminados
Para proyectos de reparación de tuberías, la Defectoscopía Radiográfica puede sustituir a los ensayos de presión legalmente requeridos.
La Defectoscopía Radiográfica permite verificar los
siguientes elementos de uniones de laminados:
- Excesivo aire atrapado (burbujas)
- Pobre alineamiento de los bordes
- Excesiva anchura de las hendiduras
- Determinación del ángulo de reducción
- Determinación de la extensión del recubrimiento
- Delaminaciones
- Falta de resina en hendiduras
El criterio de evaluación ha sido recopilado y documentado en una especificación (ver apéndice).
Este método puede ser utilizado para diámetros de hasta DN 300. Los ejemplos aparecen en las fotografías 4 y 5.
Determinación del Espesor de la Pared por Radiografía:
determinado por radiografía. Para el defectoscopio radiográfico el diámetro máximo es DN 300. Las secciones de tubería a inspeccionar no deben contener líquido.
Algunos depósitos (ej. manteca clorada) pueden influenciar los resultados al no poder distinguirse la pared y el depósito. Este método se aplica en sistemas de tuberías con entornos que causen abrasión, erosión o cualquier otro fenómeno causante de la reducción del espesor de la tubería en toda su superficie. Mediante una inspección radiográfica regular de los sistemas de tuberías se puede seguir su evolución de una forma más comprensiva que los tests de Presión que requiere la ley.
La Termografía permite la detección del crecimiento de incrustaciones en tuberías, uniones con carencia de adhesivo y desviaciones en el espesor de paredes. El principio de la técnica se basa en las diferencias de la conductividad térmica, capturando a través de una cámara de IR diferencias en la temperatura superficial. El tiempo que ocupa la transferencia de calor al interior de la tubería resulta crucial.
Si este calor se suministra de manera demasiado lenta la conductividad térmica de los materiales permitiría repartir esta energía calorífica a través de todo el material (incluyendo defectos), reduciendo así la resolución del método. Esto provoca que este Método de Ensayo No Destructivo sea menos práctico para depósitos. DOW ha evaluado tanques con esta metodología entre 1977 y 1983. Sin embargo el incremento de temperatura no resultó lo suficientemente grande como para detectar cambios de espesor. También ha llegado a la conclusión, basándose en su experiencia, que las delaminaciones no se detectan de manera fiable con este método.
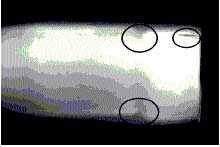
los bordes, ángulo de reducción incorrecto, excesiva
anchura de hendiduras y delaminaciones del recubrimiento.
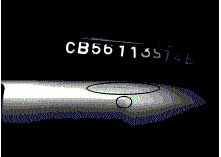
bordes y delaminaciones en el recubrimiento.
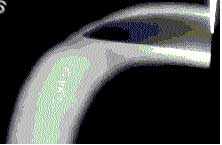
presencia de líquido.