A menudo, menos es más
Clariant GmbH, Gersthofen01/08/2004
Reportaje industria química y plásticos técnicos
Estos criterios también se han tenido en cuenta en el desarrollo de la sustancia ignífuga no halogenada Exolit OP 1312 (TP) M1 de Clariant. Incluso cantidades pequeñas de este aditivo son suficientes para dotar a las poliamidas de protección ignífuga.
Poliamida, un material con enorme potencial de crecimiento
Gracias a estas mejoras, los materiales basados en la poliamida han alcanzado importantes cuotas de mercado en áreas de uso técnico. Su consumo anual se incrementará, hasta el año 2010, en aproximadamente un 7 por ciento a escala mundial, hasta situarse en aproximadamente 3,6 millones de toneladas [1].
La industria electrónica y eléctrica es, junto con la industria automovilística, el sector con mayor consumo de materiales de poliamida con protección ignífuga. En estos sectores, la seguridad contraincendios de los componentes de plástico se encuentra regulada por varios estándares internacionales y nacionales (UL, IEC, DKE, CENELEC; véase recuadro 1), si bien las disposiciones legales en materia de protección ignífuga sin emisiones y ecológica son cada vez más estrictas, más amplias y más uniformes en todo el mundo.
Además, en el proyecto de la Comisión Europea para la Directiva WEEE (Reglamento de desechos eléctricos y electrónicos) se reclaman conceptos de reciclado para todos los materiales [2]. Según este proyecto, los plásticos con contenidos en halógenos tienen que ser recogidos y procesados o, en su caso, reciclados por separado, lo que sólo será posible a un coste sustancialmente superior. Esto causará el uso preferencial de sustancias ignífugas no halogenadas.
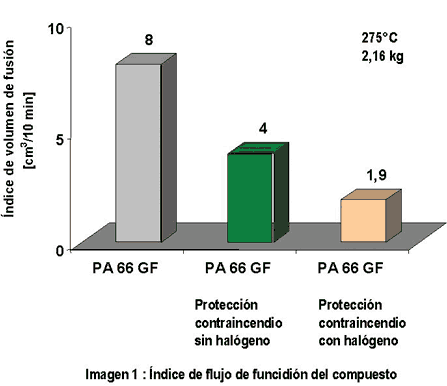
Compuestos organofosfáticos como nueva sustancia ignífuga alternativa
Los compuestos de fosfato tienen un efecto ignífugo, en caso de incendio, el compuesto de fosfato se descompone y genera una densa e impermeable capa de carbono que protege al plástico de una ulterior oxidación. Además, en muchas sustancias ignífugas con base de fósforo se provoca la espumación de esta capa, lo que aísla de las llamas al material aún no incendiado (intumescencia). Como este proceso se produce exclusivamente en la superficie sólida del material, las emisiones son minimizadas, una propiedad extremadamente decisiva para las sustancias ignífugas del futuro. De esta circunstancia también resulta la propiedad positiva de la reducción de la densidad de gas de combustión y la disminución de gases de combustión corrosivos y tóxicos comparado con sustancias ignífugas con contenido en halógeno.
Sin embargo, en el desarrollo de nuevas sustancias ignífugas hay otros aspectos importantes además de los de seguridad y los medioambientales. Para una producción baja en costes también una buena formación de compuestos y la procesabilidad de los polímeros con protección ignífuga ha de ser garantizada. Otro aspecto importante es que por la añadidura de las sustancias ignífugas no se pueden perjudicar las propiedades mecánicas y eléctricas de los materiales de poliamida.
En una serie de pruebas se determinaron las propiedades más importantes de compuestos con Exolit OP 1312 (TP) M1 sin halógenos, de poliamida sin protección ignífuga y de una poliamida con halógenos y con protección ignífuga, comparando a continuación los resultados.
La industria electrónica y eléctrica es, junto con la automovilística, el sector con mayor consumo de materiales de poliamida con protección ignífuga

Condiciones de prueba
Índice de fusión
Propiedades eléctricas
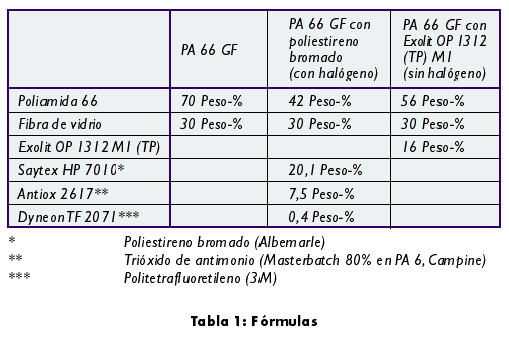
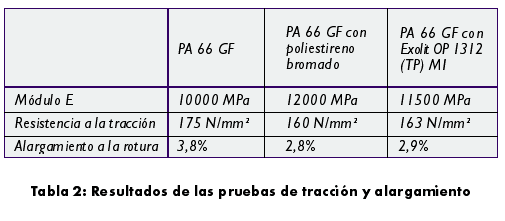
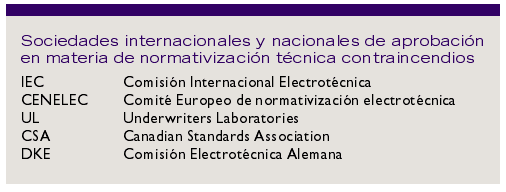
Densidad de los compuestos
El segundo aspecto, y que realmente es más importante, es la posibilidad relacionada de realizar una construcción más ligera, algo que resulta importante sobre todo en el sector automovilístico y en materia de transportes. En la imagen 3 se representan las densidades de los compuestos. Comparado con el material ignífugo con contenido en halógeno, Exolit OP 1312 (TP) M1 ofrece la ventaja de que el efecto de protección contraincendios requerido ya se consigue con reducidas cantidades de aditivos y con una baja densidad del material ignífugo, lo que tiene un efecto positivo sobre la densidad de los compuestos equipados de esta forma.
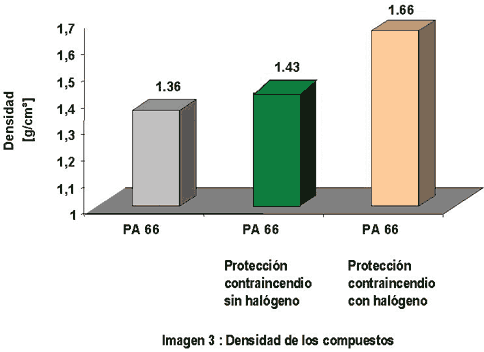

Propiedades mecánicas
Los resultados de la prueba de resistencia al estiramiento están resumidos en la tabla 2. Todos los datos han sido obtenidos con muestras condicionadas (almacenamiento bajo condiciones de clima normal, 23°C, 50 por ciento de humedad relativa) que son también los más representativos del uso cotidiano. Ambos compuestos de protección ignífuga muestran un aumento del módulo E que se debe al efecto de los materiales de relleno. La composición de los compuestos ignífugos no es tan homogénea como en la Poliamida 6.6 GF, por ello la resistencia a la tracción desciende hasta un nivel del 80 por ciento del valor de partida sin protección ignífuga. Sin embargo, esto es suficiente para la mayoría de las aplicaciones. Algo parecido ocurre también con el alargamiento a la rotura. Por lo tanto, los datos de tracción y alargamiento de los dos compuestos con protección ignífuga apenas se distinguen entre ellos.
En resumen hay que constatar que las propiedades mecánicas de ambos sistemas de protección contraincendios apenas se diferencian entre ellos. Ambos cumplen los mismos elevados requisitos en cuanto a la estabilidad mecánica que se exige a la poliamida 6.6 con refuerzo de fibra de vidrio.
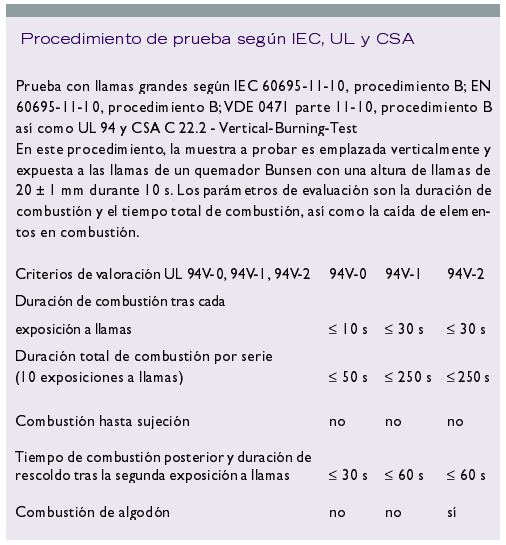
Conclusiones
Por otra parte, los reducidos grados de relleno de la sustancia ignífuga ofrecen, en comparación con los aditivos convencionales con halógenos, unas posibilidades de diseño mucho más amplias en el procesado, así como una mayor funcionalidad de las piezas terminadas. Como, además, el Exolit OP 1312 (TP) M1 es blanco y tiene un poder coloreante reducido, los ajustes de color se pueden realizar sin ningún tipo de problemas. En este sentido, esta nueva categoría de sustancias ignífugas sin contenido en halógenos nos debe hacer esperar evoluciones interesantes tanto de los materiales como de las aplicaciones..
Bibliografía
[2] Directive of the European Parliament and the Council on Waste Electrical and Electronic Equipment, Draft Proposal, Brussels 2001
[3] W. Wanzke, S. Hörold, R. Walz, “Neue Entwicklungen mit Phosphorverbindungen für technische Kunststoffe“, 3ª Jornada Sectorial Plásticos, Sustancias antiincendio e ignífugas, Süddeutsches Kunststoff-Zentrum, Würzburg, 1998, Clariant GmbH