Secado por spray
15 de marzo de 2011
El polvo base no es algo que una empresa pueda desarrollar en solitario, la demanda de los consumidores establece que diferentes beneficios nutricionales y de salud se obtienen a partir del producto. Los departamentos de marketing creen que una serie de envases en constante cambio ganarán cuota de mercado, e investigación y desarrollo siempre estarán desarrollando nuevos productos. Todos estos productos consisten en polvo base mezclado con varias vitaminas, aditivos, colorantes y, más tarde, probióticos.
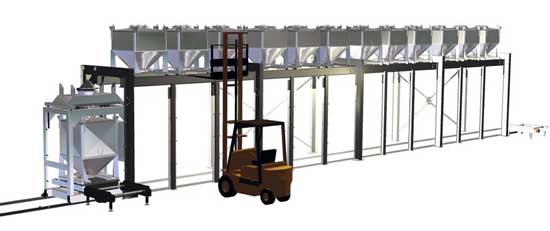
Sin tener en cuenta los desarrollos realizados en la ampliación de la vida útil de estos productos, si el proceso de fabricación no es flexible y ágil, esto conducirá inevitablemente a la fabricación por stock, y no se fabricará para satisfacer los pedidos del cliente. El almacén de productos acabados podría contener enormes existencias. No es raro para las empresas, cuyos procesos de elaboración dictan el nivel de existencias, tener varios millones de euros en inventario, dinero que se podría utilizar de mejor manera.
Si el atomizador es la “planta petrolera”, luego el envasado es todo lo contrario. Las máquinas de envasado son la lancha rápida multidireccional, capaces de arrancar y parar rápidamente, cambiar de dirección varias veces al día (incluso cada hora) y siempre están en una carrera con varias máquinas de envasado. Lo que sucede en el medio es la clave para obtener varios productos en el mercado, sin inventarios masivos.
· Secado por spray
· Formulación
· Mezclado
· Aseguramiento la calidad
· Envasado
· Limpieza
Secado por spray
Se debe ir con cuidado en qué parte del proceso se añaden los ingredientes minoritarios y microingredientes, esto requiere tener en cuenta los daños potenciales que pueden ocurrir si estos ingredientes importantes y sensibles se añaden antes del secado por pulverización. Puede haber daños causados a la funcionalidad de las vitaminas, aditivos y especialmente por los probióticos debido al calor, pero el más importante es que los atomizadores son depósitos enormes que requieren días para poder limpiarlos, por lo que cualquier cambio en la receta (que debe ser una metodología habitual para evitar la acumulación de existencias) significa grandes tiempos de inactividad.
Formulación
La receta de adiciones minoritarias y micro necesarias para producir cualquier variación en el polvo base, ahora pueden formularse fuera de línea ('offline'). Esto simplemente se puede hacer mediante formulación manual o, si los volúmenes son suficientes, es preferible utilizar la formulación automática. Estas fórmulas no mezcladas son luego premezcladas para poder realizar adiciones automáticas a la mezcla base.
Formulaciones minoritarias y micro son siempre añadidas en un IBC ya que son transportables y el premezclado se puede llevar a cabo en el IBC. El beneficio de mezclar en un IBC con un agitador giratorio es que el siguiente IBC puede contener una formulación completamente diferente, por lo tanto no hay ningún mezclador estático a limpiar. La variedad se puede añadir a esta base sin tener que interrumpir la producción.
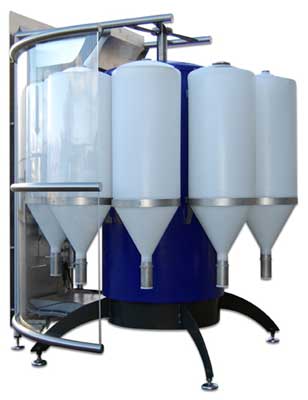
Mezclado
Este se puede realizar por lotes o en continuo. Según los objetivos de estas tareas y debido al hecho de que el mezclado continuo requiere automatización, para una formulación en continua, se amplia la información referente al mezclado por lotes.
· Mezclador giratorio de IBC – el polvo base y la formulación de minoritarios y micros son añadidos a un IBC, y este es posteriormente volteado para producir una mezcla final. Normalmente esto se puede lograr usando el mismo mezclador giratorio utilizado para la formulación de la premezcla.
· Mezclador estático – el polvo base y la formulación pueden ser transferidos en un mezclador estático fijo. Si se usa este tipo de mezclador, el tiempo de limpieza entre diferentes recetas se debe considerar, si bien ahora el número de lotes por hora puede ser bastante alto.
Con un mezclador giratorio, cualquier limpieza entre recetas se lleva a cabo ‘off line’. Aunque el total de lotes que pueden obtenerse es menor, probablemente próximo a los 4 lotes por hora, el tiempo de mezclado para un mezclador giratorio es mayor que el de un mezclador estático.
Asegurando la calidad
Normalmente el aseguramiento de la calidad se lleva a cabo después de la mezcla, pero antes del envasado. Esto puede comportar muchas tareas de trabajo que podrán implicar un importante retraso, hasta 24 horas en garantizar la calidad. Trabajando a 5 toneladas por hora, significa que más de 100 toneladas están a la espera de poder pasar el control de Aseguramiento de la Calidad para controlar el producto y tenerlo listo para el envasado. La alternativa actual consiste en permitir realizar el envasado al mismo tiempo que se controla la calidad mediante la verificación del producto. La trazabilidad es esencial para permitir que esto suceda, sin embargo, esto sólo significa trasladar las 100 toneladas al almacén de productos terminados.
Una fábrica bien diseñada permitirá tener un proceso que deberá ser validado. Siempre que las materias primas entren en el proceso de forma constante y dentro de un margen de tolerancia, no será necesario comprobar la calidad del producto terminado. La excepción a esto son controles periódicos de la calidad para asegurar que la validación se mantiene. Un compromiso sensible se basa en el procedimiento de control de la calidad en una escala reducida, permitiendo al producto ser envasado e introducido en la cadena logística. En el caso de cualquier no conformidad del producto, puede ser recuperada antes de que sea en la plataforma, debido a la trazabilidad del producto.
Envasado
Debido a los constantes cambios en los tamaños de envase y de las recetas de los productos, es habitual disponer de varias máquinas de envasado. Cuando el proceso incluye un mezclador estático fijo, es esencial separar el mezclador de las máquinas de envasado para permitir la flexibilidad de la producción. En caso de utilizar un mezclador giratorio de IBC, el mezclador ya está desconectado y permite el transporte del producto a la máquina de envasado, permitiendo al IBC rígido ser utilizado para la mezcla.
Los IBC permiten una total flexibilidad con cualquiera de los procesos de mezcla. Si la exigencia de grandes cantidades de producto en una cola de garantía de calidad se ha eliminado, entonces el número de IBC se reduce.
Se puede llegar a producir en líneas de envasado con capacidades superiores a 15 toneladas por hora. Estas máquinas normalmente superan el nivel de producción del secador por pulverización, por lo tanto nos podríamos preguntar si se podrían utilizar 3 o 4 máquinas más pequeñas y económicas, dando una mayor flexibilidad a la producción. La verdad es que el 'Lean' no se usa sólo para utilizar una sola máquina de envasado de grandes dimensiones 4 horas y luego tenerla que limpiar durante 6 horas, sino que sería más eficiente poder utilizar 2 o 3 máquinas durante 8 horas y luego limpiarlas 2 horas.
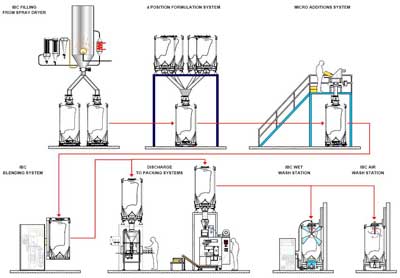
Limpieza
La utilización de IBC para el premezclado entre el mezclador y las máquinas de envasado elimina el uso de sistemas neumáticos estáticos, que son difíciles de limpiar. Limpiando los IBC 'off line' se puede tener una producción continua. Tradicionalmente, esto se ha hecho utilizando el agua como medio de lavado, sin embargo, tratándose de un lavado convencional requiere mucho tiempo y el ciclo de secado puede ser hasta 40 minutos. La limpieza por aire de los IBC ya está disponible, de esta manera se pueden reducir los tiempos de limpieza alrededor de 10 minutos, con la ventaja de que no haya efluentes, únicamente el polvo del aire a tratar. El número de IBC se pueden reducir sustancialmente, ya que se devuelven al proceso en cuestión de minutos.
Conclusiones
Si la filosofía 'Lean Manufacturing' se emplea después del secado por pulverización, el uso de un sistema IBC es de suma importancia para permitir:
· Premezclado de los minoritarios y micros.
· Separar el mezclador con la cadena de envasado.
· Trazabilidad de los lotes
· Posibilidad de mezclar el producto final
No hay razón para que las instalaciones no puedan fabricar los pedidos del cliente o lograr previsiones semanales e incluso diarias. Los productos terminados almacenados deben ser una cosa del pasado, al igual que grandes cantidades de productos semi-terminados en una cadena de procesos.