Lubricar o no lubricar, esa es la cuestión
El uso de fluidos de corte se hace esencial a la hora de preservar o incluso mejorar la integridad superficial de las piezas durante el mecanizado. Por ello, éstos forman parte esencial del día a día en los talleres. De hecho, el control de las técnicas de refrigeración y lubricación implica directamente un aumento de la productividad y una drástica reducción de costes no sólo económicos sino también medioambientales. Hay que tener en cuenta que el uso de fluidos de corte puede llegar a representar entre el 7% y 17% del coste de fabricación de una pieza [1], pudiendo llegar a oscilar entre el 20% y 30% en materiales de difícil maquinabilidad cuyo uso en el sector aeronáutico cada vez es más habitual [2].
Taladrina a alta presión
El mecanizado con taladrina a alta presión se basa en la inyección de un chorro de taladrina a más de 30 bares. En el caso del torneado, como se puede apreciar en la figura 1, se utilizan portaherramientas específicos los cuales están dotados de unas toberas que dirigen el chorro generalmente a la cara de desprendimiento del inserto y en algunos casos también a la cara de incidencia. De este modo se consiguen dos efectos. El primero es lograr un menor rozamiento entre la herramienta y la pieza. El segundo es que se consigue controlar la direccionalidad de la viruta. La unión de ambos fenómenos se traduce en un menor desgaste de la herramienta frente a la utilización de taladrina tradicional. Además, el caudal de esta se reduce drásticamente, lo que implica menores cantidades de emulsiones de taladrina a almacenar, tratar y eliminar una vez terminada su vida útil.
En cuanto a fresado, debido a que la herramienta se encuentra en constante giro se puede optar por dos opciones. La primera es utilizar herramientas provistas de conductos internos por los cuales circula la taladrina, siendo ésta inyectada en la cara de incidencia de la fresa. La otra opción es la utilización de tobera direccionables las cuales son dirigidas a la zona de corte en función de la longitud de la herramienta. Ambas opciones son mostradas en la figura 2.
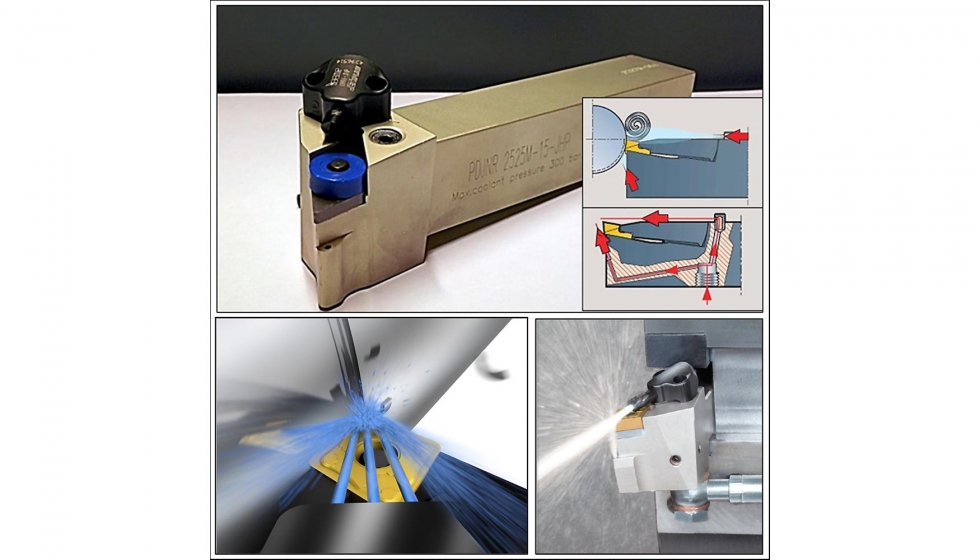
![Figura 2. Fresado con taladrina a alta presión. [3-5] Figura 2. Fresado con taladrina a alta presión. [3-5]](https://img.interempresas.net/fotos/1459641.jpeg)
Con ambas tecnologías el factor clave es la presión a la que se inyecta la taladrina. Un claro ejemplo donde se estudió dicha influencia está en la revista Precision Engineering [6]. En dichas pruebas se torneó una aleación de titanio (Ti17), utilizada en aeronáutica para la fabricación de los discos de presión-media del compresor, la cual se mecanizó con una velocidad de corte de 88 m/min, una profundidad de pasada de 1,5 mm y un avance por vuelta de 0,1 mm/rev. Durante los tests se probaron diferentes insertos bajo diferentes presiones de inyección de la taladrina. Los resultados mostrados en la figura 3 resaltan como a medida que aumenta la presión la vida de herramienta es mayor. Esto se debe al efecto que la fuerza con que incide la taladrina en el filo de corte evite un desgaste prematuro de ésta.
![Figura 3. Vida y estado de insertos utilizados [6] Figura 3. Vida y estado de insertos utilizados [6]](https://img.interempresas.net/fotos/1459643.jpeg)
Mínima cantidad de lubricación (MQL)
Sin embargo, en caso de querer reducir al máximo el uso de fluidos de corte la mínima cantidad de lubricación se presenta como una solución en la que los consumos de aceite de corte se reducen a caudales que oscilan entre 10 y 100 ml/h. Además, presenta otra ventaja característica de esta tecnología de lubricación y es la posibilidad de utilizar aceites biodegradables durante su utilización. La reducción de caudales se consigue gracias a la pulverización del aceite en forma de micropartículas mediante efecto Venturi. Con ello se consigue inyectar una fina película de aceite entre la zona de interacción herramienta-viruta con la cual se consigue una lubricación que supera a la obtenida con la taladrina tradicional y una mayor estabilidad térmica. Además, el uso de esta tecnología implica obtener virutas prácticamente limpias a la vez que se aumenta la higiene industrial de los talleres.
Actualmente existen dos tipos de tecnología MQL (figura 4). Una donde la pulverización se obtiene en la salida del sistema de inyección y otra donde la pulverización se genera en un atomizador anterior al sistema de inyección [7]. Los equipos que utilizan la primera técnica se conocen como ‘MQL de dos canales’ debido a que el aceite y el aire circulan por conductos separados hasta el momento de la inyección. En cambio, los equipos que utilizan la segunda técnica se denominan ‘equipos MQL de un canal’ debido a que el aerosol ya formado es conducido hacia la zona de corte por un solo conducto [8].
![Figura 4. Tipos de tecnología MQL [9] Figura 4. Tipos de tecnología MQL [9]](https://img.interempresas.net/fotos/1459644.jpeg)
Esta tecnología es principalmente indicada para materiales donde las cargas térmicas sobre la herramienta no tienen tanta influencia en el desgaste de la herramienta como las cargas mecánicas. Este es el caso de las aleaciones de aluminio o aceros al carbono. En el primer caso, cabe destacar una investigación llevada en el taller mecánico de la ETSI de Bilbao (UPV/EHU) donde se fresó 5083-H112 a una velocidad de corte de casi 1.000 y 5.000 mm/min de avance. La herramienta utilizada fue una fresa de acero rápido (HSS) con un 8% de cobalto de 12 mm de diámetro y dos labios. Al comparar la lubricación mediante MQL durante el mecanizado a alta velocidad frente al uso de taladrina se observó cómo con la lubricación MQL se conseguía una mayor productividad gracias al aumento de corte en combinación con un menor desgaste de la herramienta debido a la penetración de las partículas de aceite en el filo de corte frente a la taladrina [10]. Esta cualidad es de gran interés para sectores como el aeronáutico donde el uso de este tipo de aleaciones de aluminio tiene gran importancia en las estructuras de la aeronave. En referencia a los aceros al carbono, cabe destacar una investigación publicada en Journal of Material Technology donde se tornea un acero AISI 9310 con un inserto de metal duro sin recubrir. En dicha investigación se concluyó que al utilizar la lubricación MQL el desgaste se reducía un 60% después de 45 minutos de mecanizado frente a la taladrina gracias a la mejor penetración de las micropartículas de aceite en la intercara herramienta/viruta [11]. De hecho, este fenómeno también fue estudiado mediante elementos finitos en la UPV/EHU donde se demostró que el uso de MQL implica una mejor penetración del fluido en la zona de corte (figura 5).
![Figura 5. Simulación de inyección de taladrina vs. MQL con fresa girando a 24.000 rpm [10] Figura 5. Simulación de inyección de taladrina vs. MQL con fresa girando a 24.000 rpm [10]](https://img.interempresas.net/fotos/1459645.jpeg)
Refrigeración criogénica
Aunque la lubricación MQL está teniendo una gran aceptación en el día a día de los talleres de mecanizado, la refrigeración criogénica presenta otras ventajas que hacen que a día de hoy esté en auge su implementación en sectores de fabricación médica y aeroespacial debido a las exigencias de limpieza que se necesitan para mecanizar el tipo de piezas desarrolladas en esa rama industrial.
La refrigeración criogénica consiste en aplicar un gas licuado a muy baja temperatura como fluido de corte. Generalmente por coste y aplicabilidad se suele utilizar nitrógeno líquido (LN2) o dióxido de carbono licuado (CO2). El primero presenta ventajas como que es abundante en la atmósfera y alcanza los -196 °C al evaporarse. Sin embargo, debido a que debe ser almacenado a -198 °C en depósitos aislados se encuentra en constante ebullición lo que hace que durante su almacenamiento exista una pérdida constante de éste. Por ello, el CO2, a pesar de alcanzar los -78 °C una vez inyectado, se posiciona como la mejor opción a la hora de ser utilizado industrialmente. No obstante, debido a las características físicas de este fluido necesita un equipo de inyección que posibilite su utilización como fluido de corte. Concretamente, lo que se evita con dicho equipo es la formación de hielo seco en los conductos que obstruyan su paso a través de ellos. En esta línea, la UPV/EHU junto con Tecnalia llevan trabajando varios años y actualmente, han desarrollado un equipo ‘plug & play’ mostrado en la figura 6.
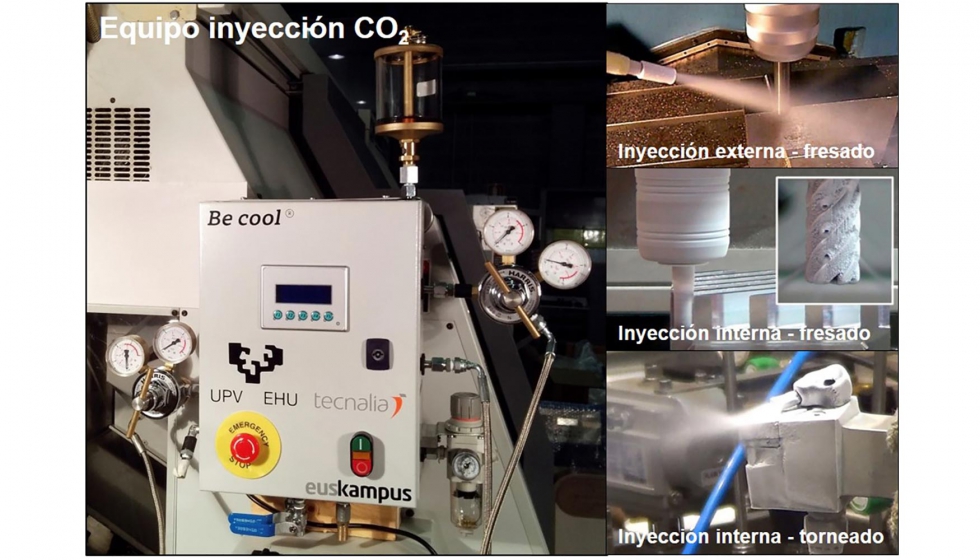
Figura 6. Equipo de inyección de CO2 y sus aplicaciones.
En cuanto su aplicabilidad durante el mecanizado, la refrigeración criogénica cobra valor en aleaciones de difícil maquinabilidad como las de titanio, que combinan una alta dureza con ductilidad. Además, en el caso concreto de esta aleación hay que tener en cuenta la alta reactividad que presenta este material con el cobalto de las herramientas de metal duro y las altas temperaturas de corte alcanzadas (>600 °C). En esta tesitura, para su fresado, la refrigeración criogénica por el interior de las herramientas se presenta como una solución, incluso para desbastes mediante fresado trocoidal. Con esta técnica, al expandir el CO2 en el interior de la herramienta, ésta se convierte en un intercambiador de calor que hace que su temperatura sea inferior a la de corte posibilitando aumentar las condiciones de corte o en su defecto aumentar la vida de herramienta. Además, la refrigeración criogénica interna hace que se puedan utilizar herramientas de diamante policristalino (PCD) sin que alcance su temperatura de grafitización. Esto supone una gran ventaja con el fin de aumentar la productividad gracias a la capacidad de este tipo de herramientas a utilizar condiciones de corte más agresivas.
Por otra parte, este tipo de técnica también es de especial relevancia para el taladrado de composites utilizados en las estructuras de las aeronaves. En la UPV/EHU se realizaron unos ensayos en este sentido donde se comparó el taladrado de stacks conformados por Ti6Al4V-CFRP utilizando CO2 como fluido de corte. Los resultados mostraron como al utilizar el CO2 se eliminaban las marcas de quemado presentes en el CFRP al mecanizar en seco (figura 7).
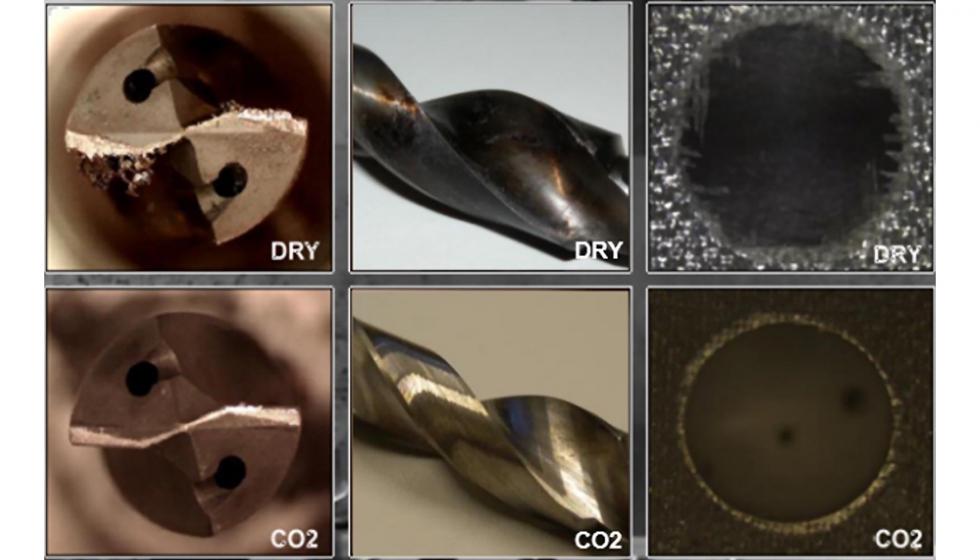
Mecanizado en seco
El mecanizado en seco presenta la gran ventaja de eliminar totalmente los fluidos de corte de las máquinas-herramienta. En esta situación el uso de herramientas recubiertas con materiales laminares que funcionen como lubricantes sólidos se convierte en una opción factible. Generalmente, los materiales que se utilizan para recubrir las herramientas son el grafito y disulfuro de molibdeno (MoS2). Al utilizar estos materiales se reduce el rozamiento entre la viruta y la herramienta, reduciéndose por tanto la temperatura de corte y consecuentemente también las fuerzas de corte [12].
Sin embargo, la utilización de herramientas formadas por nitruro de boro cúbico policristalino (PCBN), diamante policristalino (PCD) o cerámicas es lo que hoy en día tiene más calado industrialmente. En el caso de las herramientas de PCBN y PCD, éstas tienen la característica de estar compuestas normalmente por un cuerpo de metal duro a las que se adhiere un inserto de dicho material. Este tipo de herramientas son idóneas sobretodo indicadas para procesos estables debido a la gran fragilidad que presentan a pesar de su gran dureza. En el caso de las cerámicas, éstas están formadas por óxidos de aluminio, Sialon o nitruro de silicio, las cuales son sinterizadas a alta temperatura.
El PCD está indicado sobretodo en materiales no férreos ya que con aceros y fundiciones se produce un fenómeno complejo de grafitización del diamante, lo que degenera la herramienta en muy poco tiempo. En cambio, el PCBN se aplica a materiales férreos, sobretodo en fundiciones y aceros templados. Sin embargo, también posee cierta afinidad con la ferrita por lo que el porcentaje de CBN presente en la herramienta es un factor crítico. Concretamente para fundiciones se suele utilizar herramientas con un alto contenido de CBN (80-90%) y para aceros porcentajes que rondan el 40-50%. En el caso de las cerámicas, cabe destacar lo que se conoce como cerámicas reforzadas con carburos de silicio hasta un 40%, los cuales le aportan tenacidad a la herramienta.
Un ejemplo claro del uso de este tipo de herramientas se da en el sector de la automoción. En este sector el uso de herramientas de PCBN es de gran utilidad para torneado de piezas de más de 45 HRc (normalmente entre 58-64 HRc). Gracias al uso de este tipo de insertos, se consiguen acabados superficiales que alcancen los 3 micrómetros, aumentando la productividad hasta 6 veces frente al rectificado. En la figura 8 se muestra un diagrama de red donde se compara el torneado con este tipo de herramientas frente al rectificado convencional.
![Figura 8. Comparación Torneado en duro vs. Rectificado [13] Figura 8. Comparación Torneado en duro vs. Rectificado [13]](https://img.interempresas.net/fotos/1459649.jpeg)
Conclusión
Como se ha podido analizar, aunque la taladrina es lo que viene utilizándose convencionalmente, actualmente existen alternativas que minimizan el uso de fluidos de corte durante el mecanizado o incluso se consigue su completa eliminación del día a día de los talleres. Gracias a ellas se puede avanzar desde tres puntos de vista: El primero, el económico ya que una reducción de fluidos de corte se traduce en ahorro en costes en su compra, mantenimiento y disposición final una vez terminada su vida útil. El segundo, en cuanto a la mejora de la salubridad e higiene en los puestos de trabajo. El tercero, se trata de la reducción del impacto ambiental derivado del uso de los fluidos de corte, el cual puede ser prácticamente eliminado. Por tanto, ¿se debe lubricar o no? La respuesta es simple: Depende.
Referencias
[1] F. Klocke, G. Eisenblatter. Dry cutting, CIRP Annals – Manufacturing Technologies, Vol 46, 1997, pp. 519-526.
[2] A. Shokrani, V. Dhokia, S. Newman. Environmentally conscious machining of difficult-to-machine materials with regard to cutting fluids. International Journal of Machine Tools and Manufacture, Vol. 57, 2012, pp. 83-101.
[3] http://www.directindustry.com/prod/iscar-tools-5692.html (visitada el 6 de Marzo)
[4] http://www.sandvik.coromant.com/us/News/technical_articles/Pages/Troublesome-Titanium-Tips-on-machining.aspx (visitada el 8 de Marzo)
[5] http://spidercool.com/ (visitada el 8 de Marzo)
[6] Y. Ayed, G. Germain, A. Ammar, B. Furet, Tool wear analysis and improvement of cutting conditions using the high-pressure water-jet assistance when machining the Ti17 titanium alloy, Precision Engineering, Vol. 42, 2015, pp. 294-301.
[7] A. Sharma, A. Tiwari, A. Dixit. Effects of Minimum Quantity Lubrication (MQL) in machining processes using conventional and nanofluid based cutting fluids: A comprehensive review, Journal of Cleaner Production, Vol. 127, 2016, pp. 1-18.
[8] A. Attanasio, M. Gelfi, C. Giardini, C. Remino. Minimal quantity lubrication in turning: Effect on tool wear, Wear, Vol. 260, 2006, pp. 333-338.
[9] V.P. Astakhov. Ecological machining: near dry machining. Mechanics of machining: FEM simulation machining, 2009, pp. 195-223.
[10] L.N. López de Lacalle, C. Angulo, A. Lamikiz, J.A. Sánchez. Experimental and numerical investigation of the effect of spray cutting fluids in high speed milling, Journal of Materials Processing Technology, Vol. 172, 2006, pp. 11-15.
[11] M. Khan, M. Mithu, N. Dhar. Effects of minimum quantity lubrication on turning AISI 9310 alloy steel using vegetable oil-based cutting fluid, Journal of Materials Processing Technology, Vol. 209, 2009, pp. 5573-5583.
[12] O. Gonzalo, H. Jauregi, L.G. Uriarte, L.N. López de Lacalle. Prediction of specific force coefficients from a FEM cutting model, International Journal of Advanced Manufacturing Technology, 2009. doi:10.1007/s00170-008-1717-9.
[13] F. Klocke, E. Brinksmeier, K. Weinert. Capability Profile of Hard Cutting and Grinding Processes, CIRP Annals, Vol. 54, 2005, pp. 22–45.