La EDAR de Lagares contará con las tecnologías más avanzadas de Veolia
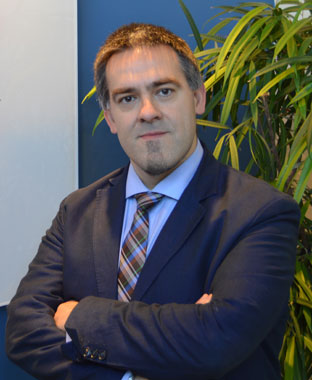
El proyecto de ampliación y modernización de la EDAR de Lagares (Vigo), adjudicado a la UTE EDAR de Lagares, es una actuación acometida por AcuaEs, Augas de Galicia y Concello de Vigo que supondrá una inversión total de casi 230 millones de euros (IVA incluido), incluyendo las obras complementarias (emisario submarino y subestación eléctrica). La nueva EDAR será una de las más grandes de España por biofiltración y una de las mayores de Europa, con una capacidad de tratamiento equivalente a 800.000 habitantes. El objetivo principal de esta instalación es mejorar la calidad de vertido de agua a la ría y minimizar el impacto medioambiental, reduciendo la emisión de olores y ruidos, consiguiendo así una máxima integración de la instalación en su entorno. Veolia Water Technologies se encarga del diseño, construcción y puesta en marcha de los procesos Biostyr, Actiflo y Biocon (las tres son marcas registradas).
1.- Tratamiento biológico. Proceso Biostyr
El tratamiento biológico se basa en el proceso Biostyr para la biofiltración de flujo ascendente por agua y aire que permite la eliminación de materia orgánica, sólidos en suspensión y nitrógeno, con una capacidad máxima de tratamiento 3,28 m3/s.
Biostyr es un proceso muy compacto, que ha permitido reducir el espacio ocupado ya que el agua tratada es de alta calidad y no requiere decantación secundaria. Además, gracias a esta compacidad, el 45% del proceso se ha realizado de forma soterrada.
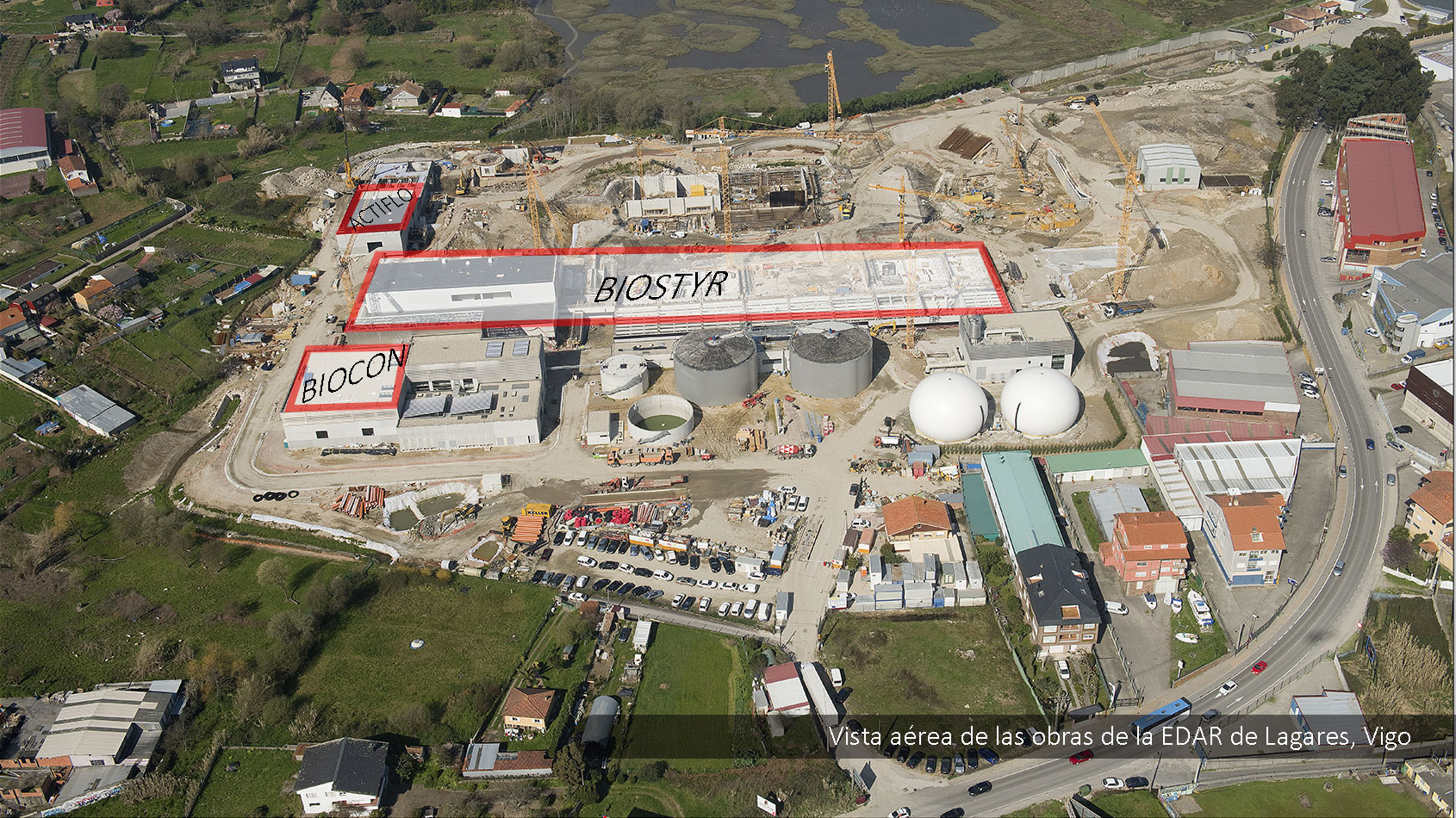
Una de las principales características del proceso Biostyr es el empleo de un lecho de pequeñas bolas flotantes muy ligeras fabricadas en poliestireno granular, denominado Biostyrene, especialmente diseñado para aguas residuales con alto contenido de DQO soluble. El peso específico del medio en la EDAR de Lagares es de 50 kg/m3.
Biostyrene queda flotando y retenido gracias a que un falso techo impide su salida. El aire de proceso es suministrado a través de una parrilla situada en el fondo de las celdas, parrilla que en el caso de las celdas anóxicas sólo se emplea durante los lavados.
Ventajas del empleo de Biostyrene
Una de las principales ventajas del empleo de Biostyrene en el proceso Biostyr es que no existe necesidad de reponer en ningún momento dicho relleno en una celda, puesto que éste no sufre desgaste. Este hecho redunda en una continuidad y estabilidad de la eliminación de contaminación incluso a largo plazo.
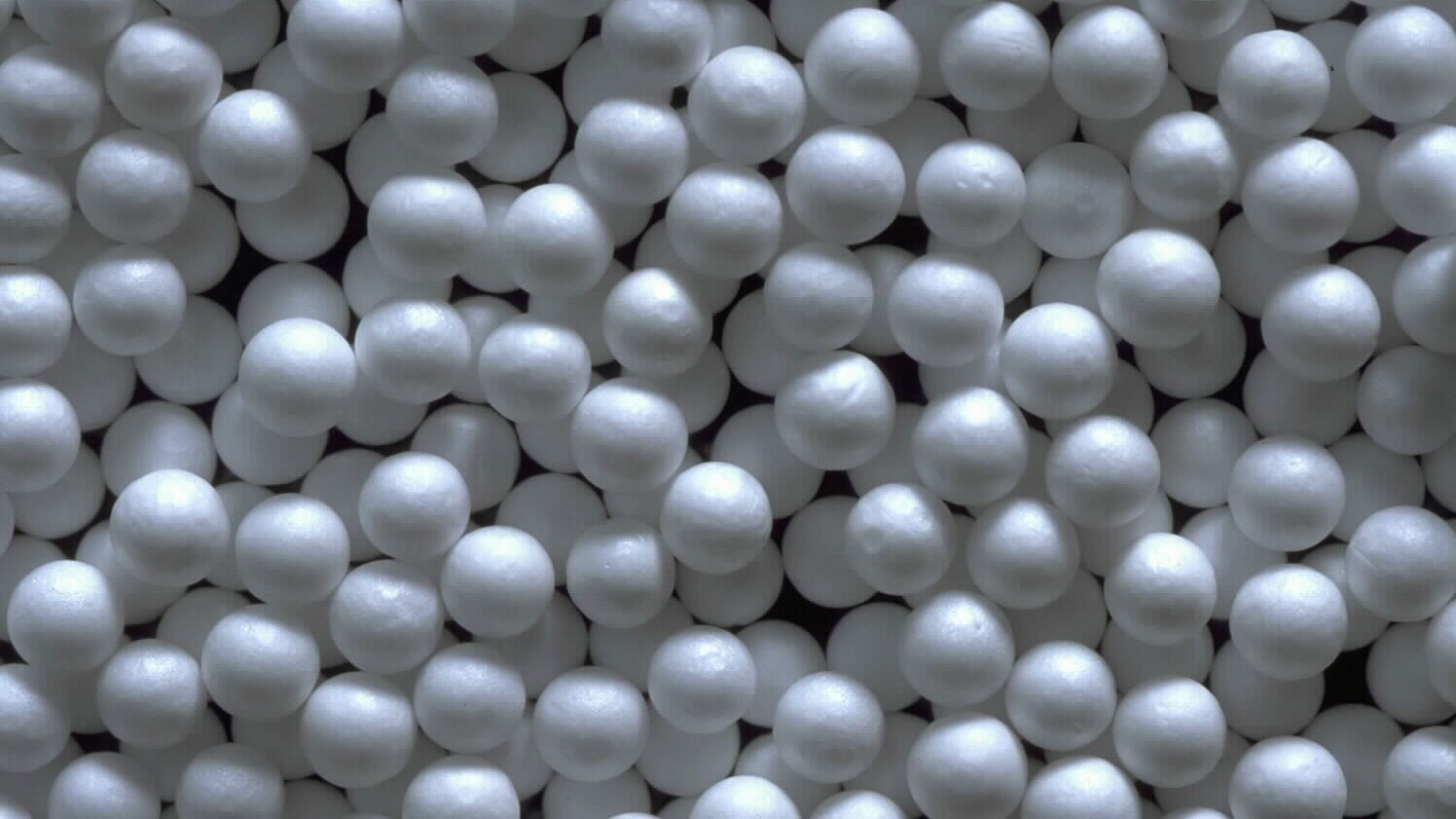
El falso techo está compuesto por placas prefabricadas estandarizadas de unos 7 m2 en donde se equireparten injertos para enroscar las boquillas de polipropileno que impiden que el medio filtrante salga con el efluente. La accesibilidad a estas boquillas es por consiguiente fácil y rápida, sin necesidad de vaciar toda la celda, además de entrar en contacto únicamente con agua ya tratada y filtrada.
Descripción del proceso de biofiltración
Todas estas características de la tecnología hacen que siempre el agua ya tratada esté en contacto con la atmósfera, incluso durante los lavados, puesto que de hecho será esa agua la empleada para esos lavados, traduciéndose en menores costes de operación y mayor respeto medioambiental al reducir las emisiones de CO2.
El proceso de biofiltración se ha construido en dos etapas, la primera para desnitrificar y la segunda para nitrificar. Tras estas etapas, el proceso consigue alcanzar una calidad de agua biofiltrada de 10 mg/l de N-total durante las situaciones de percentil 50 (actual y futuro), con una capacidad hidráulica máxima de 5,24 m3/s, considerando todas las corrientes de retorno (ej: efluente del agua de lavado tratada).
Las dos etapas son:
- Etapa 1: biofiltración con predesnitrificación en celdas anóxicas (Biostyr PreDN)
- Etapa 2: biofiltración con nitrificación en celdas aerobias (Biostyr N).
Configuración del proceso Biostyr
Celdas Predesnitrificación | Primera etapa |
Número de celdas | 10 |
Superficie unitaria de celda | 173 m2 |
Volumen unitario de celda | 518 m3 |
Altura total de medio filtrante | 3,0 m |
Tamaño de medio filtrante | 4,5 mm |
Celdas Nitrificación | Segunda etapa |
Número de celdas | 18 |
Superficie unitaria de celda | 215 m2 |
Volumen unitario de celda | 667 m3 |
Altura total de medio filtrante | 3,1 m |
Tamaño de medio filtrante | 3,6 mm |
Etapa de desnitrificación en Biostyr PreDN
Para completar la eliminación de nitrógeno, los nitratos producidos en el Biostyr N deben convertirse en nitrógeno libre. Este proceso se llama desnitrificación y se lleva a cabo por bacterias heterótrofas que utilizan la materia orgánica del propio afluente como fuente de energía y carbono.
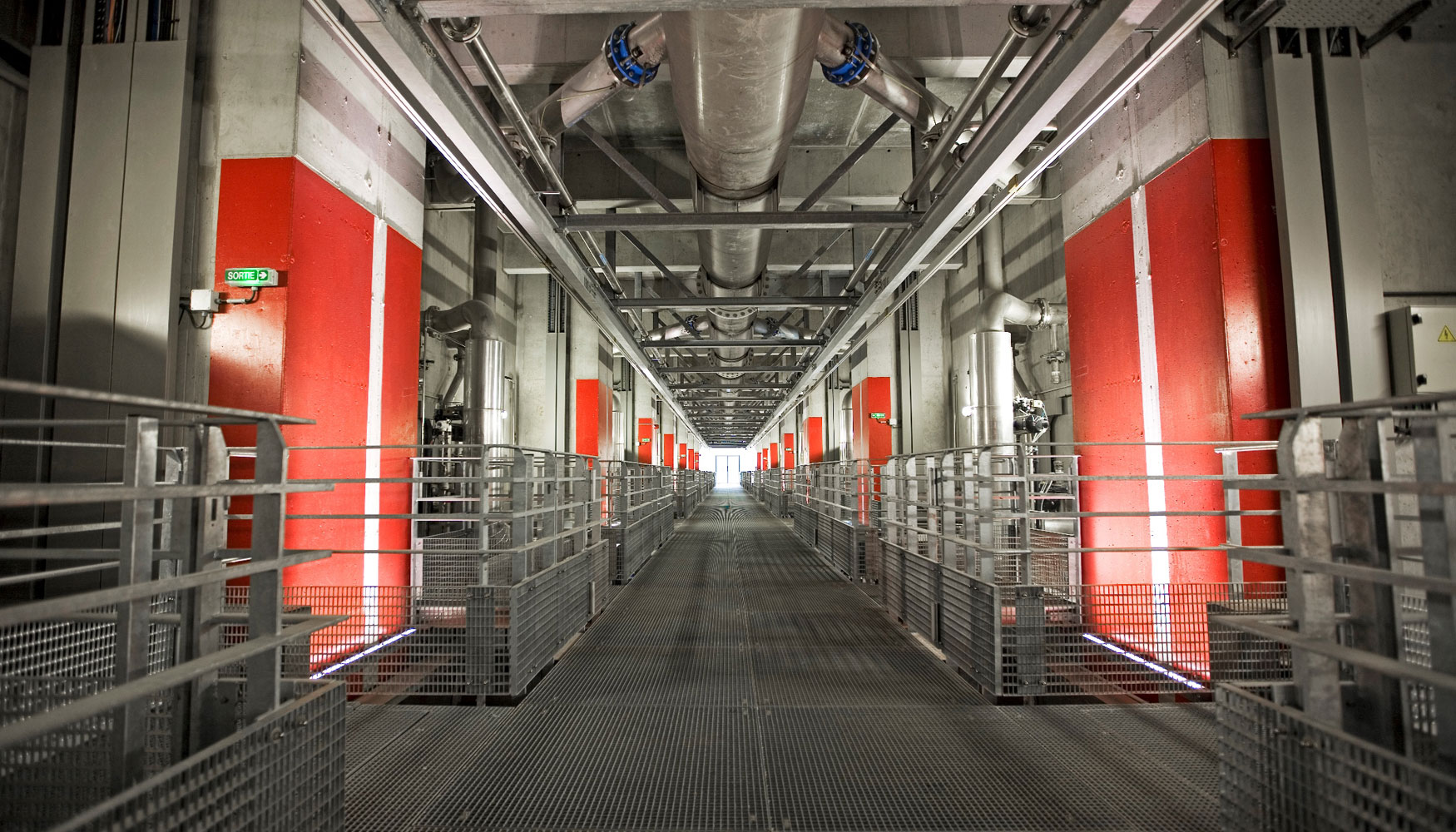
El agua bruta, procedente del tratamiento primario y del efluente del tratamiento conjunto del agua de lavado del Biostyr y de los fangos del Actiflo terciario, junto con la corriente rica en nitratos que se recircula desde la salida de Biostyr N, entra en las celdas PreDN. Aquí, las bacterias unidas al medio filtrante Biostyrene™ forman un biofilm que cubre su superficie y es donde el nitrato se convierte en nitrógeno libre.
Etapa de nitrificación en Biostyr N
El efluente del Biostyr PreDN entra en las celdas N. En esta etapa igualmente proliferan las bacterias que se adhieren al Biostyrene para formar un biofilm que cubre toda su superficie.
En esta zona aerobia, diferentes grupos de bacterias utilizan el oxígeno y la materia orgánica para formar biomasa (fango) y utilizan NH4-N junto con carbono inorgánico (HCO3) y oxígeno para formar biomasa y NO3-N. Son las denominadas bacterias autótrofas.
En esta etapa tiene lugar la transformación del nitrógeno y la eliminación de los compuestos orgánicos que quedan, para lo que es necesario introducir oxígeno, gracias al empleo de una parrilla de aireación situada en el fondo del filtro. La parrilla consiste en un número de tuberías en acero inoxidable con orificios distribuidas sobre la superficie del fondo del filtro. El aire que sale de los orificios lleva oxígeno a las bacterias situadas en el biofilm.
El agua tratada, que contiene el nitrato formado, abandona la celda a través del falso techo. Para eliminar parte de este nitrato, se recircula al canal de entrada de la primera etapa, consiguiéndose así un efluente final con menos de 10 ppm de nitrógeno total.
Contralavado
Como las celdas filtrantes se van ensuciando gradualmente, unas válvulas de apertura automática situadas en la base del filtro garantizan el contralavado del filtro mediante enjuagues por gravedad, alternados con expansiones del medio por aire.
Existe a su vez una válvula situada en la tubería común de recogida de agua de lavado que permite fijar su velocidad. Finalmente el agua es bombeada para su tratamiento fisico-quimico con decantacion lamelar, originando un efluente que es nuevamente llevado al Biostyr.
Un ciclo de contralavado puede ser completo con fases sucesivas agua - aire, así como simples minilavados donde puede lavarse el medio sólo con agua si así se quisiera.
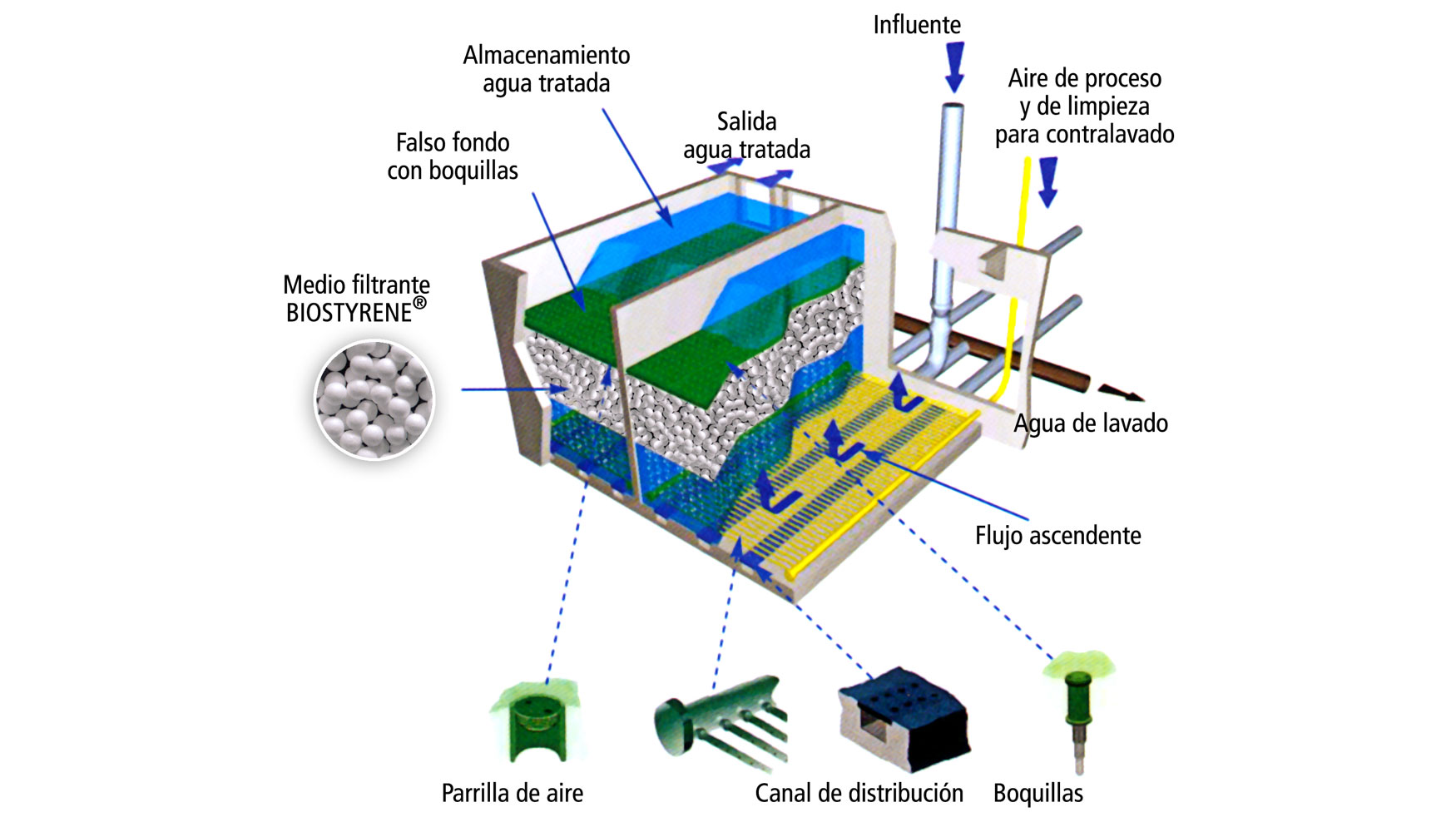
2. Tratamiento terciario para eliminación de fósforo. Proceso Actiflo Turbo
La eliminación de fósforo se realiza mediante el proceso Actiflo Turbo, que ha sido diseñado para el tratamiento del agua residual procedente del tratamiento biológico de la EDAR durante el tiempo seco, con un caudal máximo de 4,42 m3/s.
En el diseño también se ha considerado que en tiempo de lluvias, la planta trate el caudal de agua de tormentas hasta un máximo de 4 m3/s. El caudal mínimo de entrada a la planta en cualquiera de las aplicaciones propuestas será de 0,9 m3/s.
Se proponen dos líneas de Actiflo Turbo que permitirán conseguir la calidad de efluente requerida.
El proceso Actiflo Turbo es un sistema compacto de clarificación que utiliza microarena como precursor para la formación de flóculos. La microarena aporta un área superficial que mejora la floculación y actúa como lastre o peso.
El resultado de la formación de estos flóculos pesados permite un diseño del clarificador con velocidades hidráulicas elevadas y tiempos de retención cortos. Como consecuencia de ello, la superficie necesaria de implantación se reduce de 5 a 20 veces respecto a un sistema convencional de clarificación de similar capacidad.
El proceso Actiflo Turbo está basado en la precipitación química y la decantación lamelar combinada con una tecnología patentada que consiste en la floculación con microarena.
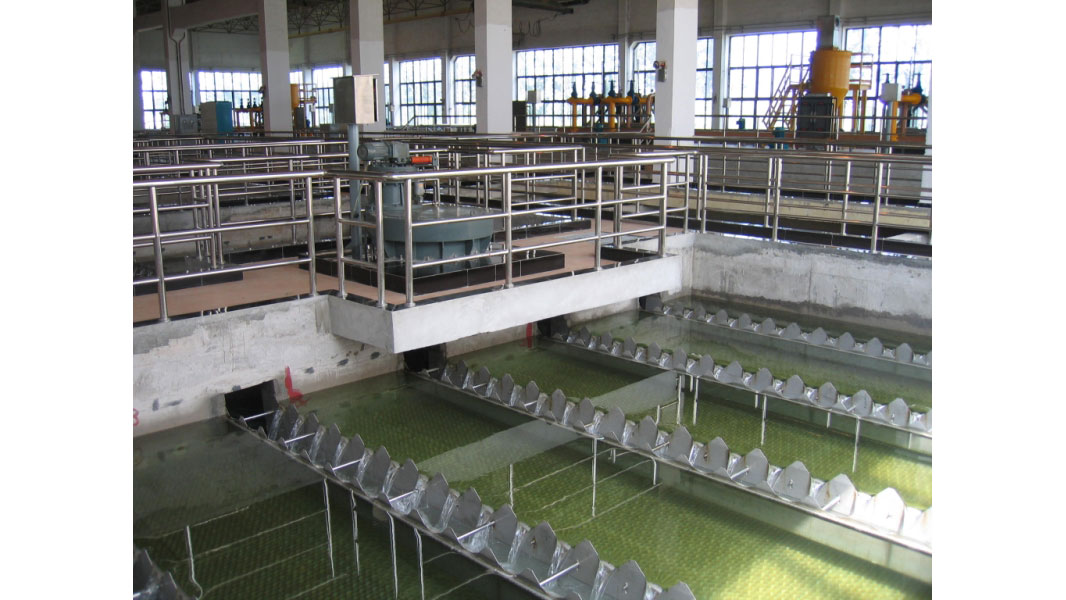
En el sistema Actiflo se añade primero un coagulante al afluente que es conducido al tanque de coagulación. El coagulante es una sal metálica, cloruro férrico o policloruro de aluminio, con la que una parte de la materia disuelta se convierte en una sustancia sólida no soluble en forma de coloide. Dichos coloides son primero desestabilizados químicamente para después ser precipitados gracias a la acción final del floculante (polímero).
El agua bruta se conduce posteriormente al tanque de floculación que está equipado con un dispositivo denominado Turbomix, que mejora la operación del agitador de velocidad lenta de dicho tanque haciendo posible reducir el tiempo de retención. Este dispositivo elimina zonas muertas, evita cortocircuitos y optimiza la agitación al convertir el flujo radial a flujo axial, acercándose a un comportamiento de flujo pistón, lo cual redunda en producir unos flóculos más homogéneos y estables de mejor decantación. En definitiva, se consigue evitar ruptura de flóculos y a su vez incrementar la velocidad de bombeo que lleva intrínseco un ahorro energético respecto al Actiflo clásico.
En el tanque de floculación es donde se añade microarena y se mezcla con el agua. La microarena tiene un tamaño efectivo de aprox. 130 µm (d10), con un peso específico de 2,65 Kg/m3 y un coeficiente de uniformidad < 1,7. En el tanque de floculación, también se añade el floculante, un polímero con una larga cadena de moléculas cargadas.
Después de la floculación, el agua entra en el decantador lamelar. Los flóculos sedimentan rápidamente, puesto que la microarena aumenta considerablemente el peso de los flóculos en comparación con otros procesos de precipitación. Esto implica que la velocidad superficial en el separador lamelar puede ser 30-80 veces superior que la de las plantas de precipitación química convencional.
El agua tratada pasa a través de las lamelas y abandona el proceso Actiflo por los canales de salida, mientras que los fangos decantados y la microarena se extraen del fondo del separador lamelar y se conducen hacia el hidrociclón. El caudal recirculado está comprendido generalmente entre el 4-6% del caudal influente, dependiendo de la aplicación.
La energía para el bombeo se convierte de manera efectiva en fuerza centrífuga dentro del cuerpo del hidrociclón haciendo que el fango químico se separe de la microarena que tiene una densidad superior. Una vez separada, la microarena se concentra y descarga desde la parte inferior del hidrociclón y se reinyecta en el proceso Actiflo Turbo para su reutilización.
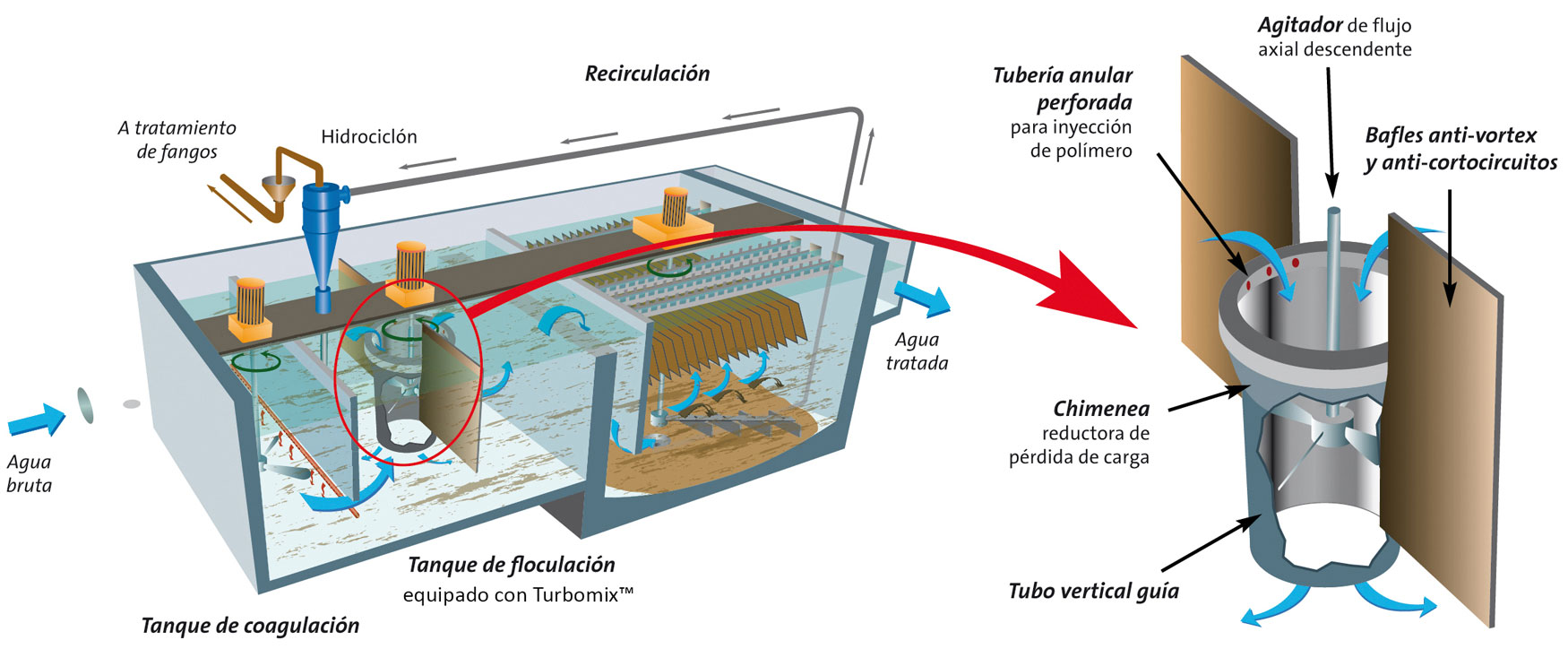
El fango de menor densidad se descarga por la parte superior del hidrociclón. El caudal de fangos es aproximadamente un 3-5% del total de agua tratada.
Bases del diseño
El agua de entrada a las líneas Actiflo Turbo presenta las siguientes características que han sido consideradas para el diseño:
Agua procedente de Biostyr
Caudal máximo | 15.912 m3/h |
Caudal mínimo | 3.240 m3/h |
Concentración media SS | 10-15 mg/l |
Concentración media P-total | 7,8 mg/l |
Agua de tormentas
Caudal máximo | 14.400 m3/h |
Caudal mínimo | 3.240 m3/h |
Concentración media SS | 211 mg/l |
Concentración media DBO5 | 271 mg/l |
Concentración media DQO | 542 mg/l |
Concentración media P-total | 12 mg/l |
Calidad del agua tratada
Se espera la siguiente calidad para el efluente del Actiflo Turbo en tiempo seco.
Calidad esperada en tratamiento terciario (tiempo seco)
P-total | ≤ 1 mg/l |
SS | ≤ 20 mg/l |
Calidad esperada en tratamiento de agua de tormentas
Sólidos en suspensión | ≥ 75% |
DQO | ≥ 45% |
DBO5 | ≥ 45% |
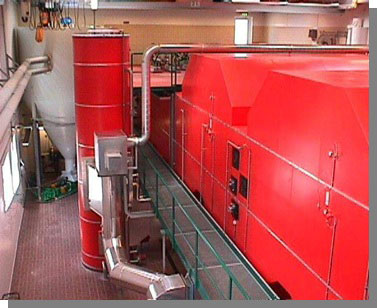
3. Secado térmico de fangos. Proceso BioCon
BioCon es un proceso para el secado térmico a baja temperatura de doble banda que ha sido diseñado para ser uno de los más seguros del mercado, al mismo tiempo que garantiza una operación eficiente y tiene un fácil mantenimiento.
La temperatura en el secador es aprox.171-102 °C en las zonas inicial e intermedia e irá reduciéndose hasta aprox. 90-70°C en la zona final de secado. El tiempo de residencia del fango en el secado es más de 1 hora, con una temperatura superior a 80°C. Por tanto, el fango procedente de una planta de secado BioCon puede ser clasificado como biosólido clase A.
Además, otras de las principales ventajas de este secado térmico son:
- Máxima seguridad al no trabajar con zonas ATEX
- Mínimo coste de explotación
- Simplicidad de operación y mantenimiento
- Cumple la sequedad requerida del 90%
Asimismo, las plantas BioCon no afectan negativamente al medioambiente, ni en lo relativo al ruido, ni al olor, ni al polvo, cumpliendo con la normativa europea a este respecto.
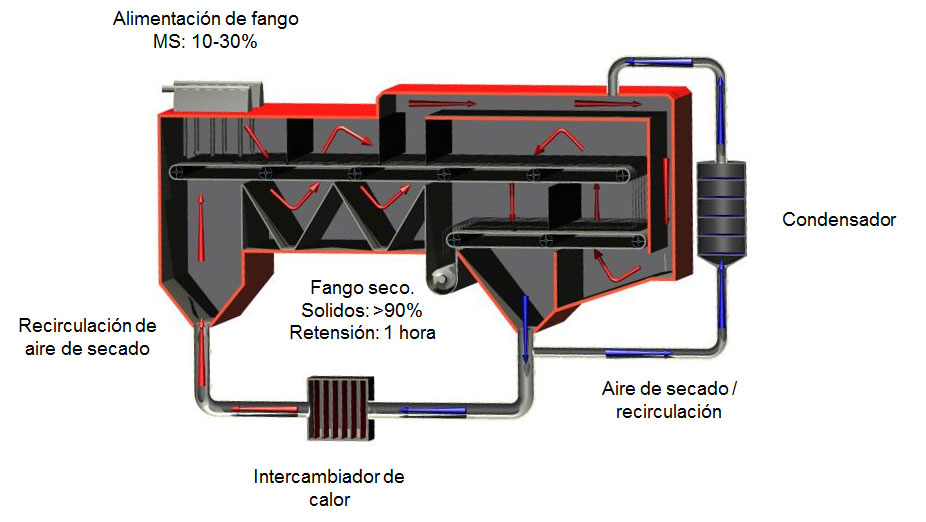
La planta BioCon consiste en una cabina, con aislamiento, en la cual se sitúan los principales componentes tales como el sistema de distribución de fangos, las dos cintas transportadoras, los ventiladores de circulación de aire de secado, el tornillo de extracción de fango seco y los intercambiadores de calor para el calentamiento del aire de secado.
Las dos cintas transportadoras están situadas una encima de la otra y conforman tres zonas de secado diferenciadas: la cinta superior recorre la primera y segunda zona de secado mientras que la cinta inferior recorre la zona final de secado.
Cada zona de secado está equipada con dos ventiladores de circulación de aire de secado y un intercambiador de calor.
El fango se distribuye en tiras en la cinta inicial a través de los sistemas de deposición de fango oscilantes. El movimiento pendular de las boquillas asegura la distribución del fango a lo largo de la superficie de secado, optimizando el proceso.
Debido a que la cinta inicial está templada y a la intensa circulación del aire, se produce un secado rápido de la superficie del fango, evitando que el fango se pegue a la cinta.
En la cinta inicial, el fango se deshidrata parcialmente. El diseño del proceso y el manejo suave de las cintas aseguran que el fango, parcialmente secado que sale de la cinta inicial, caiga sobre la cinta inferior sin ningún problema.
En la cinta final, el fango se seca hasta la concentración deseada (90%). El movimiento lento de dicha cinta transporta el lodo en la misma dirección hacia el transportador de tornillo de extracción. El transportador conduce fango seco a una válvula rotativa situada fuera de la cabina del secador.
Para eliminar el agua evaporada del sistema, una parte del aire de secado se extrae en continuo y se envía al condensador. El aire que sale del condensador es devuelto a la planta.
La temperatura disminuye a lo largo del secador, por tanto, en la zona final, cuando se alcanza la máxima sequedad del fango, la temperatura del aire es la mínima. La ventaja de este procedimiento es que se minimiza el riesgo de incendio.
Para evitar la emisión de olores, se crea un vacío en el secador, extrayendo una parte del aire del sistema de condensación, a través de un ventilador regulado por variador de frecuencia.
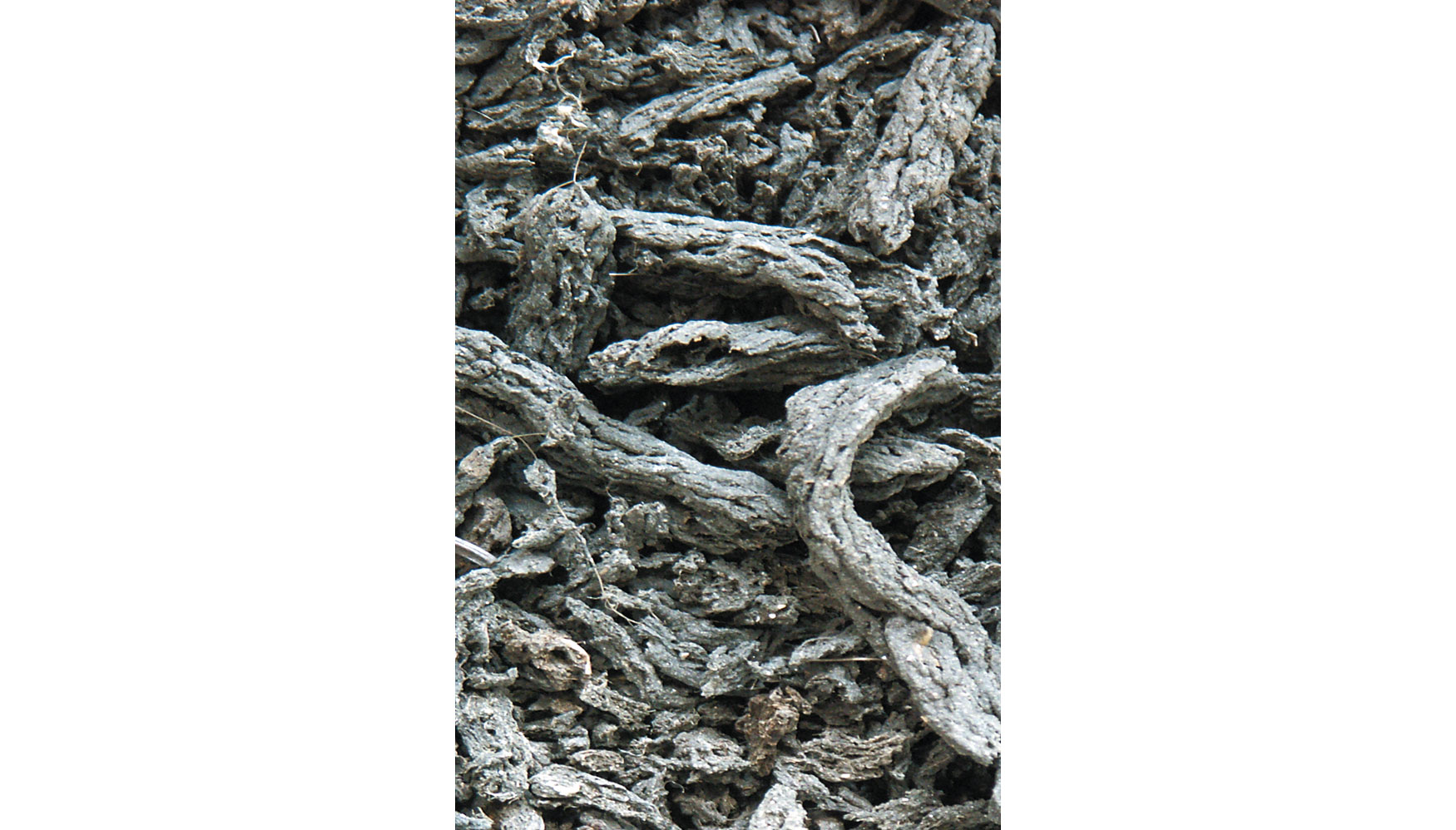
El fango seco se extrae del secador en forma granular. Este fango es adecuado para su aplicación agrícola y puede utilizarse con sistemas convencionales de distribución de fertilizantes o bien para ser utilizado como combustible en el sistema de incineración de fangos BioCon, o coincinerar en un horno de una cementera, estación eléctrica, etc.
La principal característica del secado térmico BioCon es que se controla en todo momento el tiempo de residencia y la temperatura del fango.