La combinación de torneado duro+rectificado supone una ventaja competitiva para el sector de la automoción
Torneado duro, operación para el automóvil
¿Dónde aplicarlo?
Concepto de torneado duro
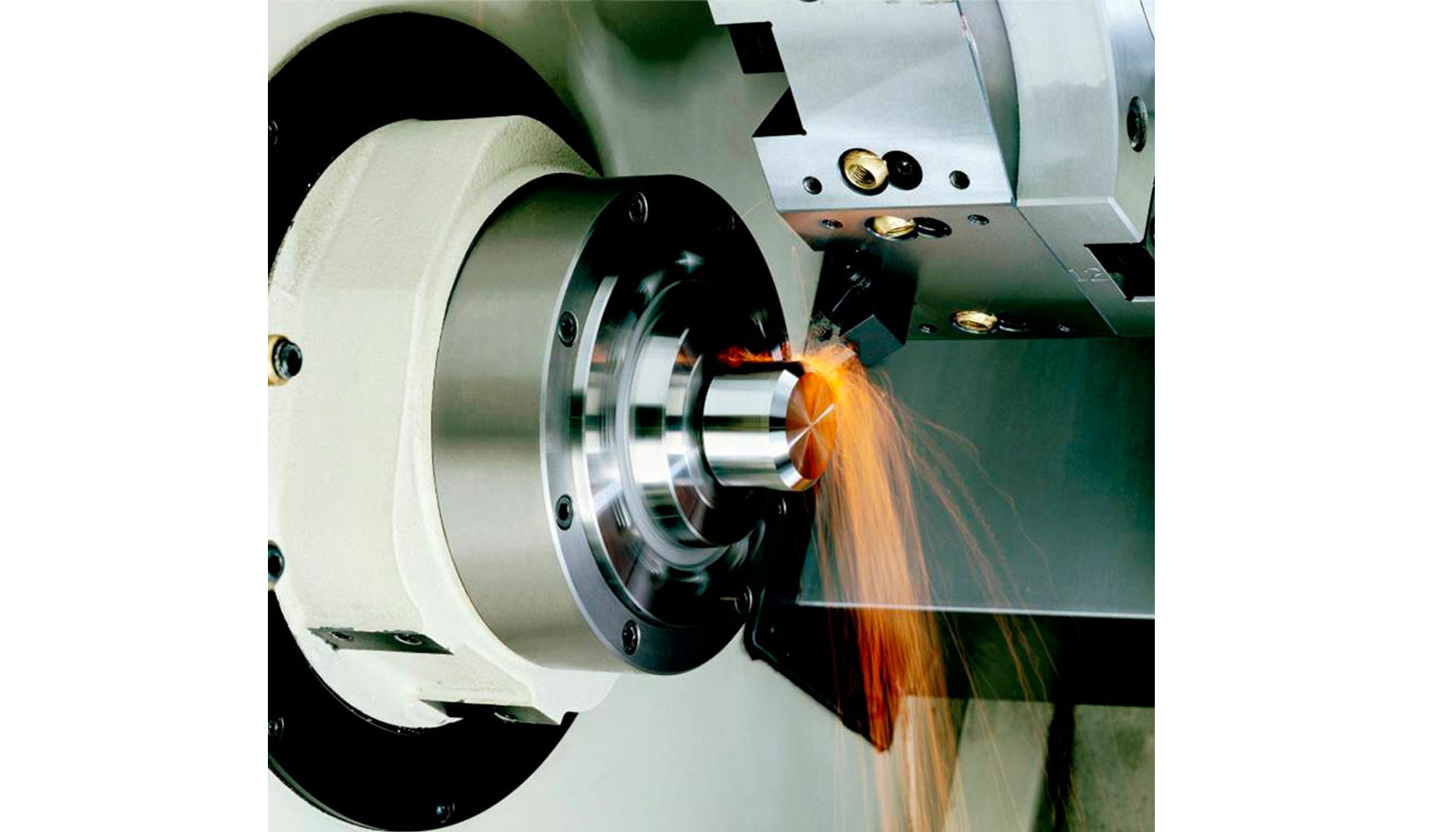
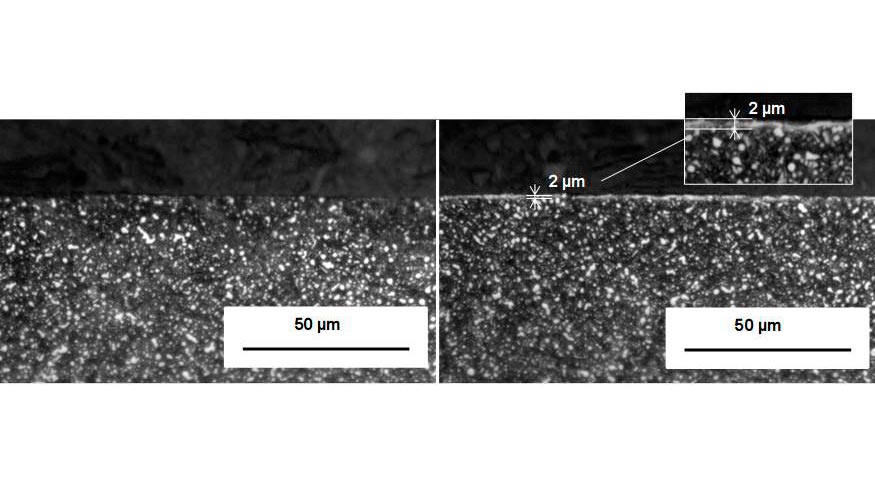
Herramientas en el torneado duro
El material para herramientas mayoritariamente utilizado durante el torneado duro es el PCBN. Esto es debido a que soporta temperaturas de corte de hasta 1.200 °C a diferencia de las cerámicas o PCD que sólo son estables hasta 900 °C y 700 °C, respectivamente. Cabe destacar que este tipo de plaquitas no son enterizas, como se puede observar en la figura 3, sino que están compuestas por un cuerpo de metal duro y sólo la punta está compuesta de PCBN. En el caso del sector automovilístico el tipo de materiales en los cuales esta técnica es principalmente factible son los aceros templados. Esto lleva a tener que utilizar plaquitas de PCBN con una proporción baja de este material (40-50%) frente al aglomerante —cobalto en la mayor parte de los casos—. Debido a lo agresivo del material es recomendable no sólo la utilización de plaquitas con ángulo de desprendimiento negativo con el fin de proteger el filo de corte sino también tener muy en cuenta la geometría de éste y el tamaño del radio de punta de la plaquita. En cuanto a la geometría del filo, en un estudio publicado en ‘Journal of Material Processing’, se obtuvo que un mayor redondeo del filo es beneficioso a medida que es mayor la dureza de la pieza ya que se consiguen mejores rugosidades superficiales. Por otra parte, un mayor redondeo del radio de punta provoca un aumento del área de contacto entre la plaquita y la pieza lo que se traduce en una mayor disipación del calor y por ende una mayor vida de herramienta. Por contrapartida, como bien es conocido, un aumento del radio de punta conlleva un aumento de la rugosidad media. Por ello, jugando con estos dos parámetros se debe alcanzar un compromiso entre calidad superficial y vida de herramienta [4].
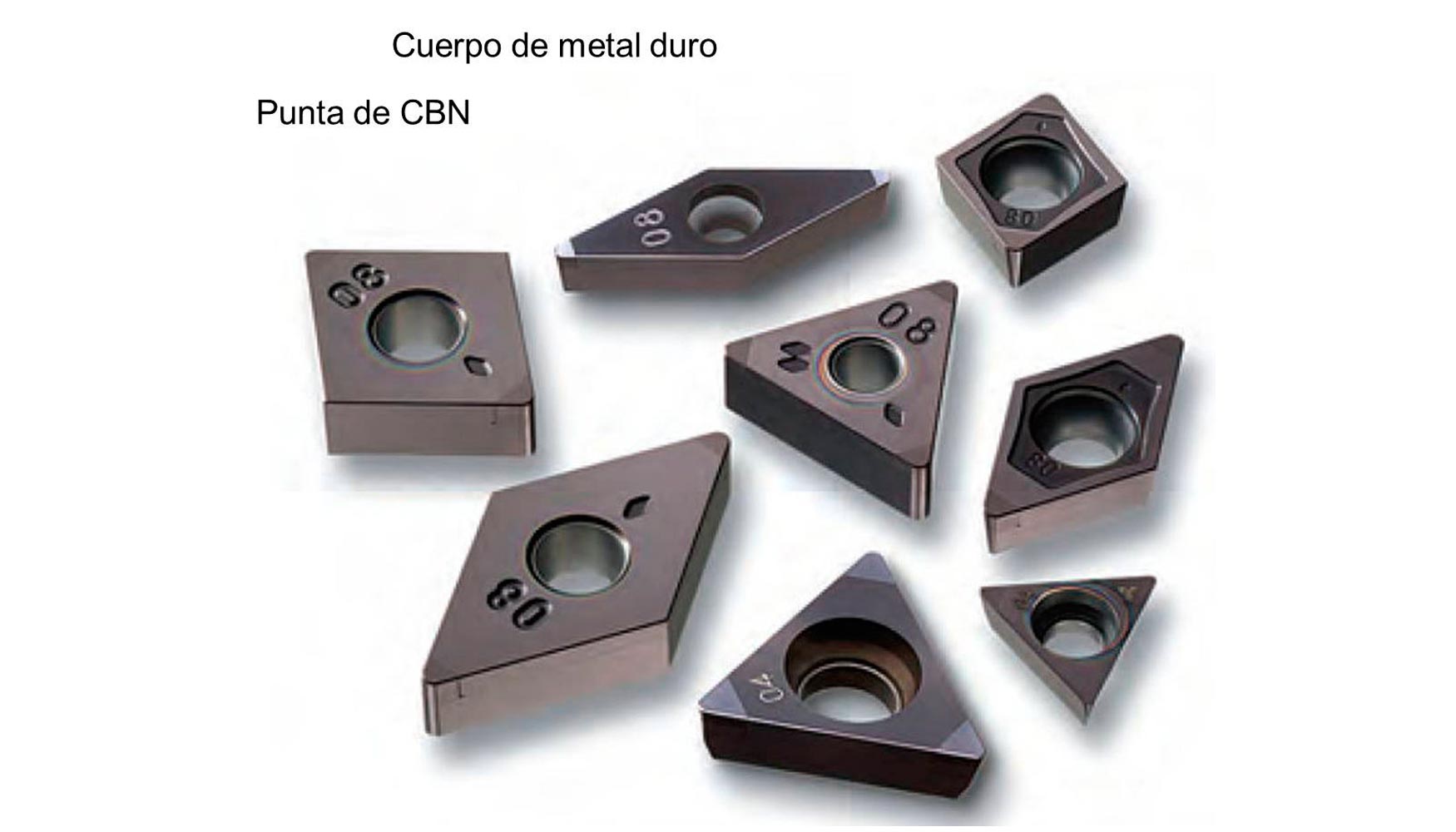
Integridad superficial
Junto con la formación de la capa blanca ya expuesta en el anterior apartado, la rugosidad superficial es otro de los aspectos a controlar en cuanto a integridad superficial se refiere. Generalmente del torneado duro se pueden llegar a esperar valores que oscilan entre 2,4 y 4 micrómetros, aunque este valor puede ser superado en el torneado duro de alta precisión llegando a valores cercanos al micrómetro, lo cual lo asimila bastante a las rugosidades medias obtenidas en los procesos de rectificado. La problemática del torneado viene dada porque es tecnológicamente costo disminuir ese valor y aunque se obtengan los mismos valores sus patrones son distintos, como se puede observar en la figura 4. Mientras que con el torneado duro se obtienen texturas regulares con el rectificado estas estructuras son periódicamente anisotrópicas y aleatorias lo que lleva a pensar que también las propiedades del material sean alteradas de forma distinta y puedan, por tanto, comportarse de forma diferente [5].
![Figura 4. Patrón de rugosidad superficial obtenida en AISI 5140. (a) Torneado duro (b) rectificado. [5] Figura 4. Patrón de rugosidad superficial obtenida en AISI 5140. (a) Torneado duro (b) rectificado. [5]](https://img.interempresas.net/fotos/1230197.jpeg)
(a) Torneado duro (b) rectificado. [5]
Torneado duro y rectificado, máquinas combinadas
Por todo ello, aunque exista una competitividad para el mecanizado de materiales de alta dureza entre el torneado duro y el rectificado, en este caso, la unión hace la fuerza ya que cada uno de estos procesos presenta diferentes ventajas respecto del otro, como se puede observar en la figura 5.
![Figura 5. Diagrama características Torneado duro y rectificado. [6] Figura 5. Diagrama características Torneado duro y rectificado. [6]](https://img.interempresas.net/fotos/1230198.jpeg)
El proceso de rectificado en este caso es seleccionado como proceso de acabado debido a su capacidad de conseguir excelentes acabados en la superficie de las piezas. Bien sea en cuanto a calidades de rugosidad así como a las estrechas tolerancias dimensionales. Mediante el rectificado se pueden conseguir rugosidades Ra menores a 2 µm, además utilizando muelas superabrasivas, estas rugosidades son susceptibles de mejora. En cuanto a geometría y dimensiones de la pieza se refiere, la tolerancia dimensional lograda es de 5 µm y la redondez de 0,7 µm. Otra ventaja del rectificado es que éste carece de las marcas propias del torneado, como se expuso anteriormente. Además, a la hora de necesitar realizar cortes interrumpidos para la generación de ranuras o estrías entre otros el rectificado no presenta problemas, ya que a diferencia de lo que ocurre con las herramientas de torneado de PCBN o cerámicas no presentan inestabilidad ante los choques térmicos.
Por otra parte, en diferentes estudios se observan las comparativas entre los dos procesos [6] y [7], en la mayoría seleccionando el torneado duro en los estudios más recientes, como sustituto del otro. Sin embargo, ningún proceso presenta todos los requerimientos del mecanizado en duro de precisión, por lo que parece una buena opción hacer a estos dos procesos complementarios, aprovechando las ventajas de cada uno de ellos para optimizar los procesos de fabricación. Esto se refleja en el mercado de la máquina-herramienta, que han optado por la creación de centros combinados en los que realizar ambas operaciones en la misma máquina, con las ventajas que supone.
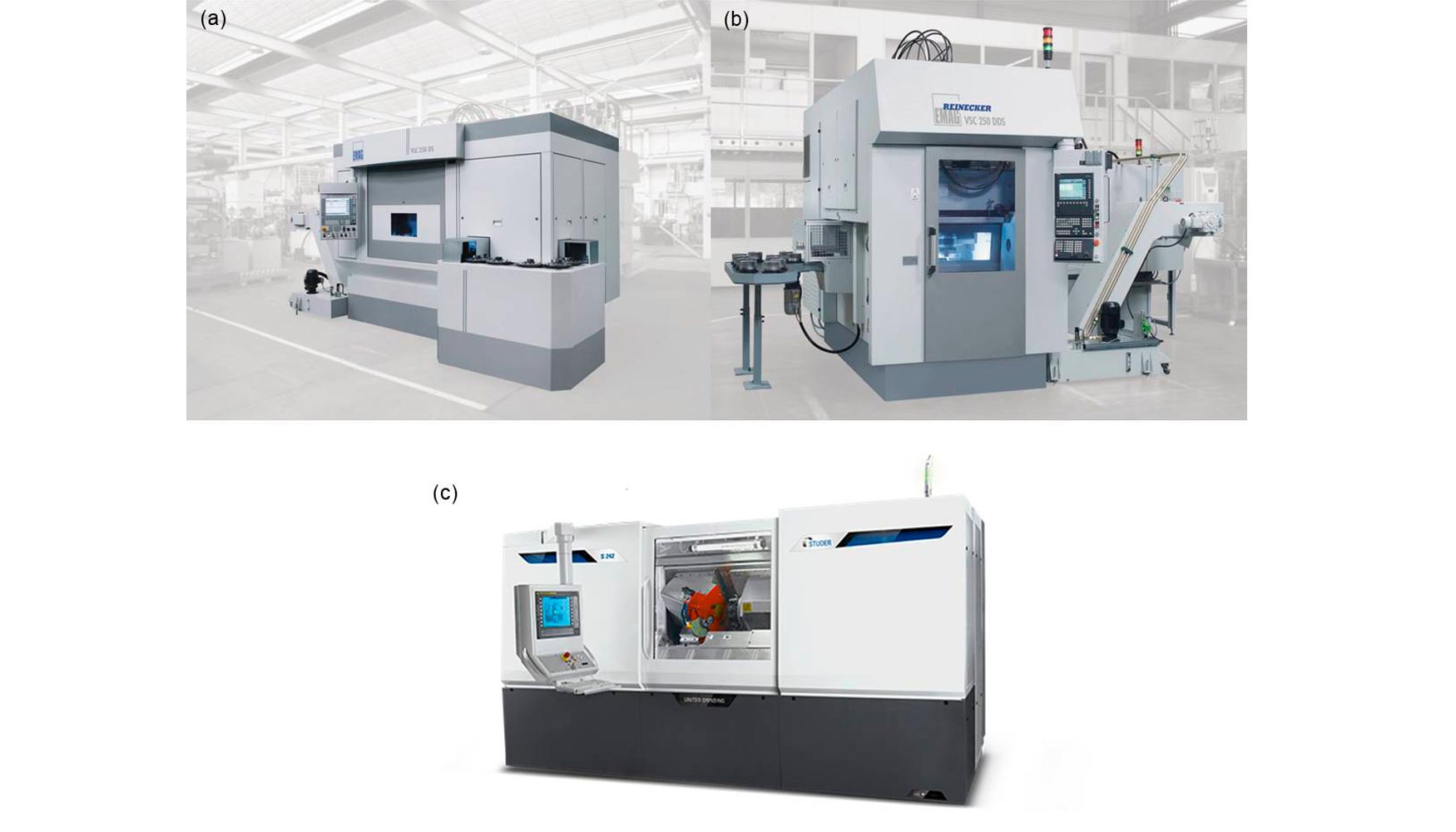
La gran ventaja que comparten todos estos centros combinados es el mecanizado de piezas en una única atada, beneficiándose de las ventajas de cada uno de los procesos y aportando de esta manera mayor calidad y flexibilidad a la fabricación de las piezas. Realizar todas las operaciones en la misma máquina y con un único amarre supone una reducción tanto de los tiempos de preparación como de los tiempos del proceso, eliminando tiempos muertos en el transporte de piezas entre máquinas y en la puesta a punto de cada operación en diferentes máquinas. Este aspecto es fundamental en el sector del automóvil donde al fabricarse series grandes de piezas, la eliminación de estos tiempos repercute positivamente en la producción final. Por otro lado, el amarre único durante todo el proceso de fabricación evita errores que se introducen en la colocación de la pieza, como el salto radial o la falta de concentricidad. Esto permite que las creces de mecanizado requeridas para el proceso de acabado en los centros combinados sean menores que si tuviéramos que realizar el proceso final en otra máquina. El amarre único desencadena un sinfín de ventajas para el proceso, traduciéndose todas ellas en una mejora en las tolerancias dimensionales así como en la calidad superficial de las piezas y una reducción en el tiempo de fabricación.
El hecho de reducir el desgaste de las muelas conlleva un gran abanico de ventajas. Se disminuye el número de diamantados, aumentándose la vida útil de las muelas y con ello un menor consumo de las mismas. Esto se traduce tanto en ahorro económico, ya que se consumen menor número de muelas, como de tiempos muertos debido a la reducción de cambios de herramienta y del número de veces que es necesario diamantarla, siempre y cuando no se realice un diamantado continuo de la muela.
En el sector automovilístico, la mayor parte de los elementos, generalmente situados en la transmisión y motor, que necesitan de esta precisión son de acero endurecido, por lo que las muelas utilizadas son bien de alúmina (Al2O3) o de CBN, ya que presentan un buen comportamiento ante el acero. Las muelas de alúmina son más baratas que las de CBN, sin embargo hay aplicaciones que requieren gran precisión geométrica en los se hace necesario el uso de este tipo de muelas como por ejemplo los cigüeñales. El motivo por el que en estas aplicaciones se tiende a utilizar muelas de CBN es porque presentan un desgaste volumétrico menor al de las muelas de alúmina, consiguiendo un mayor control de la geometría de la muela.
En cuanto a la configuración de la máquina, la posición del eje es la característica que diferencia a estos dos fabricantes de centros combinados, como se observa en las figura 7 y 8. Por un lado Emag opta por el eje vertical mientras que Studer presenta eje horizontal. Los centros combinados de Emag, debido a su configuración de eje vertical favorece la caída libre de virutas, esto supone mayor beneficio para el caso del torneado duro, debido a la ausencia de refrigeración. En el caso en el que el eje es horizontal, esta eliminación de las virutas se puede realizar mediante aire comprimido.
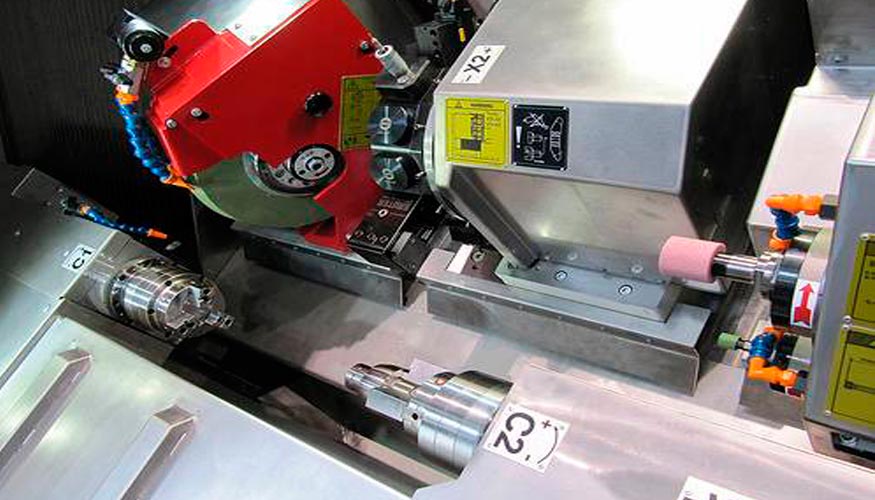
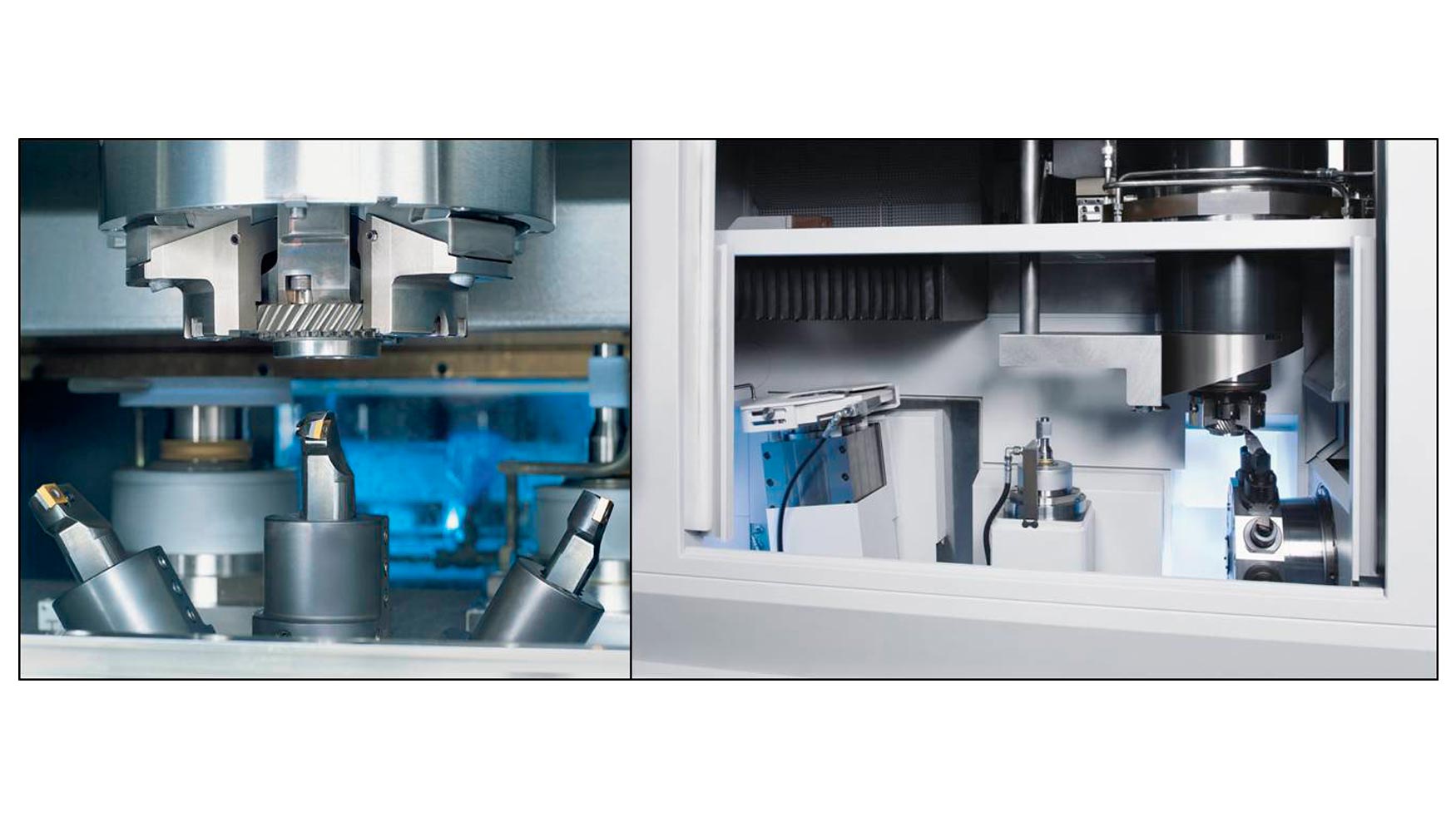
Las piezas del sector del automóvil que se fabrican combinando las operaciones de torneado duro y rectificado son de alta calidad y se producen en series medias y grandes, siendo este uno de los motivos que justificaría el reemplazamiento de un torno y una rectificadora independientes por un centro combinado. Algunas de estas piezas son los árboles de transmisión, ejes de motor o de rotor o ejes de transmisión entre muchos otros. Sin embargo, el ejemplo por excelencia de pieza de automoción de fabricación en estos centros son algunos tipos de engranajes. Los escalones de los mismos es común realizarlo mediante torneado duro. Además hay partes de los mismos en los que por su funcionalidad se requieren unos estándares de calidad, como son agujeros cilíndricos y cónicos en los que tanto el desbaste como el acabado se realizan mediante rectificado de interiores, generalmente con muelas de CBN para este caso.
Conclusión
Por ello, a día de hoy los centros combinados de torneado duro y rectificado son una de las soluciones que se va abriendo mercado en el sector automovilístico en el que muchas de las piezas de revolución como los engranajes de las cajas de discos, ejes, etc. Estas piezas requieren ser endurecidas antes de su mecanizado no sólo con el fin de mejorar su comportamiento mecánico durante su vida útil sino también para conseguir las tolerancias dimensionales y acabados superficiales dentro de unos márgenes muy estrechos. Es por ello, que el proceso de torneado duro seguido de un rectificado en las zonas de la pieza que sean funcionales es la mejor alternativa de mecanizado. Además el hecho de combinar dos operaciones en una misma máquina reduce espacio ocupado dentro de la planta de producción, siendo el espacio o el layout de la planta un inconveniente en sistemas de producción continuos. La gran ventaja de este proceso combinado comparándolo con la fabricación secuencial en diferentes máquinas es que todo el proceso se realiza con una única atada eliminando los errores provenientes del amarre como la excentricidad o la alineación de superficies planas.
Cómo se debe de trabajar con los nuevos MRLS
Los ‘Manufacturing Readiness Levels’ (MRL) también conocidos como ‘niveles de desarrollo tecnológico’ es una escala que fue propuesta por la NASA en los años 80 para todo tipo de tecnologías aeroespaciales con el fin de definir de forma cuantitativa cómo de desarrollado se encuentra un proyecto. A lo largo de estos 20 años varias han sido las modificaciones y enfoques que han sufrido hasta a ser adoptados por el sector de la fabricación.Actualmente, como se puede observar en la figura, existen 9 niveles para indicar el estado de desarrollo del proyecto. ¿Pero por qué ahora?
En el sector de la fabricación, gracias a estos niveles estandarizados se puede conocer la madurez de un proyecto/producto objetivamente, tenga la naturaleza que tenga, definiendo los esfuerzos de investigación realizados en cuanto a cercanía a la aplicación final. En el lado izquierdo de la escala, los niveles MRL1 a MRL4 indican un desarrollo tecnológico que se dan habitualmente en la esfera universitaria desde una idea inicial llegando a un test final en un demostrador de laboratorio. Del mismo modo y observando desde el lado derecho, las empresas son capaces de llegar en la escala de niveles de preparación hasta el nivel MRL7. Finalmente la unión entre ambos extremos se encuentran los niveles intermedios MRL5-6 dondese valida la tecnología a nivel de componentes y a nivel de sistema o subsistema en un entorno relevante, es decir, es donde se desarrolla la tecnología en un entorno de simulación industrial antes de pasar al entorno real. Sin embargo, debido a la exigencia de la producción diaria de las empresas y por otra parteal tamaño y limitaciones de las máquinas de laboratorio, no existe conexión entre ambos entornos.
En este contexto es donde entra en juego el nuevo Centro de Fabricación Avanzada de Aeronáutica (CFAA) donde la UPV/EHU está involucrada como agente tecnológico. Con este centro se pretende dar respuesta a los niveles intermedios MRL 5-6 y de este modo aunar esfuerzos de tal modo que los desarrollos y buenas ideas procedentes de ambos extremos no se detengan o desaparezcan en dicho nivel intermedio, conocido como “Valle de la Muerte. En otras palabras, con este centro se busca que agentes tecnológicos y empresas trabajen en la misma dirección con el fin de mejorar y hacer más productivos los procesos de fabricación actuales.
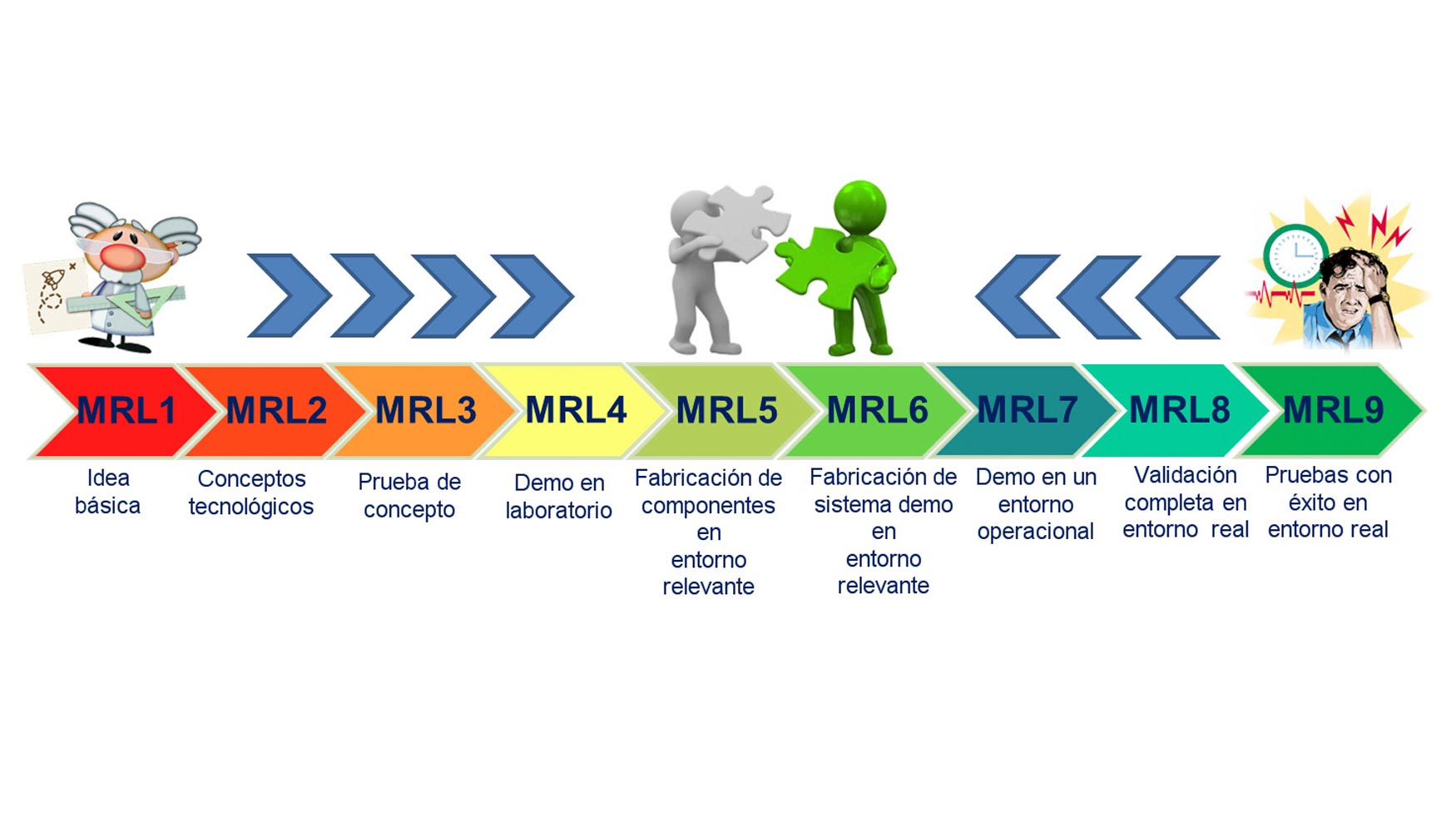
Acabado de superficies funcionales
El grupo de fabricación de la UPV/EHU lleva varios años trabajando con procesos de acabado de superficies funcionales. Algunos ejemplos son el empleo de técnicas de bruñido por deformación, pulido láser, procesos abrasivos, etc. Algunos de estos estudios son de directa aplicación a la industria del entorno, como por ejemplo el caso aquí presentado: ‘El acabado de discos de freno’.
Los discos de freno son elementos clave dentro del sistema de frenado de varios tipos de vehículos. Se trata de componentes que provienen de etapas de fundición y acabados por mecanizado en seco utilizando insertos cerámicos. Como todo proceso de torneado, se genera un patrón espiral uniforme en la superficie de la cara mecanizada, en este caso la pista de frenado. En ocasiones, este patrón puede generar problemas provocando ruido, vibraciones o incluso un desvío en la trayectoria del vehículo, sobre todo en las primeras frenadas. De cara a eliminar esta direccionalidad de la rugosidad se pueden emplear numerosas técnicas. El cepillado, utilizando cepillos directamente en un centro de mecanizado o de torneado, presenta varias ventajas respecto a otros métodos. Se trata de una técnica sencilla, barata, versátil y que no requiere de nueva maquinaria para realizarla.
En la Escuela de Ingeniería de Bilbao se han realizado varios ensayos de cepillado de discos de freno utilizando cepillos abrasivos flexibles. Estas herramientas son capaces de eliminar el patrón de rugosidad del torneado consiguiendo tiempos de proceso inferiores a 20 segundos. Los primeros ensayos muestran una solución interesante para prototipos y pre-series. De cara a implementar esta solución en un proceso productivo, lo ideal sería desarrollar un sistemas de cepillado doble para actuar sobre las dos pistas de frenada a la vez siempre trabajando con un control de fuerza sobre la superficie.
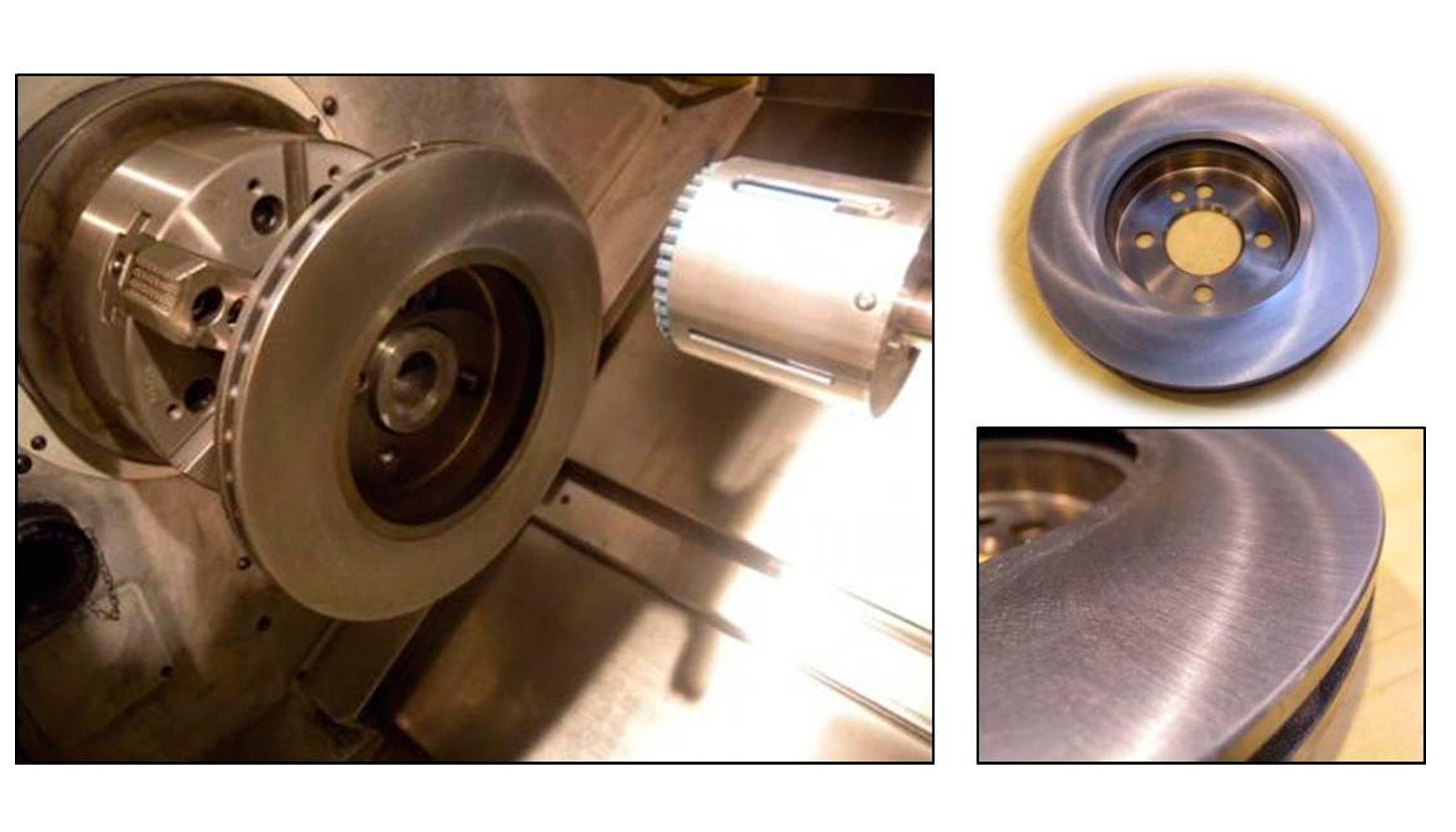
Referencias
[1] http://www.investinspain.org/invest/es/sectores/automocion/descripcion/index.html
[2] Y. Guo, A. Warren and F. Hashimoto. The basic relationships between residual stress, white layer, and fatigue life of hard turned and ground surfaces in rolling contact CIRP Journal of Manufacturing Science and Technology, 2010, 2, 129 – 134
[3] S. Hosseini, T. Beno, U. Klement, J. Kaminski and Ryttberg, K. Cutting temperatures during hard turning—Measurements and effects on white layer formation in AISI 52100 Journal of Materials Processing Technology, 2014, 214, 1293 – 1300.
[4] J. D. Thiele and S. N. Melkote. Effect of cutting edge geometry and workpiece hardness on surface generation in the finish hard turning of AISI 52100 steel Journal of Materials Processing Technology, 1999, 94, 216 – 226.
[5] W. Grzesik, K. Żak and P. Kiszka. Comparison of Surface Textures Generated in Hard Turning and Grinding Operations Procedia CIRP, 2014, 13, 84 – 89.
[6] F. Klocke, E. Brinksmeier, and K. Weinert, “Capability Profile of Hard Cutting and Grinding Processes, ” CIRP Ann., 2005, 54 22–45.
[7] Y. B. Guo and A. W. Warren, ‘Surface & Coatings Technology The impact of surface integrity by hard turning vs. grinding on fatigue damage mechanisms in rolling contact’, Surf. Coat. Technol., 2008, 203, 291–299.