Automatizaciones en el proceso productivo
25 de abril de 2012
- Repetibilidad en calidad
- Repetibilidad en el tiempo de proceso requerido
- Repetibilidad en el tiempo de proceso de cada fase
- Repetibilidad en volumen de fabricación
Sin embargo, para obtener esa repetibilidad es necesario que, en gran medida, los procesos estén automatizados, de lo contrario dependerán de las personas, luego serán variables y descontrolados. Por definición, la automatización se compone de todas las teorías y tecnologías encaminadas de alguna forma a sustituir el trabajo del hombre por el de la máquina. De esta manera, es posible encontrar tres tipos de automatización: [REF]
Automatización Fija: sistema de fabricación en el que la secuencia de las operaciones está fijada por la configuración de los equipos que lo forman. Se caracteriza porque:
- Está constituida por una secuencia sencilla de operaciones
- Necesita una inversión elevada en equipos especializados
- Posee elevados ritmos de producción
- Es muy inflexible, en general, para adaptarse a los cambios de los productos
Automatización programable: sistema de fabricación en el que los equipos de producción están diseñados para cambiar la secuencia de operaciones a fin de adaptarse a la fabricación de productos diferentes. Se inició con las máquinas-herramienta con control numérico (conocidas como CNC) y los robots industriales. Se caracteriza porque:
- Una gran inversión en equipos de aplicación general, como los propios sistemas de Control Numérico
- La necesidad de cambiar el programa y/o la disposición física de los elementos para cada lote de producción
- La existencia de un periodo de preparación previo a la fabricación de cada lote de productos distintos
Automatización flexible: es una extensión de la automatización programable que da como resultado sistemas de fabricación en los que no sólo se pueden cambiar los programas sino que además se puede cambiar la relación entre los diferentes elementos que los constituyen.
La automatización flexible ha dado lugar a los sistemas de fabricación flexible o FMS (Flexible Manufacturing Systems).
Dependiendo del tipo de producto y volumen de fabricación es posible encontrar cualquiera de los casos descritos, en cualquiera de los casos nos encontramos con producción seriada. Tradicionalmente, en las empresas del entorno se han implantado automatizaciones fijas y programables para grandes series de fabricación. Sin embargo para este tipo de instalaciones se requiere de una elevada inversión, con el hándicap añadido del ciclo de vida del producto, cada vez más corto, y la incertidumbre existente actualmente en la economía mundial, pudiendo llegar a paralizar la producción ante otra recesión.
Ante esta situación, las automatizaciones que cada vez más se abordan son las flexibles, ya que disponen de capacidad de adaptarse con mayor facilidad a variaciones de producto, al mismo producto fabricado y al volumen de demanda.
En cualquiera de los casos, el control de costes y presión sobre la producción, junto con el continuo proceso de globalización, la logística se ha convertido en un factor clave para el éxito de una empresa. Las programaciones ineficientes, la optimización local en lugar de global, la asignación ineficiente de recursos y la productividad mediocre pueden dar lugar a pérdidas económicas diarias. La necesidad de realizar entregas JIT (Just-in-time) y JIS (Just-in-sequence), introducir Kanban, planificar y construir nuevas líneas de producción y gestionar redes de producción de ámbito mundial exige contar con criterios objetivos de toma de decisiones, que ayuden a los directivos a evaluar y comparar enfoques alternativos de fabricación y automatización.
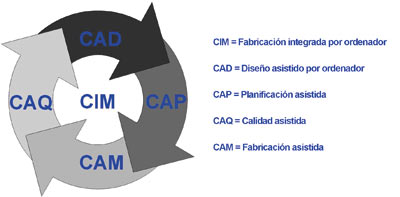
Por ello, las herramientas de simulación de eventos discretos cada vez están tomando mayor fuerza en los entornos automatizados. Mediante estas herramientas de simulación es posible crear modelos digitales de sistemas productivos para permitir la exploración de las características de los sistemas y la optimización de su rendimiento. Mediante estas herramientas es posible realizar simulaciones de diferentes escenarios hipotéticos de los sistemas automatizados, detectando cuellos de botella, diagramas estadísticos de producción que se obtendría y evaluar diferentes escenarios de fabricación tanto en fase de concepción como posteriores. Los resultados proporcionan la información necesaria para tomar decisiones fiables con rapidez en las fases de la planificación de producción llegando a alcanzar beneficios como:
- Ahorro entre un 3 y un 6% en la inversión inicial
- Aumento de la productividad del sistema existente entre un 15 y un 20%.
- Reducción del coste de nuevos sistemas entre un 5 y un 20%.
- Optimización del consumo de recursos y su reutilización.
- Reducción de inventarios entre un 20 y un 60%.
- Reducción del tiempo de producción entre un 20 y un 60%
Cuando la serie a fabricar se convierte en unitaria o reducida la automatización toma otros matices. La problemática en este tipo de empresas se centra en cumplir la planificación y realizar las operaciones con la calidad exigida donde la distribución en planta se realiza por áreas tecnológicas. Las automatizaciones pasan por la posibilidad de paletizar los siguientes trabajos a realizar mientras la máquina ejecuta otro componente. De este modo, será posible realizar el cambio de referencia en un tiempo mínimo, dejando la máquina en funcionamiento automático y con un control autónomo.
Sin embargo para llegar a este nivel es necesario disponer de un departamento de ingeniería adecuadamente preparado: los trabajos lanzados a planta deben ser fiables al 100%, por lo que los procesos definidos deben estar verificados para no cometer ningún tipo de error. Es necesario para ello disponer de diferentes sistemas:
1. Un sistema CAD/CAM:
- Por medio del sistema CAD representaremos las diferentes fases de fabricación en las colocaciones y utillajes correspondientes. El CAD si es en 3D nos facilitará la visión de interferencias y problemas de ensamblado. El sistema CAD también facilitará la elaboración de librerías de elementos de fijación disponibles por medio de los cuales se realicen los diferentes procesos.
- El sistema CAM no es imprescindible pero gracias a él será posible desarrollar métodos de trabajo estándar para toda la planta productiva. Estos métodos también permiten actualizar herramientas/condiciones de manera rápida y extensiva. La programación también puede realizarse a mano pero es menos fiable, y más aún cuando es necesario tener en cuenta los utillajes y sus particularidades.
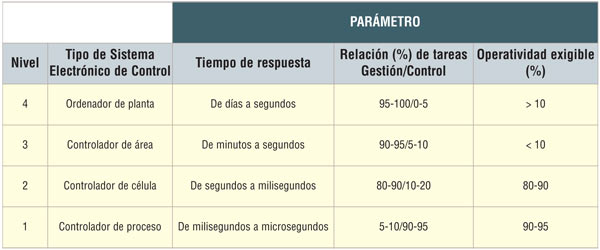
2. Simulador de procesos para fiabilizar los procesos y programas realizados. Al día de hoy es inadmisible que los procesos llevados a planta no sean fiables y se corra el riesgo de sufrir una colisión: las trayectorias a seguir por las herramientas o los propios carros/accionamientos no pueden colisionar entre sí. Para ello existen herramientas de simulación de procesos, bien integradas en el propio software CAM o software específico e independiente para ello.
3. La base de datos de herramientas también resulta clave. Es necesario que la base de datos sea única para todo la empresa, donde es habitual encontrarse con bases de datos paralelas y no coincidentes entre el departamento de ingeniería, planificación y producción. Todo ello conlleva a inestabilizar el sistema, llegando a provocar situaciones de riesgo.
Básicamente con el empleo de esos sistemas y siguiendo una metodología de trabajo es posible automatizar procesos de fabricación discretos: al final se trata de preparar todo el proceso de fabricación de manera virtual y simularlo por medio de herramientas apropiadas para que en la puesta a punto en planta se realice de manera ágil y exenta de problemas consecuentes.
Un factor común a todos los sistemas automatizados es la comunicación entre los diferentes equipos y medios productivos, transferencia de información, así como el procesamientos de los datos. Los diferentes equipos empleados deben de comunicarse entre sí, por lo que deben resolver la problemática de la transferencia de información entre los equipos de control del mismo nivel y entre los correspondientes a los niveles contiguos del CIM (Computer Integrated Manufacturing).
En la década de 1980, las comunicaciones industriales comenzaron a realizarse mediante comunicaciones digitales punto a punto para, posteriormente, evolucionar hacia la aplicación de redes multipunto.
En la actualidad, la automatización integrada de la producción se realiza mediante un conjunto de dispositivos y sistemas de control y gestión de proceso asociados a diferentes niveles y que han de estar intercomunicados.
En los niveles superiores de la arquitectura CIM se trabaja frecuentemente con grandes volúmenes de datos, aunque el tiempo de respuesta no es en general crítico y se sitúa entre pocos segundos hasta minutos o incluso horas. Por el contrario, los sistemas de control utilizados en los niveles de producción trabajan en tiempo real y debido a ello se les exigen tiempos de transmisión mucho más rápidos y, sobre todo, un comportamiento determinista de las comunicaciones, aunque los volúmenes de información a transmitir son, en general, menos elevados.
Las diferentes características (por ejemplo, tiempos de respuesta) exigidas al sistema de comunicaciones de cada uno de los niveles hacen que sea diferente el tipo de red de comunicaciones necesaria para implementarlo.
Las redes de datos de nivel de empresa, fábrica, área y, en ocasiones, de célula, están dedicadas al establecimiento de las comunicaciones entre los equipos informáticos. En este nivel se ejecutan, entre otras, las aplicaciones ERP (Enterprise Resource Planning), MES (Manufacturing Execution Systems). CAD / CAM / CAE (Computer Aided Design / Manufacturing / Engineering). Este tipo de red no ha sido diseñada, al menos inicialmente, para satisfacer determinados requisitos que son propios del ambiente industrial, entre los que destacan:
- El funcionamiento en ambientes hostiles (perturbaciones FEM, temperaturas extremas, polvo y suciedad, etc.).
- Exigencias de gran seguridad en el intercambio de datos en un intervalo cuyo límite superior se fija con exactitud (‘determinismo’) para poder trabajar correctamente en ‘tiempo real’.
- Elevada fiabilidad y disponibilidad de las redes de comunicación, mediante la utilización de dispositivos electrónicos, medios físicos redundantes y/o protocolos de comunicación que dispongan de mecanismos avanzados para detección y corrección de errores, etc.
Por ello, en las dos últimas décadas del siglo XX se acrecentó el interés por desarrollar redes de comunicación específicamente diseñadas para entornos industriales y que diesen soporte a la intercomunicación entre las operaciones del nivel de fábrica y las del nivel de empresa.
En la actualidad, constituye una línea de I+D+i de gran auge la adaptación y redefinición de las tecnologías que son normas en las redes de datos para poder utilizarlas en el ámbito del control de procesos. Surgen las conocidas como redes 'Industrial Ethernet', cuya capa de enlace está basada en la técnica Ethernet y cuyos protocolos básicos de comunicación se fundamentan en TCP/IP. A grandes rasgos, estas redes tratan de rediseñar (en mayor o menor medida) el hardware y el software asociado a las capas inferiores de Ethernet para poder aplicarlo en los ambientes más hostiles de los niveles de planta.
En lo que respecta a los protocolos de la capa de aplicación que se debe utilizar en las redes Industrial Ethernet en combinación con los protocolos de las capas inferiores, no existe actualmente una solución única normalizada y están propuestas diferentes soluciones como, Modbus TCP, EtherNet/IP, PROFINet, EtherCat, Powerlink, etc.
También está en estudio la modificación de la norma Ethernet a fin de reservar un cierto ancho de banda para las necesidades de comunicación determinista de la planta (una de las propuestas, relacionada con ‘PROFINet’, denomina a esta solución con el calificativo de ‘Isócrona’).
Históricamente, el desarrollo de esta clase de redes fue debido a la elevación de la complejidad en la automatización de los sistemas industriales, que incrementó desmesuradamente el volumen de cableado que era preciso realizar para conectar a los equipos de control con un elevado número de dispositivos sensores y actuadores mediante hilos independientes en los últimos metros del proceso.
En la actualidad, estas redes de comunicación permiten desplegar todo el potencial de comunicación tanto a nivel de negocio como a nivel de campo, posibilitando una ingeniería simple, homogénea y abierta mediante bloques de función que se encargan de facilitar la parametrización y el diagnóstico facilitando la puesta en marcha y el manejo y aumentando la cantidad y la calidad de las información útil.
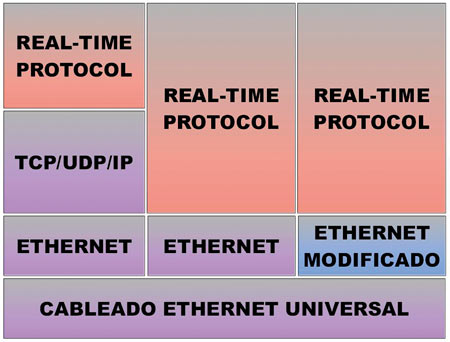
Como consecuencia del despliegue de esta tecnología en la industria, los últimos avances giran en torno a conceptos como:
- Gestión de energía (debido a una gran transparencia gracias a la integración en sistemas de gestión de energía, lectura de valores de consumo y avisos de diagnóstico).
- Aumento de la disponibilidad de la instalación reduciendo los tiempos de parada y mantenimiento gracias a un diagnóstico aplicado de toda la planta y a la mayor rapidez en la eliminación de errores.
- Posible mantenimiento preventivo.
- Reducción del tiempo necesario para la ingeniería (Ingeniería eficiente).
- Mayor flexibilidad (posibilidad de integrar en la ingeniería dispositivos IO-Link de otros fabricantes).
- Configuración y programación homogénea y transparente (Mediante herramientas software integradas).
- Menores tasas de error en el diseño de esquemas de circuitos gracias a la reducción del cableado de control y las herramientas CAD.
- Montaje más rápido con tasas de error minimizadas mediante la reducción del cableado de control.
- Menos espacio en el armario eléctrico.
- Tiempos de cambio de equipo más cortos gracias a la gestión de parámetros y recetas centralizada, también para equipos de campo.