Los vehículos eléctricos y su influencia en el procesado de chapa metálica
Algunos hablan sin parar de ella, otros la observan con sentimientos encontrados, otros la rechazan. Y, sin embargo, la movilidad eléctrica es imparable. Pero, ¿cómo afecta la alternativa a los motores de gasolina y diésel al procesado de chapa? ¿Es necesario reinventar este proceso, o se pueden adaptar las técnicas de construcción y los procesos de fabricación probados a los coches eléctricos? Una mirada entre bastidores.
¿Cómo será el coche eléctrico del futuro? ¿Será alimentado por un motor eléctrico alimentado por una pila de combustible o por una batería? ¿funcionará el motor solo o en combinación con un motor de combustión interna (híbrido)? ¿Qué será más demandado: un coche de ciudad o un vehículo de larga distancia con una costosa red de recarga? No hay duda de ello: la movilidad eléctrica es uno de los retos más apasionantes para la industria del automóvil en los últimos años.
En el estudio de 2018 de la VDMA ‘Los conductores están cambiando’, FEV Consulting GmbH analizó detalladamente cómo la electrificación de los sistemas de conducción de los vehículos tendría un impacto en Europa, EE UU y China. Los expertos de FEV esperan que las ventas de motores de combustión interna (incluidos los motores híbridos) disminuyan un 10% en el sector de los turismos entre 2016 y 2030. Sin embargo, esto también significa que los vehículos clásicos de motores de combustión continuarán dominando, aunque al menos uno de cada cinco vehículos en los tres mercados principales analizados (estudio: 22%) será impulsado por un motor eléctrico.
Vela Performance GmbH, en Berlín, entiende muy bien este impacto en la construcción de vehículos porque, como proveedor de servicios de ingeniería, pone en marcha proyectos de carreras de automóviles. También en este caso se observa una tendencia a la movilidad eléctrica. Para hacer frente a los retos que plantea este cambio, el director general Andreas Puschel apuesta por un enfoque integrado, ya que “un cambio en el tren de tracción recorre todo el vehículo como una cadena”. La pesada batería, por ejemplo, obliga al diseñador a encontrar soluciones ligeras que no sólo sirven para reducir el peso al de un vehículo con motor de combustión interna. Mucho más, el objetivo es hacer que el vehículo sea más eficiente en todos los aspectos, para ahorrar costes con respecto a los coches eléctricos estándar.
Superfluo: planta de prensado, taller de carrocería y taller de pintura
El profesor Günther Schuh, de la Universidad de Aquisgrán, también ha aprendido un poco de las carreras de coches. En 2017, el director del laboratorio de máquinas-herramienta y Fraunhofer IPT presentó el concepto de producción del coche eléctrico de la ciudad, e.GO, en el famoso AWK Aachen Machine Tool Colloquium. Este coche se basa en la experiencia adquirida en el desarrollo y fabricación del transportador eléctrico StreetScooter, que ahora está siendo construido por el Grupo Deutsche Post DHL no sólo para su propio uso, sino también en una segunda fábrica recientemente inaugurada para otras empresas.
En ese momento, había evitado cualquier cosa que pudiera aumentar los costes del StreetScooter eléctrico, por ejemplo, las costosas estructuras de la carrocería y las herramientas de encofrado. La idea detrás del e.GO eléctrico es similar. Como CEO de e.GO Mobil AG, Schuh y su equipo se han mantenido con el concepto de bastidor espacial, en el que la cadena de tolerancia se construye de adentro hacia afuera. Este concepto radical de cuadro ya ha demostrado su eficacia en los coches de carreras de Fórmula 1: en lugar de un cuerpo autoportante, se utiliza un marco de perfil de aluminio soldado y se cubre con molduras de plástico. Schuh explica: “Espero las más mínimas desviaciones en la tolerancia y una mínima modificación”.
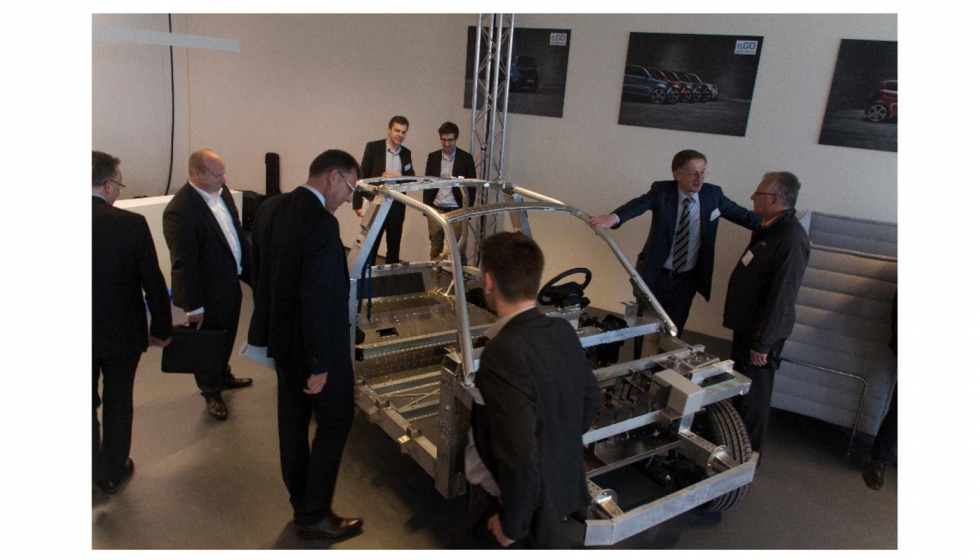
Minimalismo: En lugar de una carrocería autoportante, el coche eléctrico e.GO se conforma con un bastidor de perfil de aluminio soldado cubierto con molduras de plástico. Imagen: Fecht.
Después de la inauguración oficial de la nueva fábrica el 13 de julio en Aquisgrán, todo estará claro: la planta funcionará sin necesidad de un taller de prensado, un taller de carrocería y un taller de pintura. En lugar de conformar la chapa metálica en componentes de carrocería, el experto en producción confía en “perfiles de aluminio algo sobredimensionados, que son soldados por robots automatizados en un cubo robusto en una carcasa en bruto mucho más pequeña”. Al igual que con el StreetScooter, las tablas de plástico de colores se montarán en la parte superior de este cubo. De esta manera, la producción de chasis requiere pocos y pequeños componentes integrales, lo que resulta en unos costes de herramientas bastante bajos.
El concepto sugiere que puede ser implementado no sólo en una fábrica en un terreno no urbanizado, sino también en una “planta industrial abandonada” existente. El montaje funciona según el concepto de gimnasio, lo que significa que no requiere equipo pesado. Los camiones inteligentes que se desplazan por el suelo entran en el salón de actos y la estructura vertical restante se cuelga bajo el techo. Schuh dice: “Y este concepto puede ser implementado en cualquier sala de forma eficiente, práctica y sencilla”.
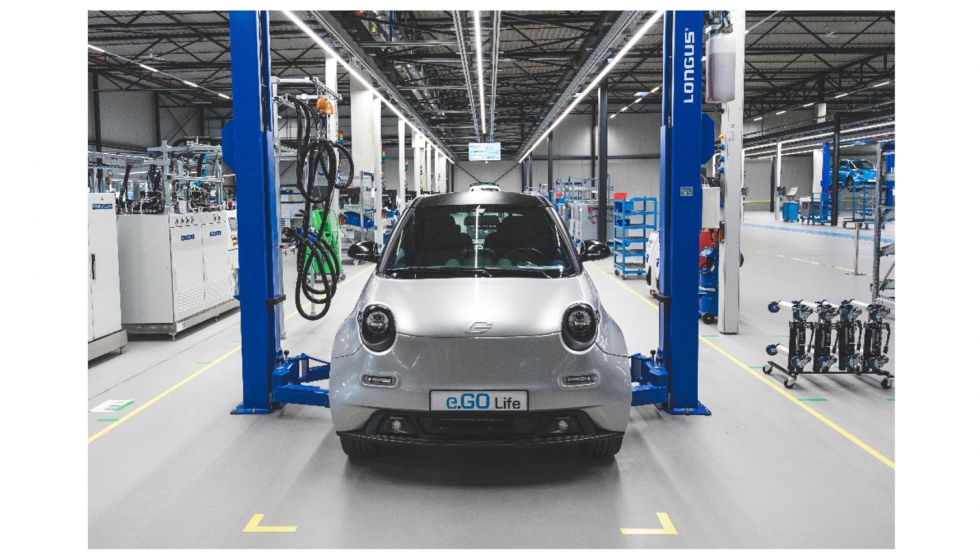
Estreno el 13 de julio de 2018: Inauguración de la nueva fábrica de eGO Mobile AG, que producirá 10.000 coches eléctricos en un solo turno a partir de 2019. Foto: e.GO.
Mientras que los ingenieros de Aquisgrán prescindirán de la tecnología y las herramientas de conformado, otros continúan desarrollándolas bajo los requisitos especiales de la electro-movilidad. En el caso de los vehículos eléctricos, se requiere una construcción ligera debido a que la batería es pesada; y debido a que hay un mayor número de variantes y tamaños de lote inicialmente más pequeños, se requieren procesos de fabricación altamente flexibles. La flexión giratoria incremental debe cumplir ambos requisitos. Este proceso, que forma la chapa paso a paso en frío, se originó en el marco del proyecto ISB Elektro, financiado por el Ministerio Federal de Economía y Energía de Alemania. Fue desarrollado por EDAG Engineering GmbH de Wiesbaden junto con el proveedor de la industria automovilística Kirchhoff Automotive, Kronenberg Profil GmbH, Lewa Attendorn y la Cátedra de Tecnología de Conformado de la Universidad de Siegen.
Sustitución de la construcción de carcasa convencional
El curvado giratorio incremental (ISB) es un proceso que dobla y forma perfiles semiacabados y permite producir estructuras ligeras escalables de forma flexible en la construcción de perfiles hasta un tamaño de lote de 1. Después de un desarrollo y pruebas exitosas, incluso tiene el potencial, en casos especiales, como la construcción de vehículos eléctricos, de sustituir a la construcción de carcasas convencionales. Sin embargo, requiere una herramienta de conformado que pueda adaptarse a diferentes geometrías de curvatura. Después de sujetar la pieza semielaborada, una unidad giratoria forma un área parcial. A continuación, se realiza la flexión giratoria del siguiente elemento curvado, una vez que la pieza ha sido liberada y el perfil ha sido posicionado más adelante. De esta manera, la pieza semiacabada se forma en frío paso a paso.
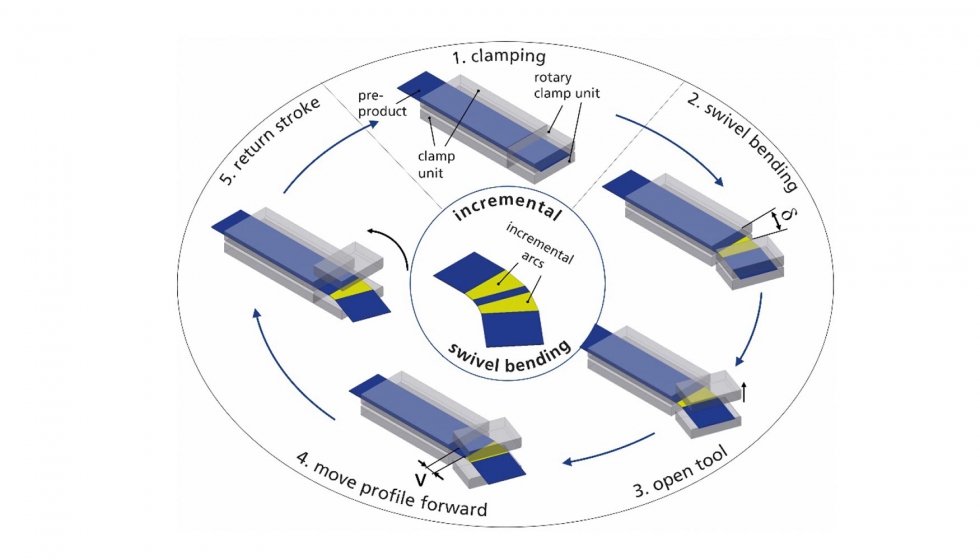
El diseño y la fabricación de un larguero de marco de 2 mm de espesor para un vehículo eléctrico sirve para demostrar el nuevo proceso. Para probar el proceso se utilizó una servoprensa del Automotive Center Südwestfalen GmbH en Attendorn, Alemania, en la que se formaron en frío con una herramienta piezas semielaboradas de acero de doble fase (DP800). Según un artículo especializado de la revista ATZ (05/2017), los expertos pudieron generar de forma fiable diferentes ángulos de flexión de 14 a 36 ° variando los parámetros del proceso. Los autores de la ZTA explican: “Junto con las curvas ilustradas alrededor del eje transversal del perfil, ha sido posible producir el larguero por medio de ISB”.
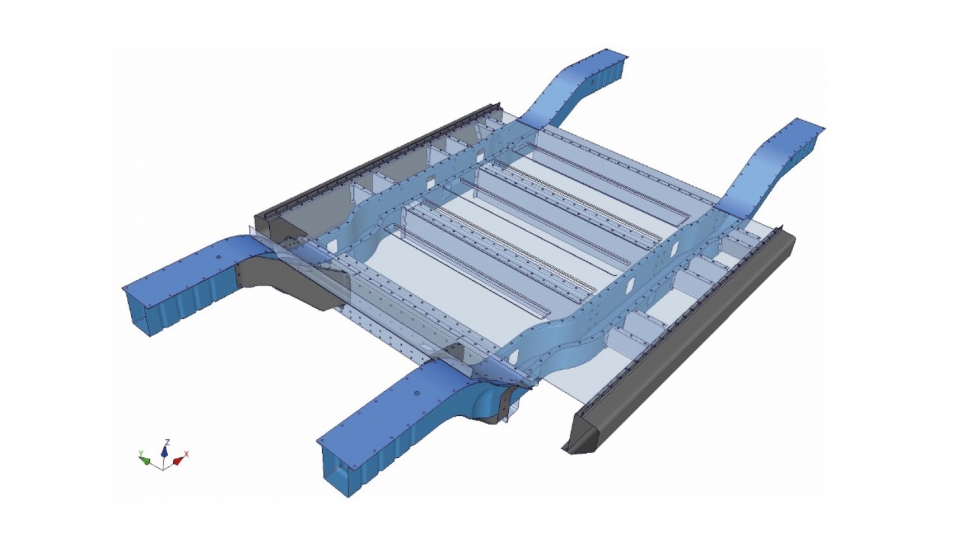
Rediseño: El grupo de bajos de un coche eléctrico recibió una nueva estructura longitudinal formada por una flexión giratoria incremental. Gráfico: EDAG.
Primero decapar, luego soldar
La electro-movilidad también impone exigencias especiales a la tecnología de unión. “Las baterías y los sistemas de accionamiento electrónicos utilizan materiales como el cobre o el aluminio, que son menos importantes para los motores de combustión interna”, comenta Rüdiger Brockmann, director de gestión y marketing industrial y de productos de Trumpf Laser- und Systemtechnik GmbH en Ditzingen. La empresa ya ha recibido solicitudes para el ensamblaje de láminas de cobre delgadas hasta electrodos gruesos. El láser también se utiliza para quitar la pintura de las horquillas de los motores eléctricos, que sustituyen a los devanados. La pintura se utiliza para aislar las horquillas y debe ser eliminada en las soldaduras. Idealmente, esto se hace con láser porque es más limpio, más preciso, más suave y más rápido que un proceso de remoción mecánica. La soldadura posterior se realiza también por láser.
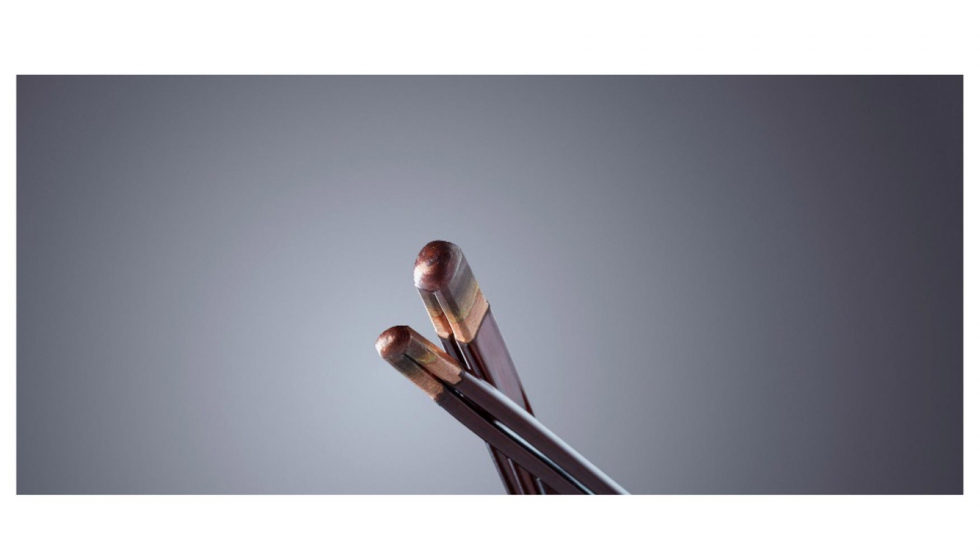
Doble uso: La tecnología láser elimina la pintura de las llamadas horquillas (sustitución de los bobinados de los motores eléctricos) y luego los suelda en estos puntos. Imagen: Trumpf.
En el campo del procesado por láser de compuestos de cobre-cobre o cobre-aluminio, Trumpf también apuesta por el láser verde: “Estas fuentes láser estándar de la industria que estamos introduciendo actualmente tienen un brillo significativamente mayor que los diodos láser azules y cuyo desarrollo llevará varios años más”, dice Brockmann. “En nuestro laboratorio de Schramberg ya hemos realizado experimentos con tres láseres de disco de 1 kW acoplados en verde. De esta manera, podríamos alcanzar una potencia de tres kilovatios a partir de una fibra de 200 μm, que permite tanto la soldadura por conducción térmica rápida y sin salpicaduras como la soldadura profunda en cobre”.
Soldadura por láser sin salpicaduras gracias a la guía de tres haces
Un proceso de soldadura láser de la empresa Laserline GmbH de Mülheim-Kärlich es adecuado para los estuches de baterías; la empresa recibió recientemente el ‘Innovation Award Laser Technology 2018’ en el Congreso de Tecnología Láser AKL'18 en Aquisgrán. El proceso fue encargado por el fabricante de automóviles VW, que había sido perturbado por las salpicaduras anteriores durante la soldadura láser. La petición de VW era que desarrollaran un método limpio y basado en láser para soldar acero galvanizado. En estrecha colaboración con Volkswagen, desarrolló una nueva óptica con guía de tres haces y un punto rectangular optimizado: Los rayos frontales más pequeños dispuestos alrededor del punto principal eliminan el galvanizado en los bordes de la costura soldada, mientras que la viga principal se funde y se une al alambre de soldadura.
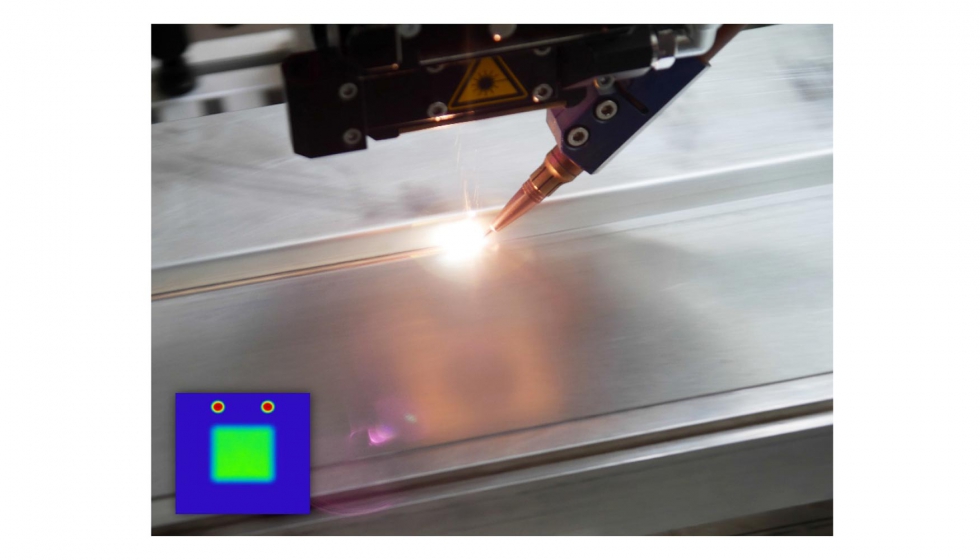
Sistema de tres haces: La tecnología láser multihaz desarrollada para VW no sólo es adecuada para soldar acero galvanizado (en la foto), sino también para la soldadura láser de carcasas de baterías. Imagen: Laserline.
Las vigas se alinean entre sí exactamente para estabilizar el proceso de soldadura. De hecho, se trata de una solución versátil que también es adecuada para los requisitos especiales de la construcción de vehículos eléctricos ligeros, según los expertos en automoción que asistieron a la presentación del proceso en el Congreso de Tecnología Láser AKL'18 en mayo. Una variante del proceso láser prácticamente sin salpicaduras suelda los paneles de aluminio de la carrocería en Porsche. El rendimiento del proceso también habla a favor del módulo multipunto integrado en la óptica láser, ya que aumenta tanto la profundidad de penetración como la velocidad de soldadura. Dado que las impresoras 3D de bajo coste han estado disponibles en tiendas de electrónica, algunos esperan maravillas reales de este tipo de fabricación aditiva. Pero la prensa de consumo ha perdido interés en el tema después de los informes iniciales de las supuestamente completamente impresas en 3D subametralladoras, automóviles y casas. La situación es diferente en el caso de las principales partes interesadas en la fabricación de aditivos, que han estado utilizando esta tecnología casi desde el principio. Estamos hablando de BMW AG en Múnich, que lleva casi 30 años fabricando componentes de plástico y metal. Sin embargo, el fabricante de automóviles se limitó anteriormente a construir piezas de repuesto o componentes para la competición, que sólo se fabrican en cantidades muy pequeñas.
BMW presenta los primeros componentes del mundo impresos en 3D producidos en serie
En la AKL'18 de Aquisgrán, Maximilian Meixlsperger, director de fabricación de aditivos de BMW, presentó con orgullo lo que, según la empresa, es el primer componente metálico fabricado y producido en masa con aditivos del mundo: A primera vista no es una innovación sensacional. Es el único soporte de la cubierta del techo del nuevo BMW i8 roadster, que el fabricante del coche fabrica utilizando una aleación de aluminio (AlSi10Mg) con Laser Power Bed Fusion (también conocido como Selective Laser Melting SLM). Sustituye a los componentes anteriores de plástico reforzado con fibra de vidrio (PA5GF30).
Pero lo emocionante, sin embargo, no es la impresión en 3D y las ventajas técnicas (en comparación con la parte plástica anterior, la nueva parte es diez veces más fuerte, mientras que su masa es casi la mitad), sino el aspecto financiero: Con este proceso, BMW es capaz de reducir los costes de fabricación en un 30% en comparación con la fundición a presión de magnesio prevista originalmente, especialmente porque la producción está totalmente automatizada en una operación de tres turnos sin necesidad de personal. La fundición a presión sólo vale la pena a partir de 60.000 piezas. Este estreno mundial es un gran paso adelante, pero los expertos en impresión 3D de la industria del automóvil y de los institutos habían asumido que sólo se necesitarían de cinco a diez años para producir en masa y de forma económica componentes metálicos impresos en 3D. Como explica Meixlsperger: “Actualmente estamos investigando cómo podemos producir en masa muchos componentes con impresión en 3D, algunos de los cuales también se pueden utilizar en la carrocería”. Y quizás este sea otro estreno mundial en la serie i eléctrica de BMW.
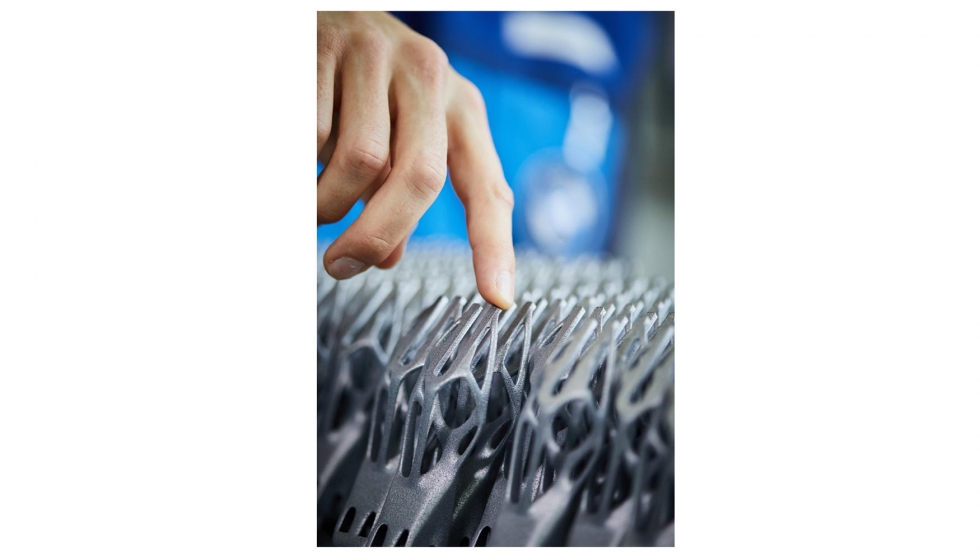
¿Primero la bisagra, luego el cuerpo? El soporte fabricado en serie para el techo convertible del BMW i8 Roadster es más económico que la fundición a presión de magnesio. Imagen: BMW.