Mecanizado de componentes aeroespaciales de titanio utilizando la avanzada estrategia de mecanizado para un mayor volumen de extracción de metal
El complejo diseño de las piezas y la creciente demanda ha forzado el desarrollo de nuevas tecnologías y soluciones de mecanizado, con objeto de asistir a la pequeña y mediana empresa para que su producción sea más competitiva. Iscar ha desarrollado unos procesos de torneado, fresado y taladrado muy avanzados, combinados con las más innovadoras calidades y geometrías y exclusivos rompevirutas, capaces de mecanizar las formas más complejas manteniendo ceñidas tolerancias.
La utilización de titanio para la estructura de las aeronaves no ha parado de crecer desde los años 80, se empezó a utilizar en programas militares, pasando luego al sector comercial. Las aleaciones de titanio son una fuerte competencia para las aleaciones férricas, de níquel y aluminio, tanto en la industria militar como en la aeronáutica comercial.
Estas aplicaciones cubren completamente la gama de todas las piezas estructurales; desde las estructuras de las alas, sometidas a fuertes tensiones, y componentes de los trenes de aterrizaje, a pequeños pero críticos componentes como tubos hidráulicos, resortes y abrazaderas. Los nuevos productos de titanio, aleaciones y métodos de fabricación se emplean cada vez más en aeronáutica, por lo que la utilización del titanio está en proceso de continua expansión.
Los ingredientes que hacen que el titanio sea especial
La elección del titanio para aplicaciones aeronáuticas se debe a las propiedades específicas de este metal, como son:
- relación entre peso y resistencia
- fiabilidad
- resistencia a la corrosión
- excelentes propiedades mecánicas
- expansión térmica
Características del mecanizado de titanio y sus limitaciones
El titanio 6AL-4V es el material más utilizado en aeronáutica debido a la relación existente entre su ligero peso y su elevada resistencia. El mecanizado de aleaciones de titanio requiere unas fuerzas de mayores que las necesarias para acero. Sin embargo, las aleaciones de titanio presentan unas características metalúrgicas que hacen que su mecanizado sea más difícil que el de aceros de equivalente dureza.
El titanio es conocido por su capacidad de endurecimiento. Esta condición obliga a emplear ángulos de corte positivos en el mecanizado, que hace que la superficie de contacto de la viruta con la zona de corte de la herramienta sea muy pequeña. La elevada presión junto con la fricción generada por el paso de la viruta da como resultado un aumento de la temperatura en una zona localizada de la herramienta. El calor generado durante el mecanizado de titanio no se disipa rápidamente, debido a la escasa conductividad. Por tanto, una sustancial cantidad de calor queda atrapada entre el filo de corte y la superficie frontal de la herramienta.
Esta combinación de elevadas fuerzas de rozamiento y temperatura produce un mecanismo de desgaste por craterización en la proximidad del filo de corte, dando como resultado una rápida rotura de la herramienta.
Dado su relativamente bajo modulo de elasticidad, el titanio es más flexible que el acero, por lo que el área que se está cortando tiende a rechazar la herramienta, a menos que el amarre de la pieza sea el idóneo o que se apliquen condiciones de mecanizado pesado. Las piezas de paredes delgadas tienden a curvarse bajo la presión de la herramienta, ocasionando vibraciones, erosión en la herramienta y problemas de tolerancia. La solución es garantizar la rigidez de todo el sistema y utilizar herramientas con filos de corte vivos y las correctas características geométricas.
Para empeorar las cosas, las aleaciones de titanio tienen una fuerte tendencia a alearse o reaccionar químicamente con el material de la herramienta a la temperatura generada durante el mecanizado, y a ocasionar desgaste por transferencia de material, ya que las virutas se sueldan al filo de corte.
Fresado trocoidal, solución avanzada para una elevada extracción de metal
Una estrategia que está cobrando fuerza para obtener unos elevados índices de extracción de metal en el mecanizado de titanio es el fresado trocoidal. El mecanizado de cavidades en titanio, ya sean de poca o mucha profundidad, es una tarea difícil. Para empezar, una gran porción de la herramienta está continuamente en contacto con la pieza, por lo que las fuerzas de corte y el calor generado son muy elevados. Un segundo punto a tener en cuenta es la desigual carga de viruta por diente, más elevada en el punto de la herramienta que más ha avanzado, y menor en el resto. El último punto es la evacuación de viruta, ya que la herramienta ocupa casi todo el ancho de la ranura. Queda muy poco espacio, por lo que la posibilidad de volver a introducir viruta en el corte es muy elevada y nada recomendable, debiéndose evitar en lo posible.
El centro de investigación y desarrollo de Iscar impulsa y recomienda el fresado trocoidal y ha potenciado el desarrollo de fresas con mango de metal duro integral y fresas multidiente para una elevada productividad utilizando plaquitas intercambiables.
En este sentido, el fresado trocoidal puede aplicarse fácilmente utilizando una gran variedad de fresas Iscar. Sin embargo, para obtener unos excelentes resultados se recomienda utilizar el nuevo desarrollo Chatterfree (Antivibratorias) de Iscar, y las líneas Helido ó Helimill (geometrías helicoidales) con plaquitas intercambiables.
El reto en el mecanizado de titanio es todavía mayor cuando las ranuras son relativamente profundas en relación con su ancho, ya que la evacuación de la viruta es más difícil. Este punto se dificulta aún más en el caso de ranuras curvas.
Normalmente estas dificultades hacen necesario que se trabaje con bajos avances y profundidades de corte, para evitar vibraciones y una rotura prematura de la herramienta. Estas condiciones hacen que la productividad disminuya. Incluso con bajos avances, la duración de la herramienta es menor cuando se mecanizan ranuras.
Fresado trocoidal, una solución potencial
El fresado trocoidal, o espiral, ofrece una solución potencial a este problema. La idea básica es que la fresa se mueva siguiendo un patrón circular en el que cada círculo avance en el corte. Una ventaja clave del fresado trocoidal es que sólo una pequeña parte de la fresa está en contacto con la pieza. El avance es constante. Además, el fresado trocoidal hace posible utilizar una fresa de menor diámetro que la ranura o cajera y facilita la evacuación de viruta (ver fig. 1 y 2)
Las fresas Chatterfree de Iscar, con configuración de paso variable, no sólo elimina la vibración armónica durante el fresado trocoidal, también ha demostrado tener una extraordinaria capacidad para abrir ranuras completas y cavidades, en cuanto a los índices de extracción de metal. Chatterfree también ofrece la ventaja adicional de tener una duración más prolongada gracias a la reducción de vibraciones. Chatterfree puede mecanizar ranuras completas de hasta 2xD con 4 ó 5 labios, incluso en máquinas de baja potencia con adaptaciones ISO40 ó BT40, sin reducir la productividad.
La excepcional calidad IC900 de Iscar con el avanzado recubrimiento PVD TiAlN ofrece unas incomparables propiedades mecánicas que hacen que esta fresa de metal duro integral sea la selección óptima para el fresado trocoidal.
Una alternativa es la utilización de plaquitas intercambiables, como las líneas Helido ó Helimill de Iscar, con fresas multidiente. Una vez que la fresa multidiente ha iniciado el fresado trocoidal, cada filo de corte individual entra en la pieza generando un calor y un esfuerzo mínimos. La ventaja de utilizar fresas multidiente es el elevado avance por diente que se puede aplicar, lo que se traduce en una productividad mucho mayor.
A pesar de su potencial, el fresado trocoidal también presenta algunos retos. La fresa debe realizar un complicado movimiento que puede ir más allá de la capacidad de los sistemas de programación CNC convencionales. Además, la máquina debe ser lo suficientemente rígida y rápida para el fresado trocoidal. La fresa debe ser capaz trabajar a velocidades elevadas y ser adecuada para el material. La rigidez de la máquina determina el grado de agresividad posible del fresado trocoidal. Otros factores que influyen son el tamaño de la fresa, el material de la pieza y la profundidad de corte.
La idea básica del mecanizado trocoidal implica un sustancial aumento de las velocidades de corte y de los índices de avance; las virutas se cortan a su máximo espesor al principio del corte y va disminuyendo hasta el final del mismo (fresado en concordancia). La trayectoria de cada diente se basa en los resultados de ciclos de mecanizado anteriores, eliminando movimientos en el aire y minimizando los movimientos de retracción.
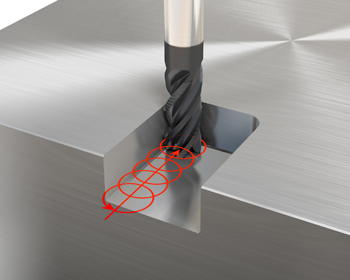
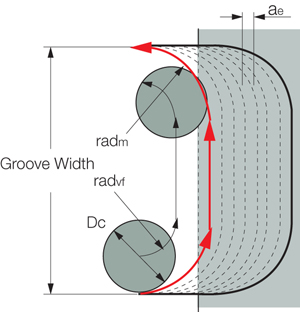
Beneficios de Costes
Uno de los beneficios es que se pueden mecanizar ranuras de mayor diámetro que el de corte. Esto quiere decir que se pueden mecanizar diferentes anchos de ranuras con el mismo diámetro de herramienta de una forma eficiente. Como la profundidad de corte es pequeña, se pueden utilizar fresas con mayor número de dientes, lo que implica mayores avances y velocidades de corte que en aplicaciones convencionales de fresado de ranuras.
Fresado trocoidal, retos de programación
El software de programación CNC convencional normalmente no puede generar programas para el fresado trocoidal. La única forma de realizar este tipo de fresado para el programador era codificar manualmente los complejos movimiento que debía realizar la herramienta. Sin embargo, el programador no podía comprobar visualmente el programa sin ejecutarlo en máquina. Por esta razón el fresado trocoidal no se utiliza mucho. Recientemente los diseñadores de software CAM han añadido secciones de rutinas para el fresado trocoidal con objeto de reducir el tiempo necesario de programación CNC. Esta opción da al programador acceso a otras herramientas como el simulador gráfico de mecanizado.
Las pruebas realizadas han demostrado que es más rápido el fresado trocoidal que el sistema convencional de fresado de ranuras, ya que se pueden aplicar unas condiciones mucho mayores.
Un ejemplo de cómo el fresado trocoidal puede mejorar la productividad y reducir el ciclo de mecanizado, así como los costes asociados, es ver la fresa Chatterfree de Iscar en acción.
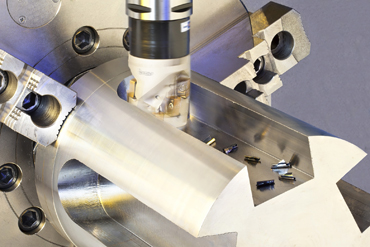
Caso real de mecanizado de una pieza aeronáutica de titanio mediante fresado trocoidal
El fresado trocoidal mejora sustancialmente la productividad de operaciones de fresado de ranuras. La práctica habitual de fresado de ranuras es aplicar un avance de aproximadamente el 20% del que se utilizaría para un fresado lateral normal. El fresado trocoidal permite incrementar el avance hasta un 80% del utilizado para fresado convencional. La intención es demostrar claramente cómo el fresado trocoidal reduce las tensiones y el calor generados durante el mecanizado. A pesar de que las velocidades y los avances son mucho mayores que para un fresado de ranuras convencionales, el desgaste de la herramienta es idéntico. El material utilizado ha sido titanio Ti-6Al-4V (Calidad 5), Recocido.
Fresado Trocoidal
Fresa Iscar: ECH160B32-6C16
Calidad de metal duro IC900
Diámetro de fresa: 16 mm
Vc=115 m/min
Fz=0.12 mm/d
Ap= 22 mm
Ae=1-1.5 mm
Refrigerante: Emulsión
Tiempo para producir una pieza: 33 minutos
Duración de la fresa: 4 pzas.
Adaptación: BT40
Notas: Sustancial reducción de la carga de la máquina. La máquina realiza operaciones fáciles y suaves, como si trabajara con material de fácil mecanización.
Fresado Convencional
Fresa Iscar: EFS-B44 16-34W16-92
Calidad de metal duro: IC900
Diámetro de fresa: 16 mm
Vc=45 m/min
Fz=0.04 mm/d
Ae=12 mm
Ap=12mm
Refrigerante: Emulsión
Duración de la fresa: 4 pzas.
Tiempo para producir una pieza: 55 min
Adaptación: BT40
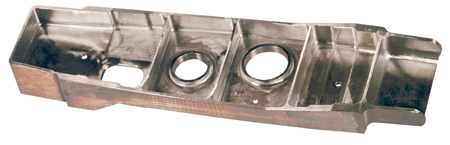