Aprovechando el poder del IoT en la gestión del aire comprimido
Roger Savo, director de Posventa de ELGi Compressors Europe
08/04/2024El concepto de Internet industrial de las cosas (IIoT) ha sido el punto central de los debates en torno a la evolución del sector manufacturero. Representa la integración de sistemas ciber físicos, análisis avanzados y conectividad de red en entornos industriales, lo que significa un cambio fundamental en los procesos industriales y de fabricación. Dentro de estos conceptos, las industrias pueden monitorear, analizar y mejorar las operaciones en tiempo real, y la maquinaria y los sistemas pueden incluso mejorar los procesos de forma autónoma a través de la autoptimización y la autoconfiguración, lo que lleva a una fabricación más inteligente.
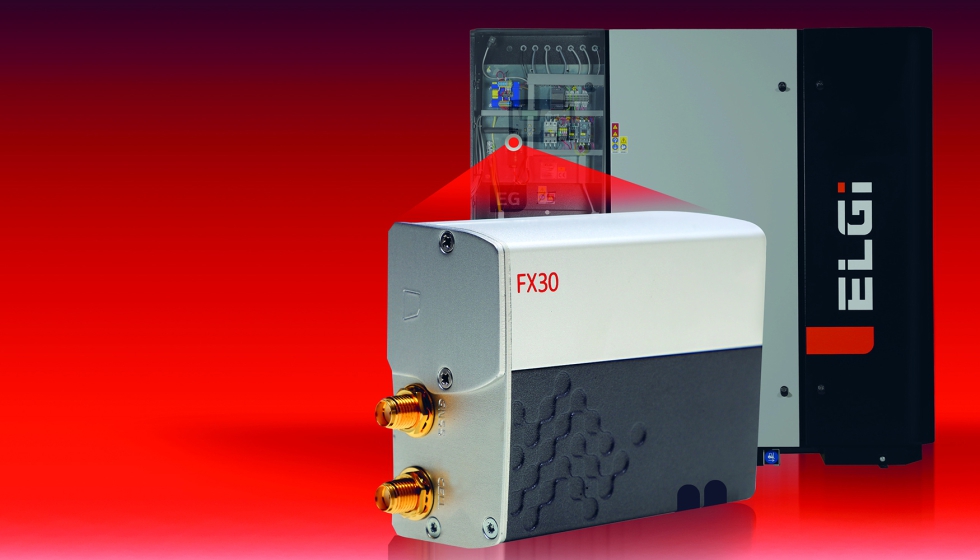
A medida que las industrias avanzan hacia entornos más inteligentes y conectados, los sistemas de aire comprimido (el componente vital de la industria y la piedra angular de las operaciones industriales) son otra área que presencia avances transformadores gracias al IIoT.
Cerrando la brecha humana
El panorama de la fabricación europea está cambiando. La escasez de mano de obra, especialmente en puestos técnicos, es cada vez más frecuente. Como resultado, muchos procesos de fabricación necesitan más manos humanas. Esto ha generado importantes desafío s para la continuidad del negocio, el mantenimiento de equipos y la producción. Al mismo tiempo, la creciente automatización y la necesidad de una mayor eficiencia han llevado a las industrias a buscar soluciones innovadoras.
IIoT ofrece un remedio. Al conectar equipos y activos a paneles que interpretan datos, IIoT proporciona información que permite a los técnicos realizar un trabajo más específico con todo el trabajo de investigación ya realizado en segundo plano. La automatización, el seguimiento y las acciones preventivas basadas en los datos recopilados son esenciales.
Gestión del aire comprimido en la era de los datos
Tradicionalmente, monitorear los sistemas de aire comprimido implicaba verificaciones manuales periódicas. Sin embargo, a medida que las industrias crecen y la demanda aumenta, el monitoreo manual se vuelve insostenible. Aquí es donde entra en juego el poder de la adquisición automatizada de datos.
Los sistemas remotos de monitoreo de aire comprimido como Air-Alert recopilan datos de compresores en funcionamiento, almacenan datos históricos y evalúan parámetros. Ya sea que se trate de mantenimiento correctivo o preventivo, los sistemas de monitoreo remoto intervienen cuando la intervención humana es insuficiente; para ello, ofrece gráficos de tendencias e información sobre los parámetros operativos, incluida la presión de descarga, la temperatura del aceite, la velocidad del variador de frecuencia (VFD), las horas totales de funcionamiento, los ciclos y las alertas en una interfaz en vivo en línea a la que se puede acceder de forma remota desde cualquier parte del mundo.
Antes, diagnosticar un problema requería participación e interacción humana en varios niveles del árbol de decisiones en la planta. Ahora, con la conectividad y la inteligencia incorporadas a la gestión del aire comprimido, los técnicos pueden profundizar en el historial del dispositivo, comprender las anomalías y abordarlas de forma proactiva.
Los datos actuales e históricos permiten a los profesionales de servicios comprender lo que sucedió y si podría haberse anticipado o no.
También ayuda a los OEM de compresores y a los proveedores de servicios a pronosticar actividades, programar recursos y realizar operaciones de mantenimiento para un compresor o para toda la flota instalada, ya que todo puede estar visible en un panel. También ayuda a los distribuidores y técnicos a pronosticar lo que será necesario hacer con la base instalada de la que es responsable la persona.
Del mantenimiento preventivo al predictivo
Sin embargo, el verdadero poder de los sistemas de monitorización remota está en la transición del mantenimiento preventivo al predictivo. Si bien el mantenimiento preventivo es crucial, el predictivo lo lleva un paso más allá.
Al examinar el comportamiento del ciclo de un compresor, como las frecuencias de carga/descarga en el caso de las unidades VFD, los técnicos pueden comprender el estado actual de la unidad. Pueden ver si hubo un aumento en el consumo de energía e investiga r si fue una anomalía o no y, potencialmente, dónde ocurrió el problema. La observación de parámetros como la presión y el consumo de energía también puede proporcionar información sobre si un compresor tiene el tamaño óptimo para la producción.
Cuantos más sistemas estén interconectados, más rico será el conjunto de datos, lo que permitirá que los algoritmos y los sistemas lógicos evalúen estos datos para predecir posibles fallos antes de que ocurran. Imagine conocer el posible fallo de un compre sor semanas antes de que suceda, todo ello basado en análisis de datos históricos y en tiempo real.
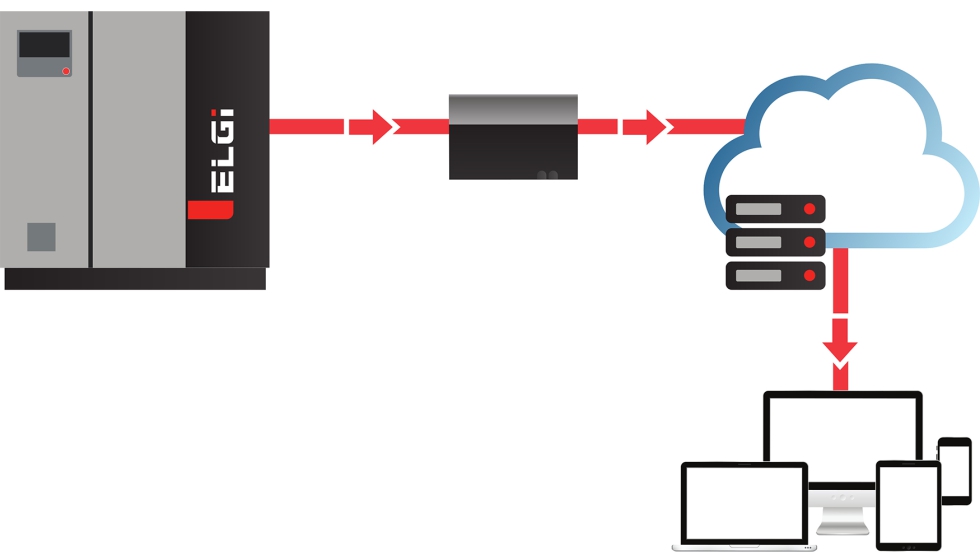
Poner a trabajar los datos de producción y aire comprimido... juntos
Aún queda por implementarse otra capa de integración: alinear los datos del compresor con los datos de producción. Si una empresa puede proporcionar su línea de tendencia de producción de qué y cuándo están produciendo, y se puede superponerla con los dato s del compresor de los sistemas de monitoreo remoto, se vuelve obvio conocer las ineficiencias y las fugas de aire aguas abajo de la sala de compresores. Si un compresor diseñado para operaciones de un turno se pone en marcha en medio de la noche, significa que hay consumo de aire en alguna parte del sistema. Si hay consumo de aire pero no hay actividad de producción, sólo puede significar una cosa: una fuga en alguna parte.
Por supuesto, muchas empresas tienen actuadores específicos para evitar esto, pero también hay plantas donde los compresores funcionan todo el día y toda la noche a presiones más bajas durante el tiempo de inactividad para evitar reiniciar los sistemas cuando comienza la producción. Otros detienen los compresores por la noche o durante el tiempo de inactividad y luego los reinician poco antes del inicio de la producción para que el sistema esté en funcionamiento. Sin embargo, todo esto en conjunto no impide que se produzca la fuga.
Las fugas suelen ocurrir en todo sistema de aire con el tiempo. Mangueras envejecidas, uniones inadecuadas, procedimientos de ajuste insuficientes, piezas incorrectas y/o corrosión pueden causarlo. Se ha estimado que entre el 20 y el 30 % del flujo de aire comprimido se puede perder debido a fugas.
Una fuga a través de un orificio de 3 mm (~1/8") puede consumir 4 kW (5 CV) de electricidad, lo que genera una pérdida anual de 19.200 kWh (a 7 bar g) (100 psi g.) 16 h/día durante 300 días al año). Esto crea una importante oportunidad de mejora.
Si bien algunos pueden decir que esto es solo aire, para ponerlo en perspectiva, hay que recordar que los compresores de aire consumen aproximadamente el 12% de la energía eléctrica utilizada en los procesos de fabricación que utilizan aire comprimido. Durante la vida útil de un compresor de aire, el 75% del costo es el uso de energía, el 15% es el costo d e la unidad y el 10% es el costo de mantenimiento.
Conclusión
El futuro de la gestión del aire comprimido y, de hecho, del sector manufacturero en general, reside en aprovechar el poder del IIoT. La innovación está impulsando la gestión del aire comprimido hacia una nueva era.
A medida que cambia la dinámica de la fuerza laboral y crece la demanda de métodos de producción eficientes, las plataformas IIoT, como los sistemas de monitoreo remoto de aire comprimido, brindan datos que no solo informan las decisiones sino que también impulsan acciones para operaciones industriales más innovadoras y eficientes.
Información basada en datos sobre la gestión del aire comprimido
-Monitoreo del rendimiento: medir los parámetros vitales de los compresores y visualizar estos datos en sistemas centralizados en tiempo real puede ofrecer una imagen precisa del rendimiento de cada máquina.
- Análisis de tendencia: el comportamiento del compresor se puede visualizar a lo largo del tiempo, lo que permite a los expertos ver tendencias que podrían indicar problemas potenciales.
- Eficiencia energética: al analizar los datos de los dispositivos de monitoreo, las industrias pueden identificar ineficiencias como fugas o modos operativos subóptimos, lo que genera ahorros sustanciales de energía y costos.
- Reducción del tiempo de inactividad: una de las ventajas más importantes del uso del análisis de datos en sistemas de aire comprimido es el mantenimiento predictivo. Al analizar datos históricos y en tiempo real, se pueden identificar problemas potenciales antes de que causen fallas, lo que reduce significativamente los tiempos de inactividad no planificados.
- Integración con datos de producción: la conexión de los datos del compresor con las métricas de producción permite obtener una visión global de las operaciones. Por ejemplo, si los datos de un compresor muestran un alto consumo de energía, pero las métricas de producción indican un rendimiento bajo, podría haber un problema de eficiencia. Los datos nos permiten discutir y analizar con el cliente si hubo un cambio en la producción, un cambio en el producto fabricado en esa línea de producción que podría conducir a un cambio en el comportamiento de un compresor, o si ocurrió algo más en ese momento. Esto ayuda tanto a los OEM como a los clientes finales a ajustar sus sistemas.