Soluciones para Industria 4.0 e IoT sencillas, abiertas y estandarizadas
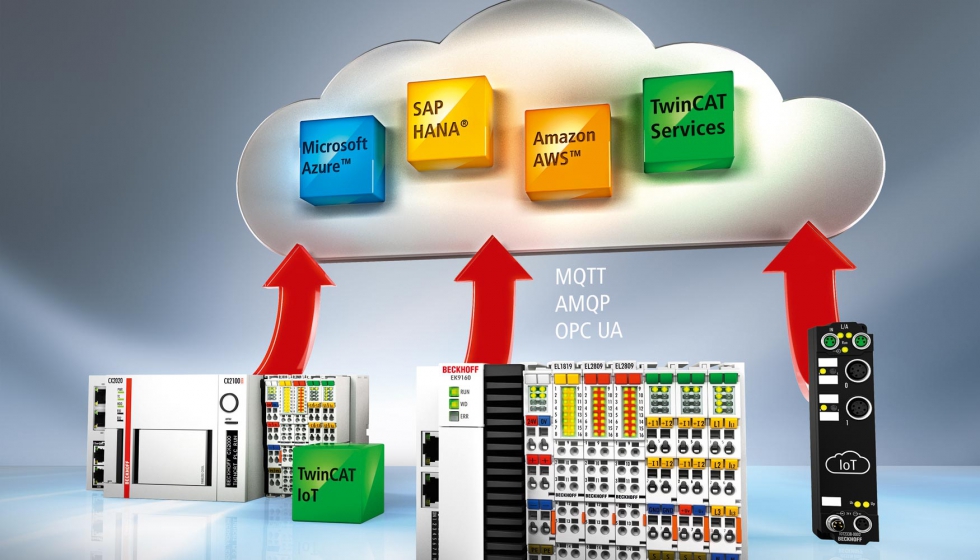
Los conceptos de Industria 4.0 e Internet of Things (IoT) establecen elevados requisitos a la interconexión y la comunicación de dispositivos y servicios. Desde el punto de vista de la pirámide de comunicación clásica (figura 1) se intercambian grandes cantidades de datos entre los sensores y las capas de orden superior. Pero también la comunicación horizontal entre los controladores PLC juega un papel importante en todas las modernas fábricas de producción. En este sentido, la tecnología de control basada en PC representa una base esencial y ya no es posible imaginar proyectos de automatización sin ella. Con el nuevo TwinCAT IoT, el software de control e ingeniería TwinCAT 3 pone a disposición una tecnología adecuada para conceptos Industria 4.0 y comunicación IoT. También los nuevos componentes I/O de Beckhoff, compatibles con IoT, permiten una integración idónea y de fácil configuración en aplicaciones en la nube pública o privada.
Definición de objetivos comerciales para aumentar las ventajas competitivas
Industria 4.0 e Internet of Things (IoT) no comienzan al mismo tiempo que la tecnología utilizada en cada caso, sino mucho antes. Para la implementación de proyectos IoT es de fundamental importancia comprobar en primer lugar los propios objetivos comerciales, es decir, establecer las ventajas que se quieren obtener como empresa de un proyecto de este tipo. Desde el punto de vista del fabricante de automatización se pueden definir en este sentido dos categorías diferentes de clientes: el fabricante de máquinas y sus clientes finales, es decir, el usuario de las máquinas automatizadas.
Justamente en el caso de una fábrica, naturalmente existirá interés en reducir los costes propios de producción, por ejemplo, mediante un control eficiente y fiable de la producción o, dado el caso, también mediante reducción de los productos producidos y desechados. El fabricante de máquinas tradicional pretende lograr objetivos similares y estará interesado en fabricar sus máquinas de forma más económica, aunque manteniendo o incluso aumentando la calidad. Naturalmente, también podrán tener cierta importancia aspectos como la optimización del consumo de energía y de los ciclos de producción de una máquina o también el mantenimiento preventivo y el diagnóstico de fallos. Los últimos dos puntos ofrecen al fabricante de máquinas una buena base para establecer servicios que pueden ofrecerse al cliente final como modelo de negocio adicional. En definitiva, para ambas categorías de clientes lo fundamental es lograr un diseño más atractivo de la máquina o el propio producto para aumentar la competitividad en el mercado.
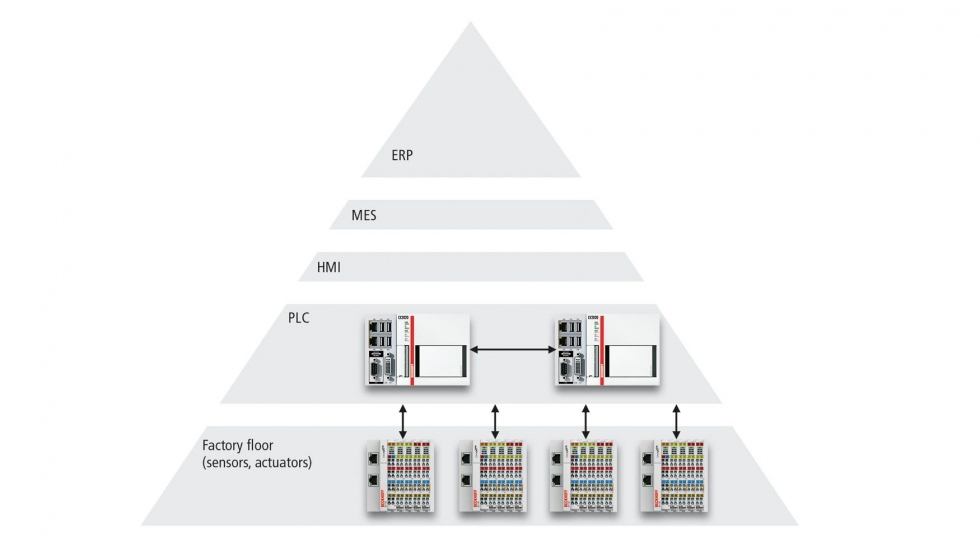
Captura, agrupación y análisis de datos de proceso
Los datos de proceso utilizados en el proceso de producción ofrecen una buena base para crear dicho valor añadido y lograr dichos objetivos comerciales. Entre otros, los valores de una máquina registrados por un sensor y transferidos al PLC a través de un bus de campo. Estos datos pueden ser analizados directamente en el control para supervisar el estado de una instalación con la ayuda de las bibliotecas TwinCAT Condition Monitoring integradas en el software de control TwinCAT 3, lo que permite reducir los tiempos de parada y los costes de mantenimiento.
No obstante, en áreas de producción con varios controladores distribuidos no siempre es suficiente con el análisis de datos de un controlador individual. Frecuentemente se necesitan los datos acumulados de varios o incluso todos los controladores de una instalación de producción o un tipo de máquina determinado para realizar un análisis de datos y una previsión analítica del sistema completo. Para ello se requiere la correspondiente infraestructura de TI. Las implementaciones realizadas hasta ahora preveían el uso de un sistema de servidor central establecido en la red empresarial o de las máquinas y equipado con una memoria de datos, frecuentemente en forma de un sistema de base de datos. Un software de análisis podía acceder entonces directamente a los datos acumulados en la base de datos y realizar las correspondientes evaluaciones (figura 2).
Aunque este tipo de procedimiento para realizar una acumulación y un análisis de datos en la planta de producción seguramente funcionaba bien, rápidamente surgieron varios problemas: En primer lugar se debía poner a disposición la infraestructura de TI necesaria. Resulta evidente que esto implica elevados costes de hardware y software para el correspondiente sistema de servidor. En segundo lugar, pero también importante se encuentra el aspecto del personal. Debido a la creciente complejidad en la conexión en red de las instalaciones de producción, precisamente en el caso de varios emplazamientos de producción distribuidos, se requiere del correspondiente personal para llevar a cabo la implementación. Un obstáculo adicional es que la escalabilidad de una solución de este tipo es muy reducida. Y finalmente, en algún momento se alcanzan los límites físicos del sistema de servidor, ya sea de la memoria disponible o también del tamaño de la memoria RAM o el rendimiento de la CPU necesario para los análisis. Cuando se requerían ampliaciones de la instalación con nuevas máquinas o controladores, esto conllevaba frecuentemente complejos trabajos de reestructuración manual. Además, el sistema central de servidor también debía crecer de forma acorde para poder manipular y procesar estos volúmenes de datos adicionales.
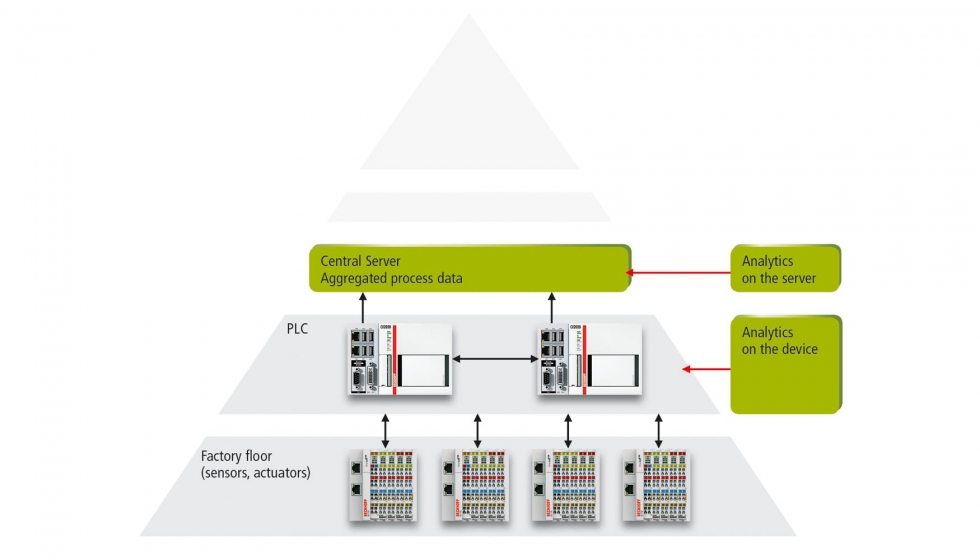
El camino hacia la nube pública
Los servicios de comunicación y datos basados en la nube intentan evitar las mencionadas desventajas poniendo a disposición del usuario un punto de vista abstracto de los sistemas de hardware y software en que se basan. Abstracto significa en este caso que el usuario no debe preocuparse por el sistema de servidor correspondiente para poder utilizar un servicio. Solo debe preocuparse por el uso del correspondiente servicio. Todos los trabajos de mantenimiento y conservación de la infraestructura de TI son realizados por el proveedor del sistema en la nube. Este tipo de sistemas en la nube se pueden subdividir en términos de nube pública y nube privada.
Los denominados proveedores de servicios en la nube pública como, por ejemplo, Microsoft Azure o Amazon Web Services (AWS), ponen a disposición del usuario diversos servicios de sus propios centros de cálculo. Esto abarca desde máquinas virtuales, en las que el usuario tiene el control sobre el sistema operativo y las aplicaciones instaladas, hasta servicios de comunicación y servicios abstractos, que pueden ser integrados por el usuario en una aplicación. Estos últimos incluyen, por ejemplo, también el acceso a algoritmos de Machine Learning, que pueden realizar previsiones y clasificaciones en relación a determinados estados de datos basándose en determinadas informaciones de las máquinas y la producción. Los algoritmos reciben los contenidos necesarios para ello con la ayuda de los servicios de comunicación.
Estos servicios de comunicación se basan habitualmente en protocolos de comunicación que se basan a su vez en el principio Publish/Subscriber. Esto tiene como consecuencia importantes ventajas gracias al desacoplamiento de todas las aplicaciones que se comunican entre sí. En primer lugar, los participantes de las comunicaciones ya no necesitan conocerse entre sí, por lo que se reduce el complejo proceso de dar a conocer la información de dirección. Todas las aplicaciones realizan las comunicaciones a través del servicio central en la nube. Por otro lado, en el caso de la comunicación de datos con el servicio en la nube, el denominado Message Broker (figura 3), se trata, desde el punto de vista del dispositivo terminal, de una comunicación puramente saliente, independientemente de que se envíen (Publish) o reciban (Suscribe) datos. Las ventajas resultantes para la configuración de la infraestructura de TI son evidentes: No se debe configurar ninguna conexión de comunicación entrante, por ejemplo, en cortafuegos u otros dispositivos finales de la red. Esto reduce considerablemente los costes de instalación y mantenimiento de la infraestructura de TI. En el caso de los protocolos de transporte utilizados para la comunicación de datos se trata de protocolos muy esbeltos y estandarizados como, por ejemplo, MQTT y AMQP. Además se cuenta con diversos mecanismos de seguridad integrados, por ejemplo, el cifrado de la comunicación de datos y la autenticación contra el bróker de mensajería. El protocolo de comunicaciones estandarizado OPC UA también ha reconocido el valor añadido de un escenario de comunicación basado en Publish/Subscribe e inducido los pasos correspondientes para integrar este principio de comunicación en la especificación. De este modo, además de MQTT y AMQP, otro estándar estará disponible como mecanismo de transporte hasta la nube.
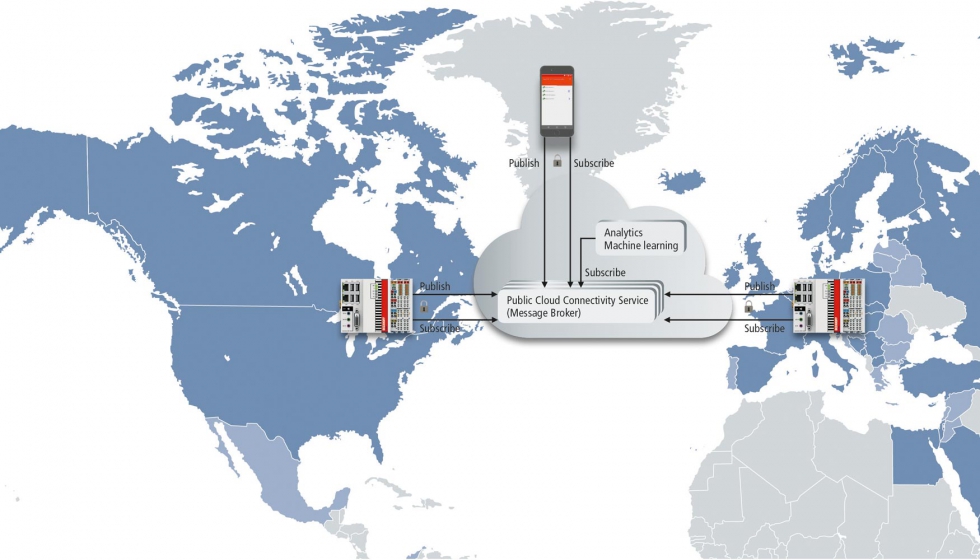
La nube privada
Sin embargo, estos mecanismos Publish/Subscribe no solo pueden ser útiles en los sistemas de nube pública, sino también en la red empresarial o de las máquinas. En el caso de MQTT y AMQP, la infraestructura necesaria en forma de un denominado Message Broker (bróker de mensajería) se puede instalar y poner a disposición fácilmente en cualquier PC. De este modo se pueden realizar, tanto escenarios M2M, como también la conexión de cualquier dispositivo terminal como, por ejemplo, un teléfono inteligente, al controlador. Además, permite asegurar aún más el acceso a estos dispositivos a través de sistemas cortafuegos (figura 4). También las ampliaciones de la especificación OPC-UA en cuanto a Publish/Subscribe facilitan a futuro la configuración y el uso de escenarios de comunicación 1:N dentro de una red de máquinas.
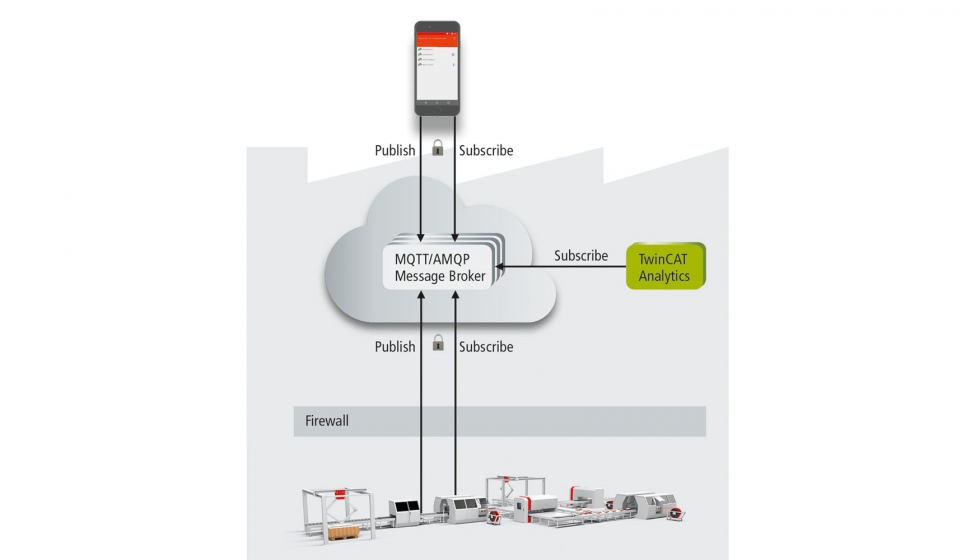
Productos para Industria 4.0 e IoT
Beckhoff pone a disposición de los usuarios diversos componentes para una integración sencilla y estandarizada en servicios de datos y comunicación basados en la nube. Los productos IoT dentro del software de automatización TwinCAT 3 ofrecen diferentes funcionalidades para intercambiar datos de proceso a través de protocolos de comunicación estandarizados basados en Publish/Subscribe y acceder a los servicios de datos y comunicación especiales de proveedores de servicios en la nube pública. Los correspondientes servicios se pueden albergar en sistemas en la nube pública, como Microsoft Azure o Amazon Web Services (AWS), pero del mismo modo también se pueden utilizar en sistemas en la nube privada.
El acceso a estas funciones IoT puede tener lugar a elección a través de módulos de función especiales, directamente desde el programa de control, o se puede configurar a través de una aplicación denominada ‘TwinCAT IoT Data Agent’ de forma externa al programa de control. Los datos de proceso que se van a transmitir se pueden seleccionar fácilmente a través de un configurador gráfico y configurar para la transferencia a un determinado servicio. Una gran ventaja consiste en que el Data Agent también permite la integración de servicios basados en la nube en instalaciones TwinCAT más antiguas ya existentes. Además, la lectura de los datos de proceso también puede realizarse a través del protocolo de comunicaciones estandarizado OPC UA, lo que también permite el uso de datos de sistemas que no sean de Beckhoff (figura 5). Una aplicación móvil disponible adicionalmente permite la indicación móvil de avisos de alarma y estado de una máquina.
Para el reenvío directo de señales I/O sin programa de control, a través del acoplador de bus IoT EK9160 de Beckhoff se pueden parametrizar los datos I/O para el envío a un servicio en la nube a través de una página web de fácil configuración en el dispositivo. El acoplador de bus se encarga automáticamente del envió de los datos I/O digitales o analógicos al servicio en la nube. Una estación de acoplador IoT está compuesta en este caso por un EK9160 y un gran número de terminales EtherCAT ultrarrápidos de alto rendimiento. Los datos transmitidos al servicio en la nube, opcionalmente también cifrados, son enviados en un formato JSON estandarizado y de uso sencillo. También se dispone de mecanismos ampliados, como un buffering local de los datos I/O en caso de interrupción de la conexión a internet o la supervisión de los buses de campo conectados. De este modo es posible recolectar las señales I/O no solo a través de EtherCAT, sino también, por ejemplo, a través de CANopen o Profibus.
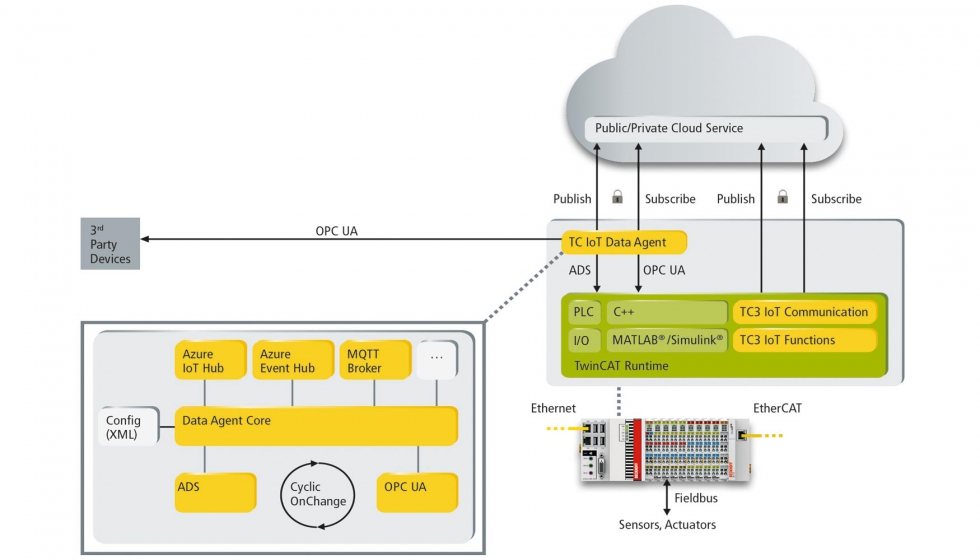
Analytics y Machine Learning
Una vez que los datos han sido enviados a un servicio en la nube pública o privada, la siguiente cuestión es de qué modo se continuarán procesando los datos. Como ya se ha mencionado anteriormente, muchos proveedores en la nube pública ofrecen diversos servicios de Analytics y Machine Learning que se pueden utilizar para el procesamiento posterior de los datos de proceso. Beckhoff también dispone de una plataforma propia de Analytics llamada TwinCAT Analytics. Esta pone a disposición los mecanismos correspondientes para el análisis de datos para registrar con precisión cíclica todos los datos de proceso relevantes de una máquina. De este modo se genera una transcripción completa de todos los procesos de la máquina.
Estos datos se pueden recolectar y analizar según sea necesario, bien localmente en el ordenador de la máquina o dentro de una solución en la nube pública o privada. TwinCAT Analytics utiliza TwinCAT IoT para la conexión a las soluciones en la nube, ofreciendo una comunicación de datos idónea. Como consecuencia resultan muchas nuevas ideas y modelos de negocio para el fabricante de máquinas y sus clientes finales.
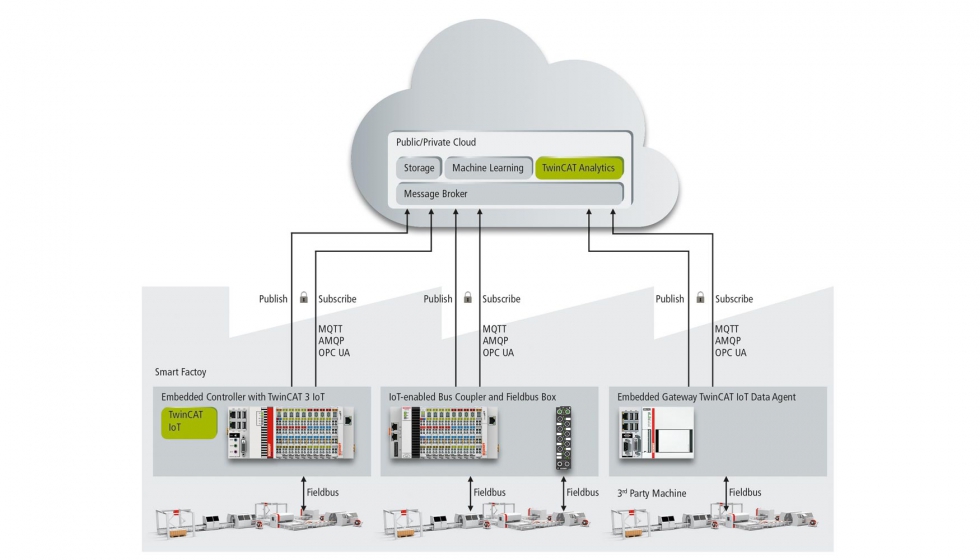
Conclusión
Industria 4.0 e IoT está en boca de todos. Para la realización de nuevos modelos de negocio también se necesitan requisitos innovadores en relación a la infraestructura de base, lo que impulsa aún más la fusión del nivel de TI y de automatización. Los servicios de datos basados en la nube pueden ayudar a realizar este tipo de proyectos de automatización. Permiten al fabricante de máquinas o cliente final prescindir de los conocimientos de TI correspondientes. Con TwinCAT IoT, así como con el acoplador de bus en la nube EK9160, Beckhoff pone a disposición de sus clientes dos series de productos que permiten integrar este tipo de servicios de datos basados en la nube de forma rápida y sencilla en el proyecto de control. El uso adicional de TwinCAT Analytics permite complementar este tipo de proyectos con una poderosa plataforma de análisis que analiza los datos de proceso registrados.