Tuning 4.0 y Servicios 4.0 para máquina-herramienta
Actualmente, para conseguir los objetivos de tiempos y calidad en los mecanizados de alta velocidad, es necesario un conocimiento exhaustivo del sistema completo, siendo necesario conocer con profundidad tanto el procedimiento de ajuste de los servos, los algoritmos de HSC del CNC y los distintos componentes mecánicos empleados. Históricamente el procedimiento de ajuste se ha basado en personal muy cualificado y con gran experiencia. Hoy en día debido al incremento de la complejidad en los algoritmos de HSC y del software de los servos, es muy difícil conseguir realizar los ajustes de una forma óptima sin una gran inversión en tiempo y formación del personal. Además debido a la gran cantidad de parámetros implicados y la compleja interrelación entre ellos, es fácil que se cometan errores humanos a la hora de parametrizar el sistema. FineTune es el resultado de un conjunto de tecnologías que permite un ajuste óptimo mediante el uso de sistemas expertos, fuzzy logic y la información acumulada en la base de datos de ajustes. Es por todo ello que a medida que la construcción de las máquinas evoluciona, FineTune se adapta a las nuevas arquitecturas, técnicas constructivas y materiales usados, basándose en el feedback de los ajustes. Actualmente este feedback se puede acceder de una forma manual debido a que todavía no es común que un CNC tenga acceso a internet.
Toda la información del proceso se recopila y puede ser mandada manualmente a Fagor Automation para añadirla a la base de datos y mejorar los futuros ajustes. Adicionalmente se crea un informe para el usuario en formato html y pdf que puede ser usado como referencia del estado de la máquina en el momento del ajuste. La figura 1 muestra el informe de una de las maquinas ajustadas. El informe puede ser visto desde cualquier navegador que soporte html 5. El CNC incorpora un servidor de http que hace que, si el CNC tiene conexión a Internet, los informes de la máquina puedan ser vistos desde cualquier dispositivo.
Para el desarrollo de Fine Tune ha sido necesario crear una infraestructura que ha abierto las puertas a nuevos desarrollos y servicio s 4.0 para el CNC 8065 que podrán ser desarrollados en el futuro tanto por parte de Fagor Automation como por terceras empresas. A continuación se enumeran algunas de las posibilidades de desarrollo de estos servicios.
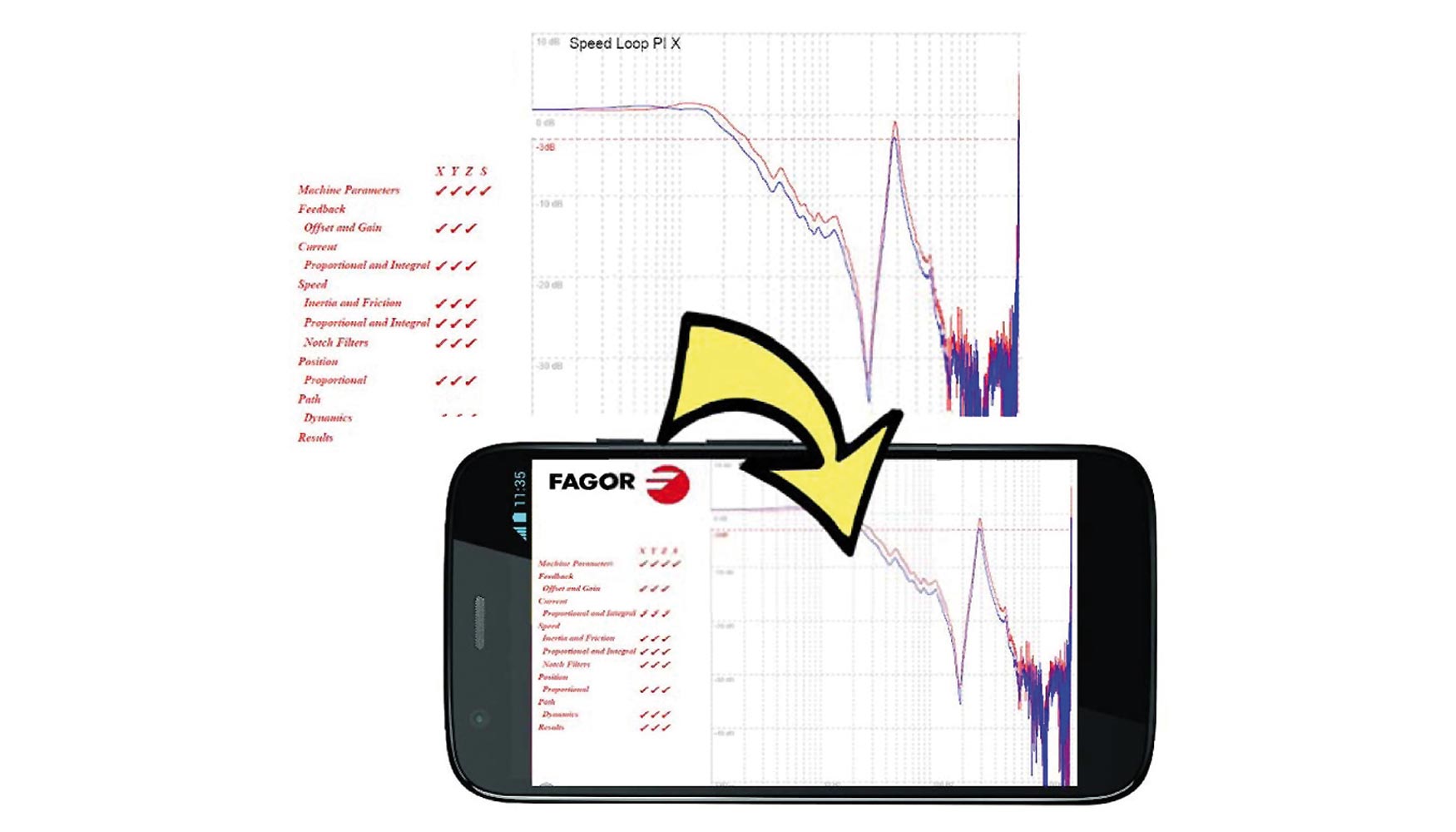
Estado de máquina
Además de las funcionalidades de envío de sms/emails para la notificación de eventos de la máquina, gracias al servidor de http es posible desarrollar los servicios para comprobar en tiempo real el estado de la máquina, número de piezas fabricadas, alarmas y errores, programa ejecutándose, etc.
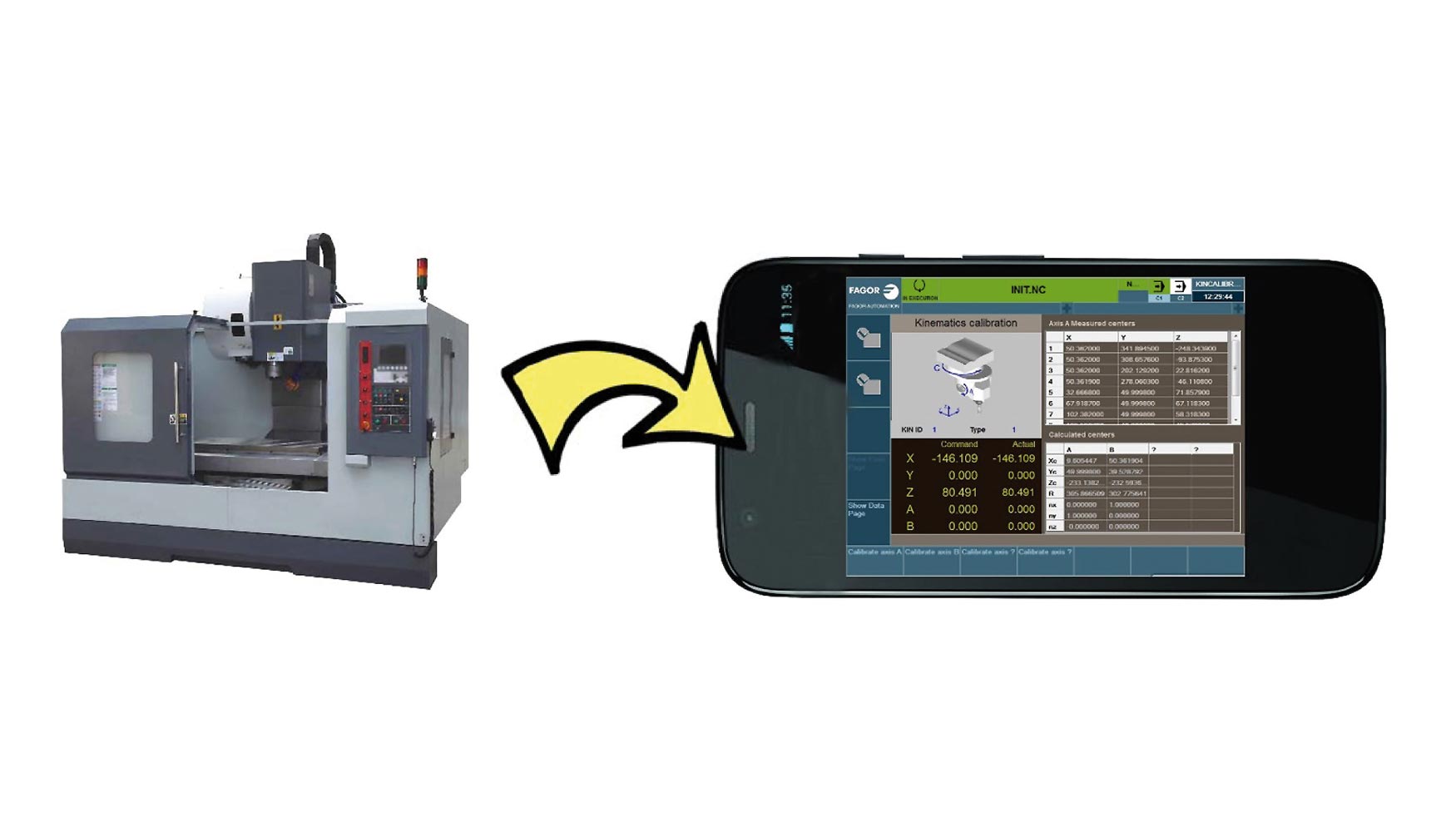
Optimización mecanizados
En la figura 4 se muestra cómo se puede mostrar información muy diversa como por ejemplo el tipo de movimiento ejecutado en la pieza siendo G00 verde, G01 rojo y G02/G03 azul. Toda la información disponible mostrada mediante gráficos permite de una diagnosis rápida y sencilla de la pieza y poder dar recomendaciones del estilo:
- “El 30% de las veces que se limita el avance es debido al jerk del eje X, se recomienda usar G132 X120 para aumentar un 20% el jerk del eje”
- “El error cordal recomendado para esta pieza es de 0,050”
- “Es recomendable regenerar el programa pieza con más decimales”
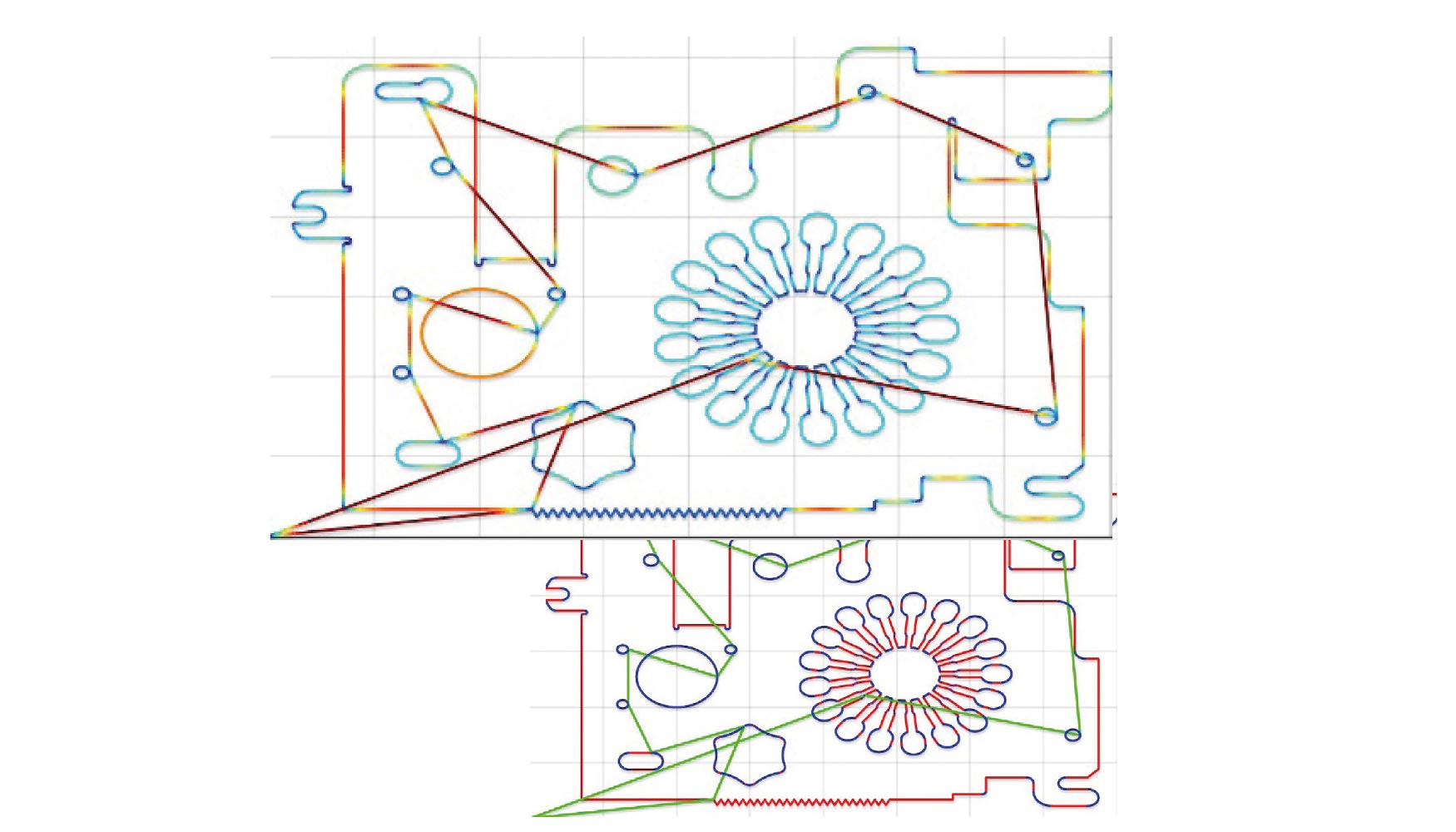
Arriba, figura 3. Abajo, figura 4.
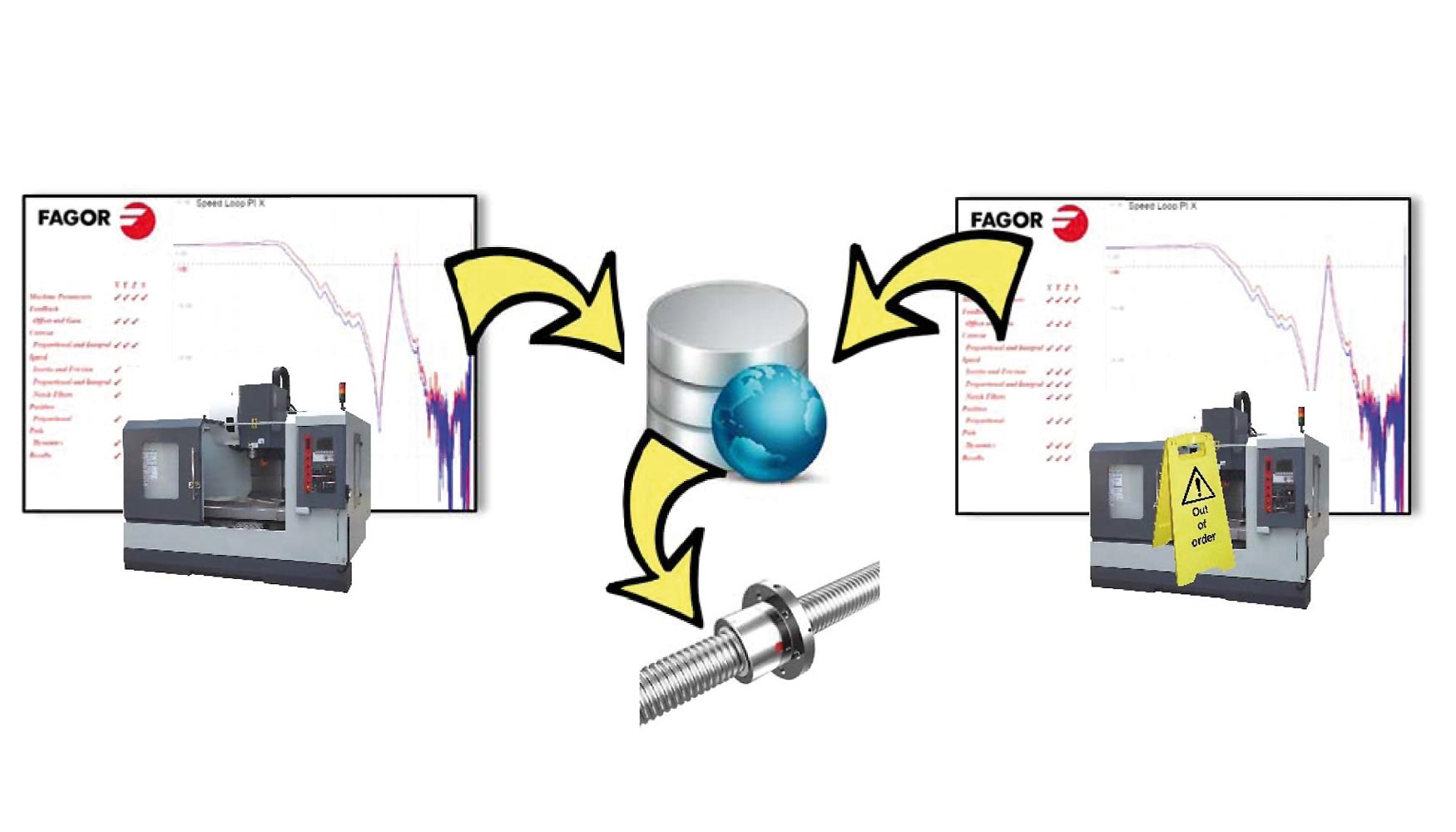
Mantenimiento
También es posible dar servicios CBM (Condition Based Maintenance), brevemente resumido como el mantenimiento que se hace cuando es realmente necesario. Para desarrollo de este tipo de servicios se necesita gran cantidad de información del sistema, la evolución histórica y los datos de máquinas similares. Toda esta información se obtiene a través del CNC y de la base de datos del servidor central. En la figura 5 se muestra el flujo de información del proceso. Cuando la máquina se fabrica se manda al servidor toda la información disponible de la máquina y se usará como punto de partida de la evolución de la máquina. A continuación se van haciendo ensayos periódicamente que se mandan al servidor central y se añaden al historial de la máquina. Con el historial de la máquina y la información de la base de datos se analizan los parámetros que definen ese tipo de máquina y si alguno de los parámetros se sale de la evolución natural se pueden recomendar ensayos adicionales para afinar en la diagnosis y hacer un mantenimiento si fuera necesario.
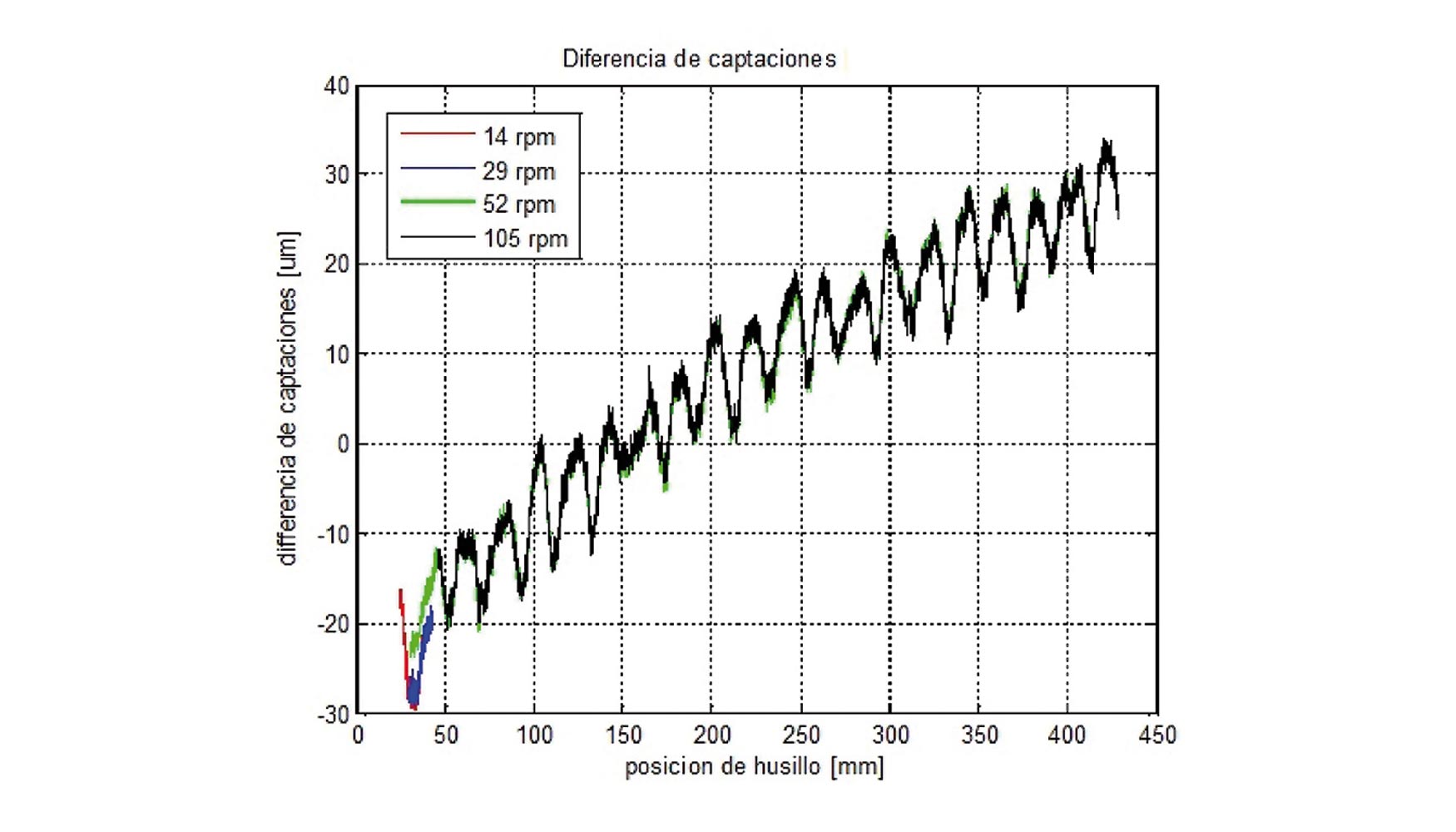
Diagnosis
Otro tipo de servicios 4.0 que se pueden dar basados en los desarrollos realizado son la diagnosis de las máquinas en la fase de puesta a punto. En el momento de ajuste de las máquinas suelen darse situaciones en las que después de haber montado la máquina se detectan comportamientos no deseados, como vibraciones, errores de seguimiento anómalos, y otros efectos no deseados. Mediante el uso de la información acumulada en la base de datos y la posibilidad de acceder a la información de todos los sensores es posible diagnosticar el origen de los problemas y solucionarlos de una forma rápida y eficiente. En caso de ser necesario es posible incluso añadir al sistema acelerómetros en los lugares deseados y obtener información adicional de estos acelerómetros sincronizada en tiempo real con el resto de información del CNC, como par motor, aceleraciones, velocidades, etc.
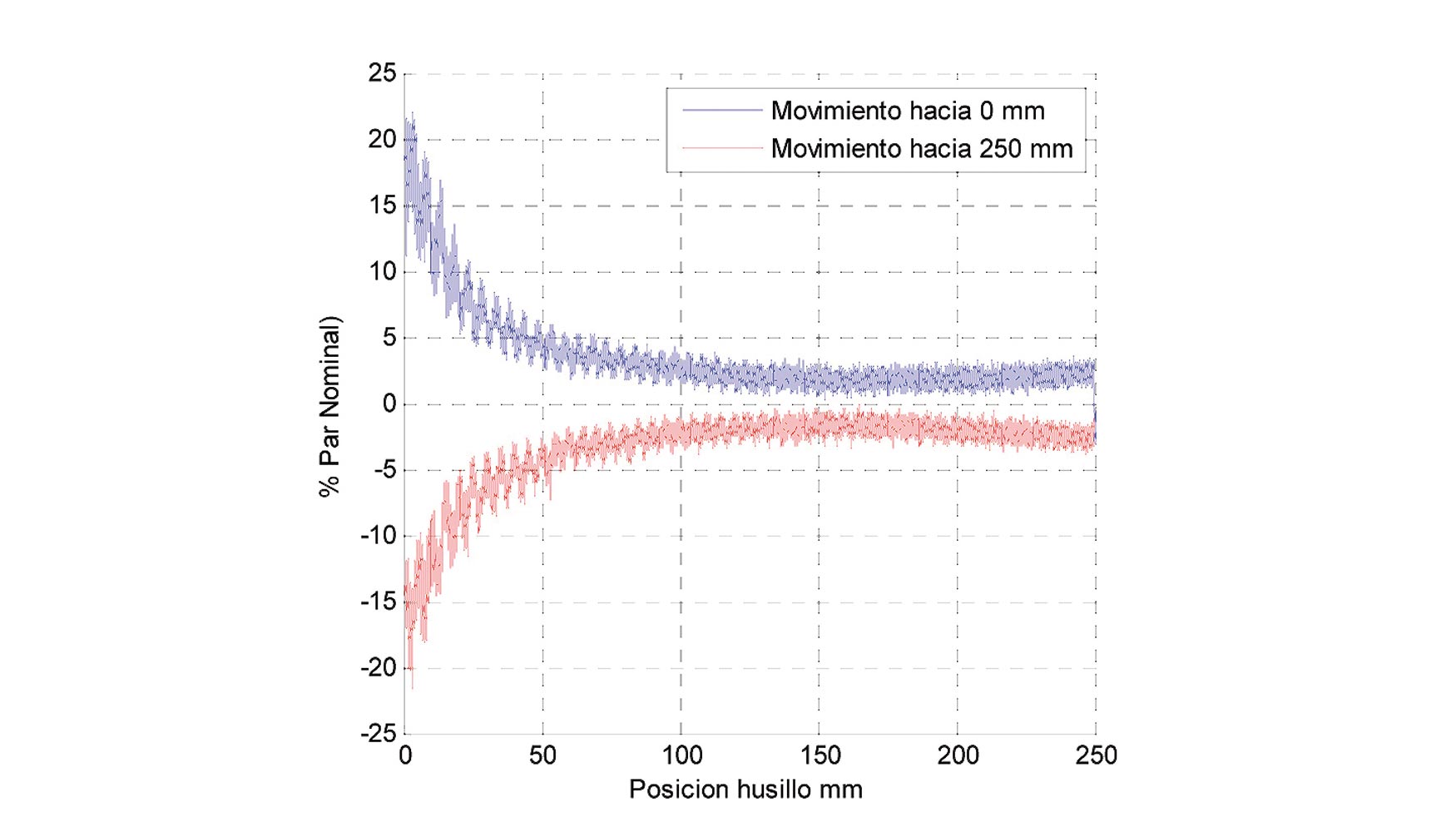
En las siguientes figuras se pueden observar algunos ejemplos reales. En la figura 6 se ve la Diferencia entre la captación del motor frente a la posición del husillo. Podemos contemplar cómo la diferencia de captaciones aumenta al cambiar la posición del husillo. Este aumento será debido, con mucha probabilidad, a un desalineamiento entre husillo-guías y regla, de forma que la pendiente indica precisamente el ángulo de desvío entre ambas rectas. Este efecto puede ser complicado de detectar de otra manera y si este defecto no se detecta en la puesta a punto puede causar desgastes y fatiga en la mecánica, que a medio plazo causará problemas en la máquina.
En la figura 7 podemos observar el par que hace el motor al moverse de un extremo del husillo al otro. En este caso podemos observar como al llegar a un extremo el par incrementa notablemente. Este efecto indica normalmente un des alineamiento entre los centros de la tuerca del husillo y el centro del rodamiento del husillo.
Conclusiones
Con el desarrollo de la aplicación FineTune se han cumplido el objetivo planteado de conseguir un ajuste óptimo de una manera sencilla, rápida y sin necesidad de mano de obra tan cualificada. Para lograr este objetivo ha sido necesario desarrollar una arquitectura basada en la recopilación de datos de los ajustes de las máquinas que permiten que FineTune evolucione y se vaya adaptando a las nuevas máquinas. Este desarrollo ha permitido que se analice la viabilidad de distintos servicios 4.0 como los presentados en este artículo.