Requisitos de los revestimientos protectores de larga durabilidad y su empleo en estructuras de hormigón
Borja Jimenez. Departamento Técnico de Sika, S.A.U.
17/04/2020Las estructuras de hormigón armado en general, y los puentes en particular, son susceptibles de sufrir el deterioro de sus condiciones de durabilidad originales debido a diversos factores, como por ejemplo, la carbonatación del hormigón, la presencia de humedad, la contaminación atmosférica u otros materiales o sustancias nocivas en general, especialmente en ambientes urbanos.
Para evitar los efectos de los agentes anteriores, y con objeto de prolongar la durabilidad de las estructuras de hormigón, existen diversos métodos que nos ayudan a conseguirlo, siendo la aplicación de revestimientos protectores una de las opciones más empleadas. Cuando se utilizan las tecnologías y los productos más adecuados para cada estructura en particular, y además se aplican correctamente, la efectividad de algunos sistemas de protección ha sido demostrada durante largos periodos de tiempo, en ocasiones de hasta 20 años.
En este artículo se describen algunas de las características específicas para estos tipos de sistemas, tales como la permeabilidad al agua, la transpirabilidad al vapor, resistencia a la difusión de CO2, etc. que contribuyen a la eficacia de un revestimiento protector. Además, se presentan varios casos de estudio a través de los cuales queremos demostrar la durabilidad de estos sistemas en obras reales y que han perdurado en el tiempo.
1.- Introducción
Estructuras como puentes, localizadas en medio urbano, han servido durante años para descongestionar ciudades del tráfico habitual, permitiendo un transporte más eficaz, tanto a nivel particular como a nivel comercial. Con el tiempo, las estructuras de hormigón armado, en particular los puentes, acaban estando sometidos a diversos agentes atmosféricos que, numerosas veces de forma prematura, se ven afectadas por los agentes antes comentados.
Con el objetivo de incrementar y mejorar la durabilidad de esas estructuras, tanto desde el momento de la concepción de estas como en intervenciones posteriores, se han venido protegiendo, por ejemplo, empleando revestimientos protectores especialmente formulados para hacer frente a esos agentes.
2.- Deterioro de las estructuras de puentes de hormigón
Las estructuras de los puentes de hormigón tienden a deteriorarse por diversos factores, entre los que se encuentra la corrosión de armaduras debido a la presencia de cloruros o por la carbonatación del hormigón, el ataque de los sulfatos, la reacción álcali-sílice, así como la acción del hielo y deshielo. Existen otros tipos de deterioro (por ejemplo, la presencia de aguas blandas, etc.) que no son tratados en el presente artículo.
2.1.- Cloruros
La presencia de cloruros es la causa que genera de forma más habitual un mayor número de anomalías en términos de durabilidad en las estructuras de hormigón. Las armaduras de acero, protegidas naturalmente por la alcalinidad del hormigón circundante, ven comprometidas sus condiciones de durabilidad en ambientes marinos, o bien debido a la acción de las sales fundentes, debido a que los cloruros llegan a penetrar en el hormigón y alcanzan la posición de éstas.
La presencia de oxígeno, junto a cantidades suficientes de iones de cloruro disueltos en el agua presente en los poros del hormigón, produce la corrosión del acero incluso en condiciones altamente alcalinas. Esto genera picaduras de corrosión en puntos localizados de las armaduras en las que la capa pasiva original es ligeramente más débil, debido principalmente a la formación de sales de ácido clorhídrico.
Bajo ciertas condiciones, estas picaduras pueden crecer rápidamente y causar una importante pérdida de la sección transversal del acero, con las consiguientes implicaciones estructurales.
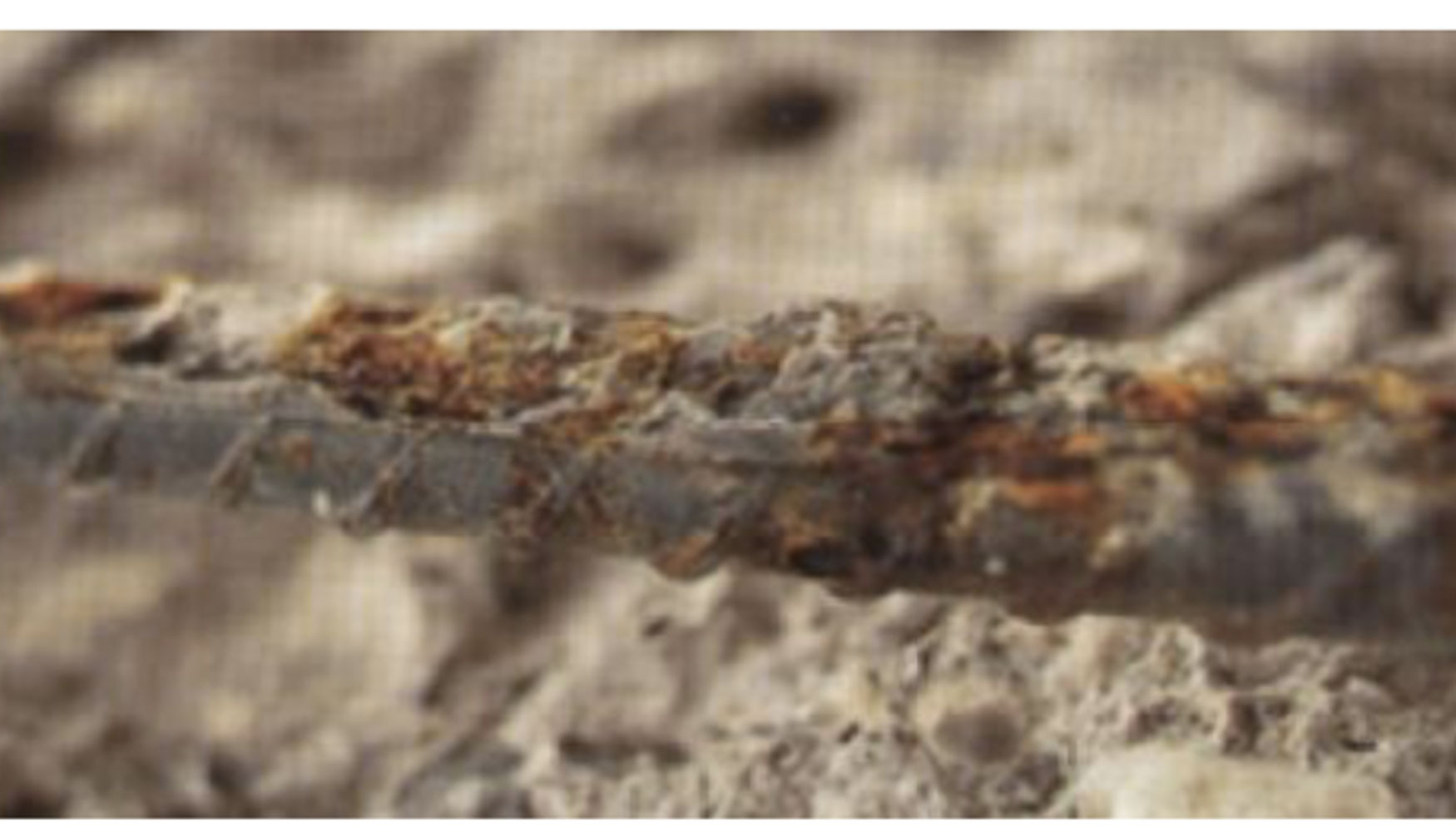
2.2.- Carbonatación
La segunda causa más común que provoca la aparición de daños en el hormigón es el fenómeno natural de la carbonatación. Por lo general, el hormigón suele encontrarse en contacto con el aire del ambiente y por lo tanto, dependiendo de la ubicación de la estructura, se encuentra expuesto a diferentes concentraciones de dióxido de carbono. En el caso del hormigón producido con cemento Pórtland ordinario, la portlandita, presente en cantidades relativamente altas (40 a 50%), reaciona con el dióxido de carbono del aire del ambiente, creando carbonato cálcico según se observa en la siguiente ecuación: Ca(OH)2 + CO2 + H2O → CaCO3 + 2(H2O).
Una de las consecuencias de la carbonatación es la reducción gradual del nivel del pH del hormigón, desde 13, valor original, hasta por debajo de valores en torno a 8-9, los cuales se alcanzan una vez una vez completada la reacción. El avance del frente de carbonatación, el cual indica la profundidad de penetración del dióxido de carbono y la consiguiente reducción de la alcalinidad que pasiva del acero, llega finalmente a las barras. En consecuencia, el acero pierde la protección original que le confería la alcalinidad del hormigón, dejándole desprotegido, por lo que la humedad y el oxígeno presentes en los poros del hormigón acaban generando la corrosión de las armaduras, cuyo carácter expansivo genera la fisuración del hormigón de recubrimiento, dejando en ocasiones las armaduras vistas.
![Figura 2: Comportamiento típico de la carbonatación en estructuras de hormigón [1] Avance del frente de carbonatación en función del tiempo... Figura 2: Comportamiento típico de la carbonatación en estructuras de hormigón [1] Avance del frente de carbonatación en función del tiempo...](https://img.interempresas.net/fotos/2198135.jpeg)
2.3.- Ataque por sulfatos
Los sulfatos están siempre presentes en el cemento, por lo que la formación de etringita (lo cual se produce a edades muy tempranas) se produce normalmente en los hormigones y morteros de cemento. El proceso anterior es debido al yeso molido (principalmente sulfato de calcio) el cual se añade en planta como regulador del tiempo de fraguado, reaccionando con los aluminatos de calcio del cemento durante las primeras horas después de la adición de agua como parte del proceso de producción de hormigón.
Los agentes expansivos a base de sulfatos también se utilizan a veces para compensar la pérdida de volumen inicial de hormigones y morteros.
La aparición de daños en el hormigón debido a los sulfatos tienen su origen en la reacción de éstos, bien cuando se produce el acceso de nuevos sulfatos procedentes del medio que rodea a la estructura, o bien cuando se liberan de forma tardía, por ejemplo, por el empleo de árido contaminado con yeso. Este fenómeno suele ser llamado Formación de Ettringita Retardada, y se produce de forma heterogénea y mucho más tarde (tras meses o incluso años). Estas reacciones expansivas también pueden producir fisuración, desconchones, etc, así como una pérdida de capacidad estructural, ya que se producen dentro de la matriz del hormigón endurecido. En la figura 3 se muestra un ejemplo de ataque por la presencia de sulfatos.
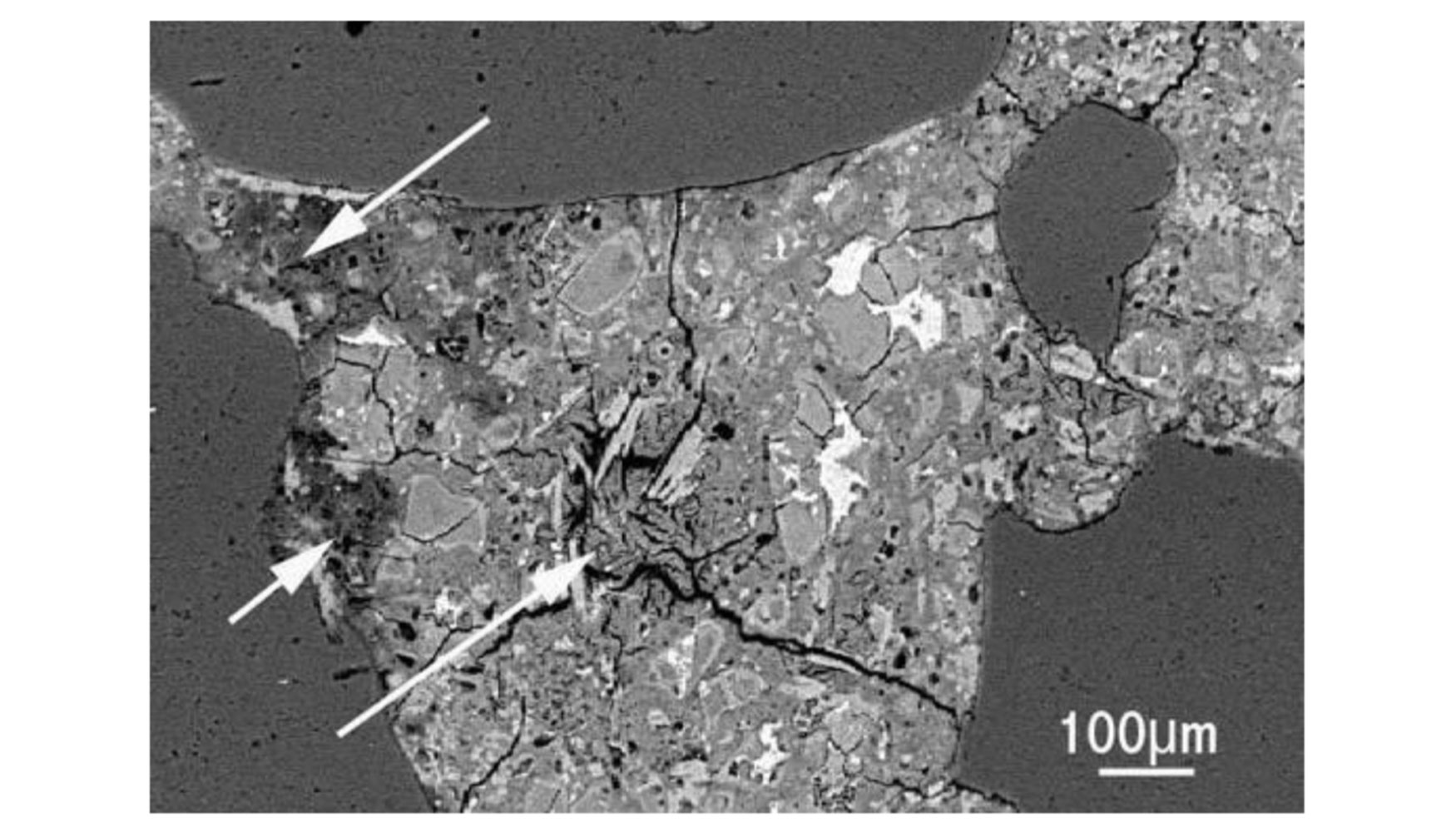
2.4.- Reacción árido - álcali
La reacción árido-álcali (también conocida como reacción de los agregados alcalinos o 'cáncer del hormigón') es la reacción que se produce cuando se posicionan agregados reactivos silíceos, con material alcalino, en presencia de humedad.
La reacción árido-álcali fue identificada por primera vez como causa de deterioro del hormigón hace más de 80 años por Stanton [3], en la década de 1930. Desde el descubrimiento inicial, se han reportado numerosos casos en todo el mundo.
Es ampliamente aceptado que los tres componentes esenciales y necesarios para que se produzca este tipo de daño en las estructuras de hormigón son los siguientes:
- Sílice reactiva proveniente de los áridos incorporados en el hormigón.
- La presencia de álcalis, principalmente proveniente del cemento Portland, aunque también puede provenir de otros materiales constituyentes.
- Suficiente humedad.
En la primera etapa, el álcali proviene principalmente del cemento, que migra dentro de la trama de poros del hormigón y entra en contacto con los agregados reactivos, dando como resultado un gel de silicato alcalino. Posteriormente, en una segunda etapa, este gel de silicato reacciona aún más con la cal presente en la matriz del hormigón, dando lugar a un segundo gel, bastante más complejo, y con mayor capacidad de absorber humedad, lo que genera un incremento de volumen. El resultado es la aparición de unos esfuerzos que generan la expansión de la zona de hormigón afectada, dando lugar a una fisuración característica en la estructura de hormigón. A continuación, se muestra un mapa de Estados Unidos, en el que se localizan las estructuras diagnosticadas con este aspecto, a fecha de emisión del presente documento, obtenido de la Administración General de Carreteras.
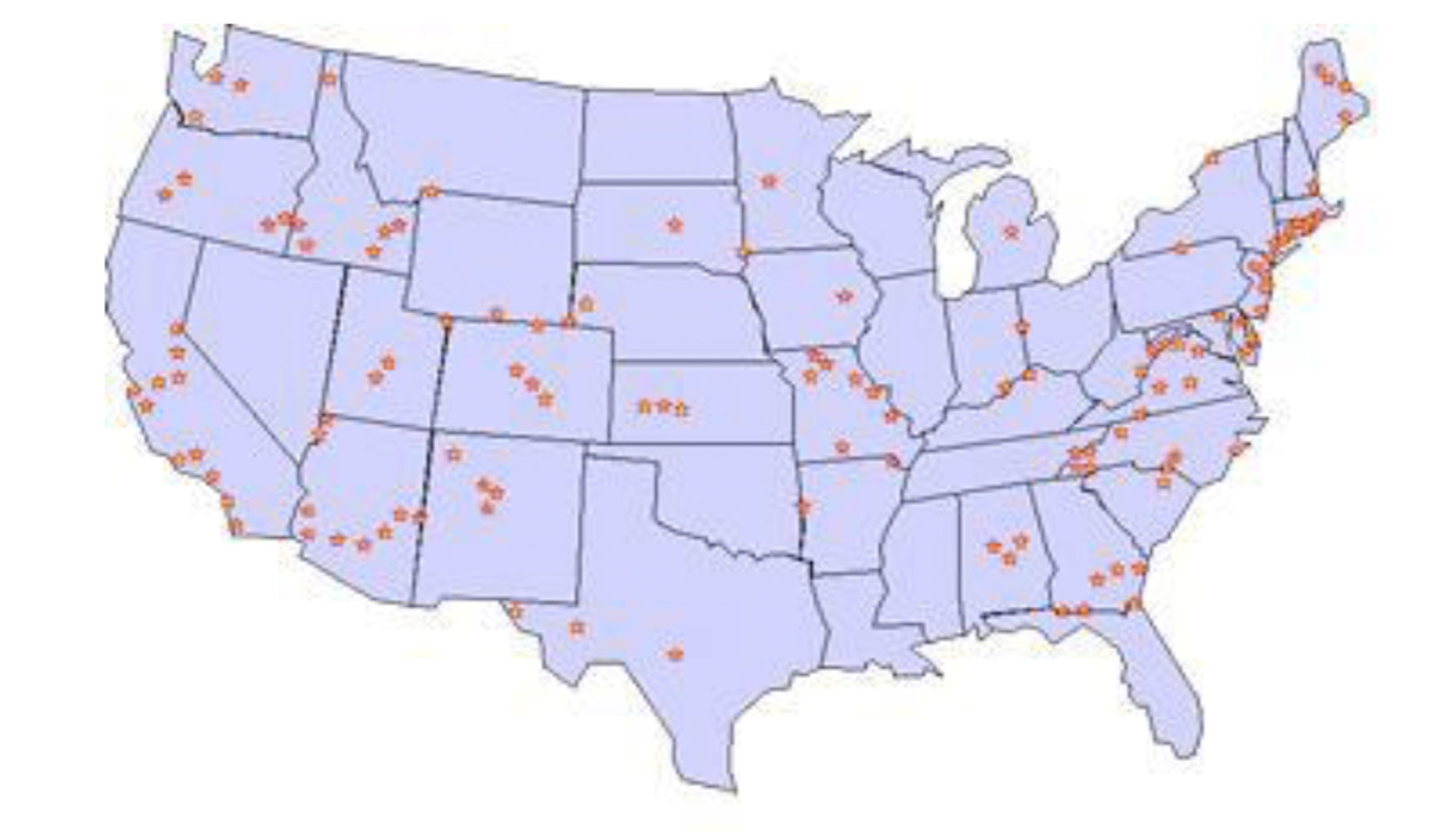
2.5.- Hielo – Deshielo
Este fenómeno tiene lugar principalmente en países o zonas sujetas a condiciones invernales frías, donde además, los daños se acentúan muy a menudo por la presencia de sales de deshielo, como las que se utilizan en los tableros de los puentes, para reducir la formación de hielo en las carreteras y evitar así accidentes de vehículos.
Los principales síntomas son la formación de escamas en la superficie del hormigón y el incremento de volumen diferencial aparente de parte o del total de la estructura, junto con la aparición de fisuras. En casos extremos, la estructura puede quedar completamente dañada, como se muestra en la figura 5.
Como ejemplo, un estudio realizado en el Reino Unido en 1997 mostró que el 10% de todas las estructuras de hormigón armado se han visto afectadas por el ataque hielo-deshielo.
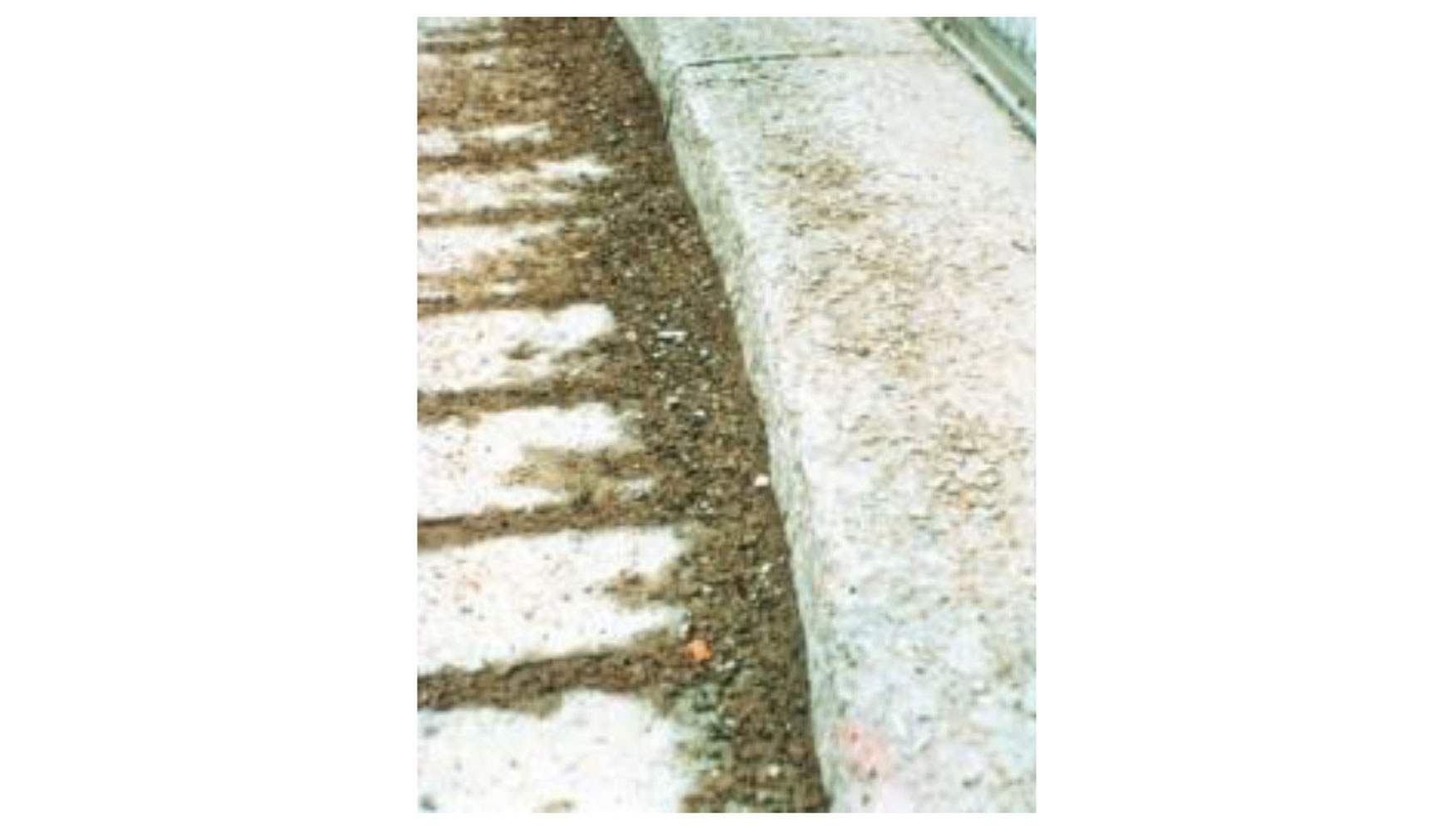
3.- Requerimientos habituales de los revestimientos de protección
Antes de considerar el uso del revestimiento protector, se debe realizar un análisis que permita determinar las causas existentes (y potenciales) a fin de asegurar que las funciones de protección del revestimiento puedan abordar adecuadamente esos requerimientos. Una vez hecho lo anterior, se podrá seleccionar el sistema de protección superficial. Como guía, pueden considerarse las recomendaciones incorporadas en la norma europea EN 1504-9, las cuales se describen a continuación:
- Investigación y análisis
- Selección de los principios de protección basados en los resultados de los análisis
Como ejemplo, en la EN 1504-9, para la protección frente al ingreso (P1), el control de la humedad (P2) y el incremento de la resistividad (P8), se pueden considerar los siguientes sistemas de protección.
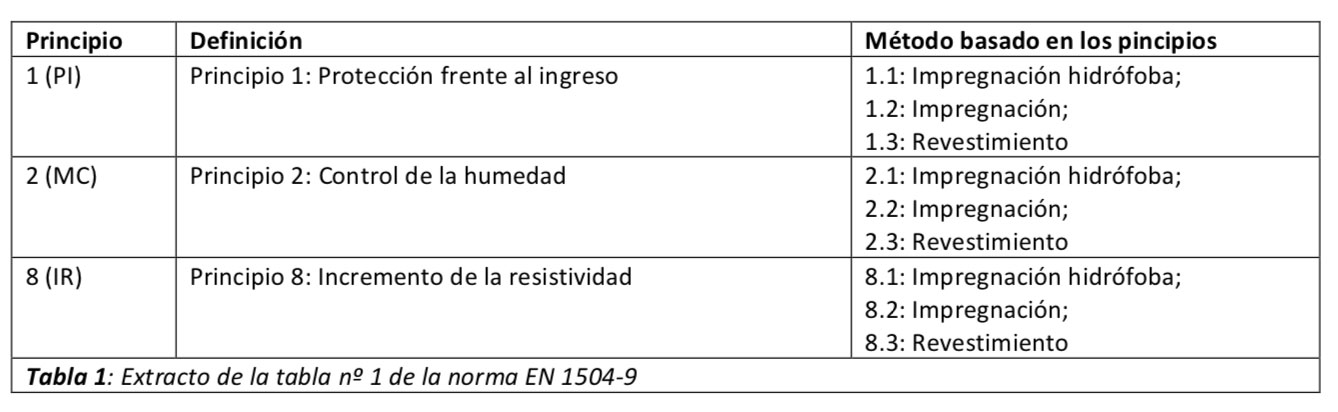
Según el nivel y el tipo de protección requerido, el material de protección presentará las siguientes características:
- Resistencia frente a los ciclos hielo-deshielo (revestimiento e impregnación hidrófoba)
- Resistencia a las sales fundentes (revestimientos e impregnación hidrófoba)
- Resistencia a la intemperie
- Prevención frente a la entrada de agua
- Transpirabilidad
- Impermeabilidad al dióxido de carbono
- Compatibilidad con el sistema de reparación
- En función de la necesidad, capacidad de puentear fisuras
- Capacidad de penetración
- Resistencia a los álcalis
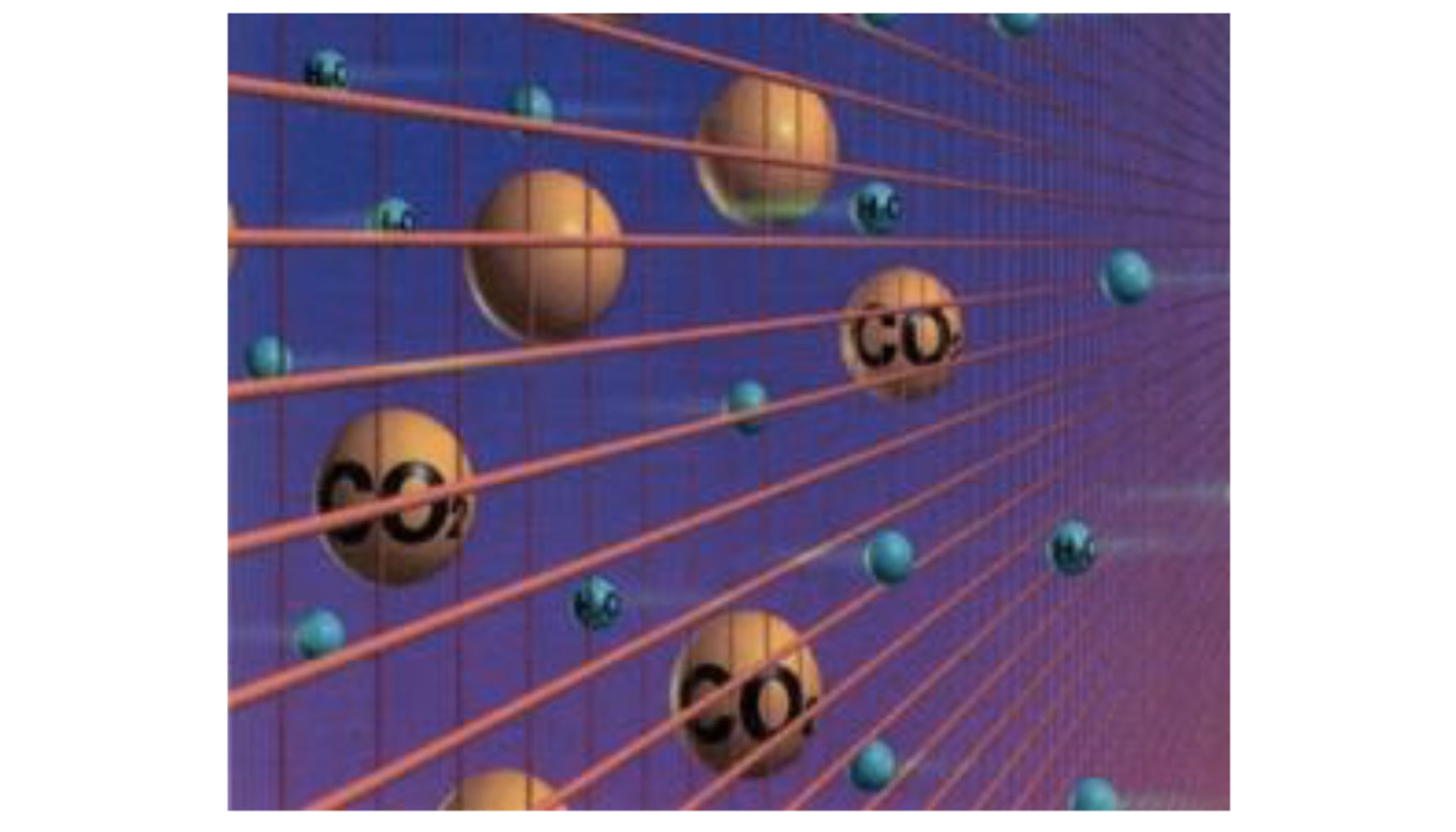
Fig 6: Las moléculas de CO2 son bloqueadas por la capa protectora mientras que las moléculas de menor tamaño, las de vapor de agua, pueden migrar libremente dejando respirar al soporte.
Análisis aparte merece la protección frente a la carbonatación. La norma EN 1504-2 exige para tal fin que los revestimientos proporcionen una protección de un espesor de aire equivalente (SD) de al menos 50 metros. La lógica de este valor se explica gráficamente utilizando la Fig. 7[1].
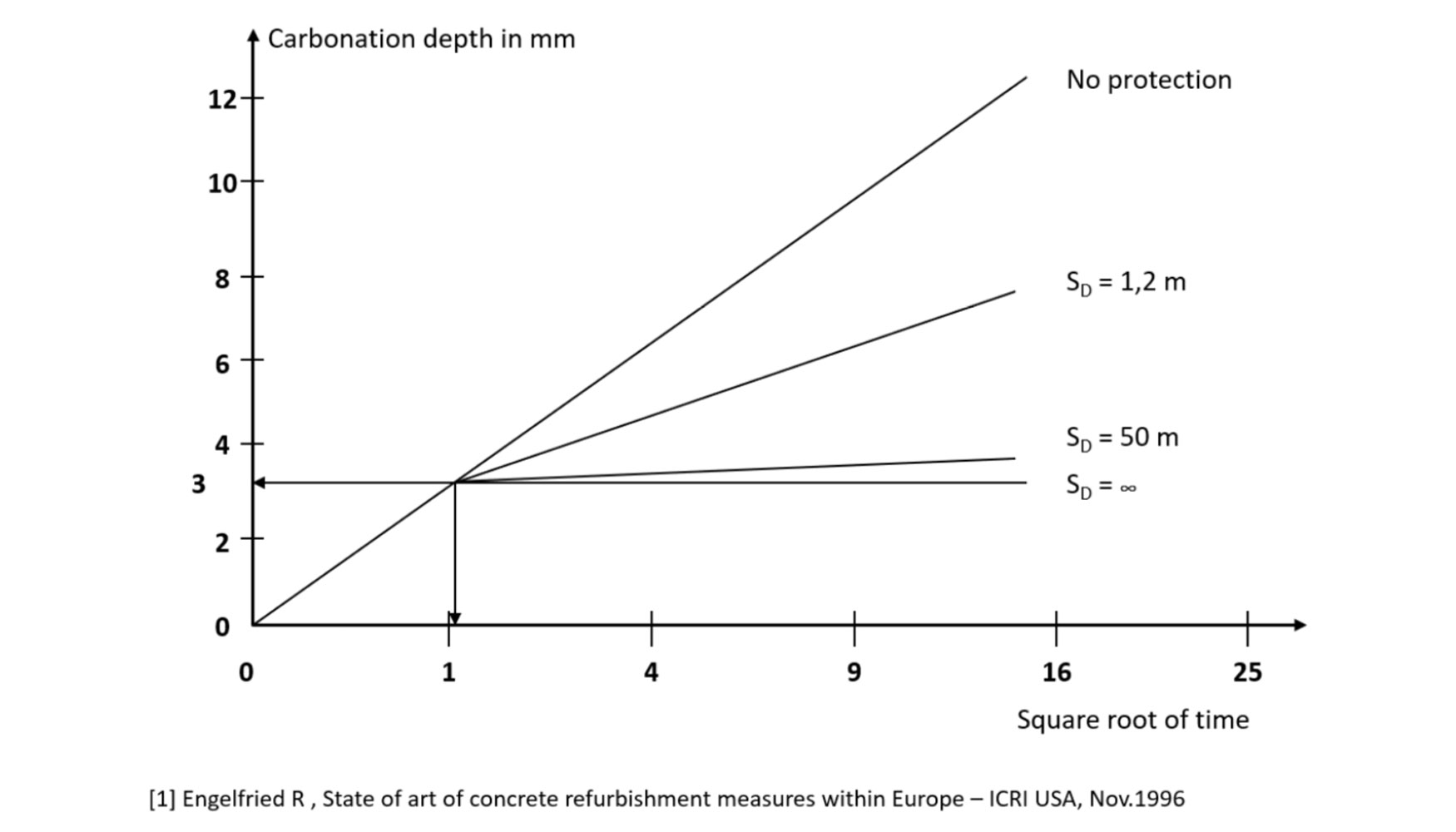
Observando la progresión típica de la carbonatación, un hormigón de 25 MPa presentaría una carbonatación de 3 mm de profundidad tras un año. En el caso de no llevar a cabo ninguna acción preventiva (SD = 0 m), es esperable una carbonatación lineal en función del tiempo. En ese caso, el coeficiente de resistencia a la carbonatación de este hormigón corresponde a: µCO2 = 200.
En consecuencia, dicho hormigón carbonatado tiene una resistencia a la difusión de SD = 3 mm x 200 = 600 mm = 0,6 m. Si, por ejemplo, se aplicara una capa uniforme de un revestimiento protector sobre la superficie del hormigón al año de haber ejecutado la estructura, si se quisiera duplicar hasta SD = 1,2 m, entonces la velocidad de carbonatación se reduciría a la mitad.
Si en su lugar se aplicara un revestimiento que alcanzara el umbral EN 1504-2 (SD = 50 m), la profundidad de carbonatación se reduciría a un nivel muy cercano al que se obtendría si se lograse una detención completa del proceso de carbonatación (SD = ∞). Esto demuestra claramente que un revestimiento puede considerarse como una buena barrera de carbonatación si su espesor de nivel de aire equivalente de difusión es igual a SD = 50 m [4-5].
4.- Control de calidad
Para asegurar una buena calidad de la aplicación, y por lo tanto para obtener la durabilidad deseada, se deberá llevar a cabo una planificación, así como un control de calidad para cada una de las etapas del proceso de aplicación. En el cuadro 2 se presenta un ejemplo de dicho plan, creado a partir de las recomendaciones que figuran en la norma EN 1504-10.
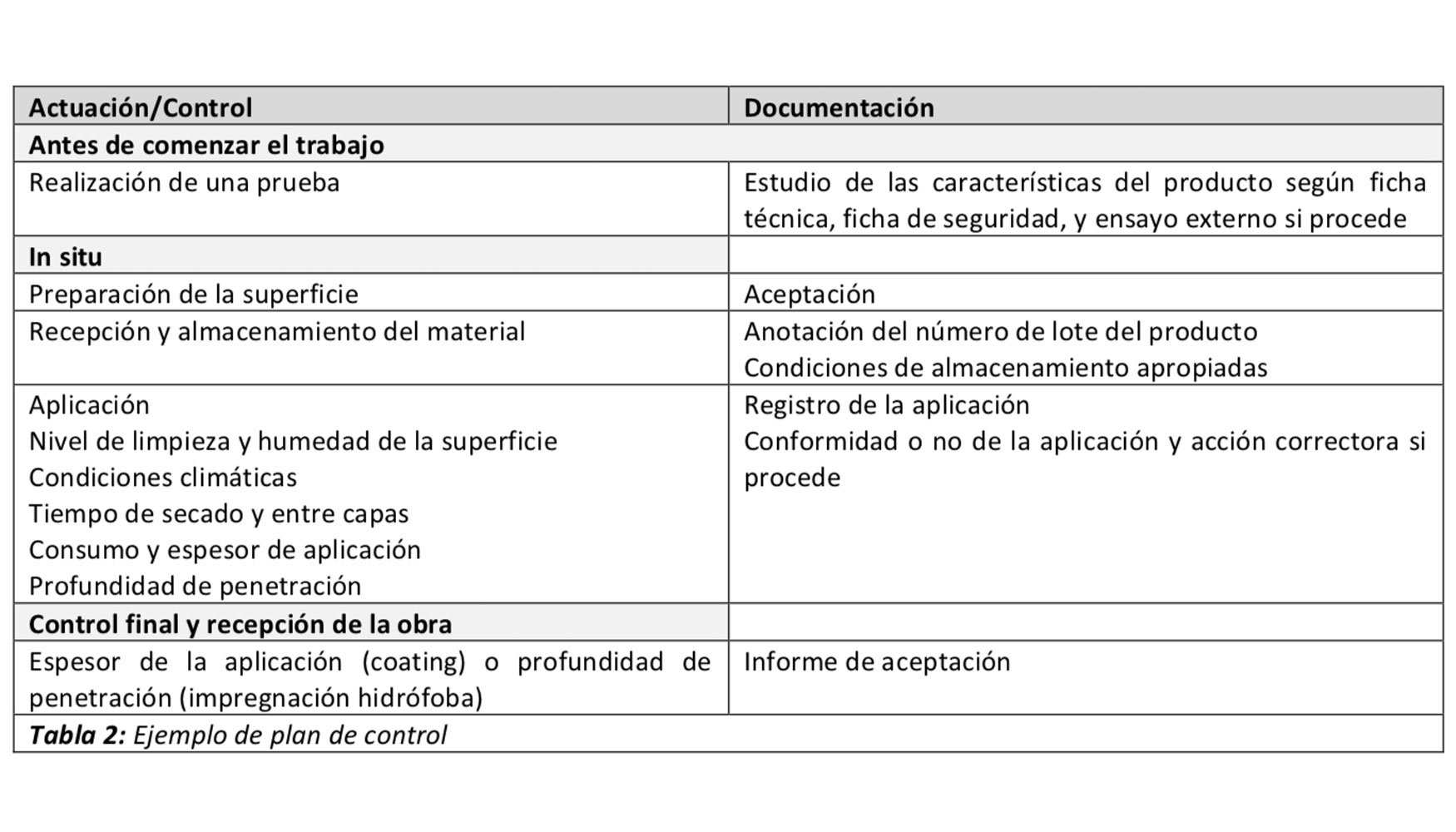
5.- Casos de estudio
5.1.- Puente sobre la autopista A2 en Lämershagen, Alemania [6]
El puente de Lämershagen sobre la autopista A2, cerca de Bielefeld en Alemania fue construido antes de la Segunda Guerra Mundial, en forma de puente arco de hormigón armado. Fue destruido en gran parte en 1945 y reconstruido después de la guerra. Con el paso del tiempo, se produjeron desprendimiento de hormigón con origen en la corrosión de las armaduras. Esto obligó al Departamento de Autopistas a llevar a cabo reparaciones generalizadas en 1981, principalmente para evitar la caída de cascotes de hormigón causando un peligro para el tráfico de la autopista.
La preparación del soporte se llevó a cabo mediante un chorreado. El hormigón con daños fue reparado mediante morteros de reparación. Todas las superficies fueron niveladas con un mortero de alisado para homogeneizarlas, y finalmente, se aplicó una película de protección en base disolvente sobre la superficie de hormigón.
Los trabajos de reparación y protección tuvieron lugar durante el invierno de octubre de 1981 a enero de 1982, es decir, una fase normalmente no apropiada para realizar este tipo de trabajos si tenemos en cuenta el clima característico de esas fechas (alta humedad y/o muy baja temperatura).
15 años más tarde, se realizó un estudio independiente para evaluar las condiciones del puente. Aunque visualmente el aspecto era bueno, se observaron defectos superficiales que indicaban que la protección del hormigón no se mantenía en las condiciones originales en algunas áreas localizadas.
Los técnicos que realizaron el estudio en 1997 llegaron a la conclusión de que, en lo que respecta al puente de la autopista de Lämershagen, el sistema de reparación y protección que se utilizó era adecuado en su diseño y ha demostrado su eficacia a largo plazo. Sin embargo, el estado de las reparaciones era insatisfactorio después de 15 años.
Las principales razones fueron, principalmente, el periodo de aplicación, entre octubre de 1981 y enero de 1982, en el que no se logró un correcto endurecimiento/curado o secado de los materiales de reparación debido a las bajas temperaturas y la combinación de alta humedad. Estas condiciones deben ser evitadas en este tipo de trabajos de reparación y protección.
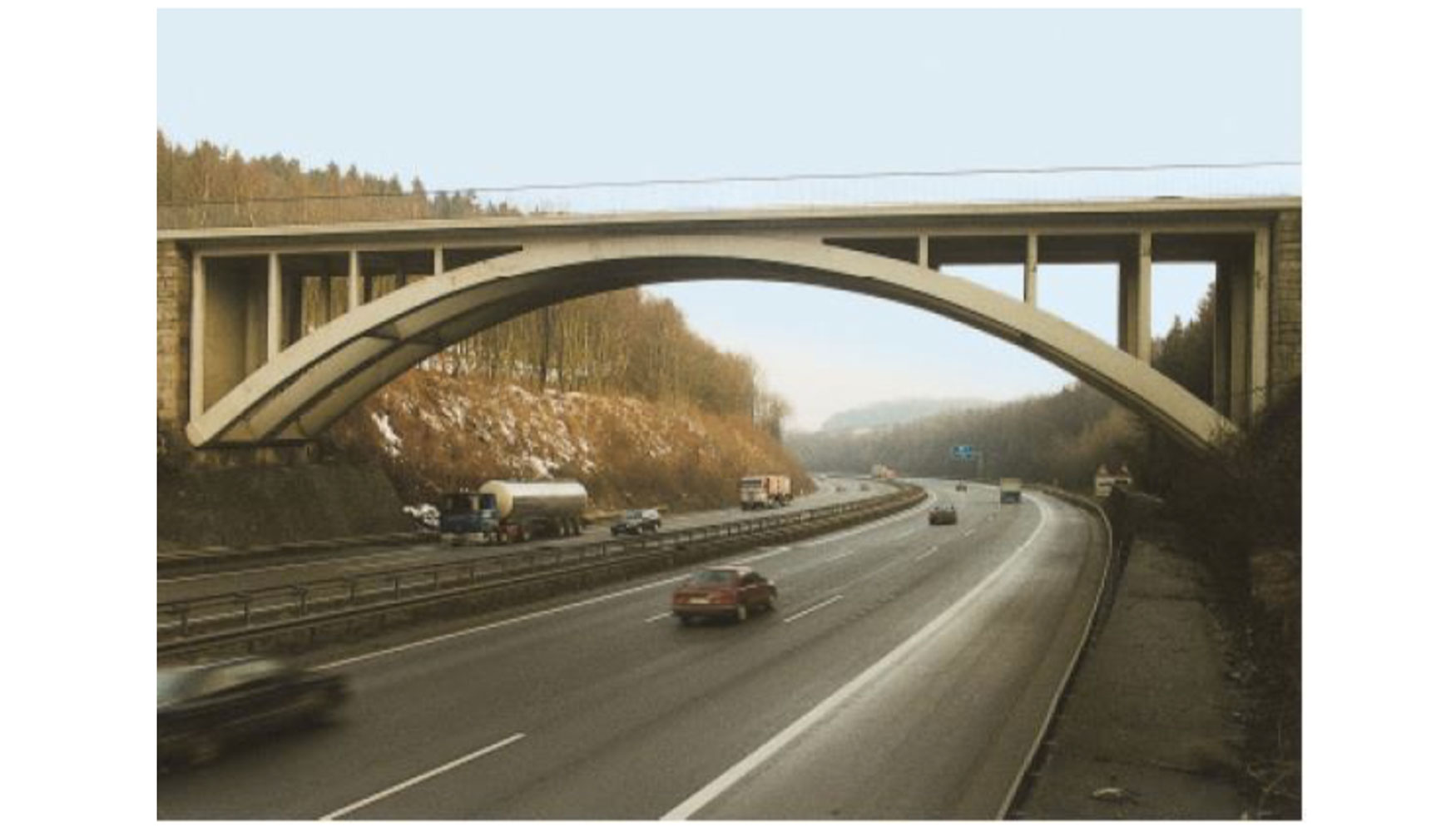
5.2.- Puentes de hormigón en Jutland, Dinamarca [7]
En dos grandes autopistas, la M60 y la M61, las autoridades viales danesas seleccionaron cinco puentes y caracterizaron sus daños para su estudio, reparación y protección. El Grupo de Trabajo reunió todos los datos de la construcción original relativos a los puentes. El contenido de humedad del hormigón se midió in situ. Se determinó que las fisuras de los puentes tenían su origen en una combinación de la fisuración inicial por contracción, junto con fisuras posteriores debido a la reacción árido - álcali. Se determinó previamente mediante análisis realizados por un laboratorio externo que el origen se encontraba en el empleo de áridos reactivos (véase la figura 9).
Sobre la base de esta información y los análisis realizados, el Grupo de Trabajo seleccionó un revestimiento de alto rendimiento para la protección general de los puentes, con el objetivo de que cumpliera específicamente el requisito de frenar el acceso a la humedad exterior. Se eligió este material por sus excelentes propiedades de resistencia al agua, flexibilidad (puenteo de fisuras) y su baja resistencia a la difusión del vapor de agua (alta transpirabilidad).
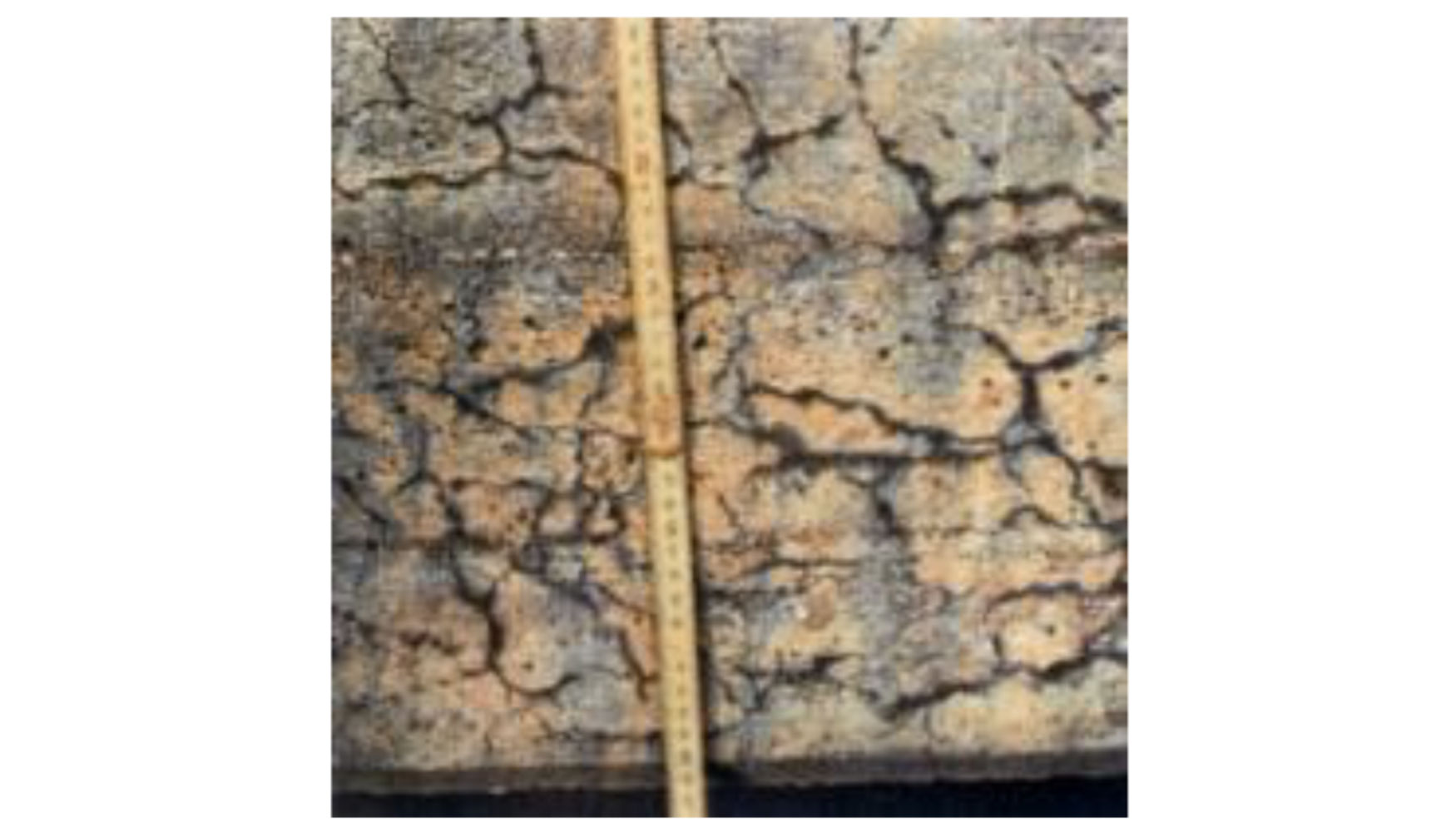
Figura 9: Imagen de la fisuración provocada por la reacción árido - álcali.
En tres de los cinco puentes seleccionados se repararon parapetos y vigas de borde, para lo que se emplearon morteros de reparación. Posteriormente, se protegieron con un revestimiento elastomérico en 1983.
Después de cinco años, la protección de la superficie seguía intacta - brillante, con una efectiva propiedad de puenteo de fisuras y una buena adhesión al soporte.
El hormigón protegido no mostró cambios significativos en el nivel de humedad. Este hecho pone de manifiesto la importancia de este tipo de sistemas, ya que, las estructuras que no habían sido protegidas presentaban unos niveles de humedad y de daños visibles que había incrementado respecto a las inspecciones iniciales. Tanto la inspección visual como la medición de la humedad indicaban claramente que, en los tres puentes protegidos, el progreso del deterioro se había detenido o reducido muy significativamente.
En 1994 las autoridades viales hicieron una nueva inspección de seguimiento de su investigación original de 1988 (véase la figura 10). La conclusión fue que el sistema de reparación y protección seleccionado había mantenido todas las propiedades deseadas después de más de 10 años de servicio y citan “probablemente funcionará durante mucho más tiempo”.
Basándose en estos informes y en la evaluación de las pruebas de laboratorio detalladas de los productos, en lo que respecta a la protección de las estructuras frente a la penetración de cloruros, sales de deshielo, etc, las autoridades viales emplean rutinariamente este sistema para la protección de sus puentes de carretera.
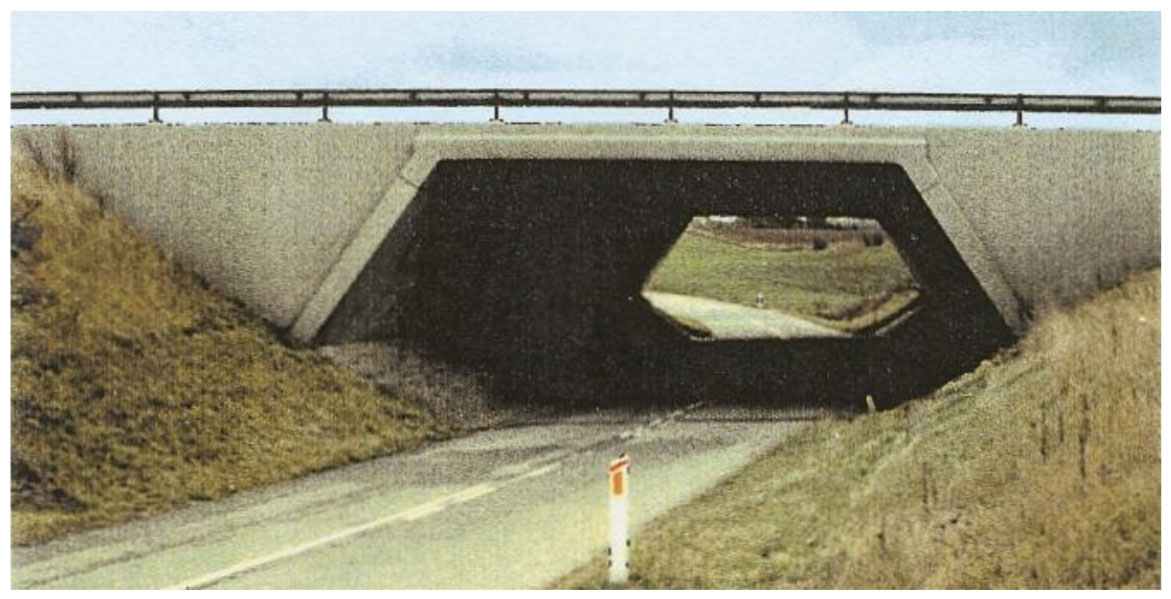
5.3.- Torre de refrigeración en Turów, Polonia [8]
La central eléctrica de Turów está situada cerca de la frontera entre Alemania y la República Checa. En los años 90, todas las torres de refrigeración de tiro natural fueron renovadas usando sistemas más novedosos.
En la cara interior se aplicó un sistema en base resina epoxi, mientras que en la cara exterior se utilizó una combinación de impregnación hidrofóbica y revestimiento de metacrilato.
En 2008, el Instituto de Investigación de Varsovia realizó un análisis exhaustivo de los revestimientos de dos torres de refrigeración. La conclusión de la investigación fue que “las propiedades de rendimiento técnico de los sistemas de revestimiento de epoxi y siloxano/metacrilato, sometidos a las agresivas condiciones de exposición de las torres de refrigeración de la central eléctrica, no se han deteriorado ni siquiera después de 16 años de servicio. Todos los sistemas de revestimiento probados siguen proporcionando protección contra el agua y la penetración de la condensación, la penetración del vapor de agua (o permitir la difusión según corresponda). También presentan una elevada resistencia a la difusión del dióxido de carbono. Su rendimiento como barrera protectora sigue cumpliendo o superando los requisitos de EN 1504-2.”
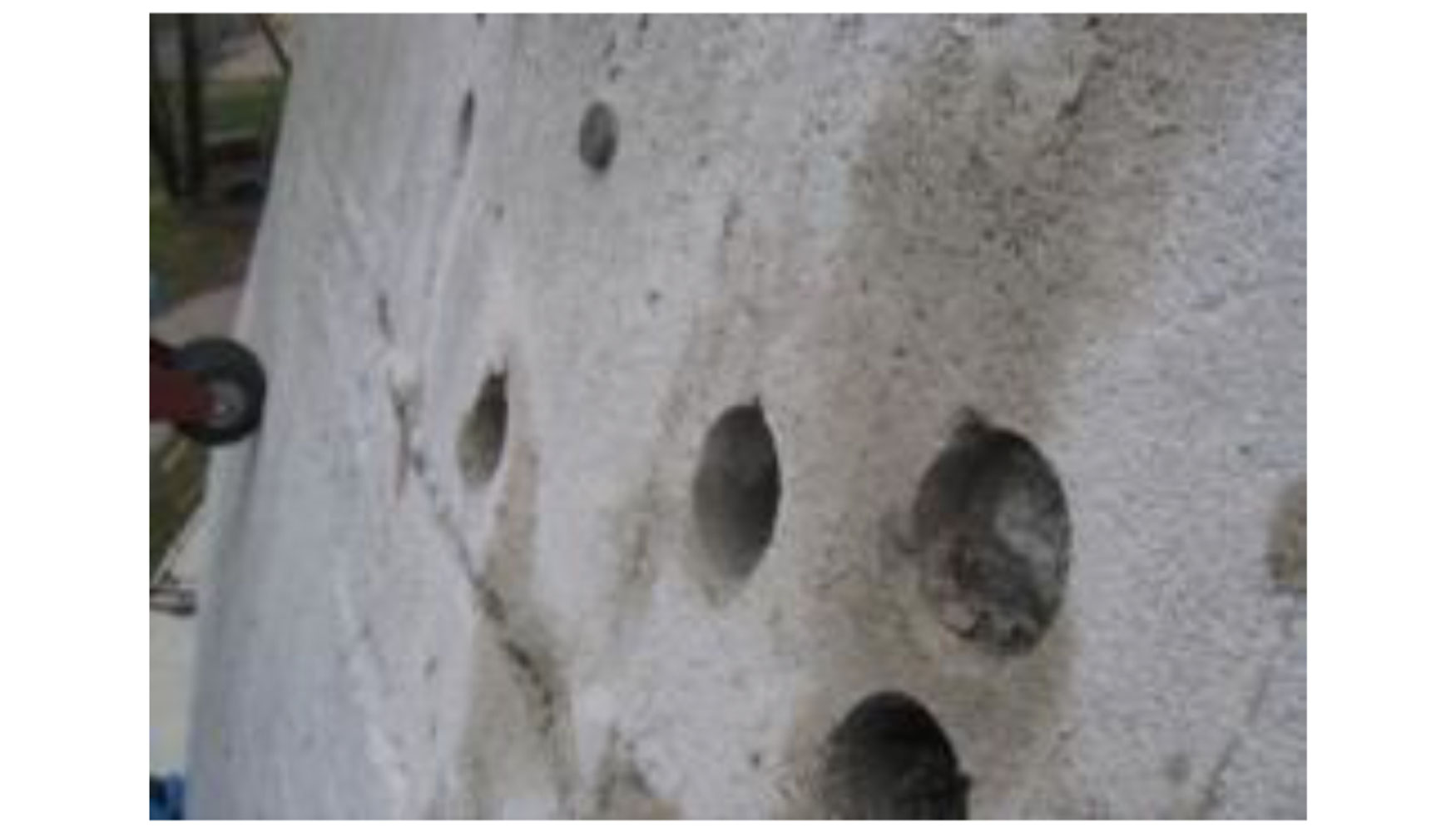
A continuación, se muestran los resultados de los análisis antes descritos:
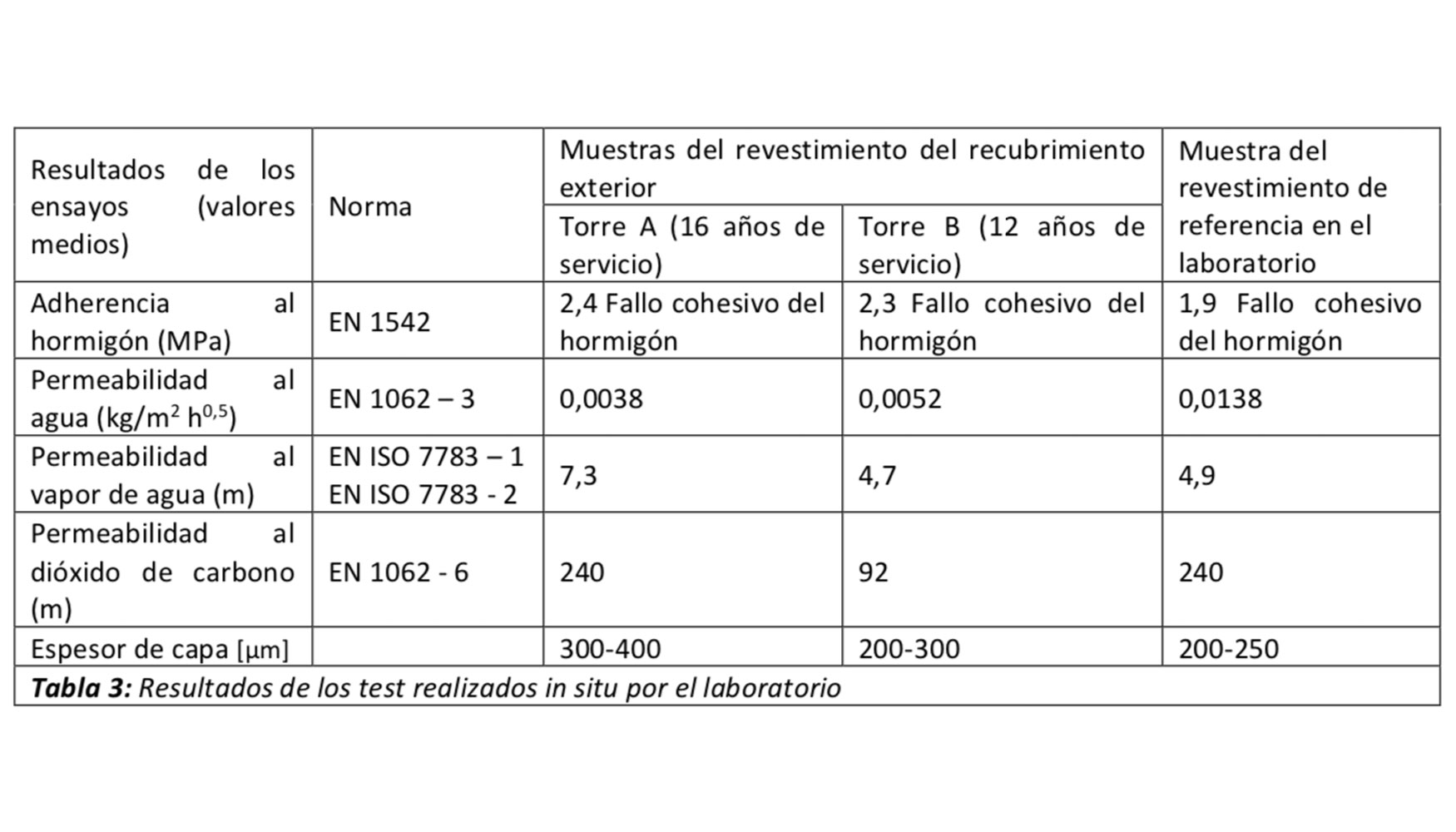
6.- Conclusiones
El presente documento muestra el efecto de los diferentes elementos perjudiciales a los que se somete un puente de hormigón durante su vida útil.
Con el fin de mejorar la durabilidad de las estructuras de ingeniería civil, los revestimientos protectores bien diseñados pueden ser empleados con total garantía. Requisitos como la permeabilidad al agua, la transpiración del vapor de agua, la resistencia a la difusión del dióxido de carbono, etc., pueden lograrse con los revestimientos protectores apropiados.
Cuando se utilizan estos revestimientos bien diseñados, pueden mejorar la durabilidad de las estructuras y permanecer en uso en largos periodos de tiempo, como lo demuestran los diferentes estudios de casos reales presentados.
7.- Bibliografía
- [1] Dr.-Ing. Robert Engelfried, University of Dortmund, Germany, Construction Engineering and Building Physic, State-of-art of Concrete Refurbishment Measures within Europe, especially in Germany, ICRI, International Concrete Repair Institute, Annual Meeting New Orleans USA, October 31 to November 01 1996
- [2] http://www.understanding-cement.com/sulfate.html
- [3] http://www.fhwa.dot.gov/pavement/concrete/asr/history.cfm
- [4] Klopfer, H.: Bauphysikalische Aspekte der Betonsanierung Bautenschutz und Bausanierung Heft 4/1980, Seiten 128 bis 131
- [5] Engelfried, R.: Diffusionswiderstandszahlen fur Kohlendioxid und Wasser und deren praktische Anwendung, farbe + lack Nr. 7/1983, Seiten 513 bis 518
- [6] Lamershagen Bridge Sika article; Survey carried out by Prof. Engelfried
- [7] Jutland Bridge Sika article; Survey carried out by Danish Road Authorities
- [8] T. Mozaryn, ITB Research Institute, Warsaw, Poland, The Service Life of Coatings System Applied on Cooling
- Towers – A Laboratory Study and In-Situ Investigations, NUCPERF 2009, Cadarache, France, March 30 - April 2, 2009
Notas legales
Las informaciones contenidas en este documento están dadas de buena fe, basadas en el conocimiento actual y la experiencia de Sika de los productos cuando son correctamente almacenados, manejados y aplicados, en situaciones normales, dentro de su vida útil, de acuerdo con las recomendaciones de Sika. La información se aplica únicamente a la (s) aplicación (es) y al (los) producto (s) a los que se hace expresamente referencia. En caso de cambios en los parámetros de la aplicación, como por ejemplo cambios en los soportes, etc., o en caso de una aplicación diferente, consulte el Servicio Técnico de Sika previamente a la utilización de los productos Sika. La información aquí contenida no exonera al usuario de ensayar los productos para la aplicación y la finalidad deseadas. Los pedidos son aceptados en conformidad con los términos de nuestras vigentes Condiciones Generales de Venta y Suministro. Los usuarios deben conocer y utilizar la versión última y actualizada de las Hojas de Datos de Productos, copias de las cuales se mandarán a quién las solicite.