Respuesta microestructural de Rene 80 a los parámetros de laser cladding
S. Moralejo (sgarcia@ideko.es), L. Huarte-Mendicoa y X. Penaranda, del Centro tecnológico IK4-Ideko; y A. Lamikizb, del departamento de Ingeniería Mecánica de la Universidad del País Vasco ETSI, ETSII-UPV
14/04/2020El análisis metalográfico muestra una buena unión microestructural entre el sustrato y el material aportado. La evaluación de las microdurezas presenta valores constantes en muestras monocristalinas, alcanzando valores similares a los obtenidos con tratamientos térmicos extras para homogeneizarlos. Se observa una tendencia similar en la monitorización del eje menor de la piscina fundida, con una ligera desviación de un valor fijo para las muestras SX y una mayor desviación en aquellas con granos no orientados. Se ha verificado la idoneidad de la ventana de trabajo para obtener microestructura monocristalina mediante la reparación de la punta de un álabe con anchura variable.
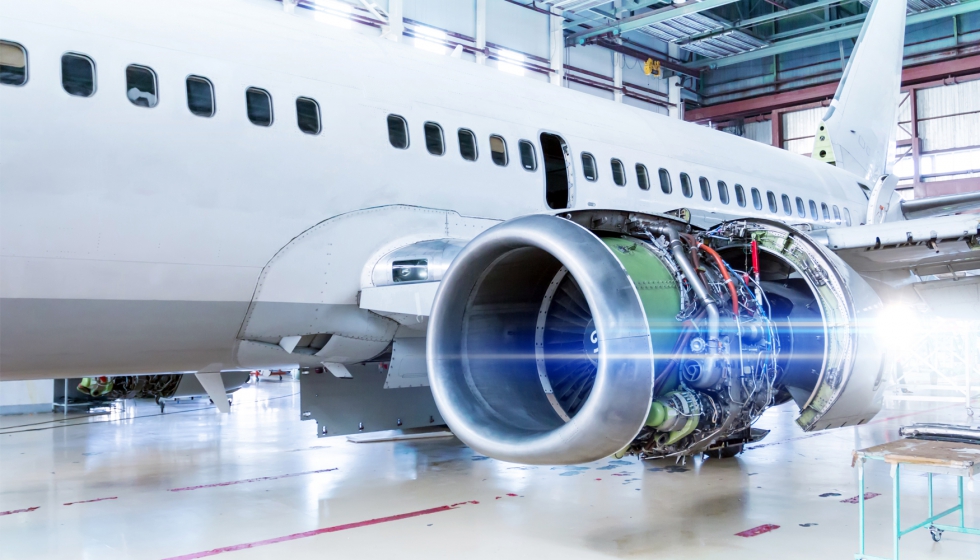
1. Introducción
Las turbinas de gas modernas de los motores de avión y los sistemas de generación de energía son extremadamente fiables. Sin embargo, durante el funcionamiento, las tensiones térmicas y mecánicas críticas y las condiciones corrosivas en las que trabajan generan defectos, como grietas en la base o erosión de la punta de sus álabes, que son inevitables en condiciones de alta temperatura, lo que limita la vida útil de estos componentes de alto valor. Se ha detectado un gran interés económico en su reparación, apareciendo nuevos métodos de reparación de estas áreas dañadas que prolongan el ciclo de vida de estos componentes en lugar de desecharlos y reemplazarlos. En el futuro se espera que los nuevos avances provengan de tecnologías de fabricación alternativas, que ofrezcan mejor calidad, nuevas propiedades y menores costos. Konter y Thurmann [1] ofrecieron una descripción general de la selección de los mejores materiales para la fabricación de turbinas de gas, con tendencias en materiales de alta temperatura y recubrimientos protectores. Una forma de aumentar la eficiencia de estos componentes es aumentar su temperatura de trabajo utilizando aleaciones monocristalinas que no contienen fronteras de grano, de modo que es también necesario que la técnica de reparación a su vez genere estructura monocristalina, asegurando la conservación de la naturaleza SX de la aleación. Las superaleaciones con base de níquel monocristalinas se han utilizado en turbinas de gas de alta temperatura para la fabricación de álabes y vanos debido a sus excelentes propiedades mecánicas a temperaturas elevadas, lo que produce una mejora notable de la eficiencia de las turbinas de gas. Sin embargo, estas superaleaciones contienen una alta concentración de Al + Ti, presentando una capacidad de soldadura limitada debido a su baja resistencia al agrietamiento de la zona afectada por el calor (HAZ) durante la soldadura y durante el posterior tratamiento térmico de la soldadura [2].
En ese sentido, se han llevado a cabo varios trabajos para encontrar el mejor proceso de fabricación de SX. Henderson et al. [3] utiliza arco de tungsteno de gas (GTA), soldadura por haz de electrones (EB), deposición de polvo por láser y soldadura por fricción. Encontraron que la composición, el tamaño del grano, el tratamiento previo y posterior a la soldadura, así como el proceso en sí, eran factores que afectaban la propensión a los defectos. Para el refundido de la superficie por láser, tanto los modelos matemáticos como los resultados experimentales indicaron que los parámetros geométricos de la piscina fundida tenían una gran influencia en la velocidad de crecimiento de la dendrita y el patrón de crecimiento [4]. La formación de granos aislados (SG) y la pérdida de epitaxialidad en el sustrato se atribuyeron al aumento de la tendencia de la formación de granos aislados resultantes de la segregación de la composición en la región interdendrítica del sustrato [5]. Estos hallazgos demostraron que un tratamiento para los sustratos antes del procesamiento con láser puede evitar efectivamente la formación de SG y la pérdida de epitaxialidad. Las pruebas con scanning laser epitaxy (SLE) realizadas para establecer la influencia de los parámetros de proceso en la evolución microestructural de CMSX-4 [6] encontraron un rango óptimo en los cuales el material depositado no mostró agrietamiento.
En laser cladding se realizaron mapas de proceso para CMSX-4 [7] para relacionar la microestructura de solidificación esperada y las morfologías de crecimiento con las condiciones de proceso. Los resultados indicaron que solo se producían monoscristales con una fusión suficiente para el crecimiento epitaxial. Así se descubrió que el laser cladding tenía ventajas potenciales sobre los procesos convencionales, ya que expone la pieza a mucho menos calor que las técnicas de soldadura convencionales, y la zona afectada por el calor es mucho más pequeña, lo que reduce significativamente la degradación mecánica y estructural de la pieza mientras repara un área específica. Gracias al uso focalizado de calor y al aporte de material controlado, el laser cladding permitió la solidificación del material con la misma orientación que la microestructura original mediante la introducción de gradiente térmico que guiaba el crecimiento del grano. Sin embargo, existen desafíos para lograr una estructura SX sin grietas ni poros.
Rottwinkel et al. [8] usaron el laser cladding para evaluar los parámetros clave que influyen en la microestructura del cordón realizado, pero en el estudio no se obtuvo un cordón completo monocristalino ya que se obtenía microestructura SX con grietas o microestructura policristalina sin grietas, ambas con precalentamiento previo. Llegaron a la conclusión de que un ajuste adecuado del enfriamiento indirecto era el parámetro más prometedor para lograr los mejores resultados. En investigaciones posteriores [9], se determinó que una combinación de precalentamiento y enfriamiento era la más adecuada. Por otro lado, otra investigación sobre la reparación de la punta de los álabes mediante laser cladding concluyó que se puede obtener un crecimiento epitaxial adecuado en sustratos monocristalinos con un impacto de calor mínimo en el componente si se seleccionan los parámetros de proceso adecuados [3].
Para el trabajo que se presenta en este estudio se ha seleccionado la superaleación con base de níquel Rene 80, marca registrada de GE, debido a su amplio uso como aleación para fabricar álabes de turbina. La aleación posee una muy buena resistencia a la corrosión en caliente, estabilidad a largo plazo y resistencia a altas temperaturas, pero debido a su alta concentración de Al + Ti (8% en peso) es muy susceptible al agrietamiento en el HAZ y es difícil de soldar. Se pueden encontrar pocos estudios sobre Rene 80 monocristalino, y se refieren principalmente a investigaciones sobre agrietamiento [10, 11], concluyendo que la potencia láser y el tamaño de grano tuvieron un efecto significativo en la aparición y la longitud de las grietas. La aplicación de un tratamiento térmico previo a la soldadura impidió la formación de boruros intergranulares e indujo una dureza moderada a la aleación dando como resultado un HAZ casi libre de grietas [12]. Con soldadura GTA la respuesta microestructural de SX Rene 80 [2] dio lugar a una microfisura a lo largo de algunos límites de grano. Por otro lado, se investigaron los efectos de un recubrimiento manual y con laser cladding [13] en Rene 80, donde la resistencia mecánica de la muestra realizada por laser cladding fue menor que la de la soldadura manual, pero tras aplicar HIP, los huecos producidos durante el laser cladding se redujeron considerablemente y ambas muestras se volvieron similares.
Por lo tanto, estudios previos han demostrado que la susceptibilidad de Rene 80 al agrietamiento en el HAZ se controla mediante tratamientos térmicos previos a la soldadura y que sus propiedades mecánicas pueden mejorarse con tratamientos posteriores. Sin embargo, existe una falta de información en la literatura sobre cómo obtener un buen monocristal de Rene 80 mediante la selección de las condiciones de proceso adecuadas. El objetivo de este trabajo es correlacionar los parámetros del proceso y las propiedades del crecimiento con la microestructura de Rene 80 obtenida, determinando un rango de trabajo que promoverá la morfología SX. Este trabajo aprovecha la tecnología del laser cladding para crear un gradiente de temperatura y una velocidad de solidificación favorables mediante el ajuste de los parámetros del proceso.
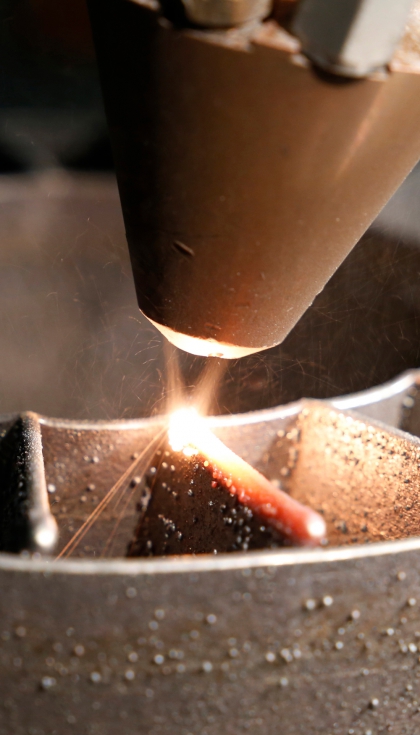
2. Proceso experimental
2.1. Equipamiento experimental
El sistema experimental consistió en un cabezal láser High Yag BIMO y una boquilla de aporte láser de IWS COAXpowerline. Todo el sistema estaba situado en una máquina de seis ejes controlada por un CNC. El polvo se almacenó en un alimentador de polvo Sulzer Metco Twin-10C y la tolva se calentó hasta 50°C mediante una cubierta de calentamiento individual. Se usó argón 99,991% como gas transporte. El cono de polvo se optimizó con un flujo de gas argón de 5 l/min y se hizo coincidir el punto focal del polvo con el plano de enfoque del láser, optimizando la captura de polvo. Se utilizó una cámara de 160 fps Photonfocus MV-D1024E-160-CL CMOS situada perpendicular a la boquilla para monitorizar la piscina fundida. Una tarjeta de adquisición Dalsa Xcelera-CL-PX4 gobiernó la cámara y enviaba la imagen a un PC para analizarla. La combinación de un filtro de hendidura de 1064 nm y un filtro de paso largo de 700 nm optimizó la calidad de la piscina fundida monitorizada, evitando los destellos del polvo y del haz láser. La cámara se alineó con el eje de la máquina y se calibró, obteniendo una equivalencia de 17,5 micras/píxel.
2.2. Diseño de experimentos
Los experimentos de laser cladding se realizaron sobre placas base SX Rene 80 utilizando también polvo SX Rene 80 como material de aporte. La granulometría del polvo era -125 + 45 micras y se fabricó por atomización de gas. En las placas base se realizaron análisis de composición y RX para asegurar idoneidad, encontrándose la orientación <001> normal a la superficie. Durante las pruebas láser, la placa base se mantuvo fija y el cabezal de laser cladding se movió perpendicularmente a ella. Los experimentos se llevaron a cabo variando los parámetros del proceso para determinar la ventana de proceso óptima para obtener la microestructura SX. La tabla 1 muestra los valores utilizados del diámetro del haz láser, la velocidad de avance del cabezal, la potencia del láser y el flujo del polvo. Todas las pruebas se realizaron sin calentamiento del sustrato. En los primeros experimentos se instaló una cubierta de protección y se usó gas Ar para tener un área aportada libre de oxígeno y por tanto inerte. Además, también se utilizó láser desfocalizado. No se observaron diferencias con respecto al proceso de cladding correspondiente sin el entorno inerte o con láser focalizado. Se realizaron cordones individuales de 20 mm de longitud y se analizaron metalográficamente, seleccionando los parámetros que generaron SX. A continuación, se realizaron por laser cladding paredes de hasta 10 capas para estudiar la microestructura en función de la altura. Se prepararon probetas metalográficas cortando el área de interés, encapsulando la muestra, enfriando con agua y puliendo con soluciones de diamante de 6, 3 y 0,1 micras. Las probetas se atacaron con reactivo Kalling y se observaron con un microscopio óptico.
3. Resultados y discusión
Los resultados del análisis experimental del efecto de los parámetros de laser cladding sobre la microestructura mostraron que, dependiendo de la densidad de energía utilizada, era crucial para tener estructura monocristalina el tipo de combinación entre la velocidad del aporte y la potencia del láser. Además, el resultado más importante de este estudio fue la indicación de la posibilidad de producir una microestructura monocristalina cuando se trabaja en el rango apropiado de parámetros sin necesidad de ningún tratamiento adicional. El extenso estudio experimental para encontrar la ventana de trabajo se muestra gráficamente en la figura 1. Esta figura muestra el efecto de variar la velocidad del aporte y la potencia con diferentes diámetros de haz láser. Los resultados incluyen diferentes caudales de polvo. En las gráficas se pueden distinguir diferentes áreas en función de la microestructura obtenida. Las áreas blancas corresponden a zonas de microestructura SX y las áreas negras a zonas policristalinas o con grietas y poros. Se han definido tres microestructuras intermedias mediante patrones con distinto grado de entramado, correspondientes a la aparición de defectos: monocristal con granos aislados (SG), policristal y policristal con poros. Con el diámetro de haz láser más pequeño se requirieron bajas potencias y altas velocidades de aporte para obtener SX, mientras que con el tamaño de haz más grande, dos áreas generaron microestructura SX, correspondiendo a trabajar a potencias y velocidades de aporte bajas o a potencias y velocidades de aporte altas. Esta diferencia se explicó en función de la diferente densidad de energía de ambos escenarios, factor que gobernó los valores de las condiciones del proceso requeridas para hacer crecer un SX. Considerando el diámetro de haz láser más pequeño, la alta densidad de energía en sí misma poseía el calor necesario para promover la microestructura SX y, en este sentido, las bajas potencias y la alta velocidad eran suficientes para obtenerla. Además, en este caso se observó que el exceso de calor debido a las altas potencias y la baja velocidad se convirtió en grietas y poros. Por otro lado, considerando el diámetro de haz láser más grande, la baja densidad de energía no fue suficiente para generar SX, requiriéndose una combinación adecuada de potencia y velocidad para producirla. Ensayos con diámetros de haz láser intermedios confirmaron las tendencias. Con respecto al polvo, los valores altos favorecieron la microestructura SX a altas densidades de energía, mientras que se observó una tendencia opuesta para densidades de energía bajas.
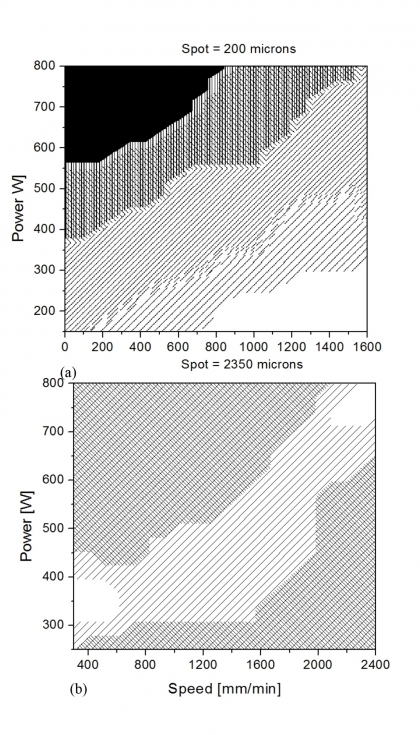
En la figura 2 se muestran imágenes ópticas de distintos tipos de microestructura obtenida en los ensayos realizados por laser cladding. Defectos como grietas o poros se observaron en cordones donde se utilizaron parámetros fuera de la ventana de proceso definida como ideal. Al comparar las condiciones del proceso y el haz generado, se apreció que la velocidad de aporte era el parámetro principal que la afectaba, causando un haz más profundo a bajas velocidades.
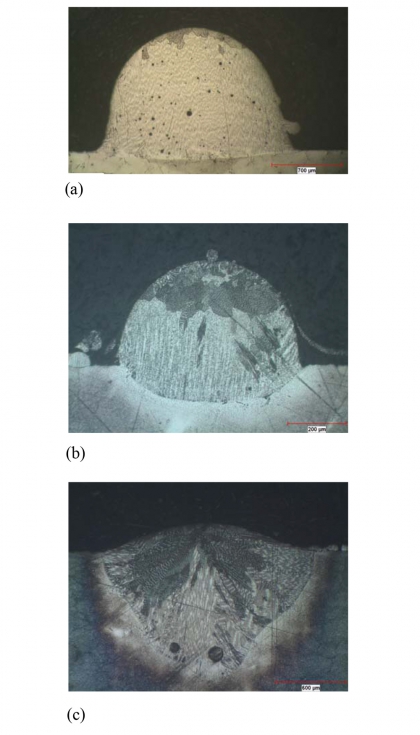
Se mecanizaron paredes rectas delgadas de 0,95 a 1,4 mm de ancho para observar el comportamiento de la microestructura SX en función de distintas anchuras base y, analizando de este modo el rendimiento de la velocidad de enfriamiento. No se detectó diferencia entre la microestructura obtenida en las placas base y la correspondiente sobre pared delgada. Así, la ventana de trabajo obtenida trabajando en las placas fue válida también para las paredes delgadas. Los experimentos realizados en paredes delgadas con el diámetro de haz láser mayor mostraron una disminución en el ancho del cordón con respecto al esperado. Esto se explicó por la pérdida de polvo debida a la delgada anchura de las paredes mecanizadas, que contrastaba con una mayor captura de polvo sobre las placas. Se aplicó una disminución en la velocidad de aporte para ajustar el ancho.
La figura 3 muestra un corte transversal a través de paredes con ocho capas aportadas alcanzando una altura de 4,3 mm. En las imágenes se aprecia el crecimiento SX a través de las diferentes capas, uniéndose adecuadamente la microestructura de la base y el material nuevo aportado. En la parte superior de la pared aportada hay una capa con granos aislados que se obtuvo en todos los cordones debido a las partículas de polvo que no se vuelven a fundir. Además, las áreas externas del aporte mostraron también este aumento de zonas policristalinas. De cara a trabajos de reparación, el crecer una altura mayor a la necesaria u obtener más grosor que el requerido permite eliminar estas áreas no deseadas mediante una operación de posprocesamiento y al mismo tiempo dejar el sobreespesor de material SX necesario para los componentes.
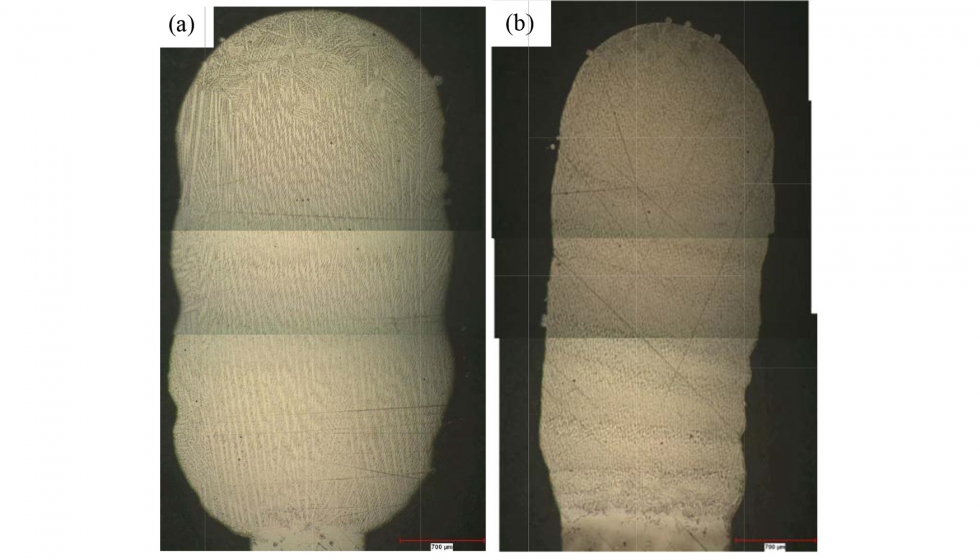
En la figura 4 se presentan las figuras de polos inversos (IPF) y los mapas de estructura de grano de EBSD de una sección transversal de la pared aportada. Se analizaron las desorientaciones de punto a punto y de origen a punto. Los resultados confirmaron la microestructura SX de las capas sucesivas y los granos aislados en la parte superior y en las áreas externas del aporte. Sí se detectaron pocos granos aislados especialmente en el haz, con una desorientación de hasta 5 º con respecto a la microestructura SX, mientras que en el análisis metalográfico estos granos fueron difíciles de detectar, incluso con un gran aumento.
Teniendo en cuenta los granos que aparecen en las áreas externas del aporte, la desorientación aumenta hasta 18º. Las zonas negras indican zonas con patrones de difracción de baja calidad. La figura 4 (c) incluye una representación esquemática superpuesta de la orientación de los cristales. Las fronteras de grano de ángulo alto (>12º) se muestran en azul, mientras que para valores bajos (3-12º) se usó el color negro.
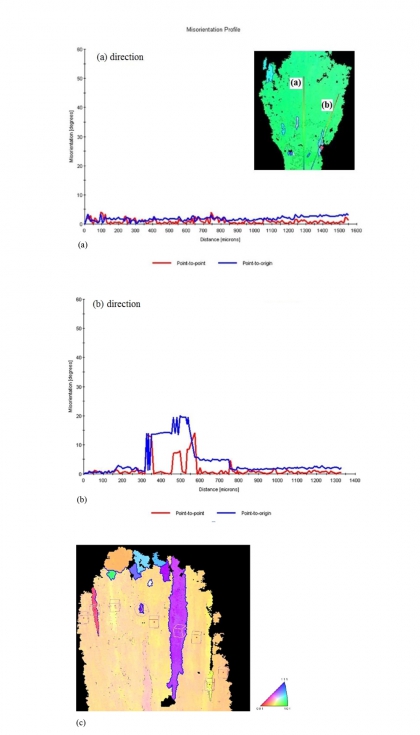
Se realizaron mediciones de microdureza para relacionarla con la microestructura obtenida. Las mediciones se llevaron a cabo tanto vertical como horizontalmente cada 250 micras en cordones aportados que presentaban microestructuras SX y no SX. Las mediciones verticales (figura 5a) mostraron que en las muestras SX la microdureza permaneció constante, aumentando ligeramente en el HAZ y en las primeras micras del material aportado con respecto al valor del material base. En muestras con cierto grado de policristalinidad o policristalinas la microdureza cambió drásticamente debido a las zonas policristalinas presentes. La misma tendencia se observó en las mediciones horizontales de microdureza (figura 5b), aumentando la variación del valor al deteriorarse la monocristalinidad. Comparando estos resultados con la bibliografía, se observó que los valores de microdureza de la microestructura SX de Rene 80 obtenidos por aporte láser eran similares a aquellas muestras que se habían sometido a tratamientos térmicos o condiciones de fabricación en atmósfera de vacío [14, 15].
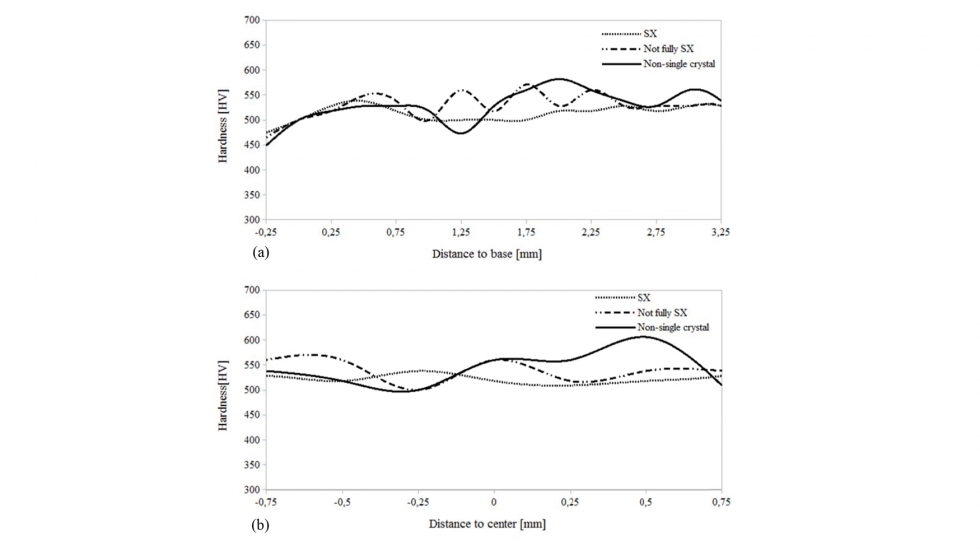
El tamaño de la piscina fundida se monitorizó para correlacionarlo con la microestructura del material. Las imágenes en tiempo real fueron tomadas y analizadas determinando los valores de área, eje mayor y menor. En estudios de monitorización previos [16] se obtuvo que el eje menor era el parámetro más estable para analizar el tamaño de la piscina fundida, tendencia que se verificó también en esta investigación. La figura 6 muestra los resultados de la monitorización de dos muestras con diferentes microestructuras. Mientas que un SX completo presentaba una ligera desviación del valor de tamaño de eje menor, en la muestra con aporte policristalino se apreciaba más variación. El valor del eje menor monitorizado concuerda con el ancho de cordón medido físicamente.
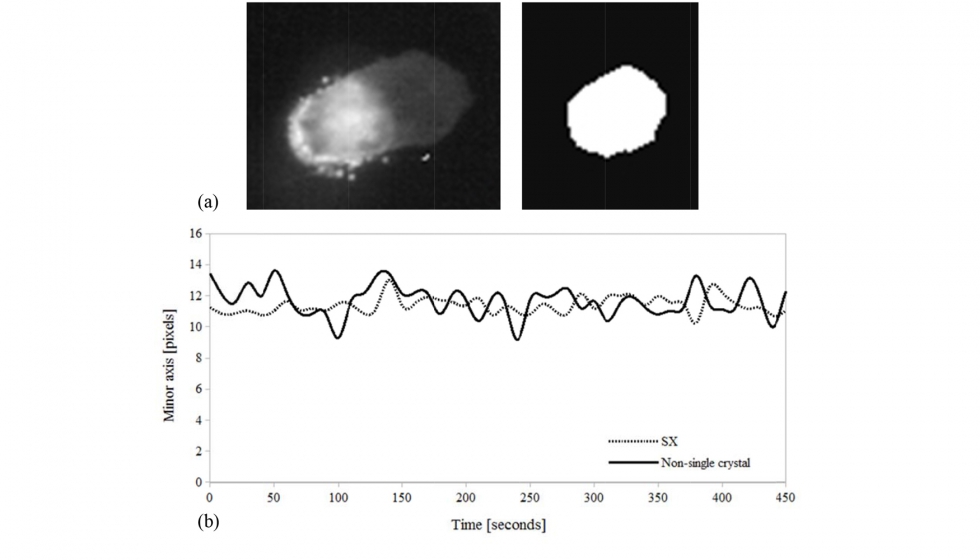
Figura 6. (a) Señal de monitorización de la piscina fundida e imagen binarizada; (b) Evolución del eje menor en muestras SX y policristalinas.
Finalmente, la experimentación se concluyó con la reparación de la punta de un álabe de turbina de Rene 80 mediante laser cladding. La figura 7 muestra una vista general del recrecido realizado sobre placa base y en el perfil mecanizado de un álabe de turbina. Debido a los cambios en el ancho del álabe se utilizaron diferentes combinaciones de parámetros para tener suficiente material sin sobrecalentamiento, poniendo especial cuidado en no fundir los bordes mientras se aseguraba una buena forma. El análisis metalográfico reveló que la orientación monocristalina de la placa base se mantuvo a través de la unión con el material depositado y se mantuvo a lo largo de las capas a pesar de no utilizar parámetros de proceso constantes.
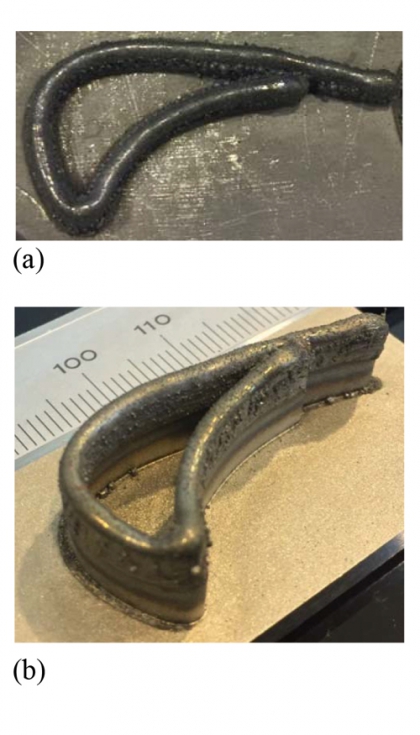
4. Conclusiones
Se realizó una investigación experimental sobre el uso de la técnica de laser cladding con la superaleación con base de níquel Rene 80 para estudiar la relación de la microestructura obtenida, las condiciones del proceso utilizadas y las propiedades de los cordones realizados. Se ha demostrado que no solo se puede lograr con laser cladding un crecimiento de Rene 80 sin grietas, sino también una microestructura monocristalina, dependiendo de la elección ideal de los parámetros del proceso, sin ningún tratamiento adicional. Las principales conclusiones pueden resumirse como:
- El aporte de material por laser cladding presentó una buena unión microestructural entre la base y el material aportado.
- Se obtuvieron diferentes microestructuras en función de los valores de los parámetros del proceso seleccionados, variando de SX a policristalino o policristalino con grietas y poros. El factor clave que gobernó el resultado fue la densidad de energía utilizada. Los mapas de EBSD confirmaron los resultados mostrados en los resultados metalográficos.
- Se definieron mapas de microestructura delimitando la ventana de trabajo y los correspondientes valores de los parámetros necesarios en función de la microestructura a obtener.
- Utilizando los mismos valores en los parámetros, no se detectó ninguna diferencia entre la microestructura obtenida en las placas y la correspondiente sobre paredes delgadas, lo que refleja la independencia de la microestructura y el ancho de la base.
- En las muestras monocristalinas la microdureza se mantuvo constante, mientras que las zonas policristalinas hicieron variar la microdureza drásticamente. Los resultados obtenidos con el aporte láser sin ningún tratamiento térmico adicional fueron similares a los resultados encontrados en literatura en los que las muestras de Rene 80 se sometieron a tratamientos térmicos de homogeneización adicionales y condiciones de fabricación en atmósfera de vacío.
- El eje menor monitorizado fue el parámetro más estable para analizar el tamaño de la piscina fundida. Las microestructuras monocristalinas presentaron una ligera desviación en el valor del tamaño de eje menor, mientras que se observó una mayor variación en las muestras con microestructura policristalina.
- Para la validación del proceso se realizó la reparación de la punta de un álabe variando los parámetros de proceso con el fin de adecuar la anchura de la pared aportada a la del perfil del álabe. Los resultados fueron satisfactorios, manteniéndose la microestructura monocristalina tanto en altura, a través de la unión de las distintas capas, como en longitud, a través de la unión de zonas con distintos parámetros de trabajo.
Agradecimientos
Los autores desean agradecer al Ministerio de Economía y Competitividad español por su apoyo en el proyecto Retos-Colaboración ‘Cladplus: Sistemas avanzados para la fabricación y reparación inteligente de componentes por plaqueado láser’ (RTC-2014-2163-5).
Referencias
[1] Konter, M., Thurmann, M.: Materials and manufacturing of advanced industrial gas turbine components. J. Mater. Process. Tech. 117, 386-390 (2001)
[2] Sidhu, R.K., Ojo, O.A., Chaturvedi, M.C.: Microstructural response of directionally solidified René 80 superalloy to gas-tungsten arc welding. Metall. Mater. Trans. A 40A, 150-162 (2009)
[3] Henderson, M.B., Arrell, D., Heobel, M., Larsson, R., Marchant G.: Nickel-based superalloy welding practices for industrial gas turbine applications. Sci. Technol. Weld. Joi. 9 (1), 13-21 (2004)
[4] Liu, W., DuPont, J.N.: Effects of melt-pool geometry on crystal growth and microstructure development in laser surface-melted superalloy single crystals. Mathematical modeling of single-crystal growth in a melt pool (part I). Acta Mater. 52, 4833-4847 (2004)
[5] Liang, Y.J., Wang, H.M.: Origin of stray-grain formation and epitaxy loss at substrate during laser surface remelting of single-crystal nickel-base superalloys. Mater. Design. 102, 297-302 (2016)
[6] Bansal, R., Acharya, R., Gambone, J.J., Das, S.: Experimental and theoretical analysis of scanning laser epitaxy applied to nickel-based superalloys. Solid Freeform Fabrication proceedings 496-503 (2011)
[7] Gaumann, M., Bezencon, C., Canalis, P., Kurz, W.: Single-crystal laser deposition of superalloys: processing-microstructure maps. Acta Mater. 49, 1051-1062 (2001)
[8] Rottwinkel, B., Schweitzer, L., Noelke, C., Kaierle, S., Wesling, V.: Challenges for singlecrystal (SX) crack cladding. Phys. Procedia 56, 301-308 (2014)
[9] Rottwinkel, B., Noelke, C., Kaierle, S., Wesling, V.: Laser cladding for crack repair of CMSX-4 single-crystalline turbine parts. Lasers in manufacturing and Materials Processing 4 (1), 13-23 (2017)
[10] Rush, M.T., Colegrove, P.A., Zhang, Z., Courtot, B.: An investigation into cracking in nickelbase superalloy repair welds. Adv. Mat. Res. 89-91, 467-472 (2010)
[11] Osterle, W., Krause, S., Moelders, T., Neidel, A., Oder, G., Volker, J.: Influence of heat treatment on microstructure and hot crack susceptibility of laser-drilled turbine blades made from René 80. Mater. Charact. 59, 1564-1571 (2008)
[12] Osoba, L.O., Sidhu, R.K., Ojo, A.: On preventing HAZ cracking in laser welded DS Rene 80 superalloy. Mater. Sci. Tech. Ser. 27 (5), 897-902 (2011)
[13] Kim, H.I., Park, H.S., Koo, J.M., Seok, C.S., Yang S.H., Kim, M.Y.: Evaluation of welding characteristics for manual overlay and laser cladding materials in gas turbine blades. J. Mech. Sci. Technol. 26 (7), 2015-2018 (2012)
[14] Ekrami, A., Moeinifar, S., Kokabi, A.H.: Effect of transient liquid phase diffusion bonding on microstructure and properties of a nickel base superalloy Rene 80. Mat. Sci. Eng. A-Struct. 456, 93-98 (2007)
[15] Barjesteh, M.M., Abbasi S.M., Madar, K.Z., Shirvani, K.: The effect of heat treatment on characteristics of the gamma prime phase and hardness of the nickel-based superalloy Rene 80. Mat. Chem. Phys. 227, 46-55 (2019)
[16] Moralejo, S., Penaranda, X., Nieto, S., Barrios, A., Arrizubieta, I., Tabernero, I., Figueras, J.: A feedforward controller for tuning laser cladding melt pool geometry in real time. Int. J. Adv. Manuf. Technol. 89 (1), 821-831 (2016)